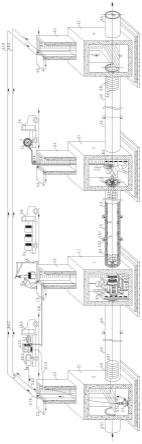
1.本发明属于城镇埋地给排水管道领域,涉及一种用于埋地给排水管道内衬非开挖修复方法、系统。
背景技术:2.作为重要的公共基础设施,城镇给排水管道在保障供水、消除内涝、防洪减灾、削减污染等方面发挥着重大作用。以埋地排水管道为例,经常运行过程中,路面车辆长期动静载施加、管顶回填土密实度降低、塑料管材韧性变差、水中污染气体腐蚀、接口胶圈老化脆变、管底基础软化沉降等各种内外因,都会造成管壁腐蚀破裂、管壁结构性裂缝和变形、管接口脱节和错位、管基不均匀沉降导致管道起伏等各种结构性缺陷。相对于功能性缺陷,比如管底污物沉积、管壁结垢、水面浮渣,结构性缺陷更会加速管道老化和结构破坏,形成地下水渗漏污染、道路空洞病害、路面下陷坍陷等安全隐患。严重时,路面塌陷空洞会造成路面车辆和行人突然跌入,导致生命安全事故。
3.如果埋地缺陷管道大都位于交通繁忙、环境敏感、施工空间受限等区域,则优选采用非开挖修复技术。各种非开挖方法施工过程中,遇到的最大难题是管道的整体结构性修复。管道内壁腐蚀造成管壁开裂严重,或者长期受压管道变形较大,管道结构遭受损伤,存在较大的刚度、韧性和结构稳定性缺陷,已经无法长期承受外部土压力、动荷载、地下水位压力和内部流动水压情况,为避免开槽埋管、就地翻排所带来的交通影响和场地影响,采用非开挖方式对其进行整体结构性更新或者替换,称之为整体结构性修复。其修复对象多为接近或超过20年管龄的老旧破裂钢筋混凝土管道。对于此类修复,施工工序繁多、过程复杂、材料等级和管道接口密封要求高,并且要求修复后形成的内衬管不影响原过水面积和流量。
4.老旧缺陷管道直径大于800mm时,操作人员可进入管内,整平错位缺陷,采用贴壁内衬等人工修复方法。但是,对于直径小于800mm的中小管道修复,操作人员无法进入。如采用树脂原位固化法或者喷涂法话,其结构厚度有限(小于16mm),无法在老旧缺陷管道内壁实现稳定的自持结构层。此类管道的结构性修复一直是业内难题。针对此类口径管道,传统整体结构性修复方法多采用管道内衬加固技术。内衬管材多采用高密度聚乙烯(hdpe)缠绕结构壁管、玻璃钢夹砂管(连续缠绕、离心浇筑、定长缠绕)、树脂混凝土管、给水用聚乙烯(pe)实壁管、给水用聚乙烯(pe)实壁管、ss316材质不锈钢套筒等轻质薄璧短管;内衬方式为多根短管连续跟进串接插入,形成连接整体;接口方式多此采用传统弹性胶圈密封接口。多根内衬短管连接而成的内衬整体对老旧缺陷管道某一部分或者通长整段进行内衬加固,独立承受原管道内、外全部压力。
5.限于传统内衬短管接口方式,穿插方式多采用井内小型液压千斤顶推入顶进,路由遇到中老旧缺陷管道接口错位、脱节部分,顶进会受阻,并且顶进过程无轴向测量控制,偏差较大,无论承插接口、全宽套筒接口,还是熔焊接口,为了保护接口结构,避免形成接口空隙过大造成拉伸出断开,一般多采用顶进式推入。路由当中,如遇到老旧缺陷管道接口错
位、脱节较大部位,内衬管段在此处会受到错台部位的顶力,无法继续顶进。对于内径大于800mm老旧管道,施工人员可以进入对受阻部位进行处理,使其顺接平缓,便于继续推入;对于内径小于800mm情况,限于管径尺寸,施工人员无法进入整平受阻接口,就会造成工期延误,无法正常完成修复。另外,传统顶进施工方法无精准的轴向测量控制手段,老旧管道的设计中轴线和内衬管段中轴线两者之间容易形成水平和高度偏差。此偏差不但造成内衬管道坡向不顺,而且是的内衬管外壁和老旧管道内壁间的环向空隙厚薄不一。顶进完成后,需要对此环向空隙进行水泥砂浆注入时,无法保证均匀填充密实。如无法填充密实,内衬管段运行阶段受压不平衡会造成管道轴向拉伸、变形,无法保证运行质量。
技术实现要素:6.基于此,针对现有技术的不足,本发明的目的在于提供一种用于埋地给排水管道内衬非开挖修复方法、系统。
7.为达到上述目的,本发明采用的技术方案是:
8.一方面,本发明提供一种用于埋地给排水管道内衬非开挖修复方法,对位于两个井室之间的排水管道进行修复,其中,所述两个井室按流体流动方向分为上游井室和下游井室,包括:
9.步骤s1,对上游井室的前一座井室的出水管道以及下游井室后一座井室的进水管道进行临时断水封堵,通过临排设备将上游井室的前一座井室中污泥水引至下游井室后一座井室的后端以在管道修复期间保证上游来水正常顺行;
10.步骤s2,完成上述临时断水措施后,在保证待修复排水管道干管前提下,通过管道机器人对其进行有线闭路电视检测检测,管道机器人上挂载有组成管道检测闭路电视系统的线摄像头及探照灯具,在待修复管道内行进并摄录内壁图像,针对检测破裂、变形、错位、脱节、渗漏、腐蚀结构性缺陷部位进行识别和记录;
11.步骤s3,对检测到管道内壁上有接口错位、脱节渗漏点缺陷处进行预处理;
12.步骤s4,按照《城镇排水管道检测与评估技术规程》,判断整个待修复管道的缺陷种类、数量和等级,以此确定是否需要整体结构性修复;
13.步骤s5,若判断需要结构性修复,在待修复管道中设置内衬管状结构,在设置时,内衬管状结构以若干内衬短管的形式进入待修复管道,内衬短管两个端部分别设有内螺纹和外螺纹,前后内衬短管通过此螺纹快速拧合且通过遇水膨胀环向胶圈以辅助增加止水密封性,螺纹接口位置的壁厚较厚,其环刚度、环柔度不小于待修复管道本体,可实现零渗漏,螺纹连接部位无管径缩小且完全顺直平滑;
14.步骤s6,施工过程中采用全程激光导向轴线测量控制技术,对内衬管道的水平和垂直位移偏差进行严格控制,精准控制管道轴向轨迹以控制内衬管段的路由标高、管道底坡,确保修复后维持顺畅的坡向重力流流态,且内衬短管穿插方式采用“前拉后推”结合施工方法,后端千斤顶油缸提供推力,前端卷扬机软绳提供牵引拉力,在二者合力左右下,可克服沿途接口部位错台阻力,实现顺畅穿插内衬,螺纹的特殊咬合方式会使得“前拉后推”进程中,受后端顶力左右,螺纹连接愈加紧密牢靠,不会发生轴向拉伸脱节;
15.步骤s7,内衬短管顶进到位后,其轴线和待修复管道管中心轴线保持在预设误差范围内,稳管定位后,使内衬新管道外壁和修复老管内壁间具有3~5cm的均匀间隙,便于形
成厚度均匀的环向空隙注浆稳管层,采用分层灌浆方式对新旧管道内外壁环向间隙注浆,环向空隙注浆稳管层采用高强度快干水泥砂浆灌浆料;
16.步骤s8,施工过程中清淤出的管道底泥和施工泥浆水通过车载式通沟污泥一体化处理装置现场原位处理,无需污泥外运并节省通沟水源耗量,车载式通沟污泥一体化处理装置对其进行泥水分离,筛选出砂砾和大颗粒悬浮固体回用做建筑材料,分离上清液回用做通沟清淤和水力清洗用水,处理过程全封闭和零排放,确保全程无温室气体散发和资源化回收利用。
17.在步骤s1中,所述临时断水封堵被配置成在上游井室的前一座井室的出口处及下游井室后一座井室的出口处设置封堵气囊一体化装置,其中,所述封堵气囊一体化装置包括车载式无油螺杆空压机、储气柜、充气软管尼龙绳和带导流孔的封堵气囊供气,所述车载式无油螺杆空压机与所述储气柜连接以提供压缩空气气源,所述储气柜通过充气软管尼龙绳向封堵气囊供气,气囊充气后膨胀,与待修复管道内壁严实贴紧以起到止水密封效果,充气软管尼龙绳自带在线压力表显示工作压力1.0mpa,则停止鼓入压缩空气,完成气囊临时封堵安装后,上游井室的前一座井室的出口通过封堵气囊中间的导流孔仍旧可以过水,其水位也不会过高增加;当操作人员将临排设备设置好之后,将带导流孔的封堵气囊中间的导流孔封闭,从井室返回地面。
