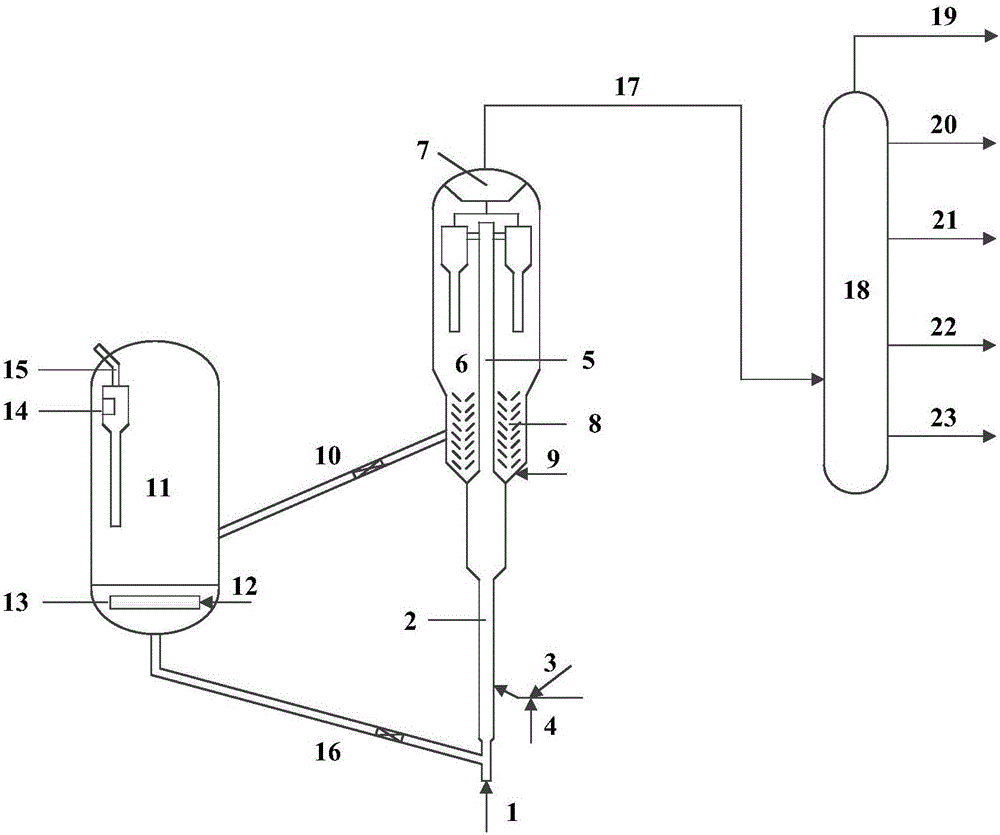
本发明涉及一种生产高辛烷值汽油的催化裂化方法。
背景技术:
:近年来,伴随经济的快速发展,我国汽车保有量逐年增加,因此对汽油的需求也日益提高。催化裂化(fcc)汽油是我国车用汽油的主要来源,占成品汽油的比例超过60%。我国催化裂化汽油的研究法辛烷值一般低于93,烯烃含量较高,其体积分数一般在35%以上,而芳烃含量较低,其体积分数一般为10%~25%。与此同时,日益严格的环保法规对车用汽油的硫含量、烯烃含量和芳烃含量等指标的限制也更为严苛。现行车用汽油标准gb17930-2016规定,车用汽油via阶段和vib阶段烯烃体积分数上限值分别为18%和15%。烯烃是催化裂化汽油辛烷值的主要贡献者,因此,如何在降低烯烃含量的同时提高汽油的辛烷值,是催化裂化工艺必须解决的难题。中国专利cn101362959a公开了一种制取丙烯和高辛烷值汽油的催化转化方法,该方法将难裂化原料先与催化剂接触,在较苛刻的条件下进行催化裂化反应,反应物流与易裂化原料混合,继续裂化,反应产物中馏程为180~260℃的馏分、重芳烃抽余油作为易裂化原料返回装置回炼。该方法获得的汽油产率达35.20重%,汽油研究法辛烷值(ron)为97.1,马达法辛烷值(mon)为85.0。美国专利us5009769公开了一种采用双提升管裂化不同性质烃类原料生产高辛烷值汽油的方法。蜡油和渣油注入第一根提升管,在剂油比5~10、停留时间1~4秒的条件下裂化;直馏汽油、直馏中间馏分油和催化重汽油注入第二根提升管,在剂油比3~12、停留时间1~5秒的条件下裂化。两根提升管的末端进入同一个沉降器,并且共用后续分馏系统。中国专利cn101469274a公开了一种生产高辛烷值汽油的方法,该方法将重质原料油在反应温度460~720℃,压力0.1~0.5兆帕,停留时间0.2~2秒,剂油重量比4~20的条件下,在催化裂化反应器内与催化剂接触反应,分馏得到100~360℃的重汽油和轻柴油馏分,然后将该段馏分经或不经加氢处理后返回催化裂化装置回炼。该方法所得汽油的研究法辛烷值可以达到94.9,其中芳烃含量高达59.32重%。中国专利cn1069054a公开了一种采用两根提升管分别加工轻质烃类和重质烃类的催化裂化方法。在第一根提升管反应器中,轻质烃类与热催化剂在600~700℃、剂油重量比10~40、停留时间2~20秒、催化剂碳含量0.1~0.4重%的条件下进行反应,以达到增产烯烃,提高汽油辛烷值的目的;然后催化剂进入常规提升管参与重质烃类的催化裂化反应。该方法流程复杂,提高辛烷值的能力有限,并且不利于降低汽油烯烃含量。目前,催化裂化装置多采用变径提升管反应器,追求汽油产率的最大化,从而导致催化裂化柴油(或称“轻循环油”)的品质较差。对轻循环油进行加氢处理,然后进催化裂化可以提高汽油辛烷值,同时获得较高的汽油收率,但流程复杂,氢耗较高,操作费用较大。美国专利us4585545公开了一种将催化裂化轻循环油全馏分先进行加氢处理,得到的加氢柴油再进催化裂化生产富含单环芳烃汽油的催化裂化方法。该方法所得汽油的辛烷值不低于91,汽油中单环芳烃的体积分数为35%~55%。中国专利cn104560166a公开了一种轻循环油加氢处理生产高辛烷值汽油的催化转化方法。