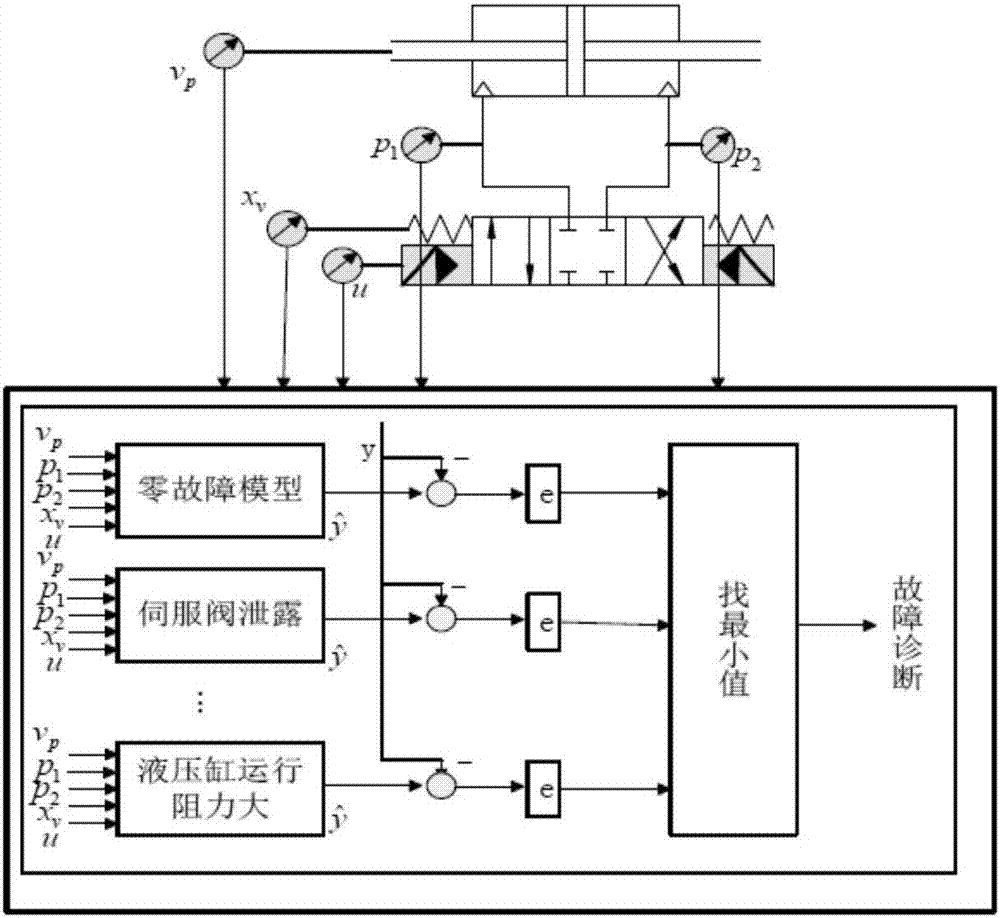
本发明属于机械设备故障诊断领域,具体涉及一种基于多模型的液压作动器故障诊断方法。
背景技术:在飞机起飞、飞行及着陆的过程中,接收来自驾驶员的指令信号,带动舵面偏转,实现飞机的各种运动。因此,液压伺服作动器(也称液压作动器)的性能与可靠性的好坏,对飞行控制系统乃至整个飞机的性能与安全至关重要。所以液压作动器在飞行控制系统中通常认为是关键部件。然而其中的液压作动器由于长期处于受力和不停地动作中,常常不可避免地出现各种故障而影响飞机正常飞行,可能引起一系列的连锁反应,甚至出现重大事故,引起巨大的损失。在液压作动器运行过程中,不可避免存在油液污染、磨损等问题,容易造成液压作动器的渐发性故障,这些渐发性故障的产生并不会马上造成液压作动器无法运行,但是会降低系统的效率与性能。针对系统的状态进行及时有效的维护,不仅可以减少维护所需的投入资源,提高系统的利用率和可靠性,还能降低维护的成本。
技术实现要素:本发明的目的在于,针对液压作动器可能出现的故障,提出一种基于多模型的液压作动器故障诊断方法。本发明首先建立液压作动器的状态空间模型,然后根据故障类型建立能够反映液压作动器正常和故障情况的多个模型,将实际输入代入各个模型,依次将实际输出与各个模型的输出利用积分型性能指标进行比较,残差较小的模型所代表的情况即可反应液压作动器的状态。本发明提供了一种基于多模型的液压作动器故障诊断方法,具体步骤如下:步骤一:建立液压作动器的状态空间模型;由液压作动器各典型方程,通过合理选状态变量建立状态空间方程;步骤二:液压作动器的多模型确定;故障引起液压作动器状态空间方程中某些参数改变,由此建立液压作动器正常情况和各个故障模式下的参数矩阵;步骤三:实际输入代入各个模型,得到残差。将实际输入代入各个模型,得到相应的模型输出,并将实际输出与各个模型输出作差,得到残差;步骤四:利用积分型性能指标判定液压作动器状态。在得到残差后,代入积分型性能指标公式中,结果最小的一项所对应的情况即为液压作动器当前的状态。本发明的优点在于:1.状态空间模型能够描述液压作动器内部信息的传递,由于液压作动器的状态空间模型中的参数都具有实际意义,因而参数矩阵的变化能够代表液压作动器的状态变化情况,不同的参数能够代表液压作动器处于不同的工况。2.将实际输出与各个典型工况下的状态空间模型输出依次带入积分型性能指标公式,通过残差比较能够很容易的判断出两个模型间的差异大小。结果越小则说明相应的模型所代表的工况越接近液压作动器当前状态,从而实现液压作动器的故障诊断。附图说明图1是现有技术中的液压作动器的结构示意图;图2是利用多模型进行故障诊断的过程示意图。具体实施方式下面将结合附图对本发明的技术方案进行详细说明。本发明针对的对象是由电液伺服阀和液压缸构成的液压作动器,如图1所示,所述的液压缸为双出杆液压缸,双出杆液压缸与电液伺服阀连接,在运行时,电液伺服阀(简称伺服阀)接收控制信号,将其转换为阀芯的位移,使得双出杆液压缸中活塞两侧的油液产生压力差,作动杆在压力差的作用下进行运动,从而带动舵面偏转。本发明提供的基于多模型的液压作动器故障诊断方法,具体步骤如下:第一步,建立液压作动器的状态空间模型:对于所述的液压作动器,首先作出如下假设:①液压作动器的供油压力保持恒定,②伺服阀与液压缸的连接管道对称且足够粗,管道中的压力损失和管道动态特性忽略不计,③油液油温保持不变,油温为常数,④伺服阀的阀芯具有的理想的零开口和节流口是对称匹配的,⑤伺服阀力矩马达的非线性忽略。