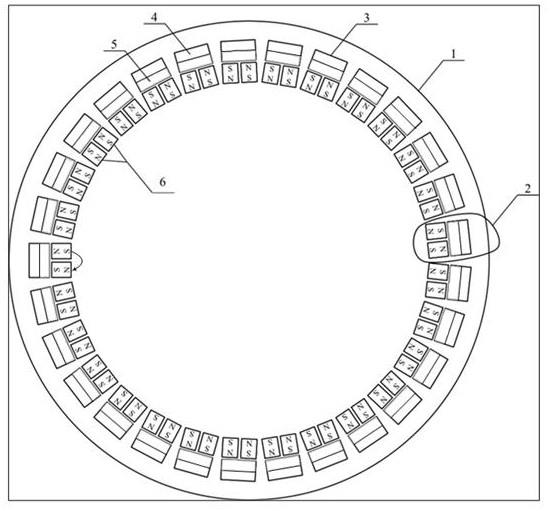
1.本发明属于无损检测技术领域,涉及一种金属管道裂纹检测传感器及检测方法。
背景技术:2.管道在石油、化工等行业得到了广泛的应用,主要起到了输送石油或天然气的作用,但是由于在制造过程中加工工艺的水平有限,管道中存在夹渣、缩孔、疏松等缺陷,在服役过程中由于压力、潮湿、高温差等复杂多变的服役环境,管道会产生裂纹,影响管道的结构安全性,严重时会造成管道泄漏,造成重大的安全生产事故与经济损失,因此定期对金属管道裂纹进行高效定位及精准定量评估具有重要意义。
3.传统的检测方法包括漏磁检测、超声检测等,这些方法需通过检测探头/传感器在管道内部运行对裂纹检测,但是由于运行速度慢,检测效率较低,检测时间过长,影响管道的正常生产运行,造成一定的经济损失,且设备结构复杂、成本较高,因此设计开发一种检测效率高、结构相对简单、可靠性高的金属管道裂纹检测传感器及检测方法具有重要的工程应用价值。
技术实现要素:4.为了解决上述问题,本发明提供一种金属管道裂纹检测传感器,能够对金属管道裂纹进行快速、精准的在线检测,可靠性高,适用性强,成本低,具有重要的工程应用价值。
5.本发明的另一目的是,提供一种金属管道裂纹检测方法。
6.本发明所采用的技术方案是,一种金属管道裂纹检测传感器,包括骨架,骨架为环形,与待测管道内部相匹配;传感单元,结构相同的多个所述传感单元等间距圆周排列的方式安装于骨架单侧;摄像头,用于拍摄传感单元中磁流体的形态;每个所述传感单元包括永磁铁组件,所述永磁铁组件包括一个或两个永磁铁,每个永磁铁的两个磁极均沿径向分布;容器,容器内充满了透明溶液与磁流体,透明溶液与磁流体密度相同,互不相容、且不发生化学反应;其中,骨架在径向上不阻挡传感单元。
7.进一步的,所述永磁铁组件中两个永磁铁同侧的磁极相反,两个永磁铁间距小于相邻两个传感单元的间距。
8.进一步的,所述容器位于一组永磁铁的外侧,靠近金属管道内壁的位置。
9.进一步的,所述传感单元与待测金属管道内壁的距离为壁厚的1/10。
10.进一步的,所述容器的形状、尺寸和一组永磁铁的形状、尺寸相匹配。
11.进一步的,所述容器的内壁存在均匀、透明的疏油涂层。
12.进一步的,所述骨架与待测管道同轴。
13.进一步的,所述骨架、摄像头安装于牵引装置上。
14.进一步的,所述摄像头位于骨架的轴线上,且沿轴线方向与骨架的距离等于骨架的外径。
15.一种金属管道裂纹检测传感器的检测方法,采用上述金属管道裂纹检测传感器,具体按照以下步骤进行:步骤1,建立裂纹深度标定曲线;骨架与传感单元置于无裂纹标准管道内,骨架与无裂纹标准管道同轴,通过摄像头对传感单元进行拍摄,得n个传感单元检测无裂纹标准管道时对应磁流体的区域分别为s1、s2、s3、s4…
sn;在多个相同的标准管道上分别加工深度不同的周向裂纹,拖动骨架、传感单元与摄像头一起在标准管道内以恒定速度进行轴向运动,传感单元通过裂纹时,通过摄像头得n个传感单元检测深度不同裂纹时磁流体的区域分别为s
j,1
、s
j,2
、s
j,3
、s
j,4
…sj,n
,j表示对应的裂纹深度,计算s
j,1
、s
j,2
、s
j,3
、s
j,4
…sj,n
分别在s1、s2、s3、s4…
sn上的投影面积为δs
j,1
、δs
j,2
、δs
j,3
、δs
j,4
…
δs
j,n
,则sj=(δs
j,1
+δs
