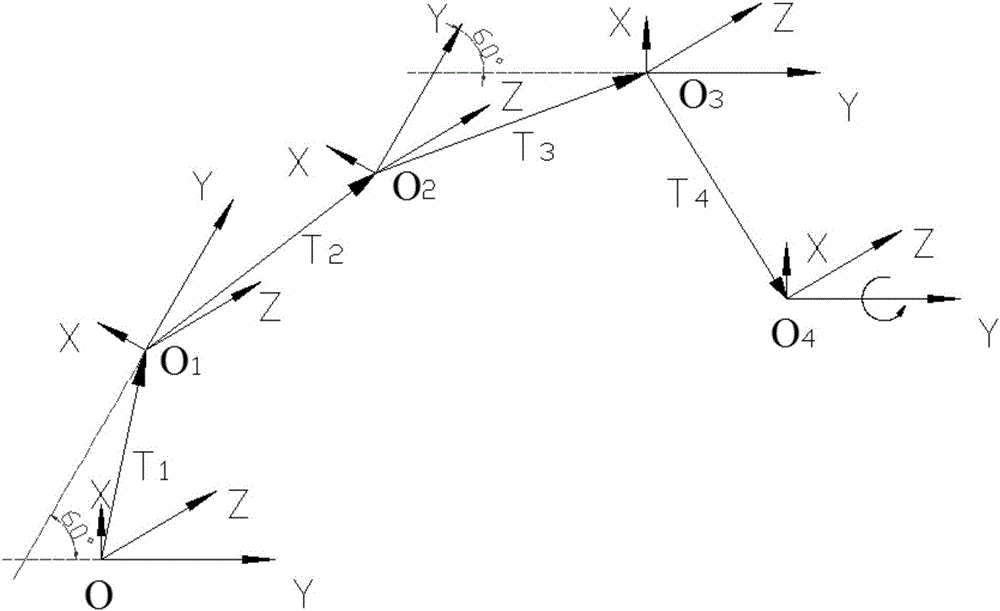
本发明涉及机床
技术领域:
,尤其是涉及一种车铣复合加工中心在线防碰撞系统部件模型位姿变换方法。
背景技术:
:近年来,在传统数控车床和加工中心的基础上,增加C轴分度、Y轴运动、动力刀架或铣削电主轴等功能配置而发展起来的车铣加工中心大量出现,可通过一次装夹完成多步工序和多种工艺,大大提高了加工效率。但是,这类机床在加工过程中的走刀路径和机床部件运动十分复杂,使得加工过程中容易发生诸如刀具与工件或者刀具与机床之间的碰撞事故。为了尽可能避免此类事故发生,在数控系统中集成在线防碰撞系统是一种可行方案。由于加工中心部件一直处于复杂的空间运动过程中,而碰撞检测算法要求被检测对象的空间模型基于同一个空间坐标系。因此,高效的部件位姿变换算法是实现防碰撞系统碰撞检测功能的基础。常用的姿态变描述法主要有欧拉角法、四元数法和齐次变换法三种。由于机床部件主要运动形式为沿X、Y、Z轴的平移和绕B轴、C轴的旋转,采用齐次坐标变换法可以最为快速有效地实现各部件的位姿变换。中国专利CN103076762A公开了一种基于HTM40100车铣复合加工中心三位在线防碰撞方法,实现卧式车铣复合加工中心的在线防碰撞检测。本发明选用SINUMERIK840D系统作为开发平台,以HTM40100卧式车铣复合加工中心为研究对象,在西门子的标准界面下,利用西门子OEM软件开发包提供的标准编程语言,将自行开发的三维防碰撞系统集成于数控系统中。该专利并未提及如何最为快速有效地进行车铣复合加工中心的各部件的位姿变换。技术实现要素:本发明的目的就是为了克服上述现有技术存在的缺陷而提供一种车铣复合加工中心在线防碰撞系统部件模型位姿变换方法,可快速且有效地实现各部件的位置变换。本发明的目的可以通过以下技术方案来实现:一种车铣复合加工中心在线防碰撞系统部件模型位姿变换方法包括以下步骤:S1:构建基于STL格式的部件模型三角面片化数据结构,包括用于存储部件初始模型数据的部件初始模型数据结构和用于存储部件实时模型数据的部件实时模型数据结构;S2:构建基于各伺服轴坐标参数的各部件位姿变换矩阵函数;S3:部件模型位姿变换过程:S3-1:根据车铣复合加工中心三维模型对步骤S1的部件模型三角面片化数据结构内的模型数据进行初始化;S3-2:根据车铣复合加工中心伺服轴坐标参数识别位姿变化的部件,并基于步骤S2的各部件位姿变换矩阵函数获取位姿变化的部件的位姿变换矩阵;S3-3:根据步骤S3-1中的部件初始模型数据结构的模型数据和步骤S3-2的位姿变化的部件的位姿变换矩阵更新步骤S3-1中的部件实时模型数据结构内的模型数据。所述部件初始模型数据结构包括用于存储部件与顶点的映射关系的初始模型部件层和用于存储顶点坐标值的初始模型空间点层;所述部件实时模型数据结构包括用于存储部件与三角面片的映射关系的实时模型部件层、用于存储三角面片与顶点的映射关系的实时模型三角面片层以及用于存储顶点坐标值的实时模型空间点层。所述初始模型部件层与初始模型空间点层之间根据顶点建立链接关系。所述实时模型部件层与实时模型三角面片层之间根据三角面片建立链接关系,所述实时模型三角面片层和实时模型空间点层根据顶点建立链接关系。