该方法的重质石油烃在主提升管反应器进行反应,然后将分馏得到的催化裂化轻循环油切割为轻馏分和重馏分,轻馏分和经过加氢处理的重馏分分层注入副提升管内。该方法的汽油收率可达65.63%,汽油的研究法辛烷值可高达95.8。从上述公开的文献可以看出,提高催化裂化汽油辛烷值的途径主要是对汽油或轻循环油进行改质,而改善重质烃类原料的裂化性能以提高汽油辛烷值的报道较少。催化裂化装置的原料为减压蜡油或掺渣的重质油,原料油的雾化状况对催化裂化反应及产品分布起关键作用。为了满足日益增长的车用汽油需求,有必要开发一种将重质原料高效转化生产高辛烷值汽油同时降低汽油烯烃含量的催化裂化方法。技术实现要素:本发明的目的是提供一种生产高辛烷值汽油的催化裂化方法,本发明的方法能够多产高辛烷值汽油,同时降低汽油中的烯烃含量。为了实现上述目的,本发明提供一种生产高辛烷值汽油的催化裂化方法,该方法包括:将预热后的原料油经雾化介质雾化后引入催化裂化装置中与催化裂化催化剂接触并进行催化裂化反应,得到反应油气和待生催化剂;其中,所述雾化介质为干气或者为干气和水蒸气的混合物;将所得待生催化剂进行烧焦再生,所得再生催化剂作为所述催化裂化催化剂返回所述催化裂化装置中;将所得反应油气进行分离,得到干气产物、液化气产物、汽油产物、柴油产物和重油产物。可选的,所述雾化介质中的干气为选自所述干气产物、外产催化裂化干气、焦化干气和加氢裂化干气中的至少一种。可选的,所述雾化介质与原料油的重量比为0.01-0.20。可选的,所述雾化介质中干气的重量比例为0.2-1。可选的,所述雾化介质中干气的c3及以上烃类的体积分数不高于10体%。可选的,所述催化裂化装置为选自提升管反应器、流化床反应器、上行式输送线和下行式输送线中的至少一种。可选的,所述催化裂化装置包括提升管反应器和套设在该提升管反应器上部的流化床反应器,所述流化床反应器包括上下同轴且流体连通的扩径反应段和缩径稀相出口段,所述缩径稀相出口段设置于所述扩径反应段的上方,所述扩径反应段与所述提升管反应器相连,且所述缩径稀相出口段的内径长度为所述扩径反应段内径长度的30-60%。可选的,所述催化裂化装置还包括上下同轴且流体连通的沉降器和汽提器,所述提升管反应器由下至上从汽提器伸入所述沉降器中,且所述流化床反应器位于所述沉降器中;所述缩径稀相出口段的顶部开口与所述沉降器相连通。可选的,所述提升管反应器的催化裂化反应条件包括:温度为450-650℃,油气停留时间为0.1-5秒,反应压力为0.1-1兆帕,剂油重量比为4-50;所述流化床反应器的催化裂化反应条件包括:温度为200-550℃,停留时间为2-16秒,反应压力为0.1-0.5兆帕,剂油重量比为10-100。可选的,所述原料油为石油烃和/或其它矿物油,其中,所述石油烃为选自减压瓦斯油、减压渣油、常压瓦斯油、常压渣油、焦化瓦斯油、脱沥青油、加氢精制油、加氢裂化尾油和原油中的至少一种,所述其它矿物油为选自煤液化油、页岩油、动植物油脂和油砂油中的至少一种。可选的,所述催化裂化催化剂包括10-50重量%沸石、10-90重量%无机氧化物和0-70重量%粘土,所述沸石为含或不含稀土的y型分子筛、hy型分子筛、超稳y型分子筛、zsm-5型分子筛、具有五元环结构的高硅分子筛和beta分子筛中的至少一种。与现有技术相比,本发明提供的方法具有下列优点:1、充分利用炼厂低附加值的干气资源,减少水蒸气使用,不仅有利于节约能源,而且减少废水排放。