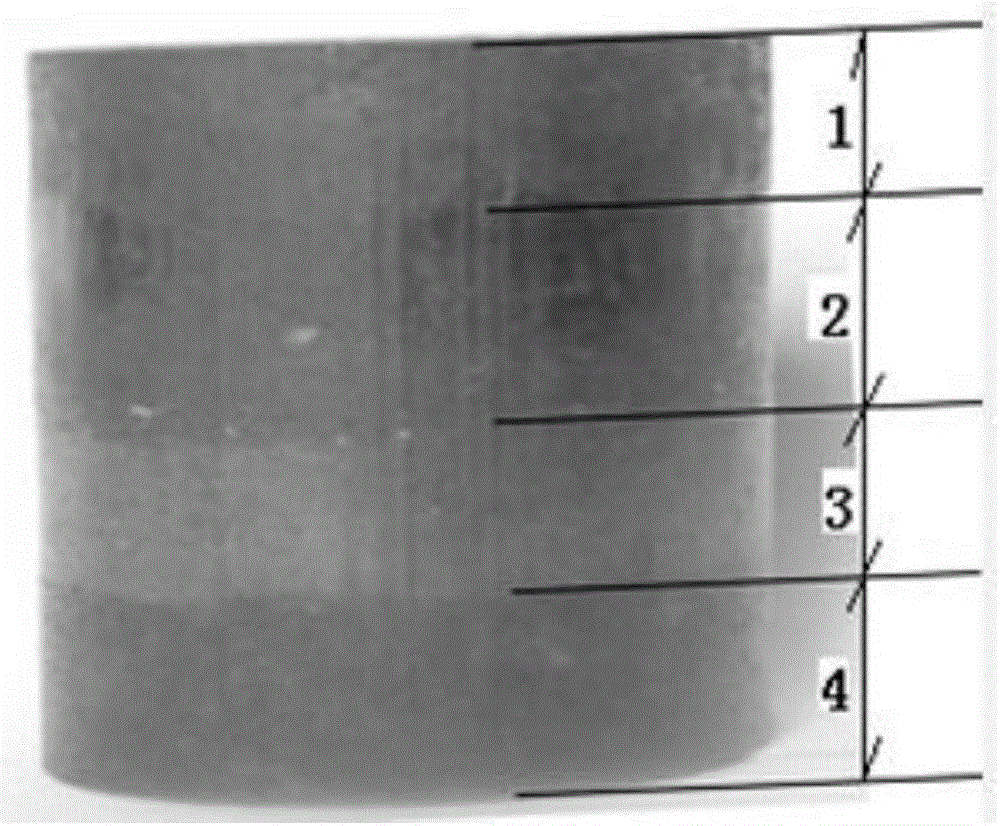
本发明属于摩擦材料领域,具体涉及一种无石棉可控梯度弹性制动片及其制备方法。
背景技术:
:制动过程的缓冲主要是为了消除运动机械突然停顿导致的惯性力,以保证制动过程平稳性和设备安全性,这对于大型起吊设备和高温炼铁炉翻转设备等高危设备的制动过程尤为重要。目前大型起吊设备的制动片大都采用带橡胶垫的石棉纤维层制动片,即在石棉摩擦纤维层下方粘接(或安装)橡胶垫以缓冲其制动过程,其工程性是在利用石棉纤维的摩擦制动性能的同时,使具有弹性性能的橡胶垫缓冲其制动瞬间的冲击力。由于石棉的优良摩擦制动性能与隔热性以及橡胶垫的良好弹性性能,使带橡胶垫的石棉纤维层制动片能长期使用在起吊设备的电机制动系统中。然而,由于石棉为高温挥发物属强致癌物质,石棉纤维在摩擦制动过程产生的挥发物对环境污染较大,因此无石棉制动片成为近年来摩擦材料的发展趋势。迄今为止,传统缓冲制动片的结构由摩擦制动层与橡胶垫两部分粘结而成,涉及的结构工艺复杂;此外大多数无石棉摩擦制动层的低隔热性使摩擦制动热将迅速传递到橡胶垫,橡胶垫的非导热特性和低热软化性严重制约了其制动效率和使用寿命。技术实现要素:本发明的目的是针对上述该领域技术存在的不足,提供一种无石棉可控梯度弹性制动片,它为依次设置的摩擦制动层和梯度弹性模量层形成的梯度弹性模量的连续耦合结构,可基于制动缓冲要求,量化设计其弹性复层的弹性模量,满足大惯量缓冲制动系统的变化量缓冲涉及要求,同时在弹性复层之间可设置强韧层,以提高大惯量缓冲制动稳定性;且涉及的原料不含石棉,环境友好,适用范围广。为实现上述目的,本发明采用的技术方案为:一种无石棉可控梯度弹性制动片,它包括依次设置的摩擦制动层和梯度弹性模量层,其中梯度弹性模量层由若干个弹性复层组成,且自与摩擦制动层接触的弹性复层起,弹性复层的弹性模量逐层降低。优选的,所述摩擦制动层和梯度弹性模量层之间设置强韧层。更优选的,所述梯度弹性模量层中的弹性复层之间设置强韧层。上述方案中,所述摩擦制动层中各组分及其所占重量份数为:改性酚醛树脂粉15-25份,增强纤维5-10份,金属粉10-15份,摩擦粉15-20份,矿物填料30-55份。上述方案中,所述梯度弹性模量层中的弹性复层选自如下配比方案,配比方案1:改性酚醛树脂粉10-15重量份,金属粉10-15重量份,橡胶粉5-15份,矿物填料55-75;配比方案2:改性酚醛树脂粉10-15重量份,金属粉10-15重量份,橡胶粉15-20份,矿物填料50-65;配比方案3:改性酚醛树脂粉10-15重量份,金属粉10-15重量份,橡胶粉20-25份,矿物填料45-60重量份;配比方案4:改性酚醛树脂粉10-15重量份,金属粉10-15重量份,橡胶粉25-30份,矿物填料40-55;配比方案5:改性酚醛树脂粉10-15重量份,金属粉10-15重量份,橡胶粉35-40份,矿物填料30-45。不同弹性复层的配比及其对应的弹性模量见表1。表1编号改性酚醛树脂粉金属粉橡胶粉矿物填料弹性模量(MPa)110-1510-155-1555-751100-850210-1510-1515-2050-65850-650310-1510-1520-2545-60650-450410-1510-1525-3040-55450-300510-1510-1535-4030-45300-200上述方案中,所述强韧层中各组分所占重量份数为:改性酚醛树脂粉10-15份,金属纤维20-30份,增强纤维25-35份,矿物填料20-45份。