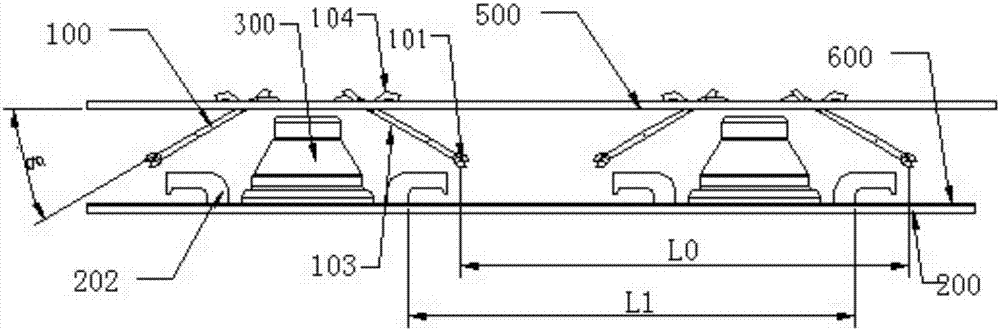
本发明涉及进行敲键操作的键开关装置,特别涉及一种用于支撑键帽的支撑件安装方法、支撑件安装装置以及设置有支撑件安装装置的自动安装装置。
背景技术:现有笔记本型键盘、掌上计算机型键盘或者其他薄型键盘中普遍采用薄型支撑件结构支撑键帽,通过于中部或端部相互支撑的支撑件分别与支承底板、键帽连接形成相互联动的支撑结构。一个键盘的一般由70-82个键开关单元构成,支撑一个键帽需两个支撑件,由于支撑件结构纤细,要将140个-164个形成支撑配合的支撑件安装在支承底板上难很大且工效非常低。如图12和13所示,由两个结构相同的第一支撑件103、第二支撑件100交叉排列或对应排列构成支撑件单元105,成行成列排列(图中未表示)或成行纵横排列的支撑件单元105通过工艺连接筋501连接构成支撑件排列板500,其中第一支撑件103、第二支撑件100交叉排列(图中未表示)最省料。所述两个结构相同的第一支撑件103、第二支撑件100形成端部相互支撑的结构,参见图8。如图14和图15所示,由一个第一支撑件103、第二支撑件100交叉排列或对应排列构成支撑件单元105,成行成列排列或成行纵横排列(图中未表示)的支撑件单元105通过工艺连接筋501连接构成支撑件排列板500,所述第一支撑件103、第二支撑件100形成中部相互支撑的结构,参见图16。所述支撑件排列板500也可分别由第一支撑件103或第二支撑件100成行成列排列(图中未表示)或成行纵横排列构成。以现有键盘为例,如图9、图10、图11所示,现有键盘的标键区(包括数字键、字母键等)的键帽间的间距大多约为19mm,相邻的键开关单元的支承底板连接部202的配合部间的间距L1=19mm,行间距L11=19mm。但之前公开的申请人的发明之中(PCT/CN2011/001295),如图1、图2、图3所示,将第一支撑件103、第二支撑件100成型为与支撑件排列板500成夹角g度,夹角g的大小应确保第一支撑件103、第二支撑件100呈安装姿态(支撑件下配合部101与支承底板连接部202的入口对应)。如图2所示,第一支撑件103、第二支撑件100的支撑件下配合部101与支承底板连接部202位置安装对应,要实现连续成行或成列多个支撑件同时安装,必须确保支承底板200上相邻的支承底板连接部202间的间距L1=支撑件排列板500上的相邻的支撑件单元105间的间距L0。如果L0与L1不相等,就会出现始终只有一个按键单元的一对支撑件下配合部与支承底板连接部202位置安装对应。其余的支撑件下配合部101均与支承底板连接部202错位,错位的距离=L0-L1的差值。如图3、图4所示,安装过程中,支撑件排列板500与支承底板200相对移动至支撑件下配合部101与支承底板200的上板面或薄膜开关片上表面接触,支撑件排列板500与支承底板200距离为H。第一支撑件103、第二支撑件100同时绕支撑件排列板500旋转,支撑件与支撑件排列板500的夹角g逐渐变大,支撑件排列板500与支承底板200的距离H也逐渐变大,工艺连接筋501的变形量也逐渐变大,在安装过程中,同时必须确保支撑件下配合部101与支承底板200的上板面或薄膜开关片上表面一直接触。至第一支撑件103、第二支撑件100使支承底板连接部202产生弹性变形后,第一支撑件103、第二支撑件100越过支承底板连接部202的悬臂凸包205,支撑件下配合部101进入支承底板连接部202的配合部的配合空间内。如图5所示,剪掉工艺连接筋501后,第一支撑件103、第二支撑件100形成相互撑的联动支撑结构(图中键帽400未表示,薄膜开关片001位于支承底板200的上板面)。上述方案存在以下问题:1、支撑件成型为与支撑件排列板500成夹角g,工艺连接筋501折弯过程中会产生硬化现象。在安装过程中,支撑件绕支撑件排列板500转动易出现工艺连接筋501断裂。工艺连接筋501强度太大时,支撑件需较大的转动推力,易使支撑件变形导致装配精度下降,强度太小时,支撑件要越过承底板连接部202的悬臂凸包205困难,会出现支撑件未进入支承底板连接部202的配合部的配合空间工艺连接筋501就断裂,批量安装时只要有一个工艺连接筋501断裂,就会造成安装效率的大幅下降。2、在安装过程中,必须确保支撑件下配合部101与支承底板200的上板面或薄膜开关片上表面接触,同时支撑件排列板500与支承底板200相对移动,夹角g逐渐变大,距离H也逐渐变大。机构设计复杂且可靠性低。3、两个以上支撑件安装时必须确保L0=L1,必然导致材料的大量浪费,约浪费材料约36%。4、安装工序多、工装数量多。5、单个一个键单元一个地安装支撑件效率太低。如图6和7所示,第一支撑件103、第二支撑件100结构及尺寸相同,支撑件的水平配合尺寸为L2,支撑件有左右对称的支撑件下配合部101、支撑件上配合部104,在支撑件的上端部的左右分别有支撑件上触压部102、支撑件下触压部106。一个键开关单元的支承底板200尺寸比键帽400(图中未表示)尺寸略大,一个单元的支承底板200尺寸等于相邻的两个键帽400间的间距,支承底板连接部202由四个支承底板转动部201构成,四个支承底板转动部201分别位于两个支撑垂直折弯边上,一个单元的支承底板200的支承底板转动部201的配合部水平间距为L3,垂直间距为L4,其中L3略大于L2。如图8和16所示,每个键盘均由多个键开关单元成行成列排列构成,键开关单元的键帽400与支承底板200上的一组支承底板连接部202的配合部对应,每个键开关单元均由有开关触发点的橡胶弹圈300、有开关触点电路的薄膜开关片001、键帽400、一组支撑件单元105构成,其中支撑件上配合部104与键帽400(图中未表示)配合连接,支撑件下配合部101与支承底板连接部202配合连接,支撑件上触压部102、支撑件下触压部106形成相互支撑并支撑键帽400的联动结构,并通过呈圆拱状动作部件--橡胶弹圈300将键帽400向上顶起。如图6和8所示,支撑件上触压部102、支撑件下触压部106位于支撑件单元105的端部,用于端部相互支撑的第一支撑件103、第二支撑件100结构尺寸相同并支撑键帽400(图中未表示),且从侧面看呈近似的八型。支撑件上配合部104与键帽400(图中未表示)转动连接,支撑件下配合部101与支承底板连接部202滑动连接。如图16所示,支撑件上触压部102、支撑件下触压部106位于支撑件单元105的中部,用于中部相互支撑的第一支撑件103、第二支撑件100支撑键帽400(图中未表示),且从侧面看呈近似的X型,支撑件上配合部104与键帽400(图中未表示)滑动连接,支撑件下配合部101与支承底板连接部202转动连接。现有方案要将支撑件排列板500上的成行或成列的支撑件单元105连续高效地安装在支承底板连接部202的配合部内,应确保在支撑件排列板500上的同一行的支撑件单元105间的间距L0必须等于同一行的相邻键开关单元的支承底板连接部202的配合部间的间距L1。同时在同一键开关单元内,第一支撑件103、第二支撑件100呈安装姿态时,第一支撑件103、第二支撑件100的支撑件下连接部101间的间距L0必须大于或等于支承底板连接部202的配合部间的间距L1。如图12和13所示,用于端部相互支撑的第一支撑件103、第二支撑件100对应排列构成支撑件单元105,支撑件排列板500上支撑件单元105间的间距L6=10.6mm、L7=14mm,如果采用上述专利的安装方式,支撑件单元105的间距也必须冲压成19mm*19mm。如此造成以下问题:1、必然导致材料的大量浪费,约浪费材料约36%。2、单个一个键单元一个地安装效率又太低。如图14所示,用于中部相互支撑的第一支撑件103、第二支撑件100对应排列构成支撑件单元105,支撑件单元105间的间距L6=12mm、L7=22mm,L7大于支撑件单元105的间距19mm,导致无法成行成列地安装支撑件单元105,只能一次安装一个支撑件单元105,要实现成行成列地安装支撑件单元105,第一支撑件103,第一支撑件103、第二支撑件100的长度均必须控制在8mm以内,第一支撑件103、第二支撑件100分别与键帽400、支承底板200连接形成相互支撑的结构时,第一支撑件103、第二支撑件100分别与键帽400的连接太集中于键帽400的中部附近,导致键帽连接部100分布困难,橡胶弹圈300无安装位置。如图15所示,用于中部相互支撑的第一支撑件103、第二支撑件100交叉排列构成支撑件单元105,支撑件单元105间的间距L6=17mm、L7=16.8mm,但由于在同一支撑件单元105内,第一支撑件103、第二支撑件100无法相对移动、无法呈安装姿态同时安装,只能采用先安装完所有的第一支撑件103后,再安装第二支撑件100,同时支撑件单元105的第一支撑件103、第二支撑件100交叉排列,组成一个支撑件单元105的间距应保证为19mm*19mm,此交叉排列的第一支撑件103、第二支撑件100构成的支撑件排列板500。如果采用上述方案的安装方式:1、增加了安装工序、增加了工装数量。2、同时安装效率大幅下降。3、同时浪费材料。而且,采用工艺连接筋501工艺连接筋501连接后折弯至一定角度,工艺连接筋501容易断裂,安装过程中很不稳定。如图9、现有的笔记本电脑型键盘打字键区的键行与行之间错位排列,其中,第一行为功能键区,包括F1、F2等键;第二行共有12个大小相同的键;第三行的Q字母键的左边缘的位置在第二行的1数字键的中部附近,第三行共有12个大小相同的键;第四行的A字母键的左边缘的位置在第三行的Q字母键的左边缘向右1/3附近,第四行共有11个大小相同的键;第五行的Z字母键的左边缘的位置在第四行的A字母键的中部附近,第五共有10个大小相同的键。所有型号相同键盘(包括台式机键盘、笔记本电脑型键盘)的打字键区(字母键,如A符号键、B符号键等)的键,其大小同、相对位置均相同、符号的排列方式相同,一般情况现有笔记本电脑型键盘第一行功能键区排列有16-19个键,第二行排列有15-17个键。除功能键所在行以外,其它行一般都存在一些按键的大小与打字键区按键不同的按键,如Enter键等。因为支撑件采用步进模具连续冲压,支撑件之间的距离都是一致的,即使像Enter键之类的按键采用同样的支撑件也是无法实现连续安装的,必须采用额外的多余支撑个收集装置进行安装。