18.根据待修复管道封堵内径大小选用不同规格的封堵气囊;当管道内径<φ600mm时,选用泄气状态长度为800~1000mm,直径200~280mm规格气囊;当φ600mm<管道内径<φ1200mm时,选用泄气状态长度为1000~1700mm,直径280~480mm规格气囊;当管道内径>φ1200mm时,选用泄气状态长度为1700~3200mm,直径480~1250mm规格气囊。
19.修复管道过程中,通过车载控制系统可视化平台对前期预处理、轴向定位控制、顶进路由、竣工质量监测实现全程数字化控制,施工期间和验收阶段所有工程材料形成平台大数据,上传到城市公共管线综合信息管理平台,并将此数据记录反映到修复管道检查井井盖镶砌二维码上,管网维保人员通过扫描此二维码,可现场查知管道修复所有历史记录,助力城市公共管网运维数字化转型阶段数字底座建设。
20.步骤s1之后,还包括:完成上述临时断水措施后,采用水力清通法或/和辅以清洗剂清洗对待修复管道进行通沟疏浚和水力清洗,清洗水可来自于离心潜污泵出水,泵送至专用高压清洗车储罐,经由车载高压水泵增压后,通沟衬胶橡皮软管对待修复管道内壁仅高压水射流清洗。
21.在步骤s3中,当检测到管道内壁上错位宽度或脱节高差>3cm时,结合路面探底雷达技术,对道路路面下层土体进行进一步空洞判断检测,若存在较大路面下土体空洞,为防止管道修复完成后残存土体空洞进一步导致沉降,应对接口部位进行局部压密注浆加固预处理,视待修复管道内径大小、错位宽度或脱节高差大小,采用地面注浆或管内注浆方式,采用采用注浆管,局部注浆时采用间隔交错分层注浆,注浆管每次提升50cm,注浆过程中要确保浆液能到位,而不至于外渗和冒溢,注浆完成后,待浆液初凝后再拔出注浆管,同时,对接口缝隙部位进行封堵、修复处理。
22.所述局部压密注浆范围为待修复管道接口前后各1m,两侧1.5m,管顶以上0.5m,管底以下2m,其注浆液采用42.5级水泥,细粉煤灰添加比为50~70%,水玻璃添加比为0.8~1.2%,配成双快水泥,注浆压力为0.2~0.5mpa。
23.所述视待修复管道内径大小、错位宽度或脱节高差大小,采用地面注浆或管内注浆方式,包括:
24.①
当3cm<接口错位宽度或脱节高差<1/2管道壁厚,暨中等结构缺陷情况时:
25.若待修复管道管径>800mm,操作员工进入管内,在缺陷接口部位,采用管内注浆局部土体加固方式,管内向管外四周注浆,形成防水帷幕,对四周土体内的空穴进行填充加固,注浆结束后,接口裂缝部位采用聚氨酯遇水膨胀发泡胶裂缝嵌补局部修复,同时,对管道接口错位或脱节部位内壁整平,便于内衬短管顺利穿插进入;
26.若待修复管道管径<800mm时,在缺陷接口位置处,采用地面注浆局部土体加固方式,地面注浆管的间距布置可控制在接口位置四周50cm范围内;注浆结束后,发生接口裂缝部位采用原位树脂固化内衬局部修复,管道机器人拖入浸润不饱和聚酯树脂+热/光固化添加剂的玻璃纤维布,气囊加压粘贴,热蒸汽或紫外光照射树脂固化,形成局部光滑树脂固化内衬层,固化宽度≮400m,固化厚度3~4mm,目的是修复接口缝隙和光滑缺陷处内壁,并便于内衬短管顺利穿插进入。
27.②
当1/2管道壁厚<接口错位宽度或脱节高差<管道壁厚,暨为严重结构缺陷情况时:
28.若待修复管道管径>800mm,局部土体加固方式:操作人进入管内,在缺陷接口部位,采用管内注浆局部土体加固方式,管内向管外四周注浆,形成防水帷幕,对四周土体内的空穴进行填充加固,注浆结束后,接口裂缝部位采用聚氨酯遇水膨胀发泡胶裂缝嵌补局部修复,同时,对管道接口错位或脱节部位内壁整平,便于内衬短管顺利穿插进入;接口裂缝部位局部修复方式:当人工拖入浸润不饱和聚酯树脂+热/光固化添加剂的玻璃纤维布,气囊加压粘贴,热蒸汽或紫外光照射树脂固化,在原有的聚氨酯遇水膨胀发泡胶裂缝嵌补基础上,增加1~2层树脂固化内衬层,形成局部增强内衬;
29.待修复管道管径>800mm时,人工拖入浸润不饱和聚酯树脂+热/光固化添加剂的玻璃纤维布,气囊加压粘贴,热蒸汽或紫外光照射树脂固化,在原有的聚氨酯遇水膨胀发泡胶裂缝嵌补基础上,增加1~2层树脂固化内衬层形成局部增强内衬;待修复管道管径<800mm时,管道机器人拖入浸润不饱和聚酯树脂+热/光固化添加剂的玻璃纤维布,气囊加压粘贴,热蒸汽或紫外光照射树脂固化,在原有的单层树脂固化内衬基础上,增加单层或双层树脂固化内衬层,形成局部增强内衬,目的也是修复接口缝隙和光滑缺陷处内壁,并便于内衬短管顺利穿插进入。
30.所述内衬短管采用了2种内衬管壁结构形式,当老旧缺陷管道内壁空间有足够内衬管径余量时,采用常规肋高的高密度聚乙烯(hdpe)缠绕结构壁内衬管材;如没有足够内衬管径余量,则采用内外壁包覆增强、薄肋高的高密度聚乙烯(hdpe)缠绕结构壁内衬管材,不过多占据原管道内壁管径,以维持原有过流面积。
31.另一方面,本发明还提供一种实现上述的用于埋地给排水管道内衬非开挖修复方法的系统,包括:
32.临排设备,包括离心潜污泵、水下电缆和临排管,所述离心潜污泵自带泵座放置在上游井室的底板上,所述水下电缆通过挂件或膨胀螺栓临时固定在上游井室的侧壁上,所述离心潜污泵用于通过水下电缆与车载式集控系统兼可视化操作数字化平台电性连接,所述临排管的一端与所述离心潜污泵出口管卡固定连接,另一端延伸出上游井室外且沿着地
面敷设至下游井室后一座井室中,并沿井筒顺下排放至井室中;
33.具有管道检测闭路电视系统的机器人,挂载有线摄像头和探照灯具,在待修复管道内行进并摄录内壁图像并上传车载式集控系统兼可视化操作数字化平台进行存储、处理;
34.封堵气囊一体化装置,包括车载式无油螺杆空压机、储气柜、充气软管尼龙绳和带导流孔的封堵气囊供气,所述车载式无油螺杆空压机与所述储气柜连接以提供压缩空气气源,所述储气柜通过充气软管尼龙绳向所述封堵气囊供气,所述封堵气囊用于设置于待修复管道内壁,当气囊充气后膨胀,与待修复管道内壁严实贴紧以起到止水密封效果,当操作人员将临排设备设置好之后,将带导流孔的封堵气囊中间的导流孔封闭;
35.用于测量轴向和径向跳动量的激光测量仪,用于对内衬管道的水平和垂直位移偏差进行严格控制,精准控制管道轴向轨迹;
36.设置于集装箱式设备车的车载式通沟污泥一体化处理装置,包括衬胶尼龙管、车载汲泥真空抽吸泵、抽吸泵出水管、设备集成水箱、链传动多刮板粗格栅、螺杆式固液分离机、转鼓细格栅、污水排放泵、污水出水管、旋流沉砂器和砂水分离机,所述车载汲泥真空抽吸泵的入口通过衬胶尼龙管真空抽吸污泥,所述车载汲泥真空抽吸泵的出口与所述抽吸泵出水管的一端连接,所述抽吸泵出水管的另一端位于所述链传动多刮板粗格栅上方,经由抽吸泵出水管压力输送至所述链传动多刮板粗格栅对污泥进行粗筛,截留粗筛栅渣通过重力落入所述螺杆式固液分离机中,所述螺杆式固液分离机进行震动截留粗筛栅渣,所述链传动多刮板粗格栅栅后的污水流过所述转鼓细格栅,所述转鼓细格栅对水中含有的细小有机纤维进行精滤,所述转鼓细格栅滤后水经所述污水排放泵增压提升后通过污水出水管排放,所述污水出水管至少具有二路支管,一路滤后水通过回用水阀将滤后水流入设备集成水箱内以使用循环水资源;另一路滤后水通过管道流经沉砂出水阀、旋流沉砂器、砂水分离机以对出水进行细砂回收。
