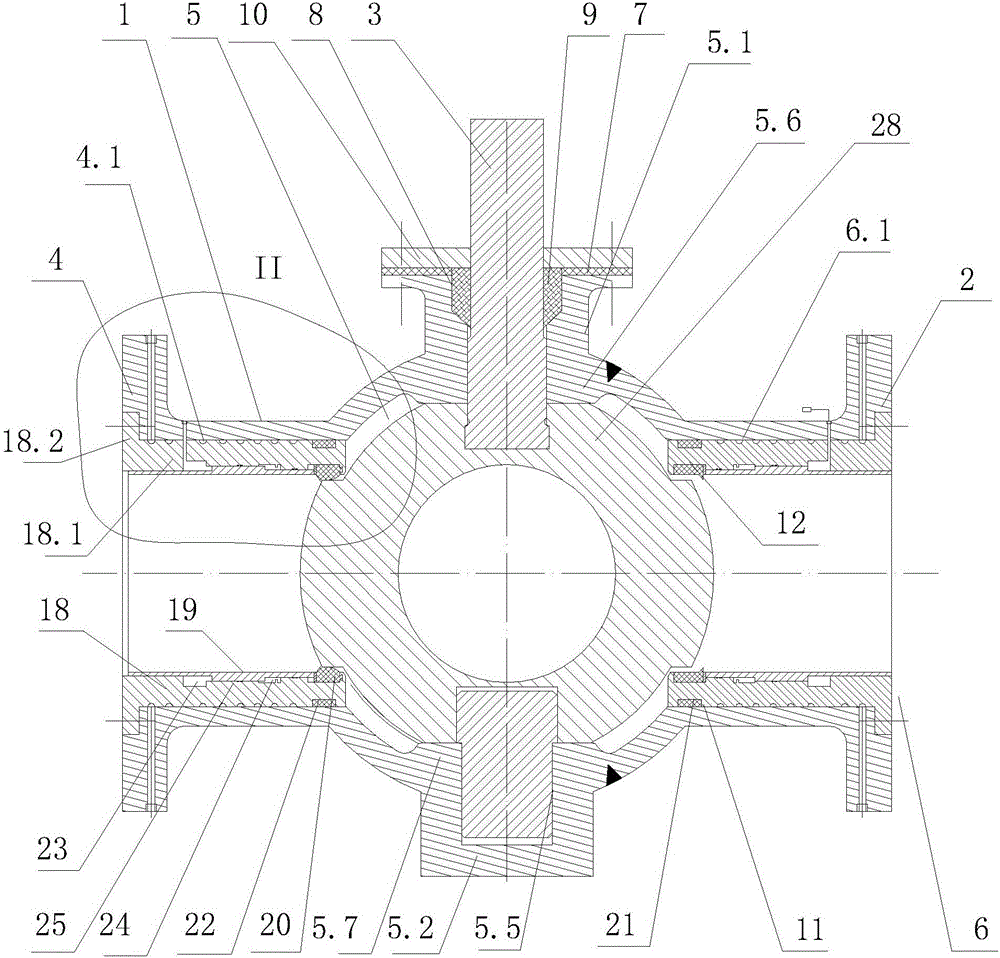
本发明涉及阀门的
技术领域:
,具体涉及一种超高温阀。
背景技术:
:超高温阀作为流体控制过程中必不可少的部分,阀门在整个流体控制中起关键作用,因而广泛应用于石油、化工、冶金、军工等领域,其流经介质为高温气体或液体,温度一般在450℃-900℃,压力大于2.5Mpa。如何设计出既满足使用要求又能保障安全的高温阀门是技术关注的焦点。目前,常用的高温阀门有水冷却阀门和无水冷却阀门。首先,阀芯与阀体的热膨胀差别是至关重要的;现有技术一般都采用适当增加阀芯与阀体之间的工作间隙的方式来解决热膨胀差别问题,以保证阀芯与阀体之间卡死或擦伤;但间隙的增加也为密封带来了更加沉重的负担。其次,密封圈的热交变问题和热疲劳也是至关重要的;介质的热交变,密封圈因一直与介质接触而受到热交变应力的影响而过度疲劳,从而丧失原有的作用。现有技术一般采用较好的密封圈材质如聚四氟乙烯或纤维增强的氟树脂材料来增加密封圈的使用寿命,但并未彻底解决热疲劳问题而导致阀门的使用维护成本增加。如何在成本合理的条件下,通过恰当的结构考虑,设计出能少考虑间隙和密封圈热疲劳问题的高温阀门成为行业发展的共性难题。技术实现要素:针对上述现有技术中存在的缺陷,本发明的目的在于提供一种超高温阀。本发明的目的是这样实现的,一种超高温阀,包括阀体、阀盖、阀杆和阀芯,阀体具有入口部、出口部和阀室,入口部具有第一通孔,第一通孔连通阀室;出口部具有第二通孔,第二通孔连通阀室;所述阀杆可旋转地设置在所述阀室中且下端固定连接阀芯以旋转阀芯控制流过阀室的流量;所述阀芯包括通水孔;所述阀芯与阀室内壁距离一间隙;入口部和/或出口部设有动压密封装置,所述动压密封装置包括动压套本体、动压套,所述动压套本体配合在第一通孔或第二通孔中;动压套可滑动地设置在动压套本体中,在动压套本体和动压套之间由外向阀芯方向依次形成彼此独立密封的流体容纳室和气体容纳室;所述动压套本体前端设有动压胶环,动压套前端抵接在动压胶环上;通过所述动压密封装置,阀芯旋转一定角度,使得所述阀体通道具有通水孔与第一通孔和第二通孔连通的通过状态和通水空不与第一通孔和第二通孔连通的密封状态。进一步地,该动压套本体包括轴向定位部、固定法兰部,所述轴向定位部配合在第一通孔中并通过所述固定法兰部压装固定在所述入口部的入口法兰上。进一步地,在阀体上设有流体填充口,流体填充口连通所述流体容纳室。进一步地,在动压套本体和动压套之间设有液/气封密封圈。进一步地,所述动压套本体前端设有胶环限位槽和第一限位凸环,所述胶环限位槽中卡设有推环和动压胶环,所述动压套的前端面抵接所述推环。进一步地,动压套本体后端设有第二限位凸环,动压套包括后端法兰,所述后端法兰和第二限位凸环之间设有复位弹簧。进一步地,第一限位凸环设有定位倒扣,所述动压胶环前端设有凸起,该凸起嵌入所述定位倒扣而对动压胶环在胶环限位槽中定位。