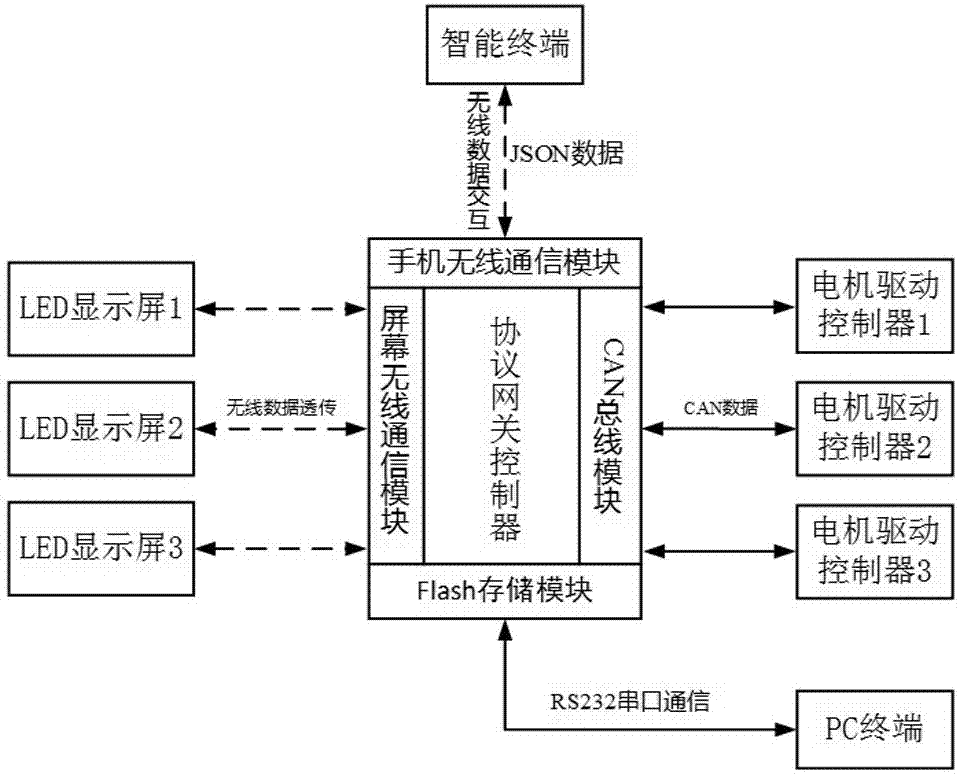
本发明涉及智能旋转标识柱领域,具体为一种智能共享信息导向标识柱控制系统。
背景技术:
目前,市场上使用的智能标识柱控制器,大多采用有线控制方式和集中控制方式,不利于维护升级和多屏扩展。其中,有线控制方式是通过串口与控制器对接实现显示信息的下载,不利于多屏扩展,且旋转角度有限,智能度低。集中控制管理方式是一个中央控制器控制一个电机驱动控制器,从而使指路牌旋转,极大增加了成本。为此,迫切需要一种新的装置,以解决上述问题。技术实现要素:本发明的发明目的在于:针对现有的智能标识柱控制器普遍存在不利于扩展,维护成本高等问题,提供一种智能共享信息导向标识柱控制系统。本发明通过一个中央控制器,能同时控制多个指路牌转动而不发生冲突,并且可以实时显示各种信息。同时,本发明有效解决了现有智能标识柱控制器普遍存在数据通信速度慢的问题,具有较好的应用效果和较高的应用价值。为了实现上述目的,本发明采用如下技术方案:智能共享信息导向标识柱控制系统,包括中央控制器、与中央控制器通过can总线连接的电机驱动控制器;所述中央控制器包括第一mcu控制单元、电源管理模块、蓝牙无线通信模块、2.4g无线通信模块、4g无线通信模块、can总线接口模块、flash存储模块、拨码开关、rs232串行总线模块;所述电源管理模块、can总线接口模块、flash存储模块和rs232串行总线模块与第一mcu控制单元连接;所述蓝牙无线通信模块、4g无线通信模块和2.4g无线通信模块与第一mcu控制单元相连;所述拨码开关通过i/o口与第一mcu控制单元相连;所述电机驱动控制器包括与第一mcu控制单元连接的第二mcu控制单元、电源管理模块、can总线通信模块、电机模块、拨码开关、光电限位感应器;所述电源管理模块、can总线通信模块通过串行总线与第二mcu控制单元相连;所述电机模块通过i/o口与第二mcu控制单元连接;所述拨码开关通过i/o口与第二mcu控制单元相连;所述光电限位感应器通过光耦隔离后与第二mcu控制单元连接;所述电机驱动控制器可通过can总线串联,由拨码开关进行编号;由can总线构成一个局部网络,并由中央控制器发布指令,各电机驱动控制器实现电机运动并反馈。所述中央控制器还包括蜂鸣器,所述蜂鸣器通过i/o口与第一mcu控制单元相连。所述中央控制器还包括led指示灯光模块,所述led指示灯光模块通过i/o口与第一mcu控制单元相连。所述蓝牙无线通信模块与智能终端通过蓝牙无线连接,2.4g无线通信模块与显示屏无线连接,4g无线通信模块与服务器连接,用于系统维护。所述中央控制器的蜂鸣器和led指示灯光模块用于实现状态指示。所述中央控制器的rs232为传统串口连接保留功能,可以实现串口数据传输。所述第一mcu控制单元、第二mcu控制单元分别为stm32f103、stm32f205系列芯片。该装置工作时,第二mcu控制器的can总线接收来自第一mcu中央控制器发出的旋转指令并向电机模块发送执行信息,同时向第一mcu中央控制器上发故障信息。与第二mcu电机驱动控制器连接的光电限位感应器用于为电机寻找机械零点。同时,与第二mcu电机驱动控制器连接的led指示灯光模块为状态指示标志。本发明中,智能共享信息导向标识柱控制系统包括中央控制器和若干电机驱动控制器,各控制器通过can总线构成一个局部网络。