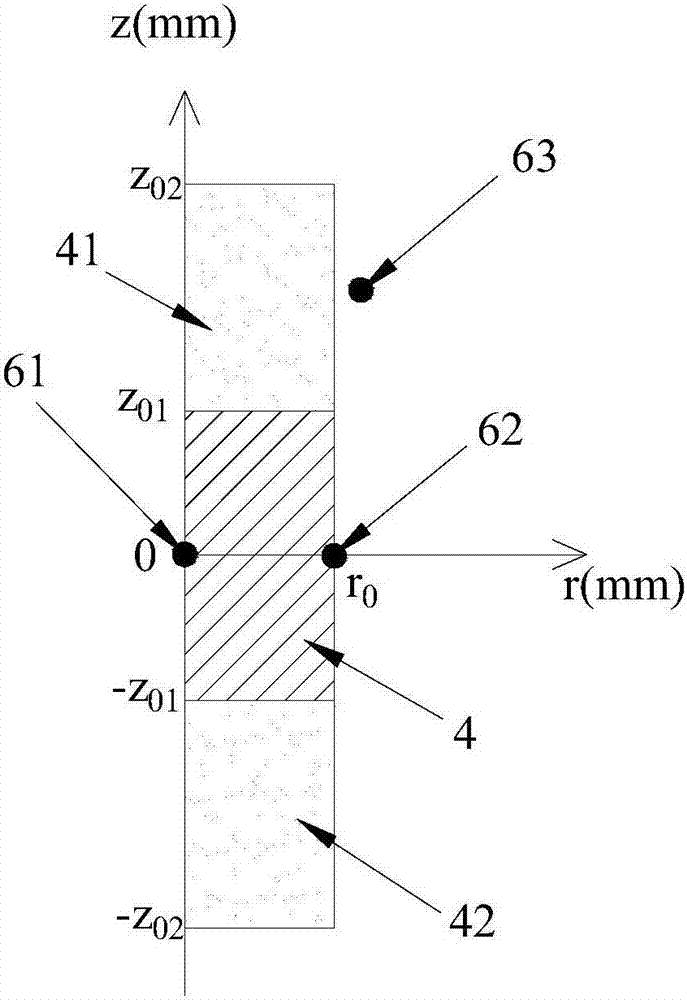
本发明涉及一种高压条件下岩石热物性测试系统,属于岩石热物性测试技术领域。
背景技术:地球内部岩层热物性,是地球内部热结构、热演化及地球动力学研究中最基础的物性参数。而不同的温、压条件下,岩石热物性存在差异。因此,深入开展不同围压条件下岩石热物性测试研究具有非常重要的意义。目前,已有的高压条件下岩石热物性测试方法和系统,是通过将热物性测试探头(包括加热源和温度传感器)与岩石样品事先组装好,一同安置在耐压罐内。启动加压泵,将耐压罐内围压加到预定压力后,维持一段时间,待整套系统的温度达到平衡后,再开启热物性测试系统进行电加热,同时监测岩石内部温度变化,从而完成不同围压条件下的热物性测试。上述现有的测试方法与系统,必需主动进行电加热(比如以恒定电流通过加热丝)作为瞬态法热物性测试所需的“热源”。因此,加热源和温度传感器必需同时安置在岩石内部,使得测试系统相对较为复杂。而且热物性参数测试对环境温度的恒温性要求特别高,而实验室条件下进行热物性测试过程中,测试系统通常直接与空气接触,很难在一个相对恒温的环境下进行测试。由于环境温度的波动难以控制,导致测试结果往往受到较大影响。这种测试方法与技术,必需主动进行电加热(比如以恒定电流通过加热丝)作为瞬态法热物性测试所需的“热源”。而我们的实验结果表明:地壳常见岩石的应力-温度响应系数(ΔT/Δσ)比较小(只有2~6mK/MPa),而传压介质(比如硅油)的应力-温度响应系数则高达138.74mK/MPa,比地壳常见岩石的应力-温度响应系数高2个数量级。因此,围压瞬间升高后,岩石样品与传压介质之间就存在温差。因此,本发明通过实时监测耐压罐内围压瞬间升高过程中岩石样品表面、中心温和传压介质的温度变化,结合有限元数值反演方法,即可获得高压条件下岩石样品的热物性参数(热导率/thermalconductivity、热扩散率/thermaldiffusivitiy、及体积热容/volumetricheatcapacity)。
技术实现要素:为克服现有技术的不足,本发明的目的之一在于提供一种高压条件下无需电加热“热源”的岩石热物性测试系统,其只在岩石样品中心、表面及传压介质中各安置一个温度传感器,通过快速打开排泄阀来实现岩石样品的瞬间加载,并监测围压瞬间升高过程中岩石样品中心、表面级传压介质的温度变化,利用建立的有限元数值反演模型,结合全局优化方法,即可获得高压条件下岩石样品的热物性参数。从而实现了无电加热“热源”的瞬态热物性测试,大大简化了高压条件下岩石热物性测试系统及其操作程序。为实现上述目的,本发明采取的技术方案是:一种高压条件下岩石热物性测试系统,其包括二个耐压罐、高压泵、温度监测模块以及围压监测模块,其中,第一耐压罐中内形成第一空腔,第二耐压罐内形成一第二空腔,所述第一空腔和第二空腔内均充满传压介质,向第一耐压罐中输送传压介质的高压泵通过第一连通管道与第一空腔相连,在所述第一连通管道上安装有第一排泄阀和第一压力传感器;在所述第二空腔内安装一岩石样品,所述岩石样品的中心及外表面以及第二空腔的传压介质中分别安装有第一温度传感器、第二温度传感器和第三温度传感器,所述第一空腔和第二空腔之间通过第二连通管道相连通,在所述第二连通管道上安装有第二排泄阀和第二压力传感器,所述第二空腔还与一第三排泄阀相连通;所述第一温度传感器、第二温度传感器、第三温度传感器的输出端均与温度监测模块的输入端相连,所述第一压力传感器和第二压力传感器的输出端均与围压监测模块的输入端相连。