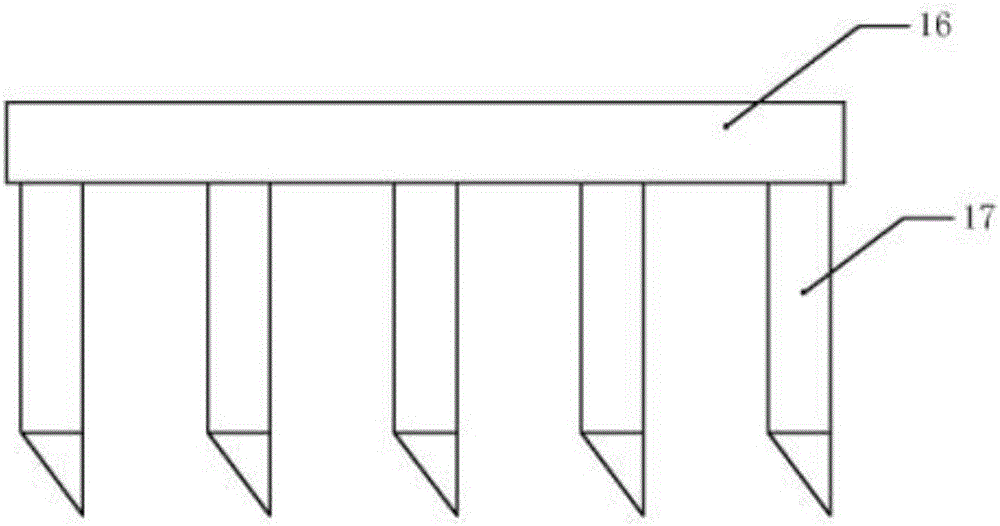
本发明属于五金机械加工设备领域,涉及一种钢板双边剪切过程中,通过数控装置来控制钢板剪切间隙的双边剪主刀间隙控制装置及计算方法。
背景技术:
:在中厚钢板轧制生产线中,双边剪是其中的重要设备之一,负责在精整工序中把轧制后已经经过矫直的钢板两侧多余的部分切除,并同时经该机组中的碎边剪把切除下来的边丝切碎成段,从废料运输链传送到废料斗;双边剪切后的钢板通过运输辊道,运输到指定位置进行下一步加工。中厚钢板生产线的精整工序中使用双边剪剪切钢板两边,剪切质量的好坏直接关系客户的体验度,合适的剪刃间隙值是制约双边剪剪切质量的关键因素。由于不同材质的钢板,材料系数不相同,同一材质的钢板在不同的温度段,材料系数也不相同,同一材质钢板的厚度不同也会导致材料系数不同,因此钢板的材质、钢板的温度以及钢板的厚度都会影响钢板切割后剪刃间隙值。现在的实际生产过程中,工人多是根据经验及质量标准进行调整,所生产钢板的双边剪口质量波动大,工人对每块钢板都要进行计算以确定间隙值,这不仅增加了劳动强度,还会因经验等人为原因造成剪切变形,高毛刺等质量事故,从而推高生产成本。技术实现要素:有鉴于此,本发明为了解决实际生产过程中,工人根据经验或者计算确定钢板间隙值的方法容易造成钢板剪切变形,高毛刺等问题,提供一种能实现实时测量、快速计算且结果有效、误差小的双边剪主刀间隙控制装置及计算方法。为达到上述目的,本发明提供如下技术方案:包括进料装置和出料装置,进料装置包括输送装置和传动电机,输送装置上放置钢板,输送装置的上方设有力矩电机和减速机,进料装置的出料端连接有出料装置,进料装置和出料装置之间的上方设有连杆,连杆上转动安装有若干钢板剪,连杆与减速机、力矩电机依次连接,输送装置上安装有高温计,高温计上信号连接有PLC控制系统,PLC控制系统上还连接有工控机,工控机上连接MES系统。本基础方案的原理在于:输送装置将待加工的钢板传递至连杆下方,输送装置上的高温计对钢板的温度进行监测,MES系统对钢板的厚度和材质等基本信息进行监测,工控机对MES系统收集的数据进行处理,高温计和工控机将收集的钢板信息传递至PLC控制系统,PLC控制系统实时接收工控机传输的钢板数据以及高温计传输的温度数据并对其进行有效处理,通过PLC内部设定的程序计算钢板的剪刃间隙值。通过PLC控制系统控制力矩电机,并接受安装在减速机后编码器的信号,力矩电机带动减速机,减速机传动至传动连杆,传动连杆带动调整楔体根据给定值实时调整剪刃间隙值。进一步,输送装置和出料装置均为传送带或者输送辊。进一步,钢板剪的下端呈楔体状,钢板剪的材质为9CrSi、T8、T10、6CrW2Si、Cr12MoV、W18Cr4V、42CrMo、LD、W6Mo4V2、W18Cr4V优质合金的一种。进一步,输送装置的外侧固定安装有工业相机。进一步,PLC控制系统包括开关模块、接受模块、计算模块和报警模块,开关模块用来控制钢板剪的开启和关闭,接受模块用来接受工控机和高温计传递过来的钢板数据,将反馈的钢板数据传递至计算模块进行处理,钢板剪上的剪刃磨损时,报警模块警示操作者更换钢板剪。