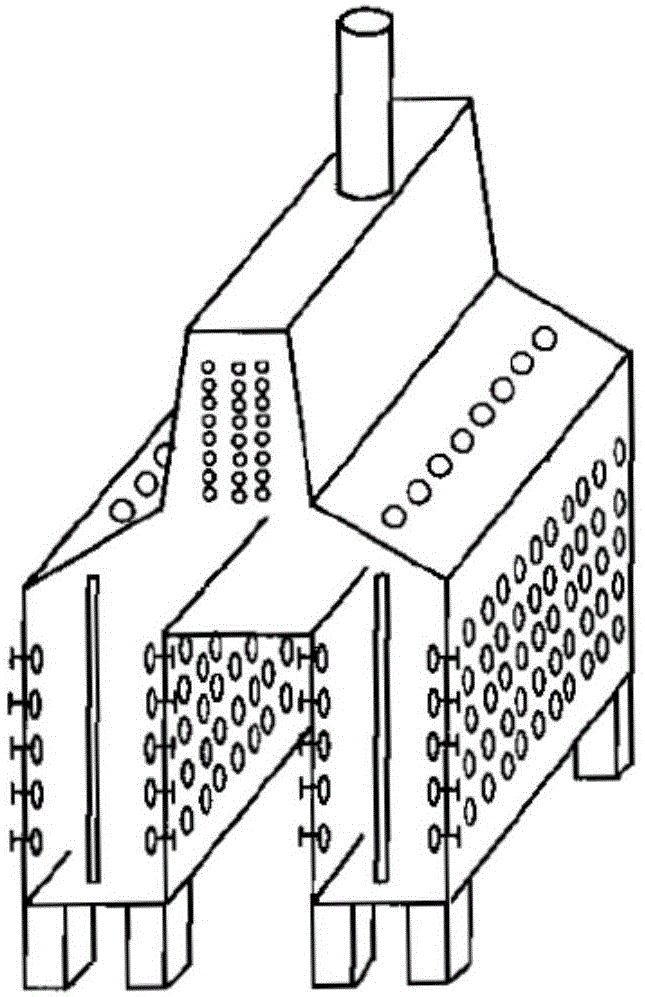
本发明涉及石油化工设备领域,更具体地,涉及一种乙烯裂解炉。
背景技术:
:采用石油烃类蒸汽裂解法制乙烯的乙烯裂解炉,通常包括辐射段、对流段、急冷锅炉、高压汽包和引风机等组成部分。在乙烯裂解炉中,辐射段的辐射炉管内进行的是强吸热的裂解反应,反应所需的热量由炉膛内的供热设备(即燃烧器)消耗燃料来供给。按照在裂解炉炉膛中的安装位置的不同,燃烧器可分为底部燃烧器和侧壁燃烧器两种,因此裂解炉的供热方式可分为三种:全底部燃烧器供热、全侧壁燃烧器供热和底部侧壁联合供热。图1所示为全部侧壁燃烧器供热的裂解炉的示意图。这种供热方式具有供热均匀、有利于减小炉膛宽度等优点,在早期的裂解炉上多有应用。但是,由于燃烧器数量较多,暴露出投资高、燃料气管线布置复杂、现场操作调整和检查维修工作量大等缺点,且只能使用气体燃料,此外炉膛外壁温度容易超温、散热损失大,在裂解炉应用中逐渐趋于被淘汰。而且此种侧壁燃烧器为预混式燃烧器,其产生的nox较高。图2所示为全部底部燃烧器供热的裂解炉的示意图。由于其燃烧器数量减少,使得燃烧器布置及燃料管线配管设计工作的难度降低,生产中操作调整和日常维护更加便利,并且可以扩大燃料的使用范围,目前在多个裂解炉专利商的设计中均有大量的应用。其缺点是受燃烧器负荷及供热高度的限制,必须采取措施如优化炉膛尺寸及燃烧器设计来改善炉膛高度方向的热量分布,而且存在底部过热的风险。当炉膛高度高和底部燃烧器负荷大时还会出现火焰翻转和舔炉管现象。目前底部燃烧器发展较快,而且其可采用分级燃料及烟气再循环技术,nox排放较低。图3所示为底部侧壁联合供热的裂解炉的示意图。底部侧壁联合供热折中考虑了前两种供热方式的优缺点,但是在应用于大型化裂解炉时,其仍存在侧壁燃烧器附近炉膛外壁容易超温以及底部燃烧器过热和火焰翻转等问题。其nox排放介于全部底部供热和全部侧壁供热之间,在现在环保要求越来越高的情况下难以满足排放标准。传统供热方式除了上述问题之外,随着裂解炉大型化发展趋势及对操作自动化要求的提高,还面临其它新的挑战:单个燃烧器负荷过大、火焰翻转舔炉管的概率大大增加,炉管局部过热,运行周期缩短的问题出现,装置长期平稳安全运转受到严重影响;另外,炉膛高度的增加使得侧壁燃烧器数量继续增加,增大了炉膛外壁温度超温的风险,加重了现场操作人员日常检维修工作的强度,这也不利于满足日益严格的节能减排及操作自动化要求。因此,期待开发一种新型乙烯裂解炉,以缓解乙烯裂解炉的燃烧系统设计复杂、单个燃烧器负载过高等问题。技术实现要素:本发明的目的是提出一种乙烯裂解炉,以提高燃烧器的供热效率、减少燃烧器的数量并减少nox的排放量。本发明提出了一种乙烯裂解炉,包括:辐射段;对流段,所述对流段与所述辐射段连通;至少一组辐射炉管,每组辐射炉管平行于所述辐射段的炉膛宽度方向设置;底部燃烧器,所述底部燃烧器以阵列方式设于所述辐射段的炉膛底部,每组辐射炉管分别设于相邻两排底部燃烧器之间,且与所述相邻两排底部燃烧器的距离相等;侧壁燃烧器,所述侧壁燃烧器设于所述辐射段的炉膛上部侧墙。