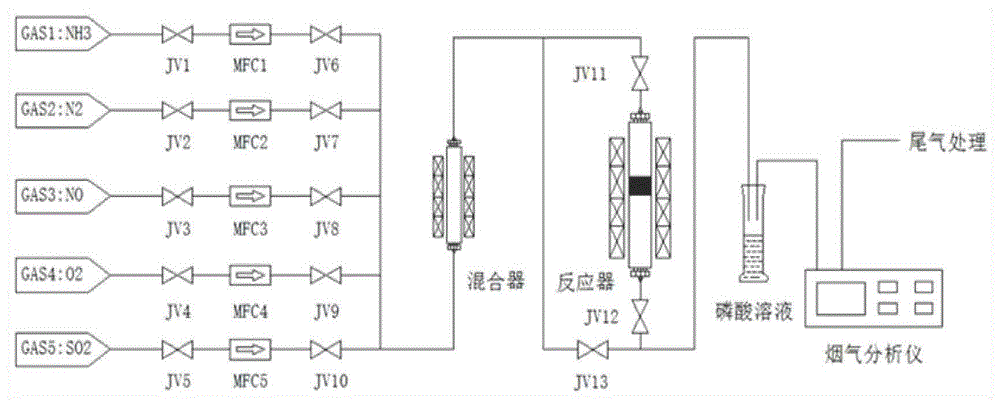
本发明涉及脱硝的
技术领域:
,具体而言,涉及钐掺杂锰系低温脱硝催化剂及其制备方法和应用。
背景技术:
:氮氧化物(nox)是pm2.5、光化学烟雾和酸雨等区域性大气污染的主要前驱体之一。nh3-scr脱硝是治理烟气中nox的主流技术,该技术的核心是脱硝催化剂。燃煤电站锅炉烟气脱硝系统中使用的钒钨钛脱硝催化剂的活性温度窗口一般为300~400℃。然而,钢铁、烧结、水泥等非电行业的烟气排放温度一般低于280℃,采用钒钨钛脱硝催化剂将难以发挥最佳的活性。因此,开发低温活性好、抗硫性能强的低温脱硝催化剂具有重要理论价值和广泛应用前景。过渡金属的氧化物作为脱硝催化剂已受到较多的研究和实践。在诸多过渡金属中,mn由于其特殊的价电子构型、良好的氧化还原性质,因此被广泛用于脱硝领域。但纯的mnox脱硝性能和n2选择性欠佳且抗硫抗水性能较差,因此通常会结合其他金属进行改性。例如,中国发明专利cn109772417a公开了一种含钐低温脱硝催化剂及其制备方法,虽然制备出了含有ti、mn和sm的脱硝催化剂,但是由于以ti(so4)2、mn(no3)2和sm(no3)3为原料以及采用沉淀法和对沉淀进行烧结,因此得到的脱硝催化剂为tio2、mno2和sm2o3构成的无序状混合物,很明显,由于脱硝活性较好的mno2和sm2o3可能被大量的tio2包裹,因此mno2和sm2o3难以充分地发挥脱硝作用。技术实现要素:本发明的主要目的在于提供脱钐掺杂锰系低温脱硝催化剂及其制备方法和应用,以解决现有技术中脱硝催化剂低温活性差的技术问题。为了实现上述目的,根据本发明的第一个方面,提供了钐掺杂锰系低温脱硝催化剂。该钐掺杂锰系低温脱硝催化剂包括载体和活性组分,所述载体为tio2,所述活性组分为fe、mn、sm的氧化物。进一步地是,所述脱硝催化剂的比表面积≥80m2/g;所述脱硝催化剂的孔体积≥0.2cm3/g;所述脱硝催化剂的孔径为6~22nm。为了实现上述目的,根据本发明的第二个方面,提供了钐掺杂锰系低温脱硝催化剂的制备方法。该钐掺杂锰系低温脱硝催化剂的制备方法包括以下步骤:(1)以tio2、sm的可溶性盐、mn的可溶性盐以及fe的可溶性盐为原料,采用沉积沉淀法获得沉淀;(2)将沉淀洗涤、干燥、煅烧,即得到钐掺杂锰系低温脱硝催化剂。进一步地是,可溶性盐为硝酸盐或水合硝酸盐;或可溶性盐为乙酸盐或水合乙酸盐;或可溶性盐为硫酸盐或水合硫酸盐。进一步地是,原料中sm:mn:fe的摩尔比为(0.05~0.8):1:1。进一步地是,按照活性组分的质量为脱硝催化剂总质量的5~30%称取原料,所述的活性组分的质量按照sm的氧化物、mn的氧化物和fe的氧化物进行计算,所述催化剂总质量为所述活性组分的质量与原料中tio2的质量之和。进一步地是,所述的沉淀法采用的沉淀剂为碳酸氨。进一步地是,所述的沉积沉淀法在50~70℃下进行。进一步地是,煅烧温度为350~650℃,煅烧时间为1~3h。为了实现上述目的,根据本发明的第三个方面,提供了脱硝方法。该脱硝方法采用上述的钐掺杂锰系低温脱硝催化剂,或采用上述的制备方法制备得到的钐掺杂锰系低温脱硝催化剂。在本发明的钐掺杂锰系低温脱硝催化剂以tio2(二氧化钛)为载体,掺杂金属的氧化物均匀地分布于tio2的表面,可以充分地发挥脱硝活性。