j,2
+δs
j,3
+δs
j,4
…
+δs
j,n
)/n,sj裂纹深度为j的信号特征;以多个不同裂纹深度j为纵坐标,以对应的sj为横坐标,得裂纹深度与信号特征的关联曲线,该曲线进行二次拟合得拟合公式h=as2+bs+c,其中h为裂纹深度,s为信号特征,a、b和c分别为二次项系数、一次项系数和常数项;步骤2,金属管道裂纹检测;拖动骨架、传感单元与摄像头一起在待测管道内以恒定速度进行轴向运动,以2v/d的角速度进行周向运动;通过摄像头对传感单元进行拍摄,得任意时刻ti时n个传感单元对应的信号特征st
i,1
、st
i,2
、st
i,3
、
…
st
i,n
, st
i,n
表示第n个传感器在时刻ti所检测管壁位置的信号特征;若其中f个传感单元对应的信号特征大于需要检出的裂纹深度对应的信号特征,则认为在ti时所述f个传感单元所检测的管壁位置处存在裂纹,根据弧长公式计算得到裂纹的总长度为fdπ/n,各传感单元投影在管壁位置处的裂纹平均深度为ast
i,f2
+bst
i,f
+c,st
i,f
表示任意时刻ti时第f个传感单元对应的信号特征。
16.本发明的有益效果是:1、本发明通过测磁流体的变形对金属管道裂纹进行检测,通常电磁噪声频率较高、无固定方向,对磁流体的变形影响较弱,对检测信号影响较低,从而使得本发明传感器抗环境电磁噪声干扰能力较强,精准度更高。
17.2、由于本传感器中透明溶液与磁流体密度相同,因此两者在抖动和滑动时相互之间不会产生额外的受力情况,使得传感器在管道内发生抖动、滑动等情况并不会影响检测结果,大幅增强了本发明传感器的可靠性和适用性。
18.3、本发明传感器结构简单、成本低,检测方法易于操作,可实现金属管道裂纹快速检测,克服了检测效率和检测精度的矛盾;同时能够对裂纹进行精准定位,获得裂纹的长度信息及深度信息,具有较高的工程应用价值。
附图说明
19.为了更清楚地说明本发明实施例或现有技术中的技术方案,下面将对实施例或现有技术描述中所需要使用的附图作简单地介绍,显而易见地,下面描述中的附图仅仅是本发明的一些实施例,对于本领域普通技术人员来讲,在不付出创造性劳动的前提下,还可以根据这些附图获得其他的附图。
20.图1为本发明实施例裂纹检测传感器的结构示意图。
21.图2为本发明实施例中检测系统结构示意图。
22.图中,1.骨架,2.传感单元,3.容器,4.透明溶液,5.磁流体,6.永磁铁,7.摄像头,8.牵引装置。
具体实施方式
23.下面将结合本发明实施例,对本发明实施例中的技术方案进行清楚、完整地描述,显然,所描述的实施例仅仅是本发明一部分实施例,而不是全部的实施例。基于本发明中的实施例,本领域普通技术人员在没有做出创造性劳动前提下所获得的所有其他实施例,都属于本发明保护的范围。
24.实施例1,一种金属管道裂纹检测传感器,包括骨架1、传感单元2和摄像头7;骨架1为环形,与待测管道内部相匹配,骨架1与待测管道同轴,骨架1单侧安装有多个等间距圆周排列的、结构相同的传感单元2,骨架1在径向上不阻挡传感单元2;每个传感单元2包括永磁铁组件和容器3,永磁铁组件包括一个或两个永磁铁6,每个永磁铁6的两个磁极均沿径向分布,产生如图1所示的磁感线,便于管道中裂纹对其进行切割,而生成感应磁场。
