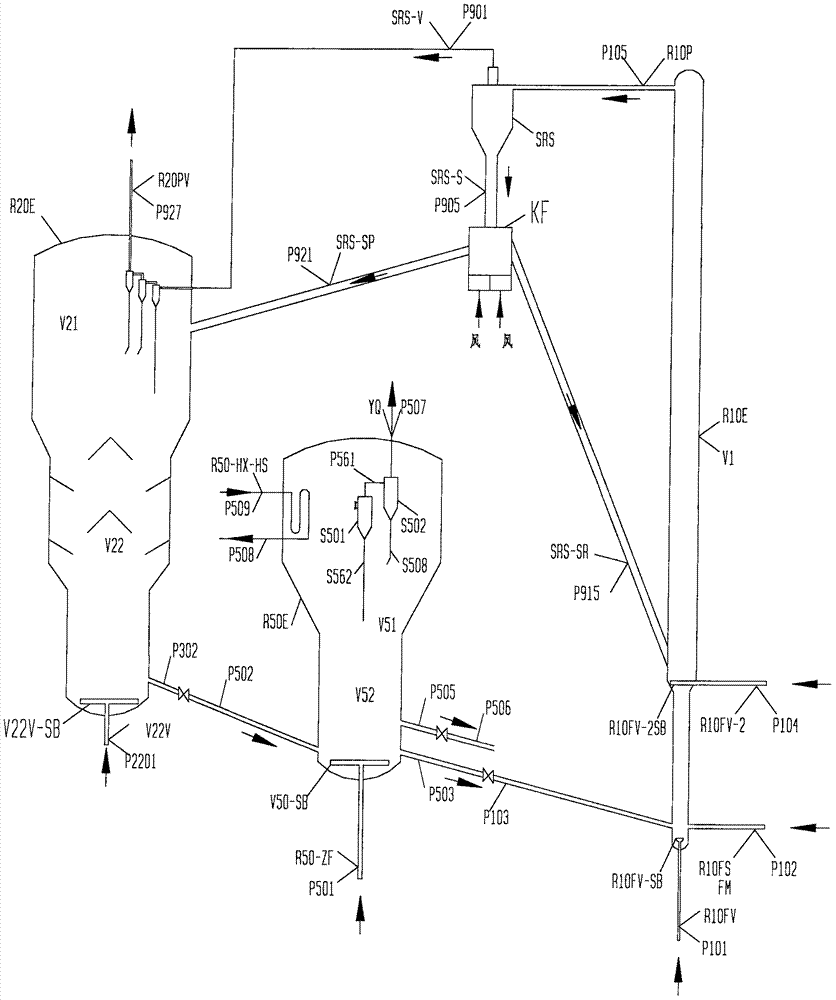
本发明涉及用双循环粉料的快速预热串联适温热解式碳氢料热解方法,特别适合于重油固化粉料热解过程,提升管热解反应器下部注入高温长循环第一固体热载体LR-DS、中部回注热解固体产物短循环固体料SR-DS,可提高长循环固体热载体温度,实现热解初期的快速预热,利于缩短重油固化粉料热解过程的软化温度点到结焦温度点的加热时间并抑制颗粒的粘结;SR-DS进行循环热解时强化适温热阶段固固混合效应,提高总体热解效率;可降低LR-DS数量,进而降低流化烧焦过程R50甚至沉降过程的规模,降低细粉颗粒产量;可提高R50温度,提高烧焦速度进而降低R50规模,利于提高回收能量的能级和回收率。
背景技术:
:以下描述煤加氢直接液化生成油分馏过程得到的残液AR10P-VS。煤加氢直接液化反应过程AR10产生煤加氢直接液化生成油AR10P-O,在煤加氢直接液化生成油AR10P-O的分离部分使用的减压蒸馏塔塔底,分离得到主要由常规沸点高于500~540℃的烃组分和固体组成的减压塔底含固液料VS即本发明所述残液,多数工艺将部分减压塔底含固液料VS返回煤加氢直接液化反应过程AR10作为循环料VS-R以多次重复利用部分催化剂颗粒、深度转化部分重质烃(胶质、沥青烯、前沥青烯),同时排出部分减压塔底含固液料VS作为残液AR10P-VS以排出废催化剂颗粒、无法液化的煤碳骨架颗粒,同时残液AR10P-VS中夹带着重质烃如油分、胶质、沥青烯、前沥青烯,残液R10P-VS的软化点通常高于100~150℃。返回煤加氢直接液化反应过程AR10作为循环料VS-R,因为含有无法液化的废催化剂颗粒、无法液化的煤碳骨架颗粒,同时夹带的部分重质烃是难以加氢轻质化的多环芳烃、胶质、沥青烯、前沥青烯,因此循环料VS-R的存在,虽然能够回收少量油品,但是显著恶化了煤加氢直接液化反应过程AR10及其相关系统的操作条件,缩短了连续运行周期、限制或压缩了原料煤种范围(主要是对粉的灰分含量和惰质组含量提出了上限要求)。随着高活性、高分散度煤液化加氢催化剂的开发成功,催化剂的废弃成本已经大幅度下降,因此可以考虑煤液化加氢催化剂单程使用后废弃的方案,在此前提下,如果能够有效回收残液AR10P-VS中的烃类而不使用循环料VS-R,则优化了加氢直接液化反应过程AR10的烃液进料性质,因此可以延长连续运行周期、扩大原料煤种范围。关于煤直接液化残渣的性质分析数据,参见文献:①出版物名称:《煤炭直接液化工艺与工程》,689页至723页;②检索用图书编码:ISBN编码:9-78703-04308-23;③编著:吴秀章、舒歌平、李克健、谢舜敏;④出版社:科学出版社。本发明所述高灰分高油分的含固油料,指的是灰分含量高、油分含量高的碳氢料如煤直接液化残渣,其深度热解过程具有如下特点:①原料灰分重量含量高,比如高达10~40%甚至更高;②原料挥发分重量含量高,比如高达30~55%甚至更高;③原料热解过程热解焦油收率高,比如高达8~25%甚至更高;④作为连续供料,其中的固体含量不均匀;⑤作为流体,难以均匀分散;⑥作为流体,难以计量;⑦热加工过程处理之,所得油气的流量、组成极不稳定,油气难以连续处理。煤直接液化残渣,其流化热解过程具有如下特点:①原料颗粒度难以控制在适中范围,原料颗粒度如果较大,则热解时间较长,热解反应器的高度太高,投资增大、气体气功率消耗高;②原料颗粒度难以控制在适中范围,原料颗粒度如果很小,则热解时间较段,但是热解产生大量细微粉尘,大幅度提高煤气深度脱尘过程的负荷,热解煤气回收的焦油中的半焦含量会升高;③由于煤直接液化残渣热解半焦中的部分连接不是稳定的化学键,而是热解结焦过程焦的“粘结”,煤直接液化残渣热解半焦的耐磨性和硬度均低于粉煤热解半焦,因此,其烧焦过程的粉化度远大于粉煤热解半焦在烧焦过程的粉化度,会生成更多的细颗粒。关于煤直接液化残渣的热解产物产率,可以参考2013年8月刊发的煤炭学报第38卷第8期,记载了北京低碳清洁能源研究所的文章“煤直接液化与残渣热解联合加工技术”,表1是煤液化残渣的组成和性质,采用类似于釜式焦化工艺的热解过程,煤液化残渣在550℃温度条件下热解2小时,表2是残渣热解试验的产品分布、产品组成和性质,热解结果如下:①可以得到16.5%(对煤液化残渣)的热解焦油收率;残渣热解油经过适当加氢处理后可以得到多环芳烃或部分饱和的多环芳烃含量超过79.2%、芳碳率为0.428的重馏分油,是理想的煤直接液化溶剂油;②气体产率为9.1%(对煤液化残渣),主要组分是甲烷、氢气、碳二烃、CO;③半焦产率为73.9%(对煤液化残渣),其灰分由原料的17.94%(对煤液化残渣)大体富集到24.28%(对热解半焦)。依据一般的流化焦化产物分布规律,大体可以推测,性质如表1的煤直接液化残渣的产品如下:①可以得到21~24%(对煤液化残渣)的热解焦油收率;②气体产率为9~13%(对煤液化残渣);③半焦产率为63~70%(对煤液化残渣),其灰分由原料的17.94%(对煤液化残渣)大体富集到25.63~28.5%(对热解半焦)。本发明所述煤直接液化残渣,其热解过程适宜的温度通常为380~650℃、一般为500~620℃、宜为530~580℃。本发明所述煤直接液化残渣,其流化热解过程适宜的温度通常为450~680℃、一般为520~650℃、宜为550~600℃。表1煤液化残渣的组成和性质表2残渣热解试验的产品分布、产品组成和性质为了提供热解过程的吸热量,通常需要烧掉相当于煤直接液化残渣重量12~20%的碳,这样,按照热平衡考虑,氧化半焦的组成将大体是:其灰分由热解半焦的25.63~28.5%(对热解半焦)大体富集到32~36%(对氧化半焦),如果考虑优先燃烧部分半角如小颗粒半焦,则其燃烧后的氧化半焦的灰含量会更高。煤直接液化残渣,如果以液体形态喷入使用固体载体的流化热解过程,因为固体含量高且固含量不稳定、粘度大,难以实现连续、平稳供料;对此,利用其软化点高于120~150℃的特点,可采用固体颗粒细粉形态喷入使用固体载体的流化热解过程,解决供料问题。煤直接液化残渣,如果以固体形态喷入使用固体载体的流化热解过程,当装置规模较大时,其热解过程气体和焦油的产量和产率将趋于平稳,可单独运行。煤直接液化残渣,如果以固体形态喷入使用固体载体的流化热解过程,当装置规模较小时,则该热解过程气体和焦油的产量和产率极不稳定,其后续连续稳定加工极其困难,对此,可与第二碳氢料粉煤热解过程形成简化流程的组合工艺,可与择CN105602593A、CN105694933A热解方法及其发展方法组合。CN105602593A、CN105694933A方法,其基本原理可以看作是在一定程度上将石油工业蜡油或渣油流态化催化裂化领域的反应再生系统技术的移植应用。在渣油流态化催化裂化的反应再生系统中,单程通过的原料是雾化的渣油、其产品是气态裂解油气,循环加工的物料是粉状固体催化剂,排出提升管催化热裂化反应器的催化剂为结焦后催化剂固体,结焦后催化剂经过沉降器内布置的旋风分离系统完成脱气、然后进入烧炭器或再生器进行烧炭再生,高温态的再生后催化剂粉料作为固体热载体和催化剂返回提升管反应器的下部入口,在提升气体作用下,与雾化的渣油混合接触进行流态化催化裂化反应,再生器产生的至少一部分热量被返回提升管催化热裂化反应器的再生后热态催化剂载入提升管催化热裂化反应器充当热裂化过程的热源。渣油流态化催化裂化的反应再生系统,已有超过50年的成功运转历史,其大型化单系列装置加工渣油量可达400~800万吨/年,催化剂循环量可达2000~4000万吨/年即2500~5000吨/时。与蜡油或渣油流态化催化裂化的反应再生系统相比,CN105602593A、CN105694933A方法,采用类似的提升管反应器进行粉煤热解反应,采用类似的旋风分离系统(布置于沉降器内)完成粉煤热解反应产物的气固分离,采用类似的烧炭器进行粉焦贫氧燃烧,烧炭器产生的热半焦的一部分作为固体热载体进入提升管反应器向煤热解反应过程供热并形成循环系统,多余的半焦排出系统和或氧化燃烧释放热量。在CN105602593A、CN105694933A所述系统中,单程通过的原料是新鲜固体粉煤,其热解产品是气态煤气和固体半焦,循环加工的物料是固体半焦(热解反应一次半焦产物或半焦循环料),高温态的固体氧化半焦作为固体热载体返回提升管反应器的下部入口,在提升气体作用下,与新鲜煤粉混合接触进行流态化热解反应。从上述对比可以看出,二种技术的热解反应器、热解产物气固分离系统、热解固体产物沉降器、循环固体料烧炭器,其相同流程位置的气固流体的流动方式基本相同。由于二者上述的相似性,CN105602593A、CN105694933A方法,极大地简化了系统的结构和操作,极大地提高了系统的安全性,是深具大型工业化潜力的技术方法。然而,无论何种方法,煤直接液化残渣的使用固体载体的流化热解应该是“快速预热段+适温热解段”热解工艺,以适应其流化热解过程的特点,理由如下:①与粉煤热解产生的煤气和焦油组分主要来自氧、硫、亚甲基桥键的热裂解键的类型不同,煤直接液化残渣中的挥发分绝大多数属于多环芳烃、胶质、沥青烯、前沥青烯,可供热裂解的键类型多属于双键,因其需要更高的离解能,煤直接液化残渣中的挥发分的适宜热解温度也必然较高;②与粉煤热解产生的煤气和焦油组分主要来自氧、硫、亚甲基桥键的热裂解键的类型不同,煤直接液化残渣中的挥发分绝大多数属于多环芳烃、胶质、沥青烯、前沥青烯,可供热裂解的键类型多属于双键,因其需要更高的离解能,煤直接液化残渣中的挥发分的适宜热解温度也必然较高,但是为了抑制过度的热裂解造气反应,工程上需要通过延长热解时间、增加单位反应空间有效供热量来适度降低热解温度,增加液体收率,这样,煤直接液化残渣固体颗粒喷入料中的挥发分如多环芳烃、胶质、沥青烯、前沥青烯,可能经历固体熔化为液体、液体流淌并导致颗粒粘结长大,破坏流化状态,因此,需要形成“快速预热段”,实现煤直接液化残渣固体颗粒的“在快速预热段快速实现汽化为油气、热裂解为油气、焦化为固体的热作用下的气、固二次分布”;③煤直接液化残渣固体颗粒“在快速预热段快速实现汽化为油气、热裂解为油气、焦化为固体的热作用下的气、固二次分布”后,为了防止油气发生大量的二次热裂解造气反应,然后必须对其降温进入“适温热解段”,使用温度合适的固体热载体是较佳的选择;④对于“适温热解段”,为了强化混合强度,提高传热、热解、颗粒表层结碳层剥皮的速度,可提高适温热阶段固体料数量,这暗示需要提高进入“适温热解段”的第二固体热载体的数量。另一方面,随着大规模粉煤流化热解过程的商业化,商业系统的工程优化也是必然的,下列粉煤流化床热解工程技术优化目标,也要求出现“快速预热段+适温热解段”热解工艺:①对于胶质体含量高、粘结性较高的粉煤,其流化床热解宜使用“快速预热段”;②为了提高烧焦过程热能回收效率和等级,进而生产高压力等级的水蒸气,需要提高烧焦过程温度;③为了降低烧焦反应空间体积,或者为了降低烟气中的CO含量,需要提高烧焦过程温度;④为了提高细碳颗粒的一次烧尽率,减少固体热载体中的细粉含量,需要提高烧焦过程温度;⑤为了降低大循环固体热载体数量,进而降低沉降器和烧焦器的体积,需要提高烧焦过程温度;⑥与大循环固体热载体的流程不同,自循环第二固体热载体的循环回路,不包括烧焦反应器及其输送系统甚至不包括沉降器,其极限受热温度也较低,因此,其粉化率较低,利于降低总系统藏量中的细粉比率;⑦短循环固体料,可以实现大小粒径固体颗粒的预分离,分出较小粒径颗粒进入沉降器及烧焦反应器,选出较大粒径固体颗粒形成短循环,一定程度形成了按粒径分类使用固体热载体,小颗粒固体热载体,可以在分离过程或沉降器或烧炭器等流程点排出热解烧焦系统,比如冷却后成为产品或热态进入气化过程、燃烧过程等,为进一步的按粒径分类使用固体创造了条件。基于上述分析,本发明的设想是:用双循环粉料的快速预热串联适温热解式碳氢料热解方法,特别适合于重油固化粉料热解过程,提升管热解反应器下部注入高温长循环第一固体热载体LR-DS、中部回注热解固体产物短循环固体料SR-DS,可提高长循环固体热载体温度,实现热解初期的快速预热,利于缩短重油固化粉料热解过程的软化温度点到结焦温度点的加热时间并抑制颗粒的粘结;SR-DS进行循环热解时强化适温热阶段固固混合效应,提高总体热解效率;可降低LR-DS数量,进而降低流化烧焦过程R50甚至沉降过程的规模,降低细粉颗粒产量;可提高R50温度,提高烧焦速度进而降低R50规模,利于提高回收能量的能级和回收率。本发明,涉及高灰分高油分的含固油料如煤液化残渣固化颗粒的流化热解方法,为了降低进入热解过程的固体热载体中细颗粒热载体的数量,可使用外部引入的大颗粒循环固体热载体形成循环固体热载体的主体,沉降过程或烧焦过程可采用分类排焦优先排出小颗粒氧化半焦产品而不作为固体热载体循环使用;煤液化残渣固化颗粒的流化热解过程可与粉煤热解烧焦系统组合,共用联合沉降器、采用分类排焦优先排出小颗粒氧化半焦产品的联合烧焦过程,联合烧焦过程向2个热解反应过程输送大颗粒固体热载体。为了减少设备数量,短循环的气固分离过程可以布置在沉降器内进行,即形成组合沉降器。为了减少短循环固体中的油气含量,通常短循环固体的缓冲器的空间内设置气提部件,使用气提气的气提出下行的短循环固体中的油气。为了降低一级热解流化床提升管反应器的高度,短循环型热载体排出口的空间高度可以合理安排在一定的高度,比如可以布置在组合沉降器的底部、下部、中部、上部等任意合适位置。本发明所述粉煤热解过程,指的是任何一种煤热解过程,最好是粉煤热解过程,优选为CN105602593A、CN105694933A及其后续发展出的工艺。本发明所述一级热解过程,可以包含1台或2台或多台串联操作的热解反应器,串联操作的热解反应器的结构可以相同或不同。本发明可以组合其它合适技术,构成组合工艺。本发明所述方法未见报道。本发明的第一目的在于提出用双循环粉料的快速预热串联适温热解式碳氢料热解方法。本发明的第二目的在于提出用双循环粉料的快速预热串联适温热解式碳氢料热解方法,适用于煤直接液化残渣固化颗粒的加工。本发明的第三目的在于提出用双循环粉料的快速预热串联适温热解式碳氢料热解方法,适用于液体烃料掺合固体形成的复合油固混合固体料,液体烃料可以是煤直接液化残渣液流、煤沥青液流、稠油液流等。