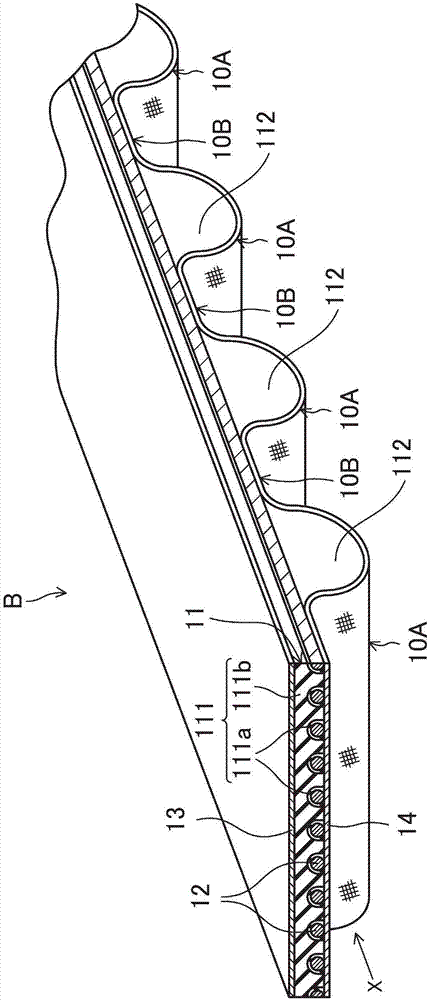
本发明涉及一种齿形带及其制造方法。
背景技术:
:在汽车发动机中作为动力传递部件使用齿形带,该动力传递部件用以利用曲轴的动力,驱动顶置凸轮轴旋转。上述齿形带通常具有橡胶制的带主体,在该带主体的背面橡胶部的内周侧以规定齿距且彼此保持间隔地设有多个齿形橡胶部,该背面橡胶部形成为环状的平带形状,多个所述齿形橡胶部与背面橡胶部设为一体。上述齿形带通常具有:带主体的设有齿形橡胶部的内周侧的表面被齿部补强布覆盖的结构。在专利文献1中公开了一种齿形带,该齿形带的背面橡胶部的橡胶硬度比齿形橡胶部高且橡胶硬度从背面橡胶部的外周面向齿形橡胶部的内周面逐渐地下降。在专利文献2中公开了一种齿形带,在该齿形带中,用含有短纤维的橡胶组合物形成齿形橡胶部而使其高硬度化,另一方面,进一步用低硬度橡胶层覆盖齿部补强布的外侧,从而提高了耐磨性和冲击吸收性,其中,该齿部补强布覆盖带主体的设有齿形橡胶部的内周侧的表面。专利文献1:日本公开专利公报特开2003-314622号公报专利文献2:日本公开专利公报特开2010-210088号公报技术实现要素:本发明涉及一种齿形带,其包括橡胶制的带主体,所述带主体具有背面橡胶部和多个齿形橡胶部,所述背面橡胶部形成为环状的平带形状,多个所述齿形橡胶部以规定齿距且彼此保持间隔设置在所述背面橡胶部的内周侧,并且每个所述齿形橡胶部与所述背面橡胶部设为一体,多个所述齿形橡胶部中的每一个所述齿形橡胶部具有内部橡胶部分和表面橡胶部分,所述内部橡胶部分通过在带宽方向上交替层叠由橡胶硬度相对较高的第一橡胶组合物形成的高硬度橡胶层和由橡胶硬度相对较低的第二橡胶组合物形成的低硬度橡胶层而构成,所述表面橡胶部分设置为覆盖所述内部橡胶部分的内周侧表面且由与所述高硬度橡胶层同一的、橡胶硬度相对较高的第一橡胶组合物形成。本发明涉及一种本发明的齿形带的制造方法,所述齿形带的制造方法使用带成型模,所述带成型模具有如下外周面,在该外周面上设置有各自形成为沿所述带成型模的轴向延伸的多个齿部形成槽,多个所述齿部形成槽彼此保持间隔沿所述带成型模的周向而设,在将芯线螺旋状地缠绕在所述带成型模的外周面上后,将片状的第一未交联橡胶组合物和片状的第二未交联橡胶组合物依次缠绕在所述芯线上而在所述带成型模上成型出未交联带坯,通过将所述未交联带坯朝着所述带成型模一侧按压并加热,使得所述第一未交联橡胶组合物和所述第二未交联橡胶组合物通过所述芯线之间并流入所述带成型模的多个所述齿部形成槽中的每一个所述齿部形成槽内,同时使所述第一未交联橡胶组合物和所述第二未交联橡胶组合物交联,其中,所述第一未交联橡胶组合物形成橡胶硬度相对较高的第一橡胶组合物,所述第二未交联橡胶组合物形成橡胶硬度相对较低的第二橡胶组合物。附图说明图1是第一实施方式的齿形带的一部分的立体图。图2是图1中的箭头x方向上的主视图。图3是第一实施方式的齿形带的两个齿部的侧视图。图4是沿图2中的iv-iv剖开的剖视图。图5是沿图2中的v-v剖开的剖视图。图6是沿图3中的vi-vi剖开的剖视图。图7是带成型模的一部分的剖视图。图8a是第一实施方式的齿形带的制造方法的第一说明图。图8b是第一实施方式的齿形带的制造方法的第二说明图。图8c是第一实施方式的齿形带的制造方法的第三说明图。图8d是第一实施方式的齿形带的制造方法的第四说明图。图9是第二实施方式的齿形带的一部分的立体图。图10是第二实施方式的齿形带的剖视图,该剖视图对应于图6。图11a是第一实施方式的齿形带的变形例的剖视图,该剖视图对应于图6。图11b是第二实施方式的齿形带的变形例的剖视图,该剖视图对应于图10。图12是第一实施方式的齿形带的另一变形例的剖视图,该剖视图对应于图6。图13是示出高负荷耐久试验用带走行试验机的带轮平面布置情况的图。图14是示出耐冲击性振动试验用带试验机的带轮平面布置情况的图。具体实施方式下面,对实施方式进行详细的说明。(第一实施方式)图1~图6示出第一实施方式所涉及的齿形带b。第一实施方式所涉及的齿形带b例如在汽车发动机中用作动力传递部件,该动力传递部件用以利用曲轴的动力,驱动顶置凸轮轴(ohc)旋转。