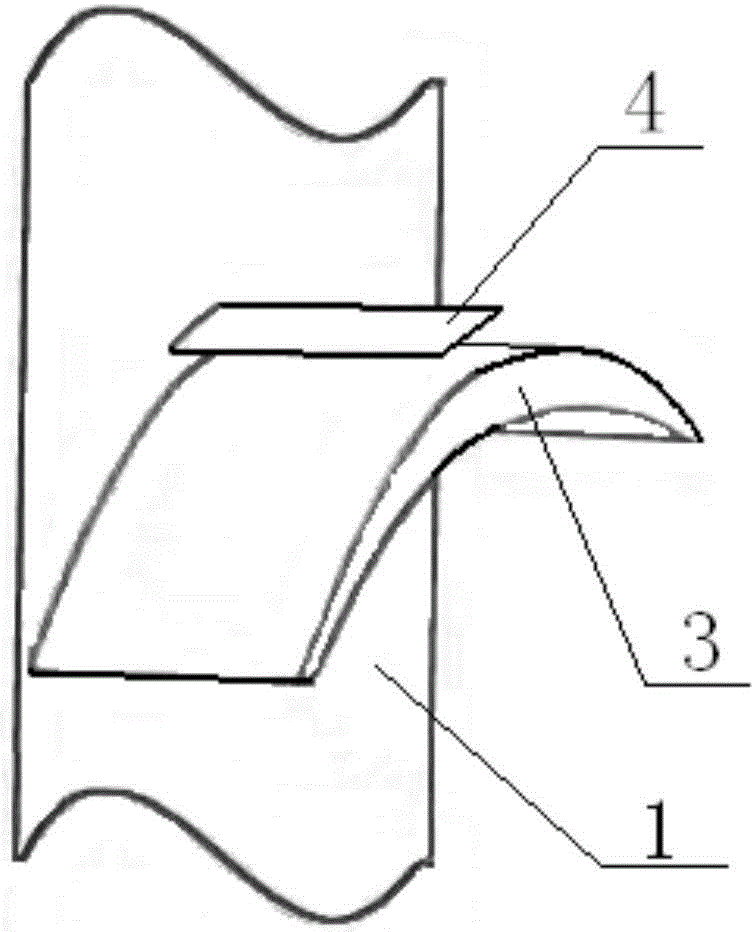
本发明涉及一种控制涡轮静子流动分离的分流小叶结构,属于叶轮机械
技术领域:
。
背景技术:
:现代高涵道比航空发动机的涡轮尺寸增大、级数增多,为了减轻发动机的重量提高发动机的推重比,通常采用减少涡轮级数或者涡轮级叶片数的设计方法,这导致涡轮叶片的负荷增加,高负荷或超高负荷涡轮叶型对应的叶片吸力面局部逆压力梯度增大,使得叶片表面容易出现流动分离、叶型损失相应增大。由于在大展弦比涡轮叶片中叶型损失占涡轮叶片损失的大部分,故涡轮叶片负荷的增加将导致涡轮效率下降,航空发动机的耗油率增大,因此,运用合适的控制手段来减小吸力面的流动分离、降低叶型损失是先进涡轮设计的一个重要目标。为了抑制涡轮静子叶片的吸力面边界层流动分离从而减小分离流动损失,现代航空发动机主要采用主动控制和被动控制两种手段。被动控制主要包括在涡轮叶片吸力面加拌线、V型槽、球窝、矩形条等控制策略,促发转捩提前发生,减小吸力面分离泡的大小,进而降低叶型损失。然而在不同飞行条件下,涡轮处于不同的工作状态,被动控制手段无法在复杂工况下保持良好的控制效果,甚至会由于工况改变对涡轮带来不利影响。主动控制方法主要包括利用定常或脉动的气流射流来控制涡轮叶片吸力面的分离;近年来等离子体主动控制等新型手段也取得了良好的主控效果,这些主动控制相较于被动控制方法而言,具有适应工作裕度宽、控制效果好等突出特点,但脉冲射流或等离子体的控制结构复杂,在涡轮流动控制上还没有进入应用阶段。因此,本领域技术人员开发了一种结构简单、成本较低、控制效果良好的控制涡轮静子流动分离的分流小叶结构,能够实现主动控制涡轮静子叶片吸力面处的流动分离,减小分离流动损失。技术实现要素:发明目的:为了克服现有技术中存在的不足,本发明提供一种控制涡轮静子流动分离的分流小叶结构,具有结构简单、成本较低、主控效果良好等优点,且能够良好工作在设计工况下及复杂非设计工况下,有效抑制涡轮静子叶片吸力面处的流动分离,从而减小分离流动损失,提高涡轮的工作效率。技术方案:为实现上述目的,本发明采用的技术方案为:一种控制涡轮静子流动分离的分流小叶结构,包括静叶轮毂及静叶机匣,在静叶轮毂及静叶机匣之间沿圆周方向均匀设置有若干静子叶片;每个静子叶片的吸力面上方设置有可调偏转角的分流小叶,分流小叶呈弧面板状,其前缘与尾缘处均为弧面;所述分流小叶的上表面为吸力面,分流小叶的下表面为压力面,分流小叶的上、下表面均为静子叶片的吸力面上与其对应部位的三维弧面;分流小叶的中弧线中点处设置有沿分流小叶叶高方向延伸的旋转轴,旋转轴与分流小叶连为一体且旋转轴的两端伸出分流小叶外;静叶轮毂及静叶机匣上均设置有与旋转轴相配合的轴承,分流小叶通过旋转轴与轴承的配合沿圆周方向均匀安装于静叶轮毂及静叶机匣之间;当分流小叶绕其旋转轴偏转0度时,分流小叶的压力面与静子叶片的吸力面之间的距离处处相等。