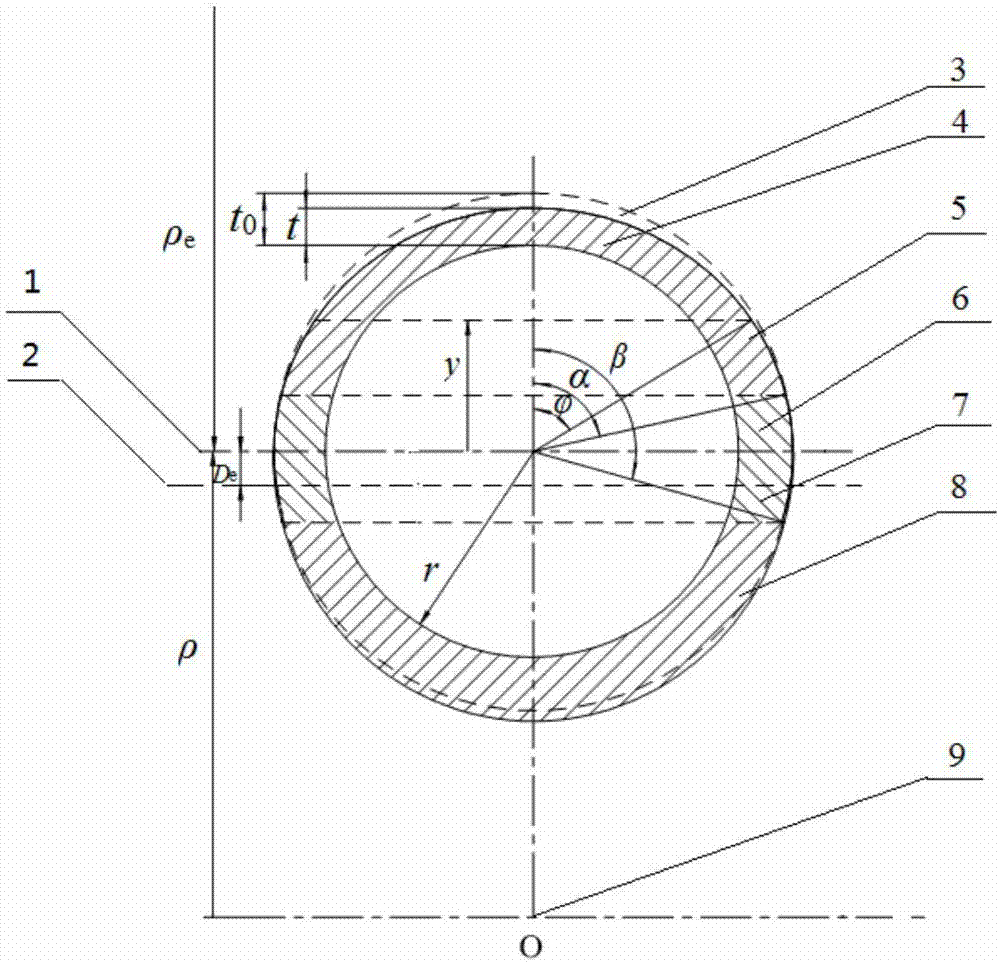
本发明涉及机械加工领域,具体是一种确定均质管材数控弯曲回弹角的方法,主要用于均质管材数控弯曲成形。
背景技术:
:管材塑性加工是以管材为毛坯,通过塑性加工手段制造管材零件的加工技术,由于容易满足对产品轻量化、强韧化、精确化和低消耗等方面的要求,在航空、航天和汽车工业中已经得到了广泛应用,已成为先进塑性加工技术面向21世纪研究与发展的一个重要方向。管材弯曲成形是将管材毛坯弯制成具有一定弯曲半径、一定弯曲角度和形状的塑性加工工序,是管材塑性加工技术的重要组成部分。目前已有多种管材弯曲成形方式,其中数控绕弯成形由于具有成形精度高、效率高和易于实现数字化和高技术化等特点,在航空、航天和汽车制造工业领域,管材数控弯曲成形已经发展成为一种先进适用技术。弯曲成形过程结束后,变形体中含有的弹性变形发生卸载,从而使零件产生回弹。对于管材弯曲成形来说,弯管内、外侧应力状态相反,卸载时回弹效应相互迭加,使得弯管件弯曲角度减小,弯曲半径增加。回弹是影响管材弯曲成形精度的一个主要因素,当回弹量超过误差所允许的范围时,零件的几何精度和形状精度就难以满足要求,而这两方面的精度会直接影响到弯管件的使用,如和其它部件连接的设计布局及结构紧凑性等。对均质管材数控弯曲回弹进行深入研究,提高回弹的预测精度,已成为发展管材数控弯曲精确成形技术所迫切需要解决的重要课题。目前关于均质管材弯曲回弹的理论解析模型大多是基于经典回弹理论(即弯曲卸载后的回弹弯矩与弯曲时的加载弯矩大小相等,方向相反)建立的,且推导过程中很少考虑收缩应变比和弹性模量等材料参数变化。h.a.al-qureshi等(h.a.al-qureshi.elastic-plasticanalysisoftubebending.internationaljournalofmachinetoolsandmanufacture,1999,39(1):87-104)基于平面应变条件,将圆管视为空心梁,采用梁弯曲理论对圆管纯弯进行了弹塑性分析,在分析过程中假设材料为理想弹塑性,横截面上具有一个与外载荷平面垂直的对称轴,忽略起皱、破裂以及包辛格效应等,得出了定量预测弯矩和回弹半径的近似公式,并通过对不同规格的同种铝合金管材进行纯弯曲实验来验证回弹计算公式,结果表明回弹的实验结果和理论预测结果吻合良好。这种理论和实验相结合的方法很具有借鉴意义。a.ei.megharbel等(a.el.megharbel,g.a.elnasser,a.el.domiaty.bendingoftubeandsectionmadeofstrain-hardeningmaterials.journalofmaterialsprocessingtechnology,2008,203(1-3):372-380)在h.a.al-qureshi的基础上,将线弹性-理想塑性材料改为更加符合实际的硬化材料,使回弹的理论解析结果更加接近实验值,但其没有考虑管材弯曲时的收缩应变比和弹性模量等材料参数变化等,与实际情况不符。