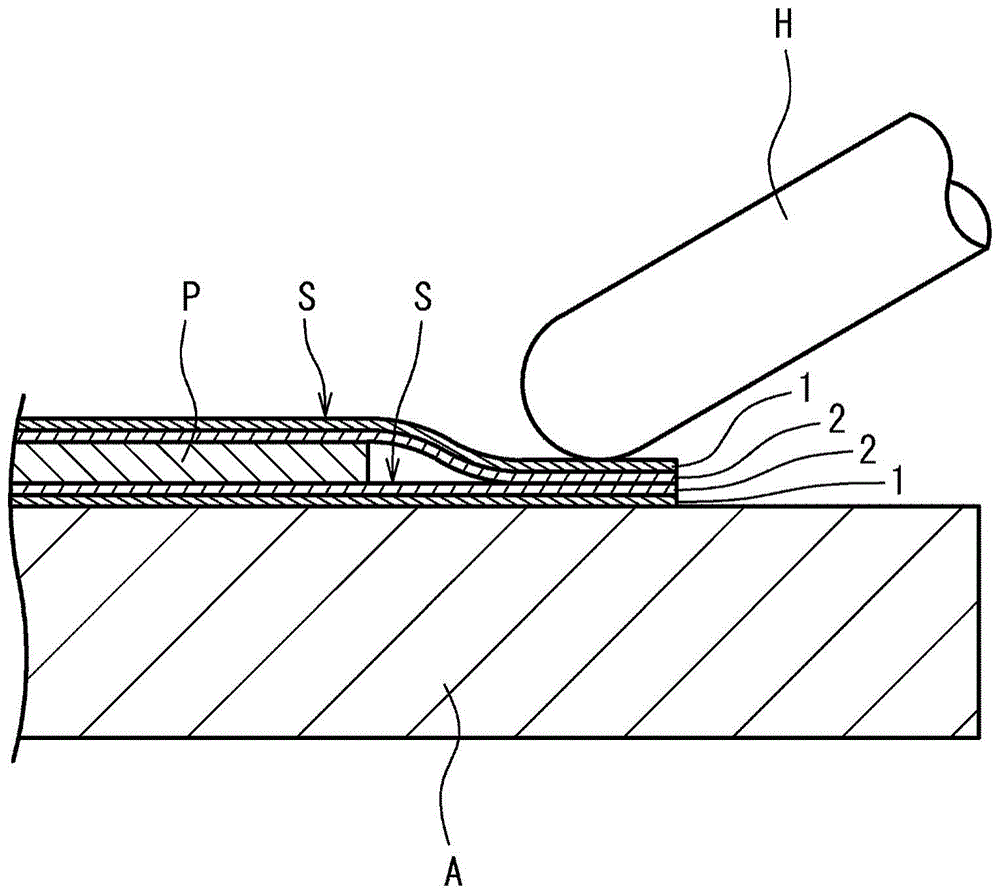
本发明涉及间隔件的超声波熔接方法。
背景技术:
:例如,在移动电话、电动汽车等各种设备中使用了能够充放电的二次电池。近年来,随着这些设备的高输出化、高性能化,寻求体积更小且电容量更大的二次电池。一般而言,二次电池通过将表面形成有正极活性物质层的正极板与表面形成有负极活性物质层的负极板隔着具有电绝缘性的间隔件交替层叠而形成。为了增大这种二次电池中的每单位体积的电容量,减薄间隔件是有效的。因此,利用树脂膜形成了间隔件的二次电池得以实用化。二次电池中,在负极处通过电析出而生成的金属析出物(例如锂枝晶)有可能贯穿间隔件而使正极板与负极板发生微短路。因此,有时采用如下构成:通过将夹着正极板或负极板的一对间隔件的外缘进行熔接而制成袋状,从而抑制产生可能生成析出物的金属离子的金属种混入至正极板附近的电解质中,抑制金属离子接触负极而发生电析出。由树脂膜形成的间隔件比较不耐热,因此,若增大二次电池的电容量,则间隔件因热而损伤,通过电析出而生成的析出物有可能贯穿间隔件而使正极板与负极板发生微短路。因此,提出了在间隔件的抵接于电极板的面形成耐热层(无机层)而使间隔件的耐热性得以提高的二次电池。然而,若使树脂膜的表面具有耐热层的间隔件中的耐热层彼此抵接并重合,则耐热层会阻碍树脂膜的熔接,因此无法容易地将间隔件进行熔接。日本特开2013-143337号公报提出了:在将隔着耐热层而层叠由树脂材料形成的间隔件层、进而自其两侧层叠有外包装材料的部分用加压施振部和夹具支承部夹住并加压同时施加振动的二次电池的制造方法中,通过在加压施振部和夹具支承部形成凸部而将耐热层破坏,在破坏部分将间隔件层树脂进行熔接。日本特开2015-185372号公报提出了:作为电气设备(装袋电极板)的间隔件接合方法,使用包含熔融材料(聚丙烯层)和耐热材料(陶瓷层)的间隔件(陶瓷间隔件),作为将夹着电极(正极或负极)并使陶瓷层彼此相对的陶瓷间隔件进行切割并接合的方法,将隔着电极相对的陶瓷间隔件的接合区域进行切割,使一个接合区域的聚丙烯层朝向其它接合区域的聚丙烯层移动,将接合区域的聚丙烯层彼此熔融并接合。现有技术文献专利文献专利文献1:日本特开2013-143337号公报专利文献2:日本特开2015-185372号公报技术实现要素:发明要解决的课题日本特开2013-143337号公报所记载的方法中,因在加压施振部和夹具支承部形成凸部而使熔接断续地进行,难以整体增大熔接面积,不易获得充分的接合强度。此外,日本特开2015-185372号公报所记载的方法中,虽然能够将聚丙烯层彼此连续熔接,但要使用比较锋利的切割刃,因此难以增大聚丙烯的熔接宽度,从而难以整体增大熔接面积,不易获得充分的接合强度。鉴于上述情况,本发明的课题在于,提供能够使具有耐热层的2片间隔件中的耐热层彼此相向并进行熔接、且接合强度较大的间隔件的超声波熔接方法。用于解决课题的方法本发明的一个方案所述的间隔件的超声波熔接方法具备以下工序:使具有树脂层和形成在上述树脂层上的耐热层的至少2片间隔件中的上述耐热层彼此相向,并利用支承部件进行支承;以及将点状抵接于上述间隔件且进行超声波振动的振动部件按压于上述至少2片间隔件,并且相对于间隔件进行相对移动。