37.较佳地,所述充气软管尼龙绳自带压力表,所述压力表将压力传感信号发送至所述车载式集控装置及可视化操作数字化平台,当压力表显示压缩空气压力小于预设值时,所述车载式集控装置及可视化操作数字化平台控制所述车载式无油螺杆空压机及储气柜进行补气,以保持管道封堵严密。
38.较佳地,所述临排管通过管夹或管抱箍临时固定在井内或地面上。
39.较佳地,所述用于测量轴向和径向跳动量的激光测量仪为奥美加lsg-2030激光测径仪直径宽度跳动测量仪。
40.较佳地,所述离心潜污泵具有浮球开关,所述浮球开关被配置成井室高位开泵和井室低位停泵。
41.较佳地,还包括设置于井室内的液位计,所述液位计用于测量井室内液位变化并反馈至所述车载式集控装置及可视化操作数字化平台,所述车载式集控装置及可视化操作数字化平台与所述离心潜污泵电性连接以根据液位控制离心潜污泵工作频率和转速。
42.由于采用了上述技术方案,本发明获得的有益效果包括:
43.(1)内衬短管优先采用绿色低碳、可回收利用的高密度聚乙烯(hdpe)材质,类型可为缠绕结构壁或实壁短管。采用经特殊设备加工而成快速螺纹接口。内衬施工时,施工场地和环境要求宽松,可带水作业电焊,无井下、熔焊、胶圈拼接等工序,极大缩短施工工期并减
少修复期间断水影响;
44.(2)快速螺纹接口部位壁厚较厚,其环刚度、环柔度不小于管道本体,二者形成整体受力结构。整体刚度大、韧性量、抗轴向拉伸性能好,可独立承受地面刚性载荷压力和内部水压,不依托外围老旧缺陷管道,做到完全意义上的自持受力。该螺纹接口随着顶力增加,越顶越紧,无拉伸松套现象发生。两侧端面设5mm遇水膨胀环向胶圈,辅助增加止水密封性,后期运行期间内可实现全程零渗漏。螺纹连接部位管径,与短管本体完全顺直平滑。不占据老旧缺陷管道内径,不影响修复后过流量。采用了2种内衬管壁结构形式,当老旧缺陷管道内壁空间有足够内衬管径余量时,采用常规肋高的高密度聚乙烯(hdpe)缠绕结构壁内衬管材;如没有足够内衬管径余量,则采用内外壁包覆增强、薄肋高的高密度聚乙烯(hdpe)缠绕结构壁内衬管材,不过多占据原管道内壁管径,以维持原有过流面积;
45.(3)不同于传统内衬短管顶推方式,采用“前拉后推”结合施工方法。后端千斤顶油缸提供推力,前端卷扬机软绳提供牵引拉力。在二者合力作用下,降低沿程阻力并克服老旧缺陷管道接口部位错台障碍,实现顺畅穿插内衬,加快施工速度;
46.(4)采用精准激光导向轴向测量控制技术,精准控制内衬管段路由标高、管道底坡,确保修复后维持顺畅的坡向重力流流态。同时,可靠保证内衬新管道外壁和修复老管内壁间3~5cm的均匀间隙,便于形成厚度均匀的内衬管段稳管注浆层,方便后续注浆操作;
47.(5)改良了内外管壁间隙层的稳管注浆方式。顶进末端设置多个注浆观察孔,采用观察孔注浆观察、分层灌注方式,保持稳管注浆层足够厚度和可靠密实性,进而保证内衬管的位置稳定性和受力传递面均匀,确保其独立承受内外应力,更好发挥其结构自持作用;
48.(6)施工过程中清淤出的管道底泥和施工泥浆水可外运到通沟污泥集中处理处置场,也可以在施工现场进行泥水分离和处理处置。
49.(7)修复过程中,通过车载控制系统可视化平台对前期预处理、轴向定位控制、顶进路由、竣工质量监测实现全程数字化控制。施工期间和验收阶段所有工程材料形成平台大数据,上传到城市公共管线综合信息管理平台,并将此数据记录反映到修复管道检查井井盖镶砌二维码上。管网维保人员通过扫描此二维码,可现场查知管道修复所有历史记录,助力城市公共管网运维数字化转型阶段数字底座建设。
附图说明
50.图1为本发明一种实施例施工流程图。
51.图2为本发明实施例中车载式通沟污泥一体化处理装置组成图。
52.图3为图2所示车载式通沟污泥一体化处理装置的结构示意图。
53.图4为图2所示车载式通沟污泥一体化处理装置的出料口位置图。
具体实施方式
54.本发明属于排水管道非开挖整体结构性修复技术,具体而言,利用多根塑料短管进行穿插内衬,对存在结构性破损的管道进行环向整体、纵向通长,整体范围的非开挖结构性修复施工工艺。
55.以下结合附图和实施例对本发明进一步加以说明。
56.本发明适用于管道内径200mm~1000mm范围内、不同材质的埋地给排水管道整体
结构性修复。以钢砼材质、承插接口、胶圈密封、存在较大结构性缺陷,需要整体结构性修复的圆形埋地排水管道为例,修复方法描述如下:
57.(1)待修复老旧缺陷管道和沿线路由检查井构筑物、修复前临时封堵和临排设备、螺纹接口内衬短管组件、配套装置/设备各部分组成及功能描述
58.(a)待修复老旧缺陷管道和沿线路由检查井构筑物
59.请参阅图1,需要整体结构性修复的管道(1.5)位于上游检查井暨始发井(1)和下游检查井暨接收井(3)之间,管线长度(l)一般在30~200m间。实施结构性修复之前,应通过常规预防性检测和评估手段进行事先判别,管道(1.5)为老旧缺陷,缺陷等级属于整体结构性修复范畴。沿线排查出上游检查井暨始发井(1)前1座检查井(2),下游检查井后1座检查井暨接收井(4),对此2座检查井进行临时断水封堵,以便待修复老旧缺陷管道(1.5)修复作业。检查井(1)~检查井(4)可为砖砌结构,也可为钢砼结构或者塑料一体化结构。上述4座检查井(1~4)各部分组成和附属设施分别为:井室(1.1、2.1、3.1、4.1)、井筒(1.2、2.2、3.2、4.2)、井盖(1.3、2.3、3.3、4.3)、检查井内玻璃钢爬梯(1.4、2.4、3.4、4.4)、检查井日常维修所需移动式1.0t手拉悬链葫芦(1.6)。需要说明的是,上述不同检查井具有相同的组成结构:井室、井筒、井盖、检查井内玻璃钢爬梯,但是是不同的部件。
60.井室(1.1、2.1、3.1、4.1)可为圆形或矩形。φ400mm以下管道检查井,圆形井直径或方形井单边尺寸不小于1200m;φ400mm以上、φ600mm以下管道检查井,圆形井直径或方形井单边尺寸不小于1200m;φ600mm以上、φ1000mm以下管道检查井,圆形井直径或方形井单边尺寸不小于1500m。井筒(1.2、2.2、3.2、4.2)为圆形或矩形,圆形直径或方形单边尺寸不小于1000m。
61.(b)修复前临封和临排设备
62.请参阅图1,修复前临封设施包括设置在检查井(2)出水口暨出水管道(2.5)位置的上游封堵气囊一体化装置(2.6),以及设置在检查井(4)进水口暨进水管道(3.5)位置的下游封堵气囊一体化装置(4.6)。上游封堵气囊一体化装置(2.6)由远程操控带导流孔的封堵气囊(2.6.1)、带有三向阀(充气、补气、泄气)和压力表的充气软管尼龙绳(2.6.2)、车载式无油螺杆空压机及储气柜(2.6.3)、综合设备车(2.6.4)、车载式集控装置兼可视化操作数字化平台(2.7.3)等组成。综合设备车(2.6.4)带有柴油发电机组,同时装载有车载式无油螺杆空压机及储气柜(2.6.3)、车载式集控装置兼可视化操作数字化平台(2.7.3)、液压站(6.7)等设备。配电箱集成设置在车载式集控装置兼可视化操作数字化平台(2.7.3)内,向修复所需机电设备、仪表及自控设备、现场照明灯具等供电。下游封堵气囊一体化装置(4.6)规格、组成与上游封堵气囊一体化装置(2.6)相同,由远程操控带导流孔的封堵气囊(4.6.1)、带有电磁三向阀(充气、补气、泄气)和在线压力表的充气软管尼龙绳(4.6.2)等组成。车载式无油螺杆空压机及储气柜(2.6.3)、综合设备车(2.6.4)、集控装置兼可视化操作数字化平台(2.7.3)为二者共用。