本发明的第四目的在于提出用双循环粉料的快速预热串联适温热解式粉煤热解方法。本发明的第五目的在于提出用双循环粉料的快速预热串联适温热解式碳氢料热解方法的设备。技术实现要素:本发明用双循环粉料的快速预热串联适温热解式碳氢料热解方法,其特征在于包含以下步骤:(1)在一级热解反应过程R10,第一碳氢粉料R10FS进行一级热解反应R10R转化为气固混相的一级热解反应产物R10P;在一级热解反应过程R10,使用提升管流化床式一级热解反应器R10E,R10E至少使用三路固体进料:第一碳氢粉料R10FS、第一固体热载体LR-DS、短循环固体料SR-DS;一级热解反应器R10E,下部注入第一碳氢粉料R10FS、第一固体热载体LR-DS,中部注入短循环固体料SR-DS,短循环固体料SR-DS进入一级热解反应器R10E的位置,将一级热解反应器R10E分为R10E的下段R10E-D和R10E的上段R10E-U:①下段R10E-D,是第一碳氢粉料R10FS的一级热解反应过程R10R的第一热解段或预热段,进行一级第一热解反应R10E-DR,为上段R10E-U提供温度合适的固体进料;在下段R10E-D,第一碳氢粉料R10FS、第一固体热载体LR-DS进入反应器R10E的下部混合,在气体进料R10FV作用下通过下段R10E-D向上流动进行一级第一热解反应R10E-DR转化为下段R10E-D顶部的气固产物R10E-D-P;②上段R10E-U,是第一碳氢粉料R10FS的一级热解反应过程R10R的第二热解段或适温热阶段;上段R10E-U空间分为2区,下区为急冷区、上区为适温热解区;上段R10E-U的急冷区,是下段R10E-D的气固产物R10E-D-P的急冷区,也是短循环固体料SR-DS的快速吸热段,通过急速降温,抑制热解焦油的再次热裂解反应和再次热缩合反应,急冷区同时进行着热解反应;上段R10E-U的适温热解区,是急冷流出物的流态化深度热解区;在上段R10E-U的下区,加入的短循环固体料SR-DS与来自下段R10E-D的气固产物R10E-D-P混合,在气体作用下通过上段R10E-U向上流动进行一级第二热解反应R10E-UR转化为上段R10E-U顶部的气固产物R10E-U-P;气固产物R10E-U-P,用作一级热解反应器R10E的最终产物R10P;(2)在短循环气固分离过程SRS,一级热解反应产物R10P分离为短循环分离气体SRS-V和短循环分离固体SRS-S;(3)在返料器KF,短循环分离固体SRS-S分为短循环固体SRS-SR和固体料SRS-SP。本发明,通常,(1)在一级热解反应过程R10,第一碳氢粉料R10FS在上段R10E-U的热解煤气和热解焦油的总产量大于在下段R10E-D的热解煤气和热解焦油的总产量。本发明,通常,(1)在一级热解反应过程R10,第一碳氢粉料R10FS在上段R10E-U的热解煤气和热解焦油的总产量大于在下段R10E-D的热解煤气和热解焦油的总产量;(4)在二级热解反应过程R20,固体料SRS-SP进行二级热解反应R20R转化为二级热解反应产物R20P并分离为含尘二级热解过程气R20EPV和二级热解半焦R20PS;二级热解半焦R20PS排出二级热解反应过程R20;(5)在气固分离过程S20,离开固体粉料主体床层后的含尘二级热解过程气R20EPV分离为排出气固分离过程S20的脱尘二级热解煤气R20PV和半焦S20PS;(6)在流化烧焦反应过程R50,基于二级热解半焦R20PS的最终热解半焦RCPS进入流化烧焦反应空间,与含氧气体接触,进行流化床烧焦反应R50R,产生高温氧化半焦R50PS和烟气YQ,烟气YQ排出流化烧焦反应过程R50;高温半焦排出流化烧焦反应过程R50。本发明,通常,(7)基于R50排出的第一高温半焦R50P1S的物流,用作第一固体热载体R10KS进入一级热解反应过程R10与第一碳氢粉料R10FS混合接触。本发明,通常,(3)在返料器KF,使用气提气KFV,气提气KFV与短循环分离固体SRS-S物料接触,气提气KFV可以选自下列中的一种或几种:①煤气脱碳过程得到的高纯度二氧化碳气体;②水蒸气;③氮气;④净化煤气;⑤合成气;⑥来自二级热解反应过程R20的煤气。本发明,通常,(2)短循环气固分离过程SRS,布置在沉降器R20E的外部和或沉降器R20E的内部:(4)在二级热解反应过程R20,二级热解反应器R20E也是沉降器。本发明,通常,(2)短循环气固分离过程SRS,使用的分离方式,可以选自下列方式中的一种或几种:①离心分离过程;②惯性分离过程;③沉降分离过程。本发明,通常,(3)返料器KF,布置在沉降器R20E的外部和或沉降器R20E的内部;(4)在二级热解反应过程R20,二级热解反应器R20E同时也是沉降器R20E。本发明,通常,(3)返料器KF,使用的返料方式,可以选自下列方式中的一种或几种:①常规返料器;②罐式返料器;③气提气的罐式返料器;④罐式返料器,使用气提气浮选筛分小颗粒进入固体料SRS-SP,使短循环固体SRS-SR颗粒平均直径大于固体料SRS-SP颗粒平均直径;⑤槽式返料器;⑥气提气的槽式返料器;⑦槽式返料器,使用气提气浮选筛分小颗粒进入固体料SRS-SP,使短循环固体SRS-SR颗粒平均直径大于固体料SRS-SP颗粒平均直径。本发明,通常,(3)返料器KF,为布置在沉降器R20E内部的槽式返料器;(4)在二级热解反应过程R20,使用沉降器R20E。本发明,通常,(3)返料器KF,为布置在沉降器R20E内部的槽式返料器;(4)二级热解反应过程R20使用沉降器R20E,沉降器R20E上部有稀相床空间R20EU、下部有密相床空间R20ED,沉降器R20E中部可能布置有折流挡板R20E-TYAY用于分散向下流动的固体物料;返料器KF,在沉降器R20E的内部的布置位置可以选自下列中的一种或几种:①沉降器R20E上部的位置,位于稀相床内;②沉降器R20E中部的位置,存在的有折流挡板R20E-TYAY的同高度段位置;③沉降器R20E下部的密相床层浅度位置;④沉降器R20E底部的密相床层。本发明,通常,热解过程使用的固体热载体,为经过脱氧气步骤后所得脱气后固体热载体。本发明,一级热解反应过程R10操作温度通常为,(1)在一级热解反应过程R10,第一固体热载体LR-DS的温度为500~750℃,短循环固体SRS-SR的温度为450~600℃。本发明,一级热解反应过程R10操作温度一般为,(1)在一级热解反应过程R10,第一固体热载体LR-DS的温度为550~700℃,短循环固体SRS-SR的温度为500~580℃。本发明,通常,(4)在二级热解反应过程R20,使用二级热解反应器R20E即沉降器R20E;在沉降器R20E底部,引入置换气V22V用于气提置换下行半焦中携带的焦油蒸汽,置换气V22V可以选自下列物料中的一种或几种:①水蒸气;②氮气;③二氧化碳气;④无氧烟道气;⑤煤气;⑥其它不含对热解过程带来不利影响的组分的气体。本发明,第一碳氢粉料R10FS的粒径:通常为0~10毫米、一般为0~6毫米、宜为0~2毫米,第一碳氢粉料R10FS可以选自下列物料中的一种或几种:①低变质粉煤;②高变质粉煤;③油母页岩粉;④油砂;⑤煤直接液化残渣液体冷却固化后制备的固体颗粒,或煤直接液化残渣液体与固体混合后冷却固化后制备的固体颗粒;⑥煤沥青液体冷却固化后制备的固体颗粒,或煤沥青液体与固体混合后冷却固化后制备的固体颗粒;⑦高软化点稠油冷却固化后制备的固体颗粒,或高软化点稠油与固体混合后冷却固化后制备的固体颗粒;⑧其它在热解过程能够产生含油蒸汽的固体粉料。本发明,通常包括以下步骤:(1)在一级热解反应过程R10,第一碳氢粉料R10FS进行一级热解反应R10R转化为气固混相的一级热解反应产物R10P;在一级热解反应过程R10,使用提升管流化床式一级热解反应器R10E,R10E至少使用三路固体进料:第一碳氢粉料R10FS、第一固体热载体LR-DS、短循环固体料SR-DS;一级热解反应器R10E,下部注入第一碳氢粉料R10FS、第一固体热载体LR-DS,中部注入短循环固体料SR-DS,短循环固体料SR-DS进入一级热解反应器R10E的位置,将一级热解反应器R10E分为R10E的下段R10E-D和R10E的上段R10E-U:①下段R10E-D,是第一碳氢粉料R10FS的一级热解反应过程R10R的第一热解段或预热段,进行一级第一热解反应R10E-DR,为上段R10E-U提供温度合适的固体进料;在下段R10E-D,第一碳氢粉料R10FS、第一固体热载体LR-DS进入反应器R10E的下部混合,在气体进料R10FV作用下通过下段R10E-D向上流动进行一级第一热解反应R10E-DR转化为下段R10E-D顶部的气固产物R10E-D-P;②上段R10E-U,是第一碳氢粉料R10FS的一级热解反应过程R10R的第二热解段或适温热阶段,第一碳氢粉料R10FS在上段R10E-U的热解煤气和热解焦油的总产量大于在下段R10E-D的热解煤气和热解焦油的总产量;上段R10E-U空间分为2区,下区为急冷区、上区为适温热解区;上段R10E-U的急冷区,是下段R10E-D的气固产物R10E-D-P的急冷区,也是短循环固体料SR-DS的快速吸热段,通过急速降温,抑制热解焦油的再次热裂解反应和再次热缩合反应,急冷区同时进行着热解反应;上段R10E-U的适温热解区,是急冷流出物的流态化深度热解区;在上段R10E-U的下区,加入的短循环固体料SR-DS与来自下段R10E-D的气固产物R10E-D-P混合,在气体作用下通过上段R10E-U向上流动进行一级第二热解反应R10E-UR转化为上段R10E-U顶部的气固产物R10E-U-P;气固产物R10E-U-P,用作一级热解反应器R10E的最终产物R10P;(2)在短循环气固分离过程SRS,使用旋风分离器,一级热解反应产物R10P分离为短循环分离气体SRS-V和短循环分离固体SRS-S;(3)在返料器KF,短循环分离固体SRS-S分流为短循环固体SRS-SR和固体料SRS-SP;(4)在二级热解反应过程R20,固体料SRS-SP进行二级热解反应R20R转化为二级热解反应产物R20P并分离为含尘二级热解过程气R20EPV和二级热解半焦R20PS;二级热解半焦R20PS排出二级热解反应过程R20;(5)在气固分离过程S20,使用旋风分离器,离开固体粉料主体床层后的含尘二级热解过程气R20EPV分离为排出气固分离过程S20的脱尘二级热解煤气R20PV和半焦S20PS;(6)在流化烧焦反应过程R50,基于二级热解半焦R20PS的最终热解半焦RCPS进入流化烧焦反应空间,与含氧气体接触,进行流化床烧焦反应R50R,产生高温氧化半焦R50PS和烟气YQ,烟气YQ排出流化烧焦反应过程R50;高温半焦排出流化烧焦反应过程R50;含尘烟气的气固分离过程S50,使用旋风分离器;第一高温半焦R50P1S排出流化烧焦反应过程R50;(7)基于R50排出的第一高温半焦R50P1S的物流,用作第一固体热载体R10KS进入一级热解反应过程R10与第一碳氢粉料R10FS混合接触。本发明,通常,(1)在一级热解反应过程R10,气体进料R10FV提供流化动力,一级热解反应过程R10的至少大部分吸热量由第一固体热载体R10KS提供;(2)短循环气固分离过程SRS,使用旋风分离器,布置于二级热解反应过程R20使用的沉降器R20E内;(3)返料器KF,使用槽式返料器,布置于二级热解反应过程R20使用的沉降器R20E内;(4)在二级热解反应过程R20,使用的沉降器R20E,固体料SRS-SP进行二级热解反应R20R转化为二级热解反应产物R20P并分离为含尘二级热解过程气R20EPV和二级热解半焦R20PS;二级热解半焦R20PS排出二级热解反应过程R20;(5)在气固分离过程S20,使用旋风分离器,离开固体粉料主体床层后的含尘二级热解过程气R20EPV,通过气固分离系统S20分离为脱尘二级热解煤气R20PV和半焦S20PS,脱尘二级热解煤气R20PV进入脱尘气体S20PV中,半焦S20PS进入二级热解反应过程R20的沉降器R20E内。本发明,通常,(4)在二级热解反应过程R20,固体料SRS-SP进入二级热解反应过程R20的反应空间,主体流向是自上而下流动,进行第二热解反应R20R产生二级热解煤气和二级解热解半焦,并完成气固分离。本发明,通常,(4)在二级热解反应过程R20,固体料SRS-SP进入二级热解反应过程R20的反应空间,主体流向是自上而下流动,进行第二热解反应R20R产生二级热解煤气和二级解热解半焦,并完成气固分离;至少一部分二级热解反应过程R20的气固流动状态表现为散式流化床。本发明,通常,(1)在一级热解反应过程R10,气体进料R10FV提供流化动力,一级热解反应过程R10的至少大部分吸热量由第一固体热载体R10KS提供;(2)短循环气固分离过程SRS,使用的旋风分离器布置于二级热解反应过程R20使用的沉降器R20E内,一级热解反应产物R10P分离为短循环分离气体SRS-V和短循环分离固体SRS-S;(3)返料器KF,使用槽式返料器,布置于二级热解反应过程R20使用的沉降器R20E内;(4)在二级热解反应过程R20,使用的沉降器R20E,固体料SRS-SP进行二级热解反应R20R转化为二级热解反应产物R20P并分离为含尘二级热解过程气R20EPV和二级热解半焦R20PS;二级热解半焦R20PS排出二级热解反应过程R20;(5)在气固分离过程S20,使用旋风分离器,离开固体粉料主体床层后的含尘二级热解过程气R20EPV,通过气固分离系统S20分离为脱尘二级热解煤气R20PV和半焦S20PS,脱尘二级热解煤气R20PV进入脱尘气体S20PV中,半焦S20PS进入二级热解反应过程R20的沉降器R20E内;气固分离过程S20,同时对短循环分离气体SRS-V进行气固分离。本发明,通常,(6)在流化烧焦反应过程R50,基于二级热解半焦R20PS的最终热解半焦RCPS进入流化烧焦反应空间,与含氧气体接触,发生流化床烧焦反应R50R,产生高温半焦R50PS和烟气YQ,烟气YQ自上部空间排出流化烧焦反应过程R50;高温半焦R50PS排出流化烧焦反应过程R50。