进一步地,还包括阀芯密封装置,入口部和/或出口部设有阀芯密封套,所述阀芯密封套设有密封圈定位环槽;所述阀芯密封装置设置在密封圈定位环槽中,所述阀芯密封装置包括弹簧、滑座和阀芯密封圈;阀芯密封圈固定在滑座的顶部;滑座通过弹簧压装在密封圈定位环槽中。进一步地,当入口部或出口部不设动压密封装置时,所述阀芯密封套设在入口部或出口部的通孔中,并通过固定法兰固定在入口法兰或出口法兰上;当入口部或出口部设置动压密封装置时,所述阀芯密封套套设在动压套的通孔中,并通过压板固定在入口法兰或出口法兰上。进一步地,所述阀盖一体焊接在所述阀体上构成阀室,同时阀室的内壁与阀芯的表面形成间隙,使得第二通孔与第一通孔同轴且与阀室串联构成为阀体通道;或者阀体包括压装部,阀盖具有第二通孔,所述阀盖压装在压装部上,使得第二通孔与第一通孔同轴且与阀室串联构成为阀体通道。所述超高温阀,为了解决“柔性密封圈和阀芯在高温环境中间隙和热疲劳使得密封难以控制”的技术难题,通过以下技术手段:1)阀芯密封装置阀芯密封装置至少设置在阀室出口处,通过弹簧将阀芯密封圈压在阀芯球面与第二通孔的过渡处,由于该过渡处正好是带有锥形弧面的,所以也设计了横截面为锥形凸弧面的阀芯密封圈,对阀体通道形成有效密封。2)动压密封装置为了弥补高温环境对阀芯密封圈的受热膨胀变形,至少在阀室入口设置动压密封装置,在阀体通道的密封状态,该动压密封装置通过流体容纳室的流体传递压力和气体的大变形性能将动压套前移致动使得动压套顶端抵压推环,推环抵压动压胶环,动压胶环受压拱起压在球面上形成密封,该密封由于是流体的持续压力作用,不受低温环境的影响。在阀体通道的非密封状态,流体容纳室的流体排出,动压胶环恢复到与球面距离一间隙。这样,当转动阀杆由密封状态向通过状态转变时,或者当转动阀杆由通过状态向密封状态转变时,动压密封装置释放球面密封,以使得转动可行。3)二者的组合形成不同密封偏向的高温阀品种通过在阀室的入口和出口设置动压密封装置和阀芯密封装置的组合,可以得到不同密封及耐用偏向的高温阀品种,其中同时在入口和出口设置动压密封装置和阀芯密封装置是最耐用密封最好的品种。动压密封装置仅在阀体通道的密封状态至少在阀室上游起一级密封辅助作用,对阀室下游的阀芯密封装置的密封功能减轻压力,密封圈的密封性能也更能耐久地保持最佳状态,因此二者具有互相协同作用。申请人既从密封圈的密封结构考虑问题,又结合动压密封考虑问题,通过以上二个结构的相互协同配合,加上不同的侧重点,大大提高了超高温阀的密封能力。附图说明图1为本发明超高温阀的实施例一的通过状态的主剖视图。图2为本发明超高温阀的实施例一的密封状态的主剖视图。图3为本发明超高温阀的图1的I放大图。图4为本发明超高温阀的图1的II放大图。图5为本发明超高温阀的图1的不同密封圈形状的I放大图。图6为本发明超高温阀的图1的不同密封圈形状的II放大图。