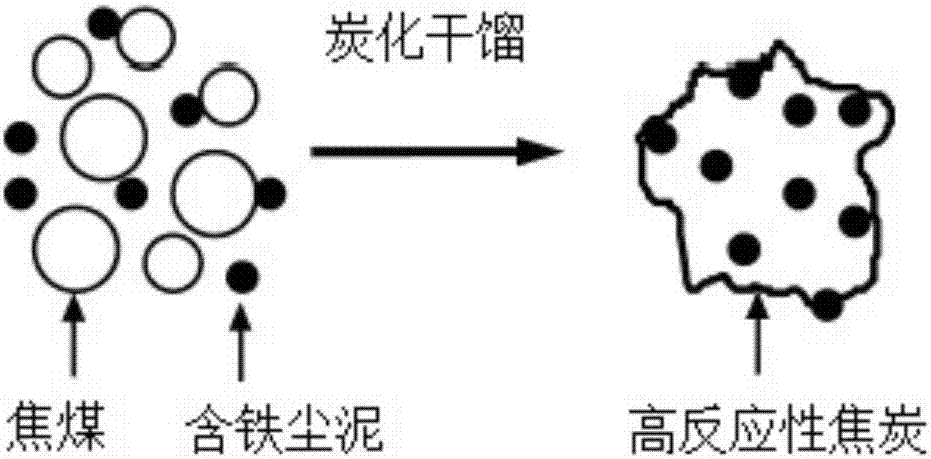
本发明涉及一种焦炭及其制备方法,特别涉及到一种利用钢铁厂含铁尘泥制备的高反应性焦炭及其制备方法,属炼焦
技术领域:
。
背景技术:
:焦炭作为高炉燃料是高炉冶炼发展史上一个重要的里程碑,其在高炉内所起的作用举足轻重。焦炭质量的研究也是众多冶金工作者长期以来研究的重点,提高焦炭质量,降低高炉焦炭用量,同时降低焦炭生产带来的环境污染,意义重大。高炉一般要求焦炭的反应性指标在一定的范围,这样可以保证高炉内焦炭的反应后强度,而高反应性焦炭是指焦炭与co2发生气化反应的能力增加而具有较高的反应性指标,通过添加催化剂(碱土金属、过渡金属)制备的焦炭比常规炼焦工艺生产焦炭反应性要高,这类焦炭通常称为高反应性焦炭。高反应性焦炭的使用可以降低焦炭气化反应温度,从而降低高炉热储备区温度,提高炉内的还原效率,最终达到降低燃料消耗的目的。制备高反应性焦炭一般有两种途径,一是通过增加在原理配煤中非粘结性煤的比例的方法,二是通过添加催化剂,例如碱金属、碱土金属和过渡金属的方法实现。日本通过长期的研究,开发和采用了两种工艺生产高反应性高强度焦炭,一种是集选择性破碎、煤调湿、混合制粒、配加弱粘结性煤、干熄焦等技术于一体的复杂的scope21炼焦工艺,该工艺复杂、投资巨大。另一种是在炼焦配煤中添加一定比例的富cao煤的炼焦工艺,在实践中,日本室兰2号高炉使用富钙焦炭,还原剂比例降低10kg/thm,但富cao煤资源稀缺,推广受到限制。cn10375701b公开了一种高反应性焦炭的生产方法,其以配合煤为原料进行炼焦,其中,在原料中添加钢渣。该案提高了所得焦炭的反应性,降低了焦炭与二氧化碳气化反应的开始温度,焦炭具有较低的气化反应开始温度可以降低高炉热储备区温度,配合还原性高的矿石使用可以降低高炉燃料消耗,同时还能保证焦炭的反应后强度满足高炉炼铁的要求,且作为添加剂的钢渣价格低廉、来源广泛。钢渣是炼钢过程中排出的副产物,以非金属硅酸盐为主,目前是生产水泥和建筑材料的主要原料,已被广泛地100%应用生产附加值更高的产品。而进行高反应焦炭制备配煤中需要添加的钢渣对粒度有一定的要求,钢渣粒度大,可磨性差,很难满足要求。另一方面,钢渣随钢铁生产工艺变化波动较大,其会严重影响高反应性焦炭的质量和性能。cn103468289b公开了一种高炉用铁焦及其制备方法,其原料由5~20%铁矿粉,80~95%配合煤组成。该案通过对铁矿石与配合煤的性能、配比、粒度以及组成等进行优化,在不外加粘结剂的情况下保证铁焦产品的强度和反应性均能满足冶炼的要求。这种方法制备的铁焦一方面对铁矿粉性能要求苛刻,选择受到限制,另一方面采用湿法熄焦技术,焦炭含水量大,会造成高炉生产过程中的能耗增加,燃料比升高。cn103468287b公开了一种高强度-高反应性含铁焦炭的制备方法,该方法包括经过两次筛选,得到适当的煤样,取粒径小于74μm的铁矿粉作为催化剂与煤样分别烘干后均匀混合形成混料,加入9~11%的水,在炼焦反应罐中捣鼓密封得到煤饼,铁矿粉占混合料质量的0~15%。该方法中添加了一定量的铁矿粉,为了能够有效防止含铁焦炭中铁矿粉与炼焦炉炉衬的反应,高强度高反应性焦炭的制备过程中炼焦终温降低,这样会影响焦炭的性能和质量。