本发明的另一方案所述的间隔件的超声波熔接方法具备以下工序:使具有树脂层和形成在上述树脂层上的耐热层的至少2片间隔件中的上述耐热层彼此相向;在进行超声波振动的振动部件与点状支承上述间隔件的支承部件之间夹持上述至少2片间隔件;以及将上述至少2片间隔件相对于上述振动部件和支承部件进行相对移动。发明的效果上述间隔件的超声波熔接方法能够使具有耐热层的间隔件中的耐热层彼此相向并进行熔接,且接合强度较大。附图说明图1是表示本发明的一个实施方式的间隔件的超声波熔接方法的示意性截面图。图2是图1的间隔件的超声波熔接方法的示意性俯视图。图3是表示本发明的与图1不同的间隔件的超声波熔接方法的示意性截面图。图4是图3的间隔件的超声波熔接方法的示意性部分截面侧面图。具体实施方式本发明人等确认到:在使用线状延伸的超声波施加部件的现有超声波熔接方法中,难以在使2片间隔件的耐热层相向的状态下将这些间隔件充分接合,针对其理由,提出下述假设。(假设1)在线状延伸的超声波施加部件中,能量容易分散。(假设2)在使用线状延伸的超声波施加部件的情况下,为了使能量尽可能集中,需要使超声波施加部件的前端变细,因此,在间隔件上形成的熔接宽度变窄,难以获得充分的接合强度。(假设3)在使用线状延伸的超声波施加部件的情况下,被超声波施加部件破坏的耐热层的碎片在间隔件内仅向以超声波施加部件的延长线为边界的两侧挤出。因此,与为了使能量集中而缩小前端的必要性一并导致间隔件上形成的熔接宽度变窄,难以获得充分的接合强度。本发明人等基于上述假设而进行了下述实验:使用进行超声波振动的振动部件(例如前端为球形的振动部件)来代替线状延伸的部件,将2片附带耐热层的间隔件进行熔接。换言之,通过将进行超声波振动的振动部件按压于2片间隔件并且相对于间隔件进行相对移动而使熔接点发生移动,由此形成线状的熔接部。令人惊讶的是:通过该方法,即使不增大超声波输出,也能够在使2片间隔件的耐热层相向的状态下将这些间隔件充分地接合。本发明的一个方案是一种间隔件的超声波熔接方法,其具备以下工序:使具有树脂层和形成在上述树脂层上的耐热层的至少2片间隔件中的上述耐热层彼此相向并利用支承部件进行支承;以及,将点状抵接于上述间隔件并进行超声波振动的振动部件按压于上述至少2片间隔件,并且相对于间隔件进行相对移动。该间隔件的超声波熔接方法通过使具有树脂层和形成在上述树脂层上的耐热层的至少2片间隔件中的耐热层彼此相向并载置在支承部件上,将进行超声波振动的振动部件(ultrasonicvibratingindenter)按压于上述至少2片间隔件,从而利用振动部件和支承部件夹住至少2片间隔件并施加超声波振动,由此能够破坏耐热层而将树脂层彼此熔接。具体而言,可以认为:该间隔件的超声波熔接方法与以往的线状延伸的超声波施加部件不同,其使用点状抵接于间隔件的振动部件,因此,通过能量集中至一处而能够得到对于破坏较大的点状区域的耐热层并将耐热层的碎片向平面方向外侧挤出而将树脂层彼此熔接而言充分的能量。此外,该间隔件的超声波熔接方法通过将振动部件相对于间隔件进行相对移动而能够进行连续的熔接。因此,能够以较大的宽度形成连续的线状熔接部,从而能够相对增大间隔件的接合强度。可以通过上述振动部件的绝对位置的移动来进行上述振动部件的相对移动。像这样,通过利用上述振动部件的绝对位置的移动来进行上述振动部件的相对移动,能够较为简化装置的构成,并且能够提高生产率。