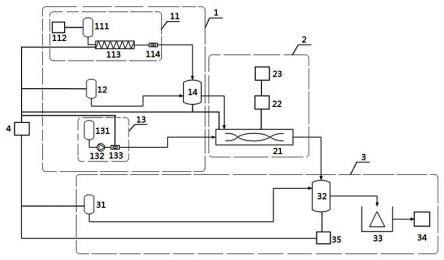
1.本发明涉及化工技术领域,具体而言,涉及一种2-甲基-5-硝基咪唑的连续化生产系统及方法。
背景技术:2.2-甲基-5-硝基咪唑,分子式c4h5n3o2。它是白色或浅黄色结晶性粉末,熔点252~254℃,难溶于水,略溶于甲醇、乙醇,易溶于强酸强碱中。2-甲基-5-硝基咪唑可用于有机合成甲硝唑、迪美唑等药物中间体。2-甲基-5-硝基咪唑用途广泛,其合成方法已被广泛研究,工业上大多采用2-甲基咪唑作为原料,在硫酸介质中,于高温条件下滴加硝酸进行硝化反应而得。现有技术中,工业化生产2-甲基-5-硝基咪唑多采用间歇操作方式,劳动强度大,生产效率低。此外,2-甲基咪唑的硝化反应过程比较独特,除非在极其苛刻的条件下,否则很难进行硝化反应,即必须使用过量的硝酸和硫酸,并在高温条件下才能进行反应。然而,在如此苛刻的条件下,硝化反应会放出大量的热。由于这些原因,现有的间歇放大生产还具有极大的潜在安全风险。中国专利cn 113788794 a,申请号202111221448.2,公布日2021.12.14,公开了一种2-甲基-5-硝基咪唑的连续硝化工艺,采用微通道反应装置进行2-甲基-5-硝基咪唑制备,会由于硝化反应大量放气导致装置内部空间利用率较低,大量的反应产气会对微通道反应器的反应收率造成非常严重的不利影响,导致2-甲基-5-硝基咪唑收率较低,无法满足工业要求,且其使用醋酐作为催化剂,会导致实际工业生产的成本大幅提升。
技术实现要素:3.本发明的主要目的在于提供一种2-甲基-5-硝基咪唑的连续化生产系统及方法,以解决现有技术中2-甲基-5-硝基咪唑制备成本高、产物收率低、工艺条件不易控制和安全风险大的问题。
4.为了实现上述目的,根据本发明的一个方面,提供了一种2-甲基-5-硝基咪唑的连续化生产系统,包括:原料预处理单元,包括2-甲基咪唑连续进料模块、硫酸连续进料模块、硝酸连续进料模块和连续配料模块,2-甲基咪唑连续进料模块和硫酸连续进料模块的出口分别与连续配料模块的进口相连,原料预处理单元用于将2-甲基咪唑和硫酸在100~140℃进行预先混合,以得到原料混合液;连续硝化单元,包括混合-反应模块和排气模块,混合-反应模块具有反应原料进口、气体出口和液体出口,反应原料进口分别与硝酸连续进料模块的出口、连续配料模块的出口相连,气体出口与排气模块的进口相连;连续硝化单元用于将原料混合液与硝酸混合并在130~170℃进行硝化反应,以得到硝化反应完成液。
5.以及连续后处理单元,包括顺次连接的碱液供应模块、连续淬灭-ph调节模块、连续固液分离模块和干燥模块,连续淬灭-ph调节模块的进口与混合-反应模块的液体出口相连;连续后处理单元用于将硝化反应完成液依次进行淬灭、ph调节得到混合产料,然后对混
合产料依次进行固液分离、干燥,以得到2-甲基-5-硝基咪唑;控制单元,分别与2-甲基咪唑连续进料模块、硫酸连续进料模块、硝酸连续进料模块、碱液供应模块电连接,用于控制各模块的进料速度;且控制单元还分别与连续配料模块、混合-反应模块电连接,用于控制配料温度和硝化反应温度。
6.进一步地,2-甲基咪唑连续进料模块包括原料储存装置、原料物位监测装置、原料进料装置、原料进料计量装置,其中,原料物位监测装置与原料储存装置电连接,用于监测原料储存装置中的原料物位;原料进料装置的进口与原料储存装置的出口相连,出口与连续配料模块的进口相连,用于2-甲基咪唑的连续进料;原料进料计量装置与原料进料装置电连接,用于向控制单元反馈2-甲基咪唑的进料量以调节2-甲基咪唑的进料速度。
7.进一步地,硝酸连续进料模块包括硝酸储存装置、硝酸进料装置、硝酸进料计量装置,其中,硝酸进料装置的进口与硝酸储存装置的出口相连,出口与混合-反应模块的进口相连,用于硝酸的连续进料;硝酸进料计量装置与硝酸进料装置电连接,用于向控制单元反馈硝酸的进料量以调节硝酸的进料速度。
