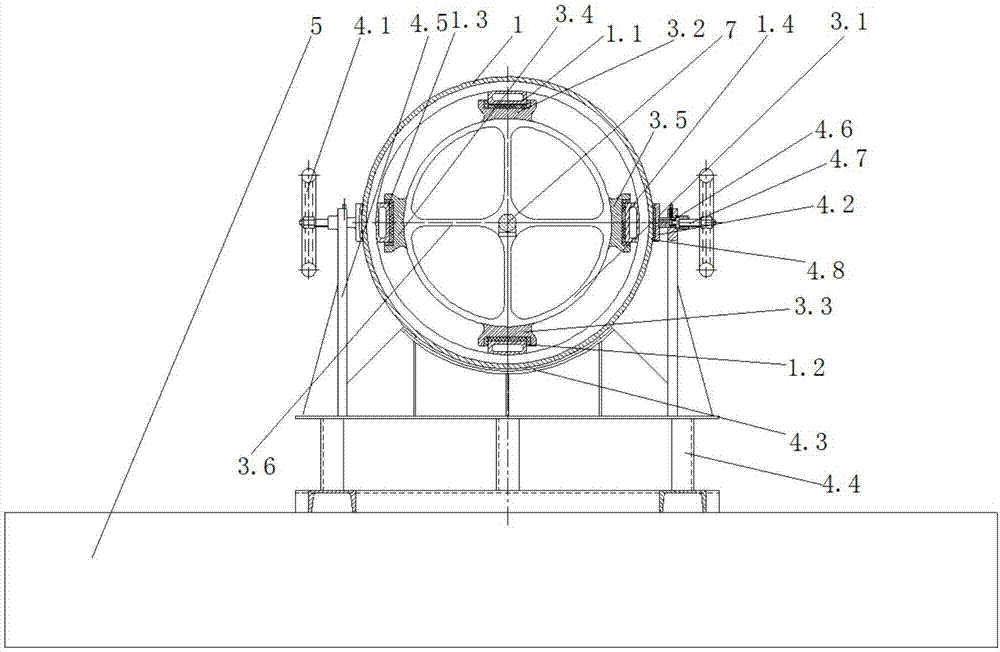
本发明涉及多导轨检测
技术领域:
,具体涉及一种四导轨装调检测装置及检测方法。
背景技术:
:一般导轨是单组安装在敞开环境中,导轨安装检测较为简便,对于在半封闭(如筒体内)安装多组导轨,且导轨安装位置度和直线度等方面的精度要求较高时,导轨精度检测难度较大。现有技术中对导轨安装检测的方式主要是依靠自准仪(或测平测直仪)进行,然而,考虑到细长筒体内,操作空间狭小,而且安装调整均要在半封闭状态下进行,在此情况下现有的检测方式难以满足操作便利性和调整精度的要求;另一方面,现有的检测方式比较适合单一导轨的检测,却难于执行多导轨的同步检测,特别是不能对现有筒体中常见的上下左右四导轨的相对位置进行检测。相应地,相关领域亟需寻找更为完善的解决方案,以便满足多导轨的高精度同步检测需求。技术实现要素:本发明的目的在于提供一种四导轨装调检测装置及检测方法,通过对其关键组件的结构及其设置方式进行设计,即便在细长筒体内和半封闭的状态下也能够很好地满足导轨的通过性检测需求,并适于对多导轨同步执行检测;此外,该检测装置还具备结构紧凑、便于操控、装调定位准确和制造成本低等特点。本发明还提供一种在导轨检测时对细长筒体进行定位装置,方便筒体固紧无松动,平稳放置在检测平台上,有利于保证导轨检测精度。为解决上述技术问题,本发明所设计的四导轨装调检测装置,其特征在于:它包括检测装置、平台和多个定位装置,其中,所述检测装置包括圆筒框架本体、上侧凸台滑块、下侧凸台滑块、左侧凸台滑块和右侧凸台滑块,所述上侧凸台滑块、下侧凸台滑块、左侧凸台滑块和右侧凸台滑块沿圆筒框架本体的周向设置,所述上侧凸台滑块用于与筒体内壁的被测上导轨滑动配合,下侧凸台滑块用于与筒体内壁的被测下导轨滑动配合,左侧凸台滑块用于与筒体内壁的被测左导轨滑动配合,右侧凸台滑块用于与筒体内壁的被测右导轨滑动配合,圆筒框架本体前端面的圆心处设置有反射镜,所述反射镜的镜片水平设置,多个定位装置并排设置在平台上,多个定位装置用于对筒体的外侧壁进行夹持,平台上设有自准仪,所述自准仪的物镜能水平对准反射镜的镜片。每个定位装置均包括手轮、压紧块、弧形托架和框架,其中,框架的底部固定在平台上,框架的中部设置弧形托架,框架的左右两侧为手轮支架,两个手轮支架上均设有螺孔,两个螺孔上均螺纹连接有螺杆,每个螺杆的内端面安装有压紧块,每个螺杆的外端面安装有手轮,所述弧形托架用于拖住筒体的底部外壁,两个压紧块用于压紧筒体的两侧外壁。所述压紧块的压紧面为与筒体匹配的弧形压紧面。所述压紧块的弧形压紧面上粘贴有软带。所述上侧凸台滑块、下侧凸台滑块、左侧凸台滑块和右侧凸台滑块均有三个,以上三个上侧凸台滑块、下侧凸台滑块、左侧凸台滑块和右侧凸台滑块分别位于圆筒框架本体的前端、中部和后端;所述上侧凸台滑块、下侧凸台滑块、左侧凸台滑块和右侧凸台滑块的滑轨接触面均安装有左滑板、右滑板和底滑板。一种利用上述装置的四导轨装调检测方法,其特征在于,它包括如下步骤:步骤1:将自准仪的视场中心与反射镜的中心调整至对齐;步骤2:自准仪射出的光线照准安放在圆筒框架本体圆心处的反射镜,将检测装置沿筒体内壁的被测导轨整个被测长度方向来回滑动,同时调整自准仪的位置,使自准仪中十字线的反射像均在视场内即可,然后将自准仪的位置加以固定;步骤3:松开自准仪的目镜头锁紧螺钉,转动目镜头以使自准仪的测微鼓轮的轴线方向平行于物镜轴方向,然后锁住目镜头,将检测装置放在筒体内壁的被测导轨起始点;步骤4:调整自准仪的位置,使自准仪的十字线影像处于视场中央,从自准仪上进行对线并得到偏移量读数a1