此外,通过移动振动部件,能够较为自由地选择例如线状、虚线状等形成于2片间隔件的熔接部的形态。可以一边搬运上述间隔件一边进行上述振动部件的相对移动。像这样,通过一边搬运上述间隔件一边进行上述振动部件的相对移动,能够进一步提高生产率。上述振动部件的抵接于上述间隔件的部分的曲率半径可以为0.5mm以上。像这样,通过使上述振动部件的抵接于上述间隔件的部分的曲率半径为0.5mm以上,能够相对增大熔接部的宽度,能够更可靠地提高间隔件之间的接合强度。需要说明的是,“曲率半径”是指下述两种曲率半径的平均值:包含与间隔件抵接的点且在与间隔件垂直的振动部件的截面之中轮廓线的曲率半径达到最大的截面的曲率半径、以及与其正交的截面中的轮廓线的曲率半径。上述振动部件的相对移动可以包括将上述振动部件相对于上述间隔件沿着第一方向进行相对移动、以及将上述振动部件相对于上述间隔件沿着与上述第一方向交叉的第二方向进行相对移动。上述振动部件的相对移动通过包括第一方向的相对移动和第二方向的相对移动,与以往的线状延伸的部件相比,能够由2片间隔件形成复杂的平面形状的熔接部。例如,在2片间隔件之间配置电极板,并沿着该电极板的轮廓形成熔接部也较为容易。可以避开将上述振动部件相对于上述间隔件沿着上述第一方向进行相对移动时形成的间隔件熔接部,将上述振动部件相对于上述间隔件沿着上述第二方向进行相对移动。像这样,通过避开已经熔接一次的部位而进行后续的熔接,能够提高生产率,且能够维持良好的熔接状态。可以还具备向上述至少2片间隔件之间配置电极板,并利用上述振动部件的相对移动而沿着上述电极板的轮廓形成线状的熔接部。像这样,通过还具备向上述至少2片间隔件之间配置电极板,且利用上述振动部件的相对移动而沿着上述电极板的轮廓形成线状的熔接部,能够高效地制造将电极板用袋状间隔件覆盖的装袋电极。本发明的另一方案是一种间隔件的超声波熔接方法,其具备以下工序:使具有树脂层和形成在上述树脂层上的耐热层的至少2片间隔件中的上述耐热层彼此相向;在进行超声波振动的振动部件与点状支承上述间隔件的支承部件之间夹持上述至少2片间隔件;以及将上述至少2片间隔件相对于上述振动部件和支承部件进行相对移动。可以认为:该间隔件的超声波熔接方法使用点状抵接于间隔件的支承部件,因此,通过能量集中于一处而能够得到对于破坏较大的点状区域的耐热层并将耐热层的碎片向平面方向外侧挤出而将树脂层彼此熔接而言充分的能量。此外,该间隔件的超声波熔接方法通过将间隔件相对于上述振动部件和支承部件进行相对移动而能够进行连续的熔接。因此,能够以较大的宽度形成连续的线状熔接部,因此,能够相对增大间隔件的接合强度。可以通过将上述至少2片间隔件相对于上述振动部件进行相对移动来切割上述至少2片间隔件。像这样,通过将上述至少2片间隔件相对于上述振动部件进行相对移动来切割上述至少2片间隔件,能够同时进行熔接工序和切断工序,提高制造效率。上述振动部件的抵接面为平面状,在与上述间隔件的相对移动方向垂直的侧面视图中,上述支承部件的支承面为圆弧状为宜。像这样,通过使上述振动部件的抵接面为平面状,且在与上述间隔件的相对移动方向垂直的侧面视图中,使上述支承部件的支承面为圆弧状,能够使夹在上述振动部件与支承部件之间的间隔件比较顺利地移动。以下,适当参照附图,针对本发明的一个实施方式所述的间隔件的超声波熔接方法进行详述。