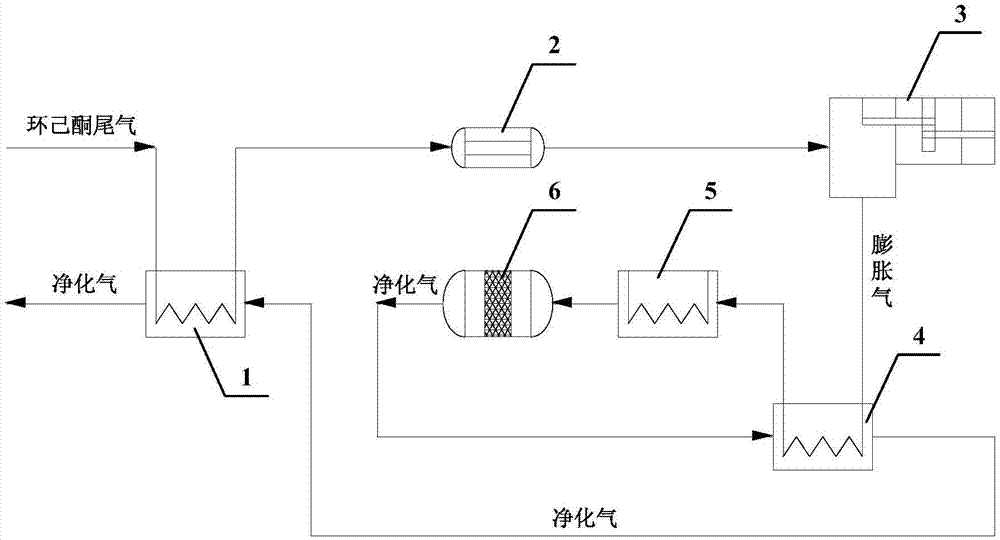
本实用新型涉及挥发性有机废气处理领域,特别涉及一种环己酮生产尾气的膨胀发电及净化处理装置。
背景技术:
:环己烷氧化法生产环己酮的装置在正常生产过程中,从尾气吸收塔(醇酮吸收塔)顶排放出来的环己酮尾气压力很高(约为10个大气压),且尾气中含有甲烷、乙烷、丙烷、丁烷、戊烷、环己烷、环己酮、环己醇等挥发性有机物和一氧化碳等可燃组份,若尾气不经处理直接排放至大气中,不仅造成能源的浪费,同时也对环境造成严重的污染。目前,公开号为CN106362548A的专利公开了一种环己烷氧化法生产环己酮过程中氧化尾气的处理方法,该方法采用水吸收塔对环己酮尾气进行吸收后再通过膨胀机将压力能转化为电能回收,但该方法存在以下缺陷:1.不能吸收尾气中的烷烃类气体;2.经水吸收塔吸收后的尾气富含饱和水,限制了膨胀机减压减温后的温度和压力(膨胀后尾气中夹带的液态水会对膨胀机叶轮造成严重破坏),也即限制了膨胀机的工作效率,使得环己酮尾气的压力能不能得到高效回收;3.水吸收塔采用废水系统的废水作为吸收剂,废水中的有机物容易被环己酮尾气反向气提,带来新的污染,同时水吸收塔底部水溶液送往废水处理系统回收醇酮又需要消耗大量热量,系统经济性较差。公开号为CN107469615A的专利公开了一种环己酮氧化尾气净化与综合利用方法,该方法采用吸附装置吸附环己酮尾气中的有机物得到第一中间气,催化氧化第一中间气得到净化气并利用净化气膨胀发电,但该方法存在以下缺陷:1.吸附装置的再生需要大量热能,且解析下来的有机物为混合物,利用价值低;同时第一中间气中仅含一氧化碳和少量有机物,不足以支撑催化氧化装置的热量平衡,也需要额外补充热能,整体经济效益低;2.吸附装置在工作时需要在吸附器之间进行切换,会对环己酮尾气的压力造成波动,影响膨胀发电机的稳定运行;3.催化氧化装置氧化过程中释放的热量不稳定,使得膨胀机工作效率大大降低;4.采用两级催化氧化,系统结构复杂,涉及压力容器多,危险性增加;技术实现要素:为了解决上述现有技术方案中的不足,本实用新型提供了一种结构简单、安全稳定运行,回收效率高、经济效益好,无污染排放的环己酮尾气处理装置。本实用新型的目的是通过以下技术方案实现的:一种环己酮尾气处理装置,所述环己酮尾气处理装置包括:第一加热器,待处理环己酮尾气经所述第一加热器加热后进入膨胀机;膨胀发电机组,所述膨胀发电机组包括膨胀机和发电机,所述膨胀机连接所述第一加热器的出口,发电机利用所述膨胀机输出的能量发电;第二加热器,膨胀尾气经第二加热器加热后进入氧化反应器;所述膨胀尾气为经膨胀机膨胀减压后的环己酮尾气;氧化反应器,膨胀尾气中的一氧化碳及挥发性有机物在所述氧化反应器中发生氧化反应转化为二氧化碳和水成为净化气。根据上述的环己酮尾气处理装置,优选地,所述环己酮尾气处理装置还包括:第一换热器,所述第一换热器位于所述第一加热器的上游,包括环己酮尾气通道和净化气通道,供待处理环己酮尾气与净化气进行热交换;所述环己酮尾气通道的出口连接所述第一加热器的入口。