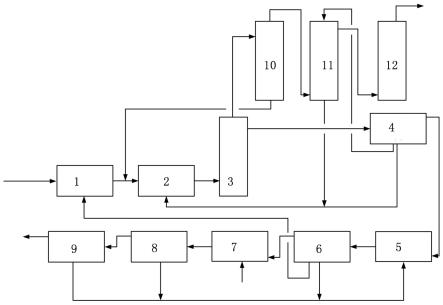
1.本实用新型涉及有机硅单体的水解领域,尤其涉及一种二甲基二氯硅烷浓酸水解系统。
背景技术:2.利用有机硅单体二甲基二氯硅烷(二甲)水解制备聚硅氧烷是有机硅行业的基础环节,该环节水解方法的不同直接影响到有机硅产品的质量以及水解过程中氯资源的回收效率。
3.二甲基二氯硅烷的水解工艺主要有两种:一种是稀酸水解(恒沸酸水解)工艺,一种是浓酸水解(或饱和酸水解)工艺。稀酸水解工艺利用二甲与稀盐酸(~20 wt%)进行水解反应,生成聚硅氧烷环体、羟基封端聚硅氧烷线体和hcl。该工艺的优点为水解产物中聚硅氧烷环体占比高,产品粘度低,同时酸值也较低。缺点为反应生成的hcl直接溶于水会释放大量热,需要耗用大量冷却水进行换热;要对hcl进行再利用,需要采用高耗能的蒸馏方式进行解吸。所以目前,稀酸水解工艺已被淘汰。浓酸水解工艺采用二甲与近饱和的浓盐酸进行混合水解。该工艺的主要优点为直接获得hcl气体,可节约大量能耗;反应中放热等控制相对稀酸水解工艺容易。这使其成为目前国内外最主流的二甲水解工艺。值得注意的是,不同于稀酸水解,浓酸水解的水解产物除聚硅氧烷环体和hcl外,还包括氯封端聚硅氧烷线体,同时氯封端聚硅氧烷线体占比较高,这使得浓酸水解之后仍存在大量未完全水解的sicl基团。所以对于浓酸水解工艺来说,无法仅用一步完成水解,需后续增加多级稀酸水解单元以进一步与-sicl反应;同时,氯封端聚硅氧烷线体易在后续水解过程中发生缩聚反应,使得聚硅氧烷链变长,产品粘度增加,进而使得油性水解物与酸液分离困难,产品酸值高(即水解物中氯离子含量高)。此外,浓酸水解产生的hcl气体逸出时,会夹带油相,造成后续氯甲烷合成单元停车检修频繁。因此,如何提高浓酸水解工艺中水解产物和hcl气体的产品质量显得尤为重要。
4.目前,浓酸水解工艺的相关专利均采用一环直接浓酸水解,使得产品氯封端聚硅氧烷线体比重仍偏高;同时,hcl气体净化时,通常仅采用冷却方式进行,这难以有效降低hcl气体中夹带的油滴,特别是粒度为微米级的油滴。而相关专利关注的重点通常在于如何降低最终水解物的酸值。如专利cn101982485b公开了一种有机氯硅烷饱和酸水解方法,利用汽化后的二甲直接进行饱和酸水解,并在后续单元采用多级水洗以降低水解产物的酸值。然而该工艺中二甲汽相进料易被生成的hcl气体夹带,造成二甲损耗以及hcl气体中杂质含量增加;同时由于水解物不溶于水,仅依靠水洗很难降低产品的酸值。专利cn101817505b通过采用两级水洗和一级碱洗的方式降低水解产物中氯离子含量。但由于水解物的疏水性,即使增加碱洗步骤也无法完全去除油性水解物中的酸液滴,同时还会导致废碱、废盐排出。专利cn110845734a采用两级萃取塔和汽提塔的组合去除水解物中的酸液滴,但该方式有效去除酸的能力仍然有限,同时会大幅增加设备投资和能耗。
5.基于现有水解工艺或方法中存在的诸多问题,亟需开发一种可以获得高质量聚硅
氧烷及hcl气体的浓酸水解装置。
技术实现要素:6.为解决以上问题,本实用新型提供一种浓酸水解制备低粘度、低酸值聚硅氧烷和高纯度hcl气体的系统,以提高产品质量。
7.为实现上述目的,本实用新型的技术方案中包括预混系统、浓酸水解系统、hcl净化系统、稀酸水解系统、水洗系统及聚结单元的相关技术方案,采用了如下技术构思:
8.预混系统:二甲基二氯硅烷与二级分离器分离获得的稀酸溶液先进行预混水解,可降低水解产物中氯封端聚硅氧烷线体占比,降低产品粘度和酸值。
9.浓酸水解系统:预混水解后的物料进入一级混合器,在此处与一级分离器分离获得的浓酸以及hcl净化系统中旋液分离器分离获得的油相进行混合后进入乳化塔水解。水解后的hcl气体进入后续hcl净化系统,水解物及盐酸溶液进入一级分离器。在一级分离器内,水解物和盐酸进行分离。分离后的水解物进入二级混合器;分离后的盐酸分为两股出料,一股返回至一级混合器参与水解,一股流入hcl净化系统中的洗涤塔用于hcl气体的洗涤。
