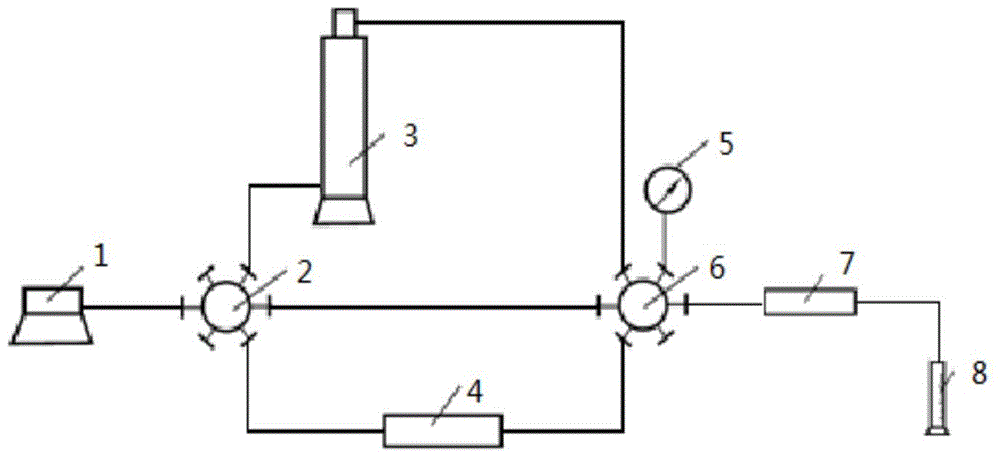
本发明涉及一种低成本提高原油采收率的方法。
背景技术:
:化学驱是通过水溶液中添加化学剂,改变注入流体的物理化学性质和流变学性质以及与储层岩石的相互作用特征而提高采收率的一种强化措施,在我国得以快速发展,其主要原因是我国储层为陆相沉积非均质性较强,陆相生油原油黏度较高,在EOR方法中更适合于化学驱。表面活性剂驱油技术就是将表面活性剂加入到注入水中,通过降低油水界面张力提高洗油能力来改善驱油效率的一种提高采收率方法。聚合物驱油技术是一种重要的提高石油采收率的方法,与一般水驱相比,聚合物驱油主要是增加水相的黏度,控制驱油体系的流度比,起到扩大波及体积的作用,相对于表面活性剂而言,成本较低。碱的加入主要是降低了表面活性剂的吸附量,增加表面活性剂的界面活性。作为化学驱中的重要技术,表面活性剂活性水驱、胶束溶液驱及微乳液驱技术、聚合物表面活性剂形成的二元复合驱油技术和聚合物表面活性剂碱形成的三元复合驱油技术已在中外进行了一些矿场试验,取得了良好的驱油效果。2002年大庆油田在外围低渗透油田开展了注活性水降压增注试验,2003年在外围低渗透油田和喇、萨、杏油田表外储层开展注活性水驱油试验,其目的是使油水界面张力大大降低,减小相间表面的作用,活化、分散滞留油块或剥离黏附的油膜,借助流动孔隙度的增加,提高油层的流动渗透率,达到降低启动压力、提高注水波及体积和驱油效率的效果。实践证明,活性水驱能够大幅度提高已投入开发区块的原油采收率,并且使一部分在目前经济技术条件下不能动用的储量有效投入开发。至1994年以来,大庆油田采用国外进口的重烷基苯磺酸盐开展了5个三元复合驱试验,在水驱采收率基础上再提高原油采收率20%,并依此明确了三元复合驱为聚合物驱之后的三次采油主导技术。油田在三元复合驱先导现场试验取得成功后,考虑到结垢和破乳难的问题,采取了二元复合驱的技术路线,使用以胜利原油为原料合成的石油磺酸盐表面活性剂为主剂,非离子表面活性为辅剂,可以在无碱条件下达到超低界面张力,并于2003年在孤东七区西南开展了矿场先导试验,提高采收率可12%,解决了结垢和破乳难问题。相比于聚合物驱油技术而言,表面活性剂作为驱油剂使用的关键是表面活性剂的性能和成本,特别是制备成本直接制约了其在油田提高采收率方面的应用。美孚石油公司的专利US3927716、US4018281、US4216097相继报道了采用碱水驱油、表面活性剂或碱水驱油及使用两性离子表面活性剂驱油的结果,采用的两性离子表面活性剂为不同链长的羧酸或磺酸盐型甜菜碱表面活性剂,在总矿化62000~160000mg/L,钙镁离子1500~18000mg/L的模拟盐水中,对德克萨斯南部原油的界面张力达10-1~10-4mN/m。美孚石油公司的专利US4370243报道了采用油溶性的醇、磺酸甜菜碱及季铵盐组成的驱油体系,该体系既可起到表面活性剂的作用,也可以起到流度控制剂的作用,其中季铵盐为亲油基碳链长为16~20的阳离子表面活性剂,采用2wt%的十八烷基二羟乙基丙基磺酸盐甜菜碱与1.0%的正己醇作为驱油剂,注入1.9PV后,原油即可100%驱出,但表面活性剂的吸附损耗较大达到6mg/g,在此基础上加入价格相对低廉的2.0%四乙基溴化铵作为牺牲剂以降低表面活性剂的吸附量。美国德克萨斯大学申请的专利US8211837,报道了采用简单廉价的线性醇在高温下催化二聚反应得到支链化的长碳醇,与环氧丙烷、环氧乙烷聚合后进行硫酸酯化反应,相对于昂贵的磺酸盐型表面活性剂,低成本合成了大亲水基聚醚硫酸盐表面活性剂,由于大亲水基团的存在,从而使得该硫酸盐表面活性剂在碱性条件下高温稳定性能优良,0.3%的支链醇聚醚硫酸盐(C32-7PO-6EO硫酸盐)与0.3%的内烯烃磺酸盐(C20~24IOS)盐水溶液在85℃与相同量的原油混合,其增溶参数为14。国外研究使用的表面活性剂由于使用量大、成本高,作为驱油剂在实际应用中受到了一定的限制。聚醚羧酸盐是一类阴离子表面活性剂,往往是由非离子表面活性剂通过羧甲基化改性而来的,兼有非离子型和阴离子表面活性剂的特征,具有表面张力低、毒性小、易生物降解等特点,是一类多功能的“绿色表面活性剂”。由于其特殊的性质,脂肪醇醚羧酸盐在化妆品、洗涤剂、生物化学、制药、食品加工、原油破乳、稠油降黏等领域有着广泛的应用。