,然后将检测装置依次从起始点步进式移至终测点处,同时分别从自准仪上进行对线,并得偏移量读数a2、a3、a4、a5、a6、a7、a8,……,an-1、an,实现水平方向的直线度测量,偏移量是指反射光线与目镜上十字指示线的差值;步骤5:当检测装置的反射镜移到终测点时,自准仪位置固定不动,松开目镜头锁紧螺钉,将目镜头顺时针旋转90°,使测微鼓轮的轴线方向与物镜方向垂直,锁紧目镜头;步骤6:使自准仪的十字线影像处于视场分划板刻线中央,记下自准仪此时位置的偏移量读数bn,然后将检测装置依次从终测点步进式移至起始测点,同时分别从自准仪上进行对线,并得偏移量读数bn-1,……,b8、b7、b6、b5、b4、b3、b2、b1,实现垂直方向的直线度测量。本发明与现有技术相比,主要具备以下的技术优点:1、通过对检测装置的整体结构形式及其关键组件的设置方式进行设计,凸台滑块结构能与待检测导轨完全贴合,在实际应用时仅需要简单的牵引操作即可完成,这样不仅极大提高了操作的便利性和效率,而且能够在箱体较长和半封闭的状态下也很好地满足多组导轨的同步检测及相互位置的检测需求;通过将滑板设置为可拆卸结构并由耐磨性材质制成,使得按照本发明的检测装置使用寿命长,便于维修加工,在维护时只需更换滑板即可。2、定位工装采用圆弧结构及增加锁紧机构,能有效对筒体进行定位固紧,保证筒体放置稳定性,同时敷设软带可有效防止产品表面划伤。3、利用检测装置与自准仪,可较好对多组导轨水平方向与垂直方向直线度进行检测,检测精度高。附图说明图1为本发明使用状态的主视结构示意图;图2为本发明使用状态的侧视结构示意图;图3为本发明中检测装置的结构示意图;图4为图3的侧视结构示意图;图5为本发明中定位装置的结构示意图;图6为图5的侧视结构示意图;其中,1—筒体、1.1—被测上导轨、1.2—被测下导轨、1.3—被测左导轨、1.4—被测右导轨、2—垫块、3—检测装置、3.1—圆筒框架本体、3.2—上侧凸台滑块、3.3—下侧凸台滑块、3.4—左侧凸台滑块、3.5—右侧凸台滑块、3.6—十字支架、3.7—左滑板、3.8—右滑板、3.9—底滑板、4—定位装置、4.1—手轮、4.2—压紧块、4.3—弧形托架、4.4—框架、4.5—手轮支架、4.6—螺孔、4.7—螺杆、4.8—软带、5—平台、6—自准仪、7—反射镜。具体实施方式以下结合附图和具体实施例对本发明作进一步的详细说明:一种四导轨装调检测装置,如图1~6所示,它包括检测装置3、平台5和多个定位装置4,其中,所述检测装置3包括圆筒框架本体3.1、上侧凸台滑块3.2、下侧凸台滑块3.3、左侧凸台滑块3.4和右侧凸台滑块3.5,所述上侧凸台滑块3.2、下侧凸台滑块3.3、左侧凸台滑块3.4和右侧凸台滑块3.5沿圆筒框架本体3.1的周向设置,所述上侧凸台滑块3.2用于与筒体1内壁的被测上导轨1.1滑动配合,下侧凸台滑块3.3用于与筒体1内壁的被测下导轨1.2滑动配合,左侧凸台滑块3.4用于与筒体1内壁的被测左导轨1.3滑动配合,右侧凸台滑块3.5用于与筒体1内壁的被测右导轨1.4滑动配合,圆筒框架本体3.1的前端面的圆心处设置有反射镜7,所述反射镜7的镜片水平设置,多个定位装置4并排设置在平台5上,多个定位装置4用于对筒体1的外侧壁进行夹持,平台5上设有自准仪6,所述自准仪6的物镜能水平对准反射镜7的镜片。自准仪6的光线射在反光镜7上,它是利用平面直线度的高低误差使反射光线与目镜上十字指示线之间产生偏移量大小,来逐段测量导轨直线度误差,最后计算出导轨的最大误差值。