li等(h.li,h.yang,f.f.song,m.zhan,l.g.jin.springbackcharacterizationandbehaviorsofhigh-strengthti-3al-2.5vtubeincoldrotarydrawbending.journalofmaterialsprocessingtechnology,2012,212(9):1973-1987)以经典回弹理论为基础,基于平面应变假设,采用指数硬化塑性材料模型,建立了考虑管材弯曲过程中壁厚变化和中性层偏移的均质管弯曲回弹理论解析模型。发现其建立的理论解析模型对ta18高强钛管弯曲回弹的预测结果与实验结果吻合良好。但其忽略了弯曲过程中的弹性变形,未考虑收缩应变比和弹性模量随塑性变形的变化,而这些参数对回弹结果的精度是有影响的。综上所述,针对管材弯曲回弹的理论解析研究都以大量的假设为基础,如将材料简化为理想弹塑性材料,忽略管材弯曲过程中的收缩应变比和弹性模量等材料参数变化等,这些都会给计算结果带来很大误差。回弹是弯曲变形中弹性变形部分恢复的结果,当材料发生纯弹性弯曲时,应变沿厚度方向呈线性分布,回弹时弹性变形能够完全恢复,回弹弯矩大小等于加载弯矩,可以采用经典回弹理论求解回弹。但当材料发生弹塑性弯曲时,变形沿厚度方向呈非线性分布,回弹时弹性变形成分不能完全恢复,残余变形、残余应力和残余弯矩均存在,弯曲时的加载力矩不等于卸载时的回弹弯矩,此时再采用经典纯弯曲理论计算回弹存在较大的误差。目前大部分文献都是以经典纯弯曲理论计算回弹的。管材弯曲过程中,弯曲外侧材料轴向受拉伸长,壁厚减薄,内侧材料轴向受压缩短,壁厚增厚,弯管中性层向弯曲内侧偏移。西北工业大学在申请号201610028006.3提出了一种确定管材数控弯曲回弹角的方法,该发明基于平衡条件,建立了考虑弹性模量变化的回弹理论解析模型。研究发现,在理论解析中将弹性模量视为常数会导致回弹解析值比实际值小,考虑弹性模量会减小回弹角计算误差。但该发明未考虑收缩应变比变化,导致回弹角计算值与试验值产生一定的误差。因此,建立基于平衡条件,考虑收缩应变比和弹性模量变化等的均质管材弯曲回弹理论解析模型是发展均质管材数控弯曲精确成形技术需要解决的重要课题。技术实现要素:为减小现有计算方法中由于理论基础和未考虑收缩应变比和弹性模量引起的误差,本发明提出了一种确定均质管材数控弯曲回弹角的方法。本发明的具体过程是:步骤1,确定应力/应变中性层偏移量de和屈服点处的应变εs:根据式(1)确定应力/应变中性层偏移量de:其中,ρ为弯曲半径,r为管材内半径。根据式(2)确定屈服点处的应变εs:e0εs=k(εs+b)n(2)其中,e0为初始弹性模量,k为强化系数,n为硬化指数,b为材料常数。