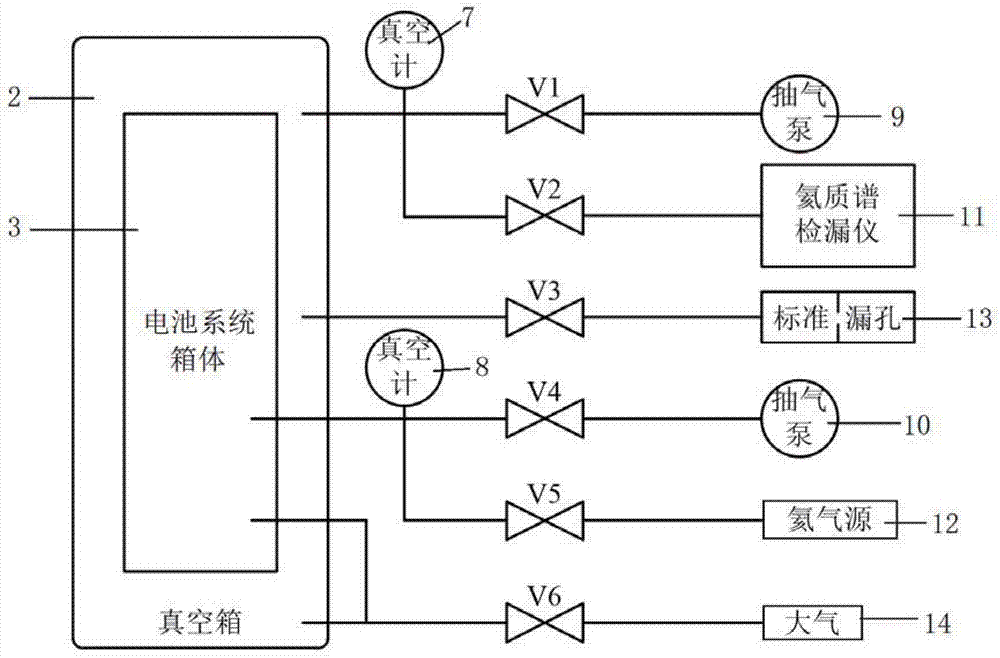
本发明涉及一种用于检测电池系统箱体密封性能的设备及方法,主要用于新能源汽车车载动力电池包或系统箱体的密封性检测或测试。
背景技术:
:目前,在新能源汽车行业,车载动力电池系统的密封等级至少需要满足ip67及以上防护等级,其中“6”代表尘密,即不允许任何灰尘进入;“7”代表短时间浸水性能,即满足30min浸水无渗漏。当前,电池厂商主要担心在车辆运行过程中,雨天或有积水较深路面情况下,液态水会进入电池包内部,进而诱发漏电等安全隐患;或者是担心水汽进入到电池系统箱内部的电芯内部,造成电解液改性,进而影响电池性能。因此,对电池系统箱体密封性的基本要求是:水不能进入到电池系统箱体内。对于新能源汽车电池系统箱体密封性检测,常用的方法包括浸水法、压力衰减法、超声波检漏法、空气压差法、喷氦法、真空氦罩法和吸枪法等。这些方法的特点如下:(1)浸水法是将电池系统箱体通过吊装机构吊入水箱中测试样品密封性的一种方法。该方法是通过人眼观察浸没在水箱中电池系统箱体是否有气泡产生,这种方法精度不高,无法定量判断,且将电池系统浸入到水中会有短路、起火、爆炸的危险。(2)压力衰减法由于采用氢氮混合物作为示踪气体,容易形成样品的氢脆现象,且氢气的使用具有安全隐患。(3)超声波检漏法不容易查找复杂工件的漏点和孔隙,也不适合查找组装工件的漏点和孔隙。(4)空气压差法主要是利用空气检漏仪和泵组相结合,通过将一定压力的空气泵入到电池系统箱体中,记录检漏仪探测到的压力值,观察一段时间(如30min)后,再记录检漏仪读取到的压力值,如果前后压力值有变化,则表明样品有泄漏,否则样品无泄漏。该方法利用空气压力差和压力的变化,由于空气的温度易受光照和热源的影响,因此测量精度不高。(5)喷氦法是利用喷枪将氦气喷到电池系统样品的表面,再通过与电池系统样品内部相连接的检漏仪读取内部的氦分子数量,经过检漏仪内部的换算机制获取泄漏量。由于在大气环境中喷氦,且样品内部有空气存在,有氦气本底,针对密封性要求较高的电池系统箱体,由于内外压力相等,喷在外部的氦气不易进入样品内,因此检测的准确度不高。(6)真空氦罩法是将样品放入充满氦气的氦罩内,一般情况下氦罩为软质材质,可以测试出总体漏率,但无法确定漏点的位置。(7)吸枪法是常用的一种方法,其主要原理是在被测样品中充满了加压的氦气。若在被测对象中存在泄漏点,被测对象内部的氦气就会沿着泄漏点外泄流出,此时利用连接在氦质谱检漏仪上的吸枪靠近被测对象的接缝处,如果有泄漏的位置,溢流出的氮气就会被吸枪管吸入,此部分的氦气就会被检漏仪精确地检测到,并测量泄漏位置的泄漏量数据。吸枪法是一种快速用于箱体类容器的检测方法,利用吸枪管可以准确的找到箱体泄漏点的位置。但是由于需要从整体的角度判断电池系统箱体的泄漏程度,需要知道电池系统箱体的整体泄漏量,而吸枪法无法从整体角度获取整体泄漏量。另外,用吸枪法查找电池系统箱体的泄漏点时,吸枪管的探头容易受到环境中其它气体的影响而导致检测准确度不高。因此吸枪法在电池系统密封性能检测方面具有一定的局限性。