所述岩石样品的外表面设置有用于对岩石样品进行封装的橡胶套,所述岩石样品的上、下两端均通过硬质硅胶密封。所述岩石样品为圆柱状。所述传压介质为硅油,当然也可以是植物油、去离子水等。本发明的另一目的在于提供一种无需电加热“热源”的高压条件下岩石热物性测试方法,其只在岩石样品中心、表面及第二耐压灌内传压介质中各安置一个温度传感器,通过快速打开排泄阀来实现岩石样品的瞬间加载,并监测围压瞬间升高过程中岩石样品中心、表面级传压介质的温度变化,利用建立的有限元数值反演模型,结合全局优化方法,即可获得高压条件下岩石样品的热物性参数。从而实现了无电加热“热源”的瞬态热物性测试,大大简化了高压条件下岩石热物性测试系统及其操作程序。为实现上述目的,本发明采取的技术方案是:一种高压条件下岩石热物性测试方法,其包括以下步骤:步骤1、将第一温度传感器和第二温度传感器安置在制备好的圆柱状岩石样品的中心和外表面,采用橡胶套将岩石样品进行水密封装,并在岩石样品的上下两端通过硬质硅胶密封,形成岩石样品组件;步骤2、将岩石样品组件、第三温度传感器放入第二耐压罐中,第二耐压罐充满传压介质后再进行密封,同时将安装有第一排泄阀和第一压力传感器的第一连通管道连接高压泵和第一耐压罐,将安装有第二排泄阀和第二压力传感器的第二连通管道连接第一耐压罐和第二耐压罐,在第二耐压罐上安装第三排泄阀,然后将第一温度传感器、第二温度传感器、第三温度传感器连接至温度监测模块,将第一压力传感器和第二压力传感器连接到围压监测模块,从而组装形成岩石热物性测试系统;开启温度监测模块和围压监测模块,开始温度和围压监测;步骤3、只打开第一排泄阀,关闭第二排泄阀和第三排泄阀,开启高压泵,将第一耐压罐中的围压升至预定压力;步骤4、瞬间加载:待整套岩石热物性测试系统处于平衡时,关闭第一排泄阀,第三排泄阀保持关闭,快速打开第二排泄阀,从而实现第二耐压罐瞬间增压;步骤5、根据温度监测模块实时监测的第一温度传感器、第二温度传感器以及第三温度传感器的温度变化和围压监测模块实时监测的第二压力传感器的围压变化,通过有限元数值模型,反演获得任意围压下岩石样品的热物性参数。所述步骤5包括以下步骤:步骤51、以圆柱状岩石样品的中心为圆点,在以圆柱状岩石样品的径向和轴向形成的柱坐标系统内基于热传导微分方程建立有限元数值模型;步骤52、设岩石样品的热导率和体积热容分别为λ和(ρc),地壳常见岩石的热导率及体积热容的范围分别为0.5~6.0W·m-1·K-1、0.5×106~5.0×106J·m-3·K-1,对求解区域中的两参数中λ、(ρc)都进行m等份剖分,获得初始的(m+1)×(m+1)个网格节点(λi,(ρc)j),其中i,j=1,2,3,...,m;步骤53、将每个网格节点(λi,(ρc)j)输入已建立的有限元数值模型中,以快速加载过程中实时监测获取的岩石样品表面的温度变化T02(t)和传