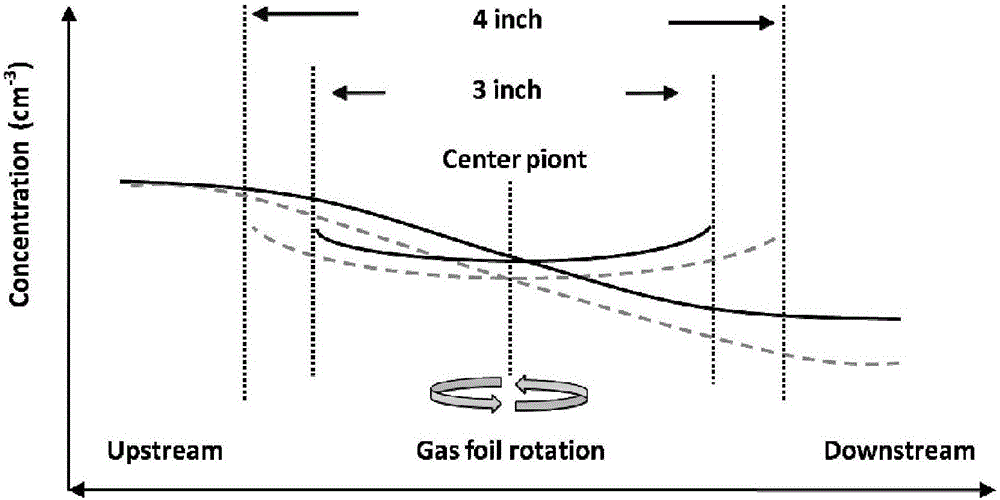
本发明涉及一种碳化硅外延片的生长方法,尤其涉及一种提高碳化硅外延兼容性的方法。
背景技术:
:SiC是继Si和GaAs等材料之后发展起来的第三代新型半导体材料,室温下SiC禁带宽度达3.0eV,击穿电场强度达3×106V/cm,热导率达4.9W/cm·℃,电子饱和漂移速度达2×107cm/s。优越的材料特性使得SiC成为高性能电子器件的理想材料。经过十几年的发展,SiC外延晶片尺寸、晶体质量、均匀性等指标有了大幅的提升,目前商业化的SiC衬底尺寸已经上升至6英寸,但是大部分的SiC器件研制流水线依旧为3英寸或4英寸,因此SiC外延材料要求覆盖3-6英寸。目前商用SiC外延炉大部分为水平式外延炉,源在进气方向的耗尽导致源在衬底上方分布不均匀,通常采用气浮旋转的方式来降低由于源耗尽引起的不均匀性。源在反应室基座和衬底上的耗尽速率不同,通常源在基座上的耗尽速率小于在衬底上的耗尽速率,因此衬底边缘存在源浓度变化不连续的点,形成边缘效应。对比不同外延尺寸的衬底,由于基座区域和衬底区域的比例不同,造成外延片中心点性能参数不同。如图1所示,长实线和长虚线分别对应3英寸和4英寸外延片的源耗尽曲线。由于3英寸基座区域的比例较大,3英寸衬底上方的源浓度要高于4英寸衬底上方相同位置的源浓度。因此即使采用相同的工艺条件,采用气浮旋转的3英寸衬底和4英寸衬底生长出来的外延片性能参数也是不同的,如图1中短实线和短虚线所示。同时由于源耗尽速率在基座和衬底边缘的不连续性,衬底边缘存在很强的边缘效应。技术实现要素:发明目的:针对以上问题,本发明提出一种提高碳化硅外延兼容性的方法。技术方案:为实现本发明的目的,本发明所采用的技术方案是:一种提高碳化硅外延兼容性的方法,包含以下步骤:(1)选用外延炉支持的最大尺寸的石墨基座;(2)基座中放入碳化硅衬底,根据衬底尺寸在石墨基座的衬底坑中放入合适尺寸的填充片,用于固定衬底;衬底尺寸与石墨基座尺寸相同时,不需要放入填充片;(3)将石墨基座放入反应室大盘内,将反应室中的空气置换为氩气,再将反应室抽至真空后通入氢气,保持氢气流量为60-120L/min;等系统升温至1300-1450℃时,将反应室的压力设置为100-200mbar,继续向反应室通入氯化氢气体,保持HCl/H2的流量比范围为0.01%-0.25%;(4)等系统继续升温至1500-1550℃时,关闭氯化氢气体,同时保持氢气流量和反应室压力不变;(5)系统继续升温,达到生长温度1570-1680℃后,维持生长温度2~10分钟;(6)向反应室通入硅源和碳源,控制硅源和氢气的流量比小于0.025%;调节碳源流量,控制进气端C/Si比小于等于1,通入氯化氢气体,控制Cl/Si比为2-6,通入氮气,生长n型缓冲层;(7)采用线性缓变的方式改变生长源和掺杂源的流量,至生长外延结构所需的设定值,生长外延结构;(8)完成外延结构的生长后,关闭生长源和掺杂源,在氢气氛围中将反应室温度降至室温,反应室温度达到室温后将反应室抽至真空,再向反应室中充入氩气,将反应室充至大气压,然后打开反应室,取出外延片。填充片是选用与放置在基座上的碳化硅衬底具有相同的掺杂类型、晶面晶向、表面形貌和厚度以及与基座具有相同尺寸的碳化硅衬底,在中心位置加工出与基座上的碳化硅衬底尺寸相同的圆形空位,圆形空位的直径为基座上的碳化硅衬底直径的1.05-1.1倍。填充片可以重复使用,重复使用过程中,当填充片的外延厚度达到200-500微米,进行机械抛光或化学机械抛光,去除填充片上的外延层。有益效果:本发明的方法通过引入和衬底具有相同掺杂类型、晶面晶向以及表面形貌的填充片的方式,使衬底区域得以延伸,从而使不同尺寸衬底对应的基座以及衬底区域比例接近,使源在实际衬底上的耗尽速率连续变化,避免边缘效应。同时通过填充片的引入,使得源在不同尺寸衬底上方相同位置的浓度相似,从而提高了不同尺寸基座的兼容性,减少不同尺寸外延炉间的浓度以及厚度标定频率;同时也可在多片式外延炉中实现不同尺寸衬底的同时生长,极大程度的减少了片间偏差。该发明简单可行,不需要对外延系统做改变,适用于现有单片以及多片式外延炉。