第一实施方式所涉及的齿形带b例如具有下述尺寸,即:带长为700mm以上2300mm以下,带宽为10mm以上40mm以下,带厚为4.5mm以上7.0mm以下。第一实施方式所涉及的齿形带b是一种啮合式传动带,该啮合式传动带在其内周侧具有以规定齿距且彼此保持间隔而设的多个齿部10a。齿部10a是由沿带宽方向延伸且侧视时呈半圆形的突条构成的所谓的圆弧齿。齿部10a的齿高h由下述尺寸规定,该尺寸为:在带长度方向上彼此相邻的一对齿部10a之间的从齿底部10b到齿部10a的顶端为止的尺寸。齿高h例如为2.5mm以上4.0mm以下。齿部10a的齿宽w由下述尺寸规定,该尺寸为:在带长度方向上夹着齿部10a彼此相邻的一对齿底部10b的齿底部端之间的尺寸。齿宽w例如为4.5mm以上8.0mm以下。齿部10a的齿距p例如为6.0mm以上10.0mm以下。需要说明的是,齿部10a也可以具有如梯形齿等其它形状,还可以是形成为沿相对于带宽方向倾斜的方向延伸的斜齿。第一实施方式所涉及的齿形带b包括带主体11、芯线12、背面补强布13和齿部补强布14。带主体11由橡胶制作,并具有背面橡胶部111和多个齿形橡胶部112。背面橡胶部111形成为环状的平带形状。背面橡胶部111的厚度例如为1.5mm以上4.0mm以下。多个齿形橡胶部112对应着齿部10a以规定齿距且彼此保持间隔设置在背面橡胶部111的内周侧,并且每个齿形橡胶部112形成为与齿部10a相对应的形状且与背面橡胶部111设为一体。齿形橡胶部112的高度h由下述尺寸规定,该尺寸为:从埋设在背面橡胶部111中的芯线12的最内周部到齿形橡胶部112的顶端为止的尺寸。齿形橡胶部112的高度h例如为2.5mm以上4.0mm以下。芯线12以沿齿形带的周向延伸且形成沿带宽方向具有螺距的螺旋的方式埋设于带主体11的背面橡胶部111的内周侧表面层中。将用玻璃纤维、芳纶纤维、碳纤维、金属纤维等制成的捻线用作芯线12。芯线12优选设置为s捻线和z捻线形成双螺旋,但也可以单独将s捻线或z捻线用作芯线12。芯线12的直径例如为0.5mm以上2.5mm以下。在带宽方向上彼此相邻的芯线12之间的间隙基本恒定,例如为0.5mm以上3.0mm以下。背面补强布13贴设在带主体11的背面橡胶部111的外周侧的表面上,以覆盖住该表面。齿部补强布14贴设在带主体11的设有多个齿形橡胶部112的内周侧的表面上,以覆盖住该表面。因此,齿形橡胶部112被齿部补强布14覆盖,以构成各个齿部10a。在齿底部10b,埋设于带主体11的背面橡胶部111中的芯线12布置在齿部补强布14的内侧且贴着齿部补强布14的位置上。背面补强布13和齿部补强布14例如由尼龙纤维(聚酰胺纤维)、聚酯纤维、芳纶纤维、棉等纱线制成的梭织布、针织物、无纺布等构成。背面补强布13和齿部补强布14优选由上述梭织布、针织物、无纺布等中的用尼龙纤维制成的梭织布构成。背面补强布13和齿部补强布14优选例如像纬纱经过假捻加工等的梭织布那样具有伸缩性。为了与带主体11黏合,优选,对背面补强布13和齿部补强布14进行下述黏合处理中的一种或两种以上黏合处理,所述黏合处理有:浸渍在所谓的rfl水溶液中后再进行加热的rfl处理;浸渍在低粘度的橡胶胶水中后再使其干燥的浸泡(soaking)处理;以及在带主体11侧的表面上涂布高粘度的橡胶胶水并使其干燥的涂层(coating)处理。在进行上述黏合处理之前,也可以对背面补强布13和齿部补强布14进行浸渍在环氧树脂溶液或异氰酸酯树脂溶液中后再加热的基础处理。背面补强布13和齿部补强布14的厚度例如为0.3mm以上2mm以下。在第一实施方式所涉及的齿形带b中,带主体11由橡胶硬度相对较高的第一橡胶组合物和橡胶硬度相对较低的第二橡胶组成物形成。带主体11的背面橡胶部111包括多个芯线包覆橡胶部分111a和除此以外的背面橡胶部分111b。多个芯线包覆橡胶部分111a在带宽方向上彼此保持间隔而设。多个芯线包覆橡胶部分111a中的每一个芯线包覆橡胶部分111a设置为埋设有一根芯线12且包覆该芯线12。芯线包覆橡胶部分111a由高硬度的第一橡胶组合物形成。