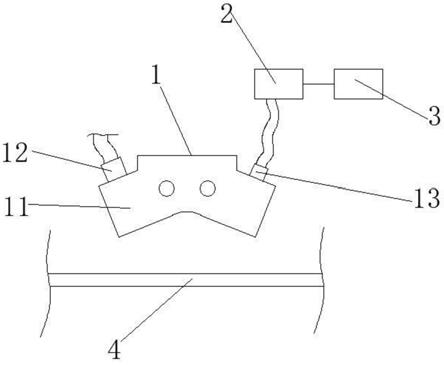
[0001]
本发明涉及定位技术领域,具体涉及一种镭射膜印刷定位检测装置及检测方法。
背景技术:[0002]
镭射膜表面光滑、颜色多变,具有防伪、耐磨、环保等特点,被广泛应用在烟酒、食品以及广告宣传等包装上。传统镭射印刷过程中需要经历镭射印刷、湿式复合、分切等过程,需要控制镭射膜与普通纸同步运行、控制分切精准定位。现有方案一般采用:(1)侧边空白处印刷定位点,定位难度大幅下降,但会造成浪费;(2)侧边处叠加印刷,由于受到全息图像的干扰,定位难度大幅提高;(3)衔接处印刷定位点,但单一图案识别度不足,容易与部分全息图像模式类似,识别度不足。因此,必须对现有的定位模式和定位检测方法进行改进。
技术实现要素:[0003]
本发明的目的在于克服现有技术的不足,提供一种镭射膜印刷定位检测装置及检测方法。
[0004]
为实现上述目的,本发明提供了如下技术方案来实现的:
[0005]
一种镭射膜印刷定位检测装置,其特征在于:包括激光传感器模块、回滞比较器、核心控制器、和设置在镭射膜上裁切衔接区的反射区,激光传感器模块包括激光传感器安装架、激光发射传感器、激光接收传感器、滤光镜、细缝块,回滞比较器负责接收激光接收传感器反馈的激光强度电信号序号,并进行高速去抖处理,核心控制器负责接收回滞比较器的去抖信号,分析信号序列是否与设定的编码序列一致,反射区包括若干间隔设置的反射条;
[0006]
激光传感器安装架上设有激光发射传感器安装孔、激光接收传感器安装孔,激光发射传感器安装在激光发射传感器安装孔内,激光接收传感器安装在激光接收传感器安装孔内,激光传感器安装架上位于激光发射传感器安装孔下方的位置设有细缝块安装槽,细缝块安装槽内安装有细缝块,激光传感器安装架上位于激光接收传感器安装孔下方的位置设有滤光镜安装槽,滤光镜安装槽内安装有滤光镜;
[0007]
激光发射传感器发射的激光信号透过细缝块上的细缝发射到反射区上,滤光镜的频率与激光发射传感器、激光接收传感器相匹配,确保滤光后的信号为所需的激光信号,激光接收传感器负责接收经过滤光镜后的激光反射信号,并转换为电信号输出给回滞比较器。
[0008]
细缝块上细缝的宽度小于0.2mm。
[0009]
反射区包括间隔设置的若干强反射条、弱反射条。
[0010]
除最前侧的强反射条外,剩余的强反射条和弱反射条宽度相同,最前侧的强反射条的宽度为剩余反射条宽度的两倍。
[0011]
最前侧的强反射条的宽度为0.4mm,剩余强反射条、弱反射条的宽度为0.2mm,反射区的长度为2mm。
[0012]
一种镭射膜印刷定位检测方法,采用镭射膜印刷定位检测装置实现,其特征在于:包括如下步骤:
[0013]
步骤1:在镭射膜的裁切衔接区印刷反射区,反射区包括若干强反射条和弱反射条,若干强反射条和弱反射条以特定顺序设置从而形成特定编码序列,将该特定编码序列输入核心控制器中作为预设值;
[0014]
步骤2:激光发射传感器连续发射特定频率激光,反射区随镭射膜的匀速移动经过激光传感器模块下方,激光经反射区中的强反射条、弱反射条反射后由激光接收传感器接收;
[0015]
步骤3:激光接收传感器接收的激光信号传输给回滞比较器,回滞比较器对信号进行去抖处理后发送至核心控制器;
[0016]
步骤4:核心控制器分析反馈信号,并与预设的特定编码序列值进行比较,从而判断当前镭射膜所处的位置,对镭射膜进行精确定位。
[0017]
步骤1中,反射区中强反射条和弱反射条的设置顺序为,最前侧设置0.4mm宽的强反射条用于产生起始检测信号的,在该反射条后循环设置0.2mm宽的弱反射条和0.2mm宽的强反射条各四根,反射区的整体宽度为2mm。
[0018]
与现有技术相比,本发明的有益效果是:通过设定特定顺序的强反射条和弱反射条从而得到特定编码序列值,向反射区发射激光信号从而得到反射信号,再通过回滞比较器、核心处理器处理分析信号,并与特定编码序列值比较以判断镭射膜当前位置,对镭射膜进行精确定位,为湿式复合提供速度反馈信号进行同步控制,或未分切环节提供启动信号。
附图说明
[0019]
图1为本发明一种镭射膜印刷定位检测装置的结构示意图;
[0020]
图2为本发明中激光传感器模块的剖视图;
[0021]
图3为本发明中激光传感器安装架的仰视图;
[0022]