美国专利US4818440报道了脂肪酰胺聚氧乙烯醚乙酸的制备及应用,其中羧甲基化反应采用的是分批次加入氢氧化钠和氯乙酸钠固体,最终聚醚转化率达到75~80%,合成的粗产品经过酸化提纯得到纯度较高的脂肪酰胺聚氧乙烯醚乙酸,作为主要成分应用于香波等日化产品中。该报道中,聚醚羧酸盐需经过提纯,合成工艺复杂,产生的三废多,制备成本较高,且未涉及在提高原油采收率方面的应用。耐温抗盐聚合物的使用是提高原油采收率的另一关键因素。早期常用于强化石油开采(EOR)的聚合物驱的工业产品仅有部分水解聚丙烯酰胺(HPAM),它依赖于高分子量和聚合物分子链上的离子和强极性侧基的排斥作用达到增黏效果。但是,高分子量聚合物当受到较大的拉伸和剪切应力时,易于发生机械降解而丧失黏度,在低渗透率岩层中注入聚合物时尤为明显。水溶液中的阳离子,尤其是二价离子,会屏蔽聚合物中的离子基团,使聚合物分子链卷曲,流体力学体积减小甚至沉淀,从而使增黏性大大降低。当地层油层温度较高时(>93℃),聚丙烯酰胺(PAM)中的酰胺基在高温水溶液中易水解,使聚合物溶液的抗盐性急剧下降。近年来,有关耐温抗盐型聚丙烯酰胺的研究主要通过在聚合物主链上引入大侧基或刚性侧基提高聚合物的热稳定性、引入抑制水解的单体或对盐不敏感的单体进行共聚来提高聚合物的耐水解及抗盐性能,或通过疏水基团的疏水缔合作用来改善聚合物的耐温抗盐性能。上述结果表明,低成本制备驱油组合物是提高原油采收率的关键。采用“一锅法”制备含聚醚羧酸盐表面活性剂的方法,可以大大降低了驱油组合物关键组分表面活性剂的生产成本,实现了表面活性剂的绿色生产。同时制备的表面活性剂的水溶液,或者表面活性剂和聚合物的水溶液,或含表面活性剂和聚合物和碱的水溶液驱油组合物对于降低原油的界面张力、乳化原油和扩大波及体积具有较好的效果,使得该类驱油组合物在油田提高采收率方面具有较大的应用前景。因此,针对高温高盐砂岩油藏的特点,发明了一种在地层温度下长时间结构稳定,并能与原油形成10-2~10-4mN/m低界面张力,有效提高原油采收率的驱油剂。本发明所述的正是这种驱油组合物、制备方法及其在提高原油采收率中的应用。技术实现要素:本发明所要解决的技术问题是现有技术中驱油组合物驱油效率低、制备成本高、抗高温和高盐性能差的问题,提供一种新的低成本提高原油采收率的方法。该方法将含表面活性剂的水溶液,或者表面活性剂、聚合物和碱性物质的水溶液作为驱油组合物用于驱油过程中,具有耐温性能好、在高温条件下驱油效率高的优点。为了解决上述技术问题,本发明采用的技术方案如下:一种低成本提高原油采收率的方法,包括以下步骤:(1)将驱油剂与水混合得到驱油体系;(2)将所述驱油体系在驱油温度25~120℃、总矿化度>500毫克/升地层水条件下与含油地层接触,将所述含油地层中的原油驱替出来;其中,所述的驱油剂,以质量份数计,包括以下组分:1)1份表面活性剂;2)0~50份聚合物;3)0~50份碱;所述聚合物和碱的量不同时为0;所述表面活性剂为阴-非离子表面活性剂与盐及醇的混合物;所述聚合物为适用于油田采油的聚合物;所述碱为无机碱或有机胺中的至少一种;所述驱油体系中,以总的驱油体系质量计,含所述表面活性剂的浓度为0.001~2.0wt%,含所述聚合物的浓度为0~1.8wt%,含所述碱的浓度为0~2.0wt%。上述技术方案中,所述表面活性剂为式I所示的聚醚羧酸盐表面活性剂、醇及盐以摩尔比为1:(1~10):(1~10)形成的混合物;R1X(CH2CH2O)m1(CH3CHCH2O)n(CH2CH2O)m2R2COOM,式I;X为O,R1为C8~C30的脂肪烃基或由C4~C20直链或支链的饱和及不饱和烃基取代的苯环或萘环;或R1X为松香酸根;m1=0~50、m2=0~50,n=0~100,R2为C1~C5的亚烷基或羟基取代亚烷基;M选自氢、碱金属或者由式NR4(R5)(R6)(R7)所示基团中的至少一种;R4、R5、R6、R7为独立选自H、(CH2)aOH或(CH2)bCH3中的一种,a=2~4、b=0~5中的任一整数;所述盐选自金属卤化物、有机酸盐中的至少一种;所述醇选自C1~C6短碳链醇。上述技术方案中,R1优选为C12~C24的烷基或由C8~C12烷基取代的苯基或R1X优选为松香酸根,R2为C1~C3的亚烷基或羟基取代亚烷基。上述技术方案中,优选m1=0~30,m2=0~30,n=0~30,且m1+m2与n不同时为零,a=2,b=0或1。上述技术方案中,所述金属卤化物优选自碱金属卤化物,所述有机酸盐优选自羟基取代的羧酸盐。