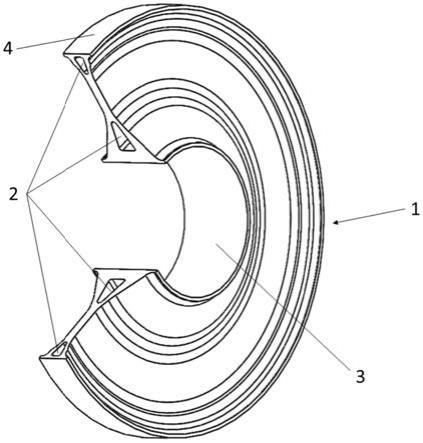
1.本实用新型涉及航空发动机技术领域,尤其涉及一种带双内环空腔的涡轮盘结构。
背景技术:2.航空发动机作为飞机的动力装置,是飞机的心脏,是保证飞机正常运行的关键。随着航空工业的不断发展,在航空发动机的设计和研发过程中,为了提高发动机工作性能,如高推重比、高可靠性、高安全性等,降低由于发动机故障所导致的飞行事故,首先应提高航空发动机的核心零部件如涡轮盘、涡轮叶片、涡轮轴的性能,使其能在更加苛刻的环境下稳定工作。因此航空发动机核心零部件的性能成为制约航空发动机整机性能的重要因素。
3.涡轮盘是航空发动机的核心零件,它的质量和应力水平对于发动机的推重比、可靠性、安全性等性能的提升具有重要的影响。在保证轮盘应力满足材料许用应力的条件下,减轻涡轮盘的质量,可以减轻航空发动机重量,降低成本,并提高发动机推重比。对涡轮盘进行结构优化设计是减轻涡轮盘质量的有效途径。
技术实现要素:4.本实用新型的目的在于解决现有技术中的上述问题,提供一种带双内环空腔的涡轮盘结构,该结构使得发动机涡轮质量大幅度降低,进一步提升航空发动机推重比。
5.为达到上述目的,本实用新型采用如下技术方案:
6.一种带双内环空腔的涡轮盘结构,包括轮盘,轮盘内部设有密闭的在轮盘内沿圆周向贯通的两个空腔;所述两个空腔位于轮盘的中心线与外轮缘之间并呈两端分布;其中,一个空腔靠近盘缘面,且口径自轮盘内侧向外轮缘逐渐变大;另一个空腔靠近轮心,且口径自轮盘内侧向外轮缘逐渐变小。
7.所述两个空腔均呈类等腰三角形设置,两个底角均由3mm圆弧倒角构成,两个顶角分别由3mm圆弧倒角和4mm圆弧倒角构成。
8.所述轮盘的外部轮廓设有多个环形凹槽,所述环形凹槽由向内凹的圆弧曲线组成,所述圆弧曲线与外部轮廓的直线段相切连接。
9.所述涡轮盘原始模型体积为4.578
×
106mm3,质量为35.847kg,所述带双内环空腔的涡轮盘结构体积为3.071
×
106mm3,质量为24.045kg。
10.相对于现有技术,本实用新型技术方案取得的有益效果是:
11.1、本实用新型的结构体积为3.071
×
106mm3,质量为24.045k,而原涡轮盘模型的体积为4.578
×
106mm3,质量为35.847kg,在应力均满足要求的情况下本实用新型较原涡轮盘质量降低32.92%,进而减轻航空发动机重量,降低成本,并提高发动机推重比。
12.2、本实用新型不仅在内部有双内环空腔的构造,而且外部结构也有合理的改变即外部体积减少,最大化的降低涡轮盘的质量,得到更为有价值的构型。
附图说明
13.图1为所述带双内环空腔的涡轮盘整体结构示意图。
14.图2为所述带双内环空腔的涡轮盘结构局部示意图。
15.图3为所述带双内环空腔的涡轮盘整体结构截面形状示意图。
16.图4为涡轮盘15
°
扇区模型提取示意图。
17.图5为涡轮盘扇区模型分块尺寸示意图。
18.图6为涡轮盘扇区模型相应载荷条件示意图。
具体实施方式
19.为了使本实用新型所要解决的技术问题、技术方案及有益效果更加清楚、明白,以下结合附图和实施例,对本实用新型做进一步详细说明。
20.如图1~3所示,本实施例包括轮盘1,轮盘1的圆心处设有轴向孔3,轮盘1内部设有密闭的双内环空腔2,双内环空腔2在轮盘1内沿圆周向贯通。
21.具体地,所述双内环空腔2呈两端分布,一个空腔靠近盘缘面4,且口径自轮盘内侧向外轮缘逐渐变大;另一个空腔靠近轮心,且口径自轮盘内侧向外轮缘逐渐变小。
22.更具体地,双内环空腔2均呈类等腰三角形设置,双内环空腔2的底角5与底角8均由3mm圆弧倒角构成,顶角6由3mm圆弧倒角构成,顶角7由4mm圆弧倒角构成。采用圆弧倒角形式可有效避免应力集中问题。
23.所述带双内环空腔的涡轮盘结构的外轮廓与原涡轮盘外轮廓完全不同。所述轮盘的外部轮廓设有多个环形凹槽,所述环形凹槽由向内凹的圆弧曲线组成,所述圆弧曲线与外部轮廓的直线段相切连接。
24.具体地,本实施例的涡轮盘外轮廓由直线段9和直线段12与圆弧曲线10、11、13、14、15和16连接而成。其中,圆弧曲线10半径为6mm,圆弧曲线11半径为10mm,圆弧曲线13半径为27.09mm,圆弧曲线14半径为50mm,圆弧曲线15半径为30mm,圆弧曲线16半径为52.25mm。
25.本实施例通过在轮盘1的内部设计空心的密闭的双内环空腔2,节省轮盘1的耗材,并使得轮盘1的结构效率得到极大提高,以最大化减轻轮盘1的整体重量,避免轮盘1的应力集中,从而达到减轻轮盘1的重量并提高发动机推重比。
26.原涡轮盘模型体积为4.578
×