8.进一步地,连续硝化单元还包括碱吸收模块,其进口与排气模块的出口相连,用于处理硝化反应产生的气体。
9.进一步地,连续后处理单元还包括ph监测模块,分别与连续淬灭-ph调节模块、控制单元电连接,用于监测混合产料的ph,并反馈给控制单元,以控制碱液供应模块的进料速度,以控制混合产料的ph为3~6。
10.根据本发明的另一方面,提供了一种2-甲基-5-硝基咪唑的连续化生产方法,使用本发明的2-甲基-5-硝基咪唑的连续化生产系统,方法包括:步骤s1,在原料预处理单元中,将2-甲基咪唑和硫酸分别通过2-甲基咪唑连续进料模块、硫酸连续进料模块送入连续配料模块在100~140℃进行预先混合,以得到原料混合液,通过硝酸连续进料模块提供硝酸;步骤s2,在连续硝化单元中,将原料混合液与硝酸在混合-反应模块中混合,在130~170℃进行硝化反应,以得到硝化反应完成液,产气进入排气模块;步骤s3,在连续后处理单元中,将硝化反应完成液依次通过连续淬灭-ph调节模块、连续固液分离模块和干燥模块,进行淬灭,并使用碱液供应模块提供的碱液调节ph,得到混合产料并进行固液分离,得到2-甲基-5-硝基咪唑粗品并进行干燥,得到2-甲基-5-硝基咪唑;其中,使用控制单元控制2-甲基咪唑、硫酸、硝酸和碱液的进料速度,以及配料温度和硝化反应温度。
11.进一步地,步骤s1中,原料混合液在连续配料模块中的停留时间为30~80min。
12.进一步地,步骤s2中,硝化反应过程中2-甲基咪唑、硫酸、硝酸的质量比为1: (1.5~2.5):(1~1.5);和/或硝化反应的温度为140~160℃,反应时间为30~150min。
13.进一步地,步骤s3中,连续淬灭-ph调节模块的温度<65℃,保留时间为10~30min。
14.进一步地,步骤s1中,原料混合液在连续配料模块中的停留时间为40~60min;和/或步骤s2中,硝化反应的反应时间为80~120min;和/或步骤s3中,连续淬灭-ph调节模块的保留时间为15~20min。
15.本发明采用上述2-甲基-5-硝基咪唑的连续化生产系统能够实现2-甲基-5-硝基咪唑连续制备和连续后处理,该系统可以实现自动化控制,节省人工,降低生产成本,提高生产效率,而且便于精确控制工艺条件。而且,上述连续化合成系统的硝化设备换热比表面积大,换热能力强,有利于反应温度的控制,排气模块的设置可以将硝化反应产生的no2等
气体及时排出,一方面可以提高硝化设备空间利用率,另一方面,在本发明较高的硝化温度下产生的水蒸气副产物能够一并排出,从而能够加快硝化反应转化率,增加2-甲基-5-硝基咪唑的收率。同时,反应产生的溶液体系可在线实时淬灭,避免了大量高反应活性的物料长时间储存带来的危险,提高整个工艺系统的安全性。
附图说明
16.构成本技术的一部分的说明书附图用来提供对本发明的进一步理解,本发明的示意性实施例及其说明用于解释本发明,并不构成对本发明的不当限定。在附图中:图1示出了根据本发明的一种实施例的2-甲基-5-硝基咪唑的连续化生产系统示意图。
17.其中,上述附图包括以下附图标记:1、原料预处理单元;11、2-甲基咪唑连续进料模块;111、原料储存装置;112、原料物位监测装置;113、原料进料装置;114、原料进料计量装置;12、硫酸连续进料模块;13、硝酸连续进料模块;131、硝酸储存装置;132、硝酸进料装置;133、硝酸进料计量装置;14、连续配料模块;2、连续硝化单元;21、混合-反应模块;22、排气模块;23、碱吸收模块;3、连续后处理单元;31、碱液供应模块;32、连续淬灭-ph调节模块;33、连续固液分离模块;34、干燥模块;35、ph监测模块;4、控制单元。
具体实施方式
18.需要说明的是,在不冲突的情况下,本技术中的实施例及实施例中的特征可以相互组合。下面将参考附图并结合实施例来详细说明本发明。