63.远程操控带导流孔的封堵气囊(2.6.1)和(4.6.1)为3层结构,内层为拉伸度较大的低硫化天然橡胶组成,中层为金属经线增强层,外层为高硫化、结构密实、耐磨防滑高硫化天然橡胶密封层,可90
°
折叠放置,工作压力>1.0mpa。视老旧缺陷管道封堵内径大小,选用不同规格的封堵气囊,带导流孔的封堵气囊可以为星辰w43466封堵气囊。管道内径<φ600mm时,选用泄气状态长度为800~1000mm,直径200~280mm规格气囊;φ600mm<管道内
径<φ1200mm时,选用泄气状态长度为1000~1700mm,直径280~480mm规格气囊;管道内径>φ1200mm时,选用泄气状态长度为1700~3200mm,直径480~1250mm规格气囊。车载式无油螺杆空压机及储气柜(2.6.3)提供压缩空气气源,通过充气软管尼龙绳(2.6.2)和充气软管尼龙绳(4.6.2)分别向封堵气囊(2.6.1)和封堵气囊(2.6.1)供气,气囊充气后膨胀,与待修复管道内壁严实贴紧,起到止水密封效果。充气软管尼龙绳(2.6.2)和充气软管尼龙绳(4.6.2)公称直径25~50mm,拉力不小于1t,长度视井深,在9~20m范围内。充气软管尼龙绳(2.6.2)和充气软管尼龙绳(4.6.2)除提供压缩空气外,在封堵完成气囊泄气后,还可将其气囊拉出至地面,起到牵引绳作用。封堵过程中,如发生漏气、气囊压力降低,充气软管尼龙绳(2.6.2)和充气软管尼龙绳(4.6.2)自带的在线压力计,会将压力下降信号传送至集控装置兼可视化操作数字化平台(2.7.3),装置发出指令,自动启动车载式无油螺杆空压机及储气柜(2.6.3)进行补气,补气到额定压力1.0mpa后自动停止。
64.检查井(2)下游出水口封堵后,井内设置临排设备(2.7)。该设施由离心潜污泵(2.7.1)、水下电缆(2.7.2)、临排管(2.7.4)等组成。离心潜污泵(2.7.1)在井室(2.1)内提升进水管(2.5.1)过水流量,在检查井(4)上游进水口完成封堵后,通过临排管(2.7.4)打入到检查井(4)井室中,经由出水管(4.5)至下游管道。在管道修复期间,可保证上游来水正常顺行。离心潜污泵(2.7.1)电力来自于综合设备车(2.6.4)自带柴油发电机组,由集控装置兼可视化操作数字化平台(2.7.3)配电箱供电。水泵采用宽通道、防堵塞、低比转数、调速变频类型,材质为不锈钢。水泵自带浮球开关,根据检查井(2)进水管(2.5.1)来水量大小,通过浮球开关自动启停离心潜污泵(2.7.1),并由集控装置兼可视化操作数字化平台(2.7.3)通过机器学习法优化离心潜污泵(2.7.1)工作频率和转速,保证来水顺畅临排前提下,节省运行电耗。该泵视进水管(2.5.1)管径大小和平时运行水量统计,配置合适流量和扬程。通常配置如下:
65.进水管(2.5.1)管径:φ200mm,配置q=30~40m3/hr,h=10~12m,p=3.0kw移动式变频调速潜污泵
66.进水管(2.5.1)管径:φ300mm,配置q=40~100m3/hr,h=10~12m,p=4.0kw移动式变频调速潜污泵
67.进水管(2.5.1)管径:φ400mm,配置q=100~250m3/hr,h=10~12m,p=11kw移动式变频调速潜污泵
68.进水管(2.5.1)管径:φ500mm,配置q=250~450m3/hr,h=10~12m,p=15kw移动式变频调速潜污泵
69.进水管(2.5.1)管径:φ600mm,配置q=450~600m3/hr,h=10~12m,p=22kw移动式变频调速潜污泵
70.进水管(2.5.1)管径超过φ600mm,或者离心潜污泵(2.7.1)功率超过22kw,在检查井(2)上游多个检查井位置,另设多个临排泵设置点,以分散单点抽排压力。水下电缆(2.7.2)与离心潜污泵(2.7.1)配套,长度为10~20m,采用铠装防水套管形式。临排管(2.7.4)视离心潜污泵(2.7.1)出水口径,匹配合适直径和选择合适材质。临排管(2.7.4)小于200mm直径时,选用衬胶编织网尼龙软管材质;大于200mm直径时,选用卡箍接口钢管材质,管壁厚度>3mm。
71.(c)螺纹接口内衬短管组件
72.请参阅图1,内衬短管(5.1)优先采用绿色低碳、可回收利用的高密度聚乙烯(hdpe)材质,类型可为缠绕结构壁或实壁短管,公称管径在200~1200mm范围。以高密度聚乙烯(hdpe)缠绕结构壁短管组件(5)为例,器材组成包括内衬短管本体(5.1)、安装在第一节短管前部的管头十字撑(5.2)、安装在接收井(3)进口内壁处的管尾十字撑(5.3)、需要整体结构性修复的管道(1.5)内壁和内衬短管本体(5.1)外壁环向空隙之间的注浆稳管层(5.4)、接收井(3)进水口侧注浆观察孔(5.5)、装载内衬短管本体(5.1)的集运卡车(5.6)等。
73.内衬短管本体(5.1)长度视始发井(1)井室(1.1)空间大小,可为200~1000mm范围。类型为高密度聚乙烯(hdpe)缠绕结构壁管,两端分别为平接螺纹内丝插口和平接螺纹外丝承口,环刚度≮8000n/m2,采用市场合格成品管道切削后二次加工成。塑料管道生产车间内,将成品管道切削成200~1000mm范围定长短管,采用两种方式形成两端螺纹接口。一种方式,将切削后定长成品短管离线送入注塑机,机内带有内丝插口和外丝承口的模具,线性低密度聚乙烯(lldpe)热熔树脂颗粒在模具内形成两端螺纹接口,与送入机内的定长短管两端相互熔焊连接形成两端螺纹接口。另一种方式,采用与内衬短管本体(5.1)的高密度聚乙烯(hdpe)材料,挤塑形成定长实壁小短管。分别在机床上车铣形成平接螺纹内丝插口和平接螺纹外丝承口,之后将此两端螺纹与定长成品短管离线熔焊连接,形成两端螺纹接口。
74.采用2种内衬短管管壁结构形式,当老旧缺陷管道内壁空间有足够内衬管径余量时,采用常规肋高高密度聚乙烯(hdpe)缠绕结构壁内衬管材;如没有足够内衬管径余量,则采用内外壁包覆增强、薄肋高高密度聚乙烯(hdpe)缠绕结构壁内衬管材,不过多占据原管道内壁管径,以维持原有过流面积。
75.常规肋高高密度聚乙烯(hdpe)缠绕结构壁内衬管材规格:
76.为环刚度≮8000n/m2的短管,其两端丝口高度约为缠绕结构壁管厚度的1/3。此条件下,公称直径200mm缠绕结构壁管,管壁厚度≮11mm,丝口高度≮3.7mm;公称直径300mm缠绕结构壁管,管壁厚度≮17mm,丝口高度不小于5.7mm;公称直径400mm缠绕结构壁管,管壁厚度≮22mm,丝口高度不小于7.3mm;公称直径600mm缠绕结构壁管,管壁厚度≮32mm,丝口高度≮10.7mm;公称直径800mm缠绕结构壁管,管壁厚度≮47mm,丝口高度不小于15.7mm;公称直径1000mm缠绕结构壁管,管壁厚度≮60mm,丝口高度不小于20.0mm;公称直径1200mm缠绕结构壁管,管壁厚度≮66mm,丝口高度不小于22mm。丝口螺纹间距、螺纹锥形尺寸视管径大小而定。