[间隔件的超声波熔接方法]本发明的一个实施方式所述的间隔件的超声波熔接方法具备以下工序:如图1所示,使具有树脂层1和形成在该树脂层1上的耐热层2的至少2片间隔件s中的耐热层2彼此相向,并利用支承部件(平台)a进行支承;以及,如图2所示,将进行超声波振动的振动部件(变幅杆)h抵接于上述至少2片间隔件s,并且相对于间隔件s进行相对移动。该间隔件的超声波熔接方法典型而言可作为用于制造装袋电极板的一个工序而采用,所述装袋电极板是将蓄电元件用的电极板p用2片间隔件s夹住,且在电极板(正极板或负极板)p的外侧熔接2片间隔件s并接合成信封状而得到的。通过使用这种装袋电极板,能够抑制在蓄电元件的正极板处因异物等的混入而生成的金属离子向负极移动而发生电析出,能够防止由电析出导致的微小短路。<间隔件>间隔件s可以由卷绕有长条片材的卷轴进行供给,并在利用该超声波熔接方法进行熔接后加以切割。此外,通过将1片大张的片材对折,也可以构成2片间隔件s。通过从卷轴连续供给2片间隔件s,能够连续且高效地制造多个装袋电极板。需要说明的是,装袋电极板可通过将利用该超声波熔接方法形成了熔接部c的长条片材在2个熔接部c之间或者1个熔接部c的中央进行切割,切下间隔件s来获得。(树脂层)树脂层1由多孔树脂膜形成。作为该树脂层1的主要成分,可以采用例如聚乙烯(pe)、聚丙烯(pp)、乙烯-乙酸乙烯酯共聚物、乙烯-丙烯酸甲酯共聚物、乙烯-丙烯酸乙酯共聚物、氯化聚乙烯等聚烯烃衍生物;乙烯-丙烯共聚物等聚烯烃;聚对苯二甲酸乙二醇酯、共聚聚酯等聚酯等。其中,作为树脂层1的主要成分,可适合地使用耐电解液性、耐久性和熔接性优异的聚乙烯和聚丙烯。需要说明的是,“主成分”是指质量含有率最大的成分。作为树脂层1的平均厚度的下限,优选为5μm、更优选为10μm。另一方面,作为树脂层1的平均厚度的上限,优选为50μm、更优选为30μm。通过将树脂层1的平均厚度设为上述下限以上,能够将间隔件s熔接而不使树脂层1断裂。此外,通过将树脂层1的平均厚度设为上述上限以下,能够使蓄电元件的单位体积的容量实现充分的大小而不使间隔件s的厚度不必要地增大。(耐热层)耐热层2被制成包含多个无机粒子和将该无机粒子之间进行连接的粘结剂的构成。作为无机粒子的主成分,可列举出例如氧化铝、氧化硅、氧化锆、氧化钛、氧化镁、氧化铈、氧化钇、氧化锌、氧化铁等氧化物;氮化硅、氮化钛、氮化硼等氮化物;碳化硅、碳酸钙、硫酸铝、氢氧化铝、钛酸钾、滑石、高岭土粘土、高岭石、埃洛石(halloysite)、叶蜡石、蒙脱石、绢云母、云母、镁绿泥石(amesite)、膨润土、石棉、沸石、硅酸钙、硅酸镁等。其中,作为耐热层2的无机粒子的主成分,特别优选为氧化铝、氧化硅和氧化钛。作为耐热层2的无机粒子的平均粒径的下限,优选为1nm,更优选为7nm。另一方面,作为无机粒子的平均粒径的上限,优选为5μm,更优选为1μm。通过将无机粒子的平均粒径设为上述下限以上,能够获得具有充分耐热性的耐热层2而不使耐热层2中的粘结剂的比率变大。此外,通过将无机粒子的平均粒径设为上述上限以下,能够容易地形成均质的耐热层2。需要说明的是,“平均粒径”是指使用透射电子显微镜(tem)或扫描电子显微镜(sem)并按照jis-r1670测定的值。作为耐热层2的粘结剂的主成分,可列举出例如聚偏氟乙烯(pvdf)、聚四氟乙烯(ptfe)等氟树脂;偏二氟乙烯-六氟丙烯-四氟乙烯共聚物等氟橡胶;苯乙烯-丁二烯共聚物及其氢化物、丙烯腈-丁二烯共聚物及其氢化物、丙烯腈.