本发明含聚醚羧酸盐表面活性剂关键有效成分是聚醚羧酸盐I,可以将所述聚醚羧酸盐表面活性剂与所述盐和醇按所需的比例混合而得,优选以下述制备方法获得。上述技术方案中,所述聚合物没有严格限制,可以是本领域技术人员所熟知的各种用于油田采油的聚合物,例如但不限定选自黄原胶、羟甲基纤维素、羟乙基纤维素、阴离子型聚丙烯酰胺、改性聚丙烯酰胺、疏水缔合聚合物、聚合物微球中的至少一种。上述技术方案中,所述疏水缔合聚合物优选由丙烯酰胺、耐温抗盐单体或疏水单体共聚而成;所述改性聚丙烯酰胺优选由丙烯酰胺、耐温抗盐单体共聚而成;耐温抗盐单体或疏水单体可以是本领域技术人员所熟知的含有大侧基或刚性侧基的单体(如苯乙烯磺酸、N-烷基马来酰亚胺、丙烯酰胺基长链烷基磺酸、长链烷基烯丙基二甲基卤化铵、3-丙烯酰胺基-3-甲基丁酸等)、含耐盐基团的单体(如2-丙烯酰胺基-2-甲基丙磺酸)、含耐水解基团的单体(如N-烷基丙烯酰胺)、含可抑制酰胺基水解的基团的单体(如N-乙烯吡咯烷酮)、含疏水基团的单体等中的至少一种,耐温抗盐单体优选为2-丙烯酰胺基-2-甲基丙磺酸,疏水单体优选为2-丙烯酰胺基十二烷基磺酸。上述技术方案中,所述的疏水缔合聚合物中丙烯酰胺与耐温抗盐单体与疏水单体的摩尔比为1:(0.1~40):(0.001~0.05),黏均分子量为500~2500万;更优选为丙烯酰胺与耐温抗盐单体与疏水单体的摩尔比为1∶(0.1~20)∶(0.001~0.01),黏均分子量为1200~2200万。上述技术方案中,所述改性聚丙烯酰胺中丙烯酰胺与耐温抗盐单体的摩尔优选比为(0.1~40)∶1。上述技术方案中,所述的疏水缔合聚合物优选丙烯酰胺、2-丙烯酰胺基-2-甲基丙磺酸和2-丙烯酰胺基十二烷基磺酸共聚而成,丙烯酰胺、2-丙烯酰胺基-2-甲基丙磺酸和2-丙烯酰胺基十二烷基磺酸摩尔比优选为1:(0.1~40):(0.001~0.05),更优选为1∶(0.1~20)∶(0.001~0.01)。上述技术方案中,所述改性聚丙烯酰胺优选由丙烯酰胺、2-丙烯酰胺基-2-甲基丙磺酸共聚而成,丙烯酰胺与2-丙烯酰胺基-2-甲基丙磺酸摩尔比优选为(0.1~40)∶1,改性聚丙烯酰胺的黏均分子量优选为800~2500万。上述技术方案中,所述无机碱性物质优选碱金属氢氧化物、碱土金属氢氧化物、碱金属碳酸盐中的至少一种;进一步优选碱金属氢氧化物选自氢氧化钠、氢氧化钾中的至少一种,碱土金属氢氧化物选自氢氧化镁、氢氧化钙中的至少一种,碱金属碳酸盐选自碳酸钠或碳酸氢钠中的至少一种。上述技术方案中,所述有机碱性物质优选分子中含有伯胺基、仲胺基、叔胺基、季铵碱基中的至少一种,进一步优选为乙醇胺、二乙醇胺、三乙醇胺或三乙胺中的至少一种。上述技术方案中,所述驱油组合物中表面活性剂与聚合物与碱性物质的质量比优选为1∶(0~2):(0~5)。上述技术方案中,所述驱油组合物的制备方法,优选方案之一包括以下步骤:(1)在碱性催化剂存在下,R1XH依次与所需量环氧乙烷、环氧丙烷、环氧乙烷反应得到R1X(CH2CH2O)m1(CH3CHCH2O)n(CH2CH2O)m2H;(2)将R1X(CH2CH2O)m1(CH3CHCH2O)n(CH2CH2O)m2H与YR2COOR3以及碱金属氢氧化物或碱金属醇盐以摩尔比1:(1~5):(1~10)混合,搅拌下于反应温度50~120℃,反应3~15小时,得到聚醚羧酸酯中间体R1X(CH2CH2O)m1(CH3CHCH2O)n(CH2CH2O)m2R2COOR3,无需分离加入水或醇水进行皂化反应,回流1~10小时后,得到所需的含聚醚羧酸盐表面活性剂混合物;(3)按所述质量份数计,将步骤(2)得到的表面活性剂混合物与聚合物、碱混合均匀,得到所述的驱油组合物。其中,R3选自C1~C8的烷基;Y选自氯、溴或碘;碱性催化剂为碱金属氢氧化物或碳酸盐、碱土金属氢氧化物或碳酸盐中的至少一种;醇水溶液中的醇为C1~C6短碳链醇。所述含聚醚羧酸盐表面活性剂的制备方法反应方程式如下:上述技术方案中,步骤(1)中反应温度优选为120~160℃,压力优选为0.30~0.60MPa表压,碱性催化剂优选为氢氧化钾或无水碳酸钾中的至少一种。上述技术方案中,优选Y为氯或溴。上述技术方案中,R3优选为C1~C4的烷基。上述技术方案中,步骤(2)中碱金属氢氧化物优选为氢氧化钾或氢氧化钠中的至少一种,R1X(CH2CH2O)m1(CH3CHCH2O)n(CH2CH2O)m2H与YR2COOR3以及碱金属氢氧化物或碱金属醇盐的摩尔比优选为1:(1~3):(2~6),短碳链醇优选为C1~C5短碳链醇。