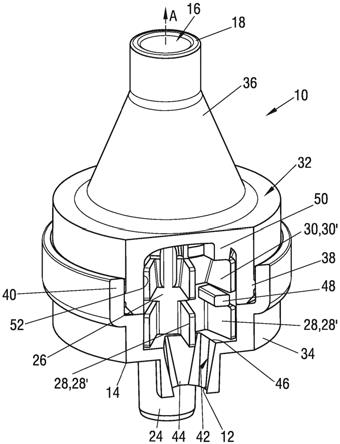
1.本发明涉及一种动态混合器,其具有布置在该动态混合器的入口侧处的两个或更多个入口以及布置在该动态混合器的出口侧处的出口,其中,该动态混合器的混合元件被构造成联接到驱动轴,以绕该混合元件的纵向轴线驱动该混合元件。本发明还涉及一种分配组件,其包括分配器、可选地填充有多组分材料、接收在该分配器中的筒和动态混合器,并且涉及一种使用动态混合器从筒分配多组分材料的方法。
背景技术:2.动态混合器或相应的它们也被称为的混合末端用于混合从多组分筒分配的多组分材料。此类混合器用于众多应用领域中,范围从工业应用,例如使用粘合剂将结构部件一个粘合到另一个,或作为建筑物或车辆的保护涂层,到医疗和牙科应用,例如制造牙科模具。
3.多组分材料例如为包括填充材料和硬化剂的双组分粘合剂。为了获得可能的最佳混合结果,例如具有期望的粘合强度的粘合剂,多组分材料必须被彻底混合。
4.为此目的,动态混合器被构造成重复地分开和重新组合多组分材料的部分流,以彻底混合多组分材料。
5.在混合多组分材料时,在分配过程之后留在动态混合器中的材料通常被丢弃,这是因为其保留在动态混合器中。根据应用领域,多组分材料可能相对昂贵,并且一次只可用于一个应用。例如在牙科领域中,特别是如此,其中,储存在筒中的多组分材料的一部分一次仅用于一个应用/患者,而剩余的多组分材料被储存在多组分筒中以备将来的应用。因此,在单次使用后过度使用动态混合器中剩余的大量多组分材料导致不必要的成本。
技术实现要素:6.为此原因,本发明的一个目的在于提供一种动态混合器,其中混合效率提高,而混合效率为低废料体积、低压力损失、低能耗和良好的混合质量之间的平衡。本发明的另一目的在于提供一种能够以尽可能容易的方式制造的动态混合器。
7.该目的通过具有权利要求1的特征的动态混合器来满足。
8.这样的动态混合器具有布置在所述动态混合器的入口侧处的两个或更多个入口和布置在所述动态混合器的出口侧处的出口,其中,所述动态混合器的混合元件被构造成经由联轴器联接到驱动轴,以绕所述混合元件的纵向轴线驱动所述混合元件,其中,所述动态混合器的混合元件包括转子体以及三排、四排或更多排转子叶片,所述转子叶片一排接一排地布置并且在所述转子体与容纳所述动态混合器的壳体之间从所述转子体远离所述纵向轴线径向突出,其中,所述转子体在尺寸上从所述入口朝向所述出口至少在所述转子体的长度的30%上减小,其中,与所述三排、四排或更多排转子叶片中的第三排转子叶片相比,所述三排、四排或更多排转子叶片中的第一排转子叶片沿所述混合元件的纵向轴线布置在不同的轴向位置处,其中,三排或更多排定子叶片设置有与所述三排、四排或更多排转
子叶片成交替布置结构布置的相应排的定子叶片,其中,每个所述入口由具有入口开口和混合器进入开口的通道形成,所述混合器进入开口特别是直接与第一排转子叶片相邻形成,其中,相应的入口开口被布置成平行于所述混合器进入开口并且平行于所述出口的出口开口,即所述入口开口和混合器进入开口相对于所述纵向轴线成90
°
的角度布置。
9.因此,该入口开口可以是通向动态混合器的开口,其距出口开口最远并且布置在形成通向动态混合器的入口的通道的端部处。
10.转子
‑
定子
‑
转子
‑
定子
‑
转子
‑
定子等的组合产生沿纵向轴线移动的旋转质量的打断。这导致剪切应力作用在可移动的转子叶片和固定的定子叶片之间的质量上。该剪切应力将间歇性停止引入到沿纵向轴线移动通过动态混合器的多组分材料流中,从而导致相应部分流的流速变化,从而产生改善的混合结果。
11.此外,该布置结构使得能够减小动态混合器中的压力损失,与改善的混合结果相结合,与现有技术的动态混合器相比,这显著提高了可实现的混合效率多达20%。
12.通过将转子体形成为使得其直径在其长度的至少一部分上减小,确保了不同材料的两个流动路径可在穿过动态混合器时逐渐结合。由此可实现改善的混合结果和减少的废料体积。