77.内外壁包覆增强、薄肋高高密度聚乙烯(hdpe)缠绕结构壁内衬管材规格:
78.为环刚度≮12000n/m2的短管,其两端丝口高度约为缠绕结构壁管厚度的1/3。此条件下,公称直径200mm薄肋缠绕结构壁管,管壁厚度≮8mm,丝口高度≮2.7mm;公称直径300mm薄肋缠绕结构壁管,管壁厚度≮13mm,丝口高度不小于4.4mm;公称直径400mm薄肋缠绕结构壁管,管壁厚度≮17mm,丝口高度不小于5.8mm;公称直径600mm薄肋缠绕结构壁管,管壁厚度≮25mm,丝口高度≮8.4mm;公称直径800mm薄肋缠绕结构壁管,管壁厚度≮36mm,丝口高度不小于12mm;公称直径1000mm薄肋缠绕结构壁管,管壁厚度≮41mm,丝口高度不小于13.8mm;公称直径1200mm薄肋缠绕结构壁管,管壁厚度≮48mm,丝口高度不小于16mm。丝口螺纹间距、螺纹锥形尺寸视管径大小而定。
79.第一节内衬短管(5.1)前部安装的管头十字撑(5.3),由4根可伸缩限位的不锈钢管支架(5.3.1)、1块钢化玻璃光靶盘(5.3.2)、4块支架末端支撑橡胶垫块(5.3.3)等组成。不锈钢管支架(5.3.1)通过橡胶垫块(5.3.3)一端固定在内衬短管(5.1)内壁上,一端支撑钢化玻璃光靶盘(5.3.2)。第一节内衬短管(5.1)管中心、钢化玻璃光靶盘(5.3.2)中心调成中对中一致。管头十字撑(5.3)随着后续内衬短管的顺序顶进,向接受井(3)移动。
80.管尾十字撑(5.2)组成与管头十字撑(5.3)类似,也是由可伸缩限位的不锈钢管支架(5.2.1)、钢化玻璃光靶盘(5.2.2)、支架末端支撑橡胶垫块(5.2.3)等组成。管尾钢化玻璃光靶盘(5.2.2)材质不同于管头钢化玻璃光靶盘(5.2.2),其类型为放大棱镜。
81.环向空隙注浆稳管层(5.4)采用高强度快干水泥砂浆灌浆料。以高强度水泥为主要胶凝材料,添加流化促变剂(羧甲基纤维素钠)和其他功能性材料而成。
82.注浆观察孔(5.5)设置在接收井(3)管道末端新旧管道环向空隙处。正视角度看此环向空隙,设置4根直径10~15mm不锈钢短管作为观察孔,分别放置在0点、3点、6点和9点处。
83.集运卡车(5.6)对施工所需内衬短管本体(5.1)进行输运。
84.(d)配套装置/设备
85.请参阅图1-4,配套装置/设备包括设置在始发井(1)内的油压顶进设备(6)、接收井(3)内的软绳牵引拉入装置(7)、始发井(1)内的激光导向轴向测量控制装置(8)以及车载式通沟污泥一体化处理装置(9)组成。
86.油压顶进设备(6)由后靠背钢板(6.1)、液压油缸(6.2)、环形或马蹄形胶合板顶板(6.3)、支撑顶入内衬短管(5.1)所需的导向支撑钢轨(6.4)、钢轨支撑方枕木(6.5)、油管(6.6)以及车载式液压站(6.7)组成。油压顶进设备(6)提供内衬短管顶进推力,主要由液压油缸(6.2)完成。始发井(1)临时断水后,在井内进水侧设置5~15cm厚q235b碳钢材质或ss316不锈钢材质后靠背钢板(6.1)。液压油缸(6.2)固定端通过钢支架锁紧在后靠背钢板(6.1)上,其推力端设3根或4根推力油杆,通过2~5cm厚环形或马蹄形胶合板顶板(6.3)作用于内衬短管(5.1)平接螺纹外丝承口管壁处。环形或马蹄形胶合板顶板(6.3)的内外径与内衬短管(5.1)平接螺纹外丝承口外径、内径、丝口高度吻合贴紧。待顶进的内衬短管(5.1)下方设2根导向支撑钢轨(6.4),钢轨高度为10~20cm,提供顶进支撑力和轴线导向。其下方设若干根钢轨支撑方枕木(6.5),
87.软绳牵引拉入装置(7)包括车载电动卷扬机(7.1)、尼龙宽带牵引绳(7.2)、接收井(3)内安装的下位导向涨紧导向轴(7.3)、地面安装的上位导向涨紧导向轴(7.4)、装载电动卷扬机(7.1)的柴油发电工具车(7.5)等。
88.激光导向轴向测量控制装置(8)由激光经纬仪(8.1)、始发井(1)底板上设置的四角可调水平支撑钢板(8.2)、始发井塔尺(8.3)、接收井塔尺(8.4)等组成。激光导向轴向测量控制装置(8)也可以是用于测量轴向和径向跳动量的激光测量仪,如奥美加lsg-2030激光测径仪直径宽度跳动测量仪。
89.采用车载式通沟污泥一体化处理装置(9),对施工过程中清淤出的管道通沟底泥和施工泥浆水在施工现场进行泥水分离和处理处置。车载式通沟污泥一体化处理装置(9)包括集装箱式设备车(9.1)、汲取通沟污泥衬胶尼龙管(9.2)、车载汲泥真空抽吸泵(9.3)、抽吸泵出水管(9.4)、设备集成水箱(9.5)、水箱内设置链传动多刮板粗格栅(9.6)、螺杆式
固液分离机(9.7)、转鼓细格栅(9.8)、污水排放泵(9.9)、污水出水管(9.10)、旋流沉砂器(9.11)、砂水分离机(9.12)等。
90.集装箱式设备车(9.1)搭载的车载汲泥真空抽吸泵(9.3),通过衬胶尼龙管(9.2)真空抽吸通沟污泥,经由抽吸泵出水管(9.4)压力打入不锈钢材质设备集成水箱(9.5)。首先流经上部安装的100mm间隙不锈钢栅条链传动多刮板粗格栅(9.6),对污泥进行粗筛,截留粗筛栅渣重力落入后续螺杆式固液分离机(9.7),栅后污水进入设备集成水箱(9.5)内。截留粗筛栅渣在螺杆式固液分离机(9.7)内进行震动遴选分离,遴选出的大颗粒轻质纤维类有机物通过无轴螺旋输送机(9.7.2)输送至集装箱式设备车(9.1)外壁。外壁开有粗筛栅渣出料口(9.7.3),大颗粒轻质纤维类有机物初筛栅渣外运至垃圾填埋场卫生填埋。遴选后的过滤污水通过滤后管(9.7.1)也进入设备集成水箱(9.5)内。设备集成水箱(9.5)内混合污水流经内进流5mm间隙的转鼓细格栅(9.8),对水中含有的细小有机纤维进行精滤,滤后栅渣经由无轴螺旋输送机(9.8.1)输送至设备车(9.1)外壁,外壁开有精滤栅渣出料口(9.8.2),细小有机纤维精滤栅渣也外运至垃圾填埋场卫生填埋。转鼓细格栅(9.8)滤后水经由污水排放泵(9.9)增压提升后,通过污水出水管(9.10)排出,污水出水管(9.10)分为3路,1路滤后水通过回用水阀(9.10.1)将滤后水进行回用,对待修复管道(1.5)进行通沟疏浚和水力清洗或者外排如城市污水收集管网;1路滤后水通过沉砂出水阀(9.10.2),经过旋流沉砂器(9.11)对出水进行细砂回收;1路滤后出水通过车内回用水阀(9.10.3),对不锈钢栅条链传动多刮板粗格栅(9.6)、车载螺杆式固液分离机(9.7)、转鼓细格栅(9.8)等筛分设备进行反冲。旋流沉砂器(9.11)通过顶部高速离心分离机(9.11.1)对来水进行砂水分离,分离后的上清液水通过出水管(9.11.2)流入设备集成水箱(9.5),分离后砂砾经由砂水分离机(9.12)输送,脱水后砂砾经由无轴螺旋输送机(9.12.1)至设备车(9.1)外壁,外壁开有砂砾出料口(9.12.2),砂砾回用做建材。