本发明,通常,(6)在流化烧焦反应过程R50,流化烧焦反应空间的上部稀相段的器内含尘烟气R50E-YQ,经过布置于流化烧焦反应器内部的上部空间的旋风分离系统S50脱尘分离为烟气YQ和半焦粉尘R50-RS;烟气YQ自上部空间离开旋风分离系统S50排出流化烧焦反应过程R50。本发明,通常,(6)在流化烧焦反应过程R50,流化烧焦反应空间的上部稀相段的器内含尘烟气R50E-YQ,经过布置于流化烧焦反应器内部的上部空间的旋风分离系统S50脱尘分离为烟气YQ和半焦粉尘R50-RS;旋风分离系统S5的旋风分离器料腿排出的半焦粉尘R50-RS返回流化烧焦反应空间循环加工。本发明,通常,(6)在流化烧焦反应过程R50,设置外取热器R50-OUT-HX,排出流化烧焦反应过程R50的热半焦进入外取热器R50-OUT-HX与取热介质间接换热降低温度后,排出外取热器R50-OUT-HX,在取热器R50-OUT-HX完成冷却步骤XH。本发明,通常,(6)在流化烧焦反应过程R50,设置外取热器R50-OUT-HX,来自流化烧焦反应过程R50的热半焦进入外取热器R50-OUT-HX与取热介质间接换热降低温度,排出外取热器R50-OUT-HX的至少一部分热半焦返回流化烧焦反应过程R50循环使用,剩余部分热半焦用作热产品R50PS-T,在取热器R50-OUT-HX完成冷却步骤XH。本发明,通常,(6)在流化烧焦反应过程R50,设置外取热器R50-OUT-HX,来自流化烧焦反应过程R50的热半焦进入外取热器R50-OUT-HX与取热介质间接换热降低温度,排出外取热器R50-OUT-HX的第一部分热半焦返回流化烧焦反应过程R50循环使用,第二部分冷却后用作产品R50PS-C,在取热器R50-OUT-HX完成冷却步骤XH。本发明热解目标,通常为,(1)在一级热解反应过程R10,第一碳氢粉料R10FS的粒径为0~6毫米,第一碳氢粉料R10FS选自煤直接液化残渣液体冷却固化后制备的固体颗粒或煤直接液化残渣液体与固体混合后冷却固化后制备的固体颗粒;(4)二级热解反应过程R20产生的焦油蒸汽重量为第一碳氢粉料R10FS重量的1~12%;二级热解反应过程R20的粉焦R20PS挥发分为3~25%;一级热解反应过程R10的焦油产量为R10PY、二级热解反应过程R20的焦油产量为R20PY与,定义KR=R20PY/(R10PY+R20PY),KR为0.03~0.50。本发明热解目标,一般为,(1)在一级热解反应过程R10,第一碳氢粉料R10FS的粒径为0~6毫米,第一碳氢粉料R10FS选自煤直接液化残渣液体冷却固化后制备的固体颗粒或煤直接液化残渣液体与固体混合后冷却固化后制备的固体颗粒;(4)二级热解反应过程R20产生的焦油蒸汽重量为第一碳氢粉料R10FS重量的1~7%;二级热解反应过程R20的粉焦R20PS挥发分为3~15%;KR为0.05~0.30。本发明主要步骤的操作条件通常为:(1)在一级热解反应过程R10,第一碳氢粉料R10FS选自煤直接液化残渣液体冷却固化后制备的固体颗粒或煤直接液化残渣液体与固体混合后冷却固化后制备的固体颗粒;一级热解反应过程R10,使用提升管流化床热解反应器,第一固体热载体R10KS为来自流化烧焦反应过程R50的高温氧化半焦,温度为600~750℃;一级热解反应过程R10的操作条件为:总体反应时间0.1~60s、第一热解段反应时间比率为2~25%,提升管反应产物出口温度即一级热解反应过程终端反应温度为450~630℃;第一固体热载体LR-DS的温度为600~750℃;短循环固体SRS-SR的温度为450~630℃;第一固体热载体R10KS的重量与第一碳氢粉料R10FS重量比值为1~22;短循环固体SRS-SR的重量与第一碳氢粉料R10FS重量比值为1~22;(4)在二级热解反应过程R20的反应空间,设置2~12副人字挡板或环形挡板,二级热解反应过程的主热解段的温度为500~700℃;二级热解段底部通入450~700℃气提气V22V进行焦油蒸汽汽提,气提气V22V通过半焦料层后向上流动并进入二级热解反应过程R20的二级热解煤气产物中;(5)在气固分离过程S20,使用旋风分离器,离开固体粉料主体床层后的含尘二级热解过程气R20EPV,通过气固分离系统S20分离为脱尘二级热解煤气R20PV和半焦S20PS,半焦S20PS进入二级热解反应过程R20的沉降器R20E内;气固分离过程S20,同时对短循环分离气体SRS-V进行气固分离;脱尘二级热解煤气R20PV中固体含量低于50克/立方米。本发明主要步骤的操作条件一般为:(1)在一级热解反应过程R10,第一碳氢粉料R10FS选自煤直接液化残渣液体冷却固化后制备的固体颗粒或煤直接液化残渣液体与固体混合后冷却固化后制备的固体颗粒;一级热解反应过程R10,使用提升管流化床热解反应器,第一固体热载体R10KS为来自流化烧焦反应过程R50的高温氧化半焦,温度为630~720℃;一级热解反应过程R10的操作条件为:总体反应时间2.0~30s、第一热解段反应时间比率为2~25%,提升管反应产物出口温度即一级热解反应过程终端反应温度为470~600℃;第一固体热载体LR-DS的温度为630~720℃;短循环固体SRS-SR的温度为470~600℃;第一固体热载体R10KS的重量与第一碳氢粉料R10FS重量比值为3~15;短循环固体SRS-SR的重量与第一碳氢粉料R10FS重量比值为3~15;(4)在二级热解反应过程R20的反应空间,设置2~12副人字挡板或环形挡板,二级热解反应过程的主热解段的温度为500~650℃;二级热解段底部通入450~650℃气提气V22V进行焦油蒸汽汽提,气提气V22V通过半焦料层后向上流动并进入二级热解反应过程R20的二级热解煤气产物中;(5)在气固分离过程S20,使用旋风分离器,离开固体粉料主体床层后的含尘二级热解过程气R20EPV,通过气固分离系统S20分离为脱尘二级热解煤气R20PV和半焦S20PS,半焦S20PS进入二级热解反应过程R20的沉降器R20E内;气固分离过程S20,同时对短循环分离气体SRS-V进行气固分离;脱尘二级热解煤气R20PV中固体含量低于10克/立方米。本发明主要步骤的操作条件宜为:(1)在一级热解反应过程R10,第一碳氢粉料R10FS选自煤直接液化残渣液体冷却固化后制备的固体颗粒或煤直接液化残渣液体与固体混合后冷却固化后制备的固体颗粒;一级热解反应过程R10,使用提升管流化床热解反应器,第一固体热载体R10KS为来自流化烧焦反应过程R50的高温氧化半焦,温度为650~700℃;一级热解反应过程R10的操作条件为:总体反应时间2.0~10s、第一热解段反应时间比率为2~25%,提升管反应产物出口温度即一级热解反应过程终端反应温度为500~580℃;第一固体热载体LR-DS的温度为650~700℃;短循环固体SRS-SR的温度为500~580℃;第一固体热载体R10KS的重量与第一碳氢粉料R10FS重量比值为6~10;短循环固体SRS-SR的重量与第一碳氢粉料R10FS重量比值为6~10;(4)在二级热解反应过程R20的反应空间,设置2~12副人字挡板或环形挡板,二级热解反应过程的主热解段的温度为550~650℃;二级热解段底部通入550~650℃气提气V22V进行焦油蒸汽汽提,气提气V22V通过半焦料层后向上流动并进入二级热解反应过程R20的二级热解煤气产物中;(5)在气固分离过程S20,使用旋风分离器,离开固体粉料主体床层后的含尘二级热解过程气R20EPV,通过气固分离系统S20分离为脱尘二级热解煤气R20PV和半焦S20PS,半焦S20PS进入二级热解反应过程R20的沉降器R20E内;气固分离过程S20,同时对短循环分离气体SRS-V进行气固分离;脱尘二级热解煤气R20PV中固体含量低于4克/立方米。本发明,短循环气固分离过程SRS使用的旋风分离器与返料器KF,可以组成组合设备。本发明,一级热解反应过程R10使用的提升管流化床热解反应器R10E,与短循环气固分离过程SRS使用的旋风分离器、返料器KF,可以组成组合设备。本发明,短循环气固分离过程SRS使用的旋风分离器、返料器KF使用的槽式返料器,与二级热解反应过程R20使用的二级流化床热解反应器R20E,可以组成组合设备。本发明,一级热解反应过程R10使用的提升管流化床热解反应器R10E,短循环气固分离过程SRS使用的旋风分离器、返料器KF使用的槽式返料器,与二级热解反应过程R20使用的二级流化床热解反应器R20E,可以组成组合设备。本发明,二级热解反应过程R20使用的二级流化床热解反应器R20E,与流化烧焦反应过程R50使用的流化床烧焦反应过程R50E,可以组成组合设备。本发明,一级热解反应过程R10使用的提升管流化床热解反应器R10E、流化烧焦反应过程R50使用的流化床烧焦反应过程R50E,可以组成组合设备。本发明,一级热解反应过程R10使用的提升管流化床热解反应器R10E、短循环气固分离过程SRS使用的旋风分离器、返料器KF使用的槽式返料器、二级热解反应过程R20使用的二级流化床热解反应器R20E、流化烧焦反应过程R50使用的流化床烧焦反应过程R50E,可以组成组合设备。本发明,二级热解反应过程R20使用的二级流化床热解反应器R20E,流化烧焦反应过程R50使用的流化床烧焦反应过程R50E均为立式设备,从空间位置标高讲,其相互位置关系可以是:流化床烧焦反应器R50E的底部比二级热解器R20E的底部更低,二级热解器R20E排出的最终热解半焦依靠料位差流入流化床烧焦反应器R50E的底部。本发明,二级热解反应过程R20使用的二级流化床热解反应器R20E,与流化烧焦反应过程R50使用的流化床烧焦反应过程R50E可以组成同轴式组合设备;同轴式指的是,二级热解反应器R20E、流化床烧焦反应器R50E为同轴式立式组合设备,从空间位置关系讲,其相互位置关系是:流化床烧焦反应器R50E的空间部分地包围着二级热解器R20E的空间;来自二级热解器R20E的底部空间的热解半焦通过立管和塞阀流入流化床烧焦反应器R50E的下部空间。本发明,各步骤操作压力为:(1)一级热解反应过程R10的操作压力为:0.1~6.0MPa,以绝对压力计;(4)在二级热解反应过程R20的操作压力为:0.1~6.0MPa,以绝对压力计;(6)在流化烧焦反应过程R50的操作压力为:0.1~6.0MPa,以绝对压力计。本发明,(1)在一级热解反应过程R10,使用提升管流化床式一级热解反应器R10E,R10E还可以加工第二碳氢粉料R10FS-X;第二碳氢粉料R10FS-X的来源不同于第一碳氢粉料R10FS的来源。本发明,(1)在一级热解反应过程R10,使用提升管流化床式一级热解反应器R10E,R10E还可以加工第二碳氢粉料R10FS-X;第二碳氢粉料R10FS-X,与第一碳氢粉料R10FS混合后加入一级热解反应器R10E。本发明,(1)在一级热解反应过程R10,使用提升管流化床式一级热解反应器R10E,R10E还可以加工第二碳氢粉料R10FS-X;第二碳氢粉料R10FS-X加入一级热解反应器R10E的方式,可以选自下列方式中的一种或几种:①第二碳氢粉料R10FS-X与第一碳氢粉料R10FS混合后一并加入一级热解反应器R10E;②第二碳氢粉料R10FS-X加入一级热解反应器R10E的下段R10E-D;③第二碳氢粉料R10FS-X与短循环固体料SR-DS混合后一并加入一级热解反应器R10E;④第二碳氢粉料R10FS-X加入一级热解反应器R10E的上段R10E-U。本发明,(1)在一级热解反应过程R10,使用提升管流化床式一级热解反应器R10E,R10E还加工第二碳氢粉料R10FS-X;第一碳氢粉料R10FS,为煤直接液化残渣液体冷却固化后制备的固体颗粒或煤直接液化残渣液体与固体混合后冷却固化后制备的固体颗粒;第二碳氢粉料R10FS-X,为粉煤。本发明,(3)在返料器KF,短循环分离固体SRS-S分为短循环固体SRS-SR和固体料SRS-SP;在返料器KF中,可以实现大粒径、小粒径固体颗粒的分离,分出较小粒径颗粒进入沉降器及烧焦反应器,选出较大粒径固体颗粒用作短循环固体料。本发明,(3)在返料器KF,短循环分离固体SRS-S分为短循环固体SRS-SR和固体料SRS-SP;在返料器KF中,可以实现大粒径、小粒径固体颗粒的分离,分出较小粒径颗粒进入沉降器及烧焦反应器,选出较大粒径固体颗粒用作短循环固体料;对于循环固体料中的小颗粒,在气固分离过程或沉降器或烧焦器排出热解烧焦系统。本发明,(1)在一级热解反应过程R10,使用提升管流化床式一级热解反应器R10E,第一碳氢粉料R10FS,为煤直接液化残渣液体冷却固化后制备的固体颗粒或煤直接液化残渣液体与固体混合后冷却固化后制备的固体颗粒;为了降低进入热解过程的固体热载体中细颗粒热载体的数量,可以使用外部引入的大颗粒固体形成循环固体热载体的主体,沉降过程或烧焦过程采用分类排焦优先排出小颗粒氧化半焦产品而不作为固体热载体循环使用。附图说明图1是本发明用双循环粉料的快速预热串联适温热解式碳氢料热解方法的第1种流程的功能及短循环步骤设备功能示意图。图1是一种使用固体热载体的煤直接液化残液的固化粉料流化床热解、流化床烧焦系统的流程图,同时是一种残液固化料提升管流化床热解、热解半焦流化烧焦、固体热载体循环的固体物料循环路径的流体力学状态示意图,用于表示残液固化料热解烧焦过程中各流程位置的功能。按照本发明,液态的煤加氢直接液化残液AR10P-VS冷却降温至软化点比如100~150℃以下即可成为固体,可采用类似于煤沥青冷却造粒成型的方法,比如煤加氢直接液化残液AR10P-VS经过布料器或分布器或喷料嘴分布后,经过有效的冷却过程比如水冷和或风冷过程降低温度至20~80℃即可成型为块料或粒料AR10P-VS-A1S。按照本发明,将块料或粒料AR10P-VS-A1S粉碎为小颗粒料AR10P-VS-LS,粉碎方式可以是任一种合适的方法比如碾压粉碎、在水中碾压粉碎然后脱水成为干品,干品经过筛分将粒径大于规定上限的颗粒返回粉碎过程重复加工;成品小颗粒料AR10P-VS-LS的粒径通常为0~6毫米、一般为0~2毫米、较佳者为0~0.2毫米、特别地为0~0.02毫米,粒径越小,其热解过程所需的时间越短,但是煤气中携带的细粉颗粒数量会增加,这要求使用能够完成高效脱除小颗粒的深度气固分离系统如使用多管式带带导流叶片的高离心力旋风管气固分离器。