13.在这方面,应注意的是,此类动态混合器能够以注射模制工艺以及以3d打印工艺以容易且可重复的方式制造。
14.在这方面,应注意的是,在一些实施例中,入口开口可相对于纵向轴线以小于60
°
、优选地小于45
°
的角度相对于混合器进入开口倾斜布置,而混合器进入开口仍然相对于纵向轴线成90
°
的角度布置。
15.该三排、四排或更多排转子叶片中的至少一排可布置在转子体的尺寸减小的部分处。以此方式,待混合的材料流在被引导至出口时仍可旋转,使得多组分材料在穿过转子体的长度的同时连续地混合。
16.转子体可包括布置在混合元件的后端处的锥形部分,其中,第三排转子叶片可布置成从该锥形部分突出。这样的锥形外部形状使得能够为多组分材料形成特别短的流动路径。
17.转子体可包括处于其前端处的圆柱形部分,其中第一和第二排转子叶片从该圆柱形部分突出。已发现这样的圆柱形部分有益于使空的动态混合器内的空气体积最小化,并且因此,使动态混合器使用后残留在动态混合器中的废料量最小化。
18.可设置三排转子叶片,其中第一和第二排转子叶片包括相同数量的转子叶片,并且第三排转子叶片包括比第一和第二排转子叶片中的任一者要少的转子叶片。转子体的较细部分处的转子叶片数量的减少确保了多组分材料的流动路径尺寸的减小,从而导致动态混合器中存在较少的可留下废料的空气体积。
19.在这方面,应当注意的是,流动路径的尺寸减小,特别是在混合器入口区域和出口之间连续地减小。
20.第一和第二排转子叶片可各自包括介于10个和20个之间、优选为14个转子叶片,和/或其中,第三排转子叶片可包括介于5个和9个之间、优选为7个转子叶片。已发现这些数量的转子叶片产生特别有益的混合结果。
21.可设置与多排转子叶片排数一样多的定子叶片,其中交替布置结构开始于入口处
以第一排转子叶片开始,并且其中,最后一排定子叶片布置成比最后一排转子叶片更靠近出口。当转子叶片相对于入口旋转时,进入动态混合器的材料流可被第一排转子叶片连续切片,以便将旋转组分引入到不同组分的轴向流中。多组分材料的不同材料切片的这种组合的轴向和旋转流确保了改善的经混合。通过形成直接与入口相邻的转子叶片,混合元件的整个长度可用于混合过程。
22.在这方面,应注意的是,可将彼此直接相邻布置而其间具有间隙的两排定子叶片认为是单排定子叶片,前提是这两排定子叶片的高度小于相邻排的转子叶片的高度。
23.还应注意的是,可将彼此直接相邻布置而其间具有间隙的两排转子叶片认为是单排转子叶片,前提是这两个彼此直接相邻布置的转子叶片的高度不超过直接相邻的一排定子叶片的高度的400%。
24.可在每排定子叶片中布置介于三个和十个之间、优选为七个定子叶片。已发现该数量的定子叶片是有利的。定子叶片的数量通常被选择为在旋转的多组分材料上产生可能的最佳剪切力,以实现有益的混合结果,为此原因,定子叶片的数量可等于或小于转子叶片的数量。
25.该联轴器可形成在转子体处或转子体中。通过在转子体中或转子体处形成联轴器,联轴器可与之一体地产生,从而减少动态混合器的部件数量。
26.可设置四排转子叶片,其中,与其余排的转子叶片相比,每排转子叶片沿混合元件的纵向轴线布置在不同的轴向位置处。考虑到留在动态混合器中的废料的最小化,这是特别有益的设计。
27.四排转子叶片中的两排或三排可包括相同数量的转子叶片。这确保了多组分材料的彻底经混合(through mixing)。
28.沿纵向轴线处于直接相邻的转子叶片和定子叶片之间的轴向间隙可在0.01 mm至0.4 mm的范围内选择,并且优选地可选择为0.2 mm。壳体的内表面与转子叶片中的一个之间的径向间隙或相应的定子叶片中的一个与转子体之间的径向间隙可在0.01 mm至0.4 mm的范围内选择,并且优选地可选择为0.2 mm。已发现这些尺寸有利地将剪切应力引入到多组分材料流中。
