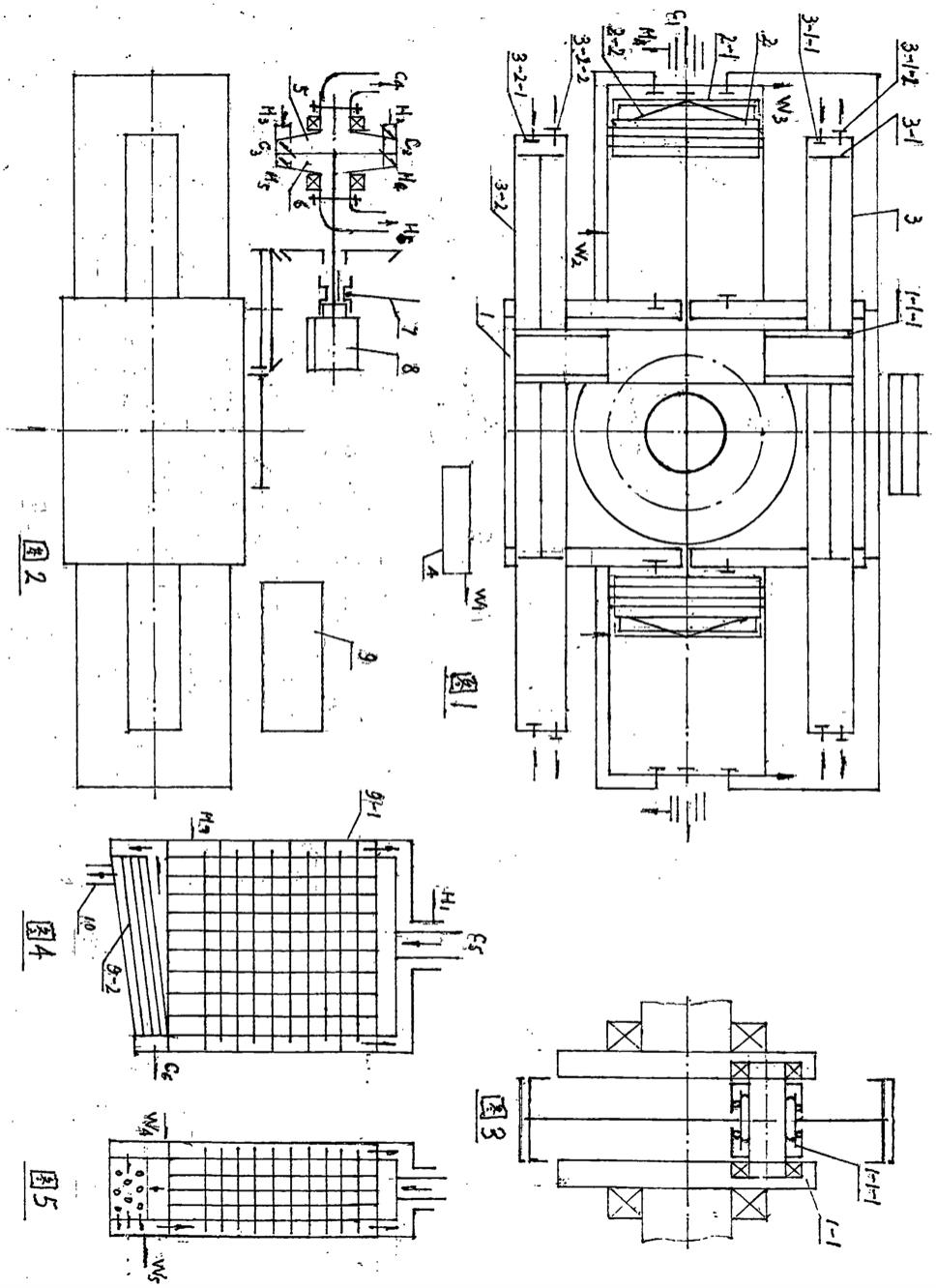
一种集成式自增压变压缩比发动机
所属技术领域:
[0001]
本发明的发动机,是以“双缸对置四冲程往复活塞式自增压发动机(专利申请号:2018107743516)”为基础,拓展成为本发明的《一种集成式自增压变压缩比发动机》。
背景技术::
[0002]
双缸对置自增压发动机,由于对置双缸共一个曲拐,又无活塞销和活塞裙,所以结构紧凑,比重量轻。用做战车和普通运载工具的动力,除了更便于安装和扩大承载空间外,自身重量的减轻等于是直接降低油耗,降低使用成本。它的自增压技术,使升功率获得重大突破,随进气量的增加而倍增。它以进气量大为基础,改变燃烧模式和燃烧质量,使整个燃烧过程更加干净彻底,燃油耗和排污值更低。它用全密封原理取代传统的活塞,活塞环对气缸的节流式密封原理,彻底消除了第一环开口处存在的干摩擦和半干摩擦现象,不仅显著地提高了发动机的做功能力,而且因为活塞泄漏的高温高压燃气,是机油最大污染源,因此,减少活塞泄漏量,不仅润滑质量更好,还能大幅度延长机油的使用和更换周期。它用直接在缸壁上形成油膜润滑取代传统的飞溅润滑,不仅减少了活塞组的运行阻力,而且可以优化油膜厚度,总的机油耗和颗粒物大幅降低。它的自增压方式,便于采用多元燃烧,勿需添加剂和预混合,就可直接参烧甲醇、乙醇、生物柴油等多种燃料,为走自然平衡之路,彻底解决内燃机co2排放量大的问题提供了技术支撑。但是,压燃式汽油机、增压机,特别是自增压机属高增压机,在增压或压燃后最大燃烧压力将大幅提高,这是自增压机必须妥善解决的技术问题。目前,有多种降低最大燃烧压力的办法,例如中冷、降低增压气体的温度,延迟进气门的关闭时间。活塞的压缩行程小于膨胀行程......。这些办法的不足之处有的是增大了总体结构,有的是工质流失或吸入量减少,不能充分发挥工质的做功效能;有的是改变气门的启闭和活塞的行程,结构复杂化,而最大的不足是增压度变大时,没有与之匹配的最大功率输出。
技术实现要素::
[0003]
本发明的发动机,是以“双缸对置四冲程往复活塞式自增压发动机”为基础,在传承其已有技术优势的基础上,更多地集成了现有内燃发动机的多个先进技术和理念,拓展成为本发明的《一种集成式自增压变压缩比发动机》。
[0004]
通过背景技术分析,针对现有发动机和已有技术存在的上述不足,本发明的集成式自增压变压缩比发动机采用的第一个技术方案是采用一种可变压缩比的组合活塞(专利申请号:202010253055.9)在不改变活塞排量的前提下,适时改变燃烧室的容积,从一个设定的较高压缩比,变成一个与即时工况相匹配的较低压缩比,从而达到调控最大燃烧压力的目的。二是针对自增压机增压后燃烧的燃料更多,通过冷却水和排气带走的总热量更大,并且这两个部分带走的能量占总的发热量的60%左右,其绝对值又大大高于自然吸气发动机的具体情况,本发明的发动机所采用的第二个技术方案就是利用废气涡轮和蒸汽涡轮,回收利用冷却水和排气中所含的能量,一、直接与发动机并联,提高最大输出功率。二、推动