技术实现要素:本发明的目的在于:针对上述存在的问题,提供一种节约材料,且能够高效地将支撑件排列板上的支撑件安装到支承底板的用于支撑键帽的支撑件安装方法、支撑件安装装置以及设置有支撑件安装装置的自动安装装置。本发明的技术方案是这样实现的:一种用于支撑键帽的支撑件安装方法,其特征在于:包括以下步骤:成型支撑件,其中所述支撑件按设计规则排列形成支撑件排列板;剪断连接支撑件的工艺连接筋,所述支撑件被移至安装位置,所述支撑件呈安装姿态;将支承底板或键帽移至安装位置;所述支撑件分别或同时进入支承底板连接部或键帽连接部内;所述支撑件形成相互支撑的结构。本发明所述的用于支撑键帽的支撑件安装方法,其剪断连接支撑件的工艺连接筋后,所述支撑件进入支撑件安装装置,并通过所述支撑件安装装置移动至安装位置。本发明所述的用于支撑键帽的支撑件安装方法,其剪断连接支撑件的工艺连接筋后,所述支撑件由水平位置旋转一定角度;支撑件继续移动,至支撑件接近支承底板连接部时,支撑件进入安装位置并呈安装姿态进入支承底板连接部或键帽连接部内。本发明所述的用于支撑键帽的支撑件安装方法,其所述支撑件的安装姿态为支撑件与竖立平面成一定夹角。本发明所述的用于支撑键帽的支撑件安装方法,其所述支撑件的安装姿态为支撑件与竖立平面的夹角在0度附近。本发明所述的用于支撑键帽的支撑件安装方法,其所述安装位置为支撑件连接部与支承底板连接部或键帽连接部位置安装对准处。本发明所述的用于支撑键帽的支撑件安装方法,其所述成型支撑件是通过冲压成型。本发明所述的用于支撑键帽的支撑件安装方法,其所述成型支撑件以及成型支承底板均是在对应金属带状料上沿长度方向连续冲压成型。本发明所述的用于支撑键帽的支撑件安装方法,其所述成型支撑件、成型支承底板以及支撑件安装过程连续、自动、同步进行。本发明所述的用于支撑键帽的支撑件安装方法,其所述支撑件与竖立平面成一定夹角进入支承底板连接部或键帽连接部后,所述支撑件绕支承底板连接部或键帽连接部旋转,所述支撑件形成相互触压的支撑结构。本发明所述的用于支撑键帽的支撑件安装方法,其所述支撑件无阻碍插入或进入支承底板连接部或键帽连接部内,所述支撑件无阻碍绕支承底板连接部或键帽连接部旋转,所述支撑件形成相互触压的支撑结构。本发明所述的用于支撑键帽的支撑件安装方法,其所述支撑件通过气流吹动绕支承底板连接部或键帽连接部旋转。本发明所述的用于支撑键帽的支撑件安装方法,其所述支承底板位于安装位置时,所述支撑件排列板距支承底板的距离≥400mm。本发明所述的用于支撑键帽的支撑件安装方法,其所述支撑件通过支撑件安装装置由水平位置旋转一定角度,位移至安装位置并呈安装姿态。本发明所述的用于支撑键帽的支撑件安装方法,其所述支撑件安装装置有通道始入口,在冲断连接支撑件的工艺连接筋后,所述支撑件进入支撑件安装装置的通道始入口或所述支撑件进入支撑件安装装置的通道始入口后再冲断工艺连接筋。本发明所述的用于支撑键帽的支撑件安装方法,其所述支撑件安装装置的通道始入口纵横排列,所述支撑件排列板上的支撑件或支撑件单元纵横排列,所述支撑件排列板的行的数量与纵横排列的通道始入口的行的数量相等。本发明所述的用于支撑键帽的支撑件安装方法,其所述成型支撑件的行数等于至少一个键盘的键帽的行数。本发明所述的用于支撑键帽的支撑件安装方法,其所述支撑件按设计规则排列:由第一支撑件成行排列或第一支撑件纵横排列构成支撑件排列板;也可由第二支撑件成行排列或第二支撑件纵横排列构成支撑件排列板。本发明所述的用于支撑键帽的支撑件安装方法,其所述支撑件按设计规则排列为支撑件交错排列或对称排列,且两两组成一个支撑件单元。本发明所述的用于支撑键帽的支撑件安装方法,其所述支撑件单元成行排列或纵横排列。本发明所述的用于支撑键帽的支撑件安装方法,其所述两个支撑件组成一个支撑件单元,其中一个支撑件单元内的两个支撑件可以先后安装至对应的支承底板连接部内;一个支撑件单元内的两个支撑件也可以同时安装至对应的支承底板连接部内。本发明所述的用于支撑键帽的支撑件安装方法,其所述支撑件排列板以速度V1相对于支撑件安装装置运动,相邻支撑件之间沿运动方向的距离为L6;所述支承底板的打字键区并沿支承底板长度方向的相邻的支承底板连接部的间距L1,所述支承底板以速度V2相对支撑件安装装置运动;其中V1/V2=n*L6/L1,确保连续冲压的支撑件通过支撑件安装装置连续进入支承底板连接部内。一种用于上述安装方法的支撑件安装装置,其所述支撑件安装装置有支撑件的收集位置及支撑件的安装位置,所述支撑件排列板上的工艺连接筋被冲断时,所述支撑件安装装置将支撑件排列板上的支撑件从收集位置移动至安装位置,其中,所述收集位置为支撑件安装装置收集从支撑件排列板上冲裁下的支撑件的位置,所述安装位置为支撑件安装装置使支撑件连接部与支承底板连接部或键帽连接部安装对准的位置,所述支撑件进入支承底板连接部或键帽连接部内,所述支撑件形成相互支撑结构。本发明所述的支撑件安装装置,其剪断连接支撑件的工艺连接筋后,所述支撑件进入支撑件安装装置,所述支撑件由水平位置旋转一定角度C;支撑件继续向下移动,至支撑件接近支承底板连接部时,所述支撑件呈一定角度C1进入支承底板连接部或键帽连接部内,所述支撑件形成相互支撑结构。本发明所述的支撑件安装装置,其所述支撑件从支撑件安装装置进入支承底板连接部或键帽连接部内后,所述支撑件绕支承底板连接部或键帽连接部旋转形成相互支撑结构。本发明所述的支撑件安装装置,其所述支撑件安装装置由通道旋转安装工装构成。本发明所述的支撑件安装装置,其所述支撑件安装装置由通道旋转安装工装以及相对移动工装构成。本发明所述的支撑件安装装置,其所述支撑件安装装置由吸附旋转安装工装构成。本发明所述的支撑件安装装置,其所述支撑件安装装置由往复旋转安装工装构成。本发明所述的支撑件安装装置,其所述通道旋转安装工装由整体式结构的通道安装工装构成。本发明所述的支撑件安装装置,其所述通道旋转安装工装由至少一个单元通道安装工装或分体式结构的通道工装构成。本发明所述的支撑件安装装置,其所述分体式结构的通道工装由I单元通道工装和II单元通道工装构成,其中I单元通道工装位于II单元通道工装之上。本发明所述的支撑件安装装置,其在所述整体式结构的通道安装工装两端分别设置有多个纵横排列的并位于收集位置的通道始入口以及多个纵横排列的并位于安装位置的通道终出口,所述通道始入口分别与支撑件排列板上的一个支撑件或一个支撑件单元位置对准,所述通道始入口、通道终出口由连接通道连通,所述支撑件由收集位置移动至安装位置。本发明所述的支撑件安装装置,其所述单元通道安装工装位于收集位置时,所述单元通道安装工装的通道始入口与支撑件排列板上的支撑件位置对准;所述单元通道安装工装位于安装位置时,所述单元通道安装工装的通道终出口与支承底板连接部位置对准,所述支撑件由收集位置移动至安装位置。本发明所述的支撑件安装装置,其分体式结构的通道工装的通道始入口位于I单元通道工装的上端,所述分体式结构的通道工装的通道终出口位于II单元通道工装的下端,所述通道始入口与通道终出口导通时,I通道与II通道连通形成连接通道。本发明所述的支撑件安装装置,其所述I单元通道工装位于收集位置时,所述支撑件进入I单元通道工装的通道始入口,所述II单元通道工装位于安装位置时,所述II单元通道工装的通道终出口与支承底板连接部安装位置对准,所述支撑件由收集位置移动至安装位置。本发明所述的支撑件安装装置,其所述通道旋转安装工装的一端有能水平容纳一个支撑件或一个支撑件单元的通道始入口,另一端有支撑件的通道终出口,所述通道终出口、通道始入口通过连接通道连通。本发明所述的支撑件安装装置,其所述通道始入口纵横排列,所述支撑件排列板上的支撑件或支撑件单元纵横排列,所述支撑件排列板的行的数量与纵横排列的通道始入口的行的数量相等。