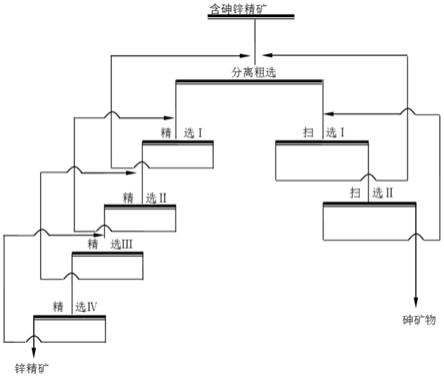
1.本发明涉及选矿技术领域,尤其涉及一种微细粒砷与锌选择性絮凝浮选分离的方法,其中微细粒砷主要是斜方砷铁矿,其次为毒砂,二者比例大于等于2:1。
背景技术:2.对于闪锌矿与含砷矿物的分离,现有技术一般有两种方法:(1)采用石灰、次氯酸钙、腐殖酸钠、亚硫酸钠、硫代硫酸钠、焦亚硫酸钠、氰化钠或其组合作为含砷矿物的抑制剂,黄药类等硫化矿捕收剂作为闪锌矿的捕收剂,采用浮选法实现锌与砷(主要是毒砂)的分离。(2)采用重选法将含砷矿物富集在重矿物中,实现闪锌矿与含砷矿物的分离。例如专利 cn201410343439.4公开了一种复杂含砷硫化铅锌矿的选矿方法,将原矿加入球磨机中磨矿,进入第一个搅拌槽后加入石灰、硫酸锌、亚硫酸钠及亚烷基二硫代氨基甲酸酯,在第二个搅拌槽加入乙硫氮和黄原酸丙烯酯及松醇油;在铅浮选的第一次扫选、第二次扫选前加入组合抑制剂和组合捕收剂;在第一次铅精选、第二次铅精选和第三次铅精选前加入组合抑制剂和组合捕收剂;铅浮选的尾矿进行锌浮选;锌第一次扫选、第二次扫选前加入组合抑制剂和组合捕收剂;在每次锌精选前加入石灰。该方案可提高锌精矿中锌品位及回收率,但锌精矿中砷含量仍较高。
3.对于粒度较细(-25μm)的矿物(砷主要是斜方砷铁矿),采用以上两种方法分离效果较差,最终导致锌精矿中有害元素砷的含量超标。
4.砷作为有害元素存在于锌精矿中,在冶炼时被氧化为剧毒物质挥发出来,对冶炼厂及其周边环境造成严重污染。因此,锌精矿深度降砷是许多研究工作者的重点方向。
5.近几年,较多研究团队对锌精矿深度降砷进行了大量的研究工作,研发了较多含砷矿物抑制剂,提出了重选分离的新思路。但对于微细粒锌与砷的分离效果仍不理想,导致锌精矿含砷仍较高(含量为0.3%~0.7%)。
6.有鉴于此,有必要设计一种改进的微细粒砷与锌选择性絮凝浮选分离的方法,以解决上述问题。
技术实现要素:7.为了克服上述现有技术的不足,本发明的目的在于提供一种微细粒砷与锌选择性絮凝浮选分离的方法,其中微细粒砷主要是斜方砷铁矿,其次为毒砂,二者比例大于等于2:1。采用选择性絮凝浮选方法实现微细粒砷与锌的深度分离,在确保锌回收率的前提下,将锌精矿中砷的含量降低至0.09%,有效降低了锌精矿中有害元素砷的含量,降低了锌精矿中有害元素砷在冶炼过程中对环境造成的污染。
8.为实现上述发明目的,本发明提供了一种微细粒砷与锌选择性絮凝浮选分离的方法,包括以下步骤:
9.s1.将含砷锌精矿加水调浆至矿浆质量浓度为15%-30%,然后向其中加入六偏磷酸钠50~100g/t,充分搅拌后加入鞣酸50~100g/t,接着加入淀粉溶液,最后加入石灰,搅
拌均匀得到浮选矿浆;
10.s2.将步骤s1得到的所述浮选矿浆加至浮选机中,加入捕收剂进行浮选粗选,得到粗选泡沫和粗选底流;
11.s3.将步骤s2得到的所述粗选泡沫进行精选得到锌精矿;将所述粗选底流进行扫选得到砷精矿。
12.作为本发明的进一步改进,所述含砷锌精矿中的微细粒砷主要是质量比大于等于2:1的斜方砷铁矿和毒砂。
13.作为本发明的进一步改进,在步骤s1中,所述淀粉溶液的用量为100~200 g/t,所述石灰的用量为800~1500g/t。
14.作为本发明的进一步改进,所述淀粉溶液为红薯淀粉溶液,将质量比为4:1 的红薯粉和碳酸钠加入水中,溶质总体积浓度为0.4%~0.6%,将溶液加热至85~ 95℃,边加热边搅拌,将配制好的溶液自然冷却至常温。
15.作为本发明的进一步改进,在步骤s2中,所述捕收剂为丁基黄药和z-200。
16.作为本发明的进一步改进,所述丁基黄药的用量为10~20g/t,所述z-200 的用量为30~50g/t。
17.作为本发明的进一步改进,在步骤s3中,所述精选的次数为四次,所述扫选的次数为两次,四次精选和两次扫选所得中矿依次返回进行下一次精选或扫选。
18.作为本发明的进一步改进,所述四次精选过程加入腐殖酸钠50~200g/t,所述扫选过程加入丁基黄药10~15g/t。