上述方案中,所述改性酚醛树脂为丁腈橡胶改性酚醛树脂。上述方案中,所述增强纤维为陶瓷纤维或矿物纤维。上述方案中,所述矿物填料为250-325目的钾长石或重晶石。上述方案中,所述金属粉为铜粉或铁粉。上述方案中,所述摩擦粉为市售摩擦粉产品,或为石墨与炭黑粉按任意比例的混合物。上述方案中,所述金属纤维为铜纤维或不锈钢纤维。上述一种无石棉可控梯度弹性制动片的制备方法,它包括如下步骤:1)配料:按上述配比要求分别称取摩擦制动层和梯度弹性模量层中的弹性浮层中的各组分,并分别搅拌均匀得各功能层的混合原料;2)装模:将各功能层的混合原料按照摩擦制动层、梯度弹性模量层的顺序分层填充至热压模中;3)控温:分别控制热压模中摩擦制动层混合原料的温度为120-160℃,梯度弹性模量层混合原料的模具温度为100-140℃;4)压制成型:在压力为10-25MPa,保压时间为60-80s/mm的条件下进行压制成型;5)分级热处理:将压制成型所得产物加热至130-150℃保温2-3h,继续升温至155-165℃保温2-3h,最后加热至170-180℃保温为1-2h后随炉自然冷却,即得所述无石棉可控梯度弹性制动片。上述方案中,所述热压模包括上模具和下模具,上模具对应摩擦制动层混合原料一端,下模具对应梯度弹性模量层混合原料一端,步骤3)中通过对上、下模具分别施不同温度,其中上模具温度高于下模具温度,控制热压模中摩擦制动层混合原料的温度为120-160℃,梯度弹性模量层混合原料的模具温度为100-140℃。优选的,所述擦制动层和梯度弹性模量层之间设置一层强韧层。更优选的,在所述梯度弹性模量层中的弹性复层之间设置强韧层。本发明的原理为:1)结构原理:采用小差异化粘结剂(改性酚醛树脂粉)组分和大差异化弹性体(橡胶粉)组分的结构与工艺设计,使各层在形成连续体耦合的同时实现其功能差异化;2)功能原理:在摩擦制动层实现其制动的同时,弹性复层吸收其制动过程中的惯性动能,而复层的弹性梯度可控其惯性动能吸收速率,从而实现制动过程的缓冲可控性。本发明的有益效果为:1)本发明采用无石棉摩擦制动层实现其制动功能,环境友好;2)本发明采用梯度弹性模量层中的弹性复层的弹性模量可变性,可有效解决缓冲制动器的量化设计和控制的技术问题,特别是高危设备制动器的缓冲控制技术难题;3)本发明可在梯度弹性模量层中耦合强韧层,解决厚弹性复层的变形失稳问题而设置,适用于具有大制动惯性动能情况。附图说明图1为本发明实施例1所得无石棉可控梯度弹性制动片,图中1为摩擦制动层,2为第一弹性复层,3为第二弹性复层,4为第三弹性复层。图2为本发明实施例2所得无石棉可控梯度弹性制动片,图中1为摩擦制动层,2为第一弹性复层,3为强韧层,4为第二弹性复层。图3为本发明实施例3所得无石棉可控梯度弹性制动片,图中1为摩擦制动层,2为梯度弹性模量层。图4为本发明实施例4所得无石棉可控梯度弹性制动片,图中1为摩擦制动层,2为强韧层,3为梯度弹性模量层。具体实施方式为了更好地理解本发明,下面结合实例进一步阐明本发明的内容,但本发明的内容不仅仅局限于下面的实施例。以下实施例中,所述无石棉可控梯度弹性制动片为摩擦制动层、梯度弹性模量层组成的连续体,其中梯度弹性模量层由若干个弹性复层组成,且弹性复层之间可设置强韧层;将上述各功能层按配比进行混料、在模具中进行分层填料,再进行热压压制成型和热处理后,即得所述无石棉梯度弹性制动片。