2、原料油转化率提高,汽油产率和辛烷值提高,同时汽油烯烃含量降低。3、工艺流程简单,易于操作,可以利用常规的催化裂化装置和催化剂,不需对现有装置作重大改动,也可以用含有提升管反应器和流化床反应器的复合反应器,分段实现裂化、氢转移和芳构化反应,最大限度地提高原料转化率。4、催化裂化装置工艺灵活度高,原料适用范围广,降低了高温水热条件对催化剂的不利影响,催化剂利用效率高。本发明的其他特征和优点将在随后的具体实施方式部分予以详细说明。附图说明附图是用来提供对本发明的进一步理解,并且构成说明书的一部分,与下面的具体实施方式一起用于解释本发明,但并不构成对本发明的限制。在附图中:图1是本发明方法一种具体实施方式的流程示意图。图2是本发明方法另一种具体实施方式的流程示意图。附图标记说明1管线2提升管反应器3管线4管线5管线6沉降器7集气室8汽提段9管线10斜管11再生器12管线13主风分配器14旋风分离器15管道16管线17管线18分馏装置19管线20管线21管线22管线23管线101提升管反应器102扩径反应段103沉降器104再生器105管线106管线107管线108缩径稀相出口段109旋风分离器110汽提段111管线112斜管113管线114空气分配器115旋风分离器116管线具体实施方式以下结合附图对本发明的具体实施方式进行详细说明。应当理解的是,此处所描述的具体实施方式仅用于说明和解释本发明,并不用于限制本发明。本发明提供一种生产高辛烷值汽油的催化裂化方法,该方法包括:将预热后的原料油经雾化介质雾化后引入催化裂化装置中与催化裂化催化剂接触并进行催化裂化反应,得到反应油气和待生催化剂;其中,所述雾化介质为干气或者为干气和水蒸气的混合物;将所得待生催化剂进行烧焦再生,所得再生催化剂作为所述催化裂化催化剂返回所述催化裂化装置中;将所得反应油气进行分离,得到干气产物、液化气产物、汽油产物、柴油产物和重油产物。本发明将干气作为雾化介质或雾化介质的组成部分能够减少废水的排放,同时增加原料油的转化率、汽油的产率和辛烷值,并同时降低汽油中烯烃的含量。根据本发明,干气是本领域技术人员所熟知的,主要成分为氢气和c1-c2的烃类,所述雾化介质中的干气可以为选自所述干气产物、外产催化裂化干气、焦化干气和加氢裂化干气中的至少一种,所述雾化介质中干气的c3及以上烃类的体积分数一般不高于10体%,优选不高于5体%,所述雾化介质中干气的重量比例可以为0.2-1,优选为0.4-1,所述雾化介质与原料油的重量比可以为0.01-0.20,优选为0.05-0.15。根据本发明,所述雾化介质中干气的温度和压力与常规水蒸气雾化介质可以相同,温度一般高于400℃,压力可以为1-3.5兆帕,例如可选3.5兆帕或1.0兆帕两个级别。根据本发明,催化裂化装置是本领域技术人员所熟知的,例如,所述催化裂化装置可以为选自提升管反应器、流化床反应器、上行式输送线和下行式输送线中的至少一种,可以是上述多种反应器的组合,也可以是多个一种反应器的组合,组合的方式可以为串联和/或并联,提升管反应器可以为常规的等直径的提升管或者是各种形式变径的提升管。所述的流化床反应器可以为选自散式流化床反应器、鼓泡床反应器、湍动床反应器和快速床反应器中的至少一种,优选湍动床反应器。流化床反应器内的气体表观线速一般低于2米/秒,与提升管反应器相比,流化床反应器内可以保持较高的催化剂床层密度,一般大于200千克/米3,优选情况下,流化床反应器内催化剂床层密度保持在300-500千克/米3。