步骤2,确定管材弯曲后横截面上随位置变化的壁厚t和轴向应变εθ:根据式(3)确定管材弯曲后横截面上随位置变化的壁厚t:其中,t0为管材的初始壁厚,为管材弯曲后横截面外表面上某一点与对称轴之间的夹角,通过管材弯曲后横截面上某一点到管材几何中性层的距离y计算弯管的轴向应变εθ,具体过程是:ⅰ确定管材弯曲后横截面上某一点到管材几何中性层的距离y根据式(4)确定管材弯曲后横截面上某一点到管材几何中性层的距离y:ⅱ确定弯管的轴向应变εθ根据式(5)确定弯管的轴向应变εθ:步骤3,确定收缩应变比csr:根据式(6)确定随塑性变形变化的收缩应变比csr:其中,a0,a1,a2,b1,b2为材料常数。步骤4,确定弯管的等效应变根据式(7)确定弯管的等效应变步骤5,确定随塑性变形变化的弹性模量e′:根据式(8)确定随塑性变形变化的弹性模量e′:其中,ea为随塑性变形的增加弹性模量趋于稳定时的值,ξ为系数。步骤6,确定管材弯曲外侧弹塑性分界处与几何中性层之间的夹角α和弯曲内侧弹塑性分界处与几何中性层之间的夹角β:根据式(9),用数值求解方法确定管材弯曲外侧弹塑性分界处与几何中性层之间的夹角α和弯曲内侧弹塑性分界处与几何中性层之间的夹角β。步骤7,确定回弹角δθ:根据式(10)确定系数p:根据式(11)和(12)确定回弹前弯管外侧塑性变形区各轴向力之和c1、回弹前弯管内侧弹性变形区各轴向力与弯管外侧弹性变形区各轴力之和c2、回弹前弯管内侧塑性变形区各轴向力之和c3、c4为回弹时弯管外侧塑性变形区各轴向力之和的-(ρe+de)倍、c5为回弹时弯管内侧弹性变形区各轴向力与弯管外侧弹性变形区各轴向力之和的-(ρe+de)倍、c6为回弹时弯管内侧塑性变形区各轴向力之和的-(ρe+de)倍:其中,ν为泊松比,q为弯管弯曲截面面积,根据式(12)得到:q=t2+2tr(12)根据式(13)得到弯管回弹后的曲率根据式(14)得到弯管的回弹角δθ:其中,θ为回弹前的弯曲角。本发明基于平衡条件,提出了一种考虑收缩应变比和弹性模量变化的均质管材弯曲回弹角计算方法,以提高回弹预测精度,从而实现对弯管成形的精确控制。本发明提出了一种基于静力平衡条件,考虑管材弯曲过程中的考虑收缩应变比和弹性模量变化的均质管材弯曲回弹角计算方法,提高了回弹预测精度,具有一定的普适性,可用于均质管材弯曲回弹的初步预测,并对研究各参数对回弹的影响具有重要指导作用。当材料发生弹塑性弯曲时,变形沿厚度方向呈非线性分布,回弹时弹性变形不能完全恢复,残余变形、残余应力和残余弯矩均存在,弯曲时的加载弯矩不等于卸载时的回弹弯矩。因此,采用经典回弹理论会产生一定的误差。与现有技术相比,一方面,本发明基于静力平衡条件,认为回弹时残余变形和残余应力均存在,对回弹的预测精度高于经典回弹理论;另一方面,本发明考虑了考虑收缩应变比和弹性模量变化,得到的回弹角计算值大于未考虑考虑收缩应变比和弹性模量变化时的计算值,且更接近实验值,使回弹预测精度得到提高。以d6mm×t0.5mm×ρ12mm(外径d为6mm,初始壁厚t0为0.5mm,弯曲半径ρ为12mm)和d12mm×t0.9mm×ρ24mm(外径d为12mm,初始壁厚t0为0.9mm,弯曲半径ρ为24mm)ta18钛合金为例,考虑收缩应变比和弹性模量变化可分别提高回弹角平均预测精度3.88%和1.83%。