压介质温度变化T03(t)作为边界条件,模拟计算(λ,(ρc))=(λi,(ρc)j)时,岩石样品中心处的温度变化,记为步骤54、利用最小二乘法,对所述有限元数值模型计算获得的与岩石样品中心实测的温度变化T01(t)进行线性拟合:求解该拟合直线斜率Ki,j和相关系数Ri,j,其中相关系数计算表达式如下步骤55、定义目标函数为F(λi,(ρc)j)=1.0-(Ri,j)2(4)并求解各网格点处的目标函数值F(λi,(ρc)j);其中:n为采样总次数,tk为第k次采样的时刻,T01(tk)为瞬间加载后tk时刻第一温度传感器采集的温度变化,1≤k≤n;步骤56、找出目标函数值最小的网格点,如果ε为判断是否满足求解要求而设定的阈值,则接受为所需要求解的岩石样品的热导率和体积热容(λ,(ρc)),否则,将以为中心的邻域为求解区域,将网格加密,返回到步骤53,直到满足为止,从而解算得到岩石样品的热导率和体积热容步骤57、最后根据热导率λ、体积热容(ρc)及热扩散率κ之间的关系式计算得到岩石样品的热扩散率。所述步骤51中,柱坐标系统下的热传导微分方程表达为其初始条件为T(r,z,0)=0,r≤r0,|z|≤z02)(7)边界条件由岩石热物性测试系统监测的样品表面温度变化T02(t)和传压介质温度变化T03(t)进行如下约束其中γ为各种介质的绝热应力变化的温度响应系数,A是由于围压变化导致温度变化所对应的热源,r0为岩石样品的半径,z01为圆柱状岩石样品顶面或底面到岩石样品中心圆柱面的垂直距离,z02为封装后的圆柱状岩石样品组件顶面或底面到岩石样品中心圆柱面的垂直距离。所述岩石样品中心实测的温度变化T01(t),岩石样品表面温度变化T02(t)和传压介质温度变化T03(t)为各时刻实测温度与瞬间加载时的温度差,即:T01(t)=T1(t)-T1(0)T02(t)=T2(t)-T2(0)T03(t)=T3(t)-T3(0)其中,T1(t)、T2(t)、T3(t)分别是瞬间加载后t时刻时第一温度传感器、第二温度传感器和第三温度传感器的实测温度,通过步骤5测得,T1(0)、T2(0)、T3(0)分别是瞬间加载前第一温度传感器、第二温度传感器和第三温度传感器的实测温度,通过步骤2测得。围压变化与之原理相同,即压力传感器在步骤5的测得值与步骤2的测得值之间的差值。第一温度传感器、第二温度传感器以及第三温度传感器测量的温度均达到稳定时,则整套岩石热物性测试系统温度达到平衡。本发明通过瞬间打开两个耐压罐(其内部围压不同,岩石样品安置在围压较低的第二耐压罐中)之间的阀门,使得围压较低的第二耐压罐内的围压瞬间升高。我们的实验结果表明:地壳常见岩石的应力-温度响应系数(ΔT/Δσ)比较小(只有2~6mK/MPa),而传压介质(比如硅油、植物油、去离子水等传压介质)的应力-温度响应系数比地壳常见岩石的高2个数量级(比如硅油的应力-温度响应系数则高达138.74mK/MPa)。因此,围压瞬间升高后,岩石样品与传压介质之间就温差。通过实时监测耐压罐围压(Confiningpressure)、岩石样品中心、表面及第二耐压灌内传压介质的温度变化,结合有限元数值反演方法,即可获得高压条件下岩石样品的热物性参数(热导率/thermalconductivity、热扩散率/thermaldiffusivitiy、及体积热容/volumetricheatcapacity)。