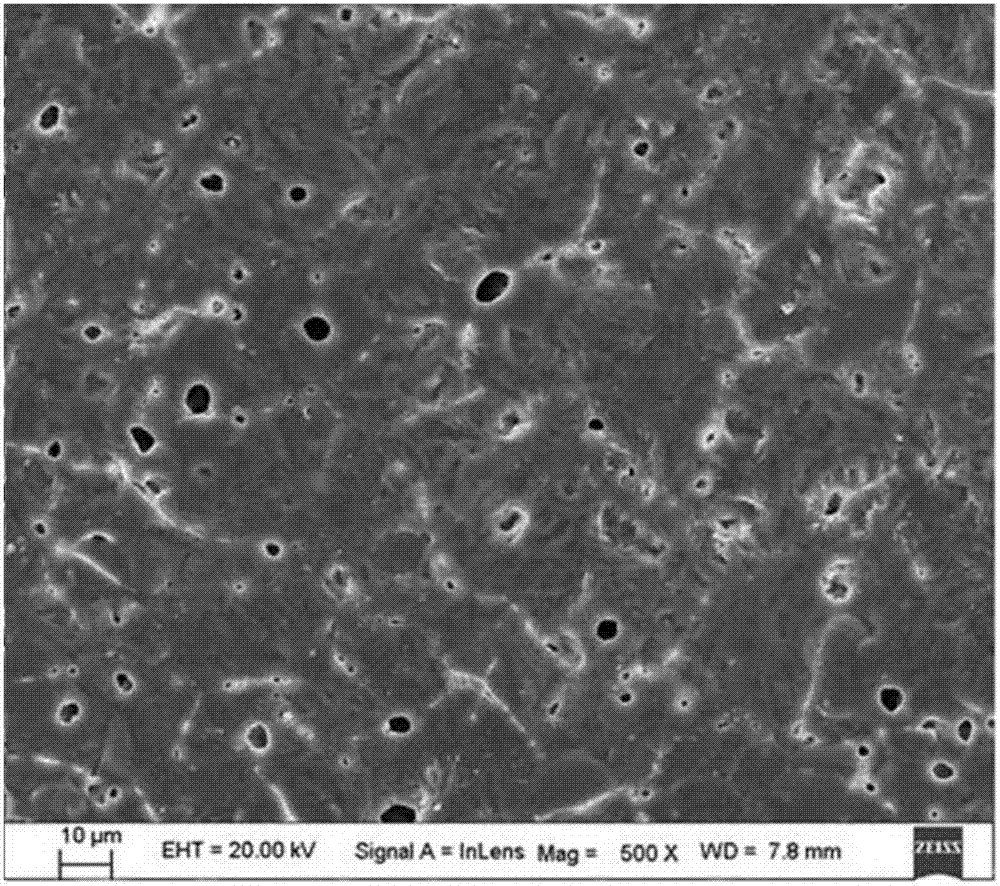
本申请涉及合金材料表面改性领域,特别是涉及一种用于微弧氧化的电解液、微弧氧化方法及应用。
背景技术:
:近年来,随着汽车工业、军事国防、航空航天、医疗器械及日常3C产品等领域的迅猛发展,人们对新材料的性能要求愈加苛刻。铝合金因其高比强度、易加工及价格低廉等优点应用广泛。但是,为满足更严苛的应用要求,铝合金的性能也在不断被提升,其中,铝合金的耐腐蚀性能一直以来都是衡量其应用前景的重要指标之一。目前,有许多方法被用来提高铝合金的耐腐蚀性能,如牺牲阳极、化学转换膜、阳极氧化、微弧氧化、物理沉积等,其大致机理均是通过改变合金组分或者在合金表面形成保护层达到提高铝合金的耐腐蚀性能的目的。其中,微弧氧化(micro-arcoxidation,缩写MAO)又称等离子体电解氧化(plasmaelectrolyticoxidation,缩写PEO),作为一种前沿的表面处理技术,因其成膜效率高,膜层结合力好,环境污染小等特点受到愈来愈多的研究和关注。同时,用该技术处理得到的氧化陶瓷膜其抗腐和耐磨性能均较常规的技术,如阳极氧化法和化学转换膜法,更加优异。采用微弧氧化得到的氧化陶瓷膜主要为金属氧化物,该膜层一般分为疏松层和致密层,其中,对抗腐蚀性能提升取决定性作用的是致密层的厚度。通过调节电解液组分和电参数,如电流密度、频率、占空比和氧化时间等,均可以一定程度上提高膜层致密层的厚度。但是,致密层的厚度提高的同时,疏松层的厚度增加速率可能高于致密层,即会获得更厚的疏松层;这导致膜层性能受到影响,比如膜层的粗糙度。另外,对于尺寸要求较高的零部件而言,膜层太厚,会影响零部件尺寸的精确度,会造成后续的组装困难等问题。技术实现要素:本申请的目的是提供一种新的用于微弧氧化的电解液,基于该电解液的微弧氧化方法及其应用。本申请采用了以下技术方案:本申请一方面公开了一种用于微弧氧化的电解液,包括终浓度为5-50g/L的磷酸盐、1-15g/L的含铁化合物和1-10g/L的络合剂,溶剂为蒸馏水,其中含铁化合物为二价铁化合物和/或三价铁化合物。需要说明的是,本申请的关键在于将磷化处理的磷酸盐加入到本申请特别配置的微弧氧化电解液中,将化学转换成膜与微弧氧化相结合,进而改善膜层致密度,提高耐腐蚀性能。还需要说明的是,磷化处理是在材料表面形成一层致密的、难溶的金属磷酸盐,以达到防腐的目的,但其主要缺点是成膜效率低、膜层结合力差,难以得到较厚的膜层,实际应用中一般只有几微米的膜厚;而本申请将其与微弧氧化相结合后,可以达到30微米的膜厚,并且采用本申请的电解液进行微弧氧化获得的膜层结合了磷化处理与微弧氧化两者的优点。此外,本申请的电解液或微弧氧化方法,与磷化处理相比,磷化处理使用的强酸性反应体系对环境具有很大的污染,而本申请的电解液或微弧氧化方法,以水为溶剂,仅需添加磷酸盐、含铁化合物和络合剂,环保安全。