图7为本发明超高温阀的实施例二的通过状态的主剖视图。图8为本发明超高温阀的实施例二的密封状态的主剖视图。图9为本发明超高温阀的图8的VI放大图。图10为本发明超高温阀的图8的IV放大图。图11为本发明超高温阀的阀芯密封圈的主剖视图。上述图中的附图标记:1阀体,2阀盖,3阀杆,4入口部,5阀室,6出口部,7密封隔热垫,8锥形孔部,9密封锥环,10压盖,11密封圈定位环槽,12内台阶,13滑槽,14滑条,15顶压弹簧,16阀芯密封圈,17滑座,18动压套本体,19动压套,20动压胶环,21阀芯密封装置,22动压密封装置,23流体容纳室,24气体容纳室,25液/气封密封圈,26推环,27流体填充口,28阀芯,29冷却流道,30复位弹簧,31第三限位凸起4.1第一通孔,6.1第二通孔5.1上颈部,5.2下颈部,5.3压装部,5.4阀杆孔,5.5盲孔,5.6上支撑台,5.7下支撑台,5.8转轴28.1通水孔,28.2阀芯面,28.3密封部16.1阀芯密封面,16.2竖直滑动环面18.1轴向定位部,18.2固定法兰部,18.3胶环限位槽,18.4第二限位凸环,18.5第一限位凸环,18.6定位倒扣具体实施方式以下结合附图对本发明的实施例作详细说明,但不用来限制本发明的范围。实施例一如图所示,一种超高温阀,包括阀体1、阀杆3,阀体1具有入口部4、阀室5、出口部6,入口部4设有第一通孔4.1,第一通孔4.1连通阀室5,出口部6设有第二通孔6.1,第二通孔6.1连通阀室5;所述阀室5具有上颈部5.1和下颈部5.2。所述上颈部5.1设有阀杆孔5.4和阀芯上支撑台5.6,所述下颈部5.2具有与所述阀杆孔5.4同轴设置的盲孔5.5和阀芯下支撑台5.7。阀杆3设置在上颈部5.1中且下端固定连接阀芯28,转轴5.8上端固定连接阀芯28,使得阀芯28在阀室5中与阀室内表面距离一间隙δ地可旋转地定位。所述阀芯28旋转支撑在上支撑台5.6和下支撑台5.7之间。所述阀体为全焊接球形阀体结构,是通过所述阀盖2一体焊接连接所述阀体1使得阀体1的阀室5构成封闭的球形阀室,使得第二通孔6.1与第一通孔1.1处于同一轴线上,同时阀室5的球形内壁与阀芯28的表面形成间隙δ。上颈部5.1设有锥形孔部8,锥形孔部8内设有密封锥环9,上颈部5.1的法兰处压装有密封隔热垫7,所述密封锥环7的厚度比密封隔热垫6高1-3mm,压盖10压装在密封隔热垫7和密封锥环9上固定。阀芯28具有通水孔6.1和球面6.2。所述阀体1的入口部4和/或出口部设有动压密封装置22,所述动压密封装置22包括动压套本体18、动压套19、动压胶环20、流体容纳室23、气体容纳室24、流体填充口27,该动压套本体18包括轴向定位部18.1、固定法兰部18.2,所述轴向定位部18.1配合在入口部4的第一通孔中并通过所述固定法兰部18.2固定在所述入口部4的入口法兰上;动压套本体18的轴向定位部18.1和第一通孔1.1之间设有冷却流道;在动压套本体18和动压套19之间设有液/气封密封圈25,这样,在动压套本体18和动压套19之间由外向阀芯28方向依次形成彼此独立密封的流体容纳室23和气体容纳室24,在阀体5上设有流体填充口27,流体填充口27连通所述流体容纳室23。