一种实施方式,所述催化裂化装置包括提升管反应器和套设在该提升管反应器上部的流化床反应器,所述流化床反应器包括上下同轴且流体连通的扩径反应段和缩径稀相出口段,所述缩径稀相出口段设置于所述扩径反应段的上方,所述扩径反应段与所述提升管反应器相连,且所述缩径稀相出口段的内径长度为所述扩径反应段内径长度的30-60%。进一步地,所述催化裂化装置还可以包括上下同轴且流体连通的沉降器和汽提器,所述提升管反应器由下至上从汽提器伸入所述沉降器中,且所述流化床反应器位于所述沉降器中;所述缩径稀相出口段的顶部开口与所述沉降器相连通。所述流化床反应器的出口通过缩径稀相出口段与所述沉降器内的气固分离设备的入口连通,可以使流化床反应器内流出的物料快速进入气固分离设备从而实现反应油气与待生催化剂的快速分离,缩短反应油气在沉降器内的停留时间,抑制热裂化等二次反应,实现降低干气产率的目的。根据本发明,催化裂化反应是本领域技术人员所熟知的,本发明不再赘述。以在提升管反应器和流化床反应器中进行催化裂化反应为例,所述提升管反应器的催化裂化反应条件可以包括:温度为450-650℃,优选480-560℃,油气停留时间为0.1-5秒,优选1-4秒,反应压力为0.1-1兆帕,优选0.1-0.5兆帕,剂油重量比为4-50,优选为6-30;所述流化床反应器的催化裂化反应条件可以包括:温度为200-550℃,优选300-500℃,停留时间为2-16秒,优选5-15秒,反应压力为0.1-0.5兆帕,优选0.15-0.3兆帕,剂油重量比为10-100。上述反应可以分别在独立的流化床反应器和提升管反应器中进行,也可以依次在包括提升管反应器和套设在该提升管反应器上部的流化床反应器的催化裂化装置中进行,在提升管反应器内主要进行原料油的裂化反应,流化床反应器主要进行烃类的氢转移反应和/或芳构化反应,从而达到降低烯烃含量提高汽油辛烷值的目的。根据本发明,为降低反应器中的油气分压,在进行所述催化裂化反应过程中可以向所述流化床反应器底部注入稀释剂,其中稀释剂可以为选自水蒸气、氮气、c1-c4烷烃、干气中的至少一种,优选水蒸气,稀释剂与原料油的重量比优选为0.01-0.5。根据本发明,用于催化裂化的原料油是本领域技术人员所熟知的,例如所述原料油可以为石油烃和/或其它矿物油,其中,所述石油烃可以为选自减压瓦斯油、减压渣油、常压瓦斯油、常压渣油、焦化瓦斯油、脱沥青油、加氢精制油、加氢裂化尾油和原油中的至少一种,所述其它矿物油可以为选自煤液化油、页岩油、动植物油脂和油砂油中的至少一种,本发明中可以在一个位置将原料油引入催化裂化装置,或在一个以上相同或不同高度的位置将原料油引入催化反应装置内。根据本发明,所述方法还可以包括:将来自再生器的热催化剂进入提升管反应器底部的预提升段,经提升介质提升上行,与经雾化介质雾化后的原料油接触反应上行,待生催化剂和反应油气通过旋风分离器分离后,待生催化剂进入汽提器,经汽提、烧焦再生后返回反应器,反应油气引入后续分馏部分分离得到干气、液化气、高辛烷值汽油、柴油和蜡油等产物,其中干气可以作为本装置的雾化介质使用。