优选地,所述底部燃烧器为非预混式燃烧器,所述侧壁燃烧器的火焰方向为水平方向,火焰为扁平火焰。优选地,所述底部燃烧器的火焰方向朝向所述辐射段的顶部。优选地,其特征在于,每组辐射炉管包括两程炉管,两程炉管的出口管集中设置,两程炉管的入口管分别设于所述出口管的两侧。优选地,每排底部燃烧器平行于所述辐射段的炉膛宽度方向设置,每列底部燃烧器平行于所述辐射段的炉膛长度方向设置。优选地,所述侧壁燃烧器分别以阵列方式设于所述炉膛的两个侧墙上,在每排侧壁燃烧器中,各侧壁燃烧器沿所述辐射段的炉膛长度方向等间距设置。优选地,所述辐射段的炉膛端墙上设有至少一排侧壁燃烧器。优选地,紧邻炉膛的端墙的侧壁燃烧器的负荷是非紧邻所述端墙的侧壁燃烧器的负荷的一半,和/或紧邻炉膛的端墙的底部燃烧器的负荷是非紧邻所述端墙的底部燃烧器的负荷的一半。优选地,所述侧壁燃烧器的供热负荷占总供热负荷的比例r满足:0.1≤r≤0.5。优选地,所述侧壁燃烧器的上底面与所述辐射段的炉膛底部之间的距离为h1,所述辐射度的炉膛顶部与炉膛底部之间的距离为h,h1/h满足:0.35≤h1/h≤0.65。本发明的有益效果在于:1、本发明的辐射炉管平行于炉膛宽度方向设置,且每组辐射炉管设于相邻两排底部燃烧器之间,即底部燃烧器平行布置于辐射段炉管的两侧。这种布置方式在满足炉管供热要求的前提下可排布更多的辐射炉管,节省炉管的排布空间;另一方面,不同的辐射炉管可以裂解不同的原料,提高了原料操作的灵活性。2、侧壁燃烧器为非预混式燃烧器,单个侧壁燃烧器相比于传统贴壁型式侧壁燃烧器能够提供更大的供热负荷,从而可减少燃烧器的使用数量,并且降低底部燃烧器的负荷,有利于降低裂解炉的制造成本和操作维护的成本、减少备品备件的数量、简化燃烧器布置及燃料管线的配管设计复杂度,既降低了投资,也有利于降低炉膛外壁温度从而降低热损失。此外,通过提高单个侧壁燃烧器的供热负荷能力,还有利于灵活合理地调整侧壁和底部供热比率关系,满足裂解反应所需的理想的供热要求,降低nox排放。3、每组辐射炉管包括两程炉管,两程炉管的出口管集中设置,两程炉管的入口管分别设于出口管的两侧。由于侧壁燃烧器设于炉膛上部侧墙,即靠近入口管,在辐射炉管入口处能够快速升温以达到裂解反应所需要的高温,在辐射炉管出口处能够避免温度过高并发生二次反应导致结焦,以及避免炉管外壁温度过高而影响裂解炉的运行周期和炉管使用寿命。附图说明通过结合附图对本发明示例性实施例进行更详细的描述,本发明的上述以及其它目的、特征和优势将变得更加明显,其中,在本发明示例性实施例中,相同的附图标记通常代表相同部件。图1示出了现有的全部侧壁燃烧器供热的裂解炉的示意图。图2示出了现有的全部底部燃烧器供热的裂解炉的示意图。图3示出了现有的底部侧壁联合供热的裂解炉的示意图。图4示出了根据本发明的一个实施例的乙烯裂解炉的结构示意图。图5示出了根据本发明的一个实施例的辐射段的正面示意图。图6示出了根据本发明的一个实施例的辐射段的侧视图。图7示出了根据本发明的一个实施例的辐射段的俯视图。图8示出了根据本发明的一个实施例的辐射段的透视图。附图标记说明:1、辐射段2、底部燃烧器3、侧壁燃烧器4、辐射炉管5、对流段6、急冷锅炉7、高压汽包8、引风机9、出口管10、入口管具体实施方式下面将参照附图更详细地描述本发明。