背面橡胶部分111b构成背面橡胶部111的背面层,在背面橡胶部分111b上贴设有背面补强布13。背面橡胶部分111b由低硬度的第二橡胶组合物形成。带主体11的多个齿形橡胶部112中的每一个齿形橡胶部112包括内部橡胶部分1121和被设置为覆盖内部橡胶部分1121的内周侧表面的表面橡胶部分1122。内部橡胶部分1121通过在带宽方向上交替层叠高硬度橡胶层1121a和低硬度橡胶层1121b而构成。高硬度橡胶层1121a在带宽方向上与背面橡胶部111的多个芯线包覆橡胶部分111a中的每一个芯线包覆橡胶部分111a相对应地设置。高硬度橡胶层1121a由与背面橡胶部111的芯线包覆橡胶部分111a同一的高硬度的第一橡胶组合物形成,因此高硬度橡胶层1121a构成为与相对应的芯线包覆橡胶部分111a连续。低硬度橡胶层1121b在带宽方向上与彼此相邻的芯线12的间隙相对应地设置。低硬度橡胶层1121b由与背面橡胶部111的背面橡胶部分111b同一的低硬度的第二橡胶组合物形成,因此低硬度橡胶层1121b构成为与相对应的背面橡胶部分111b连续。此外,所有的低硬度橡胶层1121b经由背面橡胶部分111b连接。高硬度橡胶层1121a中的每一个高硬度橡胶层1121a和低硬度橡胶层1121b中的每一个低硬度橡胶层1121b在带横截面中的层厚也可以沿带厚方向基本恒定。高硬度橡胶层1121a的层厚例如为0.5mm以上3.0mm以下。低硬度橡胶层1121b的层厚例如为0.5mm以上3.0mm以下。低硬度橡胶层1121b形成为从在带宽方向上彼此相邻的芯线12之间的间隙向内周侧垂下。带的纵截面中的低硬度橡胶层1121b的形状优选为与齿形橡胶部112的形状相对应的半圆形状。从获得后述优异的高负荷耐久性和耐冲击性的观点出发,从埋设于背面橡胶部111中的芯线12的最内周部起到该低硬度橡胶层1121b的顶端为止的平均尺寸1,相对于齿形橡胶部112的高度h的比例优选在30%以上,更优选在50%以上,进一步优选在70%以上。表面橡胶部分1122由与芯线包覆橡胶部分111a及高硬度橡胶层1121a同一的高硬度的第一橡胶组合物形成,因此表面橡胶部分1122构成为与内部橡胶部分1121的高硬度橡胶层1121a连续。所有的芯线包覆橡胶部分111a和高硬度橡胶层1121a经由表面橡胶部分1122连接。表面橡胶部分1122的厚度例如为0.5mm以上4.0mm以下。第一和第二橡胶组合物是由分别在橡胶成分中添加有各种橡胶添加剂的第一和第二未交联橡胶组合物被加热且加压而使橡胶成分交联后得到的。作为第一和第二橡胶组合物的橡胶成分,能够列举出:例如,氢化丁腈橡胶(以下称为“h-nbr”)、使甲基丙烯酸锌等不饱和金属盐微分散而进行补强的h-nbr(以下称为“补强h-nbr”)、氯磺化聚乙烯橡胶、氯丁橡胶、三元乙丙橡胶(epdm)等乙烯-α-烯烃弹性体橡胶等。橡胶成分优选使用上述橡胶成分中的一种或两种以上。第一和第二橡胶组合物优选包含相同的橡胶成分。第一和第二橡胶组合物的橡胶成分优选包含h-nbr和补强h-nbr中的至少一者。更优选,高硬度的第一橡胶组合物的橡胶成分是h-nbr和补强h-nbr的混合橡胶,且低硬度的第二橡胶组合物的橡胶成分仅是h-nbr。作为橡胶添加剂,能够列举出加工助剂、硫化活性剂、防老剂、补强剂、增塑剂、共交联剂、短纤维、交联剂等。作为加工助剂能够列举出:例如,硬脂酸、聚乙烯蜡、脂肪酸的金属盐等。加工助剂优选采用上述加工助剂中的一种或两种以上。相对于橡胶成分100质量份而言,加工助剂的含量例如为0.3质量份以上0.7质量份以下。作为硫化活性剂能够列举出:例如,氧化锌(锌白)、氧化镁等金属氧化物、金属碳酸盐、脂肪酸及其衍生物等。硫化活性剂优选使用上述硫化活性剂中的一种或两种以上。相对于橡胶成分100质量份而言,硫化活性剂的含量例如为3质量份以上15质量份以下。作为防老剂能够列举出:例如,苯并咪唑类防老剂、芳香族仲胺类防老剂、胺-酮类防老剂等。防老剂优选使用上述防老剂中的一种或两种以上。相对于橡胶成分100质量份而言,防老剂的含量例如为1.5质量份以上3.5质量份以下。作为补强剂,能够列举出炭黑、碳酸钙、二氧化硅等。