所述步骤S2具体为:S2-1:获取车铣复合加工中心的结构参数以及各伺服轴的零点位置;S2-2:根据车铣复合加工中心的结构参数以及各伺服轴的零点位置,建立以各伺服轴坐标为参变量的各部件位姿变换矩阵函数。所述各部件位姿变换矩阵为各部件向绝对坐标系的齐次坐标变换矩阵。所述步骤S3-1中对部件模型三角面片化数据结构内的模型数据进行初始化的过程具体为:1)根据车铣复合加工中心三维模型获取STL格式文件;2)去除STL格式文件内的冗余点;3)对去冗余后的STL格式文件进行封装,获取初始化的部件模型三角面片化数据结构内的模型数据。所述步骤3-2具体为:S3-2-1:实时采集车铣复合加工中心各伺服轴的坐标参数;S3-2-2:判断部件当前时刻的伺服轴的坐标参数与上一时刻的伺服轴的坐标参数是否相同,若是,则跳转步骤S3-2-1,若否,则记该部件为位姿变化的部件;S3-2-3:基于步骤S2的各部件位姿变换矩阵函数,由位姿变化的部件当前时刻的伺服轴的坐标参数获取位姿变化的部件的位姿变换矩阵。所述部件实时模型数据结构内的模型数据用于车铣复合加工中心的实时碰撞检测和实时模型显示。与现有技术相比,本发明具有以下优点:1)本发明构建机床部件模型简化的三角面片化数据结构,将传统的坐标点变换提升至模型变化的高层次,部件实时模型数据结构内的模型数据反应部件模型的三维状态,可进一步用于车铣复合加工中心的实时碰撞检测和实时模型显示,有利于加工中心的在线防碰撞规划,以保证设备运行安全。2)本发明采用以空间小三角形面片逼近三维实体表面的STL数据模型,仅对三角形面片的三个顶点进行坐标变化,大大减小所需坐标变化的处理量,提高数据处理效率。3)本发明构建部件初始模型数据结构和部件实时模型数据结构,实现结构化存储数据,降低模型数据冗余,有利于大量数据存储与调用,提高系统运行效率,消除手工推导方法中各轴坐标计算公式的推导环节,可快速处理部件模型位姿的变化状态,获得部件模型的实时空间分布。4)本发明采用齐次坐标变换法实现坐标变换,可以最为快速有效地实现各部件的位姿变换,高效的部件位姿变换算法是实现防碰撞系统碰撞检测功能的基础。附图说明图1为车铣复合加工中心的简化模型;图2为车铣复合加工中心各铣削加工部件的空间坐标变换示意图;图3为车铣复合加工中心各车削加工部件的空间坐标变换示意图;图4为部件初始模型数据结构的示意图;图5为部件实时模型数据结构的示意图;图6为位姿实时变换过程的流程图。图中:1、斜立柱Z轴溜板,2、斜立柱,3、斜立柱X轴溜板,4、铣主轴,5、副主轴,6、刀塔Z轴溜板,7、刀塔X轴溜板,8、主轴。具体实施方式下面结合附图和具体实施例对本发明进行详细说明。本实施例以本发明技术方案为前提进行实施,给出了详细的实施方式和具体的操作过程,但本发明的保护范围不限于下述的实施例。一种车铣复合加工中心在线防碰撞系统部件模型位姿变换方法包括以下步骤:S1:构建基于STL格式的部件模型三角面片化数据结构,包括用于存储部件初始模型数据的部件初始模型数据结构和用于存储部件实时模型数据的部件实时模型数据结构。STL格式是一种用空间小三角形面片逼近三维实体表面的数据模型,通过三角形的三个顶点坐标值及三角形法向向量来实现对每个三角面片的具体描述。为了降低模型数据冗余,提高系统运行效率,本方法首先对STL格式模型文件去冗余并进行结构化封装。