优选的,磷酸盐选自六偏磷酸钠、磷酸氢二钠、磷酸二氢钠、多聚磷酸钠、磷酸三钠和焦磷酸钠中的至少一种。更优选的,磷酸盐为六偏磷酸钠。优选的,含铁化合物选自草酸高铁铵、草酸铁、柠檬酸铁铵、柠檬酸铁、硝酸铁、硫酸铁、硫酸亚铁、氯化铁、氯化亚铁、普鲁士蓝、硫化亚铁、二硫化铁中的至少一种。更优选的,含铁化合物为草酸高铁铵。优选的,络合剂选自乙二胺四乙酸二钠、三乙醇胺、酒石酸钠、柠檬酸、草酸中的至少一种。更优选的,络合剂为乙二胺四乙酸二钠。优选的,电解液的pH值为4-7,电解液的离子电导率为5-50mScm-1。本申请的另一面公开了一种包括采用本申请的电解液的微弧氧化方法。优选的,电解液的温度控制在10℃-50℃;并且,微弧氧化方法使用的电源为脉冲电源,脉冲电源处理参数为恒流模式下,电流密度5-20A/dm2、处理时间5-30min、频率50-3000Hz;或者恒压模式下,电压300-600V,处理时间5-30min、频率50-3000Hz。优选的,本申请的微弧氧化方法,包括以下步骤,1)前处理,包括打磨、脱脂和去离子水洗涤;2)微弧氧化,包括将工件放入预先配置好的所述电解液中,工件连接微弧氧化电源正极,电源负极连接工作电极,工作电极与电解液接触,开启电源进行微弧氧化处理;3)后处理,包括直接用去离子水洗涤,风干即获得微弧氧化的工件。优选的,步骤1)中,脱脂采用有机溶剂超声溶解,有机溶剂包括乙醇和/或丙酮,超声时间为10-30min。本申请的另一面公开了本申请的电解液在铝合金微弧氧化中的应用。需要说明的是,本申请的电解液或者微弧氧化方法主要是针对铝合金表面处理而提出的,可以理解,本申请的电解液或微弧氧化方法并不只限用于铝合金,其它需要改善膜层致密度,提高耐腐蚀性能的合金或金属材料,同样可以采用本申请的电解液或微弧氧化方法。本申请的另一面公开了一种铝或铝合金材料,该铝或铝合金材料的表面具有采用本申请的微弧氧化方法制备的膜层,膜层以Al2O3为主体,膜层中含有P和Fe元素。优选的,膜层的厚度为5-100μm。需要说明的是,本申请的微弧氧化形成的膜层,与一般的微弧氧化不同的是,在其膜层中含有P和Fe元素,这表示本申请的膜层不仅仅是由微弧氧化形成,还发生了磷化处理,即化学转换成膜,这使得膜层致密度更强,进而提高了铝或铝合金的耐腐蚀性能。本申请的有益效果在于:本申请的用于微弧氧化的电解液,将磷酸盐、含铁化合物和络合剂溶解于水中,既满足了微弧氧化电解液的使用需求,又将磷化处理的磷酸盐引入其中,将磷化处理和微弧氧化相结合;使得采用本申请的电解液进行微弧氧化获得的膜层具有更好的致密度,进而提高了被处理工件的耐腐蚀性能。附图说明图1是本申请实施例1中采用对照电解液进行微弧氧化方法处理的铝合金的电镜扫描图;图2是本申请实施例1中采用本申请电解液进行微弧氧化方法处理的铝合金的电镜扫描图;图3是本申请实施例1中盐雾腐蚀后的3D共聚焦图片。