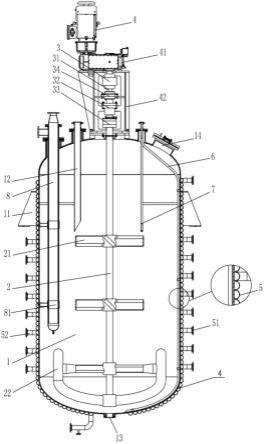
1.本实用新型涉及反应釜结构技术领域,尤其涉及一种甘氨酸合成反应釜。
背景技术:2.甘氨酸的生产过程中,反应釜是主要的生产设备。反应釜技术性能的优劣直接影响到甘氨酸的产量、质量及装置运行的经济性。目前,国内的甘氨酸合成反应釜大多单位体积小、耗能大、生产效率低、相对投资高、已呈淘汰趋势。随着国内外甘氨酸需求的快速增长,生产规模的不断扩大,市场竞争的迅速加剧,甘氨酸合成反应釜一方面向着大型化方向发展,另一方面需要不断运用新技术对现有装置进行改进和创新,以达到节约生产成本、降低劳动强度、提高设备产能、提升产品质量的目的。
3.国内现有的甘氨酸合成反应釜大多选用搪玻璃制造,并采用普通u形夹套进行传热和普通单层框式搅拌器进行搅拌。其存在的缺点主要有:
4.1、采用普通u形夹套进行传热,u形夹套内的压力导致必须增加反应釜内筒的壁厚,降低了传热系数,同时,u形夹套内冷却水的流速低,使反应釜的传热效率低,反应时间长,造成反应釜内各部分温差大,从而导致产品质量不均匀。
5.2、搅拌器为普通的单层框式搅拌器,搅拌强度弱,物料流动混合效率低,反应速度慢,每釜反应产物甘氨酸的收率较低。
6.3、采用搪玻璃制造甘氨酸合成反应釜,由于搪玻璃制造工艺的限制,反应釜大多单位体积小,无法进行大型化生产。
7.4、反应釜容积小,单台生产能力差,建设同样规模的生产装置需要的反应釜数量多,配套的仪表、阀门多,进而导致装置建设成本高,生产过程中的能耗高。
技术实现要素:8.本实用新型的目的是提供一种甘氨酸合成反应釜,该反应釜具有传热效率高、产品质量稳定的优点。
9.为实现上述目的,本实用新型提供一种甘氨酸合成反应釜,包括反应釜本体和竖直设置在其内部的搅拌轴,所述搅拌轴从上往下依次设有至少两个斜叶桨式搅拌器和一个框架式搅拌器,所述搅拌轴上端延伸至反应釜本体外并通过传动组件与驱动机构连接,所述搅拌轴四周的反应釜本体内壁上竖直设有多条内冷挡管,所述反应釜本体的顶部设有进料口和进气口,底部设有出料口,所述反应釜本体外侧壁上从上往下依次设有多组围绕其轴心设置的半管夹套。
10.作为本实用新型的更进一步改进,所述驱动机构包括通过机架安装在反应釜本体顶部的驱动电机、减速机,所述驱动电机的动力输出端与减速机的动力输入端传动连接,所述减速机的动力输出端通过传动组件与搅拌轴上端传动连接。
11.作为本实用新型的更进一步改进,位于所述传动组件与反应釜本体之间的搅拌轴上设有挂轴件,所述挂轴件与反应釜本体之间的搅拌轴上套接有环形接油件,所述环形接
油件与机架固定连接。
12.作为本实用新型的更进一步改进,所述机架上设有用于抽出环形接油件中的密封油的抽油管。
13.作为本实用新型的更进一步改进,所述传动组件通过轴向转动轴承安装到机架上。
14.作为本实用新型的更进一步改进,所述传动组件包括从上往下同轴依次连接的第一联轴器、传动轴、第二联轴器以及机械密封,所述第一联轴器与驱动机构的动力输出端传动连接,所述机械密封与搅拌轴上端传动连接。
15.作为本实用新型的更进一步改进,还包括竖直设置在反应釜本体内的用于安装温度计的温度计套管,所述进料口内设有竖直向下延伸且下端为斜切口的进料管,所述进气口内设有沿反应釜本体内壁向下延伸至其底部的进气管。
16.作为本实用新型的更进一步改进,所述反应釜本体外壁上设有耳式支座,所述反应釜本体顶部外壁上还设有带视镜的人孔。
17.作为本实用新型的更进一步改进,所述内冷挡管包括一竖直设置且上端延伸至反应釜本体外的内层输出管,所述内层输出管外套接有一上端延伸至反应釜本体外的外层输入管;所述外层输入管侧壁通过挡管安装架与反应釜本体内壁连接。