假设输入给伺服阀的输入电压为u,伺服阀通常用一个一阶环节来简化描述伺服阀的动态特性,伺服阀的动态特性方程写成微分方程形式为:式中:u--伺服阀输入电压,单位V;τ--伺服阀的时间常数;kp--伺服阀增益;xv--阀芯位移,单位m,--阀芯位移对时间的导数,单位m。假定四通滑阀节流口流出的液流为紊流状态,令伺服阀阀芯位于中间位置时,即伺服阀中挡板组件没有发生偏转,阀芯位移xv=0。当xv≥0时,液压缸活塞向右推动,则依据阀口流量—压力公式可得到流入液压缸左腔流量q1及流出液压缸右腔流量q2分别为:式中:q1--液压缸左腔流量(m3/s);q2--液压缸右腔流量(m3/s);Cd--节流口的流量系数;W--节流口的面积梯度(m);ρ--油液密度(kg/m3);ps--液压作动器供油压力(Pa);po--液压作动器回油压力(Pa);p1--液压缸左腔压力(Pa);p2--液压缸右腔压力(Pa)。同理,当xv<0时,液压缸活塞向左推动,则依据阀口流量—压力公式可得到流出液压左腔流量q′1及流入液压缸右腔流量q′2分别为:假定液压缸的内外泄漏均为层流流动,液压缸每个液压腔内各处压力相等。则依据可压缩流体的连续性方程有:式中:V--所取液压腔的体积(m3);p--所取控制腔内的液体压力(Pa);t为时间;ΣqI--流入液压腔的总流量(m3/s),;∑qo--流出液压腔的总流量(m3/s);β--流体体积弹性模量((N/m2)Pa)。将可压缩流体的连续性方程式(6)应用在液压缸左右两液压腔中可理解为:流量流进液压左腔的净流量会等于流体被压缩的流量与活塞运动所需的流量之和,即流入液压缸左腔的流量q″1满足如下关系等式:从液压缸右腔流出的流量q″2满足如下关系等式:式中:Ap--液压缸活塞有效面积(m2);xp--液压缸活塞杆位移(m);Cip--液压缸内泄漏系数(m3/s·Pa-1);βe--有效体积弹性模量(包括油液、混入油中的空气、连接油管和缸体的机械柔度)(Pa);V1--液压缸左腔容积(包括阀口至液压缸左腔油管和左腔的容积)(m3);V2--液压缸右腔容积(包括阀口至液压缸右腔油管和右腔的容积)(m3);其中液压缸左右两腔容积为:V1=VL1+V01+Apxp(9)V2=VL2+V02-Apxp(10)式中:VL1--阀口至液压缸左腔的油管容积(m3);VL2--阀口至液压缸右腔的油管容积(m3);V01--液压缸左腔的初始容积(m3);V02--液压缸右腔的初始容积(m3);xp--液压缸活塞的位移(m)。液压缸及负载主要受到的负载力包括惯性力、粘性摩擦力,则液压缸输出力与负载力的平衡方程为:式中:mt--活塞及负载折算到活塞上的总质量(kg);Bp--活塞及负载的粘性阻尼系数(N/(m/s))。选取阀芯位移xv与液压缸活塞杆速度vp、液压缸左右两腔压力p1与p2为闭环系统的状态变量,即:x=[x1x2x3x4]T=[xvvpp1p2]T(12)综合并整理上述伺服阀动态特性方程、伺服阀的负载流量方程、液压缸流量连续性方程、系统力平衡方程等基本方程,可建立电液位置伺服系统的状态空间模型为:液压作动器的输出响应为液压缸活塞杆速度,则输出方程为:y=Cx=[0100][x1x2x3x4]T(14)液压作动器的输入为伺服阀输入电压u,则液压作动器的状态方程为:或矩阵A如下(xp≥0):f(x,u)定义如下:则液压作动器的状态方程变换为:第二步,液压作动器的多模型确定。