附图说明图1是未加填充片的衬底上方的源耗尽曲线;图2是填充片的示意图;图3是增加填充片前后衬底上方的源耗尽曲线的对比图。具体实施方式下面结合附图和实施例对本发明的技术方案作进一步的说明。本发明所述的提高碳化硅外延兼容性的方法,是在使用时选择外延炉支持的最大尺寸的石墨基座。当放入小尺寸衬底时,放入合适尺寸的填充片,当衬底尺寸和基座尺寸相同时,则不需要加入填充片。如图2所示,选用系统配套的6英寸石墨基座,放入3英寸或者4英寸衬底时,需要加入相应尺寸的填充片。放入6英寸衬底时,则不需要加入填充片。加入填充片可以解决不同尺寸SiC衬底外延性质不同的问题,也可以降低外延过程中的边缘效应。填充片的加工方法是选用6英寸碳化硅衬底,利用激光切割或者金刚石划片的方法在6英寸碳化硅衬底的中心位置加工出小尺寸衬底的空位,该空位的圆心位置和6英寸碳化硅衬底的圆心位置重叠。加工填充片所选用的6英寸碳化硅衬底与放置在基座上的小尺寸衬底具有相同的掺杂类型、晶面晶向、表面形貌和厚度。通过引入和衬底具有相同掺杂类型、晶面晶向以及表面形貌的填充片,使衬底区域得以延伸,从而使不同尺寸衬底对应的基座以及衬底区域比例接近,使源在实际衬底上的耗尽速率连续变化,避免边缘效应。同时填充片的引入,使得源在不同尺寸衬底上方相同位置的浓度相似,可以很好的提高基座的兼容性。填充片中间的空位可以是正圆形也可以是带参考边的圆形,带参考边的空位直径为对应衬底直径的1.05-1.1倍,预留空隙,方便填充片的放置,避免因为热胀冷缩发生挤压。实际生长外延层时,使用单片式外延炉或者行星式多片式外延炉,选用外延炉支持的最大尺寸的石墨基座,将碳化硅衬底置于石墨基座内,在石墨基座内放入合适尺寸的填充片,利用填充片固定衬底,可以选取偏向<11-20>方向4°或者8°的碳化硅衬底。然后将石墨基座放入反应室大盘内,将反应室大盘内的空气置换为氩气,再将反应室抽至真空后向反应室内通入氢气,保持H2的流量为60~120L/min,等系统升温至1300-1450℃时,将反应室的压力设置为100-200mbar,继续向反应室通入少量氯化氢(HCl)气体,保持HCl/H2的流量比范围为0.01%-0.25%。等系统继续升温至1500-1550℃时,关闭氯化氢气体,同时保持氢气和反应室压力不变,让系统继续升温,当系统达到生长温度1570-1680℃后,维持生长温度2~10分钟。之后向反应室通入小流量硅源和碳源,可以是硅烷和乙烯,控制硅源和氢气的流量比小于0.025%,调节碳源流量,控制进气端C/Si比小于等于1,通入氯化氢(HCl)气体,控制Cl/Si比为2~6,通入高纯氮气(N2),生长出厚度为0.5-2μm,掺杂浓度为~1E18cm-3的n型缓冲层。采用线性缓变的方式改变生长源和掺杂源的流量,至生长外延结构所需的设定值,控制SiH4/H2流量比为0.2%,设定进气端C/Si比为1.05,并通入氯化氢(HCl)气体,设定进气端Cl/Si比为2.5,通入5sccm的氮气,外延时间设定为60分钟,生长外延结构。完成外延结构的生长后,关闭生长源和掺杂源,在氢气氛围中将反应室温度降至室温,反应室温度达到室温后将氢气排出反应室,将反应室抽至真空,维持3-10分钟,再向反应室中充入氩气,最终用氩气将反应室充至大气压,然后打开反应室,取出外延片。填充片可以重复使用,重复使用过程中,当填充片的外延厚度累计达到200-500微米,一般200微米左右就要进行处理,不能超过500微米,一般进行机械抛光或化学机械抛光,去除填充片上的外延层,达到和衬底相同的表面现象。如图3所示,其中点状虚线表示加入填充片后3英寸和4英寸衬底上方相同位置的源耗尽分布曲线;实线和线状虚线和图1中一样,长实线和长虚线分别对应3英寸和4英寸外延片的源耗尽曲线,短实线和短虚线表示采用气浮旋转的3英寸衬底和4英寸衬底上方相同位置的源耗尽分布曲线。对同一个外延炉生长3英寸、4英寸和6英寸外延片的中心点进行浓度和厚度测试,如表1所示。表1样品3英寸4英寸6英寸厚度(μm)29.3528.9628.06浓度(×1015cm-3)4.1E154.03E153.98E15结合图3和表1中的数据可以看出,采用本发明的方法,可以有效提高不同尺寸碳化硅外延的兼容性。当前第1页1 2 3