19.需要说明的是,本发明的硫酸是指质量浓度98%的硫酸水溶液。
20.需要说明的是,本发明的硝酸是指质量浓度90~95%的硝酸水溶液。
21.正如本发明背景技术中所述,现有技术中存在2-甲基-5-硝基咪唑制备成本高、产物收率低、工艺条件不易控制和安全风险大的问题。为了解决上述问题,在本发明一种典型的实施方式中,如图1所示,提供了一种2-甲基-5-硝基咪唑的连续化生产系统,包括:原料预处理单元1、连续硝化单元2、连续后处理单元3以及控制单元4,其中,原料预处理单元1包括2-甲基咪唑连续进料模块11、硫酸连续进料模块12、硝酸连续进料模块13和连续配料模块14,2-甲基咪唑连续进料模块11和硫酸连续进料模块12的出口分别与连续配料模块14的进口相连,原料预处理单元1用于将2-甲基咪唑和硫酸在100~140℃进行预先混合,以得到原料混合液;连续硝化单元2包括混合-反应模块21和排气模块22,混合-反应模块21具有反应原料进口、气体出口和液体出口,反应原料进口分别与硝酸连续进料模块13的出口、连续配料模块14的出口相连,气体出口与排气模块22的进口相连;连续硝化单元2用于将原料混合液与硝酸混合并在130~170℃进行硝化反应,以得到硝化反应完成液。
22.连续后处理单元3包括顺次连接的碱液供应模块31、连续淬灭-ph调节模块32、连续固液分离模块33和干燥模块34,连续淬灭-ph调节模块32的进口与混合-反应模块21的液体出口相连;连续后处理单元3用于将硝化反应完成液依次进行淬灭、ph调节得到混合产料,然后对混合产料依次进行固液分离、干燥,以得2-甲基-5-硝基咪唑。
23.控制单元4分别与2-甲基咪唑连续进料模块11、硫酸连续进料模块12、硝酸连续进料模块13、碱液供应模块31电连接,用于控制各模块的进料速度;且控制单元4还分别与连续配料模块14、混合-反应模块21电连接,用于控制配料温度和硝化反应温度。
24.具体应用过程中,首先在原料预处理单元1中,将2-甲基咪唑和硫酸分别通过2-甲基咪唑连续进料模块11、硫酸连续进料模块12送入连续配料模块14在100~140℃进行预先混合,以得到原料混合液,并通过硝酸连续进料模块13提供硝酸;其中硫酸作为催化剂,可以降低成本,又因为使用了本发明的系统,保证了2-甲基-5-硝基咪唑仍具有较高的转化率和收率,此外较高的配料温度也更适合于为后续高温硝化反应做准备,能够提高硝化反应速率,从而提高生产效率。
25.在连续硝化单元2中,将原料混合液与硝酸在混合-反应模块21中混合,在130~170℃进行硝化反应,以得到硝化反应完成液,反应产生的no2和no等酸性气体进入排气模块22,其中混合-反应模块使用换热比表面积大的硝化反应装置即可,可以设置在壳体内,且沿壳体的长度方向延伸。2-甲基-5-硝基咪唑的硝化合成反应存在大量放气、反应放热集中且剧烈等特点,采用微通道反应装置会导致装置内部空间利用率较低,大量的反应产气量会对微通道反应器的反应收率造成非常严重的不利影响,微通道反应器的反应收率不高于70%;而本发明连续化合成系统的硝化设备换热比表面积大,换热能力强,有利于反应温度的控制,排气模块的设置可以将硝化反应产生的no2等气体及时排出,一方面可以提高硝化设备空间利用率,另一方面,在本发明较高的硝化温度下产生的水蒸气副产物能够一并排出,从而能够加快硝化反应转化率,增加2-甲基-5-硝基咪唑的收率,从而在不需要使用醋酐等昂贵催化剂的情况下,也可以得到比较好的产品收率和纯度。
26.在连续后处理单元3中,将硝化反应完成液依次通过连续淬灭-ph调节模块32、连续固液分离模块33和干燥模块34,进行淬灭,并使用碱液供应模块31提供的碱液调节ph,得到混合产料并进行固液分离,得到2-甲基-5-硝基咪唑粗品并进行干燥,得到2-甲基-5-硝基咪唑。反应过程中,控制单元4按照负反馈调节的控制逻辑控制各物料的进料速度,和反应温度。其中,碱液可以是氨水、naoh水溶液和na2co3水溶液的一种或多种。