具体实施方式本申请用于微弧氧化的电解液,将磷化处理和微弧氧化相结合,一方面,与磷化处理相比,既可以形成致密的、难溶的金属磷酸盐,又能够保障膜层的厚度,可以获得30微米厚的膜层;另一方面,虽然采用本申请的电解液进行微弧氧化获得的膜层厚度,远远大于单独磷化处理的膜层厚度,但是,与单独微弧氧化,通过调节其电解液组分和电参数,提高致密层的厚度相比,采用本申请的电解液或者微弧氧化方法,不会使膜层表面粗糙。也就是说,采用本申请的电解液或者微弧氧化方法,并不会使得疏松层过厚,也不会因疏松层的原因影响膜层的粗糙度。下面通过具体实施例和附图对本申请作进一步详细说明。以下实施例仅对本申请进行进一步说明,不应理解为对本申请的限制。实施例一本例以LY12铝合金材料为例进行微弧氧化,铝合金的尺寸为25×50×2mm3。本例的电解液中,磷酸盐采用六偏磷酸钠,含铁化合物采用草酸高铁铵,络合剂采用乙二胺四乙酸二钠(即Na2EDTA),电解液制备方法如下:称取六偏磷酸钠、草酸高铁铵和Na2EDTA,将其加入蒸馏水中,搅拌使其溶解。使得六偏磷酸钠终浓度为15g/L,草酸高铁铵终浓度为5g/L,Na2EDTA终浓度为5g/L。即获得本例的电解液。本例的微弧氧化方法包括:1)前处理:对铝合金进行打磨处理,用砂纸除去合金表面及边角毛刺,去除表面异物,减少合金粗糙度;再用有机溶剂20mL丙酮和50mL乙醇,依次对合金进行超声清洗10min,去掉表面有机污染物,之后禁止用手直接接触样品表面,避免再次污染;最后用去离子水洗掉表面的有机残留,并风干。2)微弧氧化:将样品浸入到本例配制的电解液中,采用20KW高压脉冲电源,恒流模式,电流密度5A/dm2、频率200Hz、反应时间10min。反应温度通过冷却系统控制在50℃以内。3)后处理:制备的膜层用去离子水洗净,自然风干,即获得本例经过表面处理的LY12铝合金,定义为试验样品。与此同时,本例采用了未加草酸高铁铵的对照电解液作为对比,并设计了草酸高铁铵浓度为2g/L的电解液,其余组份和用量与本例前述电解液相同。微弧氧化方法也与前述方法相同。其中,未加草酸高铁铵的电解液微弧氧化处理的LY12铝合金,定义为对照样品。采用电镜扫描对本例的试验样品和对照样品进行观察,结果如图1和图2所示,其中图1是对照样品的电镜扫描图,图2是试验样品的电镜扫描图。对比两个结果可见,未加草酸高铁铵的样品,其表面孔洞较多,粗糙度大,如图1所示;加入草酸高铁铵后,得到的膜层表面孔洞减少,孔径降低,如图2所示。并且,本例的试验样品,即采用本例的电解液进行微弧氧化获得的膜层,其厚度为20μm。采用X射线能谱仪(缩写EDS)对试验样品进行检测,结果显示,膜层中含有P和Fe元素,可见本例的膜层既有微弧氧化成膜,又具有磷酸处理化学转换成膜。采用盐雾腐蚀对三个电解液微弧氧化处理的铝合金进行耐腐蚀性能测试,其中三个电解液微分别是指草酸高铁铵浓度为0g/L、2g/L和5g/L的电解液,结果如图3所示。