丁二烯-苯乙烯共聚物及其氢化物、甲基丙烯酸酯-丙烯酸酯共聚物、苯乙烯-丙烯酸酯共聚物、丙烯腈-丙烯酸酯共聚物等合成橡胶;羧甲基纤维素(cmc)、羟乙基纤维素(hec)、羧甲基纤维素的铵盐等纤维素衍生物;聚醚酰亚胺、聚酰胺酰亚胺、聚酰胺及其前体(聚酰胺酸等)等聚酰亚胺树脂;乙烯-丙烯酸乙酯共聚物等乙烯-丙烯酸共聚物、聚乙烯醇(pva)、聚乙烯醇缩丁醛(pvb)、聚乙烯基吡咯烷酮(pvp)、聚乙酸乙烯酯、聚氨酯、聚苯醚、聚砜、聚醚砜、聚苯硫醚、聚酯等。作为耐热层2的平均厚度的下限,优选为0.5μm、更优选为1μm。另一方面,作为耐热层2的平均厚度的上限,优选为10μm、更优选为6μm。通过将耐热层2的平均厚度设为上述下限以上,能够充分提高间隔件s的耐热性。此外,通过将耐热层2的平均厚度设为上述上限以下,能够使蓄电元件的单位体积的容量实现充分的大小而不使间隔件s的厚度不必要地增大。(电极板)作为电极板p,使用在金属箔的表面层叠有活性物质层的电极板。作为电极板p的金属箔的材质,在正极的情况下可以使用例如铝等,在负极的情况下可以使用例如铜、铁、不锈钢等。作为电极板p的活性物质,在正极的情况下,可以使用例如以licoo2、linio2、limn2o4等氧化物材料作为主成分的材料,在负极的情况下,可以使用例如以石墨等作为主成分的材料。(支承部件)作为支承部件a,只要是载置间隔件s的顶面平坦、且具有充分的表面硬度、具有强度的支承件即可。在将2片间隔件s一边搬运一边熔接的情况下,可以使间隔件s在支承部件a上滑动,但通过使支承部件a与间隔件s一同进行间隔进给,能够防止对间隔件s的抵接振动部件h的区域作用有不必要的张力。因此,通过将支承部件a与间隔件s一同移动,能够将多对间隔件s连续且高效地进行熔接,并且能够防止间隔件s的接合强度降低。(振动部件)作为振动部件h,只要点状抵接于间隔件s即可,可以制成例如圆棒状且前端成形为半球状的振动部件。作为振动部件h的抵接于间隔件s的部分的曲率半径的下限,优选为0.5mm、更优选为1.0mm。另一方面,作为振动部件h的抵接于间隔件s的部分的曲率半径的上限,优选为8mm、更优选为15mm。通过将振动部件h的抵接于间隔件s的部分的曲率半径设为上述下限以上,能够获得充分的接合强度而不使2片间隔件s的熔接部c的宽度变小。此外,通过将振动部件h的抵接于间隔件s的部分的曲率半径设为上述上限以下,能够高效地破坏耐热层2而不使超声波振动分散至间隔件s的广阔范围。振动部件h的振动方向优选相对于间隔件s的表面发生倾斜。通过使振动部件的振动方向相对于间隔件s的表面发生了倾斜,在利用振动部件h的超声波振动将耐热层2破坏的同时,能够利用振动部件h的超声波振动拨开已破坏的耐热层2的碎片,将树脂层1彼此较为容易地熔接。此外,通过使振动部件h的振动方向相对于间隔件s的表面发生倾斜,即使将制造时的振动部件h与支承部件a的间隙(未发生超声波振动的状态下的间隔)调整至小于基于超声波振动的振动部件h的前端的移动宽度(振幅的2倍),振动部件h与支承部件a也不会彼此碰撞。因此可以认为:通过使振动部件h的振动方向相对于间隔件s的表面发生倾斜,能够高效地传导振动部件h的超声波振动的能量,因此,能够以更少的能量形成厚度较大、剥离强度较大的熔接部c。