补强剂优选使用上述补强剂中的一种或两种以上。作为炭黑能够列举出:例如,槽黑;超耐磨炉黑(saf)、中超耐磨炉黑(isaf)、n-339、高耐磨炉黑(haf)、n-351、中耐磨炉黑(maf)、快压出炉炭黑(fef)、半补强炉黑(srf)、通用炉黑(gpf)、超导电炉黑(ecf)、n-234等炉黑;细粒子热解炭黑(finethermalfurnaceblack:ft)、中粒子热解炭黑(mediumthermalfurnnaceblack:mt)等热裂解炭黑;乙炔黑等。炭黑优选使用上述炭黑中的一种或两种以上。相对于橡胶成分100质量份而言,炭黑的含量例如为0.1质量份以上50质量份以下。在将碳酸钙用作补强剂时,相对于橡胶成分100质量份而言,碳酸钙的含量例如为5质量份以上15质量份以下。在将二氧化硅用作补强剂时,相对于橡胶成分100质量份而言,二氧化硅的含量例如为10质量份以上30质量份以下。作为增塑剂能够列举出:例如,聚醚酯、癸二酸二辛酯(dos)等癸二酸二烷基酯;邻苯二甲酸二丁酯(dbp)、邻苯二甲酸二辛酯(dop)等邻苯二甲酸二烷基酯;己二酸二辛酯(doa)等己二酸二烷基酯等。增塑剂优选使用上述增塑剂中的一种或两种以上。相对于橡胶成分100质量份而言,增塑剂的含量例如为3质量份以上15质量份以下。作为共交联剂能够列举出:例如,三羟甲基丙烷三甲基丙烯酸酯、间亚苯基双马来酰亚胺(m-phenylenedimaleimide)、二甲基丙烯酸锌、三烯丙基异氰脲酸酯等。共交联剂优选使用上述共交联剂中的一种或两种以上。相对于橡胶成分100质量份而言,共交联剂的含量例如为1质量份以上8质量份以下。作为短纤维能够列举出:例如,芳纶短纤维、尼龙短纤维、聚酯短纤维等。短纤维的长度例如为1mm以上3mm以下。短纤维优选使用上述短纤维中的一种或两种以上。相对于橡胶成分100质量份而言,短纤维的含量例如为1质量份以上5质量份以下。作为交联剂能够列举出硫磺和有机过氧化物。作为交联剂,可以仅添加硫磺,或者,也可以仅添加有机过氧化物,还可以一起使用硫磺和有机过氧化物。其中,一起使用硫磺和有机过氧化物是优选的,在此情况下,交联剂例如为如下添加量:相对于橡胶成分100质量份,硫磺为0.1质量份以上0.7质量份以下,有机过氧化物为2质量份以上5质量份以下。第一橡胶组合物的橡胶硬度高于第二橡胶组合物的橡胶硬度。从获得后述优异的高负荷耐久性和耐冲击性的观点出发,第一橡胶组合物的橡胶硬度优选为85ha以上95ha以下,更优选为88ha以上94ha以下。从同样的观点出发,第二橡胶组合物的橡胶硬度优选为50ha以上80ha以下,更优选为65ha以上75ha以下。从同样的观点出发,第一橡胶组合物的橡胶硬度与第二橡胶组合物的橡胶硬度之差优选为5ha以上45ha以下,更优选为13ha以上29ha以下。从同样的观点出发,第一橡胶组合物的橡胶硬度与第二橡胶组合物的橡胶硬度之比优选为1.1以上1.9以下,更优选为1.2以上1.5以下,进一步优选为1.2以上1.4以下。从获得后述优异的高负荷耐久性和耐冲击性的观点出发,第一橡胶组合物的纹理方向的在25℃下的拉伸强度tb优选为20mpa以上40mpa以下,更优选为25mpa以上35mpa以下。从同样的观点出发,第二橡胶组合物的纹理方向的在25℃下的拉伸强度tb优选为15mpa以上35mpa以下,更优选为20mpa以上30mpa以下。该第一橡胶组合物的拉伸强度tb优选高于第二橡胶组合物的拉伸强度tb。从获得后述优异的高负荷耐久性和耐冲击性的观点出发,第一橡胶组合物的纹理方向的在25℃下的伸长率eb优选为100%以上300%以下,更优选为150%以上250%以下。从同样的观点出发,第二橡胶组合物的纹理方向的在25℃下的伸长率eb优选为350%以上550%以下,更优选为400%以上500%以下。该第一橡胶组合物的伸长率eb优选小于第二橡胶组合物的伸长率eb。从获得后述优异的高负荷耐久性和耐冲击性的观点出发,第一橡胶组合物的纹理方向的在25℃下的伸长率100%时的拉伸应力m100优选为10mpa以上30mpa以下,更优选为15mpa以上25mpa以下。