一种双边剪主刀间隙控制装置的计算方法,包括以下步骤:A、将待加工的钢板置于输送装置上,开启传动电机,使得钢板沿着输送装置的输送方向传送;B、钢板传送至连杆下方时,高温计将感应到的钢板温度传递给PLC控制系统中的接受模块;C、MES系统将检测到的钢板厚度、材质的数据传递给工控机,所述工控机将数据处理后传递给PLC控制系统中的接受模块,PLC控制系统中的接受模块实时接收工控机传输的钢板数据及高温计传输的温度数据并对其进行有效处理,通过PLC控制系统内部设定的程序执行待剪切钢板的剪刃间隙值的计算;D、PLC控制系统根据计算得到的剪刃间隙值来控制力矩电机,并接受安装在减速机后编码器的信号,力矩电机带动减速机,减速机传动至传动连杆,传动连杆调整钢板剪之间的距离后对钢板进行剪切。进一步,剪刃间隙值的计算公式为:ΔD=a×h×(Mmax-M)/Mmax-[(T-150℃)/50℃]×0.1。其中,ΔD为双边剪主刀间隙预设定值,单位为mm,a为钢板弹性系数;板厚6-8mm时,钢板弹性系数取0.08,板厚8-10mm时,钢板弹性系数取0.09,板厚12-18mm时,钢板弹性系数取0.095,板厚20-30mm时,钢板弹性系数取0.1,板厚32-40mm时,钢板弹性系数取0.095;h为钢板厚度,单位为mm;Mmax为刀片最大剪切量,单位为吨,M为累计剪切量,单位为吨;T为温度,单位为℃。本发明的有益效果在于:该双边剪主刀间隙控制装置与整个控制装置计算方法的结合,实现了钢板精整工序双边剪主刀间隙最优值的的快速有效计算,整体控制装置简单,造价低廉,程序轻巧,计算方便且误差小,执行效率高;连杆上的钢板剪可以根据来料钢板的厚度,温度及材料系数给出最优的间隙值,进而指导力矩电机调整减速器的剪切速度和剪切位置,有效减少钢板的剪切变形,高毛刺等质量事故,提高经济效益。附图说明为了使本发明的目的、技术方案和有益效果更加清楚,本发明提供如下附图进行说明:图1为本发明双边剪主刀间隙控制装置的结构示意图;图2为本发明实施例中钢板剪的结构示意图。具体实施方式下面将结合附图,对本发明的优选实施例进行详细的描述。说明书附图中的附图标记包括:进料传送带11、传动电机12、出料传送带13、钢板14、高温计15、连杆16、钢板剪17、力矩电机18、减速机19、工业相机20、PLC控制系统21、MES系统22、工控机23。MES系统22是制造执行管理MES系统22,它是企业信息集成的纽带,是实施企业敏捷制造战略和实现车间生产敏捷化的基本技术手段。工控机23是一种专门为工业现场而设计的计算机,具有较高的防磁、防尘、防冲击的能力。如图1所示的双边剪主刀间隙控制装置,从左到右依次为出料装置和进料装置,出料装置和进料装置均设置为传送带,进料装置的传送带下设置传动电机12,待剪切的钢板14在传送带的传输下不断向左传动。进料传送带11和出料传送带13之间的上方固定安装如图2所示的钢板14剪的连杆16,输送装置的外侧固定安装两个工业相机20,该工业相机20能够实时监测钢板14的情况。