作为振动部件h的振动方向相对于间隔件s表面的倾斜角度的下限,优选为5°、更优选为10°。另一方面,作为振动部件h的振动方向相对于间隔件s表面的倾斜角度的上限,优选为70°、更优选为60°。通过使振动部件h的振动方向相对于间隔件s表面的倾斜角度在上述下限以上,能够对耐热层2高效地施加超声波振动,能够高效地破坏耐热层2,进而能够得到间隔件s的充分接合强度。此外,通过使振动部件h的振动方向相对于间隔件s表面的倾斜角度在上述上限以下,能够将已破坏的耐热层2的碎片拨开而将树脂层1彼此高效地熔接,能够提高效率。为了实现这种振动,如图1所示,可以使用在前端部抵接于间隔件s、且沿着轴向进行超声波振动的棒状的振动部件h,并将该棒状的振动部件h相对于间隔件s的表面倾斜配置。作为振动部件h的振幅的下限,优选为10μm、更优选为27μm。另一方面,作为振动部件h的振幅的上限,优选为80μm、更优选为68μm。通过使振动部件h的振幅在上述下限以上,能够容易地破坏耐热层2。此外,通过使振动部件h的振幅在上述上限以下,能够抑制树脂层1的损伤或者抑制能量效率不必要地降低。作为振动部件h的超声波振动的频率的下限,优选为10khz、更优选为20khz。另一方面,作为振动部件h的超声波振动的频率的上限,优选为80khz、更优选为40khz。通过使振动部件h的超声波振动的频率在上述下限以上,能够抑制对树脂层1造成的损伤,能够抑制间隔件s的熔接部c的强度降低或者抑制熔接时的间隔件s断裂。此外,通过使振动部件h的超声波振动的频率在上述上限以下,能够避免装置不必要地成为高价。作为振动部件h相对于间隔件s的压接力(不包括通过超声波振动而起作用的力在内)的下限,优选为5n、更优选为10n。另一方面,作为振动部件h相对于间隔件s的压接力的上限,优选为50n、更优选为30n。通过使振动部件h相对于间隔件s的压接力在上述下限以上,能够高效地破坏耐热层2。此外,通过使振动部件h相对于间隔件s的压接力在上述上限以下,能够抑制熔接部c的厚度减少、与此相伴的强度降低,此外,能够抑制熔接时的间隔件s的断裂。振动部件h的移动方向在俯视下相对于振动部件h的振动方向优选具有角度。换言之,振动部件h的振动优选具有所形成的熔接部c的宽度方向的分量。通过使俯视下的振动部件h的移动方向与振动方向不同,能够使通过振动部件h的超声波振动而形成压接点的往返移动的熔接部c的宽度增大,并且,将已破坏的耐热层2的碎片向左右拨开,将树脂层1彼此高效地熔接。作为俯视下的振动部件h的移动方向相对于振动部件h的振动方向的角度的下限,优选为30°、更优选为40°。通过使俯视下的振动部件h的移动方向相对于振动部件h的振动方向的角度在上述下限以上,能够将已破坏的耐热层2的碎片高效地向熔接部c的外侧拨开,能够高效地进行熔接或者得到间隔件s的充分接合强度。另一方面,作为俯视下的振动部件h的移动方向相对于振动部件h的振动方向的角度的上限,没有特别限定,若仅考虑到熔接性,则90°较为理想,如图2所示,在2片间隔件s形成彼此垂直的线状的熔接部c时,通过将俯视下的振动部件h的移动方向d1、d2相对于振动部件h的振动方向(振动部件h的长度方向)的角度设为45°,从而不需要更改振动部件h的朝向的机构。振动部件h通过以压接于在支承部件a上载置的2片间隔件s的上表面的状态进行超声波振动,同时移动其绝对位置,从而相对于间隔件s进行相对移动,对2片间隔件s形成线状的熔接部c。