本发明所述的支撑件安装装置,其所述支撑件排列板上的行数等于至少一个键盘的键帽的行数。本发明所述的支撑件安装装置,其所述通道终出口能水平容纳一个支撑件或一个支撑件单元。本发明所述的支撑件安装装置,其所述通道始入口向下逐渐收窄后向下贯通形成连接通道,其中通道始入口向下逐渐收窄形成旋转位移斜面。本发明所述的支撑件安装装置,其向下逐渐收窄后的连接通道由竖立通道构成或由斜向通道及竖立通道共同构成。本发明所述的支撑件安装装置,其所述连接通道末端为竖立通道。本发明所述的支撑件安装装置,其通道始入口向下逐渐收窄后与斜向通道连通,斜向通道向下再与竖立通道连通。本发明所述的支撑件安装装置,其所述通道旋转安装工装的连接通道的末端的通道延伸内侧壁或通道延伸外侧壁有旋转气流口与支撑件对准,形成支撑件气动旋转结构。本发明所述的支撑件安装装置,其所述支撑件安装时,所述支撑件从通道延伸内侧壁或通道延伸外侧壁向外或向内旋转一定角度后,由旋转限位面限制支撑件在旋转过程中从支承底板的配合部内脱出。本发明所述的支撑件安装装置,其所述通道延伸内侧壁或通道延伸外侧壁分别为连接通道的末端的延伸面,在通道延伸内侧壁或通道延伸外侧壁与旋转限位面之间有支撑件旋转空间。本发明所述的支撑件安装装置,其所述旋转限位面与支撑件绕支承底板连接部转动的圆同心。本发明所述的支撑件安装装置,其所述连接通道有向下流动的支撑件推动气流。本发明所述的支撑件安装装置,其所述相对移动工装由X驱动机构以及Y驱动机构或旋转驱动装置或往复驱动装置构成。本发明所述的支撑件安装装置,其所述支撑件由收集位置移动至安装位置是通过连接通道实现。本发明所述的支撑件安装装置,其所述支撑件由收集位置移动至安装位置是通过连接通道及相对移动工装实现。本发明所述的支撑件安装装置,其所述支撑件由收集位置移动至安装位置是通过I通道及相对移动工装使I单元通道工装与II单元通道工装产生相对位移实现。本发明所述的支撑件安装装置,其所述构成相对移动工装的X驱动机构和Y驱动机构驱动I单元通道工装、II单元通道工装产生相对移动使I单元通道工装的通道始入口与II单元通道工装的通道终出口导通或关闭。本发明所述的支撑件安装装置,其所述构成相对移动工装的X驱动机构和Y驱动机构驱动单元通道安装工装与支承底板产生相对移动,使单元通道安装工装的通道终出口与支承底板连接部位置对准。本发明所述的支撑件安装装置,其所述通道旋转安装工装有通道始入口、通道终出口,所述支撑件排列板、支承底板相对于通道旋转安装工装移动,其中所述支撑件移至通道旋转安装工装的通道始入口;所述支承底板移至通道旋转安装工装的通道终出口,所述安装位置位于通道旋转安装工装的通道终出口的位置。本发明所述的支撑件安装装置,其所述支撑件排列板为支撑件交错排列或对称排列。本发明所述的支撑件安装装置,其所述交错排列或对称排列的支撑件,两两组成一个支撑件单元,所述支撑件单元纵横排列。本发明所述的支撑件安装装置,其两个支撑件组成一个支撑件单元,其中一个支撑件单元内的两个支撑件可以先后安装至对应的支承底板连接部内;一个支撑件单元内的两个支撑件也可以同时安装至对应的支承底板连接部内。本发明所述的支撑件安装装置,其所述I单元通道工装沿II单元通道工装上的II通道导轨移动,II单元通道工装呈卡长条形,在II单元通道工装上有II通道导轨,所述I单元通道工装、II单元通道工装的移动通过相对移动工装实现。本发明所述的支撑件安装装置,其XY安装工装有安装位置及收集位置,所述安装位置是多个II单元通道工装处于最大间距及多个I单元通道工装处于最大间距时,所述收集位置是多个II单元通道工装处于最小间距及多个I单元通道工装处于最小间距时。本发明所述的支撑件安装装置,其所述支撑件排列板有n行连续的支撑件单元时,所述XY安装工装由n个II单元通道工装构成,所述I单元通道工装的数量与需要安装的支承底板连接部的配合部数量相同。本发明所述的支撑件安装装置,其所述相对移动工装由多个II单元通道工装间的有弹性元件或磁性元件、Y驱动机构、X驱动机构构成。本发明所述的支撑件安装装置,其所述同行的各相邻的I单元通道工装通过悬臂挂钩限位连接,X驱动机构可推动各I单元通道工装沿II通道导轨移动至最小间距,X驱动机构也可拉动各I单元通道工装沿II通道导轨移动至悬臂挂钩限位时,各I单元通道工装至最大间距。本发明所述的支撑件安装装置,其由I单元通道工装、呈长条形的II单元通道工装、Y驱动机构、X驱动机构构成XY安装工装。本发明所述的支撑件安装装置,其有两个或两个以上的支承底板或键排列工装的安装工位,有至少两个或两个以上的XY安装工装可沿Y方向移动;当一个或两个以上的XY安装工装位于收集位置时,至少一个XY安装工装位于安装工位,所述安装工位位于支撑件排列板一侧或两侧。本发明所述的支撑件安装装置,其所述I单元通道工装位于II单元通道工装之上,所述I单元通道工装的I通道与呈长条形的II单元通道工装的II通道连通,所述I单元通道工装、II单元通道工装刚性连接形成单元通道安装工装;所述XY安装工装由单元通道安装工装、X驱动机构构成,所述支撑件安装装置有两个安装工位,并由两个连接在一起的XY安装工装构成,当支撑件排列板有n行连续的支撑件或支撑件单元时,XY安装工装有n个,有n个安装工位,每个安装工位n个支承底板,当XY安装工装位于收集位置时,n个III通道工装间距最小,同时III通道工装的通道始入口分别与所述支撑件排列板上的支撑件或支撑件单元位置对准;在安装支撑件时,XY安装工装分别移动至n个安装工位上方,同时n个单元通道安装工装分散移动至n个支承底板的行或键排列工装一一对应。本发明所述的支撑件安装装置,其所述两个安装工位上的支承底板或键排列工装均沿X方向或Y方向同步联动,支撑件排列板沿X方向移动,n个单元通道安装工装均沿Y方向往复移动。本发明所述的支撑件安装装置,其所述支撑件可以沿行所在方向每次一个连续经由I单元通道工装进入II单元通道工装,也可以沿行所在方向每次多个连续经由I单元通道工装进入II单元通道工装。本发明所述的支撑件安装装置,其所述支撑件可以沿行垂直方向每次一列连续经由I单元通道工装进入II单元通道工装,也可以沿行垂直方向每次多列连续经由I单元通道工装进入II单元通道工装。本发明所述的支撑件安装装置,其所述支撑件安装装置内置于冲压成型支撑件排列板的模具中或冲床中;或者仅所述I单元通道工装内置于冲压成型支撑件排列板的模具中或冲床中。本发明所述的支撑件安装装置,其所述吸附旋转安装工装由在收集位置与安装位置往复运动的一个吸附旋转吸头、能水平容纳一个支撑件的通道始入口、能水平容纳一个支撑件的通道终出口、落料冲头、往复驱动装置构成,在一个往复摆杆的一端固连接吸附旋转吸头,往复摆杆的另一端与机座转动连接,往复摆杆绕机座连接部往复转动,使吸附旋转吸头作往复圆周运动;在收集位置时,往复摆杆与支撑件排列板垂直,吸附旋转吸头的端部与连接通道的通道终出口位置对准;在安装位置时,往复摆杆与支撑件排列板平行,吸附旋转吸头端部上的支撑件连接部与支承底板连接部位置对准并进入。本发明所述的支撑件安装装置,其所述往复旋转安装工装由分别作圆周运动的至少一个单元通道安装工装、旋转驱动装置、落料冲头构成或由至少一组单元通道线性阵列组、旋转装置、落料冲头构成;当作圆周往复运动的单元通道安装工装为一个或单元通道线性阵列组为一组时,一个单元通道安装工装或一组单元通道线性阵列组在收集位置与安装位置作圆周往复运动,并在运动过程中与收集位置、安装位置分别对应;当作圆周运动的单元通道安装工装为至少两个或单元通道线性阵列组为至少两组时,其中一个单元通道安装工装或一组单元通道线性阵列组位于收集位置时,另一个单元通道安装工装或另一组单元通道线性阵列组位于安装位置。一种采用了上述支撑件安装装置用于上述安装方法的自动安装装置,其特征在于:包括输送支撑件排列板的支撑件板送料装置、输送支承底板的支承底板送料装置或输送键排列工装的键排列送料装置、冲裁支撑件排列板上的工艺连接筋的落料装置、将第一支撑件或第二支撑件安装到支承底板连接部或键排列工装上的键帽连接部形成联动支撑结构的支撑件安装装置。本发明所述的自动安装装置,其所述支撑件排列板、落料装置位于支撑件安装装置一端,所述支承底板或键排列送料装置位于支撑件安装装置另一端,其中支撑件排列板位于落料装置与支撑件安装装置之间。本发明所述的自动安装装置,其所述支撑件安装装置有支撑件的收集位置及支撑件的安装位置,所述支撑件板送料装置输送支撑件排列板至收集位置,冲裁支撑件排列板上的工艺连接筋后,所述支撑件安装装置的从收集位置输送第一支撑件或第二支撑件位移至安装位置;所述支承底板送料装置输送支承底板或键排列送料装置输送键排列工装至安装位置。本发明所述的自动安装装置,其还包括支撑件步进模,所述支撑件步进模在金属带状料上成型支撑件排列板后,所述支撑件排列板被直接送入支撑件安装装置。本发明所述的自动安装装置,其所述自动安装装置还包括支承底板步进模,所述支承底板步进模在金属带状料上成型支承底板后,所述支承底板被直接送入支撑件安装装置。本发明所述的自动安装装置,其所述自动安装装置还包括薄膜电路安装装置,薄膜电路安装装置位于支承底板步进模与支撑件安装装置之间。