18.作为本实用新型的更进一步改进,所述半管夹套上设有冷却介质进管和冷却介质出管,所述冷却介质进管和冷却介质出管相对设置在反应釜本体两侧。
19.有益效果
20.与现有技术相比,本实用新型的一种甘氨酸合成反应釜的优点为:
21.1、该反应釜中,反应釜本体的顶部设有进料口和进气口,底部设有出料口。搅拌轴从上往下依次设有至少两个斜叶桨式搅拌器和一个框架式搅拌器,且搅拌轴上端延伸至反应釜本体外并通过传动组件与驱动机构连接。同时,搅拌轴四周的反应釜本体内壁上竖直设有多条内冷挡管,且反应釜本体外侧壁上从上往下依次设有多组围绕其轴心设置的半管夹套。
22.其中,搅拌轴上设计“斜叶桨式搅拌器+框式搅拌器”的组合,再加上内冷挡管构成搅拌体系,改善了搅拌强度剪切力和循环次数,避免了物料搅拌不均匀的问题,进一步提高了搅拌效果和传热效果,保证产品颗粒形态好、纯度高、分子量分布匀称。同时,设置在反应釜本体内部的内冷挡管,也进一步提升了换热效率,充分满足了反应时的换热要求,使反应温度控制在70℃左右,保证甘氨酸能达到预定的反应温度。另外,在反应釜本体外侧壁上设置采用采用全流通的半管夹套结构,还增加了反应釜本体内部和外部的换热能力,能更加精确的控制甘氨酸的反应温度。
23.采用该甘氨酸合成反应釜,能有效的提高反应釜的搅拌效果、传热能力和搅拌效率,从而极大的提高了甘氨酸的生产强度,为甘氨酸生产提供了理想装置。
24.2、位于传动组件与反应釜本体之间的搅拌轴上设有挂轴件。挂轴件与反应釜本体之间的搅拌轴上套接有环形接油件,环形接油件与机架固定连接。搅拌轴上设置挂轴件,能方便在不拆搅拌轴的情况下更换传动组件。同时,挂轴件下设置环形接油件,防止密封油进入反应釜本体内影响产品品质。
25.3、机架上设有用于抽出环形接油件中的密封油的抽油管。通过抽油管,能将环形
接油件中继续的密封油抽出,防止密封油进入反应釜本体内影响产品品质。
26.4、传动组件包括从上往下同轴依次连接的第一联轴器、传动轴、第二联轴器以及机械密封,第一联轴器与驱动机构的动力输出端传动连接,机械密封与搅拌轴上端传动连接。采用机械密封,配合环形接油件,既保证了反应釜本体密封的可靠性,又避免了产品因受到密封油污染而影响产品质量。
27.5、还包括竖直设置在反应釜本体内的用于安装温度计的温度计套管,能够实时检测反应釜本体内的温度,方便检测人员监测反应的正常运行,进而保证了产品质量。并且,进料口内设有竖直向下延伸且下端为斜切口的进料管,进料管末端斜切成尖状,能防止挂料。进气口内设有沿反应釜本体内壁向下延伸至其底部的进气管。进气管从反应釜本体的进气口进入,沿反应釜内壁往下伸到其底部,充分保证物料尽快混合均匀,有利于反应的快速进行,减少副产物的产生,提高了甘氨酸的收率。
28.6、反应釜本体顶部外壁上还设有带视镜的人孔,方便检测人员监测反应的正常运行和检修反应釜本体,进而保证了产品质量。
29.7、内冷挡管包括一竖直设置且上端延伸至反应釜本体外的内层输出管,内层输出管外套接有一上端延伸至反应釜本体外的外层输入管。外层输入管侧壁通过挡管安装架与反应釜本体内壁连接。通过内层输出管输出完成热传导的冷却介质,外层输入管输入冷却介质,完成反应物的换热过程。同时,内冷挡管改善了搅拌强度剪切力和循环次数,避免了物料搅拌不均匀的问题,进一步提高了搅拌效果和传热效果,保证产品颗粒形态好、纯度高、分子量分布匀称。
30.8、半管夹套上设有冷却介质进管和冷却介质出管,冷却介质进管和冷却介质出管相对设置在反应釜本体两侧。相对设置在反应釜本体两侧的冷却介质进管和冷却介质出管能使冷却介质完成至少半圈的环绕流动,从而带走热量,保证反应的顺利进行。