专利文献cn102353504a公开了一种电池包密封检测系统,包括测试连接管、储液容器和透明管,储液容器上设置有压缩空气进口,测试连接管与储液容器气路连通,从而利用压缩空气使透明管内的液柱保持在一定高度,并对电池包施压,若电池包漏气,则液柱下降,无需精密的气压检测传感器和精密的仪表,直接采用液柱高度检测密闭系统内的压力值和压力变化值。该检测系统利用液柱的高度检测密闭系统的压力值和压力变化值,但受到温度影响,液柱有可能会上下浮动,因此测量结果精度不高。专利文献cn105334003a公开了一种动力电池包密封性检测装置,包括箱体,箱体上腔体安装有测试仪器、工控机、显示器、扫码枪,箱体上部设有报警灯,箱体下腔设有控制电箱、气动三联件。该检测装置通过条形码输入自动调用不同型号测试流程,无需人工操作设计专用测试密封工装,确保测试中工装不会泄露。但该检测装置是利用空气压力差和压力的变化进行的检测,由于空气的温度易受光照和热源的影响,因此测量精度不高。专利文献cn106017821a公开了一种电池密封性检测系统,其通过外置的真空泵抽空并测试,在内外压差的作用下,若电池密封性不足,电池内部的氦气透过漏孔,从电芯内进入内腔,从而检测其泄漏量。该发明的缺点是需要使用真空罩和抽气泵,成本高;且无法找到泄漏点。专利文献cn106525360a公开了一种检测电池箱体密封性的方法,该方法在对电池箱体进行防水实验之前,首先通过第一管路和第二管路将待测箱体和标准箱体相连接,通过观察压力表的变化来判断箱体是否有泄露。这种方法的缺点是利用空气压力差和压力的变化,由于空气的温度易受光照和热源的影响,因此测量精度不高。专利文献cn107402107a公开了一种用于电池包密封性检测装置,包括气压获取模块,被配置为获取所述电池包内的当前气压;控制模块,被配置为在当前气压满足预设的报警条件时,控制报警装置进行报警。该发明同样是利用空气压力差和压力的变化,由于空气的温度易受光照和热源的影响,因此测量精度不高。技术实现要素:本发明的目的在于提供一种用于检测电池系统箱体密封性能的设备,利用该设备可以对电池系统箱体进行氦质谱等压式正压检漏,能够安全、高效地检测电池系统箱体的密封性能,测试精度高。本发明的另一目的在于提供一种使用所述设备检测电池系统箱体密封性能的方法,该方法可以对电池系统箱体进行氦质谱等压式正压检漏。为实现上述目的,本发明采用以下技术方案:一种用于检测电池系统箱体密封性能的设备,该设备包括:真空箱、氦质谱检漏仪、两组抽气泵组、氦气源;检测时电池系统箱体置于真空箱内;氦质谱检漏仪通过检漏管路连接真空箱;两组抽气泵组中的一组通过抽气管路连接真空箱,另一组通过抽气管路连接电池系统箱体;电池系统箱体通过充气管路连接外部氦气源;电池系统箱体和真空箱分别通过放气阀和排空阀路连接大气;真空箱和电池系统箱体外分别设有压力传感器,该两个压力传感器分别连接plc控制单元;真空箱连接标准漏孔,该标准漏孔用于对设备进行校准;各管路上分别设有电磁阀,各电磁阀均由plc控制单元控制。优选地,所述真空箱由不锈钢304制成,其箱体内表面制造后进行抛光处理,光洁度达到1.6级。优选地,所述真空箱连接抽气管路的端口处安装有多级过滤网。优选地,所述真空箱为圆柱形,在真空箱的顶部的几何位置中心设有安全泄爆口。优选地,连接所述真空箱的抽气泵组为单级真空泵。优选地,在检漏管路上的电磁阀处设有节流管路。