当涡轮静子叶片由于工况改变将要发生吸力面大尺度流动分离时,增大分流小叶的偏转角,使分流小叶的尾缘靠近静子吸力面、分流小叶的前缘远离静子吸力面;分流小叶的压力面与静子叶片的吸力面形成局部收缩流道,实现对吸力面流体的局部增压,从而实现对静子叶片吸力面处流动分离的抑制。优选的,所述分流小叶绕其旋转轴的偏转角在0-10度内。负角度偏转会扩大静子叶片吸力面处的流动分离,正角度过大会引起流道堵塞,正角度过小会使抑制流动分离的效果不明显。优选的,为了保证分流小叶与静叶轮毂、静叶机匣之间不会发生干涉从而影响分流小叶的转动效果,所述分流小叶的内、外侧面分别与静叶轮毂、静叶机匣的内壁形状相适配,且分流小叶与静叶轮毂、静叶机匣之间均有转动间隙。优选的,所述分流小叶的弦长为静子叶片的10%,分流小叶的叶高与静子叶片相同。优选的,所述旋转轴的直径为小叶弦长的50%。优选的,所述分流小叶距静子叶片吸力面的距离为静子叶片栅距的10%。优选的,所述旋转轴的内端上安装有调节分流小叶偏转角度的调整杆,调整杆与旋转轴成90°夹角并伸出至静叶机匣外。有益效果:本发明提供的一种控制涡轮静子流动分离的分流小叶结构,相对于现有技术,具有以下优点:1、结构简单,成本较低,具有良好的主控效果,且适用于多种结构类型的涡轮静子叶片;2、其适应工作裕度宽,能够良好工作在设计工况下的同时在复杂的非设计工况下能够有效抑制涡轮静子叶片吸力面处的流动分离,有效减小了分离流动损失,提高涡轮的工作效率。附图说明图1为本发明中分流小叶与静子叶片的剖面图;图2为本发明中分流小叶与静子叶片的立体图;图3为本发明一种控制涡轮静子流动分离的分流小叶结构的结构示意图;图4为本发明中分流小叶与静叶机匣的连接结构示意图;图5为本发明中分流小叶与静叶轮毂的连接结构示意图;图中包括:1、静叶轮毂,2、静叶机匣,3、静子叶片,4、分流小叶,5、旋转轴。具体实施方式下面结合附图对本发明作更进一步的说明。如图1所示为一种控制涡轮静子流动分离的分流小叶结构,包括静叶轮毂1及静叶机匣2,在静叶轮毂1及静叶机匣2之间沿圆周方向均匀设置有若干静子叶片3;每个静子叶片3的近吸力面处设置有可调偏转角的分流小叶4,分流小叶4呈弧面板状,其前缘与尾缘处均为弧面;所述分流小叶4的上表面为小叶吸力面,分流小叶4的下表面为小叶压力面,分流小叶4的上、下表面均为静子叶片3的吸力面上与其对应部位的三维弧面;分流小叶4的中弧线中点处设置有沿分流小叶4叶高方向延伸的旋转轴5,旋转轴5与分流小叶4连为一体且旋转轴5的两端伸出分流小叶4外;静叶轮毂1及静叶机匣2上均设置有与旋转轴5相配合的轴承,分流小叶4通过旋转轴5与轴承的配合沿圆周方向均匀安装于静叶轮毂1及静叶机匣2之间;当分流小叶4绕其旋转轴5偏转0度时,分流小叶4的压力面与静子叶片3的吸力面之间的距离处处相等。所述分流小叶4绕其旋转轴5的偏转角在0-10度内。负角度偏转会扩大静子叶片吸力面处的流动分离,正角度过大会引起流道堵塞,正角度过小会使抑制流动分离的效果不明显。