虽然附图中显示了本发明的优选实施例,然而应该理解,可以以各种形式实现本发明而不应被这里阐述的实施例所限制。相反,提供这些实施例是为了使本发明更加透彻和完整,并且能够将本发明的范围完整地传达给本领域的技术人员。在本发明中,如无明确相反解释,辐射炉管中的“入口管”可指烃料从其顶部进入辐射段的辐射炉管,“出口管”可指裂解后的烃料从其顶部进入冷凝锅炉的辐射炉管;“上、下、左、右、前、后、纵”可参照图4,其中“上、下”可分别指朝向辐射段顶部和底部的方向,“左、右”可分别指图4相对于读者的左和右的方向,“前、后”可分别指图4中垂直于纸面向外和向内的方向,“纵”可指从辐射段顶部至辐射段底部的方向。乙烯裂解炉的对流段炉膛横截面一般为长方形,炉膛由相对的两个侧墙和相对的两个端墙围绕形成,顶部为炉顶,与对流段连通。侧壁燃烧器设置于侧墙上。炉膛宽度方向是指平行于端墙的方向,炉膛长度方向是指平行于侧墙的方向。根据本发明实施例的乙烯裂解炉包括:辐射段;对流段,对流段与辐射段连通;至少一组辐射炉管,每组辐射炉管平行于辐射段的炉膛宽度方向设置;底部燃烧器,底部燃烧器以阵列方式设于辐射段的炉膛底部,每组辐射炉管分别设于相邻两排底部燃烧器之间,且与相邻两排底部燃烧器的距离相等;侧壁燃烧器,侧壁燃烧器设于辐射段的炉膛上部侧墙。该乙烯裂解炉在辐射段内设置至少一组辐射炉管,且每组辐射炉管均平行于辐射段的炉膛宽度方向,在辐射段的炉膛下部以阵列方式设置底部燃烧器,且辐射炉管设于相邻两排底部燃烧器之间,且与相邻两排底部燃烧器的距离相等,在辐射段的炉膛上部侧墙设置侧壁燃烧器。传统的辐射炉管沿炉膛长度方向布置,本发明的辐射炉管布置方向与传统的辐射炉管布置方向相垂直。本发明中,每组辐射炉管设于相邻两排底部燃烧器之间,即底部燃烧器平行布置于辐射段炉管的两侧,每排底部燃烧器的布置方向亦与传统的底部燃烧器的布置方向相垂直。采用本发明的辐射炉管及底部燃烧器布置方式,在满足炉管供热要求的前提下可排布更多的辐射炉管,节省炉管的排布空间;另一方面,不同组的辐射炉管可以裂解不同的原料,即提高了原料操作的灵活性。在一个示例中,侧壁燃烧器为非预混式燃烧器,侧壁燃烧器的火焰方向为水平方向,火焰为扁平火焰。底部燃烧器的火焰方向朝向辐射段的顶部。每个侧壁燃烧器的供热负荷可以相同也可以不同,每个底部燃烧器的供热负荷可以相同也可以不同。传统的全部侧壁燃烧器供热和底部侧壁联合供热的裂解炉中所采用的侧壁燃烧器都是火焰朝向辐射炉管的贴壁型式侧壁燃烧器。这种火焰朝向辐射炉管的贴壁型式侧壁燃烧器在供热负荷大的情况下容易发生火焰翻卷、舔炉管、上下燃烧器的火焰交叉干涉等现象,因此单个贴壁型式侧壁燃烧器适合提供的供热负荷较小,为达到目标负荷则需要设置较多燃烧器。在本发明实施例中,侧壁燃烧器采用非预混式燃烧器,侧壁燃烧器的火焰方向为水平方向,火焰为扁平火焰,可使得单个侧壁燃烧器相比于传统贴壁型式侧壁燃烧器能够提供更大的供热负荷,从而可减少燃烧器的使用数量,并且降低底部燃烧器的负荷。这有利于降低裂解炉的制造成本和操作维护的成本、减少备品备件的数量、简化燃烧器布置及燃料管线的配管设计复杂度,也有利于降低炉膛外壁温度从而降低热损失。