cn1264952c公开了高炉用高反应性高强度焦炭及其制造方法,该案通过使用含有大量中炭化度低流动性粘结性煤的少数几种牌号配合煤,可以廉价地制得一种焦炭强度与反应性和气孔分布均达到所需水平的高反应性高强度焦炭。但该案对配煤中炭化度和粘结性要求较高,原料来源受到限制,不利于推广应用。cn102719264b公开了一种高反应性焦炭及其生产方法,该案所生产的高反应性焦炭为内外两层结构,其内核由配好的炼焦用煤制成,外层由高挥发分煤和配好的炼焦煤混匀制成。先制成煤核,再进行软沥青喷涂,最后与外核粘结混合,最终通过炼焦制成高反应性高强度焦炭。该案生产工艺复杂,控制难度大;此外,软沥青粘结剂的使用会增加炼焦成本,影响焦炭质量,同时造成环境污染。由上可知,现有技术生产高反应焦炭的方法需使用粘结剂等添加剂,采用立式干馏炉(不适合大规模工业生产的需求,劳动强度大、生产规模小、机械化程度低)、生产工艺复杂、工业化应用受到限制。另一方面,随着我国钢铁工业的快速发展,钢铁企业生产过程中所产生的冶金粉尘对环境的影响日趋严重。2016年我国钢铁产量达到8亿吨左右,一般钢铁企业粉尘的产生量为钢产量的10%左右,按此计算我国钢铁企业每年粉尘的产生量在8000万吨左右,这些粉尘含有大量的铁元素,其中一部分粉尘还含有碳、锌、钾和钠等元素,如高炉干法除尘灰、转炉污泥、转炉除尘灰、烧结电除尘灰等。目前,对于钢厂含铁尘泥的回收利用,一般是返回烧结工序作为烧结配料,但这些粉尘中碱金属和锌等有害元素会在使用中循环富集,一方面影响烧结生产的组织和烧结矿产品质量,另一方面也会给高炉操作带来不利的影响。因此,迫切需要找到利用钢厂含铁尘泥的新方法。技术实现要素:本发明的主要的目的在于提供一种含铁尘泥的新的应用,同时寻找一种新的高反应性焦碳的制备方法。本发明通过实验表明,含铁尘泥可应用于高反应性焦炭的制备过程中,其能够制备高反应性焦炭,因此,本发明提供含铁尘泥在制备高反应性焦炭中的应用;所述含铁尘泥包括转炉细灰、转炉粗灰、电炉灰和og泥中的一种或多种。作为本发明前述应用的一具体实施方式,优选地,所述含铁尘泥中的tfe含量与cao含量之和占总质量的40%以上,含铁尘泥90%颗粒粒度范围5~50μm。另一方面,本发明提供一种高反应性焦碳的制备方法,所述方法包括如下步骤:(a)将焦煤炼焦原料进行破碎筛分,然后将其与重量比例占其1~15%的含铁尘泥混合得配加含铁尘泥的煤样,其中,所述含铁尘泥中的tfe含量与cao含量之和占总质量的40%以上,含铁尘泥90%颗粒粒度范围5~50μm;(b)将步骤(a)所得配加含铁尘泥的煤样干燥,然后配水得配水后的煤样;(c)将步骤(b)配水后的煤样捣固压实进行高温干馏炼焦,其中,首先以10~15℃/min的速率升温至500±50℃,然后以不大于10℃/min的速率升温至1100℃,于该温度下恒温12h~15h;(d)干法熄焦得所述高反应性焦碳。本发明通过控制钢铁厂含铁尘泥的粒度、添加比例及制备过程的升温方式制得了高反应性焦炭,其是一种利用钢铁厂含铁尘泥制备高反应性焦炭的方法,既实现钢铁厂粉尘固废资源的综合利用,又降低了高反应性焦炭的生产成本,本发明可利用常规焦炭生产设备生产高反应性焦炭,在炼焦配煤工序完成含铁尘泥的配入,无需增加额外的设备和能源消耗,其工艺简单,并且易于推广应用。