在掺杂金属的氧化物中,fe(铁)的氧化物在中温段具有良好催化活性并具有良好的n2选择性;sm(钐)作为稀土金属,其最外层电子结构为4f66s2,5d轨道是空轨道,空轨道可作为“电子转移站”对催化作用有一定的助力,显示出具备高储氧能力和高晶格氧化活性,能作为助剂进一步提升脱硝催化剂的性能。当然,所述的活性组分也可以是由ti、mn、fe、sm中的两种或两种以上构成的复合氧化物。综上可知,本发明以tio2为载体,成功制备出了多种掺杂金属氧化物负载的脱硝催化剂,展示出了优异的低温脱硝活性,非常适于对我国非电行业排放的低温烟气中的nox进行脱硝处理。下面结合附图和具体实施方式对本发明做进一步的说明。本发明附加的方面和优点将在下面的描述中部分给出,部分将从下面的描述中变得明显,或通过本发明的实践了解到。附图说明构成本发明的一部分的附图用来辅助对本发明的理解,附图中所提供的内容及其在本发明中有关的说明可用于解释本发明,但不构成对本发明的不当限定。在附图中:图1为模拟工业烟气成分与浓度进行nh3-scr脱硝测试的装置的结构示意图。图2为实施例1-3以及对照例1的脱硝催化剂的xrd图谱。图3为实施例1-3以及对照例1的脱硝催化剂的mn2p图谱。图4为实施例1-3以及对照例1的脱硝催化剂的sm3d图谱。图5为实施例1-3以及对照例1的脱硝催化剂的fe2p图谱。图6为实施例1-3以及对照例1的脱硝催化剂的o1s图谱。图7为实施例1-3以及对照例1的脱硝催化剂的氮气吸脱附曲线。图8为实施例1-3以及对照例1的脱硝催化剂的孔径分布图。图9为实施例1-3以及对照例1的脱硝催化剂在nh3-scr脱硝测试时no脱除效率随温度的变化曲线。图10为实施例1-3以及对照例1的脱硝催化剂经硫化处理后在nh3-scr脱硝测试时no脱除效率随温度的变化曲线。图11为mn-fe/tio2(s)和sm-mn-fe/tio2-0.3(s)的no脱除效率随时间的变化曲线。图12为sm-mn-fe/tio2-0.3持续地在温度为180℃下进行nh3-scr脱硝时no脱除效率随时间的变化曲线。图13为实施例2、4-6的脱硝催化剂的mn2p图谱。图14为实施例2、4-6的脱硝催化剂的sm3d图谱。图15为实施例2、4-6的脱硝催化剂的fe2p图谱。图16为实施例2、4-6的脱硝催化剂的o1s图谱。图17为实施例2、4-6的脱硝催化剂在nh3-scr脱硝测试时no脱除效率随温度的变化曲线。图18为sm-mn-fe/tio2-0.3(1)、sm-mn-fe/tio2-0.3(2)和sm-mn-fe/tio2-0.3(3)在nh3-scr脱硝测试时no脱除效率随温度的变化曲线。具体实施方式下面结合附图对本发明进行清楚、完整的说明。本领域普通技术人员在基于这些说明的情况下将能够实现本发明。在结合附图对本发明进行说明前,需要特别指出的是:本发明中在包括下述说明在内的各部分中所提供的技术方案和技术特征,在不冲突的情况下,这些技术方案和技术特征可以相互组合。此外,下述说明中涉及到的本发明的实施例通常仅是本发明一部分的实施例,而不是全部的实施例。因此,基于本发明中的实施例,本领域普通技术人员在没有做出创造性劳动的前提下所获得的所有其他实施例,都应当属于本发明保护的范围。关于本发明中术语和单位。本发明的说明书和权利要求书及有关的部分中的术语“包括”、“具有”以及它们的任何变形,意图在于覆盖不排他的包含。