连杆16的上方依次连接减速机19、力矩电机18。进料传送带11上安装高温计15,高温计15上连接PLC控制系统21,PLC控制系统21上连接工控机23和MES系统22。PLC控制系统21包括开关模块、接受模块、计算模块和报警模块,开关模块用来控制钢板剪17的开启和关闭,接受模块用来接受工控机23和高温计15传递过来的钢板14数据,将反馈的钢板14数据传递至计算模块进行处理,钢板剪17上的剪刃磨损时,报警模块警示操作者更换钢板剪17。以碳钢为例,该双边剪主刀间隙控制装置的计算方法如下:A、将待加工的碳钢钢板置于输送装置上,开启传动电机,使得碳钢钢板沿着输送装置的输送方向传送;B、碳钢钢板传送至连杆下方时,高温计将感应到的碳钢钢板温度传递给PLC控制系统中的接受模块;C、MES系统将检测到的钢板厚度、材质的数据传递给工控机,工控机将数据处理后传递给PLC控制系统中的接受模块,PLC控制系统中的接受模块实时接收工控机传输的碳钢钢板数据及高温计传输的温度数据并对其进行有效处理,通过PLC控制系统内部设定的程序执行待剪切钢板的剪刃间隙值的计算;D、PLC控制系统根据计算得到的剪刃间隙值来控制力矩电机,并接受安装在减速机后编码器的信号,力矩电机带动减速机,减速机传动至传动连杆,传动连杆调整钢板剪之间的距离后对碳钢钢板进行剪切。进一步,剪刃间隙值的计算公式为:ΔD=a×h×(Mmax-M)/Mmax-[(T-150℃)/50℃]×0.1。其中,ΔD为双边剪主刀间隙预设定值,单位为mm,a为钢板弹性系数;板厚6-8mm时,碳钢钢板弹性系数取0.08,板厚8-10mm时,碳钢钢板弹性系数取0.09,板厚12-18mm时,碳钢钢板弹性系数取0.095,板厚20-30mm时,碳钢钢板弹性系数取0.1,板厚32-40mm时,碳钢钢板弹性系数取0.095;h为钢板厚度,单位为mm;Mmax为刀片最大剪切量,单位为吨,M为累计剪切量,单位为吨;T为温度,单位为℃。碳钢钢板剪刃间隙的间隙计算值以及计算值与实验值的误差值见表一:表一:厚度(mm)6810121416182022最佳间隙(mm)0.50.70.91.11.31.61.72.02.2计算值(mm)0.480.720.91.1.41.331.521.712.02.2误差值(mm)-0.02+0.020+0.04+0.03-0.08+0.0100厚度(mm)242628303234363840最佳间隙(mm)2.42.62.83.03.13.23.53.63.7计算值(mm)2.42.62.83.03.043.233.423.613.8误差值(mm)0000-0.06+0.03-0.08+0.01+0.1从上述计算的绝对误差可以看出,该双边剪主刀间隙值计算公式不仅简化了计算过程,且计算数据误差很小,完全满足工艺生产要求。最后说明的是,以上优选实施例仅用以说明本发明的技术方案而非限制,尽管通过上述优选实施例已经对本发明进行了详细的描述,但本领域技术人员应当理解,可以在形式上和细节上对其作出各种各样的改变,而不偏离本发明权利要求书所限定的范围。当前第1页1 2 3