发电机发电,是发动机外的第二动力。如电力足够大,可以直接驱动汽车的前桥或后桥。如电力不足,则可以带动水泵、油泵、空调等附属设施,增加主机的输出功率。
附图说明:
[0005]
下面结合附图和实施例对本发明做进一步说明。
[0006]
图1为本发明的《一种集成式自增压变压缩比发动机》的正面示意图,表达变压缩比活塞2和4个对称分布的与活塞联动的蒸汽增压柱塞3在“双缸对置四冲程往复活塞式自增压发动机”上的安装位置。
[0007]
图2为图1的俯视图,表达第一动力:发动机和第二动力,发电机的连结和传动关系。
[0008]
图3表达了滑轨、滑块和上下活塞、活塞杆之间的连接和运转关系。
[0009]
图4是换热器9的正面示意图。
[0010]
图5是图4的侧视图。
[0011]
图例说明:
[0012]
1、双缸对置四冲程往复活塞式自增压发动机,1-1、活塞曲柄滑块机构,1-1-1、滑轨,2、可变压缩比活塞,2-1、活塞盖,2-2、碟形弹簧,3、增压柱塞,3-1、左缸上增压柱塞,3-1-1、进气阀,3-1-2、排气阀,3-2、左缸下增压柱塞,3-2-1、进气阀,3-2-2、排气阀,4、集水箱,5、废气涡轮,6、蒸汽涡轮,7、双向结合器,8、发电机,9、换热器,9-1、蒸汽过热器,9-2、蒸汽发生器,10、排污阀,w1、水泵出水口,w2缸套进水口,w3缸盖出水口,w4蒸汽发生器进水口,w5换热器出水口,c1发动机排气口,c2废气涡轮上进气口,c3废气涡轮下进气口,c4废气涡轮排气口,c5换热器进气口,c6换热器排气口,h1过热蒸汽出口,h2和h3、上下蒸汽管的进气口,h4、h5蒸汽涡轮上下进气口,h6蒸汽涡轮排气口,h7残存蒸汽入口,
↑
进出口方向。
具体实施方式:
[0013]
如图1所示,本发明采用的第一个技术拓展方案是采用了一种可变压缩比的组合活塞2。它在其内部设有布油和冷却油道的组合活塞的基础上,在活塞上加装了一个活塞盖2-1,并通过一致数个碟形弹簧2-2以弹性支承的方式支承在变压缩比活塞的活塞顶上。当实际的燃烧压力大于预设的最高燃烧压力后,活塞盖2-1在燃气压力的作用下,压缩碟形弹簧2-2,燃烧室的容积变大,实际压缩比相应降低,燃烧压力也随之降低,从而达到调控最大燃烧压力的目的。采用可变压缩比活塞调控最大燃烧压力的优点是:1、结构简单易行,调控范围大。2、活塞的排量固定,没有工质流失,工质的做功效能得到保证。3、可以采用更高的压缩比,提高循环效率。特别是对于自燃点较高的汽油机,采用的压缩比为18∶1,实现压燃,配以预混、稀气,层状燃烧,排污值更低。4、当燃烧压力小于预设的最高燃烧压力时,因压缩比高,升功率也高。当燃烧压力大于预设的最高燃烧压力后,活塞盖2-1下移压缩碟形弹簧2-2,同时将高出预设最高燃烧压力部分的燃气能量储存起来,然后以等压膨胀的形式将储存的能量释放出来,从而使发动机的循环效率得到更进一步的提高。
[0014]
如图1、图2、图3、图4、图5所示,本发明的第二个技术拓展方案是利用组合的废气涡轮5和蒸汽涡轮6来回收利用废气和冷却水中所含的能量。由于自增压机废气中含储的能量大幅增加,故本技术方案的第一步是将排气直接引入废气涡轮5,直接从废气中回收部分