从同样的观点出发,第二橡胶组合物的纹理方向的在25℃下的伸长率100%时的拉伸应力m100优选为1.5mpa以上5.5mpa以下,更优选为2.5mpa以上4.5mpa以下。该第一橡胶组合物的伸长率100%时的拉伸应力m100优选高于第二橡胶组合物的伸长率100%时的拉伸应力m100。这里,第一和第二橡胶组合物的橡胶硬度是基于jisk6253使用a型硬度计进行测量的。第一和第二橡胶组合物的纹理方向的拉伸强度tb、伸长率eb及伸长率100%时的拉伸应力m100是通过进行基于jisk6301的拉伸试验来测量的。上述结构的第一实施方式所涉及的齿形带b例如在汽车发动机中卷挂在曲轴带轮和ohc带轮之间,用作将曲轴带轮的动力传递给ohc带轮的动力传递部件。对汽车发动机存在紧凑化的要求,为了满足该要求,需要使齿形带的宽度变窄。然而,已经使宽度变窄的齿形带也需要具有与宽度变窄以前同等的高负荷持久性和耐冲击性。对此,根据本第一实施方式所涉及的齿形带b,齿形橡胶部112具有内部橡胶部分1121,此外,设置为覆盖该内部橡胶部分1121的内周侧表面的表面橡胶部分1122由与高硬度橡胶层1121a同一的、橡胶硬度相对较高的第一橡胶组合物形成,由此,能够获得优异的高负荷耐久性和耐冲击性,其中,所述内部橡胶部分1121通过在带宽方向上交替层叠由橡胶硬度相对较高的第一橡胶组合物形成的高硬度橡胶层1121a和由橡胶硬度相对较低的第二橡胶组合物形成的低硬度橡胶层1121b而构成。能够推测这是因为:由高硬度的表面橡胶部分1122来抑制齿形橡胶部112的变形,因此能够避免在齿形橡胶部112上产生直接关系到缺齿的峰值应变,除此之外,内部橡胶部分1121具有高硬度橡胶层1121a和低硬度橡胶层1121b的交替层叠结构,由此对齿形橡胶部112变形的追随性提高,并且施加到齿形橡胶部112上的负荷的负荷分布得到均匀化,因此,能够避免在齿形橡胶部112上产生直接关系到缺齿的峰值应力。接下来,参照图7和图8a~图8d对第一实施方式所涉及的齿形带b的制造方法进行说明。第一实施方式所涉及的齿形带b的制造方法包括:材料准备工序、成型工序、交联工序以及整理工序。<材料准备工序>对规定的橡胶成分进行素炼,向其中加入各种橡胶添加剂并混炼,从而得到第一未交联橡胶组合物,该第一未交联橡胶组合物形成橡胶硬度相对较高的第一橡胶组合物。然后,通过对所得到的第一未交联橡胶组合物进行压延成型等,制作片状的第一未交联橡胶组合物151。同样地,对规定的橡胶成分进行素炼,向其中加入各种橡胶添加剂并混炼,从而得到第二未交联橡胶组合物,该第二未交联橡胶组合物形成橡胶硬度相对较低的第二橡胶组合物。然后,通过对所得到的第二未交联橡胶组合物进行压延成型等,制作片状的第二未交联橡胶组合物152。对芯线12、背面补强布13和齿部补强布14都进行黏合处理。此外,将背面补强布13和齿部补强布14分别成型为筒状。<成型工序>图7示出带成型模20。所述带成型模20呈圆筒状,并具有如下外周面,在该外周面上设置有各自沿该带成型模20的轴向延伸的多个齿部形成槽21,多个所述齿部形成槽21彼此保持间隔沿该带成型模20的周向而设。如图8a所示,将筒状的齿部补强布14套在带成型模20的外周面上,然后将芯线12螺旋状地缠绕在该齿部补强布14上。这里,为了使相邻的芯线12之间的间隙基本恒定,在将s捻线和z捻线用作芯线12的情况下,使s捻线和z捻线的中心间距恒定,并且以该中心间距的两倍尺寸为螺距,将上述s捻线和z捻线双重螺旋状地缠绕即可。此外,在单独将s捻线或z捻线用作芯线12的情况下,将该捻线以恒定的螺距螺旋状地缠绕即可。接下来,将片状的第一未交联橡胶组合物151和片状的第二未交联橡胶组合物152依次缠绕在芯线12上。这里,从获得优异的高负荷耐久性和耐冲击性的观点出发,优选第一未交联橡胶组合物151缠绕得比第二未交联橡胶组合物152更厚。从同样的观点出发,第一未交联橡胶组合物151的体积与第二未交联橡胶组合物152的体积之比优选大于1,更优选在1.5以上,并且,优选在3.5以下,更优选在2.5以下。