图4为本发明中镭射膜的结构示意图;
[0023]
图5为本发明中反射区的结构示意图;
[0024]
图6为本发明中激光反射信号的变化示意图。
具体实施方式
[0025]
下面结合附图1-6对本发明的实施例进行详细阐述。
[0026]
一种镭射膜印刷定位检测装置,包括激光传感器模块1、回滞比较器2、核心控制器3、和设置在镭射膜4上裁切衔接区41的反射区5,裁切衔接区41位于镭射膜4上两个有效印刷区42之间;激光传感器模块1包括激光传感器安装架11、激光发射传感器12、激光接收传感器13、滤光镜14、细缝块15,回滞比较器2负责接收激光接收传感器13反馈的激光强度电信号序号,并进行高速去抖处理,核心控制器3负责接收回滞比较器2的去抖信号,分析信号序列是否与设定的编码序列一致,反射区5包括若干间隔设置的反射条;激光传感器安装架11上设有激光发射传感器安装孔111、激光接收传感器安装孔112,激光发射传感器12安装在激光发射传感器安装孔111内,激光接收传感器13安装在激光接收传感器安装孔112内,激光传感器安装架11上位于激光发射传感器安装孔111下方的位置设有细缝块安装槽113,
细缝块安装槽113内安装有细缝块15,激光传感器安装架11上位于激光接收传感器安装孔112下方的位置设有滤光镜安装槽114,滤光镜安装槽114内安装有滤光镜14;激光发射传感器12发射的激光信号透过细缝块15上的细缝发射到反射区5上,滤光镜14的频率与激光发射传感器12、激光接收传感器13相匹配,确保滤光后的信号为所需的激光信号,激光接收传感器13负责接收经过滤光镜14后的激光反射信号,并转换为电信号输出给回滞比较器2。
[0027]
作为优选,细缝块15上细缝的宽度小于0.2mm。
[0028]
作为优选,反射区5包括间隔设置的若干强反射条51、弱反射条52。
[0029]
作为优选,除最前侧的强反射条51外,剩余的强反射条51和弱反射条52宽度相同,最前侧的强反射条51的宽度为剩余反射条宽度的两倍。
[0030]
作为优选,最前侧的强反射条51的宽度为0.4mm,剩余强反射条51、弱反射条52的宽度为0.2mm,反射区5的宽度为2mm。
[0031]
一种镭射膜印刷定位检测方法,采用镭射膜印刷定位检测装置实现,包括如下步骤:
[0032]
1、在镭射膜的裁切衔接区印刷反射区,反射区包括若干强反射条和弱反射条,若干强反射条和弱反射条以特定顺序设置从而形成特定编码序列,将该特定编码序列输入核心控制器中作为预设值;
[0033]
2、激光发射传感器连续发射特定频率激光,激光经细缝板上的细缝后发射,反射区随镭射膜的匀速移动经过激光传感器模块下方,激光经反射区中的强反射条、弱反射条反射后由激光接收传感器接收;
[0034]
3、激光接收传感器接收的激光信号传输给回滞比较器,回滞比较器对信号进行去抖处理后发送至核心控制器;
[0035]
4、核心控制器分析反馈信号,并与预设的特定编码序列值进行比较,从而判断当前镭射膜所处的位置,对镭射膜进行精确定位。
[0036]
步骤1中,反射区包括最前侧用于产生起始检测信号的0.4mm宽的强反射条、循环设置在该0.4mm宽的强反射条后的0.2mm宽的弱反射条和0.2mm宽的强反射条,反射区的长度为2mm。
[0037]
激光射在强反射条上,反射后最终得到一个高数值的信号,射在弱反射条上,反射后最终得到一个低数值的信号。
[0038]
最前侧的强反射条宽度较宽,得到高数值的信号的持续时间长,有别于其余反射条产生的信号,从而可作为起始检测信号。
[0039]
通过获得的信号与预设值做对比,确定获得的信号位于预设值的位置,即可得到现在激光射在反射区中的精确位置,从而计算出隔离膜的所处位置。
[0040]
通过设计和检测衔接区的特定编码序列,在不浪费印刷区的情况下实现精确定位;采用激光传感发射器前安装细缝块和回滞比较器对接收信号过滤去抖等操作,提高编码序列的可识别度和识别准度;通过复杂特定编码序列和模糊检测方案,确保检测结果不受正常印刷图案干扰,大幅提高识别准确性。
[0041]
以上所述仅是本发明的优选实施方式,本发明的保护范围并不仅局限于上述实施例,凡属于本发明思路下的技术方案均属于本发明的保护范围。应当指出,对于本技术领域的普通技术人员来说,在不脱离本发明原理前提下的若干改进和润饰,这些改进和润饰也
应视为本发明的保护范围。