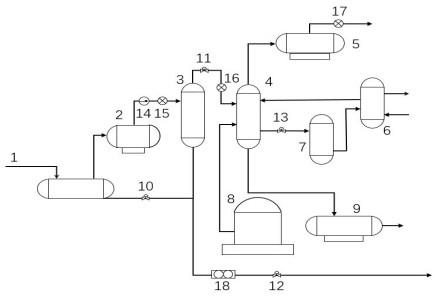
1.本发明涉及一种中含硫页岩油伴生气的络合铁脱硫工艺流程,涉及到含硫天然气的分离,净化,脱硫领域。
背景技术:2.页岩油是指以页岩为主的页岩层系中所含的石油资源。其中包括泥页岩孔隙和裂缝中的石油,也包括泥页岩层系中的致密碳酸岩或碎屑岩邻层和夹层中的石油资源。伴生气指的是因为油田在开采过程中,在油层间会出现伴随石油液体出现的气体,主要成分是甲烷,通常含有大量的乙烷和碳氢重组分。
3.在我国,目前已探明的天然气气田中,含硫天然气气田约占31.7%,必须对其进行净化处理,使其满足一定的技术指标。自20世纪60年代以来,随着络合铁法脱硫工艺的不断发展,该工艺已逐渐成为国内外的研究热点。由于络合铁法脱硫工艺具有流程简单,脱硫效率高,工艺经济合理等优点,广泛应用于天然气、石油化工领域。但中含硫天然气及潜硫量高的络合铁脱硫装置目前在工业化中还存在许多不足之处,基于此现状,对中含硫天然气的络合铁脱硫装置从工艺选择、装置优化、工程设计以及投产存在问题等方面进行了设计,以期对天然气络合铁脱硫工艺的研究与设计有一定的指导意义。
4.根据国家含硫气藏标准分类,硫化氢含量在5000~300000mg/m3为中含硫天然气,中含硫页岩油伴生气由于h2s浓度大、含水量大、温度高,脱硫处理系统设计不完善,经济性与安全性均不理想。开展中含硫页岩油伴生气脱硫工艺技术研究,实现高效脱硫的目的,确定最优的中含硫页岩油伴生气脱硫工艺流程。
5.络合铁法脱硫技术是一种以络合铁为催化剂的湿式氧化脱除硫化氢的方法,其特点是直接将气体中的h2s转变成元素s,吸收后气体中h2s的含量小于20ppm,是一种工艺简单、工作硫容高且环保无毒的新型脱硫技术,克服了传统脱硫工艺硫容量低、脱硫工艺复杂、副盐生成率高、环境污染严重等弊端,硫磺回收率达到99.99%,净化后的尾气焚烧后烟气二氧化硫含量降低到20mg/nm3,可满足不断提升的环保指标。络合铁脱硫工艺为脱除硫化氢提供了一种恒温、低成本的运行方法。其化学反应原理是利用空气中的氧气氧化气相中的硫化氢,使硫化氢被氧化为单质硫。
技术实现要素:6.本发明的目的是:提供一种适用于中含硫页岩油伴生气的络合铁脱硫工艺流程,可以有效分离并脱除页岩油伴生气中的硫化氢,同时对脱硫后产生的恶臭气体进行处理。
7.一种适用于中含硫页岩油伴生气的络合铁脱硫工艺流程实验装置,由原料气分离器1、冷却装置2、立式分离器3、湿式脱硫塔4、沉降分离器5、再生塔6、闪蒸罐7、碱液储罐8、硫浆过滤器9、第一阀10、第二阀11、第三阀12、第四阀13、第一温度计14、第一压力表15、第二压力表16、第三压力表17、原油外输流量计18共同组成。
8.其特征在于所述原料气分离器1、冷却装置2、立式分离器3、湿式脱硫塔4、沉降分
离器5再生塔6、闪蒸罐7、第二阀11、第四阀13、第一温度计14、第一压力表15、第二压力表16、第三压力表17顶部依次连接构成实验装置主循环回路;所述第一阀10、第三阀12、原油外输流量计18依次连接到原料气分离器1出口管道上;所述第一阀10将第一流量计18和原料气分离器1内部相连通;所述碱液储罐8安装到湿式脱硫塔4靠近下端入口的外壁面和内部;所述硫浆过滤器9安装到湿式脱硫塔4靠近下端入口的内部;所述第一温度计14、第一压力表15安装到冷却装置2上段出口处;所述第二阀11将立式分离器3和第二压力表16内部相连通;所述第三压力表17与沉降分离器5外部出口相连;所述第四阀13将沉降分离器5和闪蒸罐7内部相连通;