为了在进入流化热解过程之前,增加液态的煤加氢直接液化残液AR10P-VS的分散度,增加其在热解反应器中的停留时间和热解速度,可以将残液AR10P-VS与固体颗粒ZS如半焦颗粒混合得到混合物AR10P-VS-ZS,固体颗粒ZS的粒径通常为0~6毫米、一般为0~2毫米、较佳者为0~0.2毫米、特别地为0~0.02毫米;混合得到混合物AR10P-VS-ZS的过程,可以是任意一种合适的方法,比如可以是用泵循环并通过管道系统设置的混合器混合,比如可以使用固体与浆料混捏机混合。混合物AR10P-VS-ZS冷却所得固体AR10P-VS-ZS-S,指的是混合物AR10P-VS-ZS冷却降温至软化点比如100~150℃以下即可成为固体,可采用类似于煤沥青冷却造粒成型的方法,比如混合物AR10P-VS-ZS经过布料器或分布器或喷料嘴分布后,经过有效的冷却过程比如水冷和或风冷过程降低温度至20~80℃即可成型为块料或粒料AR10P-VS-ZS-S。按照本发明,将固体R10P-VS-ZS-S粉碎为小颗粒AR10P-VS-ZS-LS,粉碎方式可以是任一种合适的方法比如碾压粉碎、在水中碾压粉碎然后脱水成为干品,干品经过筛分将粒径大于规定上限的颗粒返回粉碎过程重复加工;成品小颗粒AR10P-VS-ZS-LS的粒径通常为0~6毫米、一般为0~2毫米、较佳者为0~0.2毫米、特别地为0~0.02毫米,粒径越小,其热解过程所需的时间越短,但是煤气中携带的细粉颗粒数量会增加,这要求使用能够完成高效脱除小颗粒的深度气固分离系统如使用多管式带带导流叶片的高离心力旋风管气固分离器。按照本发明,在使用固体热载体的流化床提升管热解反应过程R10,将残液AR10P-VS的固化颗粒小颗粒料AR10P-VS-LS和或小颗粒AR10P-VS-ZS-LS转化为热解煤气和热解固体,热解反应过程R10的热解操作温度通常为380~700℃、一般为400~600℃、宜为450~550℃,热解反应过程R10的热解反应末端操作温度通常为450~620℃、一般为510~600℃、宜为540~580℃。如图1所示的残液固化料提升管流化床热解流化床烧焦系统,包括残液固化料提升管流化床热解反应器、沉降器即第二热解反应器、热解半焦的流化床烧焦反应器,其中沉降器的上部空间布置有分离煤气和半焦的旋风分离器,其中流化床烧焦反应器的上部空间布置有分离烟气和半焦的旋风分离器。与常规的使用固体热载体的碳氢粉料的流化床热解、流化床烧焦系统的流程不同,图1流程包含分离出短循环固体的气固分离器、分配或控制短循环固体流量甚至粒度和沉降器固体进料流量甚至粒度的返料器或物料分配器。与常规的使用固体热载体的粉煤流化床热解方式不同,图1所示残液固化料提升管流化床热解反应器的固体进料有三路:残液固化料、第一固体热载体、短循环固体,短循环固体进入残液固化料提升管流化床热解反应器的位置,将残液固化料提升管流化床热解反应器分为两段空间:①下段R10E-D,是第一碳氢粉料R10FS的一级热解反应过程R10R的第一热解段或预热段,进行一级第一热解反应R10E-DR,为上段R10E-U提供温度合适的固体进料;在下段R10E-D,第一碳氢粉料R10FS、第一固体热载体LR-DS进入反应器R10E的下部混合,在气体进料R10FV作用下通过下段R10E-D向上流动进行一级第一热解反应R10E-DR转化为下段R10E-D顶部的气固产物R10E-D-P;一段即下段,是残液固化料预热段,本质上是为第二段即主体热解段的准备性能合适的固体进料的一个预备阶段;预热段,通常进行着初期热解反应;残液固化料预热段是第一固体热载体与残液固化料的快速混合的残液固化料预热段,也是第一固体热载体的快速预冷段;目的在于使残液固化料快速吸热升温,缩短其跨越软化温度点至结焦温度点这一温距的时间,降低残液固化料表面可能出现的液体形成固体颗粒粘结的概率或降低粘结物产量,同时较高的操作温度适应离解能高的双键或芳环π键的热解所必须的输入性能量级,总体目标是快速热解残液固化料中的有机质中的双键或芳环π键,产生热解焦油、热解煤气、及热半焦;预热段流出物,可以是残液固化料完成快速预热任务、但是尚未充分进行热解反应的物料,此种工况预热段的残液固化料的热解率很低比如低于15%;预热段流出物,可以是残液固化料完成快速预热任务、并进行适度热解反应的物料,此种工况预热段的残液固化料的热解率较高,比如可达30~60%;②上段R10E-U,是第一碳氢粉料R10FS的一级热解反应过程R10R的第二热解段或适温热阶段;上段R10E-U空间分为2区,下区为急冷区、上区为适温热解区;上段R10E-U的急冷区,是下段R10E-D的气固产物R10E-D-P的急冷区,也是短循环固体料SR-DS的快速吸热段,通过急速降温,抑制热解焦油的再次热裂解反应和再次热缩合反应,急冷区同时进行着热解反应;上段R10E-U的适温热解区,是急冷流出物的流态化深度热解区;在上段R10E-U的下区,加入的短循环固体料SR-DS与来自下段R10E-D的气固产物R10E-D-P混合,在气体作用下通过上段R10E-U向上流动进行一级第二热解反应R10E-UR转化为上段R10E-U顶部的气固产物R10E-U-P;气固产物R10E-U-P,用作一级热解反应器R10E的最终产物R10P;二段即上段,通常是残液固化料的主热解段,残液固化料在第二段的热解煤气和热解焦油总量的比例大于在第一段的热解煤气和热解焦油总量的比例,主热解段指的是残液固化料在第二段的停留时间长于在第一段的停留时间预热段,残液固化料在第二段的热解反应比例大于在第一段的热解反应比例;上段即主热解段,分为2区,二段下区为急冷区、二段上区为适温热解区:①急冷区,是预热段流出物被短循环固体快速混合的急冷区,也是短循环固体的快速吸热区;急冷区,同时进行着热解反应;由于急速降温,抑制了热解焦油的再次热裂解反应、热缩合反应,利于提高热解焦油保留率;②适温热解区,是急冷区流出物的流态化深度热解区,在此区中,固-固、气-气、气-固之间快速混合、传热,热解固体进行吸热性热解反应,气体进行吸热性热解反应,也发生放热性的热缩合反应比如结焦反应;完成预期热解反应的物料作为热解反应产物排出提升管反应器上部的排料口。如图1所示,热解反应产物进入短循环气固分离过程,短循环气固分离过程可以是任意一种合适的气固分离过程,可以是快速惯性分离过程或利用离心分离原理工作的分离过程,可以是沉降分离过程,可以使用旋风分离器或罐式分离器或槽式分离器,图1示出的是使用旋风分离器的方案。如图1所示,短循环气固分离过程分离出短循环分离气体和短循环分离固体。短循环分离气体SRS-V,自短循环气固分离器SRS的上部中心排气管管口排出SRS。短循环分离固体SRS-S,自短循环气固分离器SRS的下部排固管排出SRS,进入返料器或物料分配器KF,KF用于分配或控制短循环固体SRS-SR和沉降器固体进料SRS-SP流量。如图1所示,返料器或物料分配器KF可以是任意一种合适结构形式的返料器或物料分配器,比如可以是类似于粉煤汽化过程、粉煤流化床燃烧过程使用的循环半焦、循环灰使用的返料器或物料分配器,记载此类设备的文献见:①出版物名称:《燃烧技术手册》,644页至649页;②检索用图书编码:ISBN编码:978-7-122-01321-7,中国版本图书馆CIP数据核字(2007)第157254号;③编著:徐旭常、周力行主编;④出版社:化学工业出版社。返料器KF通常使用流化风或松动风或助推风KF-FV,KF-FV可以是任意一种温度、压力、组分组成等合适的气体,通常为水蒸气或氮气或二氧化碳气或不含氧气烟道气或净化脱油后的煤气或煤制合成气或半焦制合成气。如图1所示,返料器或物料分配器KF将固体SRS-S分离为返回提升管热解反应器中部位置的短循环固体SRS-SR和沉降器固体进料SRS-SP。从固体物料循环路径的流体力学状态方面讲,图1所示流程的功能安排是:常规的“上行(残液固化料一级热解提升管反应器)、水平流动(残液固化料一级热解反应产物气固分离)、下行(一级热解半焦在短循环气固分离器SRS的旋风分离器料腿内、短循环固体SRS-SR返回提升管热解反应器中部、SRS-SP进入沉降器固体、残液固化料二级热解反应空间)、热解半焦固体输送、流化床烧焦、固体热载体输送”,共同组成0形回路。如图1所示,与常规的使用固体热载体的粉煤流化床热解方式不同,残液固化料提升管流化床热解反应器的循环固体进料有2路:长循环固体料即第一固体热载体、短循环固体料。图2是图1所示本发明用双循环粉料的快速预热串联适温热解式碳氢料热解方法的流程的设备功能示意详图,其中沉降器R20E与烧焦器R50E为高低并列式,用于表示残液固化料热解烧焦过程中设备的结构。图2是高低并列式残液固化料热解烧焦系统;高低并列式指的是,沉降器R20E、流化床烧焦反应器R50E均为立式设备,从空间位置标高讲,其相互位置关系是:流化床烧焦反应器R50E的底部比沉降器R20E的底部更低,沉降器R20E排出的最终热解半焦可依靠料位差自流进入流化床烧焦反应器R50E的底部。沉降器R20E,因为具有一定热解功能,也可称为二级热解反应器。如图2所示,R10E为提升管式一级热解反应器,提升气R10FV经管道P101进入布置于R10E底部的分配器R10FV-SB分配后向上流动,残液固化料FM(即R10FS)经管道P102、第一固体热载体半焦R10KS经管道P103进入R10E底部混合区R10E-1在提升气R10FV作用下形成流化床沿着提升管向上移动,期间发生残液固化料第一热解反应R10R;传热途径有热载体半焦→残液固化料、高温残液固化料→低温残液固化料、热载体半焦→气体、高温气体→低温气体、高温气体→残液固化料,高频次的混合、分离形成快速传热效应,在升温过程中残液固化料进行一级热解反应;完成第一热解反应的物料作为第一热解反应流出物R10P自顶部开口R10E-OUT排出R10E,R10P是由包含焦油组分的煤气、热解半焦组成的气固混相物流。如图2所示,残液固化料提升管流化床热解反应器R10E的固体进料有三路:残液固化料、第一固体热载体、短循环固体,短循环固体进入残液固化料提升管流化床热解反应器R10E的中部位置,将残液固化料提升管流化床热解反应器分为两段空间:一段即下段是残液固化料预热段,二段即上段是残液固化料的主热解段。主热解段,分为2区,二段下区为急冷区、二段上区为适温热解区。如图2所示,一级热解反应流出物R10P经管P105进入图2示出的是使用旋风分离器的短循环气固分离过程SRS。如图2所示,短循环气固分离过程SRS分离出经管道P901输送的短循环分离气体SRS-V和经管道P905输送的短循环分离固体SRS-S。短循环分离固体SRS-S,自短循环气固分离器SRS的下部排固管P905排出SRS,进入返料器或物料分配器KF,分流或分离为经管道P915输送的返回提升管热解反应器中部位置的短循环固体SRS-SR和经管道P921输送的沉降器固体进料SRS-SP。如图2所示,沉降器固体进料SRS-SP经管P921进入沉降器R20E,沉降器R20E的上部空间布置有分离煤气和半焦的旋风分离器系统S20,包括粗旋S201,粗旋S201完成一级气固分离。如图2所示,分离段S20为沉降器固体进料SRS-SP的气固分离系统,布置于沉降器R20E内部空间的顶部位置。图3是图2中的气固分离系统S20的三级串联分离流程详图,粗旋S201为一级分离,一级主旋S202为二级分离,二级主旋S203为三级分离。图4是图3中的气固分离系统S20的粗旋S201的进料管、进料间隙式通道连接方式示意详图。如图4所示,粗旋S201进口气体输送管道与粗旋的气体进料口之间存在周隙,用作接收沉降器R20E的含尘煤气的进料口。如图4所示,在分离段S20中,含粉尘的短循环分离气体SRS-V沿管P901喷入软连接的粗旋S201的进料管P905,图4表示了一种软连接方式,进料管P905的头部是一个扩径的喇叭口敞口P9051,管P901的头部P9011是一个同径延伸管敞口P9011,P9011伸入到喇叭口P9051的空间内,粗旋S201入口气体输送管道与粗旋S201的气体进料管口之间存在周隙。如图3所示,二级热解反应器顶部的气体经开口进入粗旋S201,粗旋S201完成一级气固分离,粗旋粉料沿料腿P206下降进入沉降器R20E内部空间并通常流入密相床区域以防止粉尘过度飞扬;含粉尘的粗旋煤气沿管P207进入一级主旋S202的进料管P208,一级主旋S202完成二级气固分离,一级主旋粉料沿料腿P209下降进入沉降器R20E内部空间并通常流入稀相床区域;含少量粉尘的一级主旋煤气沿管P211进入直接连接的二级主旋S203,二级主旋S203完成三级气固分离,二级主旋粉料沿料腿P212下降进入沉降器R20E内部空间并通常流入稀相床区域;脱尘二级主旋煤气S20PV沿管P927排出系统S20。如图2所示,R20E为二级热解反应器,R20E的内部空间,按照工艺功能至少包括设置旋风分离系统的顶部空间V21、沉降器固体进料SRS-SP的沉降脱气空间或二级热解反应空间V22。通常希望二级热解反应空间呈现散式流化床形态,此时,上部为稀相空间V21、下部为密相空间V22,密相空间V22底部通常有气提气体V22V向上流动。如图2所示,系统S20的料腿中的粉焦依靠重力进入二级热解反应过程R20,即旋风分离器料腿中的粉焦依靠重力进入二级热解反应器R20E的空间。如图2所示,进入沉降器R20E反应空间V22的沉降器固体进料SRS-SP,产生主体流向为自上而下的流动并被挡板多次改变流向,挡板的结构形式有多种比如设置多块人字挡板、多块环形板等,在上述过程中沉降器固体进料SRS-SP进行第二热解反应R20R;完成二级热解反应的物料分为下行的二级热解半焦R20EPS和二级热解含尘煤气R20EPV,脱气后二级热解半焦R20PS自沉降器R20E反应空间的底部经管道P302、阀门、管道P502排出,二级热解半焦R20PS最终可以去流化床烧焦反应器R50E或冷却后储存。如图2所示,流化床烧焦系统R50使用的流化床烧焦反应器R50E内布置有顶部烟气旋风分离系统S50、底部密相床烧焦区V52。