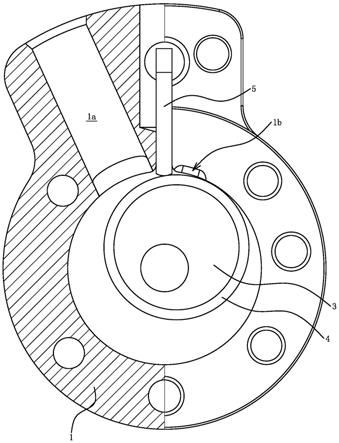
1.本发明属于压缩机技术领域,涉及一种旋转式压缩机,特别是一种旋转式压缩机冷媒排出结构。
背景技术:2.旋转式压缩机是电机直接带动旋转活塞作旋转运动来完成对制冷剂蒸气的压缩。由于活塞作旋转运动,压缩工作圆滑平稳,平衡,另外旋转式空压机没有余隙容积,无再膨胀气体的干扰,因此具有压缩效率高、零部件少、体积小、重量轻、平衡性能好、噪音低、防护措施完备和耗电量小等优点。
3.旋转式压缩机运行时,电机带动曲轴旋转,套在曲轴偏心部上的活塞沿气缸内孔壁作滚动和平面移动。叶片在弹簧的弹力作用下,叶片的r面与活塞外圆接触并将气缸内腔分作压缩腔和吸入腔。随着活塞旋转和移动吸入腔体积逐步扩大,吸入低压冷媒;同时压缩腔内体积减小,压缩腔内冷媒压力逐步增加,当活塞转动至330
°
时,压缩腔内冷媒压力达到最大值,排气阀打开,高压冷媒排出,从而完成一次工作循环。
4.旋转式压缩机的缸盖内开设有排出主通道以及气缸上开设有排出倒角通道;目前排出主通道和排出倒角通道均呈圆柱状,将排出主通道和排出倒角通道内冷媒压缩所需压力通常认为消耗的能力做了无用功。以内孔
ø
39mm的气缸和排出主通道
ø
5.5mm的旋转式压缩机为例,当活塞转至330
°
时,压缩腔为狭长的弧形三角形,压缩腔体积约为108.2mm
³
;排出主通道和排出倒角通道的总体积约为47.5mm
³
。排出主通道和排出倒角通道的总体积约为压缩腔体积的一半,由此可知压缩排出主通道和排出倒角通道内冷媒消耗能量占比较大。为了解决上述技术问题,有人提出了密封型旋转式压缩机(公开号cn1566700a),通过减少死体积,提高压缩机性能。
5.随着社会发展,对空调的节能、降耗的要求也越来越高;为此新型冷媒不断推广应用以及压缩机的输出工作压力也不断提高。目前部分压缩机的输出工作压力已提高至26-28kg/cm
²
,甚至超过40kg/cm
²
。
6.密封型旋转式压缩机(公开号cn1566700a)所记载的技术方案是否适用于工作压力超过26kg/cm
²
旋转式压缩机还需验证。虽然簧片式排气阀已广泛应用,但采用簧片式排气阀时并不能降低死体积,进而不能降低压缩机的能效比,提高压缩机性能。
技术实现要素:7.本发明提出了一种旋转式压缩机冷媒排出结构,本发明要解决的技术问题是如何提高压缩机的能效比。
8.本发明的要解决的技术问题可通过下列技术方案来实现:一种旋转式压缩机包括气缸和缸盖,旋转式压缩机冷媒排出结构包括位于缸盖上的排出主通道和位于气缸上的排出倒角通道,排出倒角通道与排出主通道相连通;缸盖上安装有能使排出主通道处于截止状态的簧片式排气阀;其特征在于,排出主通道呈腰形,排出主通道包括位于中部的条形柱
状区域和位于条状区域两侧的半圆柱区域。
9.与现有技术相比,本旋转式压缩机通过调整排出主通道的形状,不仅降低死体积,还保证排出主通道和排出倒角通道加工方便性。
10.在上述旋转式压缩机冷媒排出结构中,所述气缸内还具有呈圆柱状的腔室和与腔室相连通的进气通道,腔室内设有曲轴和活塞,活塞套设在曲轴的偏心部上;气缸上滑动连接叶片,进气通道和排出倒角通道分别位于叶片的两侧。
11.作为优先,所述条形柱状区域还呈弧形。
12.作为优先,所述条形柱状区域的弧线圆心与气缸腔室的轴心线重合。
13.作为优先,所述排出主通道的半圆柱区域侧面与叶片的侧面之间最小间隙小于0.2mm。
14.作为优先,所述排出倒角通道与排出主通道的横截面形状相同。
15.作为优先,所述排出倒角通道的纵向线相对于气缸腔室的轴心线倾斜设置,排出倒角通道的纵向线与气缸腔室的轴心线之间夹角α为30
°‑
38
°
。