其中,中央控制器接收智能终端的指令并集中处理;电机驱动控制器接收中央控制器的can信号并执行相应动作。在一个具体实例中,中央控制器中的第一mcu控制单元采用stm32f103系列芯片,其安全性高、处理能力强、计算性能好。can总线模块使用can2.0b协议,与mcu连接,可以实现与各电机驱动控制器的信息传递。flash存储模块采用w25q64,可存储最大8m字节数据,与mcu连接串行总线蓝牙无线通信模块与mcu相连可与智能终端无线通信2.4g无线通信模块通过与mcu相连,可与显示屏无线通信,4g无线通信模块与mcu相连,可与服务器通信,用于系统维护。同时,拨码开关、蜂鸣器、led指示灯光模块通过i/o口与mcu相连,可以实现故障警告、状态指示功能。而在电机驱动控制器中,串行总线can总线模块使用can2.0b协议,与第二mcu连接,可以实现与中央控制器的信息传递。电机模块与第二mcu相连,可以实现电机控制。拨码开关与第二mcu相连,可以实现不同节点的编号。光电限位感应器通过光耦隔离后与第二mcu连接,可为电机寻找机械零点。电机驱动控制器的led指示灯光模块可以实现状态指示。进一步,本发明提供采用前述智能共享信息导向标识柱控制系统的旋转装置,包括支撑单元、伺服电机、电机安装座、内啮合小齿轮、内齿圈、悬臂定子、连接轴承、悬臂转子、智能共享信息导向标识柱控制系统,所述伺服电机与智能共享信息导向标识柱控制系统相连;所述支撑单元包括底座、设置在底座上的竖直支撑件,所述竖直支撑件内部形成中空腔体,所述伺服电机设置在中空腔体内,所述伺服电机通过电机安装座与支撑单元相连且电机安装座能为伺服电机提供支撑;所述伺服电机的转轴与内啮合小齿轮相连且伺服电机能带动内啮合小齿轮转动,所述内齿圈与内啮合小齿轮相啮合且内啮合小齿轮能带动内齿圈绕内齿圈的中心转动;所述悬臂定子与支撑单元相连且支撑单元能够为悬臂定子提供支撑并保持相对静止,所述悬臂转子与悬臂定子之间通过连接轴承相连且悬臂转子能相对悬臂定子转动,所述内齿圈与悬臂转子相连且内齿圈能带动悬臂转子相对悬臂定子转动。所述悬臂转子上设置有用于与指示牌相连的连接件。还包括用于显示指定方向目的地的智能标识牌,所述智能标识牌与悬臂转子相连且悬臂转子能带动智能标识牌转动。所述竖直支撑件由至少两个支撑柱构成,所述支撑柱分别设置在底座上且支撑柱之间形成中空腔体。所述支撑柱上设置有隔套。所述支撑柱为三至十个且均布于底座上。所述连接轴承上设置有轴承挡圈。所述悬臂定子上设置有端盖。所述伺服电机的转轴位于内齿圈的同心圆环上。采用前述旋转装置的旋转标识柱,包括至少一个旋转装置。包括至少两个旋转装置,所述旋转装置从上至下依次设置构成旋转单元,上方旋转装置通过底座与下方旋转装置的竖直支撑件相连,所述旋转单元上方设置有端盖。包括至少两个旋转装置,所述旋转装置从上至下依次相连,上方旋转装置通过底座与下方旋转装置的端盖之间采用螺纹或螺杆相连。本发明中,通过智能共享信息导向标识柱控制系统与伺服电机的配合,控制伺服电机的旋转,进而实现最终的旋转。同时,支撑单元包括底座、竖直支撑件,竖直支撑件设置在底座上,竖直支撑件内部形成中空腔体。该中空腔体主要用于放置伺服电机,从而简化旋转装置的结构,减小旋转装置的体积,从而满足相应的安装需要。同时,伺服电机设置在中空腔体内,伺服电机设置在电机安装座上,电机安装座通过支撑单元与悬臂定子固定连接。另外,本发明中,伺服电机的转轴与内啮合小齿轮相连,通过伺服电机带动内啮合小齿轮转动。