如图2所示,分离段S50为烟气的二级气固分离系统,布置于烧焦器R50E内部空间的顶部位置,烟气进入二级旋风S501完成一级气固分离,一旋粉料沿料腿P562下降进入烧焦器R50E内部空间并可流入稀相床区域或密相床;含粉尘的一旋烟气沿管P561进入二级旋风S502完成二级气固分离,二旋粉料沿料腿P508下降进入烧焦器R50E内部空间并可流入密相床或稀相床,脱尘二旋烟气作为脱尘烟气YQ沿管P507排出系统R50E。如图2所示,在流化床烧焦反应器R50E,来自沉降器R20E的最终热解半焦如二级热解半焦R20PS,经过管道P302、阀门、管道P502后进入烧焦反应器R50E的烧焦段密相床V52中,含氧气提升气R50-ZF进入布置于密相床V52底部的分布器V50-SB分布后向上流动,形成半焦流化床燃烧,燃烧生成的烟气沿着流化床烧焦反应器R50E内的空间V52、V51向上移动并夹带半焦粉尘。如图2,流化床烧焦反应器R50E的烧焦段的器内烧焦烟气V50EPV,其气固分离过程S50布置于流化床烧焦反应器R50E内部空间的顶部位置,由1级旋风分离器或串联操作的2级或多级旋风分离器组成,图中示出的是2级旋风分离器串联操作的方案。气固分离过程S50,分离粉焦后所得脱尘烟气YQ经管道P507排出流化床烧焦反应器R50E并去压力能回收和或热量回收和或粉尘深度分离系统处理,通常处理后烟气YQ排入大气或部分循环利用;气固分离过程S50,分离器料腿中的粉焦R50-KR依靠重力返回流化床烧焦反应器R50E内。如图2所示,通过管道P503、滑阀和管道P103输送的氧化半焦,作为第一固体热载体R10KS进入一级热解反应器R10E。根据需要,其它热半焦通过管道P505、滑阀和管道P506输送,排出流化床烧焦反应器R50E,可以换热冷却后储存或直接用于燃过程烧或直接用于气化过程等。如图2所示,二段分离煤气S20PV通过管道P927进入后续分离回收系统S30。如图2所示的流化床烧焦反应器R50E,其器内顶部空间可以布置间接换热器R50E-HX,用以加热气相或液相或混相取热物流如循环水、待过热水蒸气、煤气物流等。图2中,气体分布器R10FV-SB或V22V-SB或V50-SB或R10FV-2SB等,可为任意合适的形式,比如可为一个开有多个小孔的顶盖的喷头或为一个开有多个小孔的环形分布管或为一个开有多个小孔的顶盖的喷气室。如图2所示,二级热解含尘煤气R20EPV进入气固分离过程S20进行气固分离,二级热解含尘煤气R20EPV离开二级热解反应空间进入系统S10的主旋进行气固分离。如图2所示,450~650℃气提气V22V沿管道P2201进入V22内布置的分配器V22V-SB分配后进入二级热解反应空间V22底部,气提气通过半焦料层后气提并携带焦油蒸汽向上流动并最终进入二级热解反应过程R20的二级热解煤气产物中。图5是本发明用双循环粉料的快速预热串联适温热解式碳氢料热解方法的第2种流程功能及短循环步骤设备功能示意图,与图1所示是本发明的第1种流程的不同之处在于:返料器KF为罐式设备,且短循环气固分离器布置在罐式返料器KF内部的顶部空间中,罐式返料器KF因为具有较大空间所以可以提供更大的缓冲空间,具有较长的停留时间,可以设置气体脱油气步骤,充分回收单程热解煤气产物。如图5所示,热解产物R10P经管道P105进入罐式返料器KF内部的顶部空间布置的旋风分离器SRS中,分离出经管道P901输送的短循环分离气体SRS-V和经管道P905输送的短循环分离固体SRS-S。如图5所示,短循环分离固体SRS-S,自短循环气固分离器SRS的下部排固管P905排出SRS,进入罐式返料器或物料分配器KF的下部的密相床中,分离为经管道P915输送的返回提升管热解反应器中部位置的短循环固体SRS-SR和经管道P921输送的沉降器固体进料SRS-SP。如图5所示,罐式返料器KF,通常使用经管道P910输送的经过分布器KFV-SB输入的气提气KFV或松动风,KFV可以是任意一种温度、压力、组分组成等合适的气体,通常为水蒸气或氮气或二氧化碳气或不含氧气烟道气或净化脱油后的煤气或煤制合成气或半焦制合成气。如图5所示,罐式返料器KF内的气体KF-G经管道P925输送进入沉降器R20E的上部的气相空间。图6是本发明用双循环粉料的快速预热串联适温热解式碳氢料热解方法的第3种流程功能及短循环步骤设备功能示意图,与图2所示是本发明的第2种流程的不同之处在于:罐式返料器KF的下部布置贯通式隔板PL910,将罐式返料器KF的下部空间分割为两个密相床空间KFA、KFB;KFA为固体进料区,在底部使用经管道PA910输送的经过分布器KFAV-SB输入的气提气KFAV或松动风或浮选风,将短循环分离固体SRS-S中的预期下限粒径D0以下的颗粒吹出,并经过隔板PL910溢流进入分流区KFB;分流区KFB也是沉降器固体进料SRS-SP的缓冲空间,通常,在底部使用经管道PB910输送的经过分布器KFBV-SB输入的气提气KFBV或松动风或浮选风。如图6所示,热解产物R10P经管道P105进入罐式返料器KF内部的顶部空间布置的旋风分离器SRS中,分离出经管道P901输送的短循环分离气体SRS-V和经管道P905输送的短循环分离固体SRS-S。如图6所示,短循环分离固体SRS-S,自短循环气固分离器SRS的下部排固管P905排出SRS,进入罐式返料器或物料分配器KF的下部的密相床KFA中,分离为经管道P915输送的返回提升管热解反应器中部位置的短循环固体SRS-SR和经过隔板PL910溢流进入分流区KFB的溢流料;分流区KFB排出的沉降器固体进料SRS-SP经过管道P921进入沉降器R20E。如图6所示,罐式返料器KF内的两个密相床空间KFA、KFB排出的上行气体,混合为气体KF-G经管道P925输送进入沉降器R20E的上部的气相空间。图1、图5、图6示出的流程中,短循环步骤设备均布置在沉降器R20E外部独立布置,其缺点在于高温设备数量多、占地面积大,其保温系统复杂。为了简化流程,减少高温设备数量多、减少占地面积、简化保温系统,提出了将短循环步骤设备均布置在沉降器R20E内部的方案,短循环步骤设备与沉降器R20E构成组合设备的4种方案分别见图7、图10、图11、图12。图7是本发明用双循环粉料的快速预热串联适温热解式碳氢料热解方法的第4种流程功能及短循环步骤设备功能示意图,与图1所示是本发明的第1种流程的不同之处在于:将短循环步骤设备布置在沉降器R20E内部,短循环步骤设备与沉降器R20E构成组合设备并布置于沉降器R20E的上部空间。如图7所示,一级热解反应器顶部的产物R10P经管道P105进入短循环气固分离器SRS即粗旋SZ201,粗旋SZ201完成一级气固分离,粗旋粉料沿料腿P905下降进入沉降器R20E内部的上部空间布置的返料器KF。如图7所示,返料器KF为由底板KF-PD、侧板KF-PS、R20E器壁构成的上部开口的槽式容器;返料器KF的下部设置输料管道P915,返料器KF的下部设置管道P910输送的经过分布器KFV-SB输入的气提气KFV或松动风或浮选风。如图7所示,槽式返料器KF将短循环分离固体SRS-S中的预期下限粒径D0以下的颗粒吹出,并经过隔板KF-PS溢流、导流板KF-PP下滑导流进入R20E的气提沉降区V22布置的人字挡板区域;槽式返料器KF也是沉降器固体进料SRS-SP的缓冲空间。如图7所示,热解产物R10P经管道P105进入沉降器R20E内部的顶部空间布置的旋风分离器SRS中,分离出经管道P901输送的短循环分离气体SRS-V和经管道P905输送的短循环分离固体SRS-S。如图7所示,短循环分离固体SRS-S,自短循环气固分离器SRS的下部排固管P905排出SRS,进入槽式返料器或物料分配器KF的下部的密相床中,分离为经管道P915输送的返回提升管热解反应器R10E中部位置的短循环固体SRS-SR和经过隔板KF-PS溢流进入R20E的气提沉降区V22的溢流料;分流区KFB排出的沉降器固体进料SRS-SP经过管道P921进入沉降器R20E。如图7所示,槽式返料器或物料分配器KF内的密相床空间排出的上行气体KF-G,混入沉降器R20E的顶部空间的气体中,并经过气固分离系统S20中的间隙流道进入气固分离系统S20进行分离。图8是图7中的气固分离系统S20的三级串联分离流程详图,粗旋SZ201为一级分离,一级主旋SZ202为二级分离,二级主旋SZ203为三级分离。图9是图8中的气固分离系统S20的一级主旋SZ202的进料管、进料间隙式通道连接方式示意详图。如图9所示,一级主旋SZ202进口气体输送管道与粗旋的气体进料口之间存在周隙,用作接收沉降器R20E的含尘煤气的进料口。如图9所示,在分离段S20中,含粉尘的短循环分离气体SRS-V沿管P901喷入软连接的一级主旋SZ202的进料管PZ208,图9表示了一种软连接方式,进料管PZ208的头部是一个扩径的喇叭口敞口PZ2081,管P901的头部是一个同径延伸管敞口P9011,P9011伸入到喇叭口PZ2081的空间内,一级主旋SZ202入口气体输送管道与气体进料管口P9011之间存在周隙。如图8所示,一级热解反应器顶部的产物R10P经管道P105进入短循环气固分离器SRS即粗旋SZ201,粗旋SZ201完成一级气固分离,粗旋粉料沿料腿P905下降进入沉降器R20E内部的上部空间布置的返料器KF的内部空间并通常流入密相床区域以防止粉尘过度飞扬;含粉尘的粗旋煤气沿管P901进入一级主旋SZ202的进料管PZ208,一级主旋SZ202完成二级气固分离,一级主旋粉料沿料腿PZ209下降进入沉降器R20E内部空间并通常流入稀相床区域;含少量粉尘的一级主旋煤气沿管PZ211进入直接连接的二级主旋SZ203,二级主旋SZ203完成三级气固分离,二级主旋粉料沿料腿PZ212下降进入沉降器R20E内部空间并通常流入稀相床区域;脱尘二级主旋煤气S20PV沿管P927排出系统S20。图7所示方案,槽式返料器KF的底部标高较高,可以适应短循环固体SRS-SR返回提升管热解反应器的返料口位置标高较高的情况,特别适合于沉降器单独布置的情况。图10是本发明用双循环粉料的快速预热串联适温热解式碳氢料热解方法的第5种流程功能及短循环步骤设备功能示意图,与图9所示是本发明的第4种流程的不同之处在于:在沉降器R20E内部,将槽式返料器KF将布置于沉降器R20E的中部空间。与图9所示本发明的第4种流程相比,图10所示方案的槽式返料器KF的底部标高有所降低但是槽式返料器KF容积便于扩大,适合于沉降器布置标高较高的情况,比如特别适合于沉降器布置在烧焦器R50E的上部形成同轴式布置方案的情况。图11是本发明用双循环粉料的快速预热串联适温热解式碳氢料热解方法的第6种流程功能及短循环步骤设备功能示意图,与图10所示是本发明的第5种流程的不同之处在于:在沉降器R20E内部,将槽式返料器KF将布置于沉降器R20E的底部空间。与图10所示本发明的第5种流程相比,图11所示方案的槽式返料器KF的底部标高更低但是槽式返料器KF容积便于扩大,适合于沉降器布置标高较高的情况,或者需要配套合适的输料方式。图12是本发明用双循环粉料的快速预热串联适温热解式碳氢料热解方法的第7种流程功能及短循环步骤设备功能示意图,与图11所示是本发明的第6种流程的不同之处在于:在沉降器R20E内部,将布置于沉降器R20E的底部空间的槽式返料器KF,用隔板KF-PS将沉降器R20E的底部空间分割为两个密相床空间KFA、KFB;KFA为固体进料和流化浮选区,在底部使用经管道PA910输送的经过分布器KFAV-SB输入的气提气KFAV或松动风或浮选风,将预期下限粒径D0以下的颗粒吹出,并经过隔板KF-PS溢流进入分流区KFB;分流区KFB,是烧焦器进料的脱焦油气、煤气的气提空间和缓冲空间,通常,在底部使用经管道P2201输送的经过分布器V22V-SB输入的气提气V22V或松动风或浮选风。如图12所示,短循环分离固体SRS-S流经沉降器的几乎大部空间,但是不会进入烧焦器R50E。如图12所示,沉降器R20E的底部空间的两个密相床空间KFA、KFB排出的上行气体,充当沉降器R20E的下行固体料的气提气,并最后经过沉降器R20E顶部的气固分离系统S20脱尘后排出。如图12所示,密相床空间KFB的顶部,用导流挡板PX将下行的固体料导入密相床空间KFA,防止下行的固体料直接进入密相床空间KFB的空间。根据需要,物料管道上布置控制流量的阀门或等效功能的控制器。根据需要,固体物料管道上布置辅助流动的松动风。本发明各具体技术方案的系统中包含了以下2个粉料循环系统:①第一固体热载体的长循环流程,第一固体热载体的循环过程经过的设备包括提升管热解反应器、短循环气固分离器SRS、返料器或物料分配器KF、沉降器、流化床烧焦反应器;②短循环固体料的短循环流程,短循环固体的循环过程经过的设备包括提升管热解反应器、短循环气固分离器SRS、返料器或物料分配器KF。具体实施方式以下详细描述本发明。本发明所述的压力,指的是绝对压力。本发明所述的常规沸点指的是物质在一个大气压力下的汽、液平衡温度。本发明所述的常规沸程指的是馏分的常规沸点范围。本发明所述的比重,除非特别说明,指的是常压、15.6℃条件下液体密度与常压、15.6℃条件下水密度的比值。本发明所述的组分的组成或浓度或含量或收率值,除非特别说明,均为重量基准值。本发明所述的常规气体烃,指的是常规条件下呈气态的烃类,包括甲烷、乙烷、丙烷、丁烷。本发明所述的常规液体烃,指的是常规条件下呈液态的烃类,包括戊烷及其沸点更高的烃类。本发明所述的杂质元素,指的是原料油中的非氢、非碳、非金属组分如氧、硫、氮、氯等。本发明所述的杂质组分,指的是原料油中非烃组分的加氢转化物如水、氨、硫化氢、氯化氢等。本发明所述的轻质烃,为石脑油组分,指的是常规沸点低于200℃的常规液体烃。本发明所述的中质烃,为柴油组分,指的是常规沸点为200~330℃的烃类。本发明所述的蜡油组分指的是常规沸点为330~530℃的烃类。本发明所述的重质烃,指的是常规沸点高于330℃的烃类。以下描述煤直接液化过程。本发明所述煤直接液化过程,指的是在溶剂油存在条件下通过加氢使煤液化的方法,根据溶剂油和催化剂的不同、热解方式和加氢方式的不同以及工艺条件的不同,可以分为以下几种工艺:①溶解热解液化法:利用重质溶剂对煤热解抽提可制得低灰分的抽提物(日本称膨润炭);利用轻质溶剂在超临界条件下抽提可得到以重质油为主的油类。