在使用片状的第一和第二未交联橡胶片151、152时,优选它们的纹理方向对应于带长方向。然后,进一步将筒状的背面补强布13套在第二未交联橡胶片152上,在带成型模20上成型出形成未交联带坯s’。<交联工序>如图8b所示,将橡胶套筒22套在带成型模20上的未交联带坯s’上,然后将它们放到硫化罐内并进行密封,向硫化罐内填充高温高压蒸气并将该状态保持规定的成型时间。通过按照上述方式将未交联带坯s’朝着带成型模一侧按压并加热,如图8c所示,使得第一和第二未交联橡胶组合物151、152通过芯线12之间并一边按压齿部补强部一边流入带成型模20的多个齿部形成槽21中的每一个齿部形成槽21内,同时使第一和第二未交联橡胶组合物151、152交联。与此同时,芯线12、背面补强布13和齿部补强布14复合成一体,最后,如图8d所示,成型出圆筒状的带坯s。这里,从使第一和第二未交联橡胶组合物151、152如图8c所示那样流动的观点出发,优选,第一未交联橡胶组合物151的在100℃下的门尼粘度比第二未交联橡胶组合物152的在100℃下的门尼粘度高。第一未交联橡胶组合物151的在100℃下的门尼粘度优选在40ml1+4(100℃)以上,更优选在50ml1+4(100℃)以上,并且,优选在70ml1+4(100℃)以下,更优选在60ml1+4(100℃)以下。第二未交联橡胶组合物152的在100℃下的门尼粘度优选在20ml1+4(100℃)以上,更优选在30ml1+4(100℃)以上,并且,优选在60ml1+4(100℃)以下,更优选在50ml1+4(100℃)以下。第一未交联橡胶组合物151的在100℃下的门尼粘度与第二未交联橡胶组合物152的在100℃下的门尼粘度之比优选大于1且在2.0以下,更优选在1.5以下。门尼粘度是根据jisk6300测量的。<整理工序>对硫化罐的内部进行减压并解除密封后,取出在带成型模20与橡胶套筒22之间成型出的带坯s并使其脱模,通过将带坯s切割成规定宽度来获得齿形带b。(第二实施方式)图9和图10示出第二实施方式所涉及的齿形带b。需要说明的是,名称与第一实施方式相同的部分用与第一实施方式相同的符号表示。在第二实施方式所涉及的齿形带b中,在带宽方向上彼此相邻的芯线12之间的间隙中有相对较小的间隙和相对较大的间隙。具体而言,芯线12之间的相对较小的间隙和相对较大的间隙在带宽方向上交替而设。而且,在芯线12之间的间隙相对较小的部分,背面橡胶部111的芯线包覆橡胶部分111a被设置成:隔着该较小的间隙而在带宽方向上彼此相邻的一对芯线12埋设于该芯线包覆橡胶部分111a,并且该芯线包覆橡胶部分111a包覆该一对芯线12。在芯线12之间的间隙相对较大的部分,齿形橡胶部112的内部橡胶部分1121的低硬度橡胶层1121b形成为在带的横截面中从该较大的间隙向内周侧垂下。也就是说,在第二实施方式所涉及的齿形带b中,对芯线12之间的较小的间隙并没有对应地设置低硬度橡胶层1121b,而设置高硬度橡胶层1121a,对芯线12之间的较大的间隙对应地设置低硬度橡胶层1121b。芯线12之间的相对较小的间隙例如为0.01mm以上0.5mm以下。芯线12之间的相对较大的间隙例如为0.5mm以上1.5mm以下。在芯线12之间的相对较大的间隙与相对较小的间隙之比优选为0.6以上100以下。就上述结构的第二实施方式所涉及的齿形带b而言,将s捻线和z捻线用作芯线12,当成型未交联带坯s’时,使s捻线和z捻线的中心间距恒定,并且以尺寸大于该中心间距的两倍尺寸的螺距,将上述s捻线和z捻线双重螺旋状地缠绕即可。因此,在此情况下,由同一芯线包覆橡胶部分111a包覆的一对芯线12是s捻线和z捻线。其它结构、作用和效果与第一实施方式相同。(其它实施方式)在上述第一和第二实施方式中,示出了高硬度橡胶层1121a和低硬度橡胶层1121b各自的带横截面中的层厚沿带厚方向基本恒定的结构,但并不特别限定于此,如与第一实施方式对应的图11a和与第二实施方式对应的图11b所示,在带横截面中的层厚从基端侧起沿着带厚方向逐渐变大后,在顶端急剧地变小的截面形状也可以呈水滴形状。需要说明的是,上述的结构能够通过设计第一和第二未交联橡胶组合物151、152的配方来调节它们的流动性而得到。