图3是盐雾腐蚀后的3D共聚焦图片,其中,0g/L、2g/L和5g/L分别指草酸高铁铵浓度0g/L、2g/L和5g/L的电解液处理获得的铝合金,0h、400h、800h、1200h、1600h、1800h分别是指盐雾腐蚀时间。图3的结果显示,本例的试验样品,即采用本例的草酸高铁铵浓度为5g/L的电解液进行微弧氧化获得的膜层,在经过1800小时的盐雾腐蚀后,仍然完好,可见采用本例的电解液进行微弧氧化,能够提高耐腐蚀性能;此外,草酸高铁铵浓度为2g/L的电解液,在经过1800小时的盐雾腐蚀后,存在细微的腐蚀现象,与草酸高铁铵浓度为0g/L的电解液相比,耐腐蚀性能明显提高。实施例二本例采用实施例一相同的LY12铝合金材料进行微弧氧化。所不同的是,本例的电解液中,磷酸盐六偏磷酸钠的终浓度为10g/L,含铁化合物采用的是终浓度为5g/L的柠檬酸铁铵,络合剂Na2EDTA的终浓度为7g/L。此外,微弧氧化方法中,恒流模式的电流密度为8A/dm2、频率200Hz、反应时间15min。其余与实施例一相同。采用电镜扫描对本例的微弧氧化处理的铝合金进行观察,结果显示,在铝合金表面形成了致密的膜层,膜层厚度为25μm。EDS发现膜层中存在P和Fe元素。同样采用盐雾腐蚀对本例的微弧氧化处理的铝合金进行耐腐蚀性能测试,结果显示,采用本例的电解液进行微弧氧化处理的铝合金,其耐腐蚀性能良好,经过1800小时的盐雾腐蚀后,未见明显的腐蚀痕迹。实施例三本例以6063铝合金材料为例进行微弧氧化,铝合金的尺寸为25×50×2mm3。本例的电解液中,磷酸盐六偏磷酸钠的终浓度为15g/L,含铁化合物采用的是终浓度为4g/L的硝酸铁,络合剂采用的是终浓度为5mL/L的三乙醇胺和终浓度为5g/L的Na2EDTA。此外,微弧氧化方法中,脉冲电源采用的是恒压模式,电压450V、频率500Hz、反应时间10min。其余与实施例一相同。采用电镜扫描对本例的微弧氧化处理的铝合金进行观察,结果显示,在铝合金表面形成了致密的膜层,膜层厚度为15μm。EDS发现膜层中存在P和Fe元素。同样采用实施例相同的方法对本例的微弧氧化处理的铝合金进行耐腐蚀性能测试,结果显示,采用本例的电解液进行微弧氧化处理的铝合金,其耐腐蚀性能良好,经过1800小时的盐雾腐蚀后,未见明显的腐蚀痕迹。实施例四本例采用实施例三相同的6063铝合金材料进行微弧氧化。所不同的是,本例的电解液中,磷酸盐采用的是终浓度为5g/L的磷酸氢二钠和10g/L的磷酸二氢钠,含铁化合物采用的是终浓度为5g/L的草酸高铁铵,络合剂采用的是终浓度为5g/L的Na2EDTA。此外,微弧氧化方法中,脉冲电源采用的是恒流模式,电流密度6A/dm2、频率800Hz、反应时间20min。其余与实施例一相同。采用电镜扫描对本例的微弧氧化处理的铝合金进行观察,结果显示,在铝合金表面形成了致密的膜层,膜层厚度为30μm。