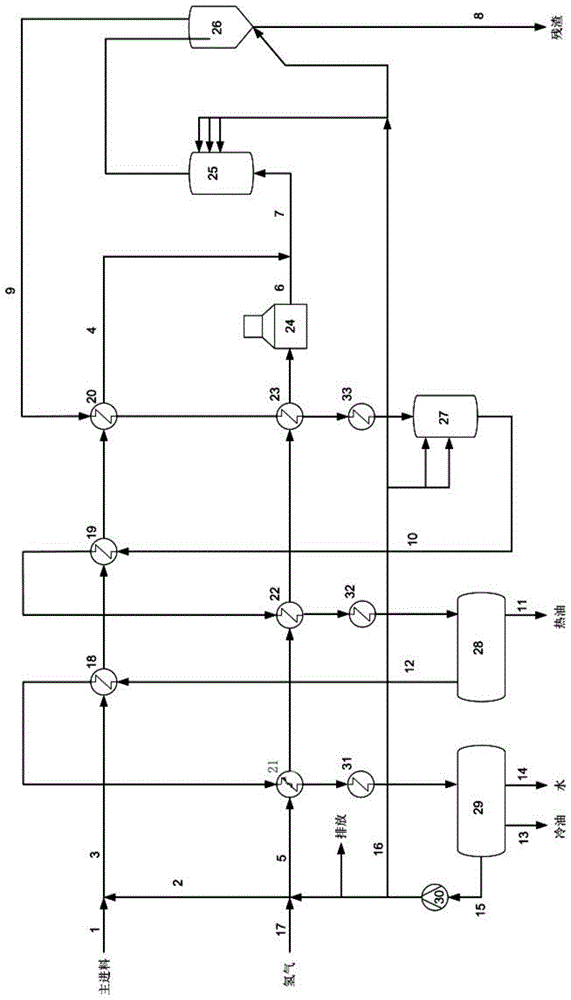
本发明属于液相重油加氢
技术领域:
,涉及液相加氢进料预热,特别涉及一种液相加氢进料预热系统。
背景技术:
:对于如来自油页岩及焦油砂的重油、常压渣油、煤焦油或沥青等液相进料的加氢工艺中,进料需要通过加热炉加热到液相反应器所需的温度。因此,加热炉在任何液相加氢反应中都是重要的关键设备,由于液相反应器需要较高的反应温度,加之进料需要混合氢气,因此加热炉的炉管中氢分压较高,管道壁温度及总压也对应很高,这将限制了液相加氢工艺的原材料。另外,由于加热进料包括气体、液体以及固体的多相流,导致加热炉的设计、压力损失及传热的计算存在很大的不确定性,且高温易磨损对加热炉的使用非常不利。由于进料条件苛刻,加热炉易造成炉管内部结垢及管内产品结焦的问题,加热炉内进料加热时间受限,同时容易引起炉管破裂等,工艺操作安全性差。技术实现要素:本发明的目的在于针对现有技术的缺陷和不足,提供一种液相加氢进料预热系统及工艺,操作安全,能够将液相进料及气相进料进行分别逆流换热预热达到所需温度,保证工艺参数,且对加热炉的损伤较小,不会出现结焦结垢等现象,保证操作安全性;同时能够对热量及氢气进行有效循环利用,提高能源利用率。本发明解决其技术问题是通过以下技术方案实现的:一种液相加氢进料预热系统,其特征在于:包括液相进料预热单元、气相进料预热单元、液相反应器、第一热分离器、气相反应器、第二热分离器、冷分离器及压缩机;所述液相进料预热单元包括依次顺序连接的液相进料管、第一液相换热器、第二液相换热器及第三液相换热器,所述第三液相反应器连接至所述液相反应器,所述气相进料预热单元包括依次顺序连接的气相进料管、第一气相换热器、第二气相换热器、第三气相换热器及加氢加热炉,所述加氢加热炉连接至所述液相反应器,所述液相反应器连接至所述第一热分离器,所述第一热分离器的底端设置有残渣排出管,所述第一热分离器的顶端回流连接至所述第三液相换热器及第三气相换热器,所述第三气相换热器连接至所述气相反应器,所述气相反应器的顶端连接至所述第二液相换热器及第二气相换热器,所述第二气相换热器连接至所述第二热分离器,所述第二热分离器的底端分离热油,顶端连接至所述第一液相换热器及第一气相换热器,所述第一气相换热器连接至所述冷分离器,所述冷分离器底端分离冷油,顶端经过压缩机分别连接至所述液相进料管及气相进料管。而且,所述冷分离器经过压缩机后连接至所述液相反应器、第一热分离器及气相反应器。而且,所述第三气相换热器与所述气相反应器之间设置有第三蒸汽发生器,所述第二气相换热器与所述第二热分离器之间设置有第二蒸汽发生器,所述第一气相换热器与所述冷分离器之间设置有第一蒸汽发生器。而且,所述第一、第二、第三液相换热器及第一、第二、第三气相换热器均为管束式换热器。一种液相加氢进料预热工艺,其特征在于:所述工艺流程为:1)混合进料:液相进料管中加入含有添加剂或催化剂的液相进料,依次通过第一、第二及第三液相换热器,气相进料管中加入气相氢气并依次通过第一、第二及第三气相换热器后进入加氢加热炉中加热,加氢加热炉的反应温度为300~650℃,所述液相进料与加热后的气相氢气混合进料至液相反应器,所述液相反应器的进料氢油比为500~1500标升/kg,反应温度为400~500℃,反应压力为150~300bar;2)逆流换热:所述液相反应器的产物进入第一热分离器进行分离,底端通过残渣排出管排出残渣,顶端气相逆流至第三液相换热器及第三气相换热器分别与液相进料及气相氢气进行连续换热,经第三蒸汽发生器调节温度后,在气相反应器中进行反应,反应温度为370~390℃,气相反应器的顶端逆流至第二液相换热器及第二气相换热器分别与液相进料及气相氢气进行连续换热,经第二蒸汽发生器调节温度后在第二热分离器中分离出热油,第二热分离器的分离温度为240~290℃,第二热分离器的顶端逆流至第一液相换热器及第一气相换热器分别与液相进料及气相氢气进行连续换热,经过第一蒸汽发生器调节温度后送至冷分离器分离分离出冷油馏分、废水及气相三相,冷分离器的分离温度为40~55℃;3)循环反应:冷分离器的气相经压缩机之后分别连接至液相反应器、第一热分离器、气相反应器、液相进料管及气相进料管进行循环利用。