实施例1钐掺杂锰系低温脱硝催化剂的制备方法如下:(1)原料为tio2、mn(ch3coo)2·4h2o、fe(no3)3·9h2o和sm(no3)3,所述的活性组分的质量按照sm2o3、mno2和fe2o3进行计算,按照活性组分的质量为脱硝催化剂(即tio2和活性组分的总质量)的25%以及sm:mn:fe的摩尔比为0.1:1:1称取原料。(2)采用沉积沉淀法获得沉淀,具体为:在60℃条件下将mn(ch3coo)2·4h2o、fe(no3)3·9h2o和sm(no3)3溶于100ml蒸馏水中,然后加入tio2并搅拌30分钟,然后滴加1.5mol/l的(nh4)2co3溶液至ph为8.4,然后继续搅拌2h,再经过滤、洗涤、烘干,即得到沉淀。(3)在流动空气气氛下,将沉淀在450℃下煅烧2h,即得到脱硝催化剂,将其命名为sm-mn-fe/tio2-0.1。实施例2与实施例1的区别仅在于:按照理论计算得到的sm:mn:fe的摩尔比为0.3:1:1称取原料,最终得到的脱硝催化剂被命名为sm-mn-fe/tio2-0.3或sm-mn-fe/tio2-450。实施例3与实施例1的区别仅在于:按照理论计算得到的sm:mn:fe的摩尔比为0.5:1:1称取原料,最终得到的脱硝催化剂被命名为sm-mn-fe/tio2-0.5。对照例1与实施例1的区别仅在于:未采用sm(no3)3,按照理论计算得到的mn:fe的摩尔比为1:1称取原料,最终得到的脱硝催化剂被命名为mn-fe/tio2。实施例4与实施例2的区别仅在于:将沉淀在350℃下煅烧2h,最终得到的脱硝催化剂被命名为sm-mn-fe/tio2-350。实施例5与实施例2的区别仅在于:将沉淀在550℃下煅烧2h,最终得到的脱硝催化剂被命名为sm-mn-fe/tio2-550。实施例6与实施例2的区别仅在于:将沉淀在650℃下煅烧2h,最终得到的脱硝催化剂被命名为sm-mn-fe/tio2-650。对照例2脱硝催化剂的制备方法如下:首先,按照实施例2的配比称取原料。然后,采用浸渍法获得沉淀,具体为:计算tio2的饱和吸水量,然后向tio2中滴加饱和吸水量的水备用;将mn(ch3coo)2·4h2o、fe(no3)3·9h2o和sm(no3)3溶于蒸馏水中,蒸馏水的使用量=100ml-饱和吸水量,然后加入已吸水饱和的tio2中并在室温下浸渍1h,然后在110℃的烘箱中浸渍12h,再经过滤、洗涤、烘干,即得到沉淀。最后,在流动空气气氛下,将沉淀在450℃下煅烧2h,即得到脱硝催化剂。所得脱硝催化剂的物相分析以及晶体结构的确定采用粉末x射线衍射(xrd)进行表征,采用浩元仪器生产的dx-2700型x射线衍射仪,实验电压为40kv,电流为30ma,采用cu靶ka辐射(λ=0.15418nm),扫描范围2θ为10~80°。根据国际衍射数据中心的参考数据对xrd结果进行索引确定物相。所得脱硝催化剂的n2吸附脱附曲线采用美国康塔仪器有限公司的autosorb-iq型气体吸附仪测定,使用brunauer-emmett-teller(bet)和barrett-joyner-halenda(bjh)方法计算比表面积,孔径分布和孔体积。所得脱硝催化剂的表面元素价态及浓度采用x射线光电子能谱(xps)进行表征,采用赛默飞escalab250xix射线电子能谱仪进行测定,并在测试后中将c的峰值与标准值(284.6ev)进行校正。用xpspeak4.1软件进行分峰拟合,根据峰面积大小计算相对元素含量。所得脱硝催化剂的催化剂活性采用图1所示的模拟工业烟气成分与浓度的装置进行测试。