部件封装的数据结构如图4和图5所示,将部件封装成两个数据结构。其一为部件实时模型数据结构,包含部件与三角面片、三角面片与顶点的映射关系以及各顶点坐标值,作为部件位姿变换的输出,用于在线防碰撞系统的碰撞检测以及模型实时显示。其二为部件初始模型数据结构,包含了部件与顶点的映射关系以及各顶点的初始坐标值,主要用于部件位姿变换的输入。S2:构建基于各伺服轴坐标参数的各部件位姿变换矩阵函数。车铣复合加工中心各部件的空间运动是通过各伺服轴的运动实现的,根据车铣复合加工中心的结构参数以及各伺服轴的零点位置,建立加工中心各部件的初始化坐标变换矩阵,并在此基础上建立以各伺服轴坐标值为参变量的加工中心各部件位姿变换矩阵函数。因此,只要确定碰撞检测点各伺服轴的坐标值参数,就可以快速映射生成各部件相应的坐标变换矩阵,以完成各部件模型的空间位姿变换。S3:根据齐次坐标变换理论,通过对部件模型三角面片化数据结构中三角面片顶点坐标的坐标变换实现部件模型的空间位姿变换,如图6所示,具体过程:S3-1:根据车铣复合加工中心各部件三维模型对步骤S1的部件模型三角面片化数据结构内的模型数据进行初始化;S3-2:根据车铣复合加工中心各伺服轴的坐标参数识别位姿变化的部件,即根据各伺服控制轴坐标值变化情况遴选需要进行位姿变换的加工中心部件,并基于步骤S2的各部件位姿变换矩阵函数获取位姿变化的部件的位姿变换矩阵;S3-3:将步骤S3-1的部件初始模型数据结构中的顶点坐标通过步骤S3-2的位姿变化的部件的位姿变换矩阵进行齐次坐标变换,最后将顶点的坐标变换结果按照映射关系储存到步骤S3-1中的初始化的部件实时模型数据结构中,以供碰撞检测算法以及实时显示使用。以HTM63150iy车铣复合加工中心为例,采用本发明方法实现部件模型实时位姿变换的过程为:一、获取加工中心的部件模型三角面片化数据结构机床部件的位姿变换矩阵是基于部件初始位姿信息的,即部件每一次的位姿变换,均是将求得的变换矩阵与该部件所有顶点的初始坐标相乘,得到部件顶点的实时坐标。因此,需要构建一个单独的数据结构,专门用于存储部件的初始模型数据。同时,需构建另外一个与之对应的数据结构,用于存储计算之后的部件实时模型数据。在此基础上,本发明方法构建了“部件初始模型数据结构”和“部件实时模型数据结构”,前者存储部件初始位姿信息,用于计算部件实时位姿;后者存储部件实时位姿信息,用于在线防碰撞系统的碰撞检测以及模型实时显示。图4和图5为三角面片化数据结构示意图。“部件初始模型数据结构”分为两层,第一层为用于存储部件与顶点的映射关系的初始模型部件层,记录该部件的所有顶点指针对象;第二层为用于存储顶点坐标值的初始模型空间点层,记录该部件所有顶点的初始坐标,初始模型部件层与初始模型空间点层之间根据顶点建立链接关系。其分层封装后的STL文件框架结构如下:“部件实时模型数据结构”分为三层,第一层为用于存储部件与三角面片的映射关系的实时模型部件层,记录该部件的所有三角面片指针对象;第二层为用于存储三角面片与顶点的映射关系的实时模型三角面片层,记录三角面片的顶点指针对象;第三层为用于存储顶点的实时坐标值的实时模型空间点层,记录该部件所有顶点的实时坐标值,实时模型部件层与实时模型三角面片层之间根据三角面片建立链接关系,实时模型三角面片层和实时模型空间点层根据顶点建立链接关系。