19.作为本发明的进一步改进,在步骤s1中,所述含砷锌精矿中锌的质量含量为35%-50%,砷的质量含量为1%-6%。
20.作为本发明的进一步改进,所述含砷锌精矿的细度满足0.074mm以下的含量占80%以上。
21.作为本发明的进一步改进,在步骤s3中,所述锌精矿中砷含量小等于于0.09%,锌回收率为98%以上。
22.本发明的有益效果是:
23.1.本发明提供的微细粒砷与锌选择性絮凝浮选分离的方法,采用选择性絮凝浮选方法实现微细粒砷与锌的深度分离,为了增强絮凝过程的选择性,在絮凝前对被絮凝矿物(斜方砷铁矿和毒砂)进行表面改性,使其表面亲水,而闪锌矿表面疏水,两种矿物在矿浆中呈分散状态,以保证絮凝砷矿物时,微细粒锌矿物不被同时絮凝,从而确保锌的回收率不会大幅下降,同时锌精矿中砷的含量降低至0.09%,有效降低了锌精矿中有害元素砷的含量,降低了锌精矿中有害元素砷在冶炼过程中对环境造成的污染。
24.2.与现有氰化钠抑制砷工艺相比,本工艺使用的药剂为无毒环保型药剂。与其它抑制剂浮选效果相比,本工艺可将微细粒砷的含量降低至0.09%,其它抑制剂浮选工艺只能将锌精矿中砷的含量降低至0.3~0.7%。其它抑制剂浮选工艺用大量抑制剂抑制砷的同时,也抑制剂了部分闪锌矿,使锌精矿的回收率降低至 95%~97%,而本工艺中锌精矿的回收率为98.85%。
附图说明
25.图1为微细粒砷与锌选择性絮凝浮选分离的方法流程图。
具体实施方式
26.为了使本发明的目的、技术方案和优点更加清楚,下面结合具体实施例对本发明进行详细描述。
27.在此,还需要说明的是,为了避免因不必要的细节而模糊了本发明,在具体实施例中仅仅示出了与本发明的方案密切相关的结构和/或处理步骤,而省略了与本发明关系不大的其他细节。
28.另外,还需要说明的是,术语“包括”、“包含”或者其任何其他变体意在涵盖非排他性的包含,从而使得包括一系列要素的过程、方法、物品或者设备不仅包括那些要素,而且还包括没有明确列出的其他要素,或者是还包括为这种过程、方法、物品或者设备所固有的要素。
29.请参阅图1所示,本发明提供的微细粒砷与锌选择性絮凝浮选分离的方法,包括以下步骤:
30.s1.将含砷锌精矿加水调浆至矿浆质量浓度为15%-30%,然后向其中加入六偏磷酸钠50~100g/t,充分搅拌后加入鞣酸50~100g/t,接着加入淀粉溶液,最后加入石灰,搅拌均匀得到浮选矿浆;
31.在步骤s1中,含砷锌精矿中锌的质量含量为35%-50%,优选为40%-48%;砷的质量含量为1%-6%,优选为1%-4%。含砷锌精矿的细度满足0.074mm以下的含量占80%以上,优选为85%-90%。含砷锌精矿中的微细粒砷主要为斜方砷铁矿和毒砂,两者质量比大于等于2:1。
32.淀粉溶液的用量为100~200g/t,石灰的用量为800~1500g/t。
33.淀粉溶液优选为红薯淀粉溶液,将质量比为4:1的红薯淀粉和碳酸钠加入水中,溶质总体积浓度为0.4%~0.6%,将溶液加热至85~95℃,边加热边搅拌,将配制好的溶液自然冷却至常温。若用于含砷高的锌矿石浮选,可根据含砷锌精矿中微细粒砷的含量适当改变红薯淀粉的用量。
34.在此步骤中,絮凝前按顺序依次加入六偏磷酸钠和鞣酸,能够很好地保证絮凝砷矿物时,锌矿物不被同时絮凝。
35.s2.将步骤s1得到的浮选矿浆加至浮选机中,加入捕收剂进行浮选粗选,得到粗选泡沫和粗选底流;
36.捕收剂为丁基黄药10~20g/t和z-200(乙硫氨脂,化学成分:o-异丙基-n
‑ꢀ
乙基硫逐氨基甲酸酯)30~50g/t。
37.s3.将步骤s2得到的粗选泡沫进行精选得到锌精矿;将粗选底流进行扫选得到砷精矿。
38.在步骤s3中,精选的次数为四次,扫选的次数为两次,四次精选和两次扫选所得中矿依次返回进行下一次精选或扫选。四次精选过程加入腐殖酸钠50~ 200g/t,扫选过程加入丁基黄药10~15g/t。