10.hcl净化系统:夹带液(油)滴的hcl气体从乳化塔顶部逸出,进入旋液分离器进行气液分离。此时可将大部分液滴从hcl气体中分离出,并返回至一级混合器再利用。初步净化后的hcl随后进行洗涤塔,并在此利用一级分离器分离获得的浓酸对hcl气体进行逆流洗涤,进一步除去油滴。洗涤后的浓酸返回至一级混合器循环利用,hcl气体再经过冷却除沫以将洗涤过程中夹带的少量盐酸去除,最终可以获得纯度较高的hcl气体。该纯度可直接用于后续氯甲烷合成单元,确保装置设备不易堵塞。
11.稀酸水解系统:从一级分离器分离出的油相进入二级混合器,在此处与二级分离器、三级分离器以及聚结单元分离得到的稀酸进行混合水解。水解后的物料进入二级分离器进行分离,分离得到的油相进入后续水洗系统,而酸液相分为两股流出,一股返回至二级混合器,一股返回至预混合器,均用于提供水解所需的水。
12.水洗系统:从稀酸水解系统流出的油相进入三级混合器,并在此处补充工艺水以对水解物进行洗涤。水洗后物料进入三级分离器,以将水解物及酸液分离。分离后的酸液返回至二级混合器参与水解反应,油相进入后续聚结单元。
13.聚结单元:从水洗系统流出的油相物料进入聚结单元,可将油相中的酸液在聚结材料上聚结,降低水解物产品的酸值,同时聚结分离后的酸液滴返回至二级混合器进行再利用。最终,从聚结单元流出的水解物酸值低、粘度低。
14.根据上述技术构思,本实用新型提供了一种二甲基二氯硅烷浓酸水解系统,二甲基二氯硅烷管道与预混合器连接,预混合器与一级混合器连接;
15.一级混合器与乳化塔连接,乳化塔与一级分离器连接,一级分离器与二级混合器连接,二级混合器与二级分离器连接,二级分离器与聚结单元连接,聚结单元连接至水解物产品罐。
16.二级分离器与聚结单元之间至少与一组混合器、分离器串联连接,即二级分离器与第n级混合器连接,第n级混合器与第n级分离器连接,第n级分离器与聚结单元连接;
17.所述的第n级混合器上设置有工艺水进料管;所述的n为1~3。
18.二级分离器与三级混合器连接,三级混合器与三级分离器连接,三级分离器与聚结单元连接;所述的三级混合器上设置有工艺水进料管。
19.乳化塔与旋液分离器连接,旋液分离器与洗涤塔连接,洗涤塔与冷却除沫器连接,冷却除沫器连接至氯化氢气体出料管。
20.旋液分离器与一级混合器连接;
21.一级分离器分别经管道与洗涤塔及一级混合器连接;
22.洗涤塔与一级混合器连接。
23.二级分离器经管道与预混合器连接;
24.二级分离器、第n级分离器、聚结单元分别经管道与二级混合器连接;
25.或二级分离器、三级分离器、聚结单元分别经管道与二级混合器连接。
26.本实用新型的上述装置中,本领域技术人员能够理解并预料得到是的在设备之间设置有开关、阀门、泵,其目的是实现物料的可控及顺利的进入下一设备中实现水解反应、洗涤或分离过程。
27.采用本实用新型的上述技术方案进行的稀盐酸水解及浓盐酸混合-水解的技术方案,使水解后的hcl中夹带的油相组分大致包括水解物、水及少量二甲基二氯硅烷,在旋液分离过程中,经离心极易使大尺寸的油滴、水滴与hcl气体分离,再在浓度为40~50 wt%的浓盐酸进行洗涤的过程中,剩余的微小油滴和水滴可以被除去,从而实现液气的分离,纯化了hcl气体。
28.本实用新型的技术方案实现的有益效果为:
29.1、二甲先与稀酸进行部分水解再与浓酸水解,可以降低氯封端聚硅氧烷线体占比,降低产品的粘度和酸值;
30.2、采用混合器混合并利用乳化塔进行水解,加强了二甲与浓酸的混合,使得水解更彻底,提高了水解物中聚硅氧烷环体的含量;
31.3、对hcl气体夹带的油滴分别采用旋液分离和水洗进行分离、回收,极大降低了hcl气体中的杂质含量,使其可直接用于氯甲烷合成,降低生产成本,延长设备运行周期;
32.4、将传统的多级水洗(+碱洗)系统优化为水洗+聚结系统,可以有效降低水解产物中的酸水含量,提升产品品质,同时避免(含盐)废水的产生,节约成本;
33.5、各级分离器以及聚结单元分离得到的含酸水相均进行循环再利用,绿色经济。
附图说明
34.图1是二甲基二氯硅烷浓酸水解系统。其中,1. 预混合器,2. 一级混合器,3. 乳化塔,4. 一级分离器,5. 二级混合器,6. 二级分离器,7. 三级混合器,8. 三级分离器,9. 聚结单元,10. 旋液分离器,11. 洗涤塔,12. 冷却除沫器。
具体实施方式