其分层封装后的STL文件框架结构如下:二、机床各部件向绝对坐标系的齐次变换矩阵HTM63150iy车铣复合加工中心的结构如图1所示,机床伺服轴部分分为:铣主轴4三个方向的直线轴,分别为图1中X1轴、Y轴和Z1轴;刀塔两个方向的直线轴,分别为图中X2轴和Z2轴;副主轴Z方向的直线轴,为图中Z3轴;铣主轴4绕Y轴的转动,为图中B轴;主轴8绕Z轴的转动,为图中C轴。HTM63150iy车铣复合加工中心主要有铣削和车削两种加工方式,主要运动方式为沿X、Y、Z轴的平移运动及绕B轴和C轴的旋转运动。图2为车铣复合加工中心各铣削加工部件的空间坐标变换示意图,其中,OXYX为绝对坐标系,O1XYZ为斜立柱Z轴溜板坐标系,O2XYZ为斜立柱坐标系,O3XYZ为斜立柱X轴溜板坐标系,O4XYZ为铣主轴坐标系。图3为车铣复合加工中心各车削加工部件的空间坐标变换示意图,其中OXYX为绝对坐标系,O6XYZ为刀塔Z轴溜板坐标系,O7XYZ为刀塔X轴溜板坐标系。得到车铣复合加工中心各部件位姿变换矩阵的步骤如下:1、获取车铣复合加工中心(图1)的结构参数以及各伺服轴的零点位置;2、建立以各伺服轴坐标值为参变量的加工中心各部件位姿变换矩阵函数。3、确定碰撞检测点各伺服轴的坐标值参数,生成变换矩阵。则HTM63150iy车铣复合加工中心各部件位姿变换矩阵函数如下:1.铣削加工部分由图2可得绝对坐标系与各铣削加工部分的部件坐标系的关系:所有坐标系的Z轴指向相同,绕Z轴旋转角度如图中标注;斜立柱Z轴溜板1只有沿其自身Z轴的平移运动,斜立柱2只有沿其自身X轴的平移运动,斜立柱X轴溜板3只有沿其自身X轴的平移运动,铣主轴4只有沿其自身Y轴的摆动,因此各部件向绝对坐标系的齐次坐标变换矩阵如下:斜立柱Z轴溜板1向绝对坐标系的齐次坐标变换矩阵为:T1=12320U1-32120V1001Z10001]]>斜立柱2向绝对坐标系的齐次坐标变换矩阵为:T2=1232032V2+U1+12Y-32120V1+12V2-32Y001W2+Z10001]]>斜立柱X轴溜板3向绝对坐标系的齐次坐标变换矩阵为:T3=100U1-32U3+32V2+32V3+12Y+2X1010-32U3+V1+12V2+12V3-32Y001W2+W3+Z10001]]>铣主轴4向机床绝对坐标系的齐次坐标变换矩阵为:T4=cosβ0sinβU1-32U3+U4+32V2+32V3+12Y+2X1010-32U3+V1+12V2+12V3+V4-32Y-sinβ0cosβW2+W3+W4+Z10001]]>其中:U1,V1,W1为铣刀斜立柱Z轴溜板坐标系原点在绝对坐标系中的初始坐标;U2,V2,W2为铣刀斜立柱坐标系原点在斜立柱Z轴溜板坐标系中的初始坐标;U3,V3,W3为斜立柱X轴溜板坐标系原点在铣刀斜立柱坐标系中的初始坐标;U4,V4,W4为铣主轴坐标系原点在斜立柱X轴溜板坐标系中的初始坐标;β为铣主轴4轴线与绝对坐标系中X轴的夹角;Z1为车铣复合加工中心Z1轴的坐标值;Y为车铣复合加工中心Y轴的坐标值;X1为车铣复合加工中心X1轴的坐标值;2.车削加工部分:通过对机床车刀轴的运动分析可知,各车削加工部分的部件坐标系的X、Y、Z轴指向均相同。