从反应产物中分离干气、液化气、汽油、柴油和蜡油等产物的方法为本领域普通技术人员所熟知;预提升介质可以选自水蒸气、干气或氮气的一种或几种,预提升介质与原料油的重量比可以为0.01-2,优选0.05-1;再生过程可以根据本领域常规的催化剂再生方法实施,例如:从再生器底部引入含氧气体(如空气),待生催化剂与氧气接触烧焦再生,生成的烟气在再生器上部进行气固分离,烟气进入后续能量回收系统。所述待生催化剂的再生条件可以为:温度600-750℃,优选650-700℃;气体表观线速0.2-3米/秒,优选0.5-2米/秒;待生催化剂平均停留时间0.5-3分钟,优选0.8-2分钟。另外,本发明所述原料油与热的催化裂化催化剂接触之前,优选将原料油预热至180-400℃,优选200-380℃。根据本发明,催化裂化催化剂是本领域技术人员所熟知的,例如,所述催化裂化催化剂可以包括10-50重量%沸石、10-90重量%无机氧化物和0-70重量%粘土,所述沸石作为活性组分,优选中孔沸石和任选的大孔沸石,所述中孔沸石占沸石总重量的30-80重%,大孔沸石占沸石总重量的20-70重%,所述的中孔沸石可以为zsm系列沸石和/或zrp沸石,所述大孔沸石可以为y型沸石或beta沸石,其中y型沸石可以为选自rey沸石、rehy沸石、usy沸石中的至少一种;进一步优选为含或不含稀土的y型分子筛、hy型分子筛、超稳y型分子筛、zsm-5型分子筛、具有五元环结构的高硅分子筛和beta分子筛中的至少一种;所述无机氧化物作为粘结剂,可以为二氧化硅(sio2)和/或三氧化二铝(al2o3);所述粘土作为基质(即载体),可以为选自高岭土、多水高岭土、蒙脱土、硅藻土、水滑石、膨润土中的至少一种。催化裂化装置平衡催化剂的微反活性(mat)≥60,优选≥62。下面通过具体实施方式来进一步说明本发明,但是本发明并不因此而受到任何限制。如图1所示,预提升介质经管线1由提升管反应器2底部进入,来自管线16的再生催化剂在预提升介质的提升作用下沿提升管反应器2向上加速运动,预热后的原料油经管线3与来自管线4的含有干气的雾化介质一起注入提升管反应器2,与提升管反应器已有的物流混合,原料油在热的催化剂上发生催化裂化反应,并向上加速运动。生成的反应油气和带炭的待生催化剂经管线5进入沉降器6中的旋风分离器,实现待生催化剂与反应油气的分离,反应油气进入集气室7,集气室中的反应油气经大油气管线17进入后续的分馏装置18,分离得到的干气产物经管线19引出,分离得到的液化气产物经管线20引出,分离得到的汽油产物经管线21引出,分离得到的柴油产物经管线22引出,分离得到的重油产物经管线23引出,一部分重油产物可返回装置回炼。各馏分的馏程根据炼厂实际需要进行调节。催化剂细粉由料腿返回沉降器,沉降器中的待生催化剂流向汽提段8,与来自管线9的蒸汽接触。从待生催化剂中汽提出的反应油气经旋风分离器后进入集气室7。汽提后的待生催化剂经待生滑阀调节后经斜管10进入再生器11,来自管线12的主风经主风分配器13后进入再生器,烧去位于再生器底部的密相床层中待生催化剂上的焦炭,使失活的待生催化剂再生,烟气经旋风分离器14的上部气体烟气管道15进入后续能量回收系统。再生后的催化剂经管线16的再生滑阀调节后返回提升管反应器。如图2所示,催化裂化装置包括复合反应器、沉降器103和再生器104,其中复合反应器由提升管反应器101和流化床反应器(包括扩径反应段102和缩径稀相出口段108)构成。