27.典型的但非限定性的,原料预处理单元1中的配料温度可以为100℃、105℃、110℃、115℃、120℃、125℃、130℃、135℃、140℃或其任意两个数值组成的范围;硝化反应的温度可以为130℃、135℃、140℃、145℃、150℃、155℃、160℃、165℃、170℃或其任意两个数值组成的范围。
28.本发明采用上述2-甲基-5-硝基咪唑的连续化生产系统能够实现2-甲基-5-硝基咪唑连续制备和连续后处理,该系统可以实现自动化控制,节省人工,降低生产成本,提高生产效率,而且便于精确控制工艺条件,硝化反应收率高。同时,反应产生的溶液体系可在线实时淬灭,避免了大量高反应活性的物料长时间储存带来的危险,提高整个工艺系统的安全性。
29.在一种优选的实施方式中,2-甲基咪唑连续进料模块11包括原料储存装置111、原料物位监测装置112、原料进料装置113、原料进料计量装置114,其中,原料物位监测装置112与原料储存装置111电连接,用于监测原料储存装置111中的原料物位,保证固体物料进料的稳定性和准确性;原料进料装置113的进口与原料储存装置111的出口相连,出口与连续配料模块14的进口相连,用于2-甲基咪唑的连续进料,可以按照事先设定的进料量准确
进料;原料进料计量装置114与原料进料装置113电连接,用于向控制单元4反馈2-甲基咪唑的进料量以调节2-甲基咪唑的进料速度,控制单元4按照负反馈调节的控制逻辑发送调节流量的指令,以确保2-甲基咪唑进料量的准确性。
30.相应地,在一种优选的实施方式中,硝酸连续进料模块13包括硝酸储存装置131、硝酸进料装置132、硝酸进料计量装置133,其中,硝酸进料装置132的进口与硝酸储存装置131的出口相连,出口与混合-反应模块21的进口相连,用于硝酸的连续进料;硝酸进料计量装置133与硝酸进料装置132电连接,用于向控制单元4反馈硝酸的进料量以调节硝酸的进料速度,控制单元4按照负反馈调节的控制逻辑发送调节流量的指令,以确保硝酸进料量的准确性。
31.在一种优选的实施方式中,连续硝化单元2还包括碱吸收模块23,其进口与排气模块22的出口相连,用于处理硝化反应产生的no2和no等酸性气体,以进一步减少环境污染,改善劳动保护。
32.控制单元4将碱液按照指定的量输入连续淬灭-ph调节模块32,可以进一步提高连续化系统的自动化程度,在一种优选的实施方式中,连续后处理单元3还包括ph监测模块35,分别与连续淬灭-ph调节模块32、控制单元4电连接,用于监测混合产料的ph,并反馈给控制单元4,以控制碱液供应模块31的进料速度,以控制混合产料的ph为3~6,保持后处理系统稳定。
33.在本发明又一种典型的实施方式中,还提供了一种2-甲基-5-硝基咪唑的连续化生产方法,使用本发明的2-甲基-5-硝基咪唑的连续化生产系统,方法包括:步骤s1,在原料预处理单元1中,将2-甲基咪唑和硫酸分别通过2-甲基咪唑连续进料模块11、硫酸连续进料模块12送入连续配料模块14在100~140℃进行预先混合,以得到原料混合液,通过硝酸连续进料模块13提供硝酸;步骤s2,在连续硝化单元2中,将原料混合液与硝酸在混合-反应模块21中混合,在130~170℃进行硝化反应,以得到硝化反应完成液,产气进入排气模块22;步骤s3,在连续后处理单元3中,将硝化反应完成液依次通过连续淬灭-ph调节模块32、连续固液分离模块33和干燥模块34,进行淬灭,并使用碱液供应模块31提供的碱液调节ph,得到混合产料并进行固液分离,得到2-甲基-5-硝基咪唑粗品并进行干燥,得到2-甲基-5-硝基咪唑;其中,使用控制单元4控制2-甲基咪唑、硫酸、硝酸和碱液的进料速度,以及配料温度和硝化反应温度。