16.作为优先,所述排出主通道的半圆柱区域半径r1为排出主通道的中心弧线弧长l1的27%-37%。
17.作为优先,所述排出主通道的中心弧线弧长l1小于或等于现有旋转式压缩机中圆柱形排出主通道的直径。
附图说明
18.图1是旋转式压缩机的剖视结构示意图。
19.图2是旋转式压缩机中气缸的剖视结构示意图。
20.图3是排出主通道横截面结构示意图。
21.图中,1、气缸;1a、进气通道;1b、排出倒角通道;2、缸盖;2a、排出主通道;2a1、条形柱状区域;2a2、半圆柱区域;3、曲轴;4、活塞;5、叶片;6、簧片式排气阀。
具体实施方式
22.以下是本发明的具体实施例并结合附图,对本发明的技术方案作进一步的描述,但本发明并不限于这些实施例。
23.如图1和图2所示,旋转式压缩机包括气缸1、缸盖2、曲轴3、活塞4和叶片5。
24.气缸1内具有呈圆柱状的腔室和与腔室相连通的进气通道1a。曲轴3穿设在气缸1腔室内,曲轴3的偏心部上套设有活塞4,活塞4的外侧面与气缸1的内侧面之间通常仅留小于0.1mm的间隙,不仅避免活塞4的外圆面与气缸1的内侧面摩擦,又能保证密封性。叶片5嵌设在气缸1的叶片5滑槽内,叶片5与气缸1之间滑动连接,叶片5在弹簧的弹力作用下始终抵靠在活塞4的外侧面上。
25.旋转式压缩机冷媒排出结构包括位于缸盖2上的排出主通道2a、位于气缸1上的排出倒角通道1b和安装在缸盖2上的簧片式排气阀6,簧片式排气阀6能使排出主通道2a处于截止状态。簧片式排气阀6可参考密封型旋转式压缩机(公开号cn1566700a)背景技术中记载的技术方案。进气通道1a和排出倒角通道1b分别位于叶片滑槽的两侧。排出主通道2a的内端内侧区域直接与气缸1的腔室相连通,排出主通道2a的内端外侧区域通过排出倒角通
道1b与气缸1的腔室相连通。
26.如图2和图3所示,排出主通道2a呈腰形,即排出主通道2a包括位于中部的条形柱状区域2a1和位于条状区域两侧的半圆柱区域2a2。条形柱状区域2a1还呈弧形,弧形的圆心与气缸1腔室的轴心线重合,这样沿着气缸1腔室的周向使条形柱状区域2a1直接与气缸1腔室相连通的宽度保持一致,进而有利于保证冷媒排出流量稳定。机加工缸盖2时铣刀沿着设定弧形轨迹线移动便能加工出上述的排出主通道2a,由此具有加工方便,加工效率高和加工成本低的优点。排出主通道2a的半圆柱区域2a2侧面与叶片的侧面之间最小间隙小于0.2mm。
27.排出倒角通道1b与排出主通道2a的横截面形状相同,这样便于排出倒角通道1b与排出主通道2a加工以及降低加工所需成本。排出倒角通道1b的纵向线相对于气缸1腔室的轴心线倾斜设置,排出倒角通道1b的纵向线与气缸1腔室的轴心线之间夹角α为30
°‑
38
°
,这样能有效平衡冷媒排出流量和排出倒角通道1b体积之间关系,即不仅能保证冷媒排出所需流量,又具有排出倒角通道1b体积小的优点。
28.为了与现有的以内孔
ø
39mm的气缸1和排出主通道2a
ø
5.5mm的旋转式压缩机比较,设定排出主通道2a的深度均为2mm,排出主通道2a的中心弧线弧长l1为5.5mm。
序号半圆柱区域2a2半径r1排出主通道2a和排出倒角通道1b总体积与现有设计体积差值预计节能%12.0537.99.66.0221.7533.214.38.9231.529.118.411.49
29.概况来说,本旋转式压缩机中排出主通道2a的中心弧线弧长与现有旋转式压缩机中排出主通道2a的直径相同时,这样便能保证沿着气缸1腔室的周向排出主通道2a侧面极限位置保持一致,进而保证冷媒排出顺畅性,同时通过调整排出主通道2a和排出倒角通道1b的横截面形状,实现降低排出主通道2a和排出倒角通道1b总体积,即降低死体积。