液压作动器中各个元部件的参数取值如表1所示。表1系统各参数取值矩阵A能够作为反映液压作动器系统状态的模型。基于测量过程解算得到的参数建立几组模型,即从获得的状态变量x、输入向量u和输出向量y,根据状态空间方程解得矩阵A,其中一组模型描述零故障情况,其他模型描述某一种故障的发生过程,这些模型作为理论模型与实际模型进行比较。理论模型和实际模型的矩阵之间的差异能够反映实际液压作动器的状况,若残差越小,则越接近这个矩阵所代表的液压作动器状态,从而确定液压作动器处于哪一种状态。将已有的液压作动器参数带入系统矩阵A,同时为了能够简便、统一地表示液压作动器状态,将kp放入矩阵A的第一行第二列,得到液压作动器在正常运行时的矩阵A为:在对液压作动器进行故障机理分析后可知,液压作动器的故障可以通过建立准确的数学模型基础上改变物理参数或结构参数来模拟液压作动器故障。如可以通过修改伺服阀增益和时间常数、液压缸的内泄漏系数和外泄漏系数、油液体积弹性模量、液压缸负载的粘性摩擦系数等来模拟系统故障。结合实际情况,表2为本实施例选择要研究的液压作动器的部分典型故障,及其物理参数改变设置。表2仿真实现部分典型故障类型根据仿真和实际运行经验,矩阵中有些参数在液压作动器正常和故障时的变化很小,这些参数包括活塞、活塞杆、油液及负载总质量mt、活塞有效作用面积Ap、阀口面积梯度W和孔口流量系数Cd,这些参数对状态变量的变化影响很小,将它们作为常数。当液压作动器正常运行时,将常数量带入公式(16)矩阵A,得到液压作动器系统矩阵A1:当液压缸存在内泄露时,设置活塞与缸筒间隙为1mm,通过仿真得知内泄露会使计算得到的Bp变小,Bp=12000,此时液压作动器系统矩阵A2为:当液压缸运行阻力大时,设置负载及活塞的粘性摩擦系数为20000(N/(m/s)),此时液压作动器系统矩阵A3为:当系统油液混入空气时,油液混入空气会使油液体积弹性模量变小,设置βe=5×108Pa,此时液压作动器系统矩阵A4为:当伺服阀泄露时,伺服阀增益kp会减小,此时液压作动器系统矩阵A5为:当伺服阀堵塞时,伺服阀的时间常数τ会增大,此时液压作动器系统矩阵A6为,第三步,将实际输入代入各个模型,即液压作动器系统矩阵A1~A6,得到多个输出。第二步中得到的多个模型能够代表系统的6个典型工作状态(式20~式25),在得到液压作动器的实际输入后,将实际输入依次代入到各个模型,得到6个模型对应的输出这个过程如图2所示。第四步,利用积分型性能指标判断故障。利用如下所示的积分型性能指标,能够合理避免突变的误差,提高判断的准确性:其中,ei(t)为模型误差,即实际输出与各个理论的模型输出的差值,c1>0和c2>0分别为暂态和记忆加权因子,合理选择c1和c2可使瞬时误差和累积误差保持合适比例,λ>0为遗忘因子,表示对性能指标的记忆效果并确保J(t)有界。遗忘因子的合理选择可以部分消除初始状态偏差,外部干扰等因素的影响。根据试凑法选择合理的c1、c2、t0、λ和τ后,将步骤三中得到的和y(t)代入上面两个式子(式26和式27),在每一时刻,指标中结果最小的一项中所代表的状态即为液压作动器系统当前的状态。