流体容纳室23能容纳一液体流体F,例如水或润滑油的液体;在气体容纳室24封装有气体;所述动压套本体18前端设有胶环限位槽18.3和第一限位凸环18.5,动压套本体18后端设有第二限位凸环18.4,所述胶环限位槽18.3中卡设有动压胶环20,所述动压套19的前端面抵接所述动压胶环20上;或者更为优选的是,所述胶环限位槽18.3中卡设推环26和动压胶环20,所述动压套19的前端面抵接所述推环26上;动压套19包括后端法兰19.1,所述后端法兰19.1和第二限位凸环18.4之间设有复位弹簧30;所述动压套本体18在第一通孔的圆周方向定位,当填充到流体容纳室23的流体F的压力P1大于气体容纳室24内的气体压力P2时,动压套19能沿动压套本体18的轴向移动,动压套19推动与之抵接的推环26轴向前移,动压胶环20由于第一限位凸环18.5的阻挡从而拱起变形;当变形时,所述动压胶环20抵压在阀芯28的密封部28.3,从而对该球面进行密封。由于持续的液体压力的作用,动压胶环20与阀芯28的密封性能非常高,而这种密封不受高温环境的影响。当阀杆再次旋转阀芯28时,由动压密封装置22密封的阀芯通过下面操作被释放开。流体F从流体容纳室23中排出,通过流体的排放,流体容纳室23的流体F的压力P1为0,气体容纳室24内的气体压力P2和复位弹簧30的作用下沿轴向向后移动,动压胶环20由自身的弹性恢复力从图4恢复到图3的状态。消失的间隙δ重新出现了,这样,阀芯28的左侧密封放开了,阀杆5能藉由驱动装置无障碍地旋转地驱动到通过状态A。更为优选地,第一限位凸环18.5设有定位倒扣18.6,所述动压胶环20前端设有凸起,该凸起嵌入所述定位倒扣18.6而对动压胶环20在胶环限位槽18.3中定位。更为优选地,为了保护动压胶环20不被动压套19的过量移位而压碎,在气体容纳室24中设有第三限位凸起31,所述第三限位凸起31对动压套19的移动起止挡作用。当需要关闭时,驱动装置无障碍地反向旋转到关闭状态B,在阀芯密封圈16的上游即阀体的入口部4和/或出口部6设有动压密封装置22,启动流体泵,将流体F填充到流体容纳室23内,动压套19前移,动压胶环20拱起紧压在阀芯28的密封部28.3上,对阀门2的阀芯进行密封。然后,在阀室内填充冷却流体,以冷却动压密封装置22和阀芯28。