由本发明制备的高反应性焦炭在反应性提高的同时焦炭的反应后强度不会大幅降低,满足高炉冶炼的需求。本发明所述高反应焦炭是指通过添加催化剂(含铁尘泥)制备的焦炭,比常规炼焦工艺生产的焦炭反应性要高。高炉使用本发明高反应性焦炭后会使焦炭溶损反应开始的温度降低,焦炭溶损反应开始温度大致与高炉热储蓄区温度相等,同时铁氧化物的还原温度也会相应降低,在低温下铁氧化物的还原会使高炉有效热消耗降低,co利用率提高,从而降低高炉焦比,因此本发明制备得到的高反应性焦炭可以提升高炉冶炼效率,降低生产成本。作为本发明上述制备方法的一具体实施方式,其中,所述含铁尘泥包括转炉细灰、转炉粗灰、电炉灰和og泥中的一种或多种。本发明于下表1中列出了几种典型的钢铁厂含铁尘泥成分,但需要说明的是所述含铁尘泥不局限于以下几种:表1粉尘类型tfemfefeosio2caomgoal2o3czn转炉细灰52.302.4815.592.376.521.050.791.520.03转炉粗灰56.3224.0426.342.9918.843.760.530.700.05电炉灰44.730.348.912.062.921.380.561.142.61og泥58.196.4359.581.9810.283.471.831.650.25只要本发明的含铁尘泥满足tfe含量与cao含量之和占总质量的40%以上,含铁尘泥90%的颗粒粒度5~50μm即可,对于其他成分并发明无强制性要求。含铁尘泥作为制备高反应性焦炭催化剂时,可以是单一的一种含铁尘泥,也可以是几种含铁尘泥的混合物。作为本发明上述制备方法的一具体实施方式,其中,所述含铁尘泥为转炉细灰。优选地,该转炉细灰中的tfe含量与cao含量之和占总质量的58%以上。优选地,该转炉细灰的添加比例为1~15%。优选地,该转炉细灰90%的粒度范围为5~10μm。更优选地,该转炉细灰满足上述条件中的两者或三种。作为本发明上述制备方法的一具体实施方式,其中,当所述含铁尘泥为转炉粗灰。优选地,该转炉粗灰中的tfe含量与cao含量之和占总质量的75%以上。优选地,该转炉粗灰的添加比例在1~15%。优选地,该转炉粗灰90%的粒度范围在10~30μm。更优选地,该转炉细灰满足上述条件中的两者或三种。作为本发明上述制备方法的一具体实施方式,所述干法熄焦包括:步骤(c)结束后,通入惰性气体进行冷却,直至炼焦后的焦炭的温度降至100℃以下,切断气体,自然冷却到室温;更优选,该惰性气体为氮气。本发明采用干法熄焦,其相比湿法熄焦工艺提升焦炭质量,降低综合能耗。本发明所指室温是指10~30℃。作为本发明上述制备方法的一具体实施方式,其中,所述焦煤炼焦原料包括但不限于主焦煤、1/3焦煤、气煤、肥煤、气肥煤、瘦煤、贫瘦煤中的一种或多种。这些炼焦煤都可以作为高反应性焦炭制备的原料。优选主焦煤和1/3焦煤;更优选地,所述焦煤炼焦原料为质量比为2:1~4:1的主焦煤和1/3焦煤。优选地,该焦煤炼焦原料中粒径不大于3mm的比例占焦煤炼焦原料总质量的80%以上。相对于其他炼焦用煤,主焦煤和1/3焦煤的成分和性能比较稳定,采用这两种原料可避免由于成分波动对炼焦过程和高反应性焦炭性能的影响,影响含铁尘泥的效果。