预提升介质经管线105由提升管反应器101底部进入,来自管线116的再生催化剂在预提升介质的提升作用下沿提升管反应器向上加速运动;预热后的原料油经管线106与来自管线107的含有干气的雾化介质一起注入提升管反应器,与提升管反应器已有的物流混合,原料油在热的催化剂上发生催化裂化反应(主要为裂化反应),并向上加速运动进入流化床反应器的扩径反应段102中,在比较缓和的条件下继续发生催化裂化反应(主要为氢转移反应和/或芳构化反应);生成的反应油气和带炭的待生催化剂经流化床反应器的缩径稀相出口段108进入沉降器103中的旋风分离器109,进行待生催化剂与反应油气的分离;所分离的反应油气进入后续分馏装置分离得到高辛烷值汽油,催化剂细粉流向汽提段110,与来自管线111的蒸汽接触,汽提后的待生催化剂经待生滑阀调节后经斜管112进入再生器104。来自管线113的空气经空气分配器114后进入再生器,烧去位于再生器底部的密相床层中待生催化剂上的焦炭,使失活的待生催化剂再生,烟气经旋风分离器115的上部气体烟气管道进入后续能量回收系统,再生后的催化剂经管线116的再生滑阀调节后返回提升管反应器。下面将通过实施例对本发明作进一步说明,但并不因此而限制本发明。在实施例和对比例中,转化率根据如下公式计算得到:转化率=干气产率+液化气产率+汽油产率+焦炭产率;实施例和对比例中所使用的原料油为85重%减压蜡油与15重%减压渣油的混合原料,其性质见表1。实施例中雾化干气为催化裂化装置脱硫干气,其性质见表2。实施例和对比例中所使用催化剂的物化性质见表3,催化剂由中国石化催化剂分公司生产,商品牌号为hac和nto-12。汽油辛烷值测定法(研究法,ron)采用gb/t5487-2015方法进行测定。实施例1本实施例按照图1所示流程,在提升管反应器中型装置上进行试验,雾化介质为催化裂化脱硫干气,催化剂为hac。原料油预热至350℃,经干气雾化均匀后注入提升管反应器,与由水蒸气提升的高温再生催化剂(650℃)接触并进行催化裂化反应。反应油气从提升管反应器出口排出后在沉降器稀相经旋风分离器分离后进入后续的分馏装置。带炭的待生催化剂进入汽提段,汽提后的待生催化剂进入再生器烧焦再生,再生后的催化剂返回提升管反应器循环使用。操作条件和试验结果见表4。从表4可以看出,采用本发明提供的方法,原料转化率和汽油产率升高,汽油芳烃含量和辛烷值也升高,同时汽油烯烃含量降低。与对比例1相比,采用本发明提供的方法,原料油转化率提高3.08个百分点,汽油产率提高2.78个百分点;汽油烯烃含量为19.50重%,降低5.37个百分点;汽油芳烃含量为41.95重%,提高近7个百分点;汽油研究法辛烷值为93.6,提高1.2个单位。实施例2本实施例采用的试验装置和操作条件与实施例1相同,不同之处在于,雾化介质为干气与水蒸气的混合物,其中干气占雾化介质的重量比例为0.5。操作条件和试验结果见表4。从表4可以看出,采用本发明提供的方法,有利于提高原料转化率和汽油产率,汽油辛烷值升高,同时汽油烯烃含量降低。与对比例1相比,采用本发明提供的方法,原料油转化率提高1.22个百分点,汽油产率提高近1个百分点;汽油烯烃含量降低2.55个百分点,汽油芳烃含量提高3.80个百分点;汽油研究法辛烷值为93.0,提高0.6个单位。实施例3本实施例使用图2所示中型试验装置,其中提升管反应器的内径为18毫米,高度为6米,流化床反应器扩径反应段的内径为64毫米,高度为1米,流化床反应器缩径稀相出口段的内径为30毫米,高度为2.1米,原料的雾化介质为催化裂化干气,催化剂为hac。