39.步骤s3得到的锌精矿中砷含量小等于于0.09%,锌回收率为98%以上。
40.本发明采用选择性絮凝浮选方法实现微细粒砷与锌的深度分离,在确保锌回收率的前提下,将锌精矿中砷的含量降低至0.09%,有效降低了锌精矿中有害元素砷的含量,降低了锌精矿中有害元素砷在冶炼过程中对环境造成的污染。
41.实施例1
42.以质量百分数计,本实施例含砷锌精矿中含zn45.25%,含as2.63%,sio20.93%。其中锌矿物主要是闪锌矿,砷矿物主要是斜方砷铁矿和毒砂,二者质量比例约为3:1,粒度小于25μm。含砷锌精矿细度为-0.074mm87.67%。
43.如图1所示,一种微细粒砷与锌选择性絮凝浮选分离的方法,具体步骤如下:
44.(1)将含砷锌精矿加水调浆至矿浆浓度为30%,向其中加入六偏磷酸钠80g/t,充分搅拌后加入鞣酸80g/t,然后加入红薯淀粉溶液,最后加入石灰800~1000g/t;
45.步骤(1)一般在矿浆搅拌桶中进行。其中红薯淀粉的配制方法为:将红薯粉和碳酸钠以质量比4:1加入水中,体积浓度为0.5%,将溶液加热至95℃,边加热边搅拌,配制好的溶液自然冷却至常温。红薯淀粉用量约160g/t。
46.(2)将步骤(1)所制矿浆加至浮选机中,加入丁基黄药15g/t和z-20040g/t进行浮选粗选。
47.(3)粗选泡沫经过四次精选得到锌精矿,粗选底流经过两次扫选,扫选底流为砷精矿。四次精选和扫选所得中矿依次返回。四次精选加腐殖酸钠100g/t,扫选加丁基黄药10g/t。
48.本实施例得到的锌精矿含zn47.55%,含砷0.09%,锌回收率为98.85%。
49.对比例1
50.对比例1提供的一种微细粒砷与锌选择性絮凝浮选分离的方法,矿石来源与实施例1相同。不同之处在于,不加六偏磷酸钠和鞣酸,其它条件与实施例1大致相同。试验结果见表1,用于与本发明对比。
51.对比例2
52.对比例2提供的一种微细粒砷与锌选择性絮凝浮选分离的方法,采用传统直接抑制工艺和药剂高碱(石灰)或六偏磷酸钠+鞣酸直接抑制砷,浮选选锌,流程不变。试验结果见表1,用于与本发明对比。
53.对比例3
54.对比例3提供的一种微细粒砷与锌选择性絮凝浮选分离的方法,采用传统直接抑制工艺和药剂高碱(石灰)或次氯酸钙、腐殖酸钠、亚硫酸钠、硫代硫酸钠和焦亚硫酸钠,直接抑制砷,浮选选锌,流程不变。试验结果见表1。
55.表1实施例1及对比例1-3的浮选工艺结果
56.[0057][0058]
从表1可以看出,采用本发明的絮凝抑制工艺,但未在加入淀粉前添加六偏磷酸钠和鞣酸时,锌回收率明显下降,砷含量明显增大,说明本发明在加入淀粉前依次加入六偏磷酸钠和鞣酸,能够增强絮凝过程的选择性,保证絮凝砷矿物时,锌矿物不被同时絮凝,并提高对砷矿物的絮凝效果。当加入六偏磷酸钠、鞣酸和石灰,进行传统的直接抑制工艺时,砷含量明显增大,锌回收率也明显下降,表明该工艺中抑制作用的针对性不够,部分砷未被有效抑制,部分锌却被抑制。当采用传统抑制工艺,且仅添加石灰时,锌回收率下降和砷含量增大最明显。说明本发明将六偏磷酸钠和鞣酸与淀粉结合,能够起到明显优于单独采用六偏磷酸钠和鞣酸,或者单独采用淀粉的絮凝浮选效果。
[0059]
综上所述,本发明提供的微细粒砷与锌选择性絮凝浮选分离的方法,采用选择性絮凝浮选方法实现微细粒砷与锌的深度分离,为了增强絮凝过程的选择性,在絮凝前对被絮凝矿物(斜方砷铁矿和毒砂)进行表面改性,使其表面亲水,而闪锌矿表面疏水,两种矿物在矿浆中呈分散状态,以保证絮凝砷矿物时,微细粒锌矿物不被同时絮凝,从而确保锌的回收率不会大幅下降,同时锌精矿中砷的含量降低至0.09%,有效降低了锌精矿中有害元素砷的含量,降低了锌精矿中有害元素砷在冶炼过程中对环境造成的污染。
[0060]
以上实施例仅用以说明本发明的技术方案而非限制,尽管参照较佳实施例对本发明进行了详细说明,本领域的普通技术人员应当理解,可以对本发明的技术方案进行修改或者等同替换,而不脱离本发明技术方案的精神和范围。