为了得到含聚醚羧酸盐表面活性剂当M为由式NR4(R5)(R6)(R7)所示基团时的产品,可在步骤(2)的基础上加入酸调节至pH=1-2,再用所需的NR4(R5)(R6)(R7)中和即可。上述技术方案中,所述式NR4(R5)(R6)(R7)所示基团相应的碱优选自氨、乙醇胺、二乙醇胺、三乙醇胺、三乙胺等。YR2COOR3的例子有但不限于氯乙酸酯(例如氯乙酸乙酯)、溴乙酸酯(例如溴乙酸乙酯)等。上述技术方案中,所述改性聚丙烯酰胺由丙烯酰胺、2-丙烯酰胺基-2-甲基丙磺酸两种单体采用水溶液聚合法而成,可以从市场购得,也可以通过常规的自由基共聚制得。无论嵌段共聚还是无规共聚,得到的产物均可用于本发明并达到本发明的目的。本发明实施例中的改性聚丙烯酰胺,是将丙烯酰胺与2-丙烯酰胺基-2-甲基丙磺酸两种单体按照摩尔比(0.1~40)∶1混合后以水为溶剂用常规自由基引发剂引发自由基聚合反应而得。上述技术方案中,所述疏水缔合聚合物由丙烯酰胺、2-丙烯酰胺基-2-甲基丙磺酸和2-丙烯酰胺基十二烷基磺酸三种单体采用水溶液聚合法而成,可以从市场购得,也可以通过常规的自由基共聚制得。无论嵌段共聚还是无规共聚,得到的产物均可用于本发明并达到本发明的目的。本发明实施例中的疏水缔合聚合物,是将丙烯酰胺、2-丙烯酰胺基-2-甲基丙磺酸与2-丙烯酰胺基十二烷基磺酸三种单体按照摩尔比1:(0.1~20):(0.001~0.01)混合后以水为溶剂用常规自由基引发剂引发自由基聚合反应而得。本发明驱油组合物的关键有效成分是所述组分1)、2)和3),本领域技术人员知道,为了便于运输和贮存或现场使用等方面考虑,可以采用各种供应形式,例如不含水的固态形式,或者含水的固态形式,或者含水的膏状形式,或者水溶液形式;水溶液形式包括用水配成浓缩液的形式,直接配成现场驱油所需浓度的驱油剂形式;其中,对水没有特殊要求,可以是去离子水,还可以是含无机矿物质的水,而含无机矿物质的水可以是自来水、油田地层水或油田注入水。本发明驱油组合物还可以含有本领域常用的泡沫剂、小分子有机物(例如异丙醇、乙二醇单丁醚、DMSO等)等采油助剂。上述技术方案中,所述驱油组合物可以采用各种常规混合方法按照所需量各组分混合得到,用于驱油时按照所需浓度用水溶解得到驱油剂用于驱油;还可以根据所需驱油剂的浓度,将所述驱油组合物中各组分分别溶解于水中得到驱油剂用于驱油。制备中所用的水可以为自来水、河水、海水,油田地层水;优选的水是:模拟油田地层水,总矿化度优选为10000~250000毫克/升。本发明采用物理模拟驱替评价方法进行效果评价,具体评价方法为:将岩心恒温烘干至恒重,测定岩心的气测渗透率;以上述模拟油田地层水饱和岩心,计算其孔隙体积,于驱油温度下,以原油饱和岩心,记录饱和原油的体积,再以0.1ml/min的速度泵入地层水,驱至含水达100%,计算水驱提高原油的采收率,然后以0.1ml/min的速度转注0.1~1PV(岩心孔隙体积)步骤(3)得到的驱油剂,以0.1ml/min的速度水驱至含水100%,计算在水驱基础上提高原油采收率的百分数。本发明采用的含聚醚羧酸盐表面活性剂的制备方法,由于得到高纯度阴离子羧酸盐表面活性剂往往比较困难,需多次酸化提纯,造成大量三废物的产生,采用将反应生成的短链碳醇作为助溶剂的方法,既可以改善表面活性剂在水中的溶解性,又可以省去分离短链碳醇的步骤,生成的副产物盐以及可能过量的碱对表面活性剂的界面性能有促进作用亦无需分离,从而在保证表面活性剂性能的基础上大大降低了表面活性剂的生产成本,实现了表面活性剂的绿色生产。制备的聚醚羧酸盐表面活性剂,由于同时含有聚醚及羧酸根阴离子基团,从而赋予了该表面活性剂优良的抗温耐盐性能,聚醚羧酸盐表面活性剂具有较低的临界胶束浓度(cmc),低于传统阴离子表面活性剂1~2个数量级,因而使得该表面活性剂的使用浓度窗口较宽,可解决油田现场使用过程中因表面活性剂浓度逐步下降而导致的界面张力上升问题,使得表面活性剂在井下运移过程中,即使浓度较低仍可保持超低的油水界面张力,从而能够提高驱油效率。组合物中的改性聚丙烯酰胺或疏水缔合聚丙烯酰胺,由于耐温抗盐片段的引入,赋予聚合物较好的耐温抗盐性能。组合物中的碱可与原油中的表面活性剂形成皂,进一步提高驱油体系的界面活性,减少表面活性剂在地层的吸附,对提高原油采收率具有较好的作用。