原料油预热至350℃,经干气雾化均匀后引入提升管反应器,与由水蒸气提升的高温再生催化剂(650℃)接触并进行催化裂化反应。操作条件和试验结果见表5。从表5可以看出,与对比例2相比,采用本发明提供的方法,原料油的转化率提高,汽油产率提高3.43个百分点,汽油烯烃含量降低4.7个百分点,汽油芳烃含量提高8.1个百分点,汽油研究法辛烷值高达95.0。实施例4本实施例使用的试验装置与实施例3相同,不同之处在于,催化剂使用nto-12。将原料油预热至350℃,经干气雾化均匀后引入提升管反应器,与由水蒸气提升的高温再生催化剂(650℃)接触并进行催化裂化反应。操作条件和试验结果见表5。从表5可以看出,与对比例2相比,采用本发明提供的方法,原料油转化率和汽油产率均有明显提高;汽油烯烃含量降低,汽油芳烃含量提高近4个百分点,汽油研究法辛烷值为94.2。对比例1本对比例按照图1所示流程,在提升管反应器中型装置上进行试验,提升管反应器的内径为18毫米,高度为6米,雾化介质为常规的水蒸气,催化剂为hac。原料油预热至350℃,经水蒸气雾化均匀后注入提升管反应器,与由水蒸气提升的高温再生催化剂(650℃)接触并进行催化裂化反应。油气从提升管反应器出口排出后在沉降器稀相经旋风分离器分离后进入后续分馏装置。带炭的待生催化剂进入汽提段,汽提后的待生催化剂进入再生器烧焦再生,再生后的催化剂返回提升管反应器循环使用。操作条件和试验结果见表4。对比例2本对比例按照图2所示流程,在提升管反应器中型装置上进行试验,雾化介质为常规的水蒸气,催化剂为hac。原料油预热至350℃,经水蒸气雾化均匀后注入提升管反应器,与由水蒸气提升的高温再生催化剂(650℃)接触并依次在提升管反应器和流化床反应器进行催化裂化反应。反应油气从流化床反应器出口排出后在沉降器稀相经旋风分离器分离后进入后续分馏系统。带炭的待生催化剂进入汽提段,汽提后的待生催化剂进入再生器烧焦再生,再生后的催化剂返回提升管反应器循环使用。操作条件和试验结果见表5。表1混合原料油性质项目数据密度(20℃),克/厘米30.9217运动粘度(80℃),毫米2/秒20.14凝点,℃29残炭,重量%1.95碱性氮,微克/克2180元素组成,重量%c87.36h12.40s0.39n0.46馏程,℃初馏点-5体积%35610体积%38330体积%42250体积%44770体积%48190体积%570表2雾化干气性质项目数据体积组成,%二氧化碳1.20氮气9.54氢气25.98甲烷29.24乙烷14.20乙烯15.14丙烷1.02丙烯2.34异丁烷0.64正丁烷0.09正丁烯0.08异丁烯0.10反丁烯0.06顺丁烯0.041,3-丁二烯-戊烷0.14戊烯0.08c6+0.11合计100.00表3催化剂的主要物化性质项目hacnto-12化学组成,重量%al2o350.545.5sio240.752.4re2o33.30.095na2o0.350.129物理性质比表面积,(米2/克)60.99116总孔体积,(厘米3/克)0.0170.183筛分组成,重量%0-40微米15.29.340-80微米64.074.2>80微米20.816.5微反活性(800℃,8h),%7065表4操作条件和产物分布表5操作条件和产物分布当前第1页12