91.整套装置封闭运行,妥善保证现场底泥处理处置安全可靠,同时进行底泥资源化利用,并防止底泥中含有的甲烷等温室气体逸散,做到全过程减污降碳。处理过程中,可喷洒植物提取液除臭剂,对局部异味溢出进行消除。
92.(2)修复方法实施过程
93.(a)预处理—待修复管道前后临时断水措施
94.请参阅图1,管道(1.5)整体结构性修复之前,需要通过临时断水对其进行有线闭路电视检测(cctv)检测,判断其缺陷种类和等级,以此确定是否需要结构性修复。确定进行结构性修复后,对实施修复施工之前,也需要对其进行临时断水,以创造施工条件。临时断水措施包括气囊临时封堵、水泵临时排水和管道临时排放。
95.在上游检查井暨始发井(1)前1座检查井(2)位置,打开井盖(2.3),按照城镇排水管渠维护维护要求,对井筒(2.2)、井室(2.1)进行有限地下空间安全操作准备。安全通风、灯照检测判别操作安全后,操作人员穿戴潜水装备和呼吸面具沿玻璃钢爬梯(2.4)进入井室(2.1),同时拖入封堵气囊(2.6.1)和充气软管尼龙绳(2.6.2)。在出水管道(2.5)管口位置放入带导流孔的封堵气囊(2.6.1),并将充气软管尼龙绳(2.6.2)通过挂件或膨胀螺栓临时固定在井壁上。充气软管尼龙绳(2.6.2)地上与车载式无油螺杆空压机及储气柜(2.6.3)连接,井下与带导流孔的封堵气囊(2.6.1)连接。同样,对接收井(2)的下游检查井(4)同样进行气囊临时封堵。组成包括带导流孔的封堵气囊(4.6.1)和充气软管尼龙绳(4.6.2),安
装和连接方式同上游检查井(2),操作方式同上。2套封堵气囊共用1套车载式无油螺杆空压机及储气柜(2.6.3)。充气软管尼龙绳(4.6.2)地面路由敷设距离较长,采用临时管卡地面固定。通过车载式集控装置兼可视化操作数字化平台(2.7.3),开启车载式无油螺杆空压机及储气柜(2.6.3),向封堵气囊(2.6.1)和封堵气囊(4.6.1)鼓入压缩空气,气囊膨胀后,外壁耐磨防滑天然橡胶密封层与原管道内壁牢牢贴紧,充气软管尼龙绳(2.6.2)和充气软管尼龙绳(4.6.2)自带在线压力表显示工作压力1.0mpa,则停止鼓入压缩空气。完成气囊临时封堵安装后,检查井(2)通过封堵气囊(2.6.1)中间的导流孔仍旧可以过水,经由检查井(2)出水管道(2.5)、上游检查井暨始发井(1)、需要整体结构性修复的管道(1.5)、下游检查井暨接收井(3)、接收井(3)出水管道暨检查井(4)进水管道(3.5)、检查井(4)正常排放。井室(2.1)内水位也不会过高增加。
96.从地面放入离心潜污泵(2.7.1)、水下电缆(2.7.2)和临排管(2.7.4)。离心潜污泵(2.7.1)由设备自带泵座放置在井室(2.1)底板上,水下电缆(2.7.2)通过挂件或膨胀螺栓临时固定在井壁上。水下电缆(2.7.2)一端与离心潜污泵(2.7.1)连接,另一端与车载式集控装置兼可视化操作数字化平台(2.7.3)连接。临排管(2.7.4)一端与离心潜污泵(2.7.1)出口固定连接,另一端沿着地面敷设至下游检查井暨接收井(2)后1座检查井(4)井口位置,沿井筒(4.2)顺下,排放至井室(4.1)中。临排管(2.7.4)小于200mm直径时,选用衬胶编织网尼龙软管材质,井内和地面上管夹临时固定;大于200mm直径时,选择卡箍接口钢管材质,管壁厚度>3mm,与井壁间管抱箍固定,地面路由采用管卡固定。上述步骤为水泵临时排水和管道临时排放安装。
97.操作人员对上述步骤检查无误后,将带导流孔的封堵气囊(2.6.1)和封堵气囊(4.6.1)中间的导流孔封闭,从井室(2.1)和井室(4.1)返回地面。车载式集控装置兼可视化操作数字化平台(2.7.3)开启离心潜污泵(2.7.1),对检查井(2)上游管道(2.5.1)来水进行临时提升,超越始发井(1)和接收井(2),直接流入检查井(4)。
98.期间,充气软管尼龙绳(2.6.2)和充气软管尼龙绳(4.6.2)自带有在线压力表,如显示压缩空气压力小于1.0mpa时,压力传感信号发送至车载式集控装置兼可视化操作数字化平台(2.7.3),车载式集控装置及可视化操作数字化平台可为服务器,尤其自动启动车载式无油螺杆空压机及储气柜(2.6.3)进行补气,以保持管道封堵严密。离心潜污泵(2.7.1)自带浮球开关,根据检查井(2)进水管(2.5.1)来水量大小,通过高位开泵和低位停泵的浮球开关设置,自动启停离心潜污泵(2.7.1)。
99.临排设备还包括设置于井室内的液位计,所述液位计用于测量井室内液位变化并反馈至所述车载式集控装置及可视化操作数字化平台,所述车载式集控装置及可视化操作数字化平台与所述离心潜污泵信号连接以根据液位控制离心潜污泵工作频率和转速。集控装置兼可视化操作数字化平台(2.7.3)也通过机器学习法优化离心潜污泵(2.7.1)工作频率和转速,在保证来水安全、顺畅临排前提下,节省施工期间临泵运行电耗。
100.(b)预处理—待修复管道通沟疏浚和水力清洗
101.完成上述临时断水措施后,采用水力清通法对待修复管道(1.5)进行通沟疏浚和水力清洗。清洗水可来自于离心潜污泵(2.7.1)出水,泵送至专用高压清洗车储罐,经由车载高压水泵增压后,通沟衬胶橡皮软管对待修复管道(1.5)内壁仅高压水射流清洗。必要时辅以清洗剂。通沟和清洗后,原管道内无沉积物、垃圾及其它障碍物,管道内无影响施工的
积水,管道内表面洁净,无附着物、尖锐毛刺和突起。
102.清洗产生的污水也抽吸至车载式通沟污泥一体化处理装置(9)集中处理。清洗时应避免高压水射流对管道造成损伤和破坏。
103.(c)预处理—待修复管道结构性缺陷有线闭路电视检测(cctv)
104.完成上述临时断水措施后,在保证待修复管道(1.5)干管前提下,对其进行有线闭路电视检测(cctv)检测。管道机器人上挂载有线摄像头和探照灯具,组成管道检测闭路电视装置,在待修复管道内行进并摄录内壁图像,主要针对检测破裂、变形、错位、脱节、渗漏、腐蚀等结构性缺陷部门进行识别和记录。采用2种方式进行检测:
105.方式1:图像人工识别。管道机器人将行进路由中的管内壁摄录图像传送至集控装置兼可视化操作数字化平台(2.7.3),操作人员人工标定缺陷位置(里程桩号)并识别缺陷类型、数量;
106.方式2:图像智能识别。集控装置兼可视化操作数字化平台(2.7.3)将管道机器人上传图像,利用平台大数据库积累的缺陷图库对其进行智能识别,判断出缺陷种类并标注发生位置、数量;需要说明的是,图像智能识别技术为现有技术。
107.着重对直线段变形和接口脱节位置进行尺寸测量,尤其是接口错位宽度或者脱节高差>3cm部位。对于管径≥800mm管道,操作人员可进入管道进行变形和接口脱节缩径位置内径测量;对于管径<800mm管道,采用cctv图像尺寸识别测量。目的是合理确定下一步内衬管道的外壁管径以及接口错位处理方式。
108.完成上述两种方式结构性缺陷检测后,按照《城镇排水管道检测与评估技术规程》,判断其缺陷种类、数量和等级,以此确定是否需要整体结构性修复。
109.(d)预处理—待修复管道内壁预处理周围土体加固以及接口错位、脱节缝隙处理