25.容器3内充满了透明溶液4与磁流体5,透明溶液4与磁流体5密度相同,互不相容、且不发生化学反应;当传感器发生抖动时,磁流体5的形状不会发生变化,保证了传感器在抖动、滑动等情况下的精度。透明溶液4不能过少,保证磁流体5变形后不会接触到容器3的顶部,提高检测精度;如果透明溶液4过少(即磁流体5过多),磁流体5变形后容易接触到容器3的顶部,导致检测精度降低;如果透明溶液4过多,磁流体5距离待测管道太远,影响检测精度;在一些实施例中,透明溶液4与磁流体5体积比4:1~1:1。
26.容器3位于一组永磁铁6的外侧(靠近金属管道内壁的位置),当管道存在裂纹时,切割磁感线产生磁场,越靠近管道内部磁场强度越强,检测信号更强。
27.摄像头7,用于拍摄传感单元2中磁流体5的形态。
28.骨架1为白色,白色作为背景色,磁流体5通常多为黑色,这样摄像头7拍摄的照片对比度较强,便于提取信号,提高准确性。
29.永磁铁组件中两个永磁铁6同侧的磁极相反,两个永磁铁6构成的传感单元2的检测效果优于一个永磁铁6构成的传感单元2。每个传感单元2中两个永磁铁6间距小于相邻两个传感单元2的间距,若相邻两个传感单元2的间距太小,产生的磁感线路径会发生变化;若间距太大,会导致检测精度降低。永磁铁组件中的两个永磁铁6间距范围越小越好(间距为0),间距越小裂纹切割磁感线生成的感应电压越强,提升检测精度。
30.永磁铁6的形状为长方体,产生的磁感线更均匀,便于切割磁感线。
31.容器3的形状、尺寸和一组永磁铁6的形状、尺寸相匹配,以保证检测分辨率;容器3为长方体,且为透明的中空结构,保证溶液不泄露的情况下,壁厚越小越好,容器3的内壁存在均匀、透明的疏油涂层。
32.传感单元2与待测金属管道内壁的距离理论上越近检测信号的灵敏度越高,越近裂纹切割的磁感线越多。在一些实施例中,传感单元2与待测金属管道内壁的距离为壁厚的1/10。
33.磁流体5在磁场作用下易变形,透明溶液4化学性能稳定,透明,与磁流体5密度相同,不与装置发生化学反应即可;透明溶液4可采用氯化钠溶液。
34.本发明实施例的检测原理是金属管道裂纹切割运动的永磁铁6的磁力线而生成感应磁场,磁流体5在感应磁场的作用下会发生变形,即遇到裂纹时,磁流体5会发生变形,通过对不同裂纹下磁流体5的变化程度进行标定,可得到裂纹的深度与长度。
35.实施例2,一种金属管道裂纹检测传感器的检测方法,具体按照以下步骤进行:步骤1,建立裂纹深度标定曲线;如图2所示,将摄像头7、骨架1、传感单元2固定在无裂纹标准管道内部的牵引装置8之上,摄像头7位于传感器骨架1的轴线上,且沿轴线方向与传感器骨架1的距离等于传感器骨架1的外径d。通过摄像头7对传感单元2进行拍摄,得n个传感单元2检测无裂纹标准管道时对应磁流体5的区域分别为s1、s2、s3、s4…
sn,如图1所示;在多个相同的标准管道上分别加工深度不同的周向裂纹,拖动骨架1与传感单元2一起在标准管道内以恒定速度v进行轴向运动,传感单元2通过裂纹时,通过摄像头7对传感单元2进行拍摄,得n个传感单元2检测深度不同裂纹的磁流体5的区域分别为s
j,1
、s
j,2
、s
j,3
、s
j,4
…sj,n
,j表示对应的裂纹深度,计算磁流体5的区域s
j,1
、s
j,2
、s
j,3
、s
j,4
…sj,n
分别在磁流体5的区域s1、s2、s3、s4…
sn上的投影面积为δs
j,1
、δs
j,2
、δs
j,3
、δs
j,4
…
δs
j,n
,则sj=(δs
j,1
+δs
j,2
+δs
j,3
+δs
j,4
…
+δs
j,n