其主要优势为:无需电加热“热源”,只在岩石样品中心、表面及第二耐压灌内传压介质中各安置一个温度传感器,用于监测围压瞬间升高过程中岩石样品中心、表面级第二耐压灌内传压介质的温度变化,利用我们建立的有限元数值反演模型,结合全局优化方法,即可获得高压条件下岩石样品的热物性参数。从而实现了无电加热“热源”的瞬态热物性测试,大大简化了高压条件下岩石热物性测试系统及其操作程序。附图说明图1为本发明水下岩石绝热应力变化的温度响应测试系统的结构示意图;图2为二维柱坐标系统下的有限元数值模型;图3为龙门山断裂带砂岩L28瞬间加载过程中的温度响应曲线;图4为印度Rajasthan砂岩RJS瞬间加载过程中的温度响应曲线;图5为龙门山断裂带砂岩L28岩样中心温度的实测结果与有限元数值模型模拟结果对比图;图6为印度Rajasthan砂岩RJS岩样中心温度的实测结果与有限元数值模型模拟结果对比图。其中,1、第一耐压罐;11、第一空腔;2、第二耐压罐;21、第二空腔;22、第三排泄阀;3、高压泵;4、岩石样品;41、上硬质硅胶;42、下硬质硅胶;43、橡胶套;5、第一连通管道;51、第一排泄阀;52、第一压力传感器;61、第一温度传感器;62、第二温度传感器;63、第三温度传感器;7、第二连通管道;71、第二排泄阀;72、第二压力传感器;8、温度监测模块;9、围压监测模块;10、处理模块。具体实施方式下面结合附图和具体实施方式对本发明的内容做进一步详细说明。实施例请参照图1所示,一种高压条件下岩石热物性测试系统,其包括二个耐压罐(分别是第一耐压罐1和第二耐压罐2)、高压泵3、温度监测模块8以及围压监测模块9,其中,第一耐压罐1中内形成第一空腔11(充满传压介质,例如硅油、植物油、去离子水等),第二耐压罐2内形成第二空腔21(充满传压介质),向第一耐压罐1中输送传压介质的高压泵3通过第一连通管道5与第一空腔11相连,在所述第一连通管道5上安装有第一排泄阀51和第一压力传感器52;在所述第二空腔21内安装一岩石样品组件(圆柱状岩石样品组件包括圆柱状岩石样品4以及其中心及表面分别安置一个第一温度传感器61和第二温度传感器62,然后将圆柱状的上硬质硅胶41和下硬质硅胶42分别放置并压紧于圆柱状岩石样品4的上、下两侧,再由橡胶套43将硬质硅胶41、圆柱状岩石样品4以及下硬质硅胶42进行包裹,实现水密封装,封装后在放在设置于第二耐压罐2的第二空腔21内),第二空腔21内安装有第三温度传感器63,所述第一空腔11和第二空腔21之间通过第二连通管道7相连通,在所述第二连通管道7上安装有第二排泄阀71和第二压力传感器72,所述第二空腔21还与一第三排泄阀22相连通;所述第一温度传感器61、第二温度传感器62、第三温度传感器63的输出端均与温度监测模块8的输入端相连,通过温度监测模块8实时监测三个温度传感器的温度变化,所述第一压力传感器52和第二压力传感器72的输出端均与围压监测模块9的输入端相连,通过围压监测模块9实时监测第二耐压罐2内的围压变化。