而内齿圈与内啮合小齿轮内啮合,该结构中,内啮合小齿轮能够带动内齿圈绕其中心转动。该结构中,内啮合小齿轮固定在伺服电机的转轴上,内齿圈固定在悬臂转子上且内齿圈与悬臂定子保持相对静止。内啮合小齿轮、内齿圈之间的内啮合使旋转装置在伺服电机的带动下,能进行任意方向、任意角度的旋转。同时,悬臂定子与支撑单元相连,通过悬臂定子为支撑单元提供支撑,且悬臂定子能够与支撑单元保持相对静止。而悬臂转子与悬臂定子之间通过连接轴承相连,使得悬臂转子能相对悬臂定子转动。另外,内齿圈与悬臂转子相连,通过内齿圈,进而带动悬臂转子相对悬臂定子转动。该装置工作时,控制系统控制伺服电机转动,伺服电机带动内啮合小齿轮转动,通过内啮合小齿轮、内齿圈的内啮合,进而带动内齿圈相对于支撑单元转动。而内齿圈与悬臂转子固定连接,进而通过内齿圈带动悬臂转子转动,实现智能旋转标识柱的旋转功能。进一步,竖直支撑件由至少两个支撑柱构成,支撑柱分别设置在底座上且支撑柱之间形成中空腔体。采用结构,有利于简化竖直支撑件的结构,减低设备的制造成本和维护成本,具有较高的应用价值。同时,支撑柱上设置有隔套;支撑柱可以为三至十个,且均布于底座上。同时,伺服电机的转轴位于内齿圈的同心圆环上。该结构中,能够保证内齿圈绕其中心转动,有利于保证结构和中心的稳定。进一步,伺服电机的转轴偏心设计,进而能够保证内齿圈绕其圆心转动,将旋转机构安装在多功能智能旋转标识柱上可以实现任意方向、任意角度的旋转。进一步,本发明提供伺服电机的s曲线加减速控制方法,包括如下步骤:(1)s曲线算法的脉冲频率表达形式假设电机加减速的需要的开始脉冲频率和结束脉冲频率相等,并且为f0;需要达到的最大脉冲频率为fmax,此时的加速度为频加速度αf,允许的最大值为αm,t1~t5分别为第一至第五阶段的用时时间;在0~t1时间内,f-t曲线为一二次多项式,设如下计算式(1):f=mt2+nt+k(1),式(1)中,m,n,k分别为待定系数;频加速度为脉冲频率关于时间的导数,则有计算式(2):αf=2mt+n(2);取f-t曲线中点(0,f0)和取af-t曲线中点(0,0)和(t1,αm)带入公式(1)和公式(2),得:将af-t曲线中点(t1,am)和m,n带入公式(2),有公式(3):则由公式(4):故在0~t1时间内,f-t函数如下式(5):采用前述类似推导过程,得到不同时间点pwm输出的脉冲频率值计算公式(6):2)加减速曲线的实现嵌入式伺服电机控制系统加减速曲线的实现主要依靠芯片输出pwm脉冲,在嵌入式系统中,pwm的输出由定时器控制,假设芯片时钟频率为fmcu,定时器自动重装载的值为arr和时钟预分频值为psc,则pwm的输出脉冲频率fpwm如下式(7):2.1)初始化参数配置根据实际允许的电机起始转速和最大转速,可以得到f0和fmax的计算公式如下式(9):式(9)中,v为电机加减速的起始速度或允许的最大速度,r/min;npus_per为电机旋转一圈需要的脉冲数;计算完成加减速需要的脉冲数npu_n,公式如下式(10):式(10)中,δang为给定角度与实际角度的差值,rate为电机的减速比;2.2)根据实际情况重新计算最大脉冲频率根据公式9计算得到f0和fmax后,计算得到按最大速度要求需要的脉冲数nmax,计算公式如下式(11):若nmax>npu_n,说明电机此次加速需要的脉冲数小于按最大速度要求需要的脉冲数,即电机不需要加速到初始