根据上述的环己酮尾气处理装置,优选地,所述环己酮尾气处理装置还包括:第二换热器,所述第二换热器设置在膨胀机和第二加热器之间的流路上,包括膨胀尾气通道和净化气通道,供膨胀尾气与净化气进行热交换;所述膨胀尾气通道的入口连接所述膨胀机的出口,膨胀尾气通道的出口连接所述第二加热器的入口;氧化反应器的出口连接所述第一换热器的净化气通道或第二换热器的净化气通道,第一换热器的净化气通道和第二换热器的净化气通道相连。根据上述的环己酮尾气处理装置,优选地,所述第一换热器为管式换热器。根据上述的环己酮尾气处理装置,可选地,所述第一换热器为翅片管式换热器,管程为环己酮尾气通道,设计温度100℃,设计压力1.1MPaG;壳程为净化气通道,设计温度150℃,设计压力:10kPaG,翅片管翅高5~25mm,翅片厚度0.8~1.5mm,翅片间距2~10mm。根据上述的环己酮尾气处理装置,优选地,所述第二换热器为板式换热器。根据上述的环己酮尾气处理装置,可选地,所述第二换热器的内程为膨胀尾气通道,设计温度350℃,设计压力10.0kPaG;外程为净化气通道,设计温度650℃,设计压力10kPaG。根据上述的环己酮尾气处理装置,可选地,所述第一加热器、第二加热器为管壳式蒸汽加热器或电加热器。根据上述的环己酮尾气处理装置,可选地,所述第一加热器采用管壳式蒸汽加热器,管程为环己酮尾气通道,设计温度200℃,设计压力1.1MPaG;壳程为蒸汽通道,设计温度200℃,设计压力1.0MPaG。根据上述的环己酮尾气处理装置,可选地,所述第二加热器采用管壳式蒸汽加热器,管程为膨胀尾气通道,设计温度350℃,设计压力10kPaG;壳程为蒸汽通道,设计温度350℃,设计压力9.0MPaG。根据上述的环己酮尾气处理装置,可选地,所述第一加热器、第二加热器采用电加热器,电加热器内电加热管采用三角型接法,设计温度350℃,设计压力10kPaG。根据上述的环己酮尾气处理装置,优选地,所述氧化反应器内装填有以蜂窝金属或蜂窝陶瓷为载体的涂覆有铂或钯的催化剂。与现有技术相比,本实用新型具有的有益效果为:1、本实用新型通过膨胀机将高压环己酮尾气膨胀减压同时利用发电机将膨胀机输出的能量发电,并催化氧化膨胀减压后的膨胀尾气以除去挥发性有机物和一氧化碳,保证环己酮尾气达标排放。2、本实用新型结构简单,不受尾气中有机物组份含量大幅波动的影响,安全稳定运行。3、本实用新型能高效回收高压环己酮尾气的压力能和尾气中可燃组份所富含的热能,回收效率高、经济效益好。4、净化气与膨胀机排出的膨胀尾气、待处理环己酮尾气热交换后排放,进一步提高热能利用率,增加收益。附图说明图1是本实用新型实施例1的环己酮尾气处理装置的结构示意图。具体实施方式图1和以下说明描述了本实用新型的可选实施方式以教导本领域技术人员如何实施和再现本实用新型。为了教导本实用新型技术方案,已简化或省略了一些常规方面。本领域技术人员应该理解源自这些实施方式的变型或替换将在本实用新型的范围内。本领域技术人员应该理解下述特征能够以各种方式组合以形成本实用新型的多个变型。由此,本实用新型并不局限于下述可实施方式,而仅由权利要求和它们的等同物限定。