本发明所述的自动安装装置,其所述自动安装装置还有键帽安装装置,所述键帽安装装置位于支撑件安装装置出口外侧。本发明所述的自动安装装置,其所述自动安装装置还有多余支撑件收集安装装置,所述多余支撑件收集安装装置用于收集支撑件排列板上每行多余的支撑件。本发明所述的自动安装装置,其所述多余支撑件收集安装装置由驱动支承底板的沿X方向移动及Y方向移动的通道移动工装、使第一支撑件或一个第二支撑件呈安装姿态的单元通道安装工装、落料装置构成。本发明所述的自动安装装置,其所述落料装置冲裁多余支撑件时,所述单元通道安装工装的通道始入口与支撑件排列板位置上每行多余支撑件位置对准,单元通道安装工装的数量与多余支撑件数量相等。本发明所述的自动安装装置,其所述多余支撑件收集安装装置位于支撑件步进模与支撑件安装装置之间或位于支撑件安装装置后方。本发明所述的自动安装装置,其所述支撑件板送料装置可以是所述支撑件步模的送料装置,也可以是独立的通常的送料装置。本发明所述的自动安装装置,其所述支承底板送料装置可以是所述支撑件步模的送料装置,也可以是独立的通常的送料装置。本发明所述的自动安装装置,其所述支撑件板送料装置输送由第一支撑件组成的支撑件排列板,完成第一支撑件在支承底板上的安装或完成第一支撑件在键排列工装上的安装。本发明所述的自动安装装置,其另一个支撑件板送料装置输送由第二支撑件组成的支撑件排列板,所述支承底板送料装置或键排列送料装置输送已完成安装第一支撑件的支承底板或已完成安装第一支撑件的键排列工装。本发明所述的自动安装装置,其所述支撑件排列板与支承底板相对于支撑件安装装置的相对运动速度为n*L6/Lc,其中L6为支撑件排列板上相邻的两组支撑件单元间的间距,Lc为支撑件安装装置从安装位置至收集位置的距离。本发明所述的自动安装装置,其所述支撑件板送料装置、支承底板送料装置分别传送的支撑件排列板、支承底板相对于支撑件安装装置的相对运动速度为n*L6/L1,其中L6为支撑件排列板上相邻的两组支撑件单元间的间距,L1为相邻的两个键开关单元所对应的支承底板连接部的配合部间的间距。本发明所述的自动安装装置,其所述支撑件板送料装置、支承底板送料装置分别传送的支撑件排列板与支承底板相对于支撑件安装装置相对运动,剪断所述工艺连接筋的剪断距离为n*L,L为成型支撑件的步进距离。由于采用了上述技术方案,本发明的有益效果是:1.本发明采用将从支撑件排列板上收集的支撑件,移动至安装位置并实现安装,可以大幅节省材料成本,最多可省料36%,同时实现了高效、自动、可靠安装。2.可对错位排列的方式生产支撑件、对应排列的方式生产支撑件等,任何形式的支撑件都可以实现安装。生产过程中支撑件的排列方式可以采用最为省料的方式排列。3.可实现支撑件的生产及安装同步连续进行。4.本发明可采用高效的步进模具连续冲压生产成型支撑件排列板,在生产支撑件排列板的同时可高效低成本将支撑件排列板上的支撑件安装于支承底板上,从生产支撑件到安装一个键盘的支撑件仅需3秒(按步进距离3*19mm=57mm,每分冲100次计)。5.多余支撑件收集安装装置使安装一个键盘所需多余的支撑件实现了自动安装,进一步提高了安装效率。6.通过连接通道使支撑件产生移动,使支撑件呈安装姿态同时使支撑件从收集位置至安装位置实现了高效安装,采用连接通道方案移动支撑件时工装无相对移动零件、在连接通道的末端支撑件通过气动旋转安装,采用通道旋转安装工装安装支撑件零件数量最少、工装的可靠性非常高。7.通过连接通道使支撑件产生移动与工装平面驱动移动的组合,可更高效率安装支撑件。8.本发明的支撑件配合结构彻底解决了塑料支撑件安装麻烦而又容易脱落的问题。支撑件配合部插入支承底板连接部之后,通过气孔旋转即可完成安装,安装过程简单。安装后,在特定的角度内,可以保证较大的过盈量,确保支撑件无法脱落。9.支撑件安装过程中,完全无变形,不会损坏支撑件以及支承底板的配合结构,可以进一步提高配合精度。而原结构,塑料支撑件、钢丝支撑件以及原来公开的钣金冲压的支撑件,在安装过程中都是通过支撑件配合部或者是支承底板连接部的弹性变形来实现安装,安装时比较困难,易产生装配精度下降,而且配合部容易断裂。10.本发明的结构可以实现支撑件的生产和安装一体化、自动化。可以减少大量的人工成本、物流成本。简化安装过程以及安装难度后,考虑到支撑件生产过程中的特点,可以实现冲压成型支撑件之后同步自动化安装支撑件。降低成本的同时,大幅提高生产效率。11.安装之后也能比较容易的取出,可实现重复安装。采用过盈安装的方式,支撑安装到支承底板连接部内之后,取出时配合部容易断裂。本发明彻底改变了现有笔记本键盘生产劳动密集型的现状,具有设备采购成本低、支撑件生产节约材料、生产及安装高效同步进行,为大规模高效自动化生产创造了条件。附图说明为了更清楚地说明本发明实施例或现有技术中的技术方案,下面将对实施例或现有技术描述中所需要使用的附图作简单地介绍,显而易见地,下面描述中的附图是本发明的一些实施例,对于本领域普通技术人员来讲,在不付出创造性劳动的前提下,还可以根据这些附图获得其他的附图。图1是支撑件排列板料上的支撑件的立体图;图2是支撑件排列板料上的支撑件安装在支承底板上的第一个状态图;图3是支撑件排列板料上的支撑件安装在支承底板上的第二个状态图;图4是支撑件排列板料上的支撑件安装在支承底板上的第三个图;图5是支撑件排列板料上的支撑件安装在支承底板后第四个状态的立体图;图6是端部相互支撑的支撑件的主视图;图7是一个单元的支承底板的主视图;图8是端部相互支撑的支撑件安装在支承底板的立体图;图9是键盘的主视图;图10是支承底板的主视图;图11是图10的局部视图;图12是相对应排列的端部相互支撑的支撑件的支撑件排列板料的主视图;图13是图12的局部视图;图14是相对应排列的中部相互支撑的支撑件的支撑件排列板料的主视图;图15是交叉排列的中部相互支撑的支撑件的支撑件排列板料的主视图;图16是中部相互支撑的支撑件安装在支承底板后的立体图;图17是本发明的自动安装装置处于收集位置时的主视图;图18是图17的府视图;图19是本发明的自动安装装置处于安装位置时的主视图;图20是图19的府视图;图21是本发明的自动安装装置有多余支撑件收集安装装置的主视图;图22是图21的府视图;图23是本发明收拢的II通道安装工装700、I通道安装工装600的装配立体图;图24是本发明放开的II通道安装工装700、I通道安装工装600的装配立体图;图25是本发明放开的II通道安装工装700、I通道安装工装600的装配主视图;图26是图25的A-A剖视图;图27是图25的B-B剖视图;图28是图27旋转安装支撑件的示意图;图29本发明的安装交叉排列的支撑件的工装的俯视图;图30本发明的安装交叉排列的支撑件的示意图;图31是图29仰视图;图32是图29的C-C剖视图;图33是图29的D-D剖视图;图34是图29的E-E剖视图;图35本发明的分体式结构的I通道安装工装600的通道始入口601的剖示图;图36本发明的分体式结构的II通道安装工装700的通道终出口702的剖示图;图37I通道安装工装600与II通道安装工装700的相对位移安装示意图;图38本发明的单元通道安装工装的剖示图;图39端部支撑件被冲入通道始入口601的剖示图;图40端部支撑件在通道始入口601内旋转位移的剖示图;图41端部支撑件在连接通道向下位移的剖示图;图42端部支撑件在连接通道末端呈安装恣态的剖示图;图43端部支撑件通过通道终出口702进入支承底板连接部202的剖示图;图44施加于端部支撑件的气流改变方向的剖示图;图45端部支撑件在气流作用下绕支承底板连接部202旋转的剖示图;图46中部支撑件在连接通道末端呈安装恣态的剖示图;图47中部支撑件通过通道终出口702进入支承底板连接部202的剖示图;图48其中一个中部支撑件在气流作用下绕支承底板连接部202旋转的剖示图;图49另一个中部支撑件在气流作用下绕支承底板连接部202旋转的剖示图;图50本发明的自动安装装置的构成立体图;图51本发明的自动安装装置为通道的整体式结构的通道安装工装的立体图;图52是图51的局部视图;图53是图51的局部视图;图54本发明的自动安装装置为通道的整体式结构的通道安装工装的俯视图;图55是图54的F-F剖视图;图56是图54的G-G剖视图;图57本发明的多安装工位的自动安装装置的位于左工位的立体图;图58本发明的多安装工位的自动安装装置的位于右工位的立体图;图59本发明的两安装工位的自动安装装置的立体图;图60是图59的主视图;图60是图60的府视图;图62本发明的另一种两安装工位的自动安装装置的立体图;图63是一个键盘的键帽内凹底面向上与支承底板安装对应的示意图;图64是图63的立体图;图65本发明的吸附旋转安装工装的吸附头17011位于收集位置的示意图;图66本发明的吸附旋转安装工装位于收集位置落料的示意图;图67本发明的吸附旋转安装工装位于安装位置落料的示意图;图68本发明的吸附旋转安装工装的多个吸附头17011位于收集位置的立体图;图69本发明的吸附旋转安装工装的多个吸附头17011开始旋转的立体图;图70本发明的吸附旋转安装工装的多个吸附头17011位于安装位置的立体图;图71本发明的往复旋转安装工装的单元通道安装工装分别位于安装位置、收集位置的立体图;图72本发明的往复旋转安装工装的多个成组的单元通道安装工装分别位于安装位置、收集位置的立体图。