化设置的最大速度,此时电机的匀速段总时间t=0,并且需要重新计算此次加速需要的最大脉冲频率,计算公式如下式(12):如果nmax≤npu_n,说明电机此次加速需要加速到初始化设置的最大速度,并且加速到最大速度后会产生一段匀速时间,此时f′max=fmax,匀速时间t计算公式如下式(13)所示:2.3)计算各阶段时间由公式3推导得到各个时间点的计算公式如下式(14所示):2.3)加减速控制假设电机加减速需要达到的最大脉冲频率与电机起始脉冲频率的差值δf=fmax-f0,通过定时器得到某时刻的时间为t;通过公式(6)计算得到pwm需要输出的脉冲频率值f后,修改定时器pwm周期和占空比,来控制速度。附图说明本发明将通过例子并参照附图的方式说明,其中:图1是本发明的总体控制系统结构框图。图2是本发明的中央控制器结构框图。图3是本发明的电机驱动控制器结构框图。图4是本发明的中央控制器实时控制流程图。图5是本发明的中央控制器rs232功能控制流程图。图6是本发明的电机驱动控制器控制流程图。图7为本发明中选择结构的结构示意图。图8本发明的s曲线加减速过程频率曲线图。图9本发明的s曲线加减速过程频加速度曲线图。图10是s曲线加速段离散化图。图11电机加减速控制曲线验证图。图中标记:1、伺服电机,2、电机安装座,3、内齿小齿轮,4、内齿圈,5、旋臂定子,6、悬臂转子,7、轴承,8、轴承挡圈,9、端盖,10、支撑柱,11、隔套,12、底座。具体实施方式本说明书中公开的所有特征,或公开的所有方法或过程中的步骤,除了互相排斥的特征和/或步骤以外,均可以以任何方式组合。本说明书中公开的任一特征,除非特别叙述,均可被其他等效或具有类似目的的替代特征加以替换。即,除非特别叙述,每个特征只是一系列等效或类似特征中的一个例子而已。实施例1如图1所示,本实施例的智能指路牌控制系统包括中央控制器和若干电机驱动控制器,各控制器通过can总线构成一个局部网络,并由中央控制器发布指令,各电机驱动控制器实现动作并反馈。电机驱动控制器可通过can总线串联,由拨码开关进行编号,串联最大数量取决于拨码开关编码数值和can总线节点总数的值。其中,中央控制器接收智能终端的指令并集中处理;电机驱动控制器接收中央控制器的can信号并执行相应动作。如图2所示,本实施例的中央控制器包括第一mcu控制单元、电源管理模块、蓝牙无线通信模块、2.4g无线通信模块、4g无线通信模块、can总线模块、flash存储模块、拨码开关、蜂鸣器、rs232串行总线以及led指示灯光模块。电源管理模块、蓝牙无线通信模块、2.4g无线通信模块、4g无线通信模块、can总线模块、flash存储模块、拨码开关、蜂鸣器、rs232串行总线以及led指示灯光模块分别与第一mcu控制单元连接。本实施例中,mcu单元采用stm32f103系列芯片,其安全性高、处理能力强、计算性能好。串行总线can总线模块使用can2.0b协议,与第一mcu连接,可以实现与各电机驱动控制器的信息传递。flash存储模块采用w25q64,可存储最大8m字节数据,与第一mcu连接。rs232与第一mcu连接,可以接收pc终端等端口信息数据。蓝牙无线通信模块与mcu相连可与智能终端无线通信2.4g无线通信模块通过与mcu相连,可与显示屏无线通信,4g无线通信模块与mcu相连,可与服务器通信,用于系统维护。同时,拨码开关、蜂鸣器、led指示灯光模块通过i/o口与mcu相连,可以实现故障警告、状态指示功能。