作为本发明上述制备方法的一具体实施方式,其中,控制所述配水后的煤样中的水分的质量分数为7~9%。优选地,步骤(b)中所述干燥是在100~110℃鼓风干燥1~3h。另一方面,本发明提供一种高反应性焦炭,其是由上述制备方法制备得到的。综上可知,本发明主要提供了一种高反应性焦碳的制备方法,该方法利用钢铁厂固废资源含铁尘泥制备高反应性焦炭,使钢铁厂大量的固废资源得到有效的利用,同时大大降低了高反应性焦炭的生产成本,其工艺简单,并且易于推广应用。由本发明制备的高反应性焦炭在反应性提高的同时焦炭的反应后强度不会大幅降低,满足高炉冶炼的需求。附图说明图1为实施例1~8的流程示意图。图2为实施例1~8的原理示意图。具体实施方式为了对本发明的技术特征、目的和有益效果有更加清楚的理解,现结合具体实施例对本发明的技术方案进行以下详细说明,应理解这些实例仅用于说明本发明而不用于限制本发明的范围。实施例中,各原始试剂材料均可商购获得,未注明具体条件的实验方法为所属领域熟知的常规方法和常规条件,或按照仪器制造商所建议的条件。实施例1~8提供的焦炭的制备方法的流程示意图如图1所示,原理示意图如图2所示,图1显示下述制备方法是先将炼焦原料破碎,然后进行配煤,该配煤与含铁尘泥混合,再经烘干、配水、捣固压实、干馏炼焦得高反应性焦炭。实施例1~4(1)首先选用成分稳定的主焦煤和1/3焦煤(主要指标及质量比请参见表2及表3)作为炼焦原料,分别进行破碎筛分,控制炼焦原料中粒径不大于3mm的比例占总质量分数的80%以上。(2)将转炉细灰按预定的比例(实施例1~4的具体比例请参见表3,该比例为转炉细灰的质量占炼焦原料的总质量)均匀的添加到步骤(1)所得炼焦原料中得配加转炉细灰的煤样,所述转炉细灰中tfe与cao质量分数之和为总质量的58%,为了保证炼焦配料的均匀性以及催化效果,转炉细灰的粒度要求越小越好,越均匀越好,优选转炉细灰90%的粒度范围为5~10μm。(3)将步骤(2)所得配加转炉细灰的煤样放入干燥箱中烘干,在105℃下鼓风干燥2h,取出后向该煤样中加入水,控制水分的质量分数为8%。(4)将步骤(3)所得物料装入钢制反应管中,捣固压实,并将反应管置于高温管式反应炉中,进行高温干馏炼焦,升温过程分为三个阶段,首先,以15℃/min的升温速率,由室温(10~30℃)升至500℃,然后,以10℃/min的升温速率由500℃升至1100℃,升温至1100℃后,保持1100℃恒温12h。(5)待步骤(4)结束后,采用干法熄焦方式熄焦,取出反应管,并同时通入200l/h流量的n2进行气体冷却,直至焦炭样品温度降至100℃以下,切断气体,自然冷却到室温,炼焦过程结束,得到焦炭。表2实施例1~4中所用炼焦原煤主要指标煤种aad/%vad/%sad/%gy/mma(主焦煤)8.521.50.358517b(1/3焦煤)8.035.50.408116表3实施例1~4采用的配比方案表方案煤a煤b转炉细灰实施例180%20%3%实施例280%20%5%实施例380%20%10%实施例480%20%15%对比例1本对比例采用与实施例1基本相同的方法制得焦炭,不同的仅是本对比例不添加转炉细灰,即不包括实施例1中的步骤(2),其余步骤均同实施例1。