优选地,所述真空箱连接有用于向真空箱内充注氮气或新鲜空气的氦气本底除污装置。一种使用所述设备检测电池系统箱体密封性能的方法,包括以下步骤:(1)在电池系统箱体整体装入真空箱内之前,开启抽气泵组将真空箱抽真空至真空度为11.6kpa以上,关闭抽气阀门,打开检漏管路上的检漏阀,获得真空箱内氦气本底值;关闭检漏阀,打开连接标准漏孔的管路上的漏孔阀,记录检漏仪的漏率显示值,用标准漏孔漏率值除以该漏率显示值得到校准系数;(2)将电池系统箱体整体装入真空箱内,连接好电池系统箱体内外抽气管路和氦气充气管路、压力传感器以及检漏仪的检漏管路,关闭真空箱门后,将真空箱和电池系统箱体同步抽真空至真空度为11.6kpa以上,关闭抽气阀门;(3)打开充气阀门,向电池系统箱体内充入氦气,至电池系统箱体内外压差≤4kpa时,关闭充气阀门,打开检漏阀,压力保持10min;检漏仪开始测量漏率值大小;(4)确认检漏结果后,将电池系统箱体和真空箱同时放大气,并保证电池系统箱体内外压力一致;(5)对于检测有泄漏点的电池系统箱体,从真空箱取出后向其中充入氦气,采用吸枪检漏法检测泄漏点的具体位置。优选地,所述步骤(2)中,对真空箱和电池系统箱体同步抽真空过程中,保证电池系统箱体的内外压差不超过4kpa。优选地,所述步骤(5)中,所述电池系统箱体内充入氦气后的压力值≤4kpa。本发明的优点在于:本发明的设备属于真空箱式等压氦质谱检测系统,在检测过程中模拟被检工件的实际工况进行氦质谱检漏,消除了负压检漏造成的误判现象,设备的整体设计保证了校准检漏量化精度,检漏结果真实准确可靠。本发明的检测方法是一种“等压式”的真空箱氦质谱检漏法,在检测过程中,通过压力传感器确保电池系统箱体内外压力以等压的方式降低,而不会破坏系统箱体的外壳,提高了检测过程和测试样品的安全性。本发明的检测方法既可以定位泄漏的位置,又可以准确量化所泄漏的泄漏量,从而通过多次的测试与经验积累,建立动力电池系统箱体的总的泄漏量和电池系统ip防护等级之间的关系,为行业内电池系统ip等级判定标准的制定提供有力的理论和数据支撑。附图说明图1为本发明用于检测电池系统箱体密封性能的设备的结构示意图。图2为本发明的设备中主要部分的连接关系图。图3为将电池系统箱体装入真空箱过程中设备的结构示意图(俯视图)。图4为采用本发明的设备检测电池系统箱体密封性能的工艺流程图。具体实施方式下面结合附图和实施例对本发明做进一步说明,但并不意味着对本发明保护范围的限制。如图1-3所示,本发明用于检测电池系统箱体密封性能的设备包括:真空箱2、氦质谱检漏仪11、真空箱抽气泵组9、电池系统箱体抽气泵组10、氦气源12;检测时电池系统箱体3置于真空箱2内;氦质谱检漏仪11通过检漏管路连接真空箱3;真空箱抽气泵组9和电池系统箱体抽气泵组10分别通过抽气管路连接真空箱2;电池系统箱体3通过充气管路连接外部氦气源12;电池系统箱体3和真空箱2分别通过放气管路连接大气;真空箱2和电池系统箱体3内分别设有压力传感器,该两个压力传感器分别连接plc控制单15元;各管路上分别设有电磁阀,各电磁阀均由plc控制单元15控制;抽气管路、检漏管路及充气管路上分别连接有真空计7、8。