EDS发现膜层中存在P和Fe元素。同样采用实施例相同的方法对本例的微弧氧化处理的铝合金进行耐腐蚀性能测试,结果显示,采用本例的电解液进行微弧氧化处理的铝合金,其耐腐蚀性能良好,经过1800小时的盐雾腐蚀后,未见明显腐蚀痕迹。实施例五本例采用实施例一相同的LY12铝合金材料进行微弧氧化。所不同的是,本例的电解液中,磷酸盐采用的是终浓度为5g/L的磷酸氢二钠和10g/L的磷酸二氢钠,含铁化合物采用的是终浓度为5g/L的氯化铁,络合剂采用的是终浓度为8g/L的酒石酸钠。此外,微弧氧化方法中,恒流模式的电流密度10A/dm2、频率1000Hz、反应时间15min。其余与实施例一相同。采用电镜扫描对本例的微弧氧化处理的铝合金进行观察,结果显示,在铝合金表面形成了致密的膜层,膜层厚度为20μm。EDS发现膜层中存在P和Fe元素。同样采用实施例相同的方法对本例的微弧氧化处理的铝合金进行耐腐蚀性能测试,结果显示,采用本例的电解液进行微弧氧化处理的铝合金,其耐腐蚀性能良好,经过1800小时的盐雾腐蚀后,未见明显的腐蚀痕迹。实施例六本例采用实施例一相同的LY12铝合金材料进行微弧氧化。所不同的是,本例的电解液中,磷酸盐采用的是终浓度为10g/L的焦磷酸钠和15g/L的磷酸二氢钠,含铁化合物采用的是终浓度为5g/L的草酸高铁铵,络合剂采用的是终浓度为5g/L的Na2EDTA。其余与实施例一相同。采用电镜扫描对本例的微弧氧化处理的铝合金进行观察,结果显示,在铝合金表面形成了致密的膜层,膜层厚度为18μm。EDS发现膜层中存在P和Fe元素。同样采用实施例相同的方法对本例的微弧氧化处理的铝合金进行耐腐蚀性能测试,结果显示,采用本例的电解液进行微弧氧化处理的铝合金,其耐腐蚀性能良好,经过1800小时的盐雾腐蚀后,未见明显腐蚀痕迹。实施例七本例采用实施例一相同的LY12铝合金材料进行微弧氧化。所不同的是,本例的电解液中,磷酸盐采用的是终浓度为10g/L的磷酸二氢钠和5g/L的多聚磷酸钠,含铁化合物采用的是终浓度为5g/L的草酸高铁铵,络合剂采用的是终浓度为5g/L的Na2EDTA。其余与实施例一相同。采用电镜扫描对本例的微弧氧化处理的铝合金进行观察,结果显示,在铝合金表面形成了致密的膜层,膜层厚度为16μm。EDS发现膜层中存在P和Fe元素。同样采用实施例相同的方法对本例的微弧氧化处理的铝合金进行耐腐蚀性能测试,结果显示,采用本例的电解液进行微弧氧化处理的铝合金,其耐腐蚀性能良好,经过1800小时的盐雾腐蚀后,未见明显的腐蚀痕迹。实施例八本例采用实施例一相同的LY12铝合金材料进行微弧氧化。所不同的是,本例的电解液中,磷酸盐采用的是终浓度为10g/L的磷酸二氢钠和5g/L的多聚磷酸钠,含铁化合物采用的是终浓度为8g/L的柠檬酸铁铵,络合剂采用的是终浓度为5g/L的Na2EDTA。其余与实施例一相同。采用电镜扫描对本例的微弧氧化处理的铝合金进行观察,结果显示,在铝合金表面形成了致密的膜层,膜层厚度为18μm。