取实施例1~4及对比例1制得的焦炭进行热态性能检测(gb/t4000-1996),结果见下表4所示。从表4中结果可以看出,不添加转炉细灰的对比例1所得焦炭的指标与常规焦炭指标基本一致,随着向炼焦配煤中添加转炉细灰的比例增加,实施例1至实施例4所得高反应性焦炭的溶损反应温度逐渐降低,焦炭的反应性指数逐渐升高,焦炭的反应后强度逐渐降低。在转炉细灰添加比例为10%时,焦炭反应性指数为30.5%,该反应性指数对应的反应后强度为62.8%,能够很好的满足高炉生产的要求。表4实施例1~4及对比例1制得焦炭的性能分析表实施例5~8(1)首先选用成分稳定的主焦煤和1/3焦煤(主要指标同实施例1,配比方案请参见表5)作为炼焦原料,分别进行破碎筛分,控制炼焦原料中粒径不大于3mm的比例占总质量分数的80%以上。(2)将转炉粗灰按预定的比例(实施例5~8的具体比例请参见表5,该比例为转炉粗灰的质量占炼焦原料的总质量的比例)均匀的添加到步骤(1)所得炼焦原料中,所述转炉粗灰中tfe与cao质量分数之和为总质量的75%,为了保证炼焦配料的均匀性以及催化效果,转炉粗灰的粒度要求越小越好,越均匀越好,优选转炉粗灰的90%粒度范围在10~30μm。(3)将步骤(2)所得配加转炉粗灰的煤样放入干燥箱中烘干,在105℃下鼓风干燥2h,取出后向该煤样中加入水,控制水分的质量分数为8%。(4)将步骤(3)所得物料装入钢制反应管中,捣固压实,并将反应管置于高温管式反应炉中,进行高温干馏炼焦,升温过程分为三个阶段,首先以15℃/min的升温速率,由室温(10~30℃)升至500℃,然后,以10℃/min的速率,由500℃升至1100℃,升温至1100℃后,保持1100℃恒温12h。(5)待步骤(4)结束后,采用干法熄焦方式熄焦,取出反应管,并同时通入200l/h流量的n2进行气体冷却,直至焦炭样品温度降至100℃以下,切断气体,自然冷却到室温,炼焦过程结束,得到焦炭。表5实施例5~8中所述配比方案表方案煤a煤b转炉粗灰实施例580%20%3%实施例680%20%5%实施例780%20%10%实施例880%20%15%对比例2本对比例采用与实施例5基本相同的方法制得焦炭,不同的仅是本对比例不添加转炉粗灰,即不包括实施例5中的步骤(2),其余步骤均同实施例5。取实施例5~8及对比例2制得的焦炭进行热态性能检测(gb/t4000-1996),结果见下表5所示。从表5中结果可以看出,不添加转炉粗灰的对比例2所得焦炭的与常规焦炭指标基本一致,随着向炼焦配煤中添加转炉粗灰的比例增加,实施例5至实施例8所得焦炭的溶损反应温度逐渐降低,焦炭的反应性指数逐渐升高,焦炭的反应后强度逐渐降低。在转炉粗灰添加比例为10%时,焦炭反应性指数为34.5%,该反应性指数对应的反应后强度为59.2%,能够很好的满足高炉生产的要求。表5实施例5~8及对比例2制得焦炭的性能分析表最后说明的是:以上实施例仅用于说明本发明的实施过程和特点,而非限制本发明的技术方案,尽管参照上述实施例对本发明进行了详细说明,本领域的普通技术人员应当理解:依然可以对本发明进行修改或者等同替换,而不脱离本发明的精神和范围的任何修改或局部替换,均应涵盖在本发明的保护范围当中。当前第1页12