110.如检测到管道内壁上有接口错位、脱节渗漏点,尤其当错位宽度或脱节高差>3cm时,则管道周边土体会存在地下水渗入管内引起土体空洞风险,进而会造成路面坍陷。这时,可结合路面探底雷达技术(gpr),对道路路面下层土体进行进一步空洞判断检测。如存在较大路面下土体空洞,为防止管道修复完成后残存土体空洞进一步导致沉降,应对接口部位进行局部压密注浆加固预处理。视待修复管道内径大小、错位宽度或脱节高差大小,采用地面注浆或管内注浆方式。压密注浆范围为待修复管道接口前后各1m,两侧1.5m,管顶以上0.5m,管底以下2m。注浆液采用42.5级水泥,细粉煤灰添加比为50~70%,水玻璃添加比为0.8~1.2%,配成双快水泥。注浆压力为0.2~0.5mpa,采用注浆管。局部注浆时采用间隔交错分层注浆,注浆管每次提升50cm,注浆过程中要确保浆液能到位,而不至于外渗和冒溢。注浆完成后,待浆液初凝后再拔出注浆管,并及时密封注浆孔,确保注浆孔不渗漏。同时,对接口缝隙部位进行封堵、修复处理。具体处理方式分为如下两种情况:
111.①
3cm<接口错位宽度或脱节高差<1/2管道壁厚,暨中等结构缺陷情况
112.待修复管道管径>800mm时,操作人进入管内,在缺陷接口部位,采用管内注浆局部土体加固方式。管内向管外四周注浆,形成防水帷幕,对四周土体内的空穴进行填充加固。注浆结束后,接口裂缝部位采用聚氨酯遇水膨胀发泡胶裂缝嵌补局部修复。同时,对管道接口错位或脱节部位内壁整平,便于内衬短管顺利穿插进入。待修复管道管径<800mm时,在缺陷接口里程桩号处,采用地面注浆局部土体加固方式。地面注浆管的间距布置可控制在接口位置四周50cm范围内。注浆结束后,发生接口裂缝部位采用原位树脂固化内衬局
部修复。管道机器人拖入浸润不饱和聚酯树脂+热/光固化添加剂的玻璃纤维布,气囊加压粘贴,热蒸汽或紫外光照射树脂固化,形成局部光滑树脂固化内衬层。固化宽度≮400m,固化厚度3~4mm。目的是修复接口缝隙和光滑缺陷处内壁,并便于内衬短管顺利穿插进入。
113.②
1/2管道壁厚<接口错位宽度或脱节高差<1.0管道壁厚,暨严重结构缺陷情况
114.局部土体加固方式同情况
①
。接口裂缝部位局部修复方式,在情况
①
基础上,接口缺陷部位增加1~2层树脂固化内衬层,形成增强内衬。待修复管道管径>800mm时,人工拖入浸润不饱和聚酯树脂+热/光固化添加剂的玻璃纤维布,气囊加压粘贴,热蒸汽或紫外光照射树脂固化,在原有的聚氨酯遇水膨胀发泡胶裂缝嵌补基础上,增加1~2层树脂固化内衬层(单层厚度为3~4mm,双层厚度为6~8mm),形成局部增强内衬;待修复管道管径<800mm时,管道机器人拖入浸润不饱和聚酯树脂+热/光固化添加剂的玻璃纤维布,气囊加压粘贴,热蒸汽或紫外光照射树脂固化,在原有的单层树脂固化内衬基础上,增加单层或双层树脂固化内衬层(单层厚度为3~4mm,双层厚度为6~8mm),形成局部增强内衬。目的也是修复接口缝隙和光滑缺陷处内壁,并便于内衬短管顺利穿插进入。
115.(e)内衬短管井内连接
116.预处理工序完成后,通过移动式1.0t手拉悬链葫芦(1.6),从集运卡车(5.6)上悬吊内衬短管本体(5.1)入上游检查井暨始发井(1)。视井室(1.1)操作空间大小,内衬短管(5.1)管径在200~1200mm范围,单根长度范围为200~1000mm。待修复管道内径宜为200~1200mm范围,在接口错位、脱节缝隙处理工序完成后,根据有线闭路电视检测(cctv)复测结果,找出待修复管道最小内径部位,按此最小内径缩小3cm配内衬短管(5.1)。如最小内径部位缩径小于原管道内径10%,采用常规肋高高密度聚乙烯(hdpe)缠绕结构壁内衬管,环刚度≮8000n/m2;如最小内径部位缩径大于原管道内径10%,采用内外壁包覆增强、薄肋高高密度聚乙烯(hdpe)缠绕结构壁内衬管,环刚度≮12000n/m2。
117.在井室(1.1)内,内衬短管(5.1)按上游外丝承口、下游内丝插口方向快速顺序螺纹连接,并送入待修复管道内壁。螺纹部位可采用不含磷酸盐的洗涤精溶液润滑,以便于拧紧。首发第一节管段前部安装管头十字撑(5.3),末端最后一节管段尾部安装管尾十字撑(5.2)。管头十字撑(5.2)随着顶进进程,一直行进到接收井(3)。管尾十字撑(5.2)随着本节管段顶入后,随即拆卸下来,改设在下一节管段尾部,随着管段不断顶入,此拆卸过程轮换进行。
118.为便于管内传插送入和进程导向,内衬短管(5.1)底部可现场熔焊高度为1~2cm的高密度聚乙烯(hdpe)导轨,导轨沿管道长度方向间隔分布。单根或多根内衬短管(5.1)快速螺纹连接后,除安装管尾十字撑(5.3)外,在最后一节内衬短管(5.1)尾部外丝承口处,放入2~5cm厚环形或马蹄形胶合板顶板(6.3)。液压油缸作用于(6.2)推力端设3根或4根推力油杆作用于胶合板顶板(6.3),将快速螺纹连接后的内衬短管(5.1),沿管底导轨定向推入待修复管内。
119.(f)内衬短管后端顶入和前端牵引(前拉后推)
120.多根连接后的内衬短管(5.1)顶进推入过程中,为更好调节轨迹姿态并减少顶力,在首发第一节管段前部安装管头十字撑(5.2)中心处连接尼龙宽带牵引绳(7.2),形成“前拉后推”方式,以减少顶入摩擦阻力。尼龙宽带牵引绳(7.2)由地面电动卷扬机(7.1)提供拉力,经由下位导向涨紧导向轴(7.3)和上位导向涨紧导向轴(7.4)传力轴力,尼龙宽带牵引
绳(7.2)始终保持涨紧状态,由导向轴(7.4)和(7.4)调节涨紧力。地面电动卷扬机(7.1)提供拉力转速和井内液压油缸作用于(6.2)推速保持一致,由车载式集控装置兼可视化操作数字化平台(2.7.3)统一控制。
121.(g)激光导向轴向测量控制
122.经由地面高程装置引入绝对标高至井室(1.1)底板,测得底板绝对标高。经由始发井塔尺(8.3),通过钢卷尺测得井室(1.1)入口原管道中心绝对标高。同理,经由接收井塔尺(8.4),测得井室(3.1)出口原管道中心绝对标高,此两点连接线即为待修复管道(1.5)管中心轴线。激光经纬仪(8.1)发出一束与待修复管道(1.5)管中心轴向一致的激光轴线,由近及远,分别投射到管尾钢化玻璃光靶盘(5.2.2)和管头钢化玻璃光靶盘(5.3.2)上,并形成光点,光点与靶盘十字中心的距离(水平方向与垂直方向)即为顶进轴向偏差。每一节管段的顶进过程中,随顶随测,随测随纠。采用动态测量方式,不断复核顶进轴线与静态激光轴线之间偏差。跟踪光靶盘十字中心与激光光点之间的水平和竖直偏移,通过光靶盘钢化玻璃的棱镜结构放大图像,供操作人员清晰观测此偏差。如有偏差,则通过后端液压油缸作用于(6.2)和前端尼龙宽带牵引绳(7.2),相互配合进行纠偏和校正。保证内衬短管(5.1)和待修复管道(1.5)之间的中心轴向误差在
±
2mm内。
123.(h)进程受阻的处理方式
124.进程中如遇到错位、脱节较大的部位,错台高差>5cm,会发生顶进受阻。通过前端尼龙宽带牵引绳(7.2)抬高或降低管节,错开此高低位置。待修复管道(1.5)≥800mm时,回缩一节内衬管道,操作人员进入管内对受阻部位进行不含磷酸盐的洗涤液润滑,方便继续顶入。
125.(i)内衬管短定位后的内外壁环向间隙注浆
126.内衬短管(5.1)顶进到位后,其轴线和待修复管道(1.5)管中心轴线保持在合理误差范围内,稳管定位后,即可保证内衬新管道外壁和修复老管内壁间3~5cm的均匀间隙,便于形成厚度均匀的环向空隙注浆稳管层(5.4)。