如图3所示,电机驱动控制器包括与第一mcu控制单元相连的第二mcu控制单元、电源管理模块、can总线通信模块、电机模块、拨码开关、光电限位感应器;其中,第二mcu控制单元分别与电源管理模块、can总线通信模块、电机模块、拨码开关、光电限位感应器相连。本实施例中,第二mcu控制单元采用stm32f205系列芯片,其计算能力更加强大。can总线模块使用can2.0b协议,与mcu连接,可以实现与中央控制器的信息传递。电机模块通过第二mcu控制单元的一路pwm调速方式实现电机控制。拨码开关通过i/o口与第二mcu相连,可以实现不同节点的编号。光电限位感应器通过光耦隔离后与第二mcu控制单元连接,可为电机寻找机械零点;电机驱动控制器的led指示灯光模块为状态指示标志。如图4所示,中央控制器实时控制步骤如下:中央控制器的蓝牙通信模块可与智能终端通信,2.4g无线通信模块与led显示屏幕无线通信,4g无线通信模块与服务器通信。中央控制器的rs232为传统串口连接保留功能,可以实现串口数据传输。如图5所示,中央控制器rs232功能控制步骤为:中央控制器的rs232为传统串口连接保留功能,可以实现pc终端等串口数据传输,pc端数据通过串口发送至中央控制器,中央控制器存储成功后回调数据id给pc端,pc端再进行下一数据的传输。如图6所示,电机驱动控制器控制步骤为:电机驱动控制器上电后先进行系统初始化,然后通过光电限位感应器检测旋转臂归零信号,若旋转臂未在零位则启动电机使旋转臂回零,旋转臂回零后向中央控制器发送一个回零准备就绪命令,等待接收来自中央控制器的旋转指令并向电机模块发送执行信息,旋转到指定的角度。该结构中,电机驱动控制器的can总线接收来自中央控制器的旋转指令并向电机模块发送执行信息,同时向中央控制器上发故障信息。电机驱动控制器的光电限位感应器可为电机寻找机械零点。电机驱动控制器的led指示灯光模块为状态指示标志。进一步,本实施例提供采用前述智能共享信息导向标识柱控制系统的旋转标识柱,包括二至六个旋转装置。其中,旋转装置从上至下依次相连,上方旋转装置通过底座与下方旋转装置的端盖之间采用螺纹或螺杆相连。本实施例中,旋转装置包括支撑单元、伺服电机、电机安装座、内啮合小齿轮、内齿圈、悬臂定子、连接轴承、悬臂转子、智能共享信息导向标识柱控制系统,伺服电机与智能共享信息导向标识柱控制系统相连。其中,支撑单元包括底座、设置在底座上的竖直支撑件,竖直支撑件内部形成中空腔体,伺服电机设置在中空腔体内,伺服电机通过电机安装座与支撑单元相连且电机安装座能为伺服电机提供支撑。本实施例中,竖直支撑件由至少两个支撑柱构成,支撑柱分别设置在底座上且支撑柱之间形成中空腔体,支撑柱上设置有隔套。同时,伺服电机的转轴位于内齿圈的同心圆环上,伺服电机的转轴与内啮合小齿轮相连,伺服电机能带动内啮合小齿轮转动;内齿圈与内啮合小齿轮相啮合,内啮合小齿轮能带动内齿圈绕内齿圈的中心转动。悬臂定子与支撑单元相连,支撑单元能够为悬臂定子提供支撑并保持相对静止;悬臂转子与悬臂定子之间通过连接轴承相连,悬臂转子能相对悬臂定子转动;内齿圈与悬臂转子相连,内齿圈能带动悬臂转子相对悬臂定子转动。本实施例中,悬臂转子上设置有用于与指示牌相连的连接件,连接轴承上设置有轴承挡圈,悬臂定子上设置有端盖。进一步,本实施例提供用于前述伺服电机的s曲线加减速控制方法,其包括如下步骤。