此法不用氢气,前一种工艺产率虽高但产品仍为固体,后一种工艺如超临界抽提(萃取)法(SCE)抽提率不太高;②溶剂加氢抽提液化法:如有溶剂精炼煤法1和II(SRC-1和SRC-II),供氢溶剂法EDS、日本新能源开发机构液化法(NEDOL)等,使用氢气,但压力不太高,溶剂油有明显的作用;③高压催化加氢法:如德国的新老液化工艺(IG和NewlG)和美国的氢煤法(H-Coal)等都属于这一类;④煤和渣油联合加工法(CO·processing):以渣油为溶剂油与煤一起一次通过反应器,不用循环油。渣油同时发生加氢裂解转化为轻质油。美国、加拿大、德国和前苏联等各有不同的工艺;⑤干馏液化法:煤先热解得到焦油,然后对焦油进行加氢裂解和提质;⑥地下液化法:将溶剂注入地下煤层,使煤解聚和溶解,加上流体的冲击力使煤崩散,未完全溶解的煤则悬浮于溶剂中,用泵将溶液抽出并分离加工。煤直接液化方法中,多数属于煤加氢直接液化制油过程,无论何种煤临氢直接液化过程,其目标均是获得油品,追求的功能均是“煤转油”,必须存在的化学变化是“煤加氢”,目前此类技术的共同特征是使用溶剂油和催化剂,溶剂油的常规沸程一般为200~450℃、多数为200~400℃,溶剂油多数为蒸馏油,所含芳烃多数为2~4个环结构的芳烃。因此,无论是何种煤临氢直接液化过程,它产生的外排油或煤液化油(通常为煤液化轻油)或煤液化油改性油,只要其组成具备本发明所述原料组成特点,均可以使用本发明方法进行加工。专利CN100547055C载明的一种用褐煤制取液体燃料的热溶催化法属于褐煤中压加氢直接液化过程,包括煤液化反应过程和煤液化油加氢改性过程共两个过程。为了提高煤炭直接液化的转化率和实现煤炭原料进入煤液化反应器,煤炭进入煤液化反应器前通常制成煤粉,与具备良好供氢能力的溶剂油配成油煤浆,油煤浆经加压、加热后进入煤液化反应器。本发明所述煤液化反应过程,指的是以煤炭和可能存在的分子氢气为原料,以特定的油品(通常为煤液化油的加氢改性油)为供氢溶剂油,在一定的操作条件(如操作温度、操作压力、溶剂油/煤重量比、氢气/溶剂油体积比和合适加氢催化剂)下,煤炭直接发生碳碳键热裂化、加氢液化的反应过程。本发明所述煤液化油,指的是所述煤液化反应过程产生的油品,它存在于煤加氢液化反应流出物中,是基于供氢溶剂油、反应消耗煤炭和反应转移氢的综合反应产物。在煤液化反应过程运转正常后,供氢溶剂油通常采用煤液化反应过程自产的煤液化油(通常为常规沸程高于165℃的馏分油)的加氢改性油,煤液化油加氢改性过程的主要目标是生产煤液化反应过程用溶剂油,具体而言就是提高油品中“具有良好供氢功能的组分”的含量,比如提高环烷基苯类、二环烷基苯类组分的含量,基于煤液化油含有大量双环芳烃和大量三环芳烃这一事实,煤液化油加氢改性过程是一个“适度芳烃饱和”的加氢过程。煤液化反应过程的最终目标是生产外供的油品,通常煤液化油加氢改性过程产生的加氢改性油分为两部分:一部分用作煤液化反应过程用供氢溶剂油,一部分用作煤液化制油过程外排油。通常,煤液化反应过程产生的至少一部分煤液化轻油用作煤制油过程外排油A,其余的煤液化油用作煤液化油加氢改性过程原料油生产煤液化反应过程用供氢溶剂油和外排油B,此时存在A和B两路外排油,A和B两路外排油的最终去向通常均是经过深度加氢提质过程生产优质油品比如柴油馏分、石脑油馏分。以下描述碳氢料的热解或干馏过程。本发明所述含碳氢元素的粉料,指的是在本发明所述热解反应过程可以产生含油蒸汽的含有碳元素、氢元素的粉料,比如挥发分含量高的低变质煤粉。现代化大型煤矿比如低变质煤矿通常采用机械化综采技术以提高采煤效率、降低成本,其煤炭采出品中的粉煤产率约为60~70%,成为主体产品,因此粉煤的深度转化和综合利用技术必将占据现代低变质煤炭利用技术的主体地位,粉煤加工的一个分支领域是“粉煤分质分级利用”,其中粉煤热解被视为有经济竞争力的技术途径。本发明所述粉煤FM即R10FS,通常为干燥后脱水粉煤,其水分重量通常低于10%、一般低于7%、较佳者低于5%。本发明所述粉煤FM即R10FS,其粒度通常为0.00001~6毫米、一般为0.0001~3.5毫米、较佳者为0.001~2毫米。本发明所述粉煤热解过程,指的是以多产煤焦油为工艺目标的在适宜的温度范围内操作的粉煤热解过程。粉煤热解过程的主要产品是焦油、煤气、半焦,其中焦油被认为是潜在经济价值最大的产品,通常期望提高其产率和或氢含量。粉煤热解商业化技术的主要目标是:提高粉煤高价值组分提取率(或提高粉煤高价值产品收率)、提高单套装置加工量、降低单位能耗、提高技术的可靠性和可控性;因此,只有在上述一个或几个目标上取得显著突破,才能支撑工业技术的经济性,并最终成为主流的粉煤热解商业化技术。目前为止,多个工业国或大型商业公司对粉煤热解技术进行了研究开发,已经提出多种工艺如德国L-R工艺即鲁奇-鲁尔工艺、美国Toscoal工艺、美国COED工艺,但是尚无大型商业化装置的成功案例。以下描述煤焦油和煤焦油加氢过程。本发明所述煤焦油,指的是来自煤热解或煤焦化或煤干馏或煤造气过程的热解步骤等过程的煤焦油或其馏分,可以是煤造气的副产物低温煤焦油或其馏分,也可以是煤炼焦煤热解过程(包括低温炼焦、中温炼焦、高温炼焦过程)副产物煤焦油或其馏分,本发明所述煤焦油还可以是上述煤焦油的混合油。本发明所述煤焦油,包括低温焦油、中温焦油、高温焦油、不同煤焦油的混合油、煤焦油的馏分油。高温炼焦属于煤高温热解过程,热解过程的最终温度一般大于900℃,通常在1000~1400℃之间。所述高温煤焦油指的是煤高温热解制取焦炭和/或城市煤气过程生产的副产物粗焦油。高温煤焦油在初级蒸馏过程,通常生产以下产品:轻油(拔顶焦油)、酚油、萘油、轻质洗油、重质洗油、轻质蒽油、重质蒽油、沥青等产品,酚油可进一步分离为粗酚和脱酚油,萘油可进一步分离为粗萘和脱萘油。本发明所述高温煤焦油轻馏分指的是:蒽油、洗油、萘油、脱萘油、酚油、脱酚油、轻油及其混合油。由于原煤性质和炼焦或造气工艺条件均在一定范围内变化,煤焦油的性质也在一定范围内变化。煤焦油初级蒸馏过程的工艺条件和产品要求也在一定范围内变化,故煤焦油轻馏分的性质也在一定范围内变化。煤焦油轻馏分的性质,比重通常为0.92~1.25,常规沸点一般为60~500℃通常为120~460℃,通常金属含量为5~80PPm、硫含量为0.4~0.8%、氮含量为0.6~1.4%、氧含量为0.4~9.0%,通常水含量为0.2~5.0%,残炭含量通常为0.5~13%。煤液化加氢过产物的分馏过程,通常得到液化残渣。煤焦油减压蒸馏过程,通常得到煤沥青。全馏分煤焦油悬浮床加氢过程的加氢生成油的减压蒸馏过程,通常得到含固油渣。以下描述本发明的特征部分。本发明用双循环粉料的快速预热串联适温热解式碳氢料热解方法,其特征在于包含以下步骤:(1)在一级热解反应过程R10,第一碳氢粉料R10FS进行一级热解反应R10R转化为气固混相的一级热解反应产物R10P;在一级热解反应过程R10,使用提升管流化床式一级热解反应器R10E,R10E至少使用三路固体进料:第一碳氢粉料R10FS、第一固体热载体LR-DS、短循环固体料SR-DS;一级热解反应器R10E,下部注入第一碳氢粉料R10FS、第一固体热载体LR-DS,中部注入短循环固体料SR-DS,短循环固体料SR-DS进入一级热解反应器R10E的位置,将一级热解反应器R10E分为R10E的下段R10E-D和R10E的上段R10E-U:①下段R10E-D,是第一碳氢粉料R10FS的一级热解反应过程R10R的第一热解段或预热段,进行一级第一热解反应R10E-DR,为上段R10E-U提供温度合适的固体进料;在下段R10E-D,第一碳氢粉料R10FS、第一固体热载体LR-DS进入反应器R10E的下部混合,在气体进料R10FV作用下通过下段R10E-D向上流动进行一级第一热解反应R10E-DR转化为下段R10E-D顶部的气固产物R10E-D-P;②上段R10E-U,是第一碳氢粉料R10FS的一级热解反应过程R10R的第二热解段或适温热阶段;上段R10E-U空间分为2区,下区为急冷区、上区为适温热解区;上段R10E-U的急冷区,是下段R10E-D的气固产物R10E-D-P的急冷区,也是短循环固体料SR-DS的快速吸热段,通过急速降温,抑制热解焦油的再次热裂解反应和再次热缩合反应,急冷区同时进行着热解反应;上段R10E-U的适温热解区,是急冷流出物的流态化深度热解区;在上段R10E-U的下区,加入的短循环固体料SR-DS与来自下段R10E-D的气固产物R10E-D-P混合,在气体作用下通过上段R10E-U向上流动进行一级第二热解反应R10E-UR转化为上段R10E-U顶部的气固产物R10E-U-P;气固产物R10E-U-P,用作一级热解反应器R10E的最终产物R10P;(2)在短循环气固分离过程SRS,一级热解反应产物R10P分离为短循环分离气体SRS-V和短循环分离固体SRS-S;(3)在返料器KF,短循环分离固体SRS-S分为短循环固体SRS-SR和固体料SRS-SP。本发明,通常,(1)在一级热解反应过程R10,第一碳氢粉料R10FS在上段R10E-U的热解煤气和热解焦油的总产量大于在下段R10E-D的热解煤气和热解焦油的总产量。本发明,通常,(1)在一级热解反应过程R10,第一碳氢粉料R10FS在上段R10E-U的热解煤气和热解焦油的总产量大于在下段R10E-D的热解煤气和热解焦油的总产量;(4)在二级热解反应过程R20,固体料SRS-SP进行二级热解反应R20R转化为二级热解反应产物R20P并分离为含尘二级热解过程气R20EPV和二级热解半焦R20PS;二级热解半焦R20PS排出二级热解反应过程R20;(5)在气固分离过程S20,离开固体粉料主体床层后的含尘二级热解过程气R20EPV分离为排出气固分离过程S20的脱尘二级热解煤气R20PV和半焦S20PS;(6)在流化烧焦反应过程R50,基于二级热解半焦R20PS的最终热解半焦RCPS进入流化烧焦反应空间,与含氧气体接触,进行流化床烧焦反应R50R,产生高温氧化半焦R50PS和烟气YQ,烟气YQ排出流化烧焦反应过程R50;高温半焦排出流化烧焦反应过程R50。本发明,通常,(7)基于R50排出的第一高温半焦R50P1S的物流,用作第一固体热载体R10KS进入一级热解反应过程R10与第一碳氢粉料R10FS混合接触。本发明,通常,(3)在返料器KF,使用气提气KFV,气提气KFV与短循环分离固体SRS-S物料接触,气提气KFV可以选自下列中的一种或几种:①煤气脱碳过程得到的高纯度二氧化碳气体;②水蒸气;③氮气;④净化煤气;⑤合成气;⑥来自二级热解反应过程R20的煤气。本发明,通常,(2)短循环气固分离过程SRS,布置在沉降器R20E的外部和或沉降器R20E的内部;(4)在二级热解反应过程R20,二级热解反应器R20E也是沉降器。本发明,通常,(2)短循环气固分离过程SRS,使用的分离方式,可以选自下列方式中的一种或几种:①离心分离过程;②惯性分离过程;③沉降分离过程。本发明,通常,(3)返料器KF,布置在沉降器R20E的外部和或沉降器R20E的内部;(4)在二级热解反应过程R20,二级热解反应器R20E同时也是沉降器R20E。本发明,通常,(3)返料器KF,使用的返料方式,可以选自下列方式中的一种或几种:①常规返料器;②罐式返料器;③气提气的罐式返料器;④罐式返料器,使用气提气浮选筛分小颗粒进入固体料SRS-SP,使短循环固体SRS-SR颗粒平均直径大于固体料SRS-SP颗粒平均直径;⑤槽式返料器;⑥气提气的槽式返料器;⑦槽式返料器,使用气提气浮选筛分小颗粒进入固体料SRS-SP,使短循环固体SRS-SR颗粒平均直径大于固体料SRS-SP颗粒平均直径。本发明,通常,(3)返料器KF,为布置在沉降器R20E内部的槽式返料器;(4)在二级热解反应过程R20,使用沉降器R20E。本发明,通常,(3)返料器KF,为布置在沉降器R20E内部的槽式返料器;(4)二级热解反应过程R20使用沉降器R20E,沉降器R20E上部有稀相床空间R20EU、下部有密相床空间R20ED,沉降器R20E中部可能布置有折流挡板R20E-TYAY用于分散向下流动的固体物料;返料器KF,在沉降器R20E的内部的布置位置可以选自下列中的一种或几种:①沉降器R20E上部的位置,位于稀相床内;②沉降器R20E中部的位置,存在的有折流挡板R20E-TYAY的同高度段位置;③沉降器R20E下部的密相床层浅度位置;④沉降器R20E底部的密相床层。本发明,通常,热解过程使用的固体热载体,为经过脱氧气步骤后所得脱气后固体热载体。本发明,一级热解反应过程R10操作温度通常为,(1)在一级热解反应过程R10,第一固体热载体LR-DS的温度为500~750℃,短循环固体SRS-SR的温度为450~600℃。本发明,一级热解反应过程R10操作温度一般为,(1)在一级热解反应过程R10,第一固体热载体LR-DS的温度为550~700℃,短循环固体SRS-SR的温度为500~580℃。本发明,通常,(4)在二级热解反应过程R20,使用二级热解反应器R20E即沉降器R20E;在沉降器R20E底部,引入置换气V22V用于气提置换下行半焦中携带的焦油蒸汽,置换气V22V可以选自下列物料中的一种或几种:①水蒸气;②氮气;③二氧化碳气;④无氧烟道气;⑤煤气;⑥其它不含对热解过程带来不利影响的组分的气体。本发明,第一碳氢粉料R10FS的粒径:通常为0~10毫米、一般为0~6毫米、宜为0~2毫米,第一碳氢粉料R10FS可以选自下列物料中的一种或几种:①低变质粉煤;②高变质粉煤;③油母页岩粉;④油砂;⑤煤直接液化残渣液体冷却固化后制备的固体颗粒,或煤直接液化残渣液体与固体混合后冷却固化后制备的固体颗粒;⑥煤沥青液体冷却固化后制备的固体颗粒,或煤沥青液体与固体混合后冷却固化后制备的固体颗粒;⑦高软化点稠油冷却固化后制备的固体颗粒,或高软化点稠油与固体混合后冷却固化后制备的固体颗粒;⑧其它在热解过程能够产生含油蒸汽的固体粉料。