附图说明图1为本发明计算方法的示意图;图2为均质管材弯曲后横截面图;图3为本发明的流程图。图中:1.几何中性层;2.应力/应变中性层;3.管材弯曲前横截面;4.管材弯曲后横截面;5.弯管外侧塑性变形区;6.弯管外侧弹性变形区;7.弯管内侧弹性变形区;8.弯管内侧塑性变形区;9.弯曲中心。具体实施方式实施例一:本实施例是一种均质管材数控弯曲回弹角计算方法。本实施例中,弯曲的管材选用ta18钛合金,外径d为12mm,初始壁厚t0为0.9mm,弯曲半径ρ为24mm,回弹前的弯曲角θ为90゜,初始弹性模量e0为100380mpa,弹性模量随塑性变形的稳定值ea为94109mpa,系数ξ、a0、a1、b1、a2和b2分别为-59.08、1.11687、3.25907、0.00409、1.02701和0.02799,泊松比ν为0.3,强化系数k为1326.47mpa,硬化指数n为0.0702,材料常数b为-0.0006。所述弯曲半径ρ为弯曲中心9至几何中性层1的距离。通过以下步骤实现弯曲回弹角的计算,其具体过程是:步骤1,确定应力/应变中性层偏移量de和屈服点处的应变εs:应力中性层是指管材在弯曲时,管材弯曲后横截面4上轴向应力为零处的中间层,应变中性层是指管材在弯曲时,管材弯曲后横截面上应变为零处的中间层。本发明假设应力中性层与应变中性层重合,即为所述的应力/应变中性层2。管材弯曲时,为了平衡管材内外侧的力矩,管材弯曲后横截面4上的应力/应变中性层2向弯曲侧偏移,不再与几何中性层1重合,所产生的偏移量为de。根据式(1)确定应力/应变中性层偏移量de:其中,ρ为弯曲半径,r为管材内半径。本实施例中,确定的应力/应变中性层偏移量de=0.55mm。根据式(2)确定屈服点处的应变εs:e0εs=k(εs+b)n(2)其中,e0为初始弹性模量,k为强化系数,n为硬化指数,b为材料常数。本实施例中,确定的屈服点处的应变εs=0.0095。步骤2,确定管材弯曲后横截面上随位置变化的壁厚t和轴向应变εθ:根据式(3)确定管材弯曲后横截面上随位置变化的壁厚t:其中,t0为管材的初始壁厚,为管材弯曲后横截面外表面上某一点与对称轴之间的夹角,本实施例中,确定的管材弯曲后横截面4上随位置变化的壁厚t:通过管材弯曲后横截面4上某一点到管材几何中性层1的距离y计算弯管的轴向应变εθ,具体过程是:ⅰ确定管材弯曲后横截面上某一点到管材几何中性层的距离y根据式(4)确定管材弯曲后横截面上某一点到管材几何中性层1的距离y:本实施例中,确定的管材弯曲后横截面4上某一点到管材几何中性层的距离y为:ⅱ确定弯管的轴向应变εθ根据式(5)确定弯管的轴向应变εθ:本实施例中,确定的弯管轴向应变εθ:步骤3,确定收缩应变比csr:根据式(6)确定随塑性变形变化的收缩应变比csr:其中,a0,a1,a2,b1,b2为材料常数。本实施例中,确定的收缩应变比csr:步骤4,确定弯管的等效应变根据式(7)确定弯管的等效应变本实施例中,确定的弯管的等效应变步骤5,确定随塑性变形变化的弹性模量e′:根据式(8)确定随塑性变形变化的弹性模量e′:其中,ea为随塑性变形的增加弹性模量趋于稳定时的值,ξ为系数。