34.本发明先将2-甲基咪唑和硫酸在100~140℃进行预先混合,以得到原料混合液,随后将原料混合液与硝酸混合,在130~170℃进行硝化反应,以得到硝化反应完成液,最后将硝化反应完成液进行淬灭,并使用碱液调节ph,得到混合产料并进行固液分离,得到2-甲基-5-硝基咪唑粗品并进行干燥,得到2-甲基-5-硝基咪唑。该制备方法简单,使用的装置可以实现自动化控制,节省人工,降低生产成本,提高生产效率,工艺系统的安全性高,而且便于精确控制工艺条件,硝化反应转化率高,2-甲基-5-硝基咪唑的收率大。
35.为进一步提高2-甲基咪唑原料和硫酸催化剂的混合效果,在一种优选的实施方式中,步骤s1中,原料混合液在连续配料模块14中的停留时间为30~80min,优选为40~60min,以确保2-甲基咪唑原料和硫酸完全混合并升温到指定温度,准备进行硝化反应。
36.在一种优选的实施方式中,步骤s2中,硝化反应过程中2-甲基咪唑、硫酸、硝酸的质量比为1:(1.5~2.5):(1~1.5),其质量比包括但不限于上述范围,将其限定在上述范围时
可以得到更佳的反应转化率和产物收率,又不至于造成原料和催化剂的浪费。
37.出于进一步增加2-甲基-5-硝基咪唑的收率的目的,在一种优选的实施方式中,步骤s2中,硝化反应的温度为140~160℃,反应时间为30~150min,优选为80~120min,此温度下也更适合于使用本发明的2-甲基-5-硝基咪唑的连续化生产系统进行生产,副产水可以更及时地从硝化装置排出,同步提高反应转化率。
38.在一种优选的实施方式中,步骤s3中,连续淬灭-ph调节模块32的温度<65℃,保留时间为10~30min,优选为15~20min。上述条件下反应体系中大量高反应活性的物料的失活更加迅速和充分,可以进一步提高整个工艺系统的安全性。
39.以下结合具体实施例对本技术作进一步详细描述,这些实施例不能理解为限制本技术所要求保护的范围。
40.实施例12-甲基咪唑、硫酸、硝酸的质量比为1:2:1.4。
41.步骤s1,在原料预处理单元1中,原料储存装置111中的2-甲基咪唑通过原料进料装置113送入连续配料模块14,硫酸通过硫酸连续进料模块12送入连续配料模块14,按照质量比进行预先混合,配料温度为120℃,原料混合液的停留时间为50min,得到原料混合液,同时原料物位监测装置112监测原料物位,原料进料计量装置114记录进料量反馈给控制单元4;硝酸储存装置131中的硝酸通过硝酸进料装置132送入混合-反应模块21,同时硝酸进料计量装置133记录进料量反馈给控制单元4;步骤s2,在连续硝化单元2中,将原料混合液与硝酸在混合-反应模块21中混合,在150℃进行硝化反应100min,以得到硝化反应完成液,产气通过排气模块22进入碱吸收模块23进行吸收;步骤s3,在连续后处理单元3中,将硝化反应完成液依次通过连续淬灭-ph调节模块32、连续固液分离模块33和干燥模块34,进行水淬灭,并使用碱液供应模块31提供的碱液调节ph,使用ph监测模块35控制体系ph在3~6,温度不超过65℃,保留时间为15min,得到混合产料并转移至离心机中进行固液分离,得到2-甲基-5-硝基咪唑粗品并进行烘干,得到2-甲基-5-硝基咪唑纯度为99.3%,反应收率为84.9%。
42.实施例2实施例2与实施例1的区别在于:步骤s1中,连续配料模块14的配料温度为100℃,原料混合液的停留时间为30min;步骤s2中,硝化反应过程中2-甲基咪唑、硫酸、硝酸的质量比为1:1.5:1;硝化反应的温度为140℃,反应时间为30min;步骤s3中,连续淬灭-ph调节模块32的温度<65℃,保留时间为10min。得到2-甲基-5-硝基咪唑纯度为99.1%,反应收率为82.1%。
43.实施例3实施例3与实施例1的区别在于:步骤s1中,连续配料模块14的配料温度为140℃,原料混合液的停留时间为80min;步骤s2中,硝化反应过程中2-甲基咪唑、硫酸、硝酸的质量比为1:2.5:1.5;硝化反应的温度为160℃,反应时间为150min;步骤s3中,连续淬灭-ph调节模块32的温度<65℃,保留时间为30min。得到2-甲基-5-硝基咪唑纯度为99.1%,反应收率为82.4%。
