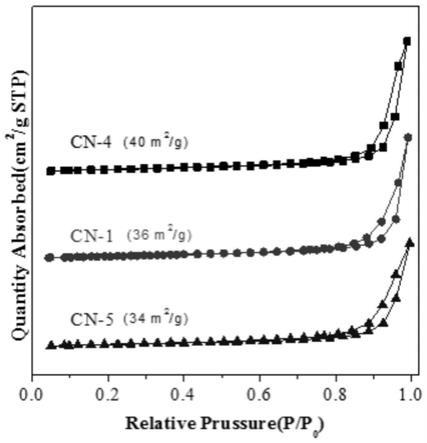
一种界面优化的mox/g-c3n4复合光催化剂及其制备方法和应用
技术领域
[0001]
本发明涉及催化剂领域,具体涉及一种界面优化的mox/g-c3n4复合光催化剂及其制备方法和应用。
背景技术:[0002]
进入21世纪,随着工业的迅速发展,环境污染和能源短缺问题日趋严重。其中水污染问题尤其严重,大量的有机污染物排放进入水中,破坏水质。考虑到水质与人们的生活密切相关,水污染问题亟需解决。相较传统的化学降解和生物降解法,光催化技术被认为是一种绿色、安全的解决方法。且太阳能储量巨大,故半导体光催化技术被认为有望解决上述问题。
[0003]
光催化的核心是光催化剂设计,相较于传统光催化剂(tio2、cds、zno等),g-c3n4由于抗酸、碱、光腐蚀,稳定性好,可见光响应,原料丰富和工艺简单得到了广泛的关注。但体相g-c3n4的比表面积小,对光的利用率有限,且光生电荷易复合,催化效率较低,限制了其应用范围。构建异质结结构可以有效促进光生电荷分离和迁移,如专利cn201910351490.2、专利cn201510661265.0、专利cn201910077846.8、专利cn201810641395.1等公开了数种半导体/氮化碳复合催化剂,助催化剂与g-c3n4间的内建电场促进了电子-空穴的迁移,同时肖特基势垒可以抑制电荷的回流从而提高光生载流子的分离效率,提升光催化性能。
技术实现要素:[0004]
本发明的目的在于针对现有技术存在的不足之处,首先,在光催化活性组分中引入多孔结构,在此基础上提高助剂在活性组分上的均匀分布,从而为传统mo
x
/g-c3n4复合结构提供一种界面优化的制备方法,并将其应用于光催化污水净化。一种界面优化的mo
x
/g-c3n4复合光催化剂,该催化剂以多孔氮化碳为载体,以金属化合物为助催化剂。
[0005]
本发明的目的可以通过以下技术方案实现:
[0006]
一种界面优化的mox/g-c3n4复合光催化剂,该复合催化剂以活性组分多孔氮化碳为载体,以金属化合物为助催化剂,以载体质量为基准,助催化剂的质量百分含量为1%~20%。
[0007]
一种上述的复合光催化剂的制备方法,该方法步骤如下:
[0008]
(1)催化剂载体的制备:
[0009]
氮化碳前驱物与模板剂研磨混合均匀;混匀后煅烧形成氮化碳-模板剂混合物;采用酸洗的方式去除混合物中的模板剂并干燥获得多孔氮化碳;
[0010]
(2)金属化合物的负载
[0011]
步骤(1)所得多孔氮化碳与助催化剂前驱物分散在水中,室温下搅拌8~24h,然后60~90℃搅拌干燥;
[0012]
(3)催化剂的煅烧
[0013]
将步骤(2)干燥后的物质在如下条件下煅烧:在空气氛下,以3~5℃/min的升温速率由室温升温至300~400℃,焙烧2~4h后自然冷却至室温,得到目标产物。
[0014]
上述制备方法中:步骤(1)中制备催化剂的前驱物为氰胺类化合物或富氮类物质。
[0015]
上述制备方法中:氮化碳前驱物与模板剂的质量比为1:1。
[0016]
上述制备方法中:所述的氰胺类化合物为氰胺、双氰胺或三聚氰胺,所述的富氮含碳物质为尿素或硫脲。
[0017]
上述制备方法中:金属化合物为ceo2、fe2o3和al2o3中的至少一种。作为优选:金属化合物为ceo2、fe2o3或al2o3。
[0018]
本发明技术方案中:所述的mo
x
/g-c3n4复合光催化剂在水污染治理领域的应用。
[0019]
本发明技术方案中:所述的模板剂为氧化镁。
[0020]
本发明的有益效果:
[0021]
相比传统的复合的催化剂,界面优化的复合催化剂mo
x
/g-c3n4,其可见光条件下rhb的降解效率提高20%。
附图说明
[0022]
图1为实施例1以及对比例1~2制备得到的催化剂氮气吸脱附等温线。
[0023]
图2为实施例1和对比例2制备得到的催化剂瞬态荧光图谱。
[0024]
图3为实施例1以及对比例1~2制备得到的催化剂可见光催化降解罗丹明b。
具体实施方式
[0025]
下面结合实施例对本发明做进一步说明,但本发明的保护范围不限于此:
[0026]
(1)多孔载体催化剂的制备
[0027]