35.下面结合附图1并通过具体实施方式来进一步说明本实用新型的技术方案。
36.因本案是流程图,有些名称不是通用名称,所以进一步进行了解释。
37.1. 预混合器,为搅拌釜或静态混合器(如sk型、sv型)。
38.2. 一级混合器,为搅拌釜或静态混合器(如sk型、sv型)。
39.3. 乳化塔,为填料塔。
40.4. 一级分离器,为液液相分离器。
41.5. 二级混合器,为搅拌釜或静态混合器(如sk型、sv型)。
42.6. 二级分离器,为液液相分离器。
43.7. 三级混合器,为搅拌釜或静态混合器(如sk型、sv型)。
44.8. 三级分离器,为液液相分离器。
45.9. 聚结单元,为聚结分离器。
46.实施例1
47.一种二甲基二氯硅烷浓酸水解系统,二甲基二氯硅烷管道13及稀盐酸管道14与预混合器1连接,预混合器1与一级混合器2连接,一级混合器2上设置有浓盐酸进料管15;
48.一级混合器2与乳化塔3连接,乳化塔3与一级分离器4连接,一级分离器4与二级混合器5连接,二级混合器5与二级分离器6连接,二级分离器6与聚结单元9连接,聚结单元9连接至水解物产品罐。
49.二级分离器6与聚结单元9之间至少与一组混合器、分离器串联连接,即二级分离器6与三级混合器7连接,三级混合器7与三级分离器8连接,三级分离器8与聚结单元9连接。
50.乳化塔3与旋液分离器10连接,旋液分离器10与洗涤塔11连接,洗涤塔11与冷却除沫器12连接,冷却除沫器12连接至氯化氢气体出料管。
51.旋液分离器10与一级混合器2连接;一级分离器4分别经管道与洗涤塔11及一级混合器2连接;洗涤塔11与一级混合器2连接。
52.二级分离器6经管道与预混合器1连接;二级分离器6、三级分离器8、聚结单元9分别经管道与二级混合器5连接;
53.所述的三级混合器上设置有工艺水进料管。
54.实施例2
55.采用实施例1的装置进行的二甲基二氯硅烷浓酸水解工艺,包括如下步骤:
56.(1)将工艺水通入至三级混合器中,将二甲基二氯硅烷通入至预混合器中,待系统稳定后自一级分离器中分离出浓盐酸,浓盐酸的浓度为40~45 wt%,二级分离器中分离出稀盐酸,稀盐酸的浓度为15~20 wt%;
57.(2)二甲基二氯硅烷与步骤(1)中分离得到的稀盐酸以进料流量比0.4:1分别进入预混合器(温度30~40℃,压力0.1~0.2 mpa),生成含聚硅氧烷环体的水解物,其中聚硅氧烷环体的占比为48 wt%;
58.(3)含聚硅氧烷环体的水解物与步骤(1)中分离得到的浓盐酸以进料比1:15分别进入一级混合器进行混合(温度30℃~40℃,压力0.1~0.2 mpa),混合后的产物进入乳化塔,在30℃~40℃条件下进行水解反应;
59.(4)步骤(3)中乳化塔进行水解后产生的hcl气体进入旋液分离器进行气液分离,在此可有效除去hcl气体夹带的直径较大的液(油)滴,之后hcl气体进入洗涤塔,并在此利用下述步骤中一级分离器分离得到的浓盐酸进行洗涤,有效去除hcl气体中粒径更小的油滴。随后再经过冷却除沫后,可大幅降低hcl气体中夹带的油相,得到的hcl气体可直接用于氯甲烷合成。另外,旋液分离器分离出的液相部分和洗涤塔内流出的液相物料均返回至一级混合器内进行循环利用。
60.水解后产生的液相进入一级分离器进行油水分离;乳化塔进行水解后产生的液相进入一级分离器进行油水分离,分离得到油相1及液相1,所述的液相1为浓盐酸,一部分补充至一级混合器,一部分作为洗涤塔的洗涤;
61.(5)分离出的油相1进入二级混合器进行稀盐酸水解,水解后的混合物进入二级分离器进行油水分离,分离得到油相2及液相2,所述的液相2为稀盐酸,一部分补充至预混合器参与水解,一部分返回至二级混合器参与水解;
62.分离出的油相2进入三级混合器进行稀盐酸水解,在该混合器内利用“纯净”的工艺水对水解物进行洗涤后,进入三级分离器进行油水分离,分离出的稀酸返回至二级混合器内参与水解,分离出的油相3进入聚结单元。
63.利用聚结单元对油相中含有的酸液滴进行聚结分离,尤其可聚结分离水洗难以除去的微小酸性液滴。聚结得到的含酸水相返回至二级混合器进行水解利用,经过聚结分离后的水解物从聚结单元中流出。该水解物具有聚硅氧烷环体占比高、酸值低、粘度低的显著特点。