因此,振动部件h优选以例如能够利用由多关节机器人、正交坐标系机器人等形成的定位驱动机构任意地移动的方式进行保持。作为振动部件h相对于间隔件s的相对移动,例如图2所示,包括第一方向d1的移动和第二方向d2的移动。由此,能够使用与间隔件s点状抵接的振动部件h,并将2片间隔件s沿着电极板p的轮廓以线状进行熔接。此时,优选按照避开先形成的第一方向d1的熔接部c地形成第二方向d2的熔接部c的方式将振动部件h进行相对移动。换言之,通过使振动部件h不会对间隔件s的相同位置按压2次以上,能够防止先形成的熔接部c的间隔件s发生剥离或者间隔件s在熔接部c处发生断裂。[其它实施方式]上述实施方式不对本发明的构成做出限定。因此,上述实施方式可基于本说明书的记载和技术常识来进行上述实施方式的各部分构成要素的省略、置换或追加,应该解释为它们均属于本发明的范围。在该间隔件的超声波熔接方法中,可以将3片以上的间隔件进行熔接。例如,通过将多个正极板和多个负极板隔着间隔件交替层叠,并在正极板和负极板的外侧将全部间隔件一并熔接,从而也可以形成电极层叠体。在该超声波熔接方法中,在将振动部件压接于间隔件的状态下进行固定,并将堆叠有间隔件的支承部件进行移动,由此也可以使振动部件相对于间隔件发生相对移动。在该超声波熔接方法中,例如,也可以形成断续成虚线状的熔接部。可以通过振动部件的相对移动将至少2片间隔件一边熔接一边切断。此时,优选以能够在所形成的熔接部的宽度方向中央处切割间隔件的方式使振动部件的抵接面的形状沿着相对移动方向的左右大致对称。在上述实施方式中,在发生超声波振动的振动部件与支承部件之间夹着2片间隔件,但本发明不限定于该形态。本发明所述的间隔件的超声波熔接方法可以具备以下工序:使具有树脂层和形成在上述树脂层上的耐热层的至少2片间隔件中的上述耐热层彼此相向;在发生超声波振动的振动部件与点状支承上述间隔件的支承部件之间夹着上述至少2片间隔件;以及使上述至少2片间隔件相对于上述振动部件和支承部件发生相对移动。上述超声波熔接方法可以使用例如图3和图4所示的超声波熔接装置来实施。在该超声波熔接装置中,发生超声波振动的振动部件h1在与间隔件s的相对移动方向垂直的侧面视图中具有延伸成直线状的、优选平面状的抵接面。另一方面,支承部件a1通过在与间隔件s的相对移动方向垂直的侧面视图中延伸成圆弧状,且与间隔件s的相对移动方向垂直的方向的宽度充分小,从而相对于间隔件s以点状进行抵接。该超声波熔接装置可特别适合地用于一边将间隔件s熔接一边进行切割。在该超声波熔接方法中,通过在振动部件h1的抵接面与支承部件a1的支承面之间加入至少2片间隔件s,并使间隔件s相对于振动部件h1和支承部件a1发生相对移动,能够沿着相对移动的方向将2片间隔件s进行熔接。可以认为:在图3的超声波熔接装置中,抵接面与支承面隔着间隔件s以点状进行接触,因此,超声波振动的能量集中至一处,由此能够得到对于将较大的点状区域的耐热层破坏、挤出耐热层的碎片并将树脂层彼此熔接而言充分的能量。如图所示,支承部件a1可以制成如下构成,其具有:形成为朝着间隔件鼓出的凸状,确保强度的基部b;以及突出成从该基部b起进而沿间隔件s的相对移动方向延伸的线状、且形成抵接于间隔件s的支承面的凸部e。