9.所述原料气分离器1对进料流体进行初步气液分离,原料气分离器1的液位指示及控制,设高低报警,气体后续进入冷却装置2;所述冷却装置2容纳立式分离器3出口管道到湿式脱硫塔4出口管道之间的所有设备和管道,维持实验必需的操作温度;所述第一温度计14、第一压力表15可对从冷却装置2流出的气体进行温度和压力控制,满足立式分离器3中进料气体的要求;所述湿式脱硫塔4对经过立式分离器3分离出的含硫气体进行脱硫,该工艺流程适合湿式脱硫法中的络合铁脱硫,络合铁脱硫富液自闪蒸罐7闪蒸后进入再生塔6顶部的喷射器,与自吸进入的空气两相混合发生氧化反应,并在再生塔6内进一步氧化再生;从湿式脱硫塔4出来的净化气进入沉降分离器5,将其中的游离水进行分离后外输。定期从碱液储罐8内补充脱硫药剂,再通过补液泵输送到立式分离器3进入整个天然气脱硫系统;脱硫后形成的固体硫磺,硫浆等经过硫浆过滤器9过滤。
10.本发明由于采取以上技术方案,可以达到以下有益效果:
11.(1)脱硫净化装置的进气要求不能含游离水及机械杂质,本工程天然气采用卧式沉降分离器进行气液分离。流程简单,操作简单,适宜撬装化、模块化。
12.(2)天然气中的硫化氢含量小于20mg/m3。
13.系统脱硫液总循环量采用贫液泵变频控制技术,调节流量大小,提高装置操作弹性,降低运行能耗。硫磺过滤部分采用全自动硫磺真空过滤机,降低工人劳动强度,生产得到的硫磺直接装车外运。
14.络合铁脱硫为放热反应,反应热为9.60kj/gh2s,在此络合铁脱硫装置中,天然气硫化氢含量高,硫化氢浓度高,系统产生的富余热量多,在经过热量平衡后,还有大量富余热量。当温度超过30℃时,降解量有上升的趋势。在温度低于45℃时,能够维持正常生产,当溶液超过该温度后,溶液降解严重,大量硫磺颗粒聚集成块,堵塞系统。为此,在该页岩油边伴生气络合铁脱硫流程设计中,增加冷却装置2,对系统贫液进行降温,保证系统正常运行。
附图说明
15.图1是本发明提供的适用于中含硫页岩油伴生气的脱硫工艺流程示意图。
16.图中:1-原料气分离器、2-冷却装置、3-立式分离器、4-湿式脱硫塔、5-沉降分离器、6-再生塔、7-闪蒸罐、8-碱液储罐、9-硫浆过滤器、10-第一阀、11-第二阀、12-第三阀、13-第四阀、14-第一温度计、15-第一压力表、16-第二压力表、17-第三压力表、18-原油外输流量计
具体实施方式
17.下面结合附图1对本发明作进一步说明,但本发明具体实施形式多种多样,并不局限于以下实施例。
18.本发明一种适用于中含硫页岩油伴生气的脱硫工艺流程,包括:1-原料气分离器、2-冷却装置、3-立式分离器、4-湿式脱硫塔、5-沉降分离器、6-再生塔、7-闪蒸罐、8-碱液储罐、9-硫浆过滤器、10-第一阀、11-第二阀、12-第三阀、13-第四阀、14-第一温度计、15-第一压力表、16-第二压力表、17-第三压力表、18-原油外输流量计。
19.具体实施方式为
20.第一步:关闭第一阀10、第二阀11、第三阀12、第四阀13;
21.第二步:开启原料气分离器1、冷却装置2,进行气液分离和除尘净化工作,使温度达到后续湿式脱硫塔3的要求。分离出的原油经过原油外输流量计18计量后外输;
22.第三步:通过第一温度计14、第一压力表15监测冷却装置出口处温度和压力,使其满足条件:温度25~45℃,压力1.2mpa~4.6mpa;
23.第四步:开启第一阀10、第二阀11、第三阀12;关闭第四阀13;
24.第五步:使经过冷却装置2,满足压力温度要求的气体进入立式分离器3分离游离水和其他轻烃物质;
25.第六步:开启第四阀13,关闭第一阀10;
26.第七步:分离净化后的天然气流入湿式脱硫塔4内进行脱硫,同时定期从碱液储罐8内补充脱硫药剂,再通过补液泵输送到分离槽进入整个天然气脱硫系统;
27.第八步:经过脱硫后湿式脱硫塔4内络合铁脱硫富液自闪蒸罐7闪蒸后进入再生塔6顶部的喷射器,与自吸进入的空气两相混合发生氧化反应,并在再生塔6内进一步氧化再生;
28.第九步:脱硫后形成的固体硫磺,硫浆等经过硫浆过滤器9过滤,生产得到的硫磺直接装车外运;
29.以上所述仅为本发明的较佳实施例而已,并不用以限制本发明。凡在本发明精神和原则之内所作的任何修改、等同替换和改进等,均应包含在本发明的保护范围之内。