29.入口的剖面尺寸可在入口开口和混合器进入开口之间增加,特别是连续增加。以此方式,可在相应的入口中实现多组分材料的特别好的流动,从而导致动态混合器内的压力损失减少。
30.每个入口可具有可在入口开口和混合器进入开口之间改变的剖面尺寸和/或形状,其中入口开口可选地具有圆形形状。通过改变入口的剖面尺寸和/或形状,混合器进入开口可形成为使得其具有的形状和尺寸理想地适于在两个直接相邻的转子叶片之间形成尽可能均匀的多组分材料切片,以获得尽可能好的混合结果,并减少动态混合器内的压力损失。
31.在一些实施例中,剖面尺寸的变化可以是尺寸的连续增大或减小,或者也可以是在通道的长度上尺寸的增大和减小之间的变化。
32.在一些实施例中,剖面形状的变化可以是从通道的圆形剖面到环段的剖面或者从圆形到多边形等的变化。
33.根据连接到动态混合器的入口的相对应的筒或类似物的出口尺寸以及壳体和布
置在动态混合器的壳体内的混合元件的实际尺寸来选择相应入口通道的尺寸和/或形状的变化。
34.第一排转子叶片中的两个直接相邻的转子叶片、转子体和壳体之间的区域可以是开放区域,并且其中,混合器进入开口具有混合器入口区域,其中混合器入口区域能够被选择为大于该开放区域。
35.该混合器入口区域可以是在直接与转子叶片相邻的通道端部处的入口通道的开口的区域。特别是在混合器入口区域的区域中,该开放区域可以是彼此相邻布置的两个转子叶片之间的区域。
36.通过将入口的通道的端部形成为使得其具有比第一排转子叶片中的直接相邻的转子叶片之间的空间更大的区域,使得引入到动态混合器中的材料流切片能够在直接相邻的转子叶片之间基本上具有一致的形状和尺寸,从而使得由于多组分材料的各个切片的尺寸均匀,可获得特别好的混合结果。每当第一排转子叶片中的一对转子叶片通过相应的混合器进入开口时,就获得切片。随着转子叶片进一步旋转,如果要用动态混合器混合双组分材料,则第一组分的切片随后与多组分材料的第二组分的切片接触,随着混合元件进一步旋转以混合相应的组分,该过程重复数次。
37.混合器入口区域可小于开放区域的两倍。如果混合器入口区域选择得过大,则动态混合器中可能会保留更多材料,这会增加动态混合器中存在的残余废料体积。
38.入口开口可具有小于混合器进入开口的混合器入口区域的入口区域。不同的筒具有不同的出口尺寸,并且为了获得尽可能好的混合结果,增加离开多组分筒的相应组分流的直径可能是有益的,使得可在混合器进入开口处提供理想量的多组分材料。此外,还可简化产生入口所需的工具作业,这是因为如果入口具有在入口的两端之间尺寸减小的形状,则可容易地例如从注射模具移除入口。
39.根据另一方面,本发明涉及一种分配组件,其包括分配器、可选地填充有多组分材料、接收在该分配器中的筒以及动态混合器,其中,该分配器包括驱动轴,该驱动轴可联接到动态混合器的混合元件,以在从所述筒分配所述多组分材料时,绕该混合元件的纵向轴线驱动该混合元件。
40.使用这样的分配组件,储存在动态混合器中的多组分材料可以特别有利的混合结果混合。
41.因此,多组分筒可填充有选自如下组的材料,该组的成员由局部药物、医用流体、伤口护理流体、化妆品和/或皮肤护理制剂、牙科流体、兽用流体、粘合流体、消毒流体、保护流体、油漆和上述各项的组合组成。
42.因此,此类流体以及因此分配组件可方便地用于治疗目标区域,例如鼻子(例如,抗组胺药膏等)、耳朵、牙齿(例如,用于植入物或口腔应用(例如,口疮(aphtas)、牙龈治疗、口腔溃疡等)的模具)、眼睛(例如,药物在眼睑上的精确沉积(例如,霰粒肿、感染、抗炎、抗生素等)、嘴唇(例如,疱疹)、口腔、皮肤(例如,抗真菌剂、黑斑、痤疮、疣、牛皮癣、皮肤癌治疗、纹身去除药物、伤口愈合、疤痕治疗、去污、止痒应用等)、其他皮肤病应用(例如,皮肤指甲(例如,抗真菌应用或强化配方等))或细胞学应用。
43.可替代地,所述流体以及因此所述分配组件也可用于工业部门,用于产品生产以及用于现有产品的修理和维护,例如用于建筑行业、汽车行业、航空航天行业中,用于能源