106mm3,质量为35.847kg;本实用新型结构体积为3.071
×
106mm3,质量为24.045kg,本实用新型在应力均满足要求的情况下较原涡轮盘质量降低32.92%,进而减轻航空发动机重量,降低成本,并提高发动机推重比,体现出本实用新型的价值所在。
27.本实用新型的结构设计方法如下:
28.第一步:将涡轮盘原始模型在ug软件中进行扇区模型切分并提取扇区模型,本实施例所述带双内环空腔的涡轮盘结构是基于提取15
°
扇区模型,如图4所示。因轮盘模型为循环对称结构,故可单独对扇区模型进行分析与优化。此步操作目的在于,降低后期软件优化时间,提升软件优化效率。
29.第二步:在ug软件中将由第一步提取的15
°
扇区模型导出为parasolid文件,文件类型为*.x_t格式。
30.第三步:根据涡轮盘原始模型的应力场分布,选取合理的模型分块尺寸。如图5所示,本实施例合理选择三个不同的半径值以涡轮盘中心向盘缘面方向进行分块,分别为r3、r4和r5,其中r3为最小分块尺寸半径值,r4为中间分块尺寸半径值,r5为最大分块尺寸半径值。将这三个半径值作为第四步对模型完成分块处理的依据。此步目的在于为拓扑优化设置相应局部应力约束提供条件。
31.第四步:运行ansys workbench软件,建立static structural模块,在engineering data中设置材料属性,并将第二步由ug软件导出的parasolid文件导入到geometry中,本实施例所述的带双内环空腔的涡轮盘结构材料属性依据材料gh4169进行设置。进入geometry对导入模型进行分块处理,然后进入model模块对模型进行网格划分处理,网格单元尺寸为2.5mm,数量为12688。进而对模型设置相应载荷条件,相应载荷条件包括:温度场载荷、转速n、叶片离心载荷p、轴向位移约束和周向位移约束(轴向位移约束施加在轮心面的轴向端,周向位移约束施加在轮心面的周向端),如图6所示。其中温度场载荷具体公式如下:
[0032][0033]
其中,r为半径,r1为盘缘面半径,r2为轮心面半径,t(r
i
)为在r
i
半径处的温度值。
[0034]
设置完相应载荷条件后进行等效应力、径向应力和周向应力模拟仿真计算。
[0035]
第五步:返回ansys workbench软件,基于static structural模块中的solution项建立topology optimization模块。进入topology optimization模块setup项设置相应拓扑优化约束条件与优化目标。所述相应拓扑优化约束条件包括:质量保留50%约束、分块局部应力800mpa约束和非优化区域为盘缘面与轮心面,盘缘面与轮心面在图4中示出;优化目标为柔度最小。具体公式如下:
[0036]
min:λ
[0037]
w.r.t.:ρ
e
[0038][0039]
其中,λ为柔度,ρ
e
为优化区域网格单元伪密度,m为拓扑优化后模型质量,m0为原始涡轮盘模型质量,σ
i
(i=1,2,3,4)为局部应力。
[0040]
设置完相应约束条件与优化目标后进行拓扑优化,软件计算后得到拓扑优化结果。考虑拓扑优化结果对温度场极为敏感,材料有无直接决定热应力的有无,故本实用新型分别开展了考虑温度场载荷和忽略温度场载荷的拓扑优化研究,并对其结果进行对比,最终选取结果较优方案。
[0041]
第六步:基于ansys workbench软件的拓扑优化结果,在ug软件中进行模型重构。选取结构去除部分关键尺寸作为设计变量,导出*.exp格式文件。所述去除部分包括涡轮盘
的内环空腔去除部分以及涡轮盘的外轮廓去除部分。此步目的在于实现对重构后模型的参数化建模。
[0042]
第七步:根据第六步选取设计变量的合理变化范围,在ug软件中对重构后模型进行尺寸优化,并将建立的模型导入ansys workbench软件进行静力学分析,具体方法如第四步所述。
[0043]
第八步:将由第七步得到的分析结果与涡轮盘材料的屈服极限值进行对比,验证尺寸优化后模型等效应力、径向应力和周向应力是否小于材料的屈服极限,如果未达到要求,重复第七步,直至满足要求,最终得到合理优化模型。本实施例提出的一种新颖的带双内环空腔的涡轮盘结构材料采用gh4169。
[0044]
根据涡轮盘原始模型的应力场分布,选取合理的模型分块尺寸,并对涡轮盘原始模型在进行拓扑优化前实施了分块处理,如步骤三所示。这样的操作有利于拓扑优化计算时更加合理的进行应力运算,进而可以得到更为合理的模型。同时,本实用新型不仅在内部有双内环空腔的构造,而且外部结构也有合理的优化,最大化地降低涡轮盘的质量,得到更为有价值的构型。