本发明,通常包括以下步骤:(1)在一级热解反应过程R10,第一碳氢粉料R10FS进行一级热解反应R10R转化为气固混相的一级热解反应产物R10P;在一级热解反应过程R10,使用提升管流化床式一级热解反应器R10E,R10E至少使用三路固体进料:第一碳氢粉料R10FS、第一固体热载体LR-DS、短循环固体料SR-DS;一级热解反应器R10E,下部注入第一碳氢粉料R10FS、第一固体热载体LR-DS,中部注入短循环固体料SR-DS,短循环固体料SR-DS进入一级热解反应器R10E的位置,将一级热解反应器R10E分为R10E的下段R10E-D和R10E的上段R10E-U:①下段R10E-D,是第一碳氢粉料R10FS的一级热解反应过程R10R的第一热解段或预热段,进行一级第一热解反应R10E-DR,为上段R10E-U提供温度合适的固体进料;在下段R10E-D,第一碳氢粉料R10FS、第一固体热载体LR-DS进入反应器R10E的下部混合,在气体进料R10FV作用下通过下段R10E-D向上流动进行一级第一热解反应R10E-DR转化为下段R10E-D顶部的气固产物R10E-D-P;②上段R10E-U,是第一碳氢粉料R10FS的一级热解反应过程R10R的第二热解段或适温热阶段,第一碳氢粉料R10FS在上段R10E-U的热解煤气和热解焦油的总产量大于在下段R10E-D的热解煤气和热解焦油的总产量;上段R10E-U空间分为2区,下区为急冷区、上区为适温热解区;上段R10E-U的急冷区,是下段R10E-D的气固产物R10E-D-P的急冷区,也是短循环固体料SR-DS的快速吸热段,通过急速降温,抑制热解焦油的再次热裂解反应和再次热缩合反应,急冷区同时进行着热解反应;上段R10E-U的适温热解区,是急冷流出物的流态化深度热解区;在上段R10E-U的下区,加入的短循环固体料SR-DS与来自下段R10E-D的气固产物R10E-D-P混合,在气体作用下通过上段R10E-U向上流动进行一级第二热解反应R10E-UR转化为上段R10E-U顶部的气固产物R10E-U-P;气固产物R10E-U-P,用作一级热解反应器R10E的最终产物R10P;(2)在短循环气固分离过程SRS,使用旋风分离器,一级热解反应产物R10P分离为短循环分离气体SRS-V和短循环分离固体SRS-S;(3)在返料器KF,短循环分离固体SRS-S分流为短循环固体SRS-SR和固体料SRS-SP;(4)在二级热解反应过程R20,固体料SRS-SP进行二级热解反应R20R转化为二级热解反应产物R20P并分离为含尘二级热解过程气R20EPV和二级热解半焦R20PS;二级热解半焦R20PS排出二级热解反应过程R20;(5)在气固分离过程S20,使用旋风分离器,离开固体粉料主体床层后的含尘二级热解过程气R20EPV分离为排出气固分离过程S20的脱尘二级热解煤气R20PV和半焦S20PS;(6)在流化烧焦反应过程R50,基于二级热解半焦R20PS的最终热解半焦RCPS进入流化烧焦反应空间,与含氧气体接触,进行流化床烧焦反应R50R,产生高温氧化半焦R50PS和烟气YQ,烟气YQ排出流化烧焦反应过程R50;高温半焦排出流化烧焦反应过程R50;含尘烟气的气固分离过程S50,使用旋风分离器;第一高温半焦R50P1S排出流化烧焦反应过程R50;(7)基于R50排出的第一高温半焦R50P1S的物流,用作第一固体热载体R10KS进入一级热解反应过程R10与第一碳氢粉料R10FS混合接触。本发明,通常,(1)在一级热解反应过程R10,气体进料R10FV提供流化动力,一级热解反应过程R10的至少大部分吸热量由第一固体热载体R10KS提供;(2)短循环气固分离过程SRS,使用旋风分离器,布置于二级热解反应过程R20使用的沉降器R20E内;(3)返料器KF,使用槽式返料器,布置于二级热解反应过程R20使用的沉降器R20E内;(4)在二级热解反应过程R20,使用的沉降器R20E,固体料SRS-SP进行二级热解反应R20R转化为二级热解反应产物R20P并分离为含尘二级热解过程气R20EPV和二级热解半焦R20PS;二级热解半焦R20PS排出二级热解反应过程R20;(5)在气固分离过程S20,使用旋风分离器,离开固体粉料主体床层后的含尘二级热解过程气R20EPV,通过气固分离系统S20分离为脱尘二级热解煤气R20PV和半焦S20PS,脱尘二级热解煤气R20PV进入脱尘气体S20PV中,半焦S20PS进入二级热解反应过程R20的沉降器R20E内。本发明,通常,(4)在二级热解反应过程R20,固体料SRS-SP进入二级热解反应过程R20的反应空间,主体流向是自上而下流动,进行第二热解反应R20R产生二级热解煤气和二级解热解半焦,并完成气固分离。本发明,通常,(4)在二级热解反应过程R20,固体料SRS-SP进入二级热解反应过程R20的反应空间,主体流向是自上而下流动,进行第二热解反应R20R产生二级热解煤气和二级解热解半焦,并完成气固分离;至少一部分二级热解反应过程R20的气固流动状态表现为散式流化床。本发明,通常,(1)在一级热解反应过程R10,气体进料R10FV提供流化动力,一级热解反应过程R10的至少大部分吸热量由第一固体热载体R10KS提供;(2)短循环气固分离过程SRS,使用的旋风分离器布置于二级热解反应过程R20使用的沉降器R20E内,一级热解反应产物R10P分离为短循环分离气体SRS-V和短循环分离固体SRS-S;(3)返料器KF,使用槽式返料器,布置于二级热解反应过程R20使用的沉降器R20E内;(4)在二级热解反应过程R20,使用的沉降器R20E,固体料SRS-SP进行二级热解反应R20R转化为二级热解反应产物R20P并分离为含尘二级热解过程气R20EPV和二级热解半焦R20PS;二级热解半焦R20PS排出二级热解反应过程R20;(5)在气固分离过程S20,使用旋风分离器,离开固体粉料主体床层后的含尘二级热解过程气R20EPV,通过气固分离系统S20分离为脱尘二级热解煤气R20PV和半焦S20PS,脱尘二级热解煤气R20PV进入脱尘气体S20PV中,半焦S20PS进入二级热解反应过程R20的沉降器R20E内;气固分离过程S20,同时对短循环分离气体SRS-V进行气固分离。本发明,通常,(6)在流化烧焦反应过程R50,基于二级热解半焦R20PS的最终热解半焦RCPS进入流化烧焦反应空间,与含氧气体接触,发生流化床烧焦反应R50R,产生高温半焦R50PS和烟气YQ,烟气YQ自上部空间排出流化烧焦反应过程R50;高温半焦R50PS排出流化烧焦反应过程R50。本发明,通常,(6)在流化烧焦反应过程R50,流化烧焦反应空间的上部稀相段的器内含尘烟气R50E-YQ,经过布置于流化烧焦反应器内部的上部空间的旋风分离系统S50脱尘分离为烟气YQ和半焦粉尘R50-RS;烟气YQ自上部空间离开旋风分离系统S50排出流化烧焦反应过程R50。本发明,通常,(6)在流化烧焦反应过程R50,流化烧焦反应空间的上部稀相段的器内含尘烟气R50E-YQ,经过布置于流化烧焦反应器内部的上部空间的旋风分离系统S50脱尘分离为烟气YQ和半焦粉尘R50-RS;旋风分离系统S5的旋风分离器料腿排出的半焦粉尘R50-RS返回流化烧焦反应空间循环加工。本发明,通常,(6)在流化烧焦反应过程R50,设置外取热器R50-OUT-HX,排出流化烧焦反应过程R50的热半焦进入外取热器R50-OUT-HX与取热介质间接换热降低温度后,排出外取热器R50-OUT-HX,在取热器R50-OUT-HX完成冷却步骤XH。本发明,通常,(6)在流化烧焦反应过程R50,设置外取热器R50-OUT-HX,来自流化烧焦反应过程R50的热半焦进入外取热器R50-OUT-HX与取热介质间接换热降低温度,排出外取热器R50-OUT-HX的至少一部分热半焦返回流化烧焦反应过程R50循环使用,剩余部分热半焦用作热产品R50PS-T,在取热器R50-OUT-HX完成冷却步骤XH。本发明,通常,(6)在流化烧焦反应过程R50,设置外取热器R50-OUT-HX,来自流化烧焦反应过程R50的热半焦进入外取热器R50-OUT-HX与取热介质间接换热降低温度,排出外取热器R50-OUT-HX的第一部分热半焦返回流化烧焦反应过程R50循环使用,第二部分冷却后用作产品R50PS-C,在取热器R50-OUT-HX完成冷却步骤XH。本发明热解目标,通常为,(1)在一级热解反应过程R10,第一碳氢粉料R10FS的粒径为0~6毫米,第一碳氢粉料R10FS选自煤直接液化残渣液体冷却固化后制备的固体颗粒或煤直接液化残渣液体与固体混合后冷却固化后制备的固体颗粒;(4)二级热解反应过程R20产生的焦油蒸汽重量为第一碳氢粉料R10FS重量的1~12%;二级热解反应过程R20的粉焦R20PS挥发分为3~25%;一级热解反应过程R10的焦油产量为R10PY、二级热解反应过程R20的焦油产量为R20PY与,定义KR=R20PY/(R10PY+R20PY),KR为0.03~0.50。本发明热解目标,一般为,(1)在一级热解反应过程R10,第一碳氢粉料R10FS的粒径为0~6毫米,第一碳氢粉料R10FS选自煤直接液化残渣液体冷却固化后制备的固体颗粒或煤直接液化残渣液体与固体混合后冷却固化后制备的固体颗粒;(4)二级热解反应过程R20产生的焦油蒸汽重量为第一碳氢粉料R10FS重量的1~7%;二级热解反应过程R20的粉焦R20PS挥发分为3~15%;KR为0.05~0.30。本发明主要步骤的操作条件通常为:(1)在一级热解反应过程R10,第一碳氢粉料R10FS选自煤直接液化残渣液体冷却固化后制备的固体颗粒或煤直接液化残渣液体与固体混合后冷却固化后制备的固体颗粒;一级热解反应过程R10,使用提升管流化床热解反应器,第一固体热载体R10KS为来自流化烧焦反应过程R50的高温氧化半焦,温度为600~750℃;一级热解反应过程R10的操作条件为:总体反应时间0.1~60s、第一热解段反应时间比率为2~25%,提升管反应产物出口温度即一级热解反应过程终端反应温度为450~630℃;第一固体热载体LR-DS的温度为600~750℃;短循环固体SRS-SR的温度为450~630℃;第一固体热载体R10KS的重量与第一碳氢粉料R10FS重量比值为1~22;短循环固体SRS-SR的重量与第一碳氢粉料R10FS重量比值为1~22;(4)在二级热解反应过程R20的反应空间,设置2~12副人字挡板或环形挡板,二级热解反应过程的主热解段的温度为500~700℃;二级热解段底部通入450~700℃气提气V22V进行焦油蒸汽汽提,气提气V22V通过半焦料层后向上流动并进入二级热解反应过程R20的二级热解煤气产物中;(5)在气固分离过程S20,使用旋风分离器,离开固体粉料主体床层后的含尘二级热解过程气R20EPV,通过气固分离系统S20分离为脱尘二级热解煤气R20PV和半焦S20PS,半焦S20PS进入二级热解反应过程R20的沉降器R20E内;气固分离过程S20,同时对短循环分离气体SRS-V进行气固分离;脱尘二级热解煤气R20PV中固体含量低于50克/立方米。本发明主要步骤的操作条件一般为:(1)在一级热解反应过程R10,第一碳氢粉料R10FS选自煤直接液化残渣液体冷却固化后制备的固体颗粒或煤直接液化残渣液体与固体混合后冷却固化后制备的固体颗粒;一级热解反应过程R10,使用提升管流化床热解反应器,第一固体热载体R10KS为来自流化烧焦反应过程R50的高温氧化半焦,温度为630~720℃;一级热解反应过程R10的操作条件为:总体反应时间2.0~30s、第一热解段反应时间比率为2~25%,提升管反应产物出口温度即一级热解反应过程终端反应温度为470~600℃;第一固体热载体LR-DS的温度为630~720℃;短循环固体SRS-SR的温度为470~600℃;第一固体热载体R10KS的重量与第一碳氢粉料R10FS重量比值为3~15;短循环固体SRS-SR的重量与第一碳氢粉料R10FS重量比值为3~15;(4)在二级热解反应过程R20的反应空间,设置2~12副人字挡板或环形挡板,二级热解反应过程的主热解段的温度为500~650℃;二级热解段底部通入450~650℃气提气V22V进行焦油蒸汽汽提,气提气V22V通过半焦料层后向上流动并进入二级热解反应过程R20的二级热解煤气产物中;(5)在气固分离过程S20,使用旋风分离器,离开固体粉料主体床层后的含尘二级热解过程气R20EPV,通过气固分离系统S20分离为脱尘二级热解煤气R20PV和半焦S20PS,半焦S20PS进入二级热解反应过程R20的沉降器R20E内;气固分离过程S20,同时对短循环分离气体SRS-V进行气固分离;脱尘二级热解煤气R20PV中固体含量低于10克/立方米。本发明主要步骤的操作条件宜为:(1)在一级热解反应过程R10,第一碳氢粉料R10FS选自煤直接液化残渣液体冷却固化后制备的固体颗粒或煤直接液化残渣液体与固体混合后冷却固化后制备的固体颗粒;一级热解反应过程R10,使用提升管流化床热解反应器,第一固体热载体R10KS为来自流化烧焦反应过程R50的高温氧化半焦,温度为650~700℃;一级热解反应过程R10的操作条件为:总体反应时间2.0~10s、第一热解段反应时间比率为2~25%,提升管反应产物出口温度即一级热解反应过程终端反应温度为500~580℃;第一固体热载体LR-DS的温度为650~700℃;短循环固体SRS-SR的温度为500~580℃;第一固体热载体R10KS的重量与第一碳氢粉料R10FS重量比值为6~10;短循环固体SRS-SR的重量与第一碳氢粉料R10FS重量比值为6~10;(4)在二级热解反应过程R20的反应空间,设置2~12副人字挡板或环形挡板,二级热解反应过程的主热解段的温度为550~650℃;二级热解段底部通入550~650℃气提气V22V进行焦油蒸汽汽提,气提气V22V通过半焦料层后向上流动并进入二级热解反应过程R20的二级热解煤气产物中;(5)在气固分离过程S20,使用旋风分离器,离开固体粉料主体床层后的含尘二级热解过程气R20EPV,通过气固分离系统S20分离为脱尘二级热解煤气R20PV和半焦S20PS,半焦S20PS进入二级热解反应过程R20的沉降器R20E内;气固分离过程S20,同时对短循环分离气体SRS-V进行气固分离;脱尘二级热解煤气R20PV中固体含量低于4克/立方米。