作为本发明的具体实施方式之一,如图3所示,上述用于检测电池系统箱体密封性能的设备由以下部分构成:1、真空箱检漏平台和工件密封夹具真空箱检漏平台为设备关键部位,根据被检工件外形尺寸及氦质谱检漏要求设计,真空箱由不锈钢304制成,箱体内表面制造后进行抛光处理,光洁度达到1.6级,以免吸附氦原子,而造成高的氦本底。真空箱门6的开启结构合理简便安全,真空箱开门机构装有接近开关,开关箱门时,需确保没有影响真空箱门运动的物体,以避免箱门开关期间可能对人物伤害。箱门装有卡紧装置,防止箱门意外冲开对人员物品造成损伤。2、电池系统箱体(工件)进出箱系统真空箱门开关与进料方式:工件3放在箱外小车5的托板4上,然后箱外小车和真空箱(箱体定向孔与箱外小车导向杆)对接,将装有工件的托板推入真空箱内,连接箱内充氦管道,手动开关箱门。托板4的表面放置非金属绝缘材料。3、电池系统箱体(工件)爆裂气压释放和粉尘过滤系统工件大漏的预检和机械应力测试是在真空箱内进行的,使用方的充压操作设计应尽量避免工件因强度问题爆裂,同时设备真空箱强度设计要求能承受工件爆裂的一般破坏;新设备在继续强化真空箱安全强度的同时,增加了迅速排除工件爆裂释放内部气体的功能,进一步保护操作者和设备的安全。泄压口1位于真空箱体的正上方的几何位置中心,防止爆破口弹出物体二次伤害。在考虑真空抽速尽量少受影响和尽量减少氦气残留的同时,真空箱预抽空口安装多级过滤网,防止粉尘杂物等进入真空泵系统。4、真空箱抽空系统由于真空箱真空度要求不高,所以选用单级真空泵即可满足抽空需求,单级泵可靠耐用,完全能够满足检测要求。真空箱上一共装有5个阀门,分别用于真空箱抽空、真空箱检漏、真空箱标漏、真空箱除污、真空箱放气,包括:用于控制真空箱抽气的抽气阀v1、用于真空箱检漏的检漏阀v2、用于真空箱标漏的漏孔阀v3、用于控制电池系统箱体抽气的抽气阀v4、用于控制向电池系统箱体充入氦气的充气阀v5、用于控制箱体放气的放气阀v6。阀门v1、v4接口可与罗茨泵组直接相连;检漏阀v2用于真空箱和氦质谱检漏仪连通和关闭。由于氦质谱检漏仪检漏时要求的真空度高,所以在检漏阀处有必要安装节流管路,保证在检漏过程中,检漏仪真空在使用范围内。漏孔阀v3主要用于标准漏孔和真空箱连接,自动标定设备时使用。放气阀v6主要用于真空箱放气,破坏真空箱内的真空,然后取放工件。5、真空箱清氦系统抽空系统预留氦气本底除污装置,当氦气本底高于设置要求影响正常工作时,设备自动报警提示,操作者可以通过除污装置强制对系统充注氮气(由图3中所示的氮气瓶17提供)或新鲜空气,置换残留的氦气,降低氦本底,使设备正常工作。6、工件充氦系统充氦系统由减压阀、压力传感器、电磁阀、安全阀、充气管路等组成。设备从氦气瓶出来的高压氦气经过设备减压阀,降低到使用压力后,才可以使用。压力传感器和电磁阀相互配合,工件充气达到工作压力后,自动切断电磁阀。7、电气控制系统(置于图2、3中的电气控制柜16内)设备电气控制系统按照国际电力安全标准设计,具有整体断电漏电保护,以及三相断相和相位相序正反识别等保护功能。对电机具有过流过热保护,电气接线有高低压警告标识,接头及线头有编号。电气控制系统的核心控制部分采用目前工业控制领域流行的可编程控制器plc和人机界面触摸屏。