实施例1图1示意性地给出了本实施例的环己酮尾气处理装置的结构简图,如图1所示,所述环己酮尾气处理装置包括:第一换热器1,所述第一换热器包括环己酮尾气通道和净化气通道,供环己酮尾气与净化气进行热交换;第一加热器2,所述第一加热器的入口连接所述环己酮尾气通道的出口;膨胀发电机组3,所述膨胀发电机组包括膨胀机和发电机,所述膨胀机连接所述第一加热器的出口,发电机利用所述膨胀机输出的能量发电;第二换热器4,所述第二换热器包括膨胀尾气通道和净化气通道,供膨胀尾气与净化气进行热交换,所述膨胀尾气通道的入口连接所述膨胀机的出口;第二加热器5,所述第二加热器的入口连接所述膨胀尾气通道的出口;氧化反应器6,所述氧化反应器的入口连接所述第二加热器的出口,氧化反应器的出口连接所述第二换热器的净化气通道的入口,第二换热器的净化气通道的出口连接所述第一换热器的净化气通道的入口。本实施例的优势在于:环己酮尾气先膨胀发电后催化氧化回收热能,装置结构简单,膨胀发电机组安全稳定、高效率运行,不受环己酮尾气中有机物组分含量大幅浮动的限制,不受催化氧化反应的影响,回收效率高、经济效益好,尾气清洁排放。实施例2本实用新型实施例1的环己酮尾气处理装置在某环己烷氧化法生产环己酮企业中的应用。在该应用例中,该环己酮生产企业的醇酮吸收塔塔顶排放的环己酮尾气流量为13000Nm3/h,压力为1.08MPaG、温度为7~9℃,尾气中气体组分具体如下:气体组分参数N297.1V%O22~3V%CO2、CO<0.1V%有机物总量2000~10000mg/Nm3,4000~20000ppm丙烷≤400mg/Nm3在该应用例中,环己酮尾气处理装置设计如下:第一换热器采用翅片管式换热器,管程为环己酮尾气通道,设计温度100℃,设计压力1.1MPaG;壳程为净化气通道,设计温度150℃,设计压力:10kPaG,翅片管翅高5~25mm,翅片厚度0.8~1.5mm,翅片间距2~10mm。第二换热器采用板式换热器,内程为膨胀尾气通道,设计温度350℃,设计压力10.0kPaG;外程为净化气通道,设计温度650℃,设计压力10kPaG。第一加热器采用管壳式蒸汽加热器,管程为环己酮尾气通道,设计温度200℃,设计压力1.1MPaG;壳程为蒸汽通道,设计温度200℃,设计压力1.0MPaG。第二加热器采用管壳式蒸汽加热器,管程为膨胀尾气通道,设计温度350℃,设计压力10kPaG;壳程为蒸汽通道,设计温度350℃,设计压力9.0MPaG。当然,第一加热器、第二加热器也可以采用电加热器,若为电加热器,则电加热管采用三角型接法,设计温度350℃,设计压力10kPaG。氧化反应器采用固定床结构,设计温度650℃,设计压力10kPaG,催化剂使用空速为5000~40000h-1。环己酮尾气处理方法如下:S1.7~9℃、1.08MPaG的高压环己酮尾气经第一换热器换热,升温至40~60℃后进入第一加热器加热至150℃;S2.150℃的环己酮尾气进入膨胀机膨胀减压至0.05MPaG、降温至5~10℃,同时驱动发电机发电;S3.减压减温后的膨胀尾气与第二换热器换热至280~300℃,并经第二加热器加热至300~350℃后进入氧化反应器;S4.尾气中的有机物(丙烷、丁烷、戊烷、环己烷、环己酮和环己醇等)和一氧化碳在氧化反应器中转化为二氧化碳和水,成为350~650℃高温净化气,S5.高温净化气经第二换热器、第一换热器换热回收热量后排放,排气温度50~250℃。本应用例中环己酮尾气处理装置可产生每小时650kW的电,尾气中的有机物含量降低到30ppm以下,净化后的尾气可以直接向大气排放。当前第1页1 2 3