上述技术方案中,每个定位装置4均包括手轮4.1、压紧块4.2、弧形托架4.3和框架4.4,其中,框架4.4的底部固定在平台5上,框架4.4的中部设置弧形托架4.3,框架4.4的左右两侧为手轮支架4.5,两个手轮支架4.5上均设有螺孔4.6,两个螺孔4.6上均螺纹连接有螺杆4.7,每个螺杆4.7的内端面安装有压紧块4.2,每个螺杆4.7的外端面安装有手轮4.1,所述弧形托架4.3用于拖住筒体1的底部外壁,两个压紧块4.2用于压紧筒体1的两侧外壁。上述定位装置4有三个,分别用于定位筒体1的前部、中部和后部。三个定位装置4能实现筒体1的准确定位。上述技术方案中,所述压紧块4.2的压紧面为与筒体1匹配的弧形压紧面。上述技术方案中,所述压紧块4.2的弧形压紧面上粘贴有软带4.8,软带4.8采用聚四氟乙烯材料制作,用于增大筒体1与定位装置摩擦系数并防止筒体1转动,可有效防止筒体1表面被划伤。上述技术方案中,所述圆筒框架本体3.1内设有十字支架3.6,所述十字支架3.6的中心为圆筒框架本体3.1的圆心,所述十字支架3.6的中心设有反射镜安装位,反射镜7安装在上述反射镜安装位上。上述技术方案中,所述检测装置3有3个,3个检测装置形成检测装置组,,所述自准仪6通过垫块2安装在平台5上。上述技术方案中,所述上侧凸台滑块3.2、下侧凸台滑块3.3、左侧凸台滑块3.4和右侧凸台滑块3.5均有三个,以上三个上侧凸台滑块3.2、下侧凸台滑块3.3、左侧凸台滑块3.4和右侧凸台滑块3.5分别位于圆筒框架本体3.1的前端、中部和后端;所述上侧凸台滑块3.2、下侧凸台滑块3.3、左侧凸台滑块3.4和右侧凸台滑块3.5的滑轨接触面均安装有左滑板3.7、右滑板3.8和底滑板3.9。左滑板3.7、右滑板3.8和底滑板3.9构成凹型槽。凹型槽与四组导轨面精密配合,检测装置可在筒内导轨上平稳滑动。左滑板3.7与对应的右滑板3.8之间的尺寸和公差由所要检测导轨的宽度尺寸和公差确定,以上滑板均由耐磨性的材料制成,由此在提供滑行功能的同时能够适于长时间的作业。此外,由于这些滑板可拆卸地安装,维修时只需要更换具有耐磨材料的滑板即可。当采用本发明的检测装置进行导轨检测时,只需将检测装置的凹型槽插入各导轨中,并将检测装置通过匀速牵引从箱体一端到箱体另一端能顺利通过即可,这样不仅可以高效率、便于操控的方式来适于多导轨的同步检测,而且还能有效检测装置各槽面与导轨之间的间隙值、以及多导轨之间的相对位置等是否满足要求。一种利用上述装置的四导轨装调检测方法,它包括如下步骤:步骤1:将自准仪6的视场中心与反射镜7的中心调整至对齐;步骤2:自准仪6射出的光线照准安放在圆筒框架本体3.1圆心处的反射镜7,将检测装置3沿筒体1内壁的被测导轨整个被测长度方向来回滑动,同时调整自准仪6的位置,使自准仪6中十字线的反射像均在视场内即可,然后将自准仪6的位置加以固定;步骤3:松开自准仪6的目镜头锁紧螺钉,转动目镜头以使自准仪6的测微鼓轮的轴线方向平行于物镜轴方向,然后锁住目镜头,将检测装置3放在筒体1内壁的被测导轨起始点;步骤4:调整自准仪6的位置,使自准仪6的十字线影像处于视场中央,从自准仪6上进行对线并得到偏移量读数a1,然后将检测装置3依次从起始点步进式移至终测点处,同时分别从自准仪6上进行对线,并得偏移量读数a2、a3、a4、a5、a6、a7、a8,……,an-1、an,每次移动检测装置必须首尾衔接,移动轨迹应成直线并与被测直线方向平行,实现水平方向的直线度测量,偏移量是指反射光线(自准仪6射出的光经过反射镜7反射)与目镜上十字指示线的差值;步骤5:当检测装置3的反射镜7移到终测点时,自准仪6位置固定不动,松开目镜头锁紧螺钉,将目镜头顺时针旋转90°,使测微鼓轮的轴线方向与物镜方向垂直,锁紧目镜头;步骤6:使自准仪6的十字线影像处于视场分划板刻线中央,记下自准仪6此时位置的偏移量读数bn,然后将检测装置依次从终测点步进式移至起始测点,返测时检测装置切勿调头,同时分别从自准仪6上进行对线,并得偏移量读数bn-1,……,b8、b7、b6、b5、b4、b3、b2、b1,实现垂直方向的直线度测量。