)/n,sj裂纹深度为j的信号特征;以多个不同裂纹深度j为纵坐标,以sj为横坐标,得裂纹深度与信号特征的关联曲线,该曲线进行二次拟合得拟合公式h=as2+bs+c,其中h为裂纹深度,s为信号特征,a、b和c分别为二次项系数、一次项系数和常数项。
36.具体的,在9个相同的标准管道上分别加工深度不同的周向裂纹,深度分别为0.1d、0.2d、0.3d、0.4d、0.5d、0.6d、0.7d、0.8d和0.9d,d表示管壁厚。
37.传感单元2通过深度为0.1d的周向裂纹时,通过摄像头7得n个传感单元2中磁流体5的区域分别为s
1,1
、s
1,2
、s
1,3
、s
1,4
…s1,n
,s
1,1
代表第一个传感单元2检测0.1d深度裂纹时磁流体5的区域,s
1,n
代表第n个传感单元2检测0.1d深度裂纹时磁流体5的区域。计算n个传感单元2检测0.1d深度裂纹时磁流体5的区域s
1,1
、s
1,2
、s
1,3
、s
1,4
…s1,n
分别在s1、s2、s3、s4…
sn上的投影面积为δs
1,1
、δs
1,2
、δs
1,3
、δs
1,4
…
δs
1,n
,计算周向裂纹深度为0.1d的信号特征s1=(δs
1,1
+δs
1,2
+δs
1,3
+δs
1,4
…
+δs
1,n
)/n。
38.同理,计算当传感单元2通过深度为0.2d、0.3d、0.4d、0.5d、0.6d、0.7d、0.8d和0.9d的周向裂纹,分别对应的信号特征s2、s3、s4、s5、s6、s7、s8和s9。以0.1d、0.2d、0.3d、0.4d、0.5d、0.6d、0.7d、0.8d和0.9d为纵坐标,以s1、s2、s3、s4、s5、s6、s7、s8和s9为横坐标,得裂纹深度与信号特征的关联曲线,该曲线进行二次拟合得拟合公式h=as2+bs+c,其中h为裂纹深
度,s为信号特征,a、b和c分别为二次项系数、一次项系数和常数项,参数a、b和c根据拟合的曲线形状得到。
39.步骤2,金属管道裂纹检测;拖动骨架1与传感单元2一起在待测管道内以恒定速度v进行轴向运动,以2v/d的角速度进行周向运动,使传感单元相对管壁的轴向速度与周向速度相同,保证检测精度;通过摄像头7对传感单元2进行拍摄,得任意时刻ti时n个传感单元2对应的信号特征st
i,1
、st
i,2
、st
i,3
、
…
st
i,n
, st
i,n
表示第n个传感器在时刻ti所检测管壁位置的信号特征;若其中f个传感单元2对应的信号特征大于s1,则认为在ti时所述f个传感单元2所检测的管壁位置处存在裂纹,根据弧长公式计算得到裂纹的总长度为fdπ/n,各传感单元2投影在管壁位置处的裂纹平均深度为ast
i,f2
+bst
i,f
+c,st
i,f
表示任意时刻ti时第f个传感单元2对应的信号特征。
40.其中,s1表示裂纹深度为0.1d的信号特征,认为只有深度大于0.1d的裂纹有检出的必要,若是实际检测中大于0.2d深度的裂纹才需要检出,也可以把s1替换为s2。
41.本技术传感器在管道内运行的恒定速度v越大,裂纹切割磁感线产生的磁场强度越大,检测信号的信号特征越大,检测精度越高,同时恒定速度v越大,单位时间内可检的管道越多,即检测效率越高,克服了检测效率和检测精度的矛盾。
42.以上所述仅为本发明的较佳实施例而已,并非用于限定本发明的保护范围。凡在本发明的精神和原则之内所作的任何修改、等同替换、改进等,均包含在本发明的保护范围内。