本实施例中,确定的随塑性变形变化的弹性模量e′:步骤6,确定管材弯曲内侧弹塑性分界处与几何中性层1之间的夹角β和弯曲外侧弹塑性分界处与几何中性层之间的夹角α:根据式(9),用数值求解方法确定管材弯曲外侧弹塑性分界处与几何中性层之间的夹角α和弯曲内侧弹塑性分界处与几何中性层之间的夹角β。本实施例中,确定的管材弯曲内侧弹塑性分界处与几何中性层之间的夹角β为1.6879,弯曲外侧弹塑性分界处与几何中性层之间的夹角α为1.6365。步骤7,确定回弹角δθ:根据式(10)确定系数p:根据式(11)和(12)确定回弹前弯管外侧塑性变形区5各轴向力之和c1、回弹前弯管内侧弹性变形区7各轴向力与弯管外侧弹性变形区6各轴力之和c2、回弹前弯管内侧塑性变形区8各轴向力之和c3、c4为回弹时弯管外侧塑性变形区5各轴向力之和的-(ρe+de)倍、c5为回弹时弯管内侧弹性变形区7各轴向力与弯管外侧弹性变形区6各轴向力之和的-(ρe+de)倍、c6为回弹时弯管内侧塑性变形区8各轴向力之和的-(ρe+de)倍:其中,ν为泊松比,q为管材弯曲前横截面3面积,根据式(12)得到:q=t2+2tr(12)本实施例中,确定的c1、c2、c3、c4、c5和c6的值如表1所示。c1c2c3c4c5c618643.42-68.34-23897.255583967.99-1588.43-6907943.17根据式(13)得到弯管回弹后的曲率本实施例中,确定的弯管回弹后的曲率为0.00402。根据式(14)得到弯管的回弹角δθ:其中,θ为回弹前的弯曲角90°。本实施例中,确定的弯管的回弹角δθ为8.87°。实施例二本实施例是一种管材数控弯曲回弹角计算方法。本实施例中,弯曲的管材选用ta18钛合金,外径d为12mm,初始壁厚t0为0.9mm,弯曲半径ρ为24mm,回弹前的弯曲角θ不同于实施例1中弯曲角为120゜,初始弹性模量e0为100380mpa,弹性模量随塑性变形的稳定值ea为94109mpa,系数ξ、a0、a1、b1、a2和b2分别为-59.08、1.11687、3.25907、0.00409、1.02701和0.02799,泊松比ν为0.3,强化系数k为1326.47mpa,硬化指数n为0.0702,材料常数b为-0.0006。通过以下步骤实现弯曲回弹角的计算,其具体过程是:步骤1,确定应力/应变中性层偏移量de和屈服点处的应变εs:应力中性层是指管材在弯曲时,管材弯曲后横截面上轴向应力为零处的中间层,应变中性层是指管材在弯曲时,管材弯曲后横截面上应变为零处的中间层。本发明假设应力中性层与应变中性层重合,即为所述的应力/应变中性层2。管材弯曲时,为了平衡管材内外侧的力矩,管材弯曲后横截面上的应力/应变中性层向弯曲侧偏移,不再与几何中性层重合,所产生的偏移量为de。根据式(1)确定应力/应变中性层偏移量de:其中,ρ为弯曲半径,r为管材内半径。本实施例中,确定的应力/应变中性层偏移量de=0.55mm。