31.通过以下的描述并结合附图,本实用新型将变得更加清晰,这些附图用于解释本实用新型的实施例。
附图说明
32.为了更清楚地说明本实用新型实施例或现有技术中的技术方案,下面将对实施例或现有技术描述中所需要使用的附图作简单地介绍,显而易见地,下面描述中的附图仅仅是本实用新型的一些实施例,对于本领域普通技术人员来讲,在不付出创造性劳动的前提下,还可以根据这些附图获得其他的附图。
33.图1为本实用新型的结构示意图;
34.图2为本实用新型中内冷挡管的结构示意图;
35.图3为本实用新型中挂轴件和环形接油件的安装示意图。
36.其中:1-反应釜本体;11-上封头;12-下封头;13-筒体;14-耳式支座;15-进料管;16-出料口;17-人孔;2-搅拌轴;21-斜叶桨式搅拌器;22-框架式搅拌器;23-挂轴件;24-环形接油件;3-第一联轴器;31-传动轴;32-第二联轴器;33-机械密封;34-转动轴承;4-驱动电机;41-减速机;42-机架;5-半管夹套;51-冷却介质进管;52-冷却介质出管;6-进气管;7-温度计套管;71-温度计;8-内冷挡管;81-挡管安装架;82-内层输出管;83-外层输入管。
具体实施方式
37.为了使本实用新型的目的、技术方案及优点更加清楚明白,以下结合附图,对本实用新型进一步详细说明。显然,所描述的实施例仅仅是本实用新型一部分实施例,而不是全部的实施例。基于本实用新型中的实施例,本领域普通技术人员在没有做出创造性劳动前提下所获得的所有其他实施例,都属于本实用新型保护的范围。
38.现在参考附图描述本实用新型的实施例。
39.实施例
40.本实用新型的具体实施方式如图1-3所示,一种甘氨酸合成反应釜,包括反应釜本体1和竖直设置在其内部的搅拌轴2。搅拌轴2从上往下依次设有至少两个斜叶桨式搅拌器21和一个框架式搅拌器22,且搅拌轴2上端延伸至反应釜本体1外并通过传动组件与驱动机构连接。本实施例中,斜叶桨式搅拌器21为四叶式结构。搅拌轴2四周的反应釜本体1内壁上竖直设有多条内冷挡管8,且反应釜本体1外侧壁上从上往下依次设有3-8组围绕其轴心设置的半管夹套5。反应釜本体1的顶部设有进料口和进气口,底部设有出料口13。
41.其中,搅拌轴2上设计“斜叶桨式搅拌器21+框式搅拌器22”的组合,再加上内冷挡管8构成搅拌体系,改善了搅拌强度剪切力和循环次数,避免了物料搅拌不均匀的问题,进一步提高了搅拌效果和传热效果,保证产品颗粒形态好、纯度高、分子量分布匀称。同时,设置在反应釜本体1内部的内冷挡管8,也进一步提升了换热效率,充分满足了反应时的换热要求,使反应温度控制在70℃左右,保证甘氨酸能达到预定的反应温度。另外,在反应釜本体1外侧壁上设置采用采用全流通的半管夹套5结构,还增加了反应釜本体1内部和外部的换热能力,能更加精确的控制甘氨酸的反应温度。
42.采用该甘氨酸合成反应釜,能有效的提高反应釜的搅拌效果、传热能力和搅拌效率,从而极大的提高了甘氨酸的生产强度,为甘氨酸生产提供了理想装置。
43.具体的,驱动机构包括通过机架42安装在反应釜本体1顶部的驱动电机4、减速机41。驱动电机4的动力输出端与减速机41的动力输入端传动连接,减速机41的动力输出端通过传动组件与搅拌轴2上端传动连接。本实施例中,传动组件通过轴向转动轴承34安装到机架42上。通过安装在机架42上的驱动电机4带动减速机41,进而带动传动组件和搅拌轴2转动,完成反应釜本体1的正常运作。