步骤7:在测量原始记录上分别记录水平方向的偏移量读数a1、a2、a3、a4、a5、a6、a7、a8,……,an-1、an和垂直方向的偏移量读数bn、bn-1,……,b8、b7、b6、b5、b4、b3、b2、b1。所述筒体1内壁的被测导轨起始点为筒体1内壁的被测导轨面向自准仪6的端部。上述技术方案中,整个测量过程分成n个测量点进行将安放着反射镜7的检测装置4起始点。整个测量过程分成n个测量点进行,测量点数的计算,见公式1。式中:l—导轨有效工作面长度,单位为mm;ld—检测装置的长度,单位为mm;n—测量点数。下面举例予以具体说明。以导轨水平方向直线度的测量过程为例,检测装置设定ld=500mm,导轨的长度设定为6000mm,设计尺寸要求被测导轨直线度不大于1mm,由公式1算出需测量12个测量点,实例说明长导轨直线度测量方法及测量数据的处理。1)测量前,自准仪光管视场中心与反射镜的中心应调整至等高。2)接通电源,使光线照准安放在检测装置上的反射镜。把检测装置沿导轨整个被测长度来回移动,同时调整自准仪的位置,使准直光管中十字线的反射像均在视场内即可。然后,将仪器主体的位置加以固定。3)水平方向的直线度测量,松开目镜头锁紧螺钉,转动目镜头以使测微鼓轮的轴线方向平行于物镜轴方向,锁住目镜头,将固定有反射镜的检测装置放在被测导轨的起始点,即靠近自准仪处。4)调整自准仪的位置,使十字线影像大致处于视场分划板刻线中央,从自准仪上进行对线并读数得偏移量读数a1,然后将检测装置依次从起始点移至终测点处(这里是导轨右侧),分别对线并得偏移量读数a2,a3,a4,a5,a6,a7,a8,a9,a10,a11,a12,每次移动检测装置必须首尾衔接,移动轨迹应成直线并与被测直线方向平行。按测量点顺序做好12个测量点的数据见下表。测量点a1a2a3a4a5a6a7a8a9a10a11a12仪器读数898800817801796787775794783801750786按照公式2至公式7进行测量数据的处理,如果计算出的直线度在设计给出的公差范围内,则直线度合格,见下表。上表中:测量点自准仪读数差的计算,见公式2:a′1=ai-a1(2)式中:ai为自准仪6在第i个测量点的偏移量的读数,单位为格;a1为自准仪6在第一个测量点的偏移量的读数,单位为格;a'i为第i个测量点与第1个测量点的读数差,单位为格。测量点读数差累积求和计算,见公式3:式中:ai为第1个测量点到第i点a'i值的累积求和。测量点的修正值计算,见公式4:式中:bi为第i个测量点的修正值。测量点的直线度误差计算,见公式5:δi=ai-bi(5)式中:δi为第i个测量点的直线度误差,单位为(格)。测量点的格值δi转换成线性值δi,按照以下公式6计算:δi=ldτδi(6)式中:δi为导轨直线度偏差,单位为微米(um);τ为自准仪6的分度值,单位为毫米每米(mm/m)。导轨直线度的计算,见公式7:f=δmax-δmin(7)式中:f为导轨的直线度,单位为微米(um);δmax为直线度偏差δi中的最大值,单位为微米(um);δmin为直线度偏差δi中的最小值,单位为微米(um)。本说明书未作详细描述的内容属于本领域专业技术人员公知的现有技术。当前第1页12