而且,通过提高单个侧壁燃烧器的供热负荷能力,还有利于灵活合理地调整侧壁和底部供热比率关系,满足裂解反应所需的理想的供热要求。另外,由于传统的贴壁型式侧壁燃烧器的火焰方向朝向辐射炉管,仅能采用气体燃料,且其产生的nox较高。本发明的侧壁燃烧器采用非预混式燃烧器,可利用燃料分级和烟气循环技术,相比于传统贴壁型式侧壁燃烧器能大大降低nox的排放量。发明人对现有的各种供热形式的乙烯裂解炉的优缺点进行深入分析后认为,在辐射炉管入口处,由于原料升温、转化率增长快,需要大量吸热,故要求供热强度大、需要快速升温以达到裂解反应所需要的高温,而在辐射炉管出口处,由于一次反应的活化能高于二次反应的活化能,如果温度过高,极易发生二次反应并结焦,同时导致炉管外壁温度过高,造成裂解炉运行周期缩短,并会对炉管造成一定损害。而现有的各种供热形式的乙烯裂解炉都没能很好地解决上述问题。因此,在一个示例中,每组辐射炉管包括两程炉管,两程炉管的出口管集中设置,两程炉管的入口管分别设于出口管的两侧。此外,由于侧壁燃烧器设于炉膛上部侧墙,即靠近入口管,可以只对入口管(第一程管)加热以实现炉管入口处的快速升温。还可以通过调整侧壁燃烧器的火焰形状和优化侧壁燃烧器的排布位置,来满足裂解反应的以下要求:在辐射炉管入口处快速升温以达到裂解反应所需要的高温,在辐射炉管出口处,避免温度过高并发生二次反应导致结焦,以及避免炉管外壁温度过高而影响裂解炉的运行周期和炉管使用寿命。在一个示例中,每排底部燃烧器平行于辐射段的炉膛宽度方向设置,每列底部燃烧器平行于辐射段的炉膛长度方向设置,每组辐射炉管分别设于相邻两排底部燃烧器之间,且与相邻两排底部燃烧器的距离相等,这样的布置可以保证每组辐射炉管两侧及各组辐射炉管都得到均匀供热。在一个示例中,侧壁燃烧器分别以阵列方式设于炉膛的两个侧墙上,在每排侧壁燃烧器中,各侧壁燃烧器沿辐射段的炉膛长度方向等间距设置。侧壁燃烧器靠近入口管,可以只对入口管加热以实现炉管入口处的快速升温。阵列方式设置可实现各组炉管均匀供热。在一个示例中,辐射段的炉膛端墙上设有至少一排侧壁燃烧器。紧邻端墙的侧壁燃烧器的负荷是非紧邻端墙的侧壁燃烧器的负荷的一半,和/或紧邻端墙的底部燃烧器的负荷是非紧邻端墙的底部燃烧器的负荷的一半。这样能够保证紧邻端墙的辐射炉管与非紧邻端墙的辐射炉管受热情况一致,即能够满足每组辐射炉管两侧及各组辐射炉管都得到均匀供热。侧壁燃烧器的供热负荷占总供热负荷的比例r满足:0.1≤r≤0.5。发明人经过大量理论仿真和实测实验,认为当0.2≤r≤0.5、特别地当0.25≤r≤0.4时,更有利于使得辐射段中沿高度方向的热量分布更为合理。各个侧壁燃烧器的供热负荷可以是相同和不同的。各个底部燃烧器的供热负荷可以是相同和不同的。侧壁燃烧器的上底面与辐射段的炉膛底部之间的距离为h1,辐射度的炉膛顶部与炉膛底部之间的距离为h,h1/h满足:0.35≤h1/h≤0.65。当0.35≤h1/h≤0.65、特别地当0.4≤h1/h≤0.6时,有利于进一步提高供热效率。此外,乙烯裂解炉还包括急冷锅炉、高压汽包、引风机,急冷锅炉与辐射炉管连通,高压汽包与急冷锅炉连通,引风机连通至对流段顶部。