行业中,例如用于风力涡轮机等。例如,该分配组件可用于分配建筑材料、密封剂、粘合材料、粘合剂、油漆、涂层和/或保护涂层。
44.根据另一方面,本发明涉及一种使用动态混合器从筒分配多组分材料的方法,该方法包括以下步骤:在动态混合器的入口处提供多组分材料的相应组分;经由动态混合器的所述入口将所述多组分材料的所述相应组分作为材料流引导向动态混合器的混合元件;当所述材料流与动态混合器的定子叶片和转子叶片中的一者接触时,重复地打断所述材料流,以引起材料流相对于纵向轴线的旋转,以便混合所述多组分材料,其中材料流在其于入口和出口之间通过时被打断至少六次。
45.使用这样的方法,可实现经混合的多组分材料的特别好的混合结果。
附图说明
46.在下面对附图的描述中描述本发明的另外的实施例。在下文中将借助于实施例并参照附图来详细地解释本发明,在附图中示出:图1示出了第一类型的动态混合器的透视局部剖视图;图2示出了图1的动态混合器的顶视图;图3示出了图1的动态混合器的视图,其中壳体的一部分沿图2的剖面线a:a被移除;图4示出了沿图2的剖面线a:a截取的另一动态混合器的剖视图;图5示出了图4的动态混合器的示意性顶视图,其中壳体部分被移除;图6示出了另一类型的动态混合器的透视局部剖视图;图7示出了图6的动态混合器的顶视图;图8示出了图6的动态混合器的视图,其中壳体的一部分沿图7的剖面线a:a被移除;以及图9示出了分配组件的示意图。
47.在下文中,相同的附图标记将被用于具有相同或等同功能的部分。考虑部件的方向所作的任何陈述都是相对于附图中所示的位置作出的,并且在实际应用位置上自然可以变化。
具体实施方式
48.图1示出了第一类型的动态混合器10的透视局部剖视图。动态混合器10具有布置在动态混合器10的入口侧14处的两个入口12。该动态混合器具有布置在动态混合器10的出口侧18处的出口16。动态混合器10的混合元件20被布置在两个入口12和出口16之间。混合元件20被构造成经由联轴器24联接到驱动轴22(参见图9),以绕混合元件20的纵向轴线a驱动混合元件。联轴器24可形成在转子体26中或形成在转子体26处,例如形成在从转子体26延伸的轴内,其中该轴与转子体26一体地形成。
49.混合元件20包括布置在入口12和出口侧18之间的转子体26。在图1中可看到第一排和第二排转子叶片28、30,每一排包括多个转子叶片28'、30'。相应的转子叶片28'、30'从
转子体26远离纵向轴线a径向突出。第一排转子叶片28被布置成比第二排转子叶片30更靠近两个入口12。
50.动态混合器10还包括容纳混合元件20的壳体32。在图1中,壳体32由两部分形成,即基部部分34和顶部部分36。顶部部分36通过压配合被接收在该基部部分中。顶部部分36的鼻部38压靠基部部分34的套环40。在替代方式中,所述部分也可借助于焊接来连接。
51.动态混合器10的入口12与基部部分34一体地形成为单件。混合元件20相对于基部部分34轴颈支承(journaled),如例如关于图4所示。
52.如在图1中还可看到的,入口12各自包括在入口开口44和混合器进入开口46之间延伸的通道42,即入口开口44远离第一排转子叶片28布置。混合器进入开口46被布置成直接与第一排转子叶片28相邻。
53.每个入口12都具有在入口开口44和混合器进入开口46之间变化的剖面尺寸和形状。如图1中所示,入口开口44可形成为具有圆形形状。在这方面,应当注意,不同于圆形形状的其他形状也是可能的。每个入口12的剖面尺寸在入口开口44和混合器进入开口46之间增加。
54.第一和第二定子叶片48、50在壳体32的切除部分中也可见。第一定子叶片48被布置在第一和第二排转子叶片28、30之间。第一和第二定子叶片48、50被布置在壳体32的内表面52处。
55.图2示出了图1的动态混合器的顶视图。出口16具有圆形的出口开口54,使用动态混合器10的混合元件20混合的组分经由该出口开口54离开动态混合器10。