根据式(2)确定屈服点处的应变εs:e0εs=k(εs+b)n(2)其中,e0为初始弹性模量,k为强化系数,n为硬化指数,b为材料常数。本实施例中,确定的屈服点处的应变εs=0.0095。步骤2,确定管材弯曲后横截面上随位置变化的壁厚t和轴向应变εθ:根据式(3)确定管材弯曲后横截面上随位置变化的壁厚t:其中,t0为管材的初始壁厚,为管材弯曲后横截面外表面上某一点与对称轴之间的夹角,本实施例中,确定的管材弯曲后横截面上随位置变化的壁厚t:通过管材弯曲后横截面上某一点到管材几何中性层的距离y计算弯管的轴向应变εθ,具体过程是:ⅰ确定管材弯曲后横截面上某一点到管材几何中性层的距离y根据式(4)确定管材弯曲后横截面上某一点到管材几何中性层的距离y:本实施例中,确定的管材弯曲后横截面上某一点到管材几何中性层的距离y为:ⅱ确定弯管的轴向应变εθ根据式(5)确定弯管的轴向应变εθ:本实施例中,确定的弯管轴向应变εθ:步骤3,确定收缩应变比csr:根据式(6)确定随塑性变形变化的收缩应变比csr:其中,a0,a1,a2,b1,b2为材料常数。本实施例中,确定的收缩应变比csr:步骤4,确定弯管的等效应变根据式(7)确定弯管的等效应变本实施例中,确定的弯管的等效应变步骤5,确定随塑性变形变化的弹性模量e′:根据式(8)确定随塑性变形变化的弹性模量e′:其中,ea为随塑性变形的增加弹性模量趋于稳定时的值,ξ为系数。本实施例中,确定的随塑性变形变化的弹性模量e′:步骤6,确定管材弯曲内侧弹塑性分界处与几何中性层之间的夹角β和弯曲外侧弹塑性分界处与几何中性层之间的夹角α:根据式(9),用数值求解方法确定管材弯曲外侧弹塑性分界处与几何中性层之间的夹角α和弯曲内侧弹塑性分界处与几何中性层之间的夹角β。本实施例中,确定的管材弯曲内侧弹塑性分界处与几何中性层之间的夹角β为1.6879,弯曲外侧弹塑性分界处与几何中性层之间的夹角α为1.6365。步骤7,确定回弹角δθ:根据式(10)确定系数p:根据式(11)和(12)确定回弹前弯管外侧塑性变形区5各轴向力之和c1、回弹前弯管内侧弹性变形区7各轴向力与弯管外侧弹性变形区6各轴力之和c2、回弹前弯管内侧塑性变形区8各轴向力之和c3、c4为回弹时弯管外侧塑性变形区5各轴向力之和的-(ρe+de)倍、c5为回弹时弯管内侧弹性变形区7各轴向力与弯管外侧弹性变形区6各轴向力之和的-(ρe+de)倍、c6为回弹时弯管内侧塑性变形区8各轴向力之和的-(ρe+de)倍:其中,ν为泊松比,q为管材弯曲前横截面3的面积,根据式(12)得到:q=t2+2tr(12)本实施例中,确定的c1、c2、c3、c4、c5和c6的值如表2所示。c1c2c3c4c5c618643.42-68.34-23897.255583967.99-1588.43-6907943.17根据式(13)得到弯管回弹后的曲率本实施例中,确定的弯管回弹后的曲率为0.00402。根据式(14)得到弯管的回弹角δθ:其中,θ为回弹前的弯曲角120°。本实施例中,确定的弯管的回弹角δθ为11.83°。当前第1页12