具体实施方式下面将结合本发明实施例中的附图,对本发明实施例中的技术方案进行清楚、完整地描述,显然,所描述的实施例是本发明一部分实施例,而不是全部的实施例。基于本发明中的实施例,本领域普通技术人员在没有做出创造性劳动前提下所获得的所有其他实施例,都属于本发明保护的范围。实施例1:如图17、18、19、20和50所示,一种将支撑键帽的支撑件安装在支承底板的自动安装装置,包括连续输送支撑件排列板500至收集位置的支撑件板送料装置(图中未表示)、连续输送支承底板200至安装位置的支承底板送料装置(图中未表示)、冲裁支撑件排列板500上的工艺连接筋501的落料装置、将第一支撑件103或第二支撑件100从收集位置移动至安装位置的支撑件安装装置、于安装位置将第一支撑件103或第二支撑件100支撑件安装到支承底板连接部202形成联动支撑结构的支撑件安装装置。如图50所示,所述自动安装装置还包括支撑件步进模、支承底板步进模、薄膜电路安装装置以及键帽安装装置。其中,所述支撑件步进模在金属带状料上成型支撑件排列板后,所述支撑件排列板被直接送入支撑件安装装置;所述支承底板步进模在金属带状料上成型支承底板后,所述支承底板被直接送入支撑件安装装置;所述薄膜电路安装装置位于支承底板步进模与支撑件安装装置之间;所述键帽安装装置位于支撑件安装装置出口外侧。所述支撑件板送料装置可以是所述支撑件步模的送料装置,也可以是独立的通常的送料装置,所述支承底板送料装置可以是所述支撑件步模的送料装置,也可以是独立的通常的送料装置。所述支撑件板送料装置输送由第一支撑件组成的支撑件排列板,完成第一支撑件在支承底板上的安装或完成第一支撑件在键排列工装上的安装,另一个支撑件板送料装置输送由第二支撑件组成的支撑件排列板,所述支承底板送料装置或键排列送料装置输送已完成安装第一支撑件的支承底板或已完成安装第一支撑件的键排列工装。其中,所述支撑件排列板、落料装置位于支撑件安装装置一端,所述支承底板或键排列送料装置位于支撑件安装装置另一端,其中支撑件排列板位于落料装置与支撑件安装装置之间,所述支撑件安装装置有支撑件的收集位置及支撑件的安装位置,其中,所述收集位置为支撑件安装装置收集从支撑件排列板上冲裁下的支撑件的位置,所述安装位置为支撑件安装装置使支撑件连接部与支承底板连接部安装对准的位置,所述支撑件板送料装置输送支撑件排列板至收集位置,冲裁支撑件排列板上的工艺连接筋后,所述支撑件安装装置的从收集位置输送第一支撑件或第二支撑件位移至安装位置;所述支承底板送料装置输送支承底板或键排列送料装置输送键排列工装至安装位置,所述支撑件进入支承底板连接部或键帽连接部内,所述支撑件形成相互支撑结构。所述自动安装装置还有多余支撑件收集安装装置,所述多余支撑件收集安装装置用于收集支撑件排列板上每行多余的支撑件,所述多余支撑件收集安装装置由驱动支承底板的沿X方向移动及Y方向移动的通道移动工装、使第一支撑件或一个第二支撑件呈安装姿态的单元通道安装工装、落料装置构成,所述落料装置冲裁多余支撑件时,所述单元通道安装工装的通道始入口与支撑件排列板位置上每行多余支撑件位置对准,单元通道安装工装的数量与多余支撑件数量相等,所述多余支撑件收集安装装置位于支撑件步进模与支撑件安装装置之间。其中,所述支撑件排列板与支承底板相对于支撑件安装装置的相对运动速度为n*L6/Lc,其中L6为支撑件排列板上相邻的两组支撑件单元间的间距,Lc为支撑件安装装置从安装位置至收集位置的距离;所述支撑件板送料装置、支承底板送料装置分别传送的支撑件排列板、支承底板相对于支撑件安装装置的相对运动速度为n*L6/L1,其中L6为支撑件排列板上相邻的两组支撑件单元间的间距,L1为相邻的两个键开关单元所对应的支承底板连接部的配合部间的间距,所述支撑件板送料装置、支承底板送料装置分别传送的支撑件排列板与支承底板相对于支撑件安装装置相对运动,剪断所述工艺连接筋的剪断距离为n*L,L为成型支撑件的步进距离。如图50所示,支撑件单元105经过模具冲压成型,其中支撑件单元105通过工艺连接筋501在支撑件排列板500上;剪断所述工艺连接筋501,所述支撑件单元105进入支撑件安装装置,所述支撑件由水平位置旋转一定角度C,并通过支撑件安装装置移动至安装位置;所述位移至安装位置的支撑件单元105进入支承底板连接部202;支撑件单元105的第一支撑件103、第二支撑件100相对位移呈安装姿态;支撑件单元105位移至安装位置,所述支撑件呈一定角度C1进入支承底板连接部或键帽连接部内,所述支撑件形成相互支撑结构。其中,支撑件排列板500沿箭头所示方向移动,支撑件排列板500由成行排列或成行成列排列的支撑件单元105通过工艺连接筋501相互连接构成,支撑件单元105由一个第一支撑件103、一个第二支撑件100交错排列或对应排列或阵列排列形成,支撑件单元105与支撑件排列板500在同一平面或所述支撑件单元105在同一平面,也可支撑件单元105与支撑件排列板500的平面成夹角,一个支撑件单元105可对应安装一个单元的键开关装置。支撑件排列板500的支撑件板送料装置(图中未表示)可由通常结构的移动装置构成,也可由成形支撑件排列板500的冲床设备的移动装置构成(连续成形支撑件排列板500的冲床设备,支撑件排列板500从冲床设备连续送出。支承底板的自动安装装置可以内置冲床设备内,也可并列安装在冲床设备后,自动安装装置与连续送出的支撑件排列板500位置对准)。支承底板200沿箭头所示方向移,支承底板200的支承底板送料装置(图中未表示)可由通常结构的移动装置构成,也可由成型支承底板200的冲床设备的移动装置构成。落料装置(图中未表示)采用通常结构的冲裁落料装置。如图17和18所示,所述支撑件安装装置由分体式结构的通道旋转安装工装构成以及相对移动工装构成,所述分体式结构的通道旋转安装工装由I通道安装工装600、II通道安装工装700构成,其中I单元通道工装位于II单元通道工装之上。在本实施例中,所述支撑件安装装置为XY安装工装1000,XY安装工装1000位于支撑件排列板500之下,并位于支承底板200之上,XY安装工装1000由呈长条形的II通道安装工装700、I通道安装工装600、框形支架800、Y方向导轨900、通道移动工装等构成,其中呈框形的框形支架800左右两端附固定安装有两根Y方向导轨900,呈长条形的II通道安装工装700两端通过II通道滑套701与Y方向导轨900滑动连接,I通道安装工装600与II通道安装工装700上的II通道导轨705滑动连接,其中II通道安装工装700呈长条形状。当支撑件排列板500有n行连续的支撑件单元105时,XY安装工装1000由n个II通道安装工装700构成,n为自然数,I通道安装工装600的数量与需要安装的支承底板连接部202的配合部数量相同。所述相对移动工装由X驱动装置(图中未表示)、弹性元件或磁性元件(图中未表示)、Y驱动装置(图中未表示)等构成。如图17、18、23、24和25所示,分体式结构的通道工装的通道始入口601位于I单元通道工装600的上端,所述分体式结构的通道工装的通道终出口702位于II单元通道工装700的下端,所述通道始入口与通道终出口导通时,I通道与II通道连通形成连接通道,支撑件单元105经冲裁工艺连接筋501后,分别或同时进入I通道安装工装600的通道始入口601。其中,I通道安装工装600即I单元通道安装工装,II通道安装工装700由多个II单元通道安装工装沿X方向刚性连接形成。多个II通道安装工装700间沿Y方向有弹性元件(图中未表示)或磁性元件(图中未表示)将各II通道安装工装700推至最大间距,Y方向产生推力的Y驱动装置(图中未表示)可克服弹性元件或磁性元件的推力将各II通道安装工装700推至最小间距。同行的各相邻的I通道安装工装600通过悬臂挂钩604限位连接,于X方向推拉的X驱动装置(图中未表示)可推动各I通道安装工装600沿II通道导轨705移动至最小间距,X驱动装置(图中未表示)也可拉动各I通道安装工装600沿II通道导轨705移动至悬臂挂钩604限位时,各I通道安装工装600至最大间距。XY安装工装1000有安装位置及收集位置,安装位置是多个II通道安装工装700处于最大间距及多个I通道安装工装600处于最大间距时;收集位置是多个II通道安装工装700处于最小间距及多个I通道安装工装600处于最小间距时。XY安装工装1000位于收集位置时,I通道安装工装600的通道始入口601与支撑件排列板500上的支撑件单元105位置对准,XY安装工装1000位于安装位置时,II通道安装工装700的通道终出口702与支承底板200上的支承底板连接部202或键帽连接部位置安装对准。