所述梯度弹性制动片中各组分摩擦制动层中各组分所占重量份数为:所述摩擦制动层中各组分及其所占重量份数为:改性酚醛树脂粉15-25份,增强纤维5-10份,金属粉10-15份,摩擦粉15-20份,矿物填料30-55份。所述强韧层中各组分所占重量份数为:改性酚醛树脂粉10-15份,金属纤维20-30份,增强纤维25-35份,矿物填料20-45份。所述梯度弹性模量层中的弹性复层选自若干个表1中的所述配方条件。表1梯度弹性模量层中不同弹性复层的配比及其对应的弹性模量编号改性酚醛树脂粉金属粉橡胶粉矿物填料弹性模量(MPa)110-1510-155-1555-751100-850210-1510-1515-2050-65850-650310-1510-1520-2545-60650-450410-1510-1525-3040-55450-300510-1510-1535-4030-45300-200以下实施例中,所述改性酚醛树脂粉为丁腈橡胶改性酚醛树脂,增强纤维为市售化学纤维,金属纤维为铜纤维;金属粉为铁粉;摩擦粉由石墨与炭黑粉按1:1的质量比混合而成;矿物填料为重晶石,粒度为200-325目。对比例一种无石棉单层制动片,其组分配比及制品性能如表2所示:表2以下实施中所采用的单层制动片组分配比(重量份数)及其制动片性能所述无石棉单层制动片的制备方法包括如下步骤:1)按表2所述配比进行配料,得混合原料;2)将所得混合原料填充至热压模中;3)控制热压模中温度为150℃;4)在压力为20MPa和保压时间为70s/mm的条件下进行压制成型;5)将压制成型所得产物加热至150℃保温2h,继续升温至160℃保温2h,最后加热至180℃保温为2h后随炉自然冷却,即得所述无石棉单层制动片。实施例1一种无石棉可控梯度弹性制动片,其结构图见图1,它自上而下包括依次设置的摩擦制动层1和梯度弹性模量层,其中梯度弹性模量层由依次设置的第一弹性复层2、第二弹性复层3和第三弹性复层4组成;所述弹性制动片中各功能层的组分配比及其所得制动片性能见表3。表3实施例1中所述弹性制动片各功能层配比(重量份数)及所得制动片性能所述无石棉可控梯度弹性制动片的制备方法包括如下步骤:1)按表3所述各功能层(摩擦制动层和梯度弹性模量)的组分配比分别备料,并分别搅拌均匀得各功能层的混合原料;2)将各功能层的混合原料按图1所述顺序分层填充至热压模中;3)分别控制热压模中摩擦制动层模具的温度为120-150℃,梯度弹性模量层模具的温度为100-120℃;4)在压力为20MPa和保压时间为70s/mm的条件下进行压制成型;5)将压制成型所得产物加热至150℃保温2h,继续升温至160℃保温2h,最后加热至180℃保温为2h后随炉自然冷却。实施例2一种无石棉可控梯度弹性制动片,其结构图见图2,它自上而下包括依次设置的摩擦制动层1和梯度弹性模量层,其中梯度弹性模量层包含依次设置的第一弹性复层2和第二弹性复层4,两个弹性复层之间耦合了强韧层3;所述弹性制动片中各功能层的组分配比及所得制品性能见表4。表4实施例2中所述弹性制动片各功能层配比(重量份数)及所得制动片性能所述无石棉可控梯度弹性制动片的制备方法包括如下步骤:1)按表4所述各功能层(摩擦制动层、梯度弹性模量、强韧层)的组分配比分别备料,并分别搅拌均匀得各功能层的混合原料;2)将各功能层的混合原料按图2所述顺序分层填充至热压模中;3)分别控制热压模中摩擦制动层和强韧层模具的温度为120-160℃,梯度弹性模量层模具的温度为100-140℃;4)在压力为20MPa和保压时间为70s/mm的条件下进行压制成型;5)将压制成型所得制品加热至150℃保温2h,继续升温至160℃保温2h,最后加热至180℃保温为2h后随炉自然冷却,即得所述无石棉可控梯度弹性制动片。