温度监测模块8和围压监测模块9的输出端还连接到一处理模块10上,可通过处理模块10计算岩石样品绝热应力变化的温度响应系数,另外,处理模块10可对高压泵3的工作进行控制,当围压监测模块9通过第一压力传感器52检测到第一耐压罐1的围压达到预定压力时,可通过处理模块10控制高压泵3停止工作。本发明涉及一种高压条件下岩石热物性测试方法与系统,先利用高压泵3将第一耐压罐1内的围压升至预定压力(比如130MPa),待带整个系统温度达到平衡后,再手动快速打开第一耐压罐1和第二耐压罐2之间的第二排泄阀71,使得1~2s内,第二耐压罐2内的围压瞬间升高,由于岩石样品与传压介质(如硅油)的应力变化温度响应系数相差两个数量级,因此岩石样品与传压介质之间就存在温差。通过监测围压瞬间升高过程中岩石样品中心、表面及第二耐压灌内传压介质的温度变化,利用我们建立的有限元数值反演模型,结合全局优化方法,即可获得高压条件下岩石样品的热物性参数。从而实现了无电加热“热源”的瞬态热物性测试,大大简化了高压条件下岩石热物性测试系统及其操作程序。热物性参数反演的有限元数值模型与方法具体如下:1)热传导微分方程由于本测试系统中的岩石样品制备成圆柱状,为了方便计算,这里第一温度传感器61位于岩石样品的中心,并且第二温度传感器62与第一温度传感器61位于岩石样品同一径向圆上。因此,其对应的柱坐标系统(2drz)下的热传导微分方程可表达成其初始条件为T(r,z,0)=0,r≤25mm,|z|≤65mm),(11)边界条件由测试系统监测的样品表面温度变化T02(t)和传压介质温度变化T03(t)进行如下约束,其中λ,ρc分别是各种介质的热导率(thermalconductivity)和体积热容(volumetricheatcapacity),γ为各种介质的绝热应力变化的温度响应系数(adiabaticpressurederivativeoftemperature),A是由于围压变化导致温度变化所对应的“热源”(heatsourcetermdrivenbychangerateofconfiningpressure)。依此热传导微分方程在柱坐标系统(2drz)建立有限元数值模型,如图2所示。步骤2、设岩石样品的热导率和体积热容分别为λ,(ρc),地壳常见岩石的热导率及体积热容的大致范围分别在0.5~6.0W·m-1·K-1、0.5×106~5.0×106J·m-3·K-1,为了拓宽本反演方法的适应性,可再次适当增大岩石热物性参数的求解区域其中λ,(ρc)两参数都进行m等份剖分,获得初始的(m+1)×(m+1)个网格节点(λi,(ρc)j),其中i,j=1,2,3,...,m;步骤3、并将每个网格节点(λi,(ρc)j)输入已建立的PT-FE有限元数值模型,以快加载过程中实时监测获取的岩石样品表面的温度变化T02(t)和传压介质(如硅油)温度变化T03(t)作为边界条件(图2),模拟计算(λ,(ρc))=(λi,(ρc)j)时,岩石样品中心处的温度变化,记为步骤4、利用最小二乘法,对上述有限元数值模型计算获得的与岩石样品中心实测的温度变化T01进行线性拟合:求解该拟合直线斜率Ki,j和相关系数Ri,j,其中相关系数计算表达式如下步骤5、定义目标函数为F(λi