其中,烟气流量为700ml/min,脱硝催化剂的装填体积为1ml,空速为42000h-1;烟气组分:no的浓度为500ppm,nh3的浓度为500ppm,o2的体积分数为5%,so2的浓度为100ppm(需要时),h2o的体积分数10%(需要时),平衡气体为n2;测试温度窗口为80~300℃,在记录数据时每隔20℃停留30分钟以保证读数稳定;质量流量计控制气体流量;通过烟气分析仪检测通过反应器后的no浓度。脱硝催化剂脱硝效率计算公式如下:no脱除效率用η表示:式中,[no]in表示no进入脱硝催化剂前的浓度;[no]out表示no通过脱硝催化剂后的浓度。以下通过表征及性能测试结果说明本发明的有益效果。实施例1-3以及对照例1的脱硝催化剂的表征及性能测试结果如下:图2为实施例1-3以及对照例1的脱硝催化剂的xrd图谱。其中,纵坐标为强度。如图2所示,四种不同sm含量的脱硝催化剂的tio2载体的衍射峰的强度和位置几乎没有变化,只存在锐钛矿型tio2的衍射峰而无金红石型tio2的衍射峰。mn-fe/tio2在2θ为33.117°时出现了一个强度较弱的fe2o3衍射峰,这说明存在部分铁氧化物出现了结晶化。引入sm后的三种脱硝催化剂中fe2o3的衍射峰消失,说明sm的引入降低了铁氧化物在载体表面的结晶程度,提高了载体表面上的铁氧化物的分散性。同时,引入sm后的三种脱硝催化剂除了tio2的衍射峰外检测不出其他物种的衍射峰,这说明活性组分能在催化剂表面均匀分散。图3-6为实施例1-3以及对照例1的脱硝催化剂的xps图谱,其中,图3为mn2p图谱,图4为sm3d图谱,图5为fe2p图谱,图6为o1s图谱。其中,横坐标为结合能,纵坐标为强度,下同。如图3所示,不对称的mn2p3/2峰证实了锰的混合价态的存在,因此可将mn2p3/2的光谱分为两个峰:641.0~641.4ev处归属于mn2o3,642.1~642.7ev归属于mno2。通过计算峰面积可以得出mn4+/mn以及mn3+/mn的数值,结果列于表1。从表1中可知,mn4+/mn含量随着sm的加入出现明显变化。其中,mn-fe/tio2的mn4+/mn最低(49.2%),而sm-mn-fe/tio2-0.3具有最高的mn4+/mn(56.8%),说明sm的引入有助于提高mn4+的含量。mn4+能够促进no氧化,生成的no2将参与快速scr反应,进而提高催化效率。如图4所示,sm的3d轨道可以分为两个峰:1081.6ev处的峰归属于sm2+,1083.6ev处的峰归属于sm3+。通过计算峰面积可以得出sm2+/sm以及sm3+/sm的数值,结果列于表1。从表1中可知,sm2+/sm的变化趋势与mn4+/mn的一致。如图5所示,位于711ev和725ev的峰分别对应fe2p3/2轨道和fe2p1/2轨道,在718ev处出现了一个卫星峰。将fe2p3/2的光谱分为两个峰:710.2~710.5ev归属于fe2+,711.8~712.4ev归属于fe3+。通过计算峰面积可以得出fe2+/fe以及fe3+/fe的数值,结果列于表1。从表1中可知,sm-mn-fe/tio2-0.3的fe2+/fe的含量最高为54%。如图6所示,o1s的轨道可以分成两个峰:529.3~529.5ev归属于晶格氧(标记为ol,如o2-),530.7~531.7ev归属于化学吸附氧(标记为os,如o22-、o-)。通过计算峰面积可以得出os/o和ols/o的数值,结果列于表1。