将实施例1和实施例2所得无石棉可控梯度弹性制动片的性能测试结果进行对比(分别见表3和表4),可以看出:(1)本发明实施例1和2所得制动片的综合弹性模量明显低于单层制动片的弹性模量(见表2),使其表现出良好的缓冲性能。(2)本发明实施例2所述制动片中耦合强韧层后,其综合弹性模量变化不大,但刚度系数明显提高,从而提高了抗变形能力,改善了其制动稳定性。实施例3一种无石棉可控梯度弹性制动片,结构图见图3,它包括依次设置的摩擦制动层1和梯度弹性模量层2;所述弹性制动片中各功能层的组分配比及所得制动片性能测试结果见表5。表5实施例3中所述弹性制动片各功能层配比(重量份数)及所得制动片性能所述无石棉可控梯度弹性制动片的制备方法包括如下步骤:1)按表5所述各功能层(摩擦制动层、梯度弹性模量)的组分配比分别备料,并分别搅拌均匀得各功能层的混合原料;2)将各功能层的混合原料按图3所述顺序分层填充至热压模中;3)分别控制热压模中摩擦制动层和强韧层模具的温度为120-160℃,梯度弹性模量层模具的温度为100-140℃;4)在压力为20MPa和保压时间为70s/mm的条件下进行压制成型;5)将压制成型所的制品加热至150℃保温2h,继续升温至160℃保温2h,最后加热至180℃保温为2h后随炉自然冷却。将本实施例所得制动片(表5)与对比例所得单层制动片(表2)进行对比,可以看出:本实施例所得制动片得综合弹性模量明显地低于单层制动片,但摩擦系数相同;从而实现其缓冲制动功能。实施例4一种无石棉可控梯度弹性制动片,其结构图见图4,它包括依次设置的摩擦制动层1、强韧层2和梯度弹性模量层3;所述弹性制动片中各功能层的组分配比及所得制动片的性能测试结果见表6。表6实施例4中所述弹性制动片各功能层配比(重量份数)及所得制动片性能所述无石棉可控梯度弹性制动片的制备方法包括如下步骤:1)按表6所述各功能层(摩擦制动层、强韧层、梯度弹性模量层)的组分配比分别备料,并分别搅拌均匀得各功能层的混合原料;2)将各功能层的混合原料按图4所述顺序分层填充至热压模中;3)分别控制热压模中摩擦制动层和强韧层模具的温度为120-150℃,梯度弹性模量层模具的温度为100-120℃;4)在压力为20MPa和保压时间为70s/mm的条件下进行压制成型;5)将压制成型所的制品加热至150℃保温2h,继续升温至160℃保温2h,最后加热至180℃保温为2h后随炉自然冷却。将实施例3和4所得无石棉可控梯度弹性制动片的性能测试结果进行对比(分别见表5和表6),可以看出:本实施例通过在摩擦制动层与弹性层之间耦合强韧层,在降低所得制动片弹性模量的同时,可大幅度地提高其刚度系数。综上,本发明可为制动片的缓冲性能设计和稳定性控制提供多种实施方式,从而拓宽其工程应用范畴,具有重要的工业应用前景。以上所述仅是本发明的优选实施方式,而并非对实施方式的限制。对于所属领域的普通技术人员而言,在上述说明的基础上还可以做出其他不同形式的变化或者变动,这里无需也无法对所有的实施方式予以穷举,因此所引申的显而易见的变化或变动仍处于本发明创造的保护范围之内。当前第1页1 2 3