,(ρc)j)=1.0-(Ri,j)2(16)并求解各网格点处的目标函数值F(λi,(ρc)j),i,j=1,2,3,...,m;步骤6、找出目标函数值最小的网格点,如果(ε为判断是否满足求解要求而设定的阈值),则接受为所需要求解的岩石样品的热导率和体积热容(λ,(ρc)),否则,将以为中心的邻域为求解区域,将网格加密,返回到步骤3,直到满足为止,从而解算得到岩石样品的热导率和体积热容步骤7、最后根据热导率、体积热容及热扩散率之间的关系式κ=λ/(ρc),可计算得到岩石样品的热扩散率。至此,某围压下岩石热物性参数求解完毕。本发明高压条件下岩石热物性测试方法步骤如下:第一步:将第一温度传感器61和第二温度传感器62安置在制备好的圆柱状岩石样品4的中心和外表面,并用橡胶套将岩石样品4进行水密封装,形成岩石样品组件。第二步:将岩石样品组件、第三温度传感器63放入第二耐压罐2中,并进行密封。同时将安装有第一排泄阀51和第一压力传感器52的第一连通管道5连接高压泵3和第一耐压罐1,将安装有第二排泄阀71和第二压力传感器72的第二连通管道7连接第一耐压罐1和第二耐压罐2,在第二耐压罐2上安装第三排泄阀22,然后将第一温度传感器61、第二温度传感器62、第三温度传感器63连接至温度监测模块8,将第一压力传感器52和第二压力传感器72连接到围压监测模块9,从而组装形成岩石热物性测试系统;开启温度监测模块8和围压监测模块9,开始温度和围压监测。第三步:只打开第一排泄阀51,关闭第二排泄阀71和第三排泄阀22,开启高压泵3,将第一耐压罐1中的围压升至预定压力。第四步:3~6小时后,待整套系统的温度趋于平衡,关闭第一排泄阀51,同时第三排泄阀22保持关闭,快速打开第二排泄阀71,从而实现第二耐压罐2瞬间增压。通过上述操作,实现岩石样品瞬间加载,且这个过程中的温度和围压变化,都被实时监测并记录,再利用上述已建立的热物性参数反演的有限元数值模型与方法,即反演获得某围压下岩石样品的热物性参数。需要说明的是,上述是通过对岩石样品进行瞬间加载的方式进行的热物性测试,事实上,在第四步后可以在关闭第一排泄阀51和第二排泄阀71后,开启第三排泄阀22,使第二耐压罐2瞬间减压实现瞬间卸载,而瞬间卸载前后的温度和围压变化同样可以反演获得某围压下岩石样品的热物性参数。图3和图4是龙门山断裂带砂岩L28与印度Rajasthan砂岩RJS瞬间加载过程中的温度响应曲线。表1为对L28与RJS两个砂岩样品分别在15.31MPa、13.61MPa围压下测试获得的热物性参数结果:表1龙门山断裂带砂岩(L28)与印度Rajasthan砂岩(RJS)的热物性反演结果对比L28和RJS岩石样品中心温度的实测结果与有限元数值模拟结果如图5和图6所示:本发明提供的方法和系统,不仅可用于高压条件下岩石热物性参数测试,而且大大简化了原有测试系统及其操作程序。虽然本发明是通过具体实施例进行说明的,本领域技术人员应当明白,在不脱离本发明范围的情况下,还可以对本发明进行各种变换及等同替代。另外,针对特定情形或应用,可以对本发明做各种修改,而不脱离本发明的范围。因此,本发明不局限于所公开的具体实施例,而应当包括落入本发明权利要求范围内的全部实施方式。