考虑到电池外壳的承压状况,设备同时配备抽电池系统箱体内部和外部气体的两个真空系统,通过监测两套真空系统中真空计的数据,并自动操作阀门,使电池系统箱体的内外真空度在抽气过程中基本一致,避免电池系统箱体内外有过大的压差造成电池系统箱体的损坏。本发明中设备的检漏示踪介质为氦气,系统检测的检漏指标设为一定量的氦气泄漏率。该氦气泄漏率是根据产品合格要求的介质的年泄漏率而设定,并可以根据国家标准和生产需要在一定范围内调整设定。其中整套设备中,起泄漏率测量的仪器为氦质谱检漏仪,是检测泄漏量的主要仪器,氦质谱检漏仪实际是在检测质谱室内的氦分压,并根据系统对氦的抽速将氦分压换算为漏率。其工作原理是:氦质谱检漏仪内部有一个离子源,将从检漏管路来的氦气送至离子源附近,离子源将各种粒子通过电场发射,在内部有一个挡板,挡板上有一个小孔,在一定的磁场作用下,此小孔只允许氦粒子通过,不允许其他轻粒子或重粒子通过,这样在另一侧的检测板就会监测到氦粒子的数量,并换算为氦气的数量,从而在显示屏上显示出氦气的泄漏率。吸枪检漏法是一种正压法检漏法,其目的是对于测试样品的局部检漏,其工作原理是,电池系统箱体中充入一定压力的氦气,若电池系统箱体的上下盖结合处或插接件与箱体的密封处有泄漏点,电池系统箱体内的氦气就会通过泄漏点流出;此时,启动连接在检漏仪上的吸枪,手持吸枪使吸枪头沿着电池系统箱体的上下盖边缘以较慢的速度移动,如果有泄漏的位置,从泄漏点泄露出的氦气就会被吸枪管吸入,进而氦气由吸枪管通过橡胶软管进入到检漏仪中,通过与标准漏孔的比较测量和计算,得到准确的检漏值,与此同时,检漏仪也会通过液晶屏报警的形式,提示操作者吸枪管所经之处有泄漏点;用同样的方法可以继续查找其他由结合处的泄漏点,这样就可以准确可靠地找出整个电池系统箱体的泄漏位置。将以上两种方法进行结合,可以获得电池系统箱体的泄漏总量以及准确定位泄漏的位置,进而充分了解电池系统箱体的密封性能。如图4所示,使用上述具体实施方式的设备进行电池系统箱体密封性能的等压式氦质谱检测,具体操作过程如下:1、检漏前的准备工作启动氦质谱检漏仪,检漏仪执行本身的自启程序,等待其正常,这个过程大概需要5分钟。在没有放入电池系统箱体时,开启抽气泵组,打开抽气隔断阀v1和v4,对真空箱和电池系统箱体同时进行抽真空,当真空箱的真空度达到12kpa(>11.6kpa)时,关闭抽气阀v1和v4,打开检漏阀v2,记录真空系统本底值。打开标准漏孔阀v3,这时检漏仪就检测到氦气,等数据稳定后,记录检漏仪的漏率显示值,用标准漏孔漏率值除以显示值得到此系统的校准系数。在实际检漏过程中,显示值要乘以系统的校准系数才得到被检件的漏率大小。2、充气检漏1)待测电池系统箱体大漏判断将动力电池系统箱体放入到真空箱中,连接电池箱体的抽气管路,关闭真空箱门,开启抽气泵组,打开真空计,打开电池系统箱体的抽气阀v1和v4,真空度抽到±2kpa后关闭阀门,等待1分钟,观察真空度值是否有明显的上升,如果没有,可以进行下一步的小漏判断,如果有明显上升,打开放气阀v6,对电池箱体和真空箱内进行压力还原,打开真空箱大门,松开管路连接,取出电池系统样品。2)待测电池系统箱体小漏判断开启抽气阀v1和v4,对真空箱体和电池系统箱体同时抽真空,使电池系统箱体内外的压力下降基本保持一致,抽到真空度为11.6kpa后,关闭v1和v4,打开检漏阀v2,观察并记录检漏仪上的氦气漏率值。