本发明中的阴离子表面活性剂含有聚醚的基团由EO-PO-EO链段结构组成,本发明人惊奇的发现,在其他结构相同且相同EO数和PO数的条件下,采用此种排列方式得到的组合物的驱油效果远优于EO-PO排列或PO-EO排列。本发明采用的驱油剂及低成本提高原油采收率的方法,用于地层温度50~100℃、矿化度10000~250000毫克/升的模拟油田地层水和原油,以质量百分比计,用量为0.005~0.6wt%表面活性剂与0~0.3wt%上述的疏水缔合聚合物与0~1.2wt%上述的碱形成驱油剂,测定了该驱油剂组合物水溶液的表观黏度,与油田脱水原油之间的动态界面张力值可达10-2~10-4mN/m,经物理模拟驱替试验室内评价,该驱油剂能在水驱基础上提高原油采收率可达19.89%,取得了较好的技术效果。附图说明图1为模拟岩心驱替试验流程图。其中,1为平流泵,2为六通阀,3为中间容器,4为药剂罐,5为压力泵,6为六通阀,7为填砂管,8为量筒。下面通过实施例对本发明作进一步阐述。具体实施方式【实施例1】(1)制备的聚醚羧酸盐表面活性剂结构式如下:向装有搅拌装置的2L压力反应器中加入242克(1摩尔)十六醇、8.6克氢氧化钾,加热至80~90℃时,开启真空系统,在高真空下脱水1小时,然后用氮气置换3~4次,将体系反应温度调至140℃缓缓通入132.0克(3摩尔)环氧乙烷,再于150℃缓缓通入469.8克(8.1摩尔)环氧丙烷,控制压力≤0.60MPa,待环氧丙烷反应结束后再将温度调至140℃缓缓通入178.2克(4.05摩尔)环氧乙烷,控制压力≤0.40MPa。反应结束后,降温至90℃,真空除去低沸物,冷却后中和、脱水,得十六醇聚氧乙烯(3)聚氧丙烯(8)聚氧乙烯(4)醚998.8克,收率98.5%。十六醇聚氧乙烯(3)聚氧丙烯(8)聚氧乙烯(4)醚507克(0.5摩尔)和61.6克(1.1摩尔)氢氧化钾加入配有机械搅拌、温度计和回流冷凝管的2500毫升的反应瓶内,搅拌下缓慢滴入91.9克(0.55摩尔)溴乙酸乙酯,控制反应温度80℃反应5小时,冷却后加入500克水及50克95%乙醇,继续加热至回流反应4小时。冷却至室温,得到所需的表面活性剂S01,以质量百分比计,十六醇聚氧乙烯(3)聚氧丙烯(8)聚氧乙烯(4)醚乙酸钾46.02%,溴化钾4.94%,羟乙酸钾0.47%,乙醇6.04%,水42.51%。(2)分别配制不同二价阳离子及总矿化度的油田模拟地层水,具体组成见表1所示。不同油田的脱水原油黏度见表2所示。以胜利油田模拟地层水A分别配制步骤(1)制备的S01表面活性剂、疏水缔合聚合物(P1,共聚AM/AMPS/2-丙烯酰胺基十二烷基磺酸摩尔比=1/0.5/0.001,黏均分子量1930万)和碳酸钠的水溶液,搅拌3小时,再将三者混合得到一种均匀的聚表碱三元体系驱油剂,测定体系在87℃时的黏度及油水界面张力,并与S01、P1及S01+P1体系相比较,见表3所示。以模拟地层水分别配制不同浓度的S01水溶液,测定其对油田脱水原油的油水界面张力,见表4所示。表观黏度由美国Brookfield公司的BROODFIELDIII型黏度计测定,界面张力由美国德克萨斯大学生产的TX500型旋转滴界面张力仪测定。(3)将人造岩心恒温烘干至恒重,测量岩心的平均直径及岩心长度,称量岩心干重,测定岩心的气测渗透率。以上述地层水饱和岩心,测试其孔隙体积。以胜利油田脱水原油饱和岩心,记录饱和原油的体积。于87℃温度下,以胜利油田模拟地层水A驱至采出液含水达100%,计算水驱提高原油的采收率,转注0.3PV(岩心孔隙体积)步骤(2)合成的聚表碱三元体系驱油剂后,水驱至含水100%,计算在水驱基础上提高原油采收率的百分数,同时与注相同PV的单一或二元驱油剂相对比,见表3所示。岩心气测渗透率用HKGP-3型致密岩心气体渗透率孔隙度测定仪测定,采用的模拟岩心驱替试验流程如图1所示。【实施例2】(1)制备的聚醚羧酸盐表面活性剂结构式如下:向装有搅拌装置的2L压力反应器中加入220克(1摩尔)壬基酚、1.5克氢氧化钾和4.6克无水碳酸钾,同【实施例1】进行除水和氮气置换,将体系反应温度调至140℃缓缓通入88.0克(2.0摩尔)环氧乙烷,再于150℃缓缓通入585.8克(10.1摩尔)环氧丙烷,控制压力≤0.60MPa,待环氧丙烷反应结束后再将温度调至140℃缓缓通入134.2克(3.05摩尔)环氧乙烷,控制压力≤0.40MPa。反应结束后,同【实施例1】后处理,得壬基酚聚氧乙烯(2)聚氧丙烯(10)聚氧乙烯(3)醚991.4克,收率97.2%。