所述分流小叶4的内、外侧面分别与静叶轮毂1、静叶机匣2的内壁形状相适配,且分流小叶4与静叶轮毂1、静叶机匣2之间均有转动间隙;所述分流小叶4的弦长为静子叶片3的10%,分流小叶4的叶高与静子叶片3相同;所述旋转轴5的直径为小叶弦长的50%;所述分流小叶4距静子叶片3吸力面的距离为静子叶片3栅距的10%;所述旋转轴5的内端上安装有调节分流小叶4偏转角度的调整杆,调整杆与旋转轴5成90°夹角并伸出至静叶机匣2外。分流小叶4在涡轮静子中的轴向位置由其控制的涡轮叶型可能出现大尺度分离位置决定,一般为静子叶片3吸力面发生倒流处。下面结合具体实施例对本发明作更进一步的说明。本实施例中,涡轮静子叶片3叶型为T106A型,分流小叶4的轴向位置位于静子叶片3轴向弦长55%处,分流小叶4的中弧线中点连线距涡轮静子叶片3吸力面的距离为15mm。本实施例中,涡轮静子叶片3的具体参数见表1:表1参数数值弦长198mm轴向弦长170mm安装角30.7°栅距208mm(高载荷工况)栅距/弦长1.05(高载荷工况)叶高375mm(全)进气角37.7°出气角62.4°本实施例中,分流小叶4的具体参数见表2:表2参数数值弦长29.7mm轴向弦长23.7mm安装角37.5°栅距208mm(高载荷工况)叶高375mm(全)其中涡轮静子叶片3、分流小叶4的叶高均为T106A叶片全叶高,且平面叶栅的计算可以说与叶高无关,但是具体应用中叶高可以做出适当修改。。分流小叶4的叶高与静子叶片3的叶高相同,但在具体应用时,分流小叶4可以结合工况、控制效果调整叶高使用,也就是说用于同样的涡轮叶片,小叶叶高可以为涡轮叶高的100%、75%、50%、25%等。本发明的具体实施方式如下:首先选取传统的可能在高负荷或变工况条件下发生大尺度吸力面流动分离的涡轮静子叶片3,在其近吸力面处可调偏转角的分流小叶4。在涡轮叶片正常工作时保持分流小叶4的压力面与静子叶片3的吸力面之间的距离处处相等,即0度偏转角位置。在涡轮静子叶片3由于工况改变将要发生吸力面大尺度流动分离时,增大分流小叶4的偏转角,使分流小叶4的尾缘靠近静子叶片3吸力面,分流小叶4的前缘远离静子叶片3吸力面;分流小叶4的压力面与静子叶片3的吸力面形成局部收缩流道,实现对静子叶片3吸力面流体的局部增压,实现对流动分离的抑制。本发明提出了一种主动控制涡轮静子叶片吸力面流动分离的方法,进一步挖掘了航空发动机涡轮静子的优化设计潜力,提出了设置有可调偏转角分流小叶的主控结构,在对涡轮单级静子性能没有明显影响的情况下,提高涡轮的性能和稳定工作域度,适用于多种结构类型的涡轮静子叶片。本发明在实际应用中,可以根据设计精度、造价、装备难度等灵活选取所述的分流小叶的结构位置与偏转角度。以上所述仅是本发明的优选实施方式,应当指出:对于本
技术领域:
的普通技术人员来说,在不脱离本发明原理的前提下,还可以做出若干改进和润饰,这些改进和润饰也应视为本发明的保护范围。当前第1页1 2 3