从表1中可知,sm-mn-fe/tio2-0.3的化学吸附氧浓度最高。化学吸附氧比晶格氧迁移性更高,os/o越高将越有利于促进no氧化为no2,从而有助于快速scr反应的进行。表1图7为实施例1-3以及对照例1的脱硝催化剂的氮气吸脱附曲线,横坐标为p/p0,纵坐标为n2吸附量。图8为实施例1-3以及对照例1的脱硝催化剂的孔径分布图,横坐标为孔径,纵坐标为孔径分布。如图7所示,四种sm含量不同的脱硝催化剂具有相似的吸附等温线,根据iupac分类规则应将其归为iv型等温线。当p/p0大于0.99时,n2吸附量并未明显增加,说明无大孔结构存在。四种脱硝催化剂均出现了明显的h3型回滞环,说明孔结构主要是由颗粒堆积而形成的狭缝孔。如图8所示,四种脱硝催化剂的孔径分布主要集中在6~22nm,这表明存在着明显的介孔特征。计算得到的比表面积、孔体积和平均孔径数据列于表2。从表2可以看出,将sm引入脱硝催化剂后,脱硝催化剂的比表面积和孔体积随着sm含量的增加呈现先增加后减小的趋势,其中,sm-mn-fe/tio2-0.3具有最大的比表面积和最大的孔体积。更大的比表面积能提供更多的活性位点,这将提高气体分子与活性位点的接触概率,进而有助于吸附气体分子从而提高催化效率。表2样品编号比表面积(m2/g)孔体积(cm3/g)平均孔径(nm)mn-fe/tio2111.060.37713.58sm-mn-fe/tio2-0.1106.720.36913.85sm-mn-fe/tio2-0.3147.040.44912.22sm-mn-fe/tio2-0.586.300.28813.37图9为实施例1-3以及对照例1的脱硝催化剂在nh3-scr脱硝测试时no脱除效率随温度的变化曲线。其中,横坐标为温度,纵坐标为no脱除效率,下同。如图9所示,mn-fe/tio2在100℃的no脱除效率为73.37%,在115℃的no脱除效率为91.12%,达到100%的no脱除效率的温度区间为135~270℃。引入sm之后的三种脱硝催化剂在100℃~140℃低温段的no脱除效率得到一定程度的提升并且拓宽了100%no脱除效率的温度区间。其中,sm-mn-fe/tio2-0.1在100℃的no脱除效率为75.74%,在115℃的no脱除效率为94.83%,在125~270℃的温度区间达到100%的no脱除效率。sm-mn-fe/tio2-0.3的no脱除效率最为优异,在100℃的no脱除效率为79.09%,在115℃的no脱除效率为97.24%,更是在120℃~270℃温度窗口都能保持100%的no脱除效率。sm-mn-fe/tio2-0.5的no脱除效率略有下降,但仍然能在125~265℃区间内能保持100%的no脱除效率。现有技术中的脱硝催化剂通常会因烟气中存在的so2和h2o发生严重的中毒现象。本发明采用了两种方法来探究so2对脱硝催化剂影响:一是采用so2预处理方式获得硫化处理后的脱硝催化剂,二是在模拟烟气中直接通入一定浓度的so2。硫化处理为:将新鲜的脱硝催化剂放置于反应器中并通入反应气,所述的反应气以n2为载体并含有浓度为100ppm的so2、体积分数为10%的h2o以及体积分数为5%的o2,在140℃下热处理1h即完成硫化。实施例1-3以及对照例1的脱硝催化剂硫化处理后分别标记为sm-mn-fe/tio2-0.1(s)、sm-mn-fe/tio2-0.3(s)、sm-mn-fe/tio2-0.5(s)和mn-fe/tio2(s)。