烃料在辐射炉管中被裂解后进入急冷锅炉,以实现后续的急冷-分馏等操作。引风机连通至对流段顶部以引入空气,空气可经过对流段进入辐射段参与燃烧。高压汽包与急冷锅炉连通,可收集来自急冷锅炉的高温蒸汽。实施例图4示出了根据本发明实施例的乙烯裂解炉的结构示意图,图5-图8分别示出了根据本发明实施例的辐射段的正面示意图、侧视图、俯视图和透视图。如图4-8所示,根据本发明实施例的乙烯裂解炉包括:辐射段1;对流段5,与辐射段1连通;6组辐射炉管4,每组辐射炉管4平行于辐射段1的炉膛宽度方向(图7中的竖直方向)设置;底部燃烧器2,底部燃烧器2共21个,以3乘7的阵列方式设于辐射段1的炉膛底部,每组辐射炉管4分别设于相邻两排底部燃烧器之间,且与相邻两排底部燃烧器的距离相等;侧壁燃烧器3,侧壁燃烧器3共28个,分别以2乘7的阵列方式设于辐射段1的炉膛上部的两个侧墙;急冷锅炉6,与辐射炉管4连通;高压汽包7,与急冷锅炉6连通;引风机8,连通至对流段5顶部。其中,每组辐射炉管4包括两程炉管,两程炉管的出口管10集中设置,两程炉管的入口管9分别设于出口管10的两侧,如图6所示。每排底部燃烧器平行于辐射段的炉膛宽度方向(图7中的竖直方向)设置,每列底部燃烧器平行于辐射段的炉膛长度方向(图7中的水平方向)设置。侧壁燃烧器3为非预混式燃烧器,底部燃烧器2的火焰方向朝向辐射段1的顶部,侧壁燃烧器3的火焰方向为水平方向。侧壁燃烧器3和底部燃烧器2均采用气体燃料。紧邻端墙的侧壁燃烧器的负荷是非紧邻端墙的侧壁燃烧器的负荷的一半,紧邻端墙的底部燃烧器的负荷是非紧邻端墙的底部燃烧器的负荷的一半。各个非紧邻端墙的底部燃烧器的供热负荷相同,各个非紧邻端墙的侧壁燃烧器的供热负荷也相同。侧壁燃烧器3的供热负荷占总供热负荷的比例r约为0.4,侧壁燃烧器3的上底面辐射段的炉膛底部之间的距离h1=7m,辐射段1的炉膛顶部与炉膛底部之间的距离为h=13m,h1/h≈0.54。根据示例性实施例的乙烯裂解炉与传统的底部侧壁联合供热的乙烯裂解炉的对比结果如表1所示:表1实施例与传统底侧联合乙烯裂解炉对比实施例传统底侧联合乙烯裂解炉底侧供热比例60:4070:30所有底部燃烧器数量/个2136底部燃烧器(紧邻端墙)数量/个6底部燃烧器(紧邻端墙)负荷/mw1.371.61底部燃烧器(非紧邻端墙)数量/个15底部燃烧器(非紧邻端墙)负荷/mw2.71.61所有侧壁燃烧器数量/个2872侧壁燃烧器排数22侧壁燃烧器(紧邻端墙)数量/个8侧壁燃烧器(紧邻端墙)负荷/mw0.690.344侧壁燃烧器(非紧邻端墙)数量/个20侧壁燃烧器(非紧邻端墙)负荷/mw1.370.344nox排放量/mg/nm380~90120~150从表1可以看出,本发明的技术方案可以显著提高燃烧器的供热效率、减少燃烧器的数量并减少nox的排放量。以上已经描述了本发明的各实施例,上述说明是示例性的,并非穷尽性的,并且也不限于所披露的各实施例。在不偏离所说明的各实施例的范围和精神的情况下,对于本
技术领域:
的普通技术人员来说许多修改和变更都是显而易见的。当前第1页1 2 3