在第一实施方式中,采用了对所有的芯线12之间的间隙对应地设置低硬度橡胶层1121b的结构,但并不特别限定于此,如图12所示,也可以包括对芯线12之间的间隙没有对应地设置低硬度橡胶层1121b的部分。在上述第一实施方式和第二实施方式中,采用了包括背面补强布13的结构,但并不特别限定于此,也可以采用不具有背面补强布13而背面橡胶部111露出的结构。实施例[未交联橡胶组合物]制备了形成高硬度的第一橡胶组合物的第一未交联橡胶组合物和形成低硬度的第二橡胶组合物的第二未交联橡胶组合物。在表1中也示出了上述未交联橡胶组合物各自的配方情况。(第一未交联橡胶组合物)将作为橡胶成分的h-nbr(日本瑞翁(zeon)公司制,商品名:zetpo12000)60质量%和补强h-nbr(日本瑞翁(zeon)公司制,商品名:zeofortezsc2195cx)40质量%投入密闭型班伯里密炼机的腔室内后进行素炼,然后相对于该橡胶成分100质量份,以投入的方式添加作为硫化活性剂的氧化锌5质量份、防老剂2.5质量份、作为补强剂的炭黑20质量份、作为补强剂的二氧化硅20质量份、增塑剂5质量份、共交联剂6质量份、芳纶短纤维(1mm)3质量份、作为交联剂的硫磺0.3质量份、以及作为交联剂的有机过氧化物3.2质量份后进行混炼,从而制作出第一未交联橡胶组合物。(第二未交联橡胶组合物)将作为橡胶成分的h-nbr(日本瑞翁(zeon)公司制,商品名:zetpo12000)投入密闭型班伯里密炼机的腔室内后进行素炼,然后相对于该橡胶成分100质量份,以投入的方式添加加工助剂0.5质量份、作为硫化活性剂的氧化锌10质量份、防老剂2.5质量份、作为补强剂的炭黑40质量份、作为补强剂的碳酸钙10质量份、增塑剂10质量份、共交联剂3质量份、作为交联剂的硫磺0.5质量份、以及作为交联剂的有机过氧化物3.2质量份后进行混炼,从而制作出第二未交联橡胶组合物。[表1]第一未交联橡胶组合物第二未交联橡胶组合物h-nbr60100补强h-nbr40硬脂酸0.5氧化锌510防老剂2.52.5炭黑2040碳酸钙10二氧化硅20增塑剂510共交联剂63芳纶短纤维3硫磺0.30.5有机过氧化物3.23.2[齿形带]制作出下述实施例、比较例1和比较例2的齿形带。在表2中也示出了上述齿形带各自的构成成分。(实施例)通过压延成型将第一和第二未交联橡胶组合物分别成型为片状。使用上述片状的第一和第二未交联橡胶组合物(第一未交联橡胶组合物67体积%和第二未交联橡胶组合物33体积%),制作出除了不具有背面补强布以外其它都与上述第一实施方式相同的齿形带,并将其作为实施例。实施例的齿形带的带长为1381mm,带宽为25mm,带厚为6.3mm。齿高h为3.5mm,齿宽w为7.4mm,齿距p为9.525mm。齿形橡胶部的高度h为3.0mm。高硬度橡胶层的层厚平均为1.5mm,低硬度橡胶层的层厚平均为1.5mm。表面橡胶部分的厚度平均为1.0mm。从芯线的最内周部到低硬度橡胶层的顶端为止的尺寸1相对于齿形橡胶部的高度h的比例平均为67%。需要说明的是,将用玻璃纤维制作的捻线用作了芯线,将用尼龙6,6纤维制作的梭织布用作了齿部补强布,其中,上述玻璃纤维和上述尼龙6,6纤维都经过了黏合处理。(比较例1和比较例2)制作出除了仅使用片状的第一未交联橡胶组合物形成带主体之外其它都与实施例相同的齿形带,并将其作为比较例1。此外,制作出除了仅使用片状的第二未交联橡胶组合物形成带主体之外其它都与实施例相同的齿形带,并将其作为比较例2。[表2][试验方法](材料试验)<门尼粘度>对于第一和第二未交联橡胶组合物,根据jisk6300分别测量了100℃下的门尼粘度。<橡胶硬度>对于使第一和第二未交联橡胶组合物交联后得到的第一和第二橡胶组合物,根据jisk6253使用a型硬度计分别测量了橡胶硬度。<拉伸特性>对于使第一和第二未交联橡胶组合物交联后得到的第一和第二橡胶组合物,通过基于jisk6301的拉伸试验,分别测量了纹理方向的拉伸强度tb、伸长率eb及伸长率100%时的拉伸应力m100。