首先,三聚氰胺与氧化镁纳米颗粒按质量比例1:1研磨混合均匀;然后,煅烧形成氮化碳-氧化镁混合物;最后,稀盐酸溶液去除氧化镁模板,并离心洗涤至中性,干燥后获得多孔氮化碳。
[0028]
(2)金属化合物的负载
[0029]
步骤(1)所得1g多孔氮化碳与0.126g ce(no3)3·
6h2o分散在水中,室温下搅拌8h,然后60℃搅拌干燥。
[0030]
(3)复合催化剂的煅烧
[0031]
将步骤(2)干燥后的物质在如下条件下煅烧:在空气氛下,以3℃/min的升温速率由室温升温至300℃;恒温2h后自然冷却至室温,得到目标产物,标记为cn-1。
[0032]
(4)光催化污染物降解
[0033]
如图1~3,80mg催化剂cn-1分散在80ml 10mg/l的罗丹明b溶液中,可见光照射2h后罗丹明b的降解率为85%。
[0034]
实施例2
[0035]
(1)催化剂载体的制备
[0036]
首先,双氰胺与氧化镁纳米颗粒按质量比例1:1研磨混合均匀;然后,煅烧形成氮化碳-氧化镁混合物;最后,稀盐酸溶液去除氧化镁模板,并离心洗涤至中性,干燥后获得多孔氮化碳。
[0037]
(2)金属化合物的负载
[0038]
步骤(1)所得1g多孔氮化碳与0.183g zn(no3)2·
6h2o分散在水中,室温下搅拌24h,然后80℃搅拌干燥。
[0039]
(3)催化剂的煅烧
[0040]
将步骤(2)干燥后的物质在如下条件下煅烧:在空气氛下,以5℃/min的升温速率由室温升温至400℃;恒温后2h自然降温至室温,得到目标产物,标记为cn-2。
[0041]
(4)光催化污染物降解
[0042]
80mg催化剂cn-2分散在80ml 10mg/l的罗丹明b溶液中,可见光照射2h后罗丹明b的降解率为95%。
[0043]
实施例3
[0044]
(1)催化剂载体的制备
[0045]
首先,三聚氰胺与氧化镁纳米颗粒按质量比例1:1研磨混合均匀;然后,煅烧形成氮化碳-氧化镁混合物;最后,稀盐酸溶液去除氧化镁模板,并离心洗涤至中性,干燥后获得多孔氮化碳。
[0046]
(2)金属化合物的负载
[0047]
步骤(1)所得1g多孔氮化碳与0.195g ni(no3)2·
6h2o分散在水中,室温下搅拌8h,然后80℃搅拌干燥。
[0048]
(3)催化剂的煅烧
[0049]
将步骤(2)干燥后的物质在如下条件下煅烧:在空气氛下,以4℃/min的升温速率由室温升温至350℃;恒温4h后自然降温至室温,得到目标产物,标记为cn-3。
[0050]
(4)光催化污染物降解
[0051]
80mg催化剂cn-3分散在80ml 10mg/l的罗丹明b溶液中,可见光照射2h后罗丹明b的降解率为80%。
[0052]
对比例1
[0053]
(1)催化剂的制备
[0054]
首先,三聚氰胺与氧化镁纳米粒子按质量比例1:1研磨混合均匀;然后,煅烧形成氮化碳-氧化镁混合物;最后,稀盐酸溶液去除氧化镁模板,并离心洗涤至中性,干燥后获得多孔氮化碳,标记为cn-4。
[0055]
(2)光催化污染物降解
[0056]
80mg催化剂cn-4分散在80ml 10mg/l的罗丹明b溶液中,可见光照射2h后罗丹明b的降解率为40%。
[0057]
(3)对比效果:催化剂光生载流子复合率较高,催化活性较低。
[0058]
对比例2
[0059]
(1)催化剂载体的制备
[0060]
首先,三聚氰胺与氧化镁纳米粒子按质量比例1:1研磨混合均匀;然后,煅烧形成氮化碳-氧化镁混合物;最后,稀盐酸溶液去除氧化镁模板,并离心洗涤至中性,干燥后获得多孔氮化碳。
[0061]
(2)金属化合物的负载
[0062]
将0.126g ce(no3)3·
6h2o与1g多孔氮化碳按比例研磨混合。以3℃/min的升温速
率由室温升温至300℃,恒温2h后自然降温至室温,得到目标产物,标记为cn-5。
[0063]
(3)光催化污染物降解
[0064]
80mg催化剂cn-5分散在80ml 10mg/l的罗丹明b溶液中,可见光照射2h后罗丹明b的降解率为70%。
[0065]
(4)对比效果:与对比例1相比,ceo2促进了光生载流子的分离和迁移,催化活性显著提高;与实施例1相比,由于ceo2的团聚和结合疏松,催化活性略有下降。