如图21、22和50所示,采用步进模连续在连续金属带状料上成型支撑件排列板500,支撑件排列板500每行的支撑件单元105数量相等,而现有的笔记本键盘每行的键帽数量不相等,为解决每行多余的支撑件单元105的自动安装,可在步进模x与支撑件安装装置(通道旋转安装工装构成)之间设置多余支撑件收集安装装置。也可沿支撑件排列板500移动方向并位于通道旋转安装工装构成(XY安装工装1000)前方或后方设置多余支撑件收集安装装置,多余支撑件收集安装装置由X驱动装置(图中未表示)及Y驱动装置(图中未表示)驱动承载支承底板200的通道移动工装(收集支板移动装置1200)、使第一支撑件103或一个第二支撑件100呈安装姿态的单元通道安装工装(通道收集安装装置1100)、落料装置等构成。将一个I单元通道安装工装、一个II单元通道安装工装固定连接形成一个单元通道安装工装(通道收集安装装置1100)。由一个或多个单元通道安装工装构成通道收集安装装置1100,支撑件排列板500相应的每行数量与安装一个键盘对应的每行需要的支撑件单元105数量不等,可将支撑件排列板500某行多余的支撑件单元105冲裁进入通道收集安装装置1100的通道始入口601,通道收集安装装置1100的通道始入口601的数量与多余的支撑件单元105的数量相同,收集支板移动装置1200移动支承底板200,使支承底板连接部202与通道收集安装装置1100的通道终出口702位置安装对齐,通道终出口702、通道始入口601通过支撑件连接通道连通。安装时,沿箭头方向移动的支撑件排列板500移动至多余支撑件收集安装装置时,多余支撑件收集安装装置的落料装置(图中未表示)从支撑件排列板500冲裁多余的支撑件单元105进入通道收集安装装置1100(单元通道安装工装)的通道始入口601,收集支板移动装置1200沿X方向Y方向移动,使支承底板连接部202与通道收集安装装置1100的通道终出口702位置对准,通过通道收集安装装置1100将多余的支撑件单元105对应安装在支承底板200的支承底板连接部202上。支撑件排列板500继续移动,移动至XY安装工装1000上方时,此时XY安装工装1000处于收集位置-----多个II通道安装工装700处于最小间距及多个I通道安装工装600处于最小间距,XY安装工装1000上的落料装置冲裁支撑件单元105进入通道始入口601,XY安装工装1000上的I通道安装工装600将支撑件单元105移动至安装位置(弹性元件或磁性元件将各I通道安装工装600、II通道安装工装700推至最大间距),I通道安装工装600、II通道安装工装700将第一支撑件103或第二支撑件100支撑件安装到支承底板连接部202形成联动支撑结构。XY安装工装1000完成一个支承底板200的安装,支撑件排列板500继续移动,多余支撑件收集安装装置又从支撑件排列板500冲裁多余的支撑件单元105进入通道始入口601,同时收集支板移动装置1200移动nL6的距离使支承底板200的支承底板连接部202与通道终出口702对应完成安装,支撑件排列板500继续移动,待XY安装工装1000安装完一个支承底板200。参见图23和24、I通道安装工装(I单元通道安装工装)600有一对挂钩臂603,在挂钩臂603的悬臂端部有悬臂挂钩604,在挂钩臂603的反方向有挂钩凹槽607,在挂钩凹槽607的左端有挂钩配合凸台602,在I通道安装工装600上端部有通道始入口601,在通道始入口601内有旋转位移斜面605,在I通道安装工装600下部有逐渐向内收拢斜面形成I配合凸台606。II通道安装工装700呈长条形,在沿II通道安装工装700长度方向有两个II通道导轨705,在II通道安装工装700的下端面有多个凹槽703。I通道安装工装600通过I配合凸台606与II通道安装工装700的II通道导轨705滑动连接,两个I通道安装工装600处于最小间距时的位置关系参见图23,两个I通道安装工装600处于最大间距时,其中一个I通道安装工装600的挂钩臂603的悬臂端部的悬臂挂钩604被另一个I通道安装工装600的挂钩配合凸台602限位。如图25、26、27和28所示,I通道安装工装600有分别连接通道始入口601、I通道出口609的I通道608,在I通道608的上部有旋转位移斜面605,通道始入口601向下逐渐收窄后形成旋转位移斜面605,通道始入口601向下逐渐收窄后与I通道608连接,通道始入口601可容纳水平状的第一支撑件103或第二支撑件100或支撑件单元105,I通道608可容纳竖立状或斜向状的第一支撑件103或第二支撑件100,I通道608的下端部为I通道出口609。II通道安装工装700有分别连接II通道入口704、通道终出口702的II通道706,在II通道安装工装700下端部有内凹空间703,内凹空间703的竖立壁面与II通道706的外臂面光滑连接,通道中隔板707在内凹空间703内向下延伸至II通道安装工装700下端部形成延伸中隔板708。应确保I通道安装工装600沿II通道安装工装700往复移动时,I通道608、II通道706处于对齐导通状态或关闭状态,即对齐导通状态时第一支撑件103或第二支撑件100可从I通道608可靠进入II通道706。应确保II通道安装工装700的通道终出口702与下方的支承底板连接部202的配合部位置对齐。I通道安装工装600可由一个I单元通道安装工装构成,也可由多个I单元通道安装工装连接构成,当由多个I单元通道安装工装连接后,其通道始入口601位于同一端。II通道安装工装700可由一个II单元通道安装工装构成,也可由多个II单元通道安装工装连接构成,当由多个II单元通道安装工装连接后,其通道终出口702位于同一端。I通道安装工装600位于II通道安装工装700之上。如图27、28和32所示,支撑件安装装置由通道旋转安装工装构成,支撑件安装装置是将从通道终出口702出来的第一支撑件103、第二支撑件100插入支承底板连接部202后,使第一支撑件103、第二支撑件100绕支承底板连接部202旋转形成相互支撑的支撑键帽400的通道旋转安装工装。第一支撑件103、第二支撑件100在重力或沿支撑件通道至上而下的气流产生的推力F1向下移动,第一支撑件103、第二支撑件100由通道终出口702进入内凹空间703后,由横向气流产生的力F2将分别将第一支撑件103、第二支撑件100的板面与II通道安装工装700的内凹空间703的竖立板面贴合,在确保F1大于F2的条件下,第一支撑件103、第二支撑件100的板面贴合内凹空间703的竖立板面向下移动,至第一支撑件103、第二支撑件100的支撑件下连接部101插入支承底板连接部202的配合部后,横向气流改变气流方向,F2推动第一支撑件103、第二支撑件100的板面使其绕支承底板连接部202旋转形成相互支撑结构。应确保第一支撑件103、第二支撑件100绕支承底板连接部202的配合部转动时不与II通道安装工装700的内凹空间703发生干涉。应确保第一支撑件103、第二支撑件100插入支承底板连接部202的配合部时,第一支撑件103、第二支撑件100的板面与II通道安装工装700的内凹空间703的竖立板面贴合。如图29-50所示,支撑件上触压部102、支撑件下触压部106位于支撑件单元105的中部的支撑件单元105,采用图示交叉排列时,I通道安装工装600的两个通道始入口601与交叉排列的第一支撑件103、第二支撑件100位置对准并交叉排列,I通道安装工装600的两个I通道出口609对齐排列,两个通道始入口601与两个I通道出口609过两个I通道608连接,两个I通道608一个呈竖直状一个呈斜向状。冲裁落料后第一支撑件103、第二支撑件100进入两个入口,并绕旋转位移斜面605的上端部旋转进入I通道608,从I通道安装工装600的两个I通道出口609出来时第一支撑件103、第二支撑件100对齐排列,从而可实现安装。通道装置由I通道安装工装600、II通道安装工装700构成,其中I通道安装工装600、II通道安装工装700可相对应动,I通道安装工装600、II通道安装工装700也可固定刚性连接为一体成为一个零件。支撑件安装装置也可以通道装置构成,由通道装置内的旋转位移斜面605构成;也可以由通道装置内的呈斜向状的I通道608构成。参见图35本发明的分体式结构的I通道安装工装600的通道始入口601能水平容纳一个支撑件或一个支撑件单元(本方案为能水平容纳一个支撑件单元),其中通道隔板6010将两个连接通道分隔开。所述通道始入口601向下逐渐收窄后向下贯通形成连接通道,其中通道始入口601向下逐渐收窄形成旋转位移斜面605,所述两个连接通道左右对称,I通道安装工装600有I通道608。参见图36本发明的分体式结构的II通道安装工装700的通道终出口702,连接通道的末端的通道延伸内侧壁709有旋转气流口7012与支撑件对准,形成支撑件气动旋转结构。所述支撑件从通道延伸内侧壁709向外旋转一定角度后,由旋转限位面7010限制支撑件在旋转过程中从支承底板的配合部内脱出。所述连接通道末端为竖立通道。