1)s曲线算法的脉冲频率表达形式假设电机加减速的需要的开始脉冲频率(以下简称频率)和结束频率相等,并且为f0,需要达到的最大频率为fmax,此时的加速度为频加速度αf,允许的最大值为αm,t1~t5为各阶段的用时时间。在0~t1时间内,f-t曲线为一二次多项式,设:f=mt2+nt+k(1)式中,m,n,k为待定系数。频加速度可以理解为频率关于时间的导数,故有:αf=2mt+n(2)取f-t曲线中点(0,f0)和取af-t曲线中点(0,0)和(t1,αm)带入公式1和2得:将af-t曲线中点(t1,am)和m,n带入2式,有:则:故在0~t1时间内,f-t函数为:其它时间段f-t函数的推导过程类似,由此可得不同时间点pwm输出的频率值f计算公式为:2)加减速曲线的实现本实施方案使用直流无刷电机与stm32单片机系统结合的方式,在stm32单片机系统中,pwm的输出由定时器控制,假设芯片时钟频率为fmcu,定时器自动重装载的值为arr和时钟预分频值为psc,则pwm的输出频率为:2.1)初始化参数配置根据实际允许的电机起始转速和最大转速,可以得到f0和fmax的计算公式如下:式中,v为电机加减速的起始速度或允许的最大速度,r/min;npus_per为电机旋转一圈需要的脉冲数。计算完成加减速需要的脉冲数npu_n,公式如下:式中,δang为给定角度与实际角度的差值,rate为电机的减速比。2.2)根据实际情况重新计算最大频率根据公式9计算得到f0和fmax后,可以得到按最大速度要求需要的脉冲数,计算公式如下:如果nmax>npu_n,说明电机此次加速需要的脉冲数小于按最大速度要求需要的脉冲数,即电机不需要加速到初始化设置的最大速度,此时电机的匀速段总时间t=0,并且需要重新计算此次加速需要的最大频率,计算公式如下:如果nmax≤npu_n,说明电机此次加速需要加速到初始化设置的最大速度,并且加速到最大速度后会产生一段匀速时间,此时f′max=fmax,匀速时间:2.3)计算各阶段时间由公式3推导得到各个时间点的计算公式如下:2.4)根据时间情况开始加减速使能一个定时器开始计时,根据时间情况切换算法公式进行加减速,假设电机加减速需要达到的最大频率与电机起始频率的差值δf=fmax-f0,通过定时器得到某时刻的时间为t。通过公式6计算得到pwm需要输出的频率值f后,就可以修改定时器pwm周期和占空比来控制速度。2.5)曲线验证设f0=300hz,fmax=20000hz,npus_per=400,最大频加速度αm=10000.0,电机初始角度为0,旋转角度为90°,启动电机,在stm32调试模式中对定时器的时间输出值t和相应的pwm频率输出值f进行随机采样,得到的数据如下表1所示。表1时间-频率记录表时刻/s频率/hz时刻/s频率/hz0.385961.9870.9003747.8551.4198366.8381.93711424.372.45612227.462.97410774.723.4957048.3444.0132702.3264.532559.784——从图11中可以看出,本次实施方案使用的直流无刷电机加减速过程符合s型曲线,本次实验加减速没有匀速过程,加减速过程平滑,没有速度的跳变,达到了预期控制效果。本发明并不局限于前述的具体实施方式。本发明扩展到任何在本说明书中披露的新特征或任何新的组合,以及披露的任一新的方法或过程的步骤或任何新的组合。当前第1页12