44.实施例4
实施例4与实施例1的区别在于:步骤s1中,连续配料模块14的原料混合液的停留时间为40min;步骤s2中,硝化反应的反应时间为80min;步骤s3中,连续淬灭-ph调节模块32的温度<65℃,保留时间为15min。得到2-甲基-5-硝基咪唑纯度为99.1%以上,反应收率为83.1%。
45.实施例5实施例5与实施例1的区别在于:步骤s1中,连续配料模块14的原料混合液的停留时间为60min;步骤s2中,硝化反应的反应时间为120min;步骤s3中,连续淬灭-ph调节模块32的温度<65℃,保留时间为20min。得到2-甲基-5-硝基咪唑纯度为99.2%以上,反应收率为84%。
46.对比例1首先,在250ml四口瓶内加入15 g硫酸溶液,控制温度不超过130℃,开始投2-甲基咪唑,投料完毕后保温5 min。然后,开始滴加硝酸,滴加时温度保持在130~170℃,滴加完毕后保温反应150min。反应完毕后,将反应体系转入预先配制好的碱液中,后用碱液将体系ph调制3~6。待温度冷却至65℃以下后,采用离心分离将2-甲基-5-硝基咪唑从固液混合物中分离出来,湿产品干燥即可得到2-甲基-5-硝基咪唑。对比例1批次反应的产品纯度为99.1%,反应收率为81.2%。
47.对比例2向一个搅拌釜中投入900kg发烟硝酸,打开冷却水开关,缓慢投加330kg硫酸铵,配制过程控制温度不超过50℃,配制完成后,用常温水对物料降温至30℃。向另一个搅拌釜中投入2000kg98%浓硫酸,打开冷却水开关,缓慢投加1000kg 2-甲基咪唑,控制温度不超过100℃,投加2-甲基咪唑完成后,加入2000kg醋酐。搅拌均匀,降温至30℃。
48.开启温水循环对四段微管反应器进行预热50℃,预先开启终止反应注水泵设定流量12000g/min,稳定后;再开启第一个搅拌釜的稳流输送计量泵,设定流量为2070g/min,运行稳定后开启另一个搅拌釜的稳流输送计量泵,设定流量为8070g/min,在多段微管反应器中进行反应。
49.注水泵对反应完成液进行连续注水稀释至终止反应,终止反应后的混合合流入中和釜后进行中和,中和完成后进行放入离心机进行固液分离,分离后对固相进行水洗干燥得到成品,对比例2微管反应器的产品纯度大于98%,反应收率为70%。
50.由上可知,对比例1采用传统批次反应,不能连续化自动生产,劳动强度大,生产效率低,生产成本高,产物收率小于本发明各实施例的数据;对比例2采用微通道反应器系统,由于硝化反应存在大量放气、反应放热集中且剧烈等特点,导致装置内部空间利用率较低,大量的反应产气也对微通道反应器的反应收率造成非常严重的不利影响,反应收率比本发明各实施例的数据差很多。
51.本发明采用上述2-甲基-5-硝基咪唑的连续化生产系统能够实现2-甲基-5-硝基咪唑连续制备和连续后处理,该系统可以实现自动化控制,节省人工,降低生产成本,提高生产效率,而且便于精确控制工艺条件。而且,上述连续化合成系统的硝化设备换热比表面积大,换热能力强,有利于反应温度的控制,排气模块的设置可以将硝化反应产生的no2等气体及时排出,一方面可以提高硝化设备空间利用率,另一方面,在本发明较高的硝化温度下产生的水蒸气副产物能够一并排出,从而能够加快硝化反应转化率,增加2-甲基-5-硝基
咪唑的收率,从而在不需要使用醋酐等昂贵催化剂的情况下,也可以得到比较好的产品收率和纯度。同时,反应产生的溶液体系可在线实时淬灭,避免了大量高反应活性的物料长时间储存带来的危险,提高整个工艺系统的安全性。
52.以上所述仅为本发明的优选实施例而已,并不用于限制本发明,对于本领域的技术人员来说,本发明可以有各种更改和变化。凡在本发明的精神和原则之内,所作的任何修改、等同替换、改进等,均应包含在本发明的保护范围之内。