壬基酚聚氧乙烯(2)聚氧丙烯(10)聚氧乙烯(3)醚510克(0.5摩尔)和60.0克(1.5摩尔)氢氧化钠加入配有机械搅拌、温度计和回流冷凝管的2500毫升的反应瓶内,搅拌下缓慢滴入102.4克(0.75摩尔)氯乙酸异丙酯,控制反应温度100℃反应3小时,冷却后加入500克水及70克异丙醇,继续加热至回流反应3小时。冷却至室温,得到所需的表面活性剂S02,以质量百分比计,壬基酚聚氧乙烯(2)聚氧丙烯(10)聚氧乙烯(3)醚乙酸钠46.21%,氯化钠2.43%,羟乙酸钠2.31%,异丙醇8.03%,水41.02%。(2)以胜利油田模拟地层水A分别配制步骤(1)制备的S02、疏水缔合聚合物(P1,共聚AM/AMPS/2-丙烯酰胺基十二烷基磺酸摩尔比=1/0.5/0.001,黏均分子量1930万)和碳酸钠水溶液,搅拌4小时,其余同【实施例1】(2),结果见表5所示。以油田模拟地层水分别配制不同浓度的S02水溶液,测定其油水界面张力,见表4所示。(3)同【实施例1】(3)进行室内模拟驱油试验,结果见表5所示。【实施例3】(1)制备的聚醚羧酸盐表面活性剂结构式如下:R1O(CH2CH2O)5(CHCH3CH2O)4(CH2CH2O)20CH2COONa其中,R1的碳链分布为:C1272.3%、C1427.7%。向装有搅拌装置的2.5L压力反应器中加入195.0克(1摩尔)混合十二/十四(C12~14)醇、14.5克无水碳酸钾,同【实施例1】进行除水和氮气置换,将体系反应温度调至140℃缓缓通入222.2克(5.05摩尔)环氧乙烷,再于150℃缓缓通入234.9克(4.05摩尔)环氧丙烷,控制压力≤0.50MPa,待环氧丙烷反应结束后,降温,于130℃缓缓通入924克(21摩尔)环氧乙烷,控制压力≤0.40MPa。反应结束后,同【实施例1】后处理,得混合十二/十四(C12~14)醇聚氧乙烯(5)聚氧丙烯(4)聚氧乙烯(20)醚1513.3克,收率99.1%。混合十二/十四(C12~14)醇聚氧乙烯(5)聚氧丙烯(4)聚氧乙烯(20)醚763.5克(0.5摩尔)和60.0克(1.5摩尔)氢氧化钠加入配有机械搅拌、温度计和回流冷凝管的2500毫升的反应瓶内,搅拌下缓慢滴入79.6克(0.65摩尔)氯乙酸乙酯,控制反应温度90℃反应4小时,冷却后加入700克水及200克95%乙醇,继续加热至回流反应5小时。冷却至室温,得到所需的表面活性剂S03,以质量百分比计,混合十二/十四(C12~14)醇聚氧乙烯(5)聚氧丙烯(4)聚氧乙烯(20)醚乙酸钠44.53%,氯化钠1.65%,羟乙酸钠0.81%,氢氧化钠0.43%乙醇12.35%,水40.23%。(2)以中原油田模拟地层水C配制步骤(1)制备的S03和疏水缔合聚合物(P2,共聚AM/AMPS/2-丙烯酰胺基十二烷基磺酸摩尔比=1/0.5/0.002,黏均分子量1800万)水溶液,搅拌4小时,测定温度为90℃,其余同【实施例1】(1),结果见表6所示。以油田模拟地层水分别配制不同浓度的S03水溶液,测定其对油田脱水原油的界面张力,见表4所示。(3)同【实施例1】(3)进行室内模拟驱油试验,不同之处在于驱油温度为90℃,结果见表6所示。【实施例4】(1)制备的聚醚羧酸盐表面活性剂结构式如下:向装有搅拌装置的2.5L压力反应器中加入158克(1摩尔)癸醇、7.2克氢氧化钾,同【实施例1】进行除水和氮气置换,将体系反应温度调至150℃缓缓通入1287.6克(22.2摩尔)环氧丙烷,控制压力≤0.50MPa,待环氧丙烷反应结束后,降温,同【实施例1】后处理,得癸醇聚氧丙烯(22)醚1365.2克,收率95.2%。癸醇聚氧丙烯(22)醚717克(0.5摩尔)和61.6克(1.1摩尔)氢氧化钾加入配有机械搅拌、温度计和回流冷凝管的2500毫升的反应瓶内,搅拌下缓慢滴入91.9克(0.55摩尔)溴乙酸乙酯,同【实施例1】反应,得到所需的表面活性剂S04,以质量百分比计,癸醇聚氧丙烯(22)醚乙酸钾54.05%,溴化钾4.05%,羟乙酸钾0.41%,乙醇5.07%,水36.42%。(2)以河南油田模拟地层水B配制步骤(1)制备的S04、改性聚丙烯酰胺(P3,共聚单体AM/AMPS摩尔比=4/1,黏均分子量1500万)和碳酸钠水溶液,搅拌4小时,测定温度为80℃,其余同【实施例1】(1),结果见表7所示。