而且,所述步骤1)中气相进料管的氢气进气量为所述液相反应器所需氢气总量的20%~95%。本发明的优点和有益效果为:1、本发明的液相加氢进料预热系统,将第一热分离器气相产品的热量通过独立的换热器进行逆流换热提供给液相进料,加氢气体在加氢加热炉中进一步加热,并同时与第一热分离器气相产品的热量进行换热,最后与液相进料混合后达到进入液相反应器所需的温度,预热效果好,减少加热炉的结焦及结垢,保证能源热量的有效循环利用。2、本发明的液相加氢进料预热系统,冷分离器经过压缩机后连接至液相反应器、第一热分离器及气相反应器,经过压缩机后的循环氢作为急冷气物流输入,可实现相反应器、第一热分离器及气相反应器的温度调节。3、本发明的液相加氢进料预热系统,第三气相换热器与气相反应器之间设置有第三蒸汽发生器,第二气相换热器与所述第二热分离器之间设置有第二蒸汽发生器,第一气相换热器与所述冷分离器之间设置有第一蒸汽发生器,能够有效调节进入气相反应器、第二热分离器及冷分离器的进气温度,保证气相物料的有效循环利用。4、本发明的液相加氢进料预热系统,第一、第二、第三液相换热器及第一、第二、第三气相换热器均为管束式换热器,温差压力小,换热效率高。5、本发明设计科学合理,操作安全,能够将液相进料及气相进料进行分别逆流换热预热达到所需温度,保证工艺参数,且对加热炉的损伤较小,不会出现结焦结垢等现象,保证操作安全性;同时能够对热量及氢气进行有效循环利用,提高能源利用率。附图说明图1为本发明的工艺流程图。附图标记说明1-液相进料管、2-合流氢气、3-混合进料、4-换热进料、5-加氢进料、6-加热氢气、7-混合进料、8-残渣排出管、9-气相逆流进料、10-气相反应器出料、11-热油、12-第二热分离器出料、13-冷油、14-废水、15-冷分离器出料、16-循环氢、17-气相进料管、18-第一液相换热器、19-第二液相换热器、20-第三液相换热器、21-第一气相换热器、22-第二气相换热器、23-第三气相换热器、24-加氢加热炉、25-液相反应器、26-第一热分离器、27-气相反应器、28-第二热分离器、29-冷分离器、30-压缩机、31-第一蒸汽发生器、32-第二蒸汽发生器、33-第三蒸汽发生器。具体实施方式下面通过具体实施例对本发明作进一步详述,以下实施例只是描述性的,不是限定性的,不能以此限定本发明的保护范围。一种液相加氢进料预热系统,其创新之处在于:包括液相进料预热单元、气相进料预热单元、液相反应器25、第一热分离器26、气相反应器27、第二热分离器28、冷分离器29及压缩机30;所述液相进料预热单元包括依次顺序连接的液相进料管1、第一液相换热器18、第二液相换热器19及第三液相换热器20,所述第三液相反应器连接至所述液相反应器,所述气相进料预热单元包括依次顺序连接的气相进料管17、第一气相换热器21、第二气相换热器22、第三气相换热器23及加氢加热炉24,所述加氢加热炉连接至所述液相反应器,所述液相反应器连接至所述第一热分离器,所述第一热分离器的底端设置有残渣排出管8,所述第一热分离器的顶端回流连接至所述第三液相换热器及第三气相换热器,所述第三气相换热器连接至所述气相反应器,所述气相反应器的顶端连接至所述第二液相换热器及第二气相换热器,所述第二气相换热器连接至所述第二热分离器,所述第二热分离器的底端分离热油,顶端连接至所述第一液相换热器及第一气相换热器,所述第一气相换热器连接至所述冷分离器,所述冷分离器底端分离冷油,顶端经过压缩机分别连接至所述液相进料管及气相进料管。冷分离器经过压缩机后连接至液相反应器、第一热分离器及气相反应器,经过压缩机后的循环氢作为急冷气物流输入,可实现相反应器、第一热分离器及气相反应器的温度调节。第三气相换热器与气相反应器之间设置有第三蒸汽发生器33,第二气相换热器与所述第二热分离器之间设置有第二蒸汽发生器32,第一气相换热器与所述冷分离器之间设置有第一蒸汽发生器31,能够有效调节进入气相反应器、第二热分离器及冷分离器的进气温度,保证气相物料的有效循环利用。