所述通道延伸内侧壁709分别为连接通道的末端的延伸面,在通道延伸内侧壁709与旋转限位面7010之间有支撑件旋转空间7011。所述旋转限位面7010与支撑件绕支承底板连接部202转动的圆同心。所述连接通道有向下流动的支撑件推动气流,II通道安装工装700有II通道706。参见图37I通道安装工装600与II通道安装工装700的相对位移,第一支撑件100、第二支撑件103交叉错位排列时,最为省料,生产过程中采用步进模具连续冲压时,效率高,生产成本低,生产出的支撑件单元105在支撑排列板500呈线性阵列排布,其中II通道安装工装700的II通道706与I通道安装工装600的I通道608连通时,由I通道608、II通道706构成连接通道。支承底板200进入安装位置后与II通道安装工装700连接,并和II通道安装工装700一起以速度V2相对于I通道安装工装600运动,所述支撑件排列板以速度V1相对于支撑件安装装置运动,相邻支撑件之间沿运动方向的距离为L6;所述支承底板的打字键区并沿支承底板长度方向的相邻的支承底板连接部的间距L1,所述支承底板以速度V2相对支撑件安装装置运动;其中V1/V2=n*L6/L1,确保连续冲压的支撑件通过支撑件安装装置连续进入支承底板连接部内,此时效果最佳。参见图38本发明的单元通道安装工装可看作是I单元通道工装位于II单元通道工装之上并刚性连接,其中II通道安装工装700的II通道706与I通道安装工装600的I通道608连通构成连接通道单元通道安装工装的通道始入口601向下逐渐收窄后向下贯通形成连接通道,向下逐渐收窄后的连接通道由竖立通道构成或由斜向通道及竖立通道共同构成。参见图39端部相互支撑的支撑件单元105被落料冲头1700冲入通道始入口601。参见图40端部相互支撑的支撑件在通道始入口601内在重力及向下气流作用下旋转位移。参见图41端部相互支撑的支撑件在连接通道向下位移。参见图42端部相互支撑的支撑件在连接通道末端呈安装恣态即与竖立平面成0度夹角并与支承底板连接部202位置对准。参见图43端部相互支撑的支撑件通过通道终出口702进入支承底板连接部202。参见图44施加于端部相互支撑的支撑件的从旋转气流口7012吹出的气流改变方向。参见图45端部相互支撑的支撑件在从旋转气流口7012吹出的气流作用下绕支承底板连接部202旋转形成相互支撑结构。参见图46中部相互支撑的支撑件在连接通道末端呈安装恣态即与竖立平面成0度夹角并与支承底板连接部202位置对准。参见图47中部相互支撑的支撑件通过通道终出口702进入支承底板连接部202,参见图36本发明的分体式结构的II通道安装工装700的通道终出口702,连接通道的末端的通道延伸外侧壁7013有旋转气流口7012与支撑件对准,形成支撑件气动旋转结构。所述支撑件从通道延伸外侧壁7013向内旋转一定角度后,由旋转限位面7010限制支撑件在旋转过程中从支承底板的配合部内脱出。所述连接通道末端为竖立通道。所述通道延伸外侧壁7013分别为连接通道的末端的延伸面,在通道延伸外侧壁7013与旋转限位面7010之间有支撑件旋转空间7011。所述旋转限位面7010与支撑件绕支承底板连接部202转动的圆同心。所述连接通道有向下流动的支撑件推动气流。参见图48其中一个中部相互支撑的支撑件在气流作用下绕支承底板连接部202旋转。参见图49另一个中部相互支撑的支撑件在气流作用下绕支承底板连接部202旋转,两支撑件旋转相互穿越交叉后形成中部相互支撑的支撑件支撑结构。如图63和64所示,是一个键盘的键帽内凹底面向上排列在键排列工装1600内,排列在键排列工装1600的键帽400与支承底板安装对应,在自动安装装置中可用键排列工装1600替代支承底板200,即用支承底板送料装置连续输送键排列工装1600至安装位置。将支撑件单元105旋转安装至键帽连接部形成相互支撑的支撑结构后,再将支承底板200上的支承底板连接部202压入所有第一支撑件103、第二支撑件100的支撑件下配合部101。键排列送料装置采用通常的送料装置结构。应确保在安装位置键帽400的键帽连接部与通道终出口702一、一对应。实施例2:如图51-56所示,所述通道旋转安装工装由整体式结构的通道安装工装构成,所述整体通道安装工装有多个纵横排列的并位于收集位置的通道始入口,所述通道始入口分别与支撑件排列板上的一个支撑件或一个支撑件单元位置对准,有多个纵横排列的并位于安装位置的通道终出口,所述通道始入口、通道终出口分别位于整体通道安装工装的两端,所述通道始入口、通道终出口由连接通道连通。支撑件安装装置由通道装置构成,由实施例1的I通道安装工装600的I通道出口609与II通道安装工装700的II通道入口704对齐连通后形成连接通道1400,再将一个或多个I通道安装工装600与再II通道安装工装700刚性连接成为一体形成整体通道安装工装1300。整体通道安装工装1300的通道始入口601与支撑件排列板500上的支撑件单元105一一收集对应;整体通道安装工装1300的通道终出口702与支承底板200上的支承底板连接部202的配合部一、一安装对应,通道始入口601、通道终出口702通过连接通道1400连接,在通道终出口702有使第一支撑件103、第二支撑件100绕支承底板连接部202旋转形成相互支撑的支撑键帽400的旋转安装结构(气动旋转安装结构)。整体通道安装工装1300的支撑件单元105或一个支撑件的通道始入口601数量与一个键盘的支承底板200上的需要安装支撑件单元105的支承底板连接部202的配合部数量相等。整体通道安装工装1300位于支撑件排列板500之下,并位于支承底板200之上。支撑件排列板500、支承底板200沿图示箭头方向移动分别进入收集位置、安装位置。如图55何56所示,连接通道1400整呈正立的八型并可左右对称,向下逐渐收窄后的连接通道由竖立通道构成或由斜向通道及竖立通道共同构成,在连接通道末端为斜向通道,整体通道安装工装1300的通道终出口702、通道始入口601与实施例1相同。其余参见实施例1。实施例3:如图57所示,自动安装装置由两个XY安装工装1000构成,XY安装工装1000有两个支承底板200的安装工位,所述安装工位位于支撑件排列板500两侧。支撑件排列板500、支承底板200沿X方向相向移动,XY安装工装1000可沿YX方向在两个安装工位间往复移动,当其中一个XY安装工装1000位于收集位置,其它的XY安装工装1000至少一个位于安装工位。XY安装工装1000位于安装工位时亦即位于安装位置。XY安装工装1000也可有两个以上,XY安装工装1000的安装工位也可有两个以上。其余参见实施例1。实施例4:如图58和59所示,I通道安装工装600的I通道出口609与II通道安装工装700的II通道入口704对齐连通后形成连接通道1400(图中未表示),再将一个或多个I通道安装工装600与再II通道安装工装700刚性连接成为一体形成整体通道安装工装1300,整体通道装置位于固定连在机座(图中未表示)上并位于支承底板200之上,整体通道安装工装1300的通道终出口702与支承底板200上的支承底板连接部202的配合部一、一安装对应,通道始入口601与通道终出口702通过竖立的连接通道1400(图中未表示)连接,支撑件排列板500、支承底板200沿图示箭头方向相向连续送入。将实施例1中的I通道安装工装600的I通道608及II通道安装工装700的II通道706取消,同时将I通道安装工装600设置与负压连通的通风孔(图中未表示),I通道安装工装600即变为支撑件吸头600a,其它结构及配合方式不变,此时I通道安装工装600--支撑件吸头600a;II通道安装工装700--II吸头移动装置700a。其中支撑件吸头600a位于支撑件排列板500、整体通道安装工装1300之上,整体通道安装工装1300位于支承底板200之上。支承底板200的安装工位有两个并位于支撑件排列板500两侧。在收集位置时,支撑件吸头600a与支撑件排列板500上的支撑件单元105收集对应,冲裁工艺连接筋501后,支撑件吸头600a吸住相应的支撑件单元105,同时向安装工位移动,至安装工位,支撑件吸头600a吸住的相应的支撑件单元105与整体通道安装工装1300的通道始入口601安装对应时,支撑件吸头600a释放支撑件单元105,支撑件单元105进入相应的通道始入口601。其余参见实施例2。实施例5:如图60所示,将实施例1中的I通道安装工装600、II通道安装工装700通道连通后刚性连接形成图中的两个连接在一起的XY安装工装1000,此时I通道安装工装600、II通道安装工装700刚性连接形成III通道安装工装1500,自动安装装置有两个安装工位,并由两个连接在一起的XY安装工装1000构成,当支撑件排列板500有n行连续的支撑件单元105时,每个安装工位有n个整齐排列的支承底板200,XY安装工装1000位于收集位置III通道安装工装1500的通道始入口601分别与所述支撑件排列板500上的支撑件单元105位置对准;在安装支撑件时,XY安装工装1000分别移动至一个安装工位,同时n个III通道安装工装1500分散移动至n个支承底板200,一一对应,III通道安装工装1500的通道终出口702与位于一个安装工位的一个支承底板200上的相应支承底板连接部21位置对准。