刀塔Z轴溜板6只有沿自身Z轴的平移运动,刀塔X轴溜板7只有沿自身X轴的平移运动。各部件向绝对坐标系的齐次坐标变换矩阵如下:刀塔Z轴溜板6向绝对坐标系的齐次坐标变换矩阵为:T6=100U6010V6001Z20001]]>刀塔X轴溜板7向绝对坐标系的齐次坐标变换矩阵为:T7=100X2+U6010V7+U6001W7+Z20001]]>其中:U6,V6,W6为刀塔Z轴溜板坐标系原点在绝对坐标系中的初始坐标;U7,V7,W7为刀塔X轴溜板坐标系原点在刀塔Z轴溜板坐标系中的初始坐标;Z2为车铣复合加工中心Z2轴的坐标值;X2为车铣复合加工中心X2轴的坐标值;3.副主轴8由于副主轴8只有沿自身Z轴的平移运动,故其向绝对坐标系的齐次变换矩阵为:T5=100U5010V5001Z30001]]>U5,V5,W5为副主轴8坐标系原点在绝对坐标系中的初始坐标;Z3为车铣复合加工中心Z3轴的坐标值;4.主轴8由于主轴8只有沿自身Z轴的旋转运动,故其向绝对坐标系的齐次变换矩阵为:T8=cosθ-sinθ0U8sinθcosθ0V8001W80001]]>U8,V8,W8为副主轴8坐标系原点在绝对坐标系中的初始坐标;θ为车铣复合加工中心C轴的转角。则通过获取机床初始化数据后,即可确定机床绝对坐标系位置和各部件相对坐标系位置,得到部件坐标系原点在绝对坐标系中的坐标,即U、V、W值(分别对应X、Y、Z三轴),根据齐次坐标变换的方法,将各部件的U、V、W值带入加工中心各部件位姿变换矩阵函数,则可以得到以各伺服轴坐标值为参变量的机床各部件向绝对坐标系的齐次变换矩阵,当伺服轴坐标参数发生变化,对应的位姿变换矩阵也需发生变化,部件模型上的任一点的初始坐标乘以实时的位姿变换矩阵,可则得到对应实时的坐标值。三、部件位姿变换流程部件位姿变换主要包括三个步骤,如图6所示:第一步初始化三角面片化的数据结构内的模型数据,具体为:1.导入STL文件。将简化的机床三维模型导出为STL文件格式,在程序中读入该文件。2.去冗余。在读取STL文件时,采用平衡二叉树的搜索方式,去除三角面片中的冗余点,同时记录数据信息。将去冗余的三角面片顶点坐标、三角面片法向量等数据分别存储于数组中并记录其个数。3.结构化数据。对STL文件进行封装,构建“部件初始模型数据结构”和“部件实时模型数据结构”,并初始化数据。第二步计算部件位姿变换矩阵1.筛选变换部件。构建一个数据结构存储机床各伺服轴坐标参数,在获取当前时刻机床各伺服轴坐标参数后,将其与上一时刻各伺服轴的坐标参数做比较,坐标发生变化的即为需要进行位姿变换计算的部件。2.获得实时位姿变换矩阵。经过筛选之后,对于位姿发生变化的部件,将当前时刻机床伺服轴坐标参数带入该部件的位姿变换矩阵函数中,得到实时位姿变换矩阵。第三步部件位姿变换1.实时位姿变换。对于位姿发生变化的部件,通过“部件初始模型数据结构”找到与其对应的顶点信息。将部件实时位姿变换矩阵与部件所有顶点的初始坐标相乘,得到部件各顶点的实时坐标。2.实时模型数据生成。将部件各顶点的实时坐标按照一一对应关系存入“部件实时模型数据结构”中。通过该结构中存储的部件与三角面片、三角面片与顶点的映射关系,有目的地调用坐标点,作为碰撞检测和实时显示的数据输入。3.碰撞检测、实时显示。当前第1页1 2 3