56.每个入口12的入口开口44平行于混合器进入开口46和出口16的出口开口54布置。
57.图3示出了沿图2的剖面线a:a截取的图1的动态混合器的剖视图。转子体26包括第三排转子叶片56,其沿混合元件20的纵向轴线a与第二排转子叶片30相邻布置。第三排转子叶片56被布置成比第一排转子叶片28更靠近出口16。
58.与第一排转子叶片28中的转子叶片28'相比,第三排转子叶片56中的转子叶片56'各自沿混合元件20的纵向轴线a具有不同的轴向位置和外部尺寸。
59.第三排转子叶片56中的转子叶片56'被布置在转子体26的锥形部分26'处。在所示示例中,转子体26的锥形部分26'相对于纵向轴线a的角度为25
°
。一般而言,锥形部分26'与纵向轴线a的角度可在10
°
至70
°
的范围内选择。转子体26的直径沿纵向轴线a在第一排转子叶片28和出口16之间减小。
60.第一排转子叶片28中的两个直接相邻的转子叶片28'、转子体26和壳体32之间的区域是混合入口端60处的开放区域58。混合器进入开口46被布置成直接与开放区域58相邻,并且因此直接与混合入口端60相邻。混合器进入开口46具有混合器入口区域46',其中该混合器入口区域大于开放区域58。更具体而言,混合器入口区域46'小于开放区域58的两倍。每个入口12的入口开口44具有入口区域44',该入口区域44'小于混合器进入开口46的混合器入口区域46'。
61.在这方面,应注意的是,如果混合器进入开口46的相应混合器入口区域46'具有的尺寸对应于入口开口44中的一个的相应入口区域44'的面积的1.4至1.6倍,优选为1.5倍或至少基本上1.5倍,则是优选的。
62.在这方面,还应注意的是,如果出口开口54的面积在每个入口12的每个入口开口
44的入口区域44'的和的0.5倍至1.5倍的范围内选择,则是优选的。
63.还应注意的是,混合器进入开口46的宽度在第一排转子叶片28中的第一叶片28'之间在相应转子叶片28'的径向最外部点处的间距的1.3至1.8倍的范围内选择,优选为1.5倍或至少基本上1.5倍。
64.相应地,混合器入口区域46'对应于开放区域58的1.4倍至1.6倍,优选为1.5倍或至少基本上1.5倍。
65.还应注意的是,取决于待混合的双组分材料的类型,两个混合器入口区域46'中的一个的区域或相应的两个入口12的入口开口44中的一个的入口区域44'在尺寸上可小于相对应的入口中的另一个,以允许动态混合器适应高粘度和低粘度的液体。
66.在顶视图中(在这方面也请参见图5),混合器进入开口46具有类似于垂直于纵向轴线a的环形部段62的形状。环形部段62具有内部和外部弯曲侧表面64、64'和平面侧表面66、66'。
67.一排定子叶片48'被布置在第一和第二排转子叶片28、30之间,第二排定子叶片50'被布置在第二和第三排转子叶片30、56之间,并且第三排定子叶片68被布置在第三排转子叶片56和出口16之间。
68.第一排转子叶片28包括比第三排转子叶片56更多的转子叶片28'。优选的是,如果在第三排转子叶片56中设置较少的转子叶片56',特别是转子叶片56'的数量为设置在第一排转子叶片28中的转子叶片28'的数量的一半。还如图3和图5中所示,在第二排转子叶片30中设置的转子叶片30'的数量与在第一排转子叶片28中设置的一样多。
69.第一和第二排转子叶片28、30包括转子叶片28'、30',它们具有相似的形状、特别是矩形形状和相似的尺寸,即平行于纵向轴线a测量的6 mm的高度。在这方面,应当注意的是,转子叶片28'的高度应当为至少5 mm,并且优选地在5 mm至10 mm的范围内选择。
70.第一排定子叶片48'中的定子叶片48的高度小于转子叶片28'、30'的高度并且尤其是小于转子叶片28'、30'的高度的一半,并且通常在转子叶片28'、30'的高度的20%至50%的范围内选择。