以油田模拟地层水配制不同浓度的S04水溶液,测定其油水界面张力,见表4所示。(3)同【实施例1】(3)进行室内模拟驱油试验,不同之处在于驱油温度为80℃,结果见表7所示。【实施例5】(1)制备的聚醚羧酸盐表面活性剂结构式如下:向装有搅拌装置的2.5L压力反应器中加入328克(1摩尔)二十二醇、15.1克无水碳酸钾,同【实施例1】进行除水和氮气置换,将体系反应温度调至140℃缓缓通入1122.0克(25.5摩尔)环氧丙烷,控制压力≤0.50MPa,待环氧丙烷反应结束后,降温,同【实施例1】后处理,得二十二醇聚氧乙烯(25)醚1408.0克,收率98.6%。二十二醇聚氧乙烯(25)醚714克(0.5摩尔)和128.8克(2.3摩尔)氢氧化钾加入配有机械搅拌、温度计和回流冷凝管的2500毫升的反应瓶内,搅拌下,缓慢滴入150.6克(1.0摩尔)氯乙酸正丁酯,控制反应温度110℃反应5小时,冷却后加入400克水及50克95%乙醇,继续加热至回流反应3小时。冷却至室温,得表面活性剂组合物S05,得到所需的表面活性剂S05,以质量百分比计,二十二醇聚氧乙烯(25)醚乙酸钾53.17%,氯化钾2.63%,羟乙酸钾4.03%,氢氧化钾1.19%,混合醇(乙醇+正丁醇)8.66%,水30.32%。(2)以中原油田模拟地层水D配制步骤(1)制备的S05和疏水缔合聚合物(P2,共聚AM/AMPS/2-丙烯酰胺基十二烷基磺酸摩尔比=1/0.5/0.002,黏均分子量1800万)水溶液,搅拌4小时,测定温度为95℃,其余同【实施例1】(1),结果见表8所示。以油田模拟地层水配制不同浓度的S05水溶液,测定其对油田脱水原油的界面张力,见表4所示。(3)同【实施例1】(3)进行室内模拟驱油试验,不同之处在于驱油温度为95℃,结果见表8所示。【实施例6】(1)制备的聚醚羧酸盐表面活性剂结构式如下:同【实施例5】,不同之处在将反应液冷却至30℃,加入浓盐酸调节pH=2,加入57.8克(0.55摩尔)的二乙醇胺中和生成的羧酸,得到所需的表面活性剂S06,以质量百分比计,二十二醇聚氧乙烯(25)醚乙酸二乙醇胺盐53.12%,氯化钾6.41%,羟乙酸钾3.76%,混合醇(乙醇+正丁醇)8.15%,水28.56%。(2)同【实施例5】(2),结果见表9、表4所示。(3)同【实施例5】(3)进行室内模拟驱油试验,结果见表9所示。【实施例7】将表面活性剂模拟盐水溶液装入20毫升安碚瓶中,密封后放入烘箱内,测定不同老化时间后表面活性剂模拟盐水对与原油的油水界面张力,发现老化后油水界面张力仍可保持10-3~10-4mN/m的超低值,见表10所示。界面张力由美国德克萨斯大学生产的TX500型旋转滴界面张力仪测定。【比较例1】同【实施例1】,不同之处在于,反应结束后,在反应混合物中加入30%盐酸调节水相的pH=1~3,减压去除乙醇,分离得到有机相即十六醇聚氧乙烯(3)聚氧丙烯(8)聚氧乙烯(4)醚乙酸,加入水,以40%氢氧化钾溶液调节产品的pH=9,得到纯化后的表面活性剂十六醇聚氧乙烯(3)聚氧丙烯(8)聚氧乙烯(4)醚乙酸S07,以质量百分比计,十六醇聚氧乙烯(3)聚氧丙烯(8)聚氧乙烯(4)醚乙酸45.89%,氢氧化钾0.87%,水53.24%。同【实施例1】测定油水界面张力,结果见表11所示。【比较例2】将一定量的对比表面活性剂以不同矿化度的模拟盐水A~D溶解,测定不同浓度对比表面活性剂溶液对几种原油的油水界面张力,结果见表11所示。界面张力由美国德克萨斯大学生产的TX500型旋转滴界面张力仪测定。表11中,S08为十六醇聚氧乙烯(3)聚氧丙烯(8)聚氧乙烯(4)醚;S09为壬基酚聚氧乙烯(2)聚氧丙烯(10)聚氧乙烯(3)醚;S10为混合十二/十四(C12~14)醇聚氧乙烯(5)聚氧丙烯(4)聚氧乙烯(20)醚;S11:癸醇聚氧丙烯(22)醚;S12:二十二醇聚氧乙烯(25)醚。【比较例3】同【实施例1】,不同之处在于,与环氧丙烷和环氧乙烷不是先后分步进行反应的,而是将两者混合后一步进行反应。即在140~150℃缓缓通入469.8克(8.1摩尔)环氧丙烷和310.2克(7.05摩尔)环氧乙烷混合物,控制压力≤0.60MPa,其余相同,得到含聚醚羧酸盐表面活性剂混合物S13。同【实施例1】进行界面性能测定试验,结果见表11所示。【比较例4】同【实施例2】,不同之处在于,与环氧丙烷和环氧乙烷不是先后分步进行反应的,而是将两者混合后一步进行反应。