实施例二入口部4和/或出口部6设有阀芯密封装置21;具体地,入口部4和/或出口部6或者动压套19内套设有阀芯密封套31,阀芯密封套31通过固定法兰固定在入口部或出口部上;阀芯密封套31的上端面设有密封圈定位环槽11和内台阶12,密封圈定位环槽11内设有滑槽13,阀芯密封装置21设置在所述密封圈定位环槽11中,所述阀芯密封装置21包括顶压弹簧15、滑座17和阀芯密封圈16;阀芯密封圈16通过燕尾槽嵌装在滑座17的顶部;滑座17外圆周面设有滑条14,滑座17通过顶压弹簧15压装在密封圈定位环槽11中,所述滑条14滑动设置在滑槽13中。阀芯密封圈16具有阀芯密封面16.1和竖直滑动环面16.2,所述竖直滑动环面16.2与密封圈定位环槽10内表面滑动接触;所述阀芯密封面16.1横截面为凸圆弧面,所述凸圆弧的弧高为1-3mm。阀芯密封圈16采用橡胶、PTFE、尼龙、PEEK等软弹性材料。对于Class600磅级以上的要求,应选用经过验证的具有防爆减压特性的材料。阀芯密封装置21和动压密封装置22可以有如下几种配合方式,方式一:所述阀体1的入口部4设有阀芯密封装置21和动压密封装置22,出口部不设密封装置;方式二:所述阀体1的入口部4设有阀芯密封装置21和动压密封装置22,出口部仅设阀芯密封装置21;方式三:所述阀体1的入口部4和出口部均设有阀芯密封装置21和动压密封装置22;首先,阀芯密封装置21是日常低成本的密封装置,当阀芯密封装置21因长期在高温环境下失去密封能力时,采用动压密封装置22对阀芯密封装置21的替代,让阀的功能延续;在工业机器停产时,对阀芯密封装置21进行拆装更换。或者在高温高压下,阀芯密封装置21不能胜任高温阀的密封工作时,则开启动压密封转轴22,利用阀芯密封装置21和动压密封装置22的两道密封对高温阀进行密封。动压密封装置22的结构及其他结构与实施例一相同。在此,对阀门进行耐高温分级:PI级:阀门的工作温度t>425~550℃(800~1000℉)定为高温Ⅰ级,简称PⅠ级。PII级:阀门工作温度t>550~650℃(1000~1200℉)定为高温Ⅱ级,简称PⅡ级。PIII级:阀门工作温度t>650~730℃(1200~1350℉)定为高温Ⅲ级,简称PⅢ级。PIV级:阀门工作温度t>730~816℃(1350~1500℉),称其为高温Ⅳ级,简称PⅣ级。PV级:阀门的工作温度t>816℃(1500℉)以上的温度区域,称为阀门的最高温度级,即高温V级,简称PV级。在不同高温环境中压力在0.5-2MPa进行持续时间6月的压力试验,对所述实施例进行液体压力试验,具体试验参数如下表1:表1样品500℃,PI级600℃,PII级700℃,PIII级800℃,PIV级900℃,PV级实施例1√√√ⅩⅩ实施例2√√√√√√:表示高温阀符合在试验持续时间内无可见泄漏的A级密封。Ⅹ:表示未通过,造成泄漏;所述超高温阀,既利用了倒锥形的阀芯密封圈结构,同时又利用了动压密封装置22的辅助作用,二者协同作用,弥补了密封圈长期高温环境中失去弹性的性能缺陷,使得高温阀的密封等级大大提高。当前第1页1 2 3