能量,推动涡轮对外做功。由于推动废气涡轮后的排出气体仍然有较高的做功能力,自增压机又采用的是高温闭式冷却循环方式,高温出水水温近于100℃,易于汽化,故第二步是进一步利用废气和高温循环水中的热量,用换热器来生产水蒸汽,然后再利用水蒸汽来推动蒸汽涡轮,并和废气涡轮一起,通过双向结合器7,直接带动发电机8发电。或者通过双向结合器7与发动机1并联,提高发动机的输出功率。
[0015]
废气涡轮驱动系统由连接发动机1的排气口c1和废气涡轮上下进气口c2和c3的管线,连接废气涡轮排气口c4和换热器进气口c5的管线和换热器9组成。所有废气连接管道外均套装有带有进出口端的蒸汽管道。为了逐次提高过热蒸汽温度,废气和蒸汽互呈逆向流动,并且在蒸汽管和高温件外覆盖有绝热保温层,废气管和蒸汽管成互为利用的结构关系。发动机排出的废气,从废气涡轮的进气口c2和c3,沿切线和相同的旋向推动废气涡轮5旋转,并与背对背设置的蒸汽涡轮6一起推动发电机8发电。
[0016]
蒸汽涡轮驱动系统由发动机的高温闭式冷却水循环系统,换热器9、增压柱塞3、蒸汽涡轮6和连接管线组成。增压柱塞3与活塞曲柄滑块机构1-1的滑轨1-1-1连接,并由可变压缩比活塞2带动,同步做往复直线运动。水泵的出水口w1与气缸体下部的w2连接,进水温度60-70℃,在对气缸和气缸盖进行冷却后,水温提高至95-100℃,然后从出水口w3流出,后接入蒸汽发生器9-2的进口w4。高温循环水从横向流过蒸汽发生器9-2的烟管进行热交换,产生水蒸汽,然后从另一侧流出,多余的循环水从出水口w5流回集水箱4。水蒸汽在蒸汽压力和增压柱塞3的抽吸作用下上行,被逐次加热成温度更高的过热蒸汽后,从蒸汽过热器9-1上部的出口h1流出,接入蒸汽套管的进汽口h2和h3,并逆行至蒸汽套管的出汽口h4流出。然后又与上下柱塞的进汽阀3-1-1和3-2-1连接,经增压柱塞3增压后,从排汽阀3-1-2和3-2-2排出的高温高压蒸汽,接入蒸汽涡轮的进汽口h4和h5,推动蒸汽涡轮和废气涡轮一起旋转发电。最后,从蒸汽涡轮流出的残汽从出口h6流出后,再接入蒸汽过热器9-1的下部接口h7,被再次加热,循环利用。这种水和蒸汽的闭式循环方式,水的用量少,汽化率高,对蒸汽的利用充分。为了减少水垢,循环水必须是蒸馏水或经过处理的软水。为了清洗方便,在换热器底部设有排污口10。
[0017]
本发明的集成式自增压变压缩比发动机,采用自增压和变压缩比技术,做功能力强,循环效率高。它利用废气和蒸汽涡轮通过直接和热交换两种方式使烟气和循环冷却水中的能量,大部得到回收利用。与同排量的发动机相比,不仅是它的升功率获得重大突破,可望提高一倍以上,而且它的燃油耗,机油耗大幅降低,热效率也可望获得重大突破,有望达到60%以上。与其它作为运载工具的动力装置相比,燃气轮机的耗油率太高;电动车和现有的燃油车结构尺寸大,重量大,无效功耗高,其发展必然受到公路承载量和停车位的约束。本发明的自增压变压缩比发动机,结构紧凑,比重量(kg/kw)轻,升功率高,使用成本低廉,所以,它是普通民众实现动力飞行,在天地间自由畅行的首选动力。