第一、第二、第三液相换热器及第一、第二、第三气相换热器均为管束式换热器,温差压力小,换热效率高。一种液相加氢进料预热工艺,其创新之处在于:所述工艺流程为:1)混合进料:液相进料管中加入含有添加剂或催化剂的液相进料与加氢进料及循环氢的合流氢气2混合形成混合进料3,该混合进料依次通过第一、第二及第三液相换热器后成为换热进料4,气相进料管中加入气相氢气,该加氢进料5并依次通过第一、第二及第三气相换热器后进入加氢加热炉中加热,气相进料管的氢气进气量为所述液相反应器所需氢气总量的20%~95%,加氢加热炉的反应温度为300~650℃,预热后的加热氢气6与换热进料混合形成混合进料7,该混合进料进入液相反应器,所述液相反应器的进料氢油比为500~1500标升/kg,反应温度为400~500℃,反应压力为150~300bar;2)逆流换热:所述液相反应器的产物进入第一热分离器进行分离,底端通过残渣排出管排出残渣,顶端的气相逆流进料9逆流至第三液相换热器及第三气相换热器分别与液相进料及气相氢气进行连续换热,经第三蒸汽发生器调节温度后,在气相反应器中进行反应,反应温度为370~390℃,气相反应器顶端的气相反应器出料10逆流至第二液相换热器及第二气相换热器分别与液相进料及气相氢气进行连续换热,经第二蒸汽发生器调节温度后在第二热分离器中分离出热油11,第二热分离器的分离温度为240~290℃,第二热分离器顶端的第二热分离器出料12逆流至第一液相换热器及第一气相换热器分别与液相进料及气相氢气进行连续换热,经过第一蒸汽发生器调节温度后送至冷分离器分离分离出冷油13、废水14及冷分离器气相出料15三相,冷分离器的分离温度为40~55℃;3)循环反应:冷分离器的冷分离器气相出料经压缩机之后的循环氢16分别连接至液相反应器、第一热分离器、气相反应器、液相进料管及气相进料管进行循环利用。实施例1选择阿拉伯轻质原油的减压渣油作为原料,混合1wt%的固体添加剂/催化剂,液相反应器入口氢油比750标立/吨油,液相反应器操作温度470℃,气相反应器操作温度370~390℃,液相反应器热高分操作温度460℃,第二热分离器操作温度270℃,冷分离器操作温度40℃,工艺参数见表1所示。表1工艺参数表物流123456温度c1804015741140480压力barg210.0210.0210.0208.5210.0207.5流量kg/hr101002021030210302722722物流789101112温度c423460460390270270压力barg207.5206.0206.0205.0204.0204.0流量kg/hr110248981312615412480110611从例中可以看出,本发明不需要重油液相进料加热炉。实施例2选择阿拉伯轻质原油的减压渣油作为原料,混合1wt%的固体添加剂/催化剂,液相反应器入口氢油比750标立/吨油,液相反应器操作温度450℃,气相反应器操作温度360-380℃,悬浮床热高分操作温度460℃,第二热分离器操作温度270℃,冷分离器操作温度40℃,工艺参数见表2所示。表2工艺参数表物流123456温度c1804015739640510压力barg210.0210.0210.0208.5210.0207.5流量kg/hr101002021030210302722722物流789101112温度c416440440380270270压力barg207.5206.0206.0205.0204.0204.0流量kg/hr1102315111251315398480310594物流1314151617温度c4040404340压力barg203.0203.0203.0210.0210.0流量kg/hr48161857615000583从例中可以看出,本发明不需要重油液相进料加热炉。尽管为说明目的公开了本发明的实施例和附图,但是本领域的技术人员可以理解:在不脱离本发明及所附权利要求的精神和范围内,各种替换、变化和修改都是可能的,因此,本发明的范围不局限于实施例和附图所公开的内容。当前第1页12