71.第三排转子叶片56中的转子叶片56'的高度大于第一或第二排转子叶片28、30中的转子叶片28'、30'的高度。优选地,转子叶片56'的高度在8 mm至20 mm的范围内选择,尤其是在10 mm至12 mm的范围内选择。
72.第三排转子叶片56中的转子叶片56'具有楔形设计。第三排转子叶片56中的转子叶片56'的设计可脱离如例如结合图8所示的楔形设计。
73.在这方面应注意的是,沿纵向轴线a处于直接相邻的转子叶片28'、30'、56'和定子叶片48、50、68'之间的轴向间隙一般在0.01 mm至0.4 mm的范围内选择,并且优选地选择为0.2 mm,如图3、图4和图8中所示。
74.还应注意的是,壳体32的内表面52与转子叶片28'、30'、56'中的一个之间的径向间隙或相应的在定子叶片48、50、68'中的一个与转子体26之间的径向间隙在0.01 mm至0.4 mm的范围内选择,并且优选地选择为0.2 mm,如图3、图4和图8中所示。
75.在这方面,应注意的是,每个转子叶片28'、30'、50'都可具有楔形的外轮廓,其中随着楔形体远离纵向轴线a延伸,该楔形体变得较小。
76.类似地,在转子体26和壳体32之间径向突出的定子叶片48'、50'、68'也具有楔状
外形,其中随着楔形体远离纵向轴线a延伸,该楔形体变得较小。
77.与第二排定子叶片50'相比,第一排定子叶片48'也可能具有更小的外周界。
78.直接邻接锥形部分26',转子体26还在其前端70处具有圆柱形部分26'',其中第一和第二排转子叶片28、30从该圆柱形部分26''突出。
79.通道74在锥形部分26'和圆柱形部分26''之间在第二排转子叶片30中的两个直接相邻的转子叶片30'和第三排转子叶片56中的两个直接相邻的转子叶片56'之间延伸。
80.相应通道74的基部74'平行于纵向轴线a延伸,并且如在图5中可以看到的,通道74具有平行于纵向轴线a的矩形剖面。设置通道74以便确保动态混合器10的可靠组装。
81.图4示出了类似于图3的视图的另一动态混合器10的剖视图。与图3中所示的动态混合器10对比,转子体26的锥形部分26'相对于纵向轴线a的角度为45
°
。
82.与图1至图3中所示的动态混合器10的转子体26一样,图4的转子体26在混合器进入开口46的区域中具有前端70,并且在出口16的区域中具有后端72。转子体26在后端72处具有外部锥形部分26',其中第三排转子叶片56从外部锥形部分26'突出。
83.图3和图5中所示的动态混合器10各自包括三排转子叶片28、30、56,其中第一和第二排转子叶片28、30包括相同数量的转子叶片28'、30',并且第三排转子叶片56包括比第一和第二排转子叶片28、30中的任一者要少的转子叶片56'。
84.在这方面,应当注意的是,一般而言,第一和第二排转子叶片28、30可各自包括介于10个和20个之间、优选地介于12个和16个之间、尤其是14个转子叶片28'、30',并且第三排转子叶片56可包括介于5个和9个之间、优选地介于6个和8个之间并且尤其是7个转子叶片56'。
85.转子体26通过相应地接合转子体26中存在的环形槽80、82的两个环形突出部76、78而轴颈支承在壳体32的基部部分34处。第一环形突出部76在形状上为大致矩形的,并且突出到第一环形槽80中。第二环形突出部78朝向纵向轴线a渐缩,并且由此接合第二环形槽80的侧壁。以此方式,在转子体26和壳体32的基部部分34之间形成密封,以避免多组分材料在联轴器24的区域中离开动态混合器10。
86.图5示出了图4的动态混合器的示意性顶视图,其中壳体32的顶部部分36被移除。如可以清楚地看到的,每个混合器进入开口46都具有类似于垂直于纵向轴线a的环形部段62的形状。此外,混合器进入开口46的面积大于第一排转子叶片28中的直接相邻的转子叶片28'、转子体26和壳体32之间的开放区域58。