所述III通道安装工装1500间的间距最小时,III通道安装工装1500位于收集位置。两个安装工位上的支承底板200均沿X方向或Y方向同步联动,支撑件排列板500沿X方向移动,n个III通道安装工装1500均沿Y方向往复移动。其余参见实施例2。实施例6:如图61和62所示,所述自动安装装置由输送支撑件排列板500的支撑件板送料装置、输送支承底板200的支承底板送料装置或输送键排列工装1600的键排列送料装置、冲裁支撑件排列板500上的工艺连接筋501的落料装置、将第一支撑件103或第二支撑件100安装到支承底板连接部202或键排列工装1600上的键帽连接部形成联动支撑结构的支撑件安装装置构成。所述支撑件板送料装置输送支撑件排列板500至收集位置;所述支承底板送料装置或键排列送料装置输送支承底板200或键排列工装1600至安装位置,所述支撑件安装装置将第一支撑件103或第二支撑件100从收集位置移动至安装位置。所述一个支撑件板送料装置输送由第一支撑件103组成的支撑件排列板500。所述另一个支撑件板送料装置输送由第二支撑件100组成的支撑件排列板500,所述支承底板送料装置或键排列送料装置输送己安装第一支撑件103的支承底板200或己安装第一支撑件103的键排列工装1600。所述第一支撑件103呈平卧状压入支承底板200的支承底板连接部202的配合部后,所述第二支撑件100再呈平卧状压入支承底板200的支承底板连接部202的配合部,所述第一支撑件103、第二支撑件100分别安装完成后,所述第一支撑件103、第二支撑件100形成相互撑的联动支撑结构。所述第一支撑件103、第二支撑件100分别呈竖立状插入支承底板连接部202的配合部。其余参见实施例4。实施例7:如图65-70所示,所述支撑件安装装置由吸附旋转安装工装构成。所述吸附旋转安装工装由在收集位置与安装位置往复运动的一个吸附旋转吸头17011、能水平容纳一个支撑件的通道始入口601、能水平容纳一个支撑件的通道终出口702、落料冲头(图示未表示)、往复驱动装置构成,支承底板200的长度方向沿Y方向布置。在一个往复摆杆的一端固连接吸附旋转吸头,往复摆杆的另一端与机座转动连接,往复摆杆绕机座连接部往复转动,使吸附旋转吸头作往复圆周运动;在收集位置时,往复摆杆与支撑件排列板垂直,吸附旋转吸头的端部与连接通道的通道终出口位置对准;在安装位置时,往复摆杆与支撑件排列板平行,吸附旋转吸头端部上的支撑件连接部与支承底板连接部位置对准并进入。本技术方案采用:在一个往复摆杆17010的一端固连接吸附旋转吸头17011,往复摆杆17010的另一端与机座转动连接,往复摆杆17010绕机座连接部1709往复转动,使吸附旋转吸头17011作往复圆周运动。在收集位置时,往复摆杆17010呈竖直状,吸附旋转吸头17011的有气流通道口的端部与连接通道的通道终出口702位置对准。在安装位置时,往复摆杆17010呈水平状,吸附旋转吸头17011通过负压吸住的支撑件连接部与支承底板连接部202位置对准并进入。吸附旋转安装工装工作时,支撑件排列板500(第一支撑件103排列成一行)沿箭头方向移动,落料冲头(图示未表示)将第一支撑件103冲入通道始入口601,在气流或重力作用下,支撑件在通道终出口702被吸附旋转吸头17011的端部吸附并定位,在旋转驱动装置作用下,吸附旋转吸头17011将第一支撑件103安装在支承底板200的一个按键单元的一个支承底板连接部202内。支承底板200压,X驱动装置、Y驱动装置作用下使下一个按键单元的一个支承底板连接部202进入安装位置,并重复上述过程直至全部安装完程。第一支撑件103完成安装后可再采用相同的装置完成第二支撑件100的安装,也可将吸附旋转吸头17011、通道始入口601、能水平容纳一个支撑件的通道终出口702、落料冲头(图示未表示)、支撑件排列板500(第二支撑件100排列成一行)等以支承底板200对称排列,支撑件排列板500(第二支撑件100排列成一行)与支撑件排列板500(第一支撑件103排列成一行)相向移动,移动至分别位于支承底板200左侧、右侧的通道终出口702,由分别位于支承底板200左侧、右侧的吸附旋转吸头17011相向旋转同时完成第二支撑件100、第一支撑件103安装。如图65-70所示,本技术方案:一个支撑件纵横排列构成支撑件排列板500,所述吸附旋转安装工装有在收集位置与安装位置往复运动的多个吸附旋转吸头17011,所述吸附旋转吸头17011的数量=支撑件沿Y方向排列的数量,在收集位置时,所有往复摆杆17010呈竖直状,同时往复摆杆17010间距最小,在安装位置时,往复摆杆17010呈水平状,同时在驱动装置作用下往复摆杆17010间距最大。完成支承底板200一行支撑件安装后,支承底板200在X驱动装置驱动下使下一行支承底板连接部202进入安装位置,也可采用支承底板200不沿X方向移动,而使往复摆杆17010沿其长度方向伸缩移动,使吸附旋转吸头17011上的支撑件与下一行的支承底板连接部202对应。也可采用支承底板200的长度方向沿Y方向布置,在安装位置时,可伸缩的往复摆杆17010使吸附旋转吸头17011上的支撑件与支承底板连接部202对应,安装完一组支撑件后,由X驱动装置移动支承底板200使下一组支撑件与下一组支承底板连接部202对应,应确保需要安装的支承底板连接部202行的数量(一般为6行)与支撑件排列板500沿Y方向的数量相等,其余与图65-70的方案相同。其余参见实施例1。实施例8:如图71所示,一个或多个单元通道安装工装700c沿圆周排列,单元通道安装工装700c通过转动连接杆17015与转动轴17019连接,多个单元通道安装工装700c随转动轴17019转动作圆周往复移动。支承底板200在X驱动装置、Y驱动装置驱动下运动。由成行排列的支撑件单元105构成支撑件排列板500。在收集位置时,单元通道安装工装700c的通道始入口601与支撑件排列板500上的支撑件单元105位置对准,当其中一个单元通道安装工装700c位于收集位置时,另一个单元通道安装工装700c位于安装位置。支承底板200的宽度方向、长度方向分别沿Y方向、X方向布置,支撑件排列板500沿Y方向移动,。安装时,落料冲头(图示未表示)将支撑件单元105冲入通道始入口601,单元通道安装工装700c随转动轴17019转动作圆周移动,同时支撑件单元105旋转进入单元通道安装工装700c的连接通道,支撑件单元105在连接通道内,被连接通道侧臂气流孔的负压吸住,支撑件单元105停留在连接通道,当载有支撑件单元105的单元通道安装工装700c旋转移动至安装位置时,连接通道侧臂气流孔的负压解除(与此同时在收集位置支撑件单元105进入另一个单元通道安装工装700c),支撑件单元105从连接通道末端的通道终出口702进入支承底板连接部202完成安装,完成一个按键单元的支撑件安装后,支承底板200在驱动装置的作用下,下一个按键单元的支承底板连接部202进入安装位置,单元通道安装工装700c随转动轴17019转动作圆周移动。如此循环直至完成全部安装。如图72所示,所述支撑件安装装置由旋转单元安装工装构成。所述往复旋转安装工装由分别作圆周运动的至少一个单元通道安装工装、旋转驱动装置、落料冲头构成或由至少一组单元通道线性阵列组、旋转装置、落料冲头构成;当作圆周往复运动的单元通道安装工装为一个或单元通道线性阵列组为一组时,一个单元通道安装工装或一组单元通道线性阵列组在收集位置与安装位置作圆周往复运动,并在运动过程中与收集位置、安装位置分别对应;当作圆周运动的单元通道安装工装为至少两个或单元通道线性阵列组为至少两组时,其中一个单元通道安装工装或一组单元通道线性阵列组位于收集位置时,另一个单元通道安装工装或另一组单元通道线性阵列组位于安装位置。转动轴17019与方形模块17018刚性连接,单元通道安装工装700c与通道滑轴17017刚连接,通道滑轴17017再与方形模块17018滑动连接。单元多个通道安装工装700c与通道滑轴17017沿X方向排列形成单元通道线性阵列组,其排列的单元通道安装工装700c的数量与支承底板200的支承底板连接部202的行的数量相等。单元通道线性阵列组按通道滑轴17017圆周阵列,支承底板200的宽度方向、长度方向分别沿X方向、Y方向布置,支撑件排列板500沿X方向移动。当其中一组单元通道线性阵列组位于收集位置时,另一组单元通道线性阵列组位于安装位置。当单元通道线性阵列组位于安装位置附近时,构成单元通道线性阵列组的各单元通道安装工装700c沿通道滑轴17017的轴线方向移动使各单元通道安装工装700c进入安装位置。其余参见实施例1。以上所述仅为本发明的较佳实施例而已,并不用以限制本发明,凡在本发明的精神和原则之内所作的任何修改、等同替换和改进等,均应包含在发明的保护范围之内。