图10为实施例1-3以及对照例1的脱硝催化剂经硫化处理后在nh3-scr脱硝测试时no脱除效率随温度的变化曲线。如图10所示,在测试温度范围内,硫化处理后的四种脱硝催化剂均无法达到100%的no脱除效率。但是,引入sm后的三种脱硝催化剂的抗硫性能明显优于无sm的mn-fe/tio2(s)。在140℃时,mn-fe/tio2(s)的no脱除效率为55%,sm-mn-fe/tio2-0.1(s)的no脱除效率提升至68%,sm-mn-fe/tio2-0.3(s)的no脱除效率可达到80%。并且,在测试温度范围内,mn-fe/tio2(s)达不到90%的no脱除效率,而sm-mn-fe/tio2-0.1(s)、sm-mn-fe/tio2-0.3(s)、sm-mn-fe/tio2-0.5(s)分别在180~300℃、160~300℃以及230~300℃达到90%以上的no脱除效率,可见,sm-mn-fe/tio2-0.3(s)具有最宽的温度窗口和更高的低温脱硝效率。将100ppm的so2引入模拟烟气中,持续地在温度为200℃、空速为42000h-1的条件下对mn-fe/tio2(s)和sm-mn-fe/tio2-0.3(s)进行nh3-scr脱硝测试。图11为mn-fe/tio2(s)和sm-mn-fe/tio2-0.3(s)的no脱除效率随时间的变化曲线。横坐标为时间,纵坐标为n2脱除效率,下同。如图11所示,在模拟烟气中引入so2之后,两种脱硝催化剂的no脱除效率均明显下降,但是sm-mn-fe/tio2-0.3(s)的抗硫性能明显优于mn-fe/tio2(s)。其中,mn-fe/tio2在引入so2后的第一个小时内no脱除效率下降十分明显(100%降至78.8%),之后两小时内缓慢下降(78.8%降至74.4%)并最终达到基本稳定状态(约73.8%),当停止引入so2后,no脱除效率恢复至86%。sm-mn-fe/tio2-0.3(s)的no脱除效率基本能够稳定在86%左右,停止so2的通入后no脱除效率可以恢复到95%。图12为sm-mn-fe/tio2-0.3持续地在温度为180℃下进行nh3-scr脱硝时no脱除效率随时间的变化曲线。在上述的四种脱硝催化剂中,sm-mn-fe/tio2-0.3的催化活性最优并且具有优异的稳定性。如图12所示,sm-mn-fe/tio2-0.3在60h内均保持100%的no脱除效率。实施例2、4-6的脱硝催化剂的表征及性能测试结果如下:图13-16为实施例2、4-6的脱硝催化剂的xps图谱,其中,图13为mn2p图谱,图14为sm3d图谱,图15为fe2p图谱,图16为o1s图谱。如图13所示,不对称的mn2p3/2峰证实了锰的混合价态的存在,因此mn2p3/2的光谱可以分成两个峰:641.0~641.5ev归属于mn2o3,642.1~642.8ev归属于mno2。通过计算峰面积可以得出mn4+/mn以及mn3+/mn的数值,结果列于表3。从表3可以看出,mn4+/mn的大小随着煅烧温度的增加呈现出先增加再减少的趋势,sm-mn-fe/tio2-450中mn4+/mn最高(56.8%),远大于sm-mn-fe/tio2-650中的mn4+/mn(41.13%)。如图14所示,sm的3d轨道可以分为两个峰:1081.6ev归属于sm2+,1083.6ev归属于sm3+。