本发明,短循环气固分离过程SRS使用的旋风分离器与返料器KF,可以组成组合设备。本发明,一级热解反应过程R10使用的提升管流化床热解反应器R10E,与短循环气固分离过程SRS使用的旋风分离器、返料器KF,可以组成组合设备。本发明,短循环气固分离过程SRS使用的旋风分离器、返料器KF使用的槽式返料器,与二级热解反应过程R20使用的二级流化床热解反应器R20E,可以组成组合设备。本发明,一级热解反应过程R10使用的提升管流化床热解反应器R10E,短循环气固分离过程SRS使用的旋风分离器、返料器KF使用的槽式返料器,与二级热解反应过程R20使用的二级流化床热解反应器R20E,可以组成组合设备。本发明,二级热解反应过程R20使用的二级流化床热解反应器R20E,与流化烧焦反应过程R50使用的流化床烧焦反应过程R50E,可以组成组合设备。本发明,一级热解反应过程R10使用的提升管流化床热解反应器R10E、流化烧焦反应过程R50使用的流化床烧焦反应过程R50E,可以组成组合设备。本发明,一级热解反应过程R10使用的提升管流化床热解反应器R10E、短循环气固分离过程SRS使用的旋风分离器、返料器KF使用的槽式返料器、二级热解反应过程R20使用的二级流化床热解反应器R20E、流化烧焦反应过程R50使用的流化床烧焦反应过程R50E,可以组成组合设备。本发明,二级热解反应过程R20使用的二级流化床热解反应器R20E,流化烧焦反应过程R50使用的流化床烧焦反应过程R50E均为立式设备,从空间位置标高讲,其相互位置关系可以是:流化床烧焦反应器R50E的底部比二级热解器R20E的底部更低,二级热解器R20E排出的最终热解半焦依靠料位差流入流化床烧焦反应器R50E的底部。本发明,二级热解反应过程R20使用的二级流化床热解反应器R20E,与流化烧焦反应过程R50使用的流化床烧焦反应过程R50E可以组成同轴式组合设备;同轴式指的是,二级热解反应器R20E、流化床烧焦反应器R50E为同轴式立式组合设备,从空间位置关系讲,其相互位置关系是:流化床烧焦反应器R50E的空间部分地包围着二级热解器R20E的空间;来自二级热解器R20E的底部空间的热解半焦通过立管和塞阀流入流化床烧焦反应器R50E的下部空间。本发明,各步骤操作压力为:(1)一级热解反应过程R10的操作压力为:0.1~6.0MPa,以绝对压力计;(4)在二级热解反应过程R20的操作压力为:0.1~6.0MPa,以绝对压力计;(6)在流化烧焦反应过程R50的操作压力为:0.1~6.0MPa,以绝对压力计。本发明,(1)在一级热解反应过程R10,使用提升管流化床式一级热解反应器R10E,R10E还可以加工第二碳氢粉料R10FS-X;第二碳氢粉料R10FS-X的来源不同于第一碳氢粉料R10FS的来源。本发明,(1)在一级热解反应过程R10,使用提升管流化床式一级热解反应器R10E,R10E还可以加工第二碳氢粉料R10FS-X;第二碳氢粉料R10FS-X,与第一碳氢粉料R10FS混合后加入一级热解反应器R10E。本发明,(1)在一级热解反应过程R10,使用提升管流化床式一级热解反应器R10E,R10E还可以加工第二碳氢粉料R10FS-X;第二碳氢粉料R10FS-X加入一级热解反应器R10E的方式,可以选自下列方式中的一种或几种:①第二碳氢粉料R10FS-X与第一碳氢粉料R10FS混合后一并加入一级热解反应器R10E;②第二碳氢粉料R10FS-X加入一级热解反应器R10E的下段R10E-D;③第二碳氢粉料R10FS-X与短循环固体料SR-DS混合后一并加入一级热解反应器R10E;④第二碳氢粉料R10FS-X加入一级热解反应器R10E的上段R10E-U。本发明,(1)在一级热解反应过程R10,使用提升管流化床式一级热解反应器R10E,R10E还加工第二碳氢粉料R10FS-X;第一碳氢粉料R10FS,为煤直接液化残渣液体冷却固化后制备的固体颗粒或煤直接液化残渣液体与固体混合后冷却固化后制备的固体颗粒;第二碳氢粉料R10FS-X,为粉煤。本发明,(3)在返料器KF,短循环分离固体SRS-S分为短循环固体SRS-SR和固体料SRS-SP;在返料器KF中,可以实现大粒径、小粒径固体颗粒的分离,分出较小粒径颗粒进入沉降器及烧焦反应器,选出较大粒径固体颗粒用作短循环固体料。本发明,(3)在返料器KF,短循环分离固体SRS-S分为短循环固体SRS-SR和固体料SRS-SP;在返料器KF中,可以实现大粒径、小粒径固体颗粒的分离,分出较小粒径颗粒进入沉降器及烧焦反应器,选出较大粒径固体颗粒用作短循环固体料;对于循环固体料中的小颗粒,在气固分离过程或沉降器或烧焦器排出热解烧焦系统。本发明,(1)在一级热解反应过程R10,使用提升管流化床式一级热解反应器R10E,第一碳氢粉料R10FS,为煤直接液化残渣液体冷却固化后制备的固体颗粒或煤直接液化残渣液体与固体混合后冷却固化后制备的固体颗粒;为了降低进入热解过程的固体热载体中细颗粒热载体的数量,可以使用外部引入的大颗粒固体形成循环固体热载体的主体,沉降过程或烧焦过程采用分类排焦优先排出小颗粒氧化半焦产品而不作为固体热载体循环使用。本发明所述反应器,其结构形式可以是任意一种合适的形式。以下结合总体流程描述各步骤具体特征。进入一级热解反应过程R10的碳氢粉料FM即R10FS,通常为干燥后脱水粉料,其水分重量通常低于10%、一般低于7%、较佳者低于5%。进入一级热解反应过程R10的碳氢粉料FM即R10FS,其粒度通常为0.00001~6毫米、一般为0.0001~3.5毫米、较佳者为0.001~2毫米。进入一级热解反应过程R10的气提气R10FV,可以是任意一种温度、压力、组分组成等合适的气体,通常为水蒸气或氮气或不含氧气烟道气或净化脱油后的煤气或煤制合成气或半焦制合成气。进入一级热解反应过程R10的第一固体热载体R10KS,通常为来自流化床烧焦反应过程R50的高温氧化半焦,其重量流量与粉煤R10FS重量流量的比值,根据需要确定,通常为0.5~30、一般为3~15、较佳者为5~10。一级热解反应过程R10,使用的一级热解反应器R10E的设备型式根据需要确定,通常使用提升管式一级热解反应器。气固分离段SRS、S20、S50,通常使用离心分离式气固分离设备元件,可以形成1级或2级或多级串联操作的气固分离系统。脱尘二级热解煤气R20PV中固体含量通常低于50克/立方米、一般低于10克/立方米、较佳者低于4克/立方米。二级热解反应过程R20,其设备型式根据需要确定,通常使用立式下流式沉降器R20E。二级热解反应器底部的气提气,通常选择惰性气体如蒸汽或氮气或无氧气的烟道气或净化煤气循环气或其它惰性气体。关于沉降器R20E结构,其工艺功能是形成流化床、最好是形成散式流化床即膨胀床,沉降器R20E的内部空间大体分为三段:上段为低气速的气体脱固空间、中段为气速适宜的二级热解主反应空间、下段为气提段。上段为低气速的气体脱固空间,因此,需要降低来自下部热解主反应空间的煤气的截面流速,也就是说要求降低气体流速即需要扩大截面面积,因此,通常上段即气体脱固空间的径向截面积大于中段即二级热解主反应空间的径向截面积。中段为气速适宜的二级热解主反应空间,在此,一级热解半焦发生二级热解反应释放出煤气、焦油蒸汽;在一级热解半焦从上而下穿过二级热解主反应空间的过程中,随着温度的升高,一级热解半焦逐步释放煤气、焦油蒸汽,二级热解主反应空间的底部排出的半焦的释放煤气、焦油蒸汽的能力已经很小。在气提段,自底部进入二级热解反应器下部气提段的向上流动的气提气,通常通过气体分布器实现初期的均匀分布,由于该气体的作用是携带二级热解反应段底部半焦中包含的焦油气,因此,气提气的流量通常是较小的,从后续煤气加工利用角度讲气提气属于无效组分(水蒸气、氮气、烟气)或循环煤气,其数量应尽可能缩小,这样气提段的截面面积通常较小。实际上,气提段的截面面积通常小于二级热解主反应空间的截面面积。脱尘热解煤气中固体含量通常低于50克/立方米、一般低于10克/立方米、较佳者低于4克/立方米。气提气,可以是任意一种温度、压力、组分组成等合适的气体,通常为水蒸气或氮气或不含氧气烟道气或净化脱油后的煤气或煤制合成气或半焦制合成气。流化床烧焦反应过程R50,流化床烧焦反应器R50E的设备型式根据需要确定,通常使用立式流化床烧焦反应器R50E。根据需要,流化床烧焦反应过程R50,可以排出热氧化半焦R50PS产品或不排出热氧化半焦R50PS产品;排出的热氧化半焦R50PS可以通过间接换热器冷却回收热能后储存。根据需要,流化床烧焦反应过程R50,可以设置循环氧化半焦物流R50RS取热器,循环氧化半焦物流R50RS通过间接换热器如蒸汽发生器外输热能冷却后返回流化床烧焦反应过程R50,此时,循环氧化半焦物流R50RS充当外输热能的热载体。提升管式一级热解反应器,可以是上下同直径的圆柱体式提升管,可以是上部大直径圆柱体、中间过渡椎体、下部小直径圆柱体组成的不等径提升管,过渡椎体部位可以布置短循环固体料的分布器。与常规的使用固体热载体的残液固化料流化床热解、流化床烧焦系统的方法相比,本发明特点在于:①对于重质油含量高的残液固化料,“快速预热段”使用温度更高的第一固体热载体,可以使残液固化料快速吸热升温,缩短其跨越软化温度点至结焦温度点这一温距的时间,降低残液固化料表面可能出现的液体形成固体颗粒粘结的概率或降低粘结物产量,同时较高的操作温度适应离解能高的双键或芳环π键的热解所必须的输入性能量级,总体目标是快速热解残液固化料中的有机质中的双键或芳环π键,产生热解焦油、热解煤气、及热半焦;②流化床烧焦反应器采用更高的操作温度,利于提高烧焦过程热能回收效率和等级,进而生产高压力等级的水蒸气;③流化床烧焦反应器采用更高的操作温度,利于降低烧焦反应空间体积,或者利于降低烟气中的CO含量;④流化床烧焦反应器采用更高的操作温度,利于提高细碳颗粒的一次烧尽率,减少固体热载体中的细粉含量;⑤流化床烧焦反应器采用更高的操作温度,利于降低大循环固体热载体数量,进而降低沉降器和烧焦器的体积;⑥短循环过程经过的设备不包括沉降器、流化床烧焦反应器及其输送系统,其极限受热温度也较低,因此,其粉化率较低,利于降低总系统藏量中的细粉比率。⑦自循环第二固体热载体的循环回路,可以实现大小粒径固体颗粒的预分离,分出较小历经颗粒进入沉降器及烧焦反应器,选出较大粒径固体颗粒形成短循环,一定程度形成了分粒径使用固体热载体,小颗粒固体热载体,可以在分离过程或沉降器或烧炭器等流程点排出热解烧焦系统,比如冷却后成为产品或热态进入气化过程、燃烧过程等,为进一步的分粒径利用固体创造了条件。实施例实施例一煤液化残渣的流化焦化过程,煤液化残渣作为非常规含固油料。用煤的工业分析与元素分析的方法对煤液化残渣进行分析表征得到的结果见表3,可以看出,残渣中含有21.64wt%的灰分,硫含量和C/H(原子比)较高。索氏萃取结果见表4、表5,残渣中含24.71wt%正己烷可萃取的油、23.90wt%的前沥青烯和沥青烯、29.67wt%为不溶物、21.64wt%的灰分。为了提高煤液化油的总体收率,采用本发明,设置煤液化残渣的用双循环粉料的快速预热串联适温热解式碳氢料热解反应过程,各步骤操作条件如下:(1)在一级热解反应过程R10,第一碳氢粉料R10FS选自软化点高于130℃的煤直接液化残渣液体冷却固化后制备的固体颗粒的干燥脱水料,颗粒粒径为0~0.8毫米,水含量低于2%,进入一级热解提升管流化床热解反应器的温度为90℃;一级热解反应过程R10,使用提升管流化床热解反应器,第一固体热载体R10KS为来自流化烧焦反应过程R50的高温氧化半焦,温度为680~720℃;一级热解反应过程R10的操作条件为:总体反应时间12.0~15s、第一热解段反应时间比率为15~20%,提升管反应产物出口温度即一级热解反应过程终端反应温度为550~580℃;第一固体热载体LR-DS的温度为680~720℃;短循环固体SRS-SR的温度为550~580℃;第一固体热载体R10KS的重量与第一碳氢粉料R10FS重量比值为8~10;短循环固体SRS-SR的重量与第一碳氢粉料R10FS重量比值为4~5;(4)在二级热解反应过程R20的反应空间,设置2~12副人字挡板或环形挡板,二级热解反应过程的主热解段的温度为500~650℃;二级热解段底部通入450~650℃气提气V22V进行焦油蒸汽汽提,气提气V22V通过半焦料层后向上流动并进入二级热解反应过程R20的二级热解煤气产物中;(5)在气固分离过程S20,使用旋风分离器,离开固体粉料主体床层后的含尘二级热解过程气R20EPV,通过气固分离系统S20分离为脱尘二级热解煤气R20PV和半焦S20PS,半焦S20PS进入二级热解反应过程R20的沉降器R20E内;气固分离过程S20,同时对短循环分离气体SRS-V进行气固分离;脱尘二级热解煤气R20PV中固体含量低于4克/立方米。一级热解反应过程R10的操作条件为:绝对操作压力为0.18~0.20MPa。煤液化残液固化粉料的流化热解产物重量收率为:挥发气体占10.3~12.5%、油50~510℃占20.1~21.5%、焦炭等固体占66.0~69.6%。50~510℃馏分油的馏分比率为50~330℃馏分占47.3%、330~510℃馏分占52.7%。对于200万吨/年投煤量的大型煤液化装置而言,60万吨/年煤液化残渣含固油料经过流化焦化组合工艺,可以回收12.06~12.90万吨/年油品,相当于提高油收率6.03~6.45%。将煤液化残渣经济地转化为油气和碳料,油气被回收,碳料用作燃料燃烧后所得灰渣制砖。表3残渣样品的工业分析和元素分析数据表4液化残渣的索氏萃取结果[单位:wt%(daf)]样品油(HS)煤沥青(HI-BS)前沥青烯(BI-THFS)不溶物(THFI)1号31.5721.548.9937.90表5液化残渣的索氏萃取结果[单位:wt%(对初始样)]样品油(HS)煤沥青(HI-BS)前沥青烯(BI-THFS)不溶物(THFI)1号24.7116.867.03729.67实施例二基于实施例一,提升管式一级热解反应器R10E,同时加工颗粒直径为0.35~0.750毫米粉煤,以改善固体循环系统的固体颗粒粒径分布。当前第1页1 2 3