3、吸枪检漏找泄漏点吸枪检漏,电池系统测试样品不需要放入真空箱体内,吸枪检漏首先需要通过充气管路对电池系统箱体进行充氦,此时压力值不能大于4kpa,以避免电池系统壳体严重变形或损坏。打开检漏仪,把检漏仪的检漏模式设置到吸枪检漏模式,用内置标准漏孔校准一下检漏仪,然后直接用吸枪对汽车动力电池系统(pack)箱体外壳的各个部位进行吸气检漏,也可以检漏仪上吸枪对准电池系统箱体的上下盖结合处缓慢移动。如果某个位置有泄漏,氦气通过吸枪进入到检漏仪中被检测到,检漏仪显示屏上会有泄漏率数值,并用记号笔准确标记吸枪所检测到的泄漏位置。实施例本实施例中的测试样品为新能源汽车用动力电池系统,其上壳为非金属类碳纤维smc材质,下壳为冷轧钢板dc01材质。一般来说,决定电池包箱体在密封性测试中的压力的大小由其上壳的可承受压差决定。测试中,需要利用plc控制器控制对真空箱和电池系统箱体的抽气速度,确保电池包箱体内外的压差不超过4kpa,当压力到达电池模组和单体电池的低气压要求值11.6kpa时,关闭抽气阀停止抽气,通过进气阀向样品内充入氦气,当压力≥11.6kp,且压差≥4kpa时,关闭进气阀,压力保持3min,通过与箱体连接的氦质谱检漏仪探测箱体内泄漏到腔内的氦气分子,如果有泄漏,则检漏仪有显示值,以表明电池包的漏率。设备所配备的检漏仪为德国inficon,型号为lds3000,检漏仪所配备的标准漏孔的漏率为10-7mbar·l/s,主要用于在每次测试前,对测试的准确度进行自校准,以此来提高检测的精度。在动力电池行业,目前尚无对电池系统箱体的漏率值与ip防护等级的准确的对应关系,但是在其他领域如航天、医疗等精密仪器行业的应用较早,因此这种检测方法具备在动力电池系统行业进行推广和应用的基础性研究。行业内漏率与漏孔等效直径的经验值关系如表1所示。表1行业内漏率范围和漏孔直径的对应表漏率范围(mbar·l/s)漏孔等效直径10410mm1021mm10.1mm10-20.01mm10-41μm(10-3mm)10-50.5μm(5×10-4mm)10-60.1μm(1×10-4mm)10-70.05μm(5×10-5mm)10-80.01μm(10-5mm)10-101nm(10-6mm)10-12angstrom(埃米,10-7mm)通过实际电池包的密封性测试,测得的漏率值为9.2×10-6mbar·l/s,但是很快漏率值下降为2.8×10-2mbar·l/s,表明电池包有泄漏。通过用吸枪法测试泄漏点,发现在电池包高压线接口处一处泄漏,该位置为泄漏点,且漏孔直径约为0.028mm。由于大气中氦气含量低,因此只要有泄漏就可以探测到,检测精度高,最小10-12mbar·l/s;在检漏过程中,都是由控制器通过压缩空气动作各个控制阀门,在很短的时间内就可以完成测试结果的确认和输出。被测样品充满氦气,放入真空容器中,可以测到总的漏率。通过吸枪法和等压式真空箱氦检法相结合,可以极大地提高电池系统箱体密封性检测的精度,以及提高查找箱体泄漏点的准确性,为动力电池系统研发人员升级改造产品提供了及时的信息反馈和有力的数据支撑。当前第1页12