通过计算峰面积可以得出sm2+/sm以及sm3+/sm的数值,结果列于表3。从表3可以看出,sm2+/sm的变化趋势与mn4+/mn的一致。如图15所示,位于711ev和725ev的峰分别对应fe2p3/2和fe2p1/2,另外,在718ev处出现了一个卫星峰。对于fe2p3/2,可以将其分为两个峰:709.7~710.5ev归属于fe2+,711.3~712.4ev归属于fe3+。通过计算峰面积可以得出fe2+/fe以及fe3+/fe的数值,结果列于表3。从表3可以看出,sm-mn-fe/tio2-450具有最高的fe2+/fe。如图16所示,sm-mn-fe/tio2-350具有三个明显的峰:位于528.9ev的峰归属于ol,位于530.9ev的峰归属于os,位于532.6ev的峰归属于羟基。羟基会因为煅烧温度的升高被分解,因此其它三种脱硝催化剂仅出现两个峰:529.2~529.5ev归属于ol,531ev的峰归属于os。通过计算峰面积可以得出os/o和ols/o的数值,结果列于表3。从表3中可知,sm-mn-fe/tio2-450的os/o为38.70%,比其余样品明显更多,表明sm-mn-fe/tio2-450表面存在更多的o22-、o-。由于化学吸附氧比晶格氧迁移性更高,催化剂中os/o高的话更有利于将no氧化为no2,从而有助于快速scr反应的进行。表3图17为实施例2、4-6的脱硝催化剂在nh3-scr脱硝测试时no脱除效率随温度的变化曲线。如图17所示,煅烧温度严重影响了四种脱硝催化剂的脱硝性能。sm-mn-fe/tio2-350在100℃的no脱除效率为66.46%,在118℃的no脱除效率为91.66%,达到100%的no脱除效率的温度区间为135~250℃;sm-mn-fe/tio2-450具有最好的低温no脱除效率以及最宽的100%no脱除率温度区间,在100℃的no脱除效率为79.1%,在120~270℃均能保持100%的no脱除效率;相较于sm-mn-fe/tio2-450,sm-mn-fe/tio2-550和sm-mn-fe/tio2-650的no脱除效率有所降低。进一步测试对照例2的no脱除效率发现,对照例2的脱硝催化剂具有明显优于对照例1但是稍弱于实施例2的脱硝活性及脱硝稳定性进一步采用实施例2的工艺参数进行三次平行实验,所制得到的脱硝催化剂分别表示为sm-mn-fe/tio2-0.3(1)、sm-mn-fe/tio2-0.3(2)和sm-mn-fe/tio2-0.3(3),然后进行了nh3-scr脱硝测试。图18为sm-mn-fe/tio2-0.3(1)、sm-mn-fe/tio2-0.3(2)和sm-mn-fe/tio2-0.3(3)在nh3-scr脱硝测试时no脱除效率随温度的变化曲线。如图18所示,sm-mn-fe/tio2-0.3(1)、sm-mn-fe/tio2-0.3(2)和sm-mn-fe/tio2-0.3(3)的no脱除效率基本一致,均能在约120~270℃达到100%的脱硝效率。可见,沉淀法更适合于制备本发明的脱硝催化剂,并且沉淀法所需时间更短,工艺简单,重现性高,有助于工业化生产。以上对本发明的有关内容进行了说明。本领域普通技术人员在基于这些说明的情况下将能够实现本发明。基于本发明的上述内容,本领域普通技术人员在没有做出创造性劳动的前提下所获得的所有其他实施例,都应当属于本发明保护的范围。当前第1页12