87.图6示出了另一类型的动态混合器10的透视局部剖视图。该设计与图1至图5中所示的设计不同。差异是由于将在下文中讨论的混合元件20的不同设计以及由于壳体32的设计差异。
88.壳体32是包括顶部部分36和基部部分34的两部分式壳体。顶部部分36的套环36'接合在基部部分34的环形突出部34''上并且接合基部部分34的鼻部34',以在壳体32的顶部和底部部分36、34之间形成密封。
89.此外,壳体32还包括翼84。设置翼84以从外部加强壳体32,以便维持壳体32的顶部和底部部分36、34之间的密封。
90.图7示出了图6的动态混合器的顶视图。可以看到设置了六个翼84。图1至图5的设计未示出翼84,然而应注意的是,图1至图5的设计也可具有设置在壳体32的顶部部分36的
外侧上的翼84。一般而言,可设置介于3个和10个之间的此类翼84。
91.图8示出了沿图7的剖面线a:a截取的图6的动态混合器的剖视图。混合元件20包括四排转子叶片28、30、56、86,其一排接一排地布置并且在转子体26和容纳动态混合器10的混合元件20的壳体32之间远离纵向轴线a从转子体26径向突出。
92.在这四排转子叶片28、30、56、86中的每一排的转子叶片28'、30'、56'、86'中的每一个的位置处,转子体26在尺寸上从入口12朝向出口16减小。因此,每排转子叶片28、30、56、86沿混合元件20的纵向轴线a布置在不同的轴向位置处。四排定子叶片48'、50'、68、88被布置在壳体32的内表面52处。这四排定子叶片48'、50'、68、88与所述四排转子叶片28、30、56、86成交替布置结构布置。开始于混合器进入开口46处的该交替布置结构是第一排转子叶片28,接着是第一排定子叶片48',接着是第二排转子叶片30,接着是第二排定子叶片50',接着是第三排转子叶片56,接着是第三排定子叶片68,接着是第四排转子叶片86,接着是第四排定子叶片88。
93.在这方面应注意的是,第四排转子叶片86包括比第一、第二或第三排转子叶片28、30、56中的任一者要少的转子叶片86'。可能的情况是设置的转子叶片86'的数量是第一、第二或第三排转子叶片28、30、56中的一半。
94.转子体26的外径的尺寸在这四排转子叶片28、30、56、86中的每一排之间减小,使得转子体26的尺寸在入口12和出口16之间减小。
95.这四排转子叶片28、30、56、86中的每一排的转子叶片28'、30'、56'、86'中的每一个都包括平行于纵向轴线a延伸的竖直壁90和与竖直壁90倾斜延伸的顶壁92。顶壁92和竖直壁90之间的倾斜角通常可在10
°
至80
°
的范围内选择,并且在图8中所示的示例中为30
°
。
96.这四排定子叶片48'、50'、68、88中的每个定子叶片48、50、68'、88'都具有平行于顶壁92延伸的底壁94和平行于纵向轴线a延伸的侧壁96。底壁94和侧壁96之间的倾斜角通常可在100
°
至170
°
的范围内选择,并且在图8中所示的示例中为120
°
。
97.因此,相应的轴向间隙在侧壁96和竖直壁90之间延伸。因此,相应的径向间隙在顶壁92和底壁94之间延伸。
98.每个入口12都由通道42形成。相应的入口开口44和混合器进入开口46被布置成彼此平行并且与出口16的出口开口54平行。
99.在所示的动态混合器10的所有设计中,应当注意的是,可在每排定子叶片48'、50'、68、88中布置介于三个和十个之间、优选为七个定子叶片48、50、68'、88'。
100.还应注意的是,与转子叶片28'、30'、56'、86'相比,设置较少的定子叶片48、50、68'、88'。