(带试验)<高负荷耐久试验>图13示出高负荷耐久试验用带走行试验机30的带轮平面布置情况。该带走行试验机30具有主动带轮31、设置在该主动带轮31的右方的从动带轮32、以及设置在该主动带轮31与该从动带轮32之间的下侧的惰轮33。在主动带轮31的外周上设有二十一个齿部啮合槽。在从动带轮32的外周上设有四十二个齿部啮合槽。惰轮33的外径为52mm。对于实施例、比较例1和比较例2各自的齿形带b进行了带走行试验,在各试验中,将实施例、比较例1和比较例2的齿形带b分别卷挂在该带走行试验机30的主动带轮31、从动带轮32及惰轮33上,并在从动带轮32上向右方施加1200n的自重(deadweight)dw,在环境温度100℃下以6000rpm的转速使主动带轮旋转。然后,测量了直到齿形带破损为止的旋转次数。<耐冲击性振动试验>图14示出耐冲击性振动试验用带试验机40的带轮平面布置情况。该带试验机40具有:主动带轮41、设置在该主动带轮41的左斜下方的固定的第一从动带轮42、设置在该主动带轮41的左斜上方的第二从动带轮43、设置在主动带轮41、第一从动带轮42和第二从动带轮43彼此之间的三个惰轮44、以及设置在第一从动带轮42和第二从动带轮43之间且紧靠惰轮44上方的张紧轮45。在主动带轮41的外周上设有二十二个齿部啮合槽。在第一从动带轮42的外周上设有二十二个齿部啮合槽。在第二从动带轮43的外周上设有四十四个齿部啮合槽。惰轮44的外径为28.5mm。张紧轮45的外径为67.7mm。对于实施例、比较例1和比较例2各自的齿形带b进行了反复旋转振动试验,在各试验中,将实施例、比较例1和比较例2的齿形带b分别卷挂在该带试验机40上,以使带的齿部与主动带轮41、第一从动带轮42及第二从动带轮43相啮合且使带的背面与惰轮44和张紧轮45相接触,使用张紧轮45对带施加设定重量(setweight),以使带张力达到800n,在环境温度为25℃下,使主动带轮41正向旋转,当在主动带轮41上产生规定的负荷时,将旋转方向改变为逆向,当在主动带轮41上产生规定的负荷时,将旋转方向再次改变为正向。然后,测量了直到齿形带发生缺齿而破损为止的振动次数。[试验结果]在表3及表4中示出了试验结果。[表3][表4]实施例比较例1比较例2高负荷耐久试验(次)8.5×1073.0×1071.0×104耐冲击性振动试验(次)1.1×1053.0×1040根据表3的材料试验的试验结果,确认了使第一未交联橡胶组合物交联后得到的第一橡胶组合物的硬度高于使第二未交联橡胶组合物交联后得到的第二橡胶组合物的硬度。还可知,形成高硬度的第一橡胶组合物的第一未交联橡胶组合物的在100℃下的门尼粘度低于形成低硬度的第二橡胶组合物的第二未交联橡胶组合物的门尼粘度。而且,可知,与使第二未交联橡胶组合物交联后得到的第二橡胶组合物相比,使第一未交联橡胶组合物交联后得到的第一橡胶组合物在纹理方向上的拉伸强度tb高、伸长率eb小、且伸长率100%时的拉伸应力m100高。根据表4的带走行试验的试验结果可知,实施例在高负荷耐久性和耐冲击性上都优于比较例1及比较例2。其中,实施例中的齿形橡胶部具有内部橡胶部分和表面橡胶部分,该内部橡胶部分通过在带宽方向上交替层叠由高硬度的第一橡胶组合物形成的高硬度橡胶层和由低硬度的第二橡胶组合物形成的低硬度橡胶层而构成,该表面橡胶部分由高硬度的第一橡胶组合物形成且设置为覆盖上述内部橡胶部分,比较例1的齿形橡胶部仅由高硬度的第一橡胶组合物形成,比较例2的齿形橡胶部仅由低硬度的第二橡胶组合物形成。产业实用性本发明在齿形带及其制造方法的
技术领域:
中是很有用的。符号说明b齿形带s带坯s’未交联带坯10a齿部10b齿底部11带主体111背面橡胶部111a芯线包覆橡胶部分111b背面橡胶部分112齿形橡胶部1121内部橡胶部分1121a高硬度橡胶层1121b低硬度橡胶层1122表面橡胶部分12芯线13背面补强布14齿部补强布151第一未交联橡胶组合物152第二未交联橡胶组合物20带成型模21齿部形成槽22橡胶套筒30、40带走行试验机31、41主动带轮32从动带轮33、44惰轮42第一从动带轮43第二从动带轮45张紧轮当前第1页12