EDS发现膜层中存在P和Fe元素。同样采用实施例相同的方法对本例的微弧氧化处理的铝合金进行耐腐蚀性能测试,结果显示,采用本例的电解液进行微弧氧化处理的铝合金,其耐腐蚀性能良好,经过1800小时的盐雾腐蚀后,未见明显的腐蚀痕迹。实施例九本例在实施例一的基础上对磷酸盐、含铁化合物和络合剂的具体化合物和用量进行了优化,按照表1的用量配制电解液,所采用的铝合金、微弧氧化以及微弧氧化后的检测与实施例一相同。表1电解液中各组分用量磷酸盐及其用量含铁化合物及其用量络合剂及其用量电解液1磷酸三钠20g/L草酸铁10g/L柠檬酸5g/L电解液2六偏磷酸钠15g/L柠檬酸铁5g/L草酸2g/L电解液3六偏磷酸钠15g/L硫酸铁5g/LNa2EDTA2g/L电解液4六偏磷酸钠5g/L硫酸亚铁1g/LNa2EDTA1g/L电解液5六偏磷酸钠25g/L氯化亚铁8g/LNa2EDTA5g/L电解液6六偏磷酸钠35g/L普鲁士蓝10g/LNa2EDTA8g/L电解液7六偏磷酸钠30g/L硫化亚铁10g/LNa2EDTA8g/L电解液8六偏磷酸钠45g/L二硫化铁12g/LNa2EDTA9g/L电解液9六偏磷酸钠50g/L草酸高铁铵15g/LNa2EDTA10g/L电解液10六偏磷酸钠5g/L草酸高铁铵1g/LNa2EDTA1g/L本例按照表1的组分和用量配制了10个电解液,分别对LY12铝合金进行微弧氧化,微弧氧化的具体方法和条件与实施例一相同。采用电镜扫描对本例的微弧氧化处理的十个铝合金进行观察,结果显示,在铝合金表面形成了致密的膜层,膜层厚度在5-50μm之间。EDS发现十个铝合金表面的膜层中都存在P和Fe元素。盐雾腐蚀的测试结果显示,除电解液4和电解液10处理的铝合金以外,其它八个电解液微弧氧化处理的铝合金,其耐腐蚀性能良好,经过1800小时的盐雾腐蚀后,未见明显的腐蚀痕迹;电解液4和电解液10处理的铝合金经过1000小时的盐雾腐蚀后,未见明显的腐蚀痕迹,但是经过1800小时的盐雾腐蚀存在细微的腐蚀现象。可见,磷酸盐终浓度为5-50g/L、含铁化合物终浓度为1-15g/L、络合剂终浓度为1-10g/L配制的电解液都能够在不同程度上提高微弧氧化膜层的耐腐蚀性能。磷酸盐可以采用六偏磷酸钠、磷酸氢二钠、磷酸二氢钠、多聚磷酸钠、磷酸三钠或焦磷酸钠,含铁化合物可以采用草酸高铁铵、草酸铁、柠檬酸铁铵、柠檬酸铁、硝酸铁、硫酸铁、硫酸亚铁、氯化铁、氯化亚铁、普鲁士蓝、硫化亚铁或二硫化铁,络合剂可以采用乙二胺四乙酸二钠、三乙醇胺、酒石酸钠、柠檬酸或草酸。以上内容是结合具体的实施方式对本申请所作的进一步详细说明,不能认定本申请的具体实施只局限于这些说明。对于本申请所属
技术领域:
的普通技术人员来说,在不脱离本申请构思的前提下,还可以做出若干简单推演或替换,都应当视为属于本申请的保护范围。当前第1页1 2 3