101.图9示出了分配组件98的示意图。该分配组件包括分配器100、填充有多组分材料m、m'、接收在分配器100中的筒102和动态混合器10。分配器100包括驱动轴22,其可被联接到动态混合器10的混合元件20的联轴器24,以在从所述筒分配所述多组分材料m、m'时,绕混合元件20的纵向轴线a驱动混合元件20。分配器100还包括驱动驱动轴22的马达104和构造成接收多组分筒102的容器106。
102.在从该筒分配多组分材料m、m'时,两个活塞(未示出)通过分配组件98的两个柱塞(也未示出)在该筒内朝向动态混合器10移动。以此方式,使得多组分材料m、m'的相应组分可在动态混合器10的两个入口12中的一个处获得。所述多组分材料m、m'的相应组分作为材
料流(未示出)经由动态混合器10的所述入口12被引导向动态混合器10的混合元件20。
103.在材料流被引导通过动态混合器10的同时,混合元件20旋转,以使多组分材料m、m'的相应组分的材料流的切片(slice)不仅沿出口16的方向而且还沿径向方向不断地移动,使得多组分材料m、m'的组分的不同切片彼此接触并由此在离开出口16之前被混合。当所述材料流与动态混合器10的定子叶片48、50和转子叶片28'、30'、56'中的一者接触时,材料流被反复打断,以引起材料流相对于纵向轴线a的旋转,以便混合多组分材料m、m',其中材料流在其于入口12和出口16之间通过时被打断六次、八次或更多次。
104.在所述相应组分被引导通过所述入口时,材料流的直径沿朝向动态混合器10的所述混合元件20的方向在入口12和混合元件20之间扩展,以降低多组分材料m、m'的流速,以便改善混合质量。
105.如果在不同排的转子叶片30、56之间设置通道74,则这些可进一步改善经混合的多组分材料m、m'的混合结果,这是因为材料流可在另外的专用位置处被打断,从而引入另外的涡流以引起多组分材料m、m'的流动的瞬时停止,这确保了多组分材料m、m'的经混合得到改善。
106.前面教导的动态混合器10例如可在注射模制工艺中或使用3d打印机由塑料材料形成。这意味着壳体32和混合元件20各自由塑料材料形成。
107.混合元件20的材料可选择为比壳体32的材料要硬。在这方面,应当注意的是,壳体的基部部分34和顶部部分36可由相同的材料或不同的材料形成。
108.混合元件20的材料以及因此混合元件20的转子叶片28'、30'、56'、86'的材料和/或壳体32的材料以及因此定子叶片48、50、68'、88'的材料可被选择为具有在50至90的范围内的肖氏d硬度,这些部件的优选材料为聚丙烯(pp)和聚甲醛(pom),并且因此,肖氏d硬度的优选范围在60至88的范围内选择。
109.附图标记列表:10 动态混合器12 入口14 入口侧16 出口18 出口侧20 混合元件22 驱动轴24 联轴器26、26' 转子体、转子体26的锥形部分26'' 转子体26的圆柱形部分28、28' 第一排转子叶片、转子叶片30、30' 第二排转子叶片、转子叶片32 壳体34、34'、34'' 基部部分、基部部分34的鼻部、环形突出部36、36' 顶部部分、顶部部分36的套环38 鼻部
40 套环42 通道44、44' 入口开口、入口区域46、46' 混合器进入开口、混合器入口区域48、48' 第一定子叶片、第一排定子叶片50、50' 第二定子叶片、第二排定子叶片52 壳体的内表面54 出口开口56、56' 第三排转子叶片、转子叶片58 开放区域60 混合入口端62 环形部段6264、64' 内部弯曲侧表面、外部弯曲侧表面66、66' 平面侧表面、平面侧表面68、68' 第三排定子叶片、定子叶片70 26的前端72 26的后端74、74' 通道、基部76 第一环形突出部78 第二环形突出部80 第一环形槽82 第二环形槽84 翼86、86' 第四排转子叶片、转子叶片88、88' 第四排定子叶片、定子叶片90 竖直壁92 顶壁94 底壁96 侧壁98 分配组件100 分配器102 筒104 马达106 容器a 纵向轴线m、m' 多组分材料的组分、多组分材料的组分。