即在140~150℃缓缓通入585.8克(10.1摩尔)环氧丙烷和222.2克(5.05摩尔)环氧乙烷混合物,控制压力≤0.60MPa,其余相同,得到含聚醚羧酸盐表面活性剂混合物S14。同【实施例1】进行界面性能测定试验,结果见表11所示。【比较例5】同【实施例3】,不同之处在于,与环氧丙烷和环氧乙烷不是先后分步进行反应的,而是将两者混合后一步进行反应。即在120~160℃缓缓通入234.9克(4.05摩尔)环氧丙烷和11144克(26.0摩尔)环氧乙烷混合物,其余相同,得到含聚醚羧酸盐表面活性剂混合物S15。同【实施例1】进行界面性能测定试验,结果见表11所示。【比较例6】同【实施例1】,不同之处在于,以高分子量阴离子聚丙烯酰胺P4(黏均分子量为2500万)替代疏水缔合聚合物P1,其余相同,结果见12所示。表1模拟盐水Ca2+(mg/L)Mg2+(mg/L)TDS(mg/L)A120040032000B20128000C150008000180000D40001250250000表2原油原油来源地下原油黏(mPa.s)I胜利油田34.55.II河南油田3.51III中原油田1.84表3表4表面活性剂模拟盐水温度(℃)原油浓度(%)IFT(mN/m)S01A87I0.60.00881S01A87I0.30.00052S01A87I0.10.00235S01A87I0.050.00524S01A87I0.0250.00742S01A87I0.010.05271S01A87I0.0050.08145S01A87I0.0010.51241S01B80II0.30.01724S01C90III0.30.21483S02A87I0.30.00071S02A87I0.050.00454S02A87I0.010.01879S02A87I0.0050.04117S02B80II0.30.00721S02C90III0.30.46772S03C90III0.60.00081S03C90III0.30.00095S03C90III0.050.00425S03C90III0.010.00851S03C90III0.0050.02221S04B80II0.40.00078S04B80II0.20.00226S04B80II0.050.00546S04B80II0.010.01579S04B80II0.0050.08635S04C90III0.10.08771S05D95III0.30.00456S05D95III0.10.00072S05D95III0.0250.00231S05D95III0.010.00667S05D95III0.0050.04331S05D95III0.0010.52121S06D95III0.30.00322S06D95III0.10.00059S06D95III0.0250.00145S06D95III0.010.00544S06D95III0.0050.06331S06D95III0.0010.09741表5表6表7表8表9表10表面活性剂模拟盐水温度(℃)原油浓度(%)老化时间(d)IFT(mN/m)S01A87I0.300.00052S01A87I0.3300.00046S01A87I0.3600.00245S01A87I0.3900.00433S01A87I0.31800.00288S02A87I0.300.00071S02A87I0.3300.00053S02A87I0.3600.00121S02A87I0.3900.00457S02A87I0.31800.00571S03C90III0.300.00095S03C90III0.3300.00107S03C90III0.3600.00367S03C90III0.3900.00256S03C90III0.31800.00546S04B80II0.200.00226S04B80II0.2600.00322S04B80II0.2900.00087S04B80II0.21800.00095S05D95III0.300.00456S05D95III0.3150.00302S05D95III0.3600.00453S05D95III0.31800.00577S06D95III0.100.00544S06D95III0.1150.00489S06D95III0.1600.00688S06D95III0.11800.00752表11表12当前第1页1 2 3