44.位于传动组件与反应釜本体1之间的搅拌轴2上设有挂轴件23。挂轴件23与反应釜本体1之间的搅拌轴2上套接有环形接油件24。环形接油件24与机架42固定连接。搅拌轴2上设置挂轴件23,能方便在不拆搅拌轴2的情况下更换传动组件。同时,挂轴件23下设置环形接油件24,防止密封油进入反应釜本体1内影响产品品质。本实施例中,机架42上设有用于抽出环形接油件24中的密封油的抽油管。通过抽油管,能将环形接油件24中继续的密封油抽出,防止密封油进入反应釜本体1内影响产品品质。
45.同时,关于传动组件,该反应釜本体1上的传动组件包括从上往下同轴依次连接的第一联轴器3、传动轴31、第二联轴器32以及机械密封33。第一联轴器3与驱动机构的动力输出端传动连接,机械密封33与搅拌轴2上端传动连接。采用机械密封33,配合环形接油件24,既保证了反应釜本体1密封的可靠性,又避免了产品因受到密封油污染而影响产品质量。
46.并且,该反应釜本体1还包括竖直设置在反应釜本体1内的用于安装温度计的温度计套管7,能够实时检测反应釜本体1内的温度,方便检测人员监测反应的正常运行,进而保
证了产品质量。进料口内设有竖直向下延伸且下端为斜切口的进料管12,进料管12末端斜切成尖状,能防止挂料。进气口内设有沿反应釜本体1内壁向下延伸至其底部的进气管6。进气管6从反应釜本体1的进气口进入,沿反应釜本体1的内壁往下伸到其底部,充分保证物料尽快混合均匀,有利于反应的快速进行,减少副产物的产生,提高了甘氨酸的收率。
47.本实施例中,反应釜本体1外壁上设有耳式支座11。反应釜本体1顶部外壁上还设有带视镜的人孔14,方便检测人员监测反应的正常运行和检修反应釜本体1,进而保证了产品质量。
48.另外,内冷挡管8包括一竖直设置且上端延伸至反应釜本体1外的内层输出管82,内层输出管82外套接有一上端延伸至反应釜本体1外的外层输入管83。外层输入管83侧壁通过挡管安装架81与反应釜本体1内壁连接。通过内层输出管82输出完成热传导的冷却介质,外层输入管83输入冷却介质,完成反应物的换热过程。同时,内冷挡管8改善了搅拌强度剪切力和循环次数,避免了物料搅拌不均匀的问题,进一步提高了搅拌效果和传热效果,保证产品颗粒形态好、纯度高、分子量分布匀称。
49.半管夹套5上设有冷却介质进管51和冷却介质出管52。冷却介质进管51和冷却介质出管52相对设置在反应釜本体1两侧。相对设置在反应釜本体1两侧的冷却介质进管51和冷却介质出管52能使冷却介质完成至少半圈的环绕流动,从而带走热量,保证反应的顺利进行。
50.本实施例中,需要注意的是:
51.斜叶桨式搅拌器21和框式搅拌器22的直径与反应釜本体1的直径之比为0.3-0.8。
52.反应釜本体1的容积为30m
3-100m3,其高径比为1.2-2.5,公称直径为2.0m-5.0m。具体的,釜体容积为95m3,高径比为1.56,公称直径为4m。
53.在大型甘氨酸合成反应生产过程中,反应物料——甘氨酸、乌洛托品、氯化铵、甲醇、氯乙酸铵、纯水从反应釜本体1上部的进料管12进入反应釜本体1内,与通过进气管6从反应釜本体1下部进入的氨气进行氨化反应,并在六次甲基四胺的催化作用下反应生成氨基乙酸和副产物氯化铵。
54.在加料过程中,通过半管夹套5内的热水进行加热,反应过程中通过半管夹套5内的冷却水进行降温,维持反应温度,同时,开启搅拌轴2使物料搅拌充分,混合均匀,保证反应釜本体1内反应温度和ph值的均衡,减少了副产物的产生。反应完成后,物料从反应釜本体1的出料口13排出并进入下道工序,反应釜本体1又开始下一轮的生产。
55.以上结合最佳实施例对本实用新型进行了描述,但本实用新型并不局限于以上揭示的实施例,而应当涵盖各种根据本实用新型的本质进行的修改、等效组合。