127.采用分层灌浆方式对新旧管道内外壁环向间隙注浆。环向空隙注浆稳管层(5.4)采用高强度快干水泥砂浆灌浆料。以高强度水泥为主要胶凝材料,添加流化促变剂(羧甲基纤维素钠)和其他功能性材料而成,形成快干快硬注浆料。该浆料具有良好的流动性,可在注浆层内(5.4)内快速流动,不产生灌浆死角。干化和硬化速度快,物理力学指标优异。具有良好的抗压和抗弯性能,保证内衬短管(5.1)连接后形成的内衬长管位置稳定,不发生偏移,完全能够承受上部地面载荷和原管道下部基础完全变形,不产生不均匀沉降。主要性能指标如下:
128.抗压强度(mpa):干化1天后≥20;干化3天后≥40;干化28天后≥60;
129.抗弯/折强度(mpa):干化1天后≥3;干化3天后≥5;干化28天后≥10;
130.竖向膨胀率(%):3hr=0.1~3.5;24hr和3hr之间的膨胀值偏差=0.02~0.5
131.注浆观察孔(5.5)设置在接收井井室(3.1)出口侧管道末端新旧管道环向空隙处。正视角度看此环向空隙,设置4根直径10~15mm不锈钢短管作为观察孔,分别放置在0点、3点、6点和9点处。注浆观察孔(5.5)的不锈钢短管用环形钢板封闭固定,环形钢板搭接固定在市室(3.1)内壁上。
132.始发井井室(1.1)入口侧,待修复管道(1.5)与内衬短管(5.1)之间的环向缝隙用
环形钢板封闭,此钢板上开若干注浆孔。将接收井井室(3.1)内的4根观察孔打开,始发井井室(1.1)注浆孔泥浆泵打入高强度快干水泥砂浆灌浆料,注浆压力不超过0.2mpa。观察到6点方向观察孔出浆时,即可验证环向空隙注浆稳管层(5.4)路由顺畅,排气畅通,关闭此孔;继续注浆,待3点和9点方向观察孔出浆时,停止注浆,关闭此两孔,等待浆料在间隙中沉淀凝结,时间约30min~1.0hr,以减小对内衬管的浮力并排出之前注浆水分;继续注浆,带顶部0点方向观察孔出浆时,停止注浆,关闭此孔,等待浆料最后凝结,
133.待修复管道(1.5)管径>1000mm,亦可采用内衬短管(5.1)内顶部开孔进行注浆,孔距2m左右,逐孔注入。
134.(j)修复管道前后端口处理
135.环向空隙注浆完成后,对始发井井室(1.1)入口侧和接收井井室(3.1)出口侧设置的环形封闭钢板拆除,缝隙间填充双组分聚硫密封胶,嵌实密封。
136.(k)内衬管道渗水检测和闭水试验
137.修复完成后,进行有线闭路电视检测(cctv)内衬管道内壁质量检测,观察有无渗水部位。
138.内衬管道闭水试验采用补水法进行,试验程序按现行国家标准《给水排水管道工程施工及验收规范》规定执行,单位延米24hr内渗水量(l/24hr.m)不大于0.0046d(d为内衬管道内径)。
139.(l)绿色低碳修复材料选用、“三废”处理处置(通沟污泥)、减污降碳措施(资源化回收利用)
140.内衬短管优先采用绿色低碳、可回收利用的高密度聚乙烯(hdpe)材质,类型可为缠绕结构壁或实壁短管。
141.(m)修复过程中数字化管理手段、大数据形成
142.修复过程中,通过车载式集控装置兼可视化操作数字化平台(2.7.3)对前期预处理、轴线定位控制、顶进路由、竣工质量监测实现全程数字化控制。施工期间和验收阶段所有工程材料形成平台大数据,上传到城市公共管线综合信息管理平台,并将此数据记录反映到修复管道检查井井盖镶砌二维码上。信息二维码反映信息如下:
143.设施名称:排水管道整体结构性修复设施编号:
144.排水体制(分流/合流):
ꢀꢀꢀꢀꢀꢀꢀꢀꢀꢀꢀꢀꢀꢀꢀꢀ
所属排水装置:
145.输送介质(污水/雨水/合流):
ꢀꢀꢀꢀꢀꢀꢀꢀꢀꢀꢀ
地面标高:井深(m):
146.原管道属性:
147.管径:管材:管中心标高:
148.内衬管道属性:
149.管径:管材:管中心标高:
150.修复方法:修复时间:修复工艺:过程中三废处理处置:
151.工程建成时间/建设单位/设计单位/施工单位/管理养护单位::
152.日常养护记录:日常养护照片时间及照片记录:其他:
153.管网维保人员通过扫描此二维码,可现场查知管道修复所有历史记录。
154.由于采用了上述施工方法,其有益效果包括:
155.(1)内衬短管优先采用绿色低碳、可回收利用的高密度聚乙烯(hdpe)材质,类型可
为缠绕结构壁或实壁短管。采用经特殊设备加工而成快速螺纹接口。内衬施工时,施工场地和环境要求宽松,可带水作业,无井下电焊、熔焊、胶圈拼接等工序,极大缩短施工工期并减少修复期间断水影响;
156.(2)快速螺纹接口部位壁厚较厚,其环刚度、环柔度不小于管道本体,二者形成整体受力结构。整体刚度大、韧性量、抗轴向拉伸性能好,可独立承受地面刚性载荷压力和内部水压,不依托外围老旧缺陷管道,做到完全意义上的自持受力。该螺纹接口随着顶力增加,越顶越紧,无拉伸松套现象发生。两侧端面设5mm遇水膨胀环向胶圈,辅助增加止水密封性,后期运行期间内可实现全程零渗漏。螺纹连接部位管径,与短管本体完全顺直平滑。不占据老旧缺陷管道内径,不影响修复后过流量。采用了2种内衬管壁结构形式,当老旧缺陷管道内壁空间有足够内衬管径余量时,采用常规肋高的高密度聚乙烯(hdpe)缠绕结构壁内衬管材;如没有足够内衬管径余量,则采用内外壁包覆增强、薄肋高的高密度聚乙烯(hdpe)缠绕结构壁内衬管材,不过多占据原管道内壁管径,以维持原有过流面积;
157.(3)不同于传统内衬短管顶推方式,采用“前拉后推”结合施工方法。后端千斤顶油缸提供推力,前端卷扬机软绳提供牵引拉力。在二者合力作用下,降低沿程阻力并克服老旧缺陷管道接口部位错台障碍,实现顺畅穿插内衬,加快施工速度;
158.(4)采用精准激光导向轴向测量控制技术,精准控制内衬管段路由标高、管道底坡,确保修复后维持顺畅的坡向重力流流态。同时,可靠保证内衬新管道外壁和修复老管内壁间3~5cm的均匀间隙,便于形成厚度均匀的内衬管段稳管注浆层,方便后续注浆操作;
159.(5)改良了内外管壁间隙层的稳管注浆方式。顶进末端设置多个注浆观察孔,采用观察孔注浆观察、分层灌注方式,保持稳管注浆层足够厚度和可靠密实性,进而保证内衬管的位置稳定性和受力传递面均匀,确保其独立承受内外应力,更好发挥其结构自持作用;
160.(6)施工过程中清淤出的管道底泥和施工泥浆水可外运到通沟污泥集中处理处置场,也可以在施工现场进行泥水分离和处理处置。
161.(7)修复过程中,通过车载控制装置可视化平台对前期预处理、轴向定位控制、顶进路由、竣工质量监测实现全程数字化控制。施工期间和验收阶段所有工程材料形成平台大数据,上传到城市公共管线综合信息管理平台,并将此数据记录反映到修复管道检查井井盖镶砌二维码上。管网维保人员通过扫描此二维码,可现场查知管道修复所有历史记录,助力城市公共管网运维数字化转型阶段数字底座建设。
162.上述相关说明以及对实施例的描述是为便于该技术领域的普通技术人员能理解和应用本发明。熟悉本领域技术的人员显然可以容易地对这些内容做出各种修改,并把在此说明的一般原理应用到其他实施例中而不必经过创造性的劳动。因此,本发明不限于上述相关说明以及对实施例的描述,本领域的技术人员根据本发明的揭示,不脱离本发明范畴所做出的改进和修改都应该在本发明的保护范围之内。