作为凸部e的平均宽度(相对于间隔件s的实质性的抵接宽度)的下限,优选为0.1mm、更优选为0.2mm。另一方面,作为凸部e的平均宽度的上限,优选为1mm、更优选为0.6mm。通过使凸部e的平均宽度为上述下限以上,能够充分确保所形成的熔接部的宽度。此外,通过使凸部e的平均宽度为上述上限以下,能够避免与间隔件s接触的接触面积变得过大,能够可靠地进行熔接。支承部件a1因凸部e的宽度特别小而实质上相对于间隔件s以点状进行抵接。凸部e相对于间隔件s的抵接点可以具有1mm左右的宽度,因此,作为凸部e的前端部的截面形状,没有特别限定,例如可以采用方形、梯形、半圆形等各种形状。作为特别优选的例子,凸部e的前端部截面形状可以制成半径为0.2mm左右的半圆形状。此外,作为从与间隔件s的相对移动方向垂直的方向观察时的凸部e的外形形状,可以制成圆弧状或椭圆弧状。作为从与间隔件s的相对移动方向垂直的方向观察时的凸部e与间隔件s接触的位置处的曲率半径的下限,优选为1cm,更优选为2cm。另一方面,作为上述凸部e的接触位置处的曲率半径的上限,优选为10cm,更优选为8cm。通过使上述凸部e的接触位置处的曲率半径在上述下限以上,能够容易进行间隔件s的相对移动。此外,通过使上述凸部e的接触位置处的曲率半径为上述上限以下,能够避免支承部件a1相对于间隔件s以线状抵接而导致压接力分散,能够可靠地进行间隔件s的熔接。振动部件h1的振动方向优选为与间隔件s的移动方向(表面方向)垂直的方向。由此,装置构成变得较为简单,且间隔件s的相对移动容易容易。此外,通过使振动部件h1的振动方向垂直于间隔件s的面方向,能够在所形成的熔接部的中央切割间隔件s。需要说明的是,振动部件h1与支承部件a1的位置关系可任意地变更,例如,可以使振动部件h1抵接于间隔件s的下表面,且支承部件a1抵接于间隔件s的上表面。实施例以下,基于实施例来详述本发明,但本发明不因该实施例的记载而受到限定性解释。(间隔件)作为要进行超声波熔接的间隔件,准备了将以聚丙烯作为主成分而形成的平均厚度为16μm的多孔膜制成树脂层,且在该树脂层的表面具有将氧化铝粉末以聚偏氟乙烯作为粘结剂进行涂布而形成的平均厚度为5μm的耐热层的间隔件。将2片间隔件按照以下说明的要领进行使耐热层彼此相向而发生超声波熔接的试验。此外,为了对比,准备未层叠耐热层而仅由上述树脂层构成的间隔件。(试验no.1)作为试验no.1,使用前端为半径3.25mm的球形的棒状振动部件,将该振动部件以轴向相对于间隔件的表面倾斜20°的方式进行支承并压接于间隔件。使该振动部件沿着轴向以39.5khz的频率进行振动,使其沿着俯视下与振动方向垂直的方向移动,由此将2片间隔件进行熔接。在该试验no.1中,将相对于间隔件的压接载重设定为16n,将振动部件的振幅设定为最大振幅(67.7μm)的80%,将振动部件的移动速度设为500mm/sec。利用显微镜对如此熔接的2片间隔件进行观察,并测定熔接部的平均厚度,结果为31.2μm。进而,作为2片间隔件的接合强度的指标,使用将所熔接的2片间隔件切割成宽3cm而得的试验片,进行基于jis-k6854-3(1999)的t型剥离试验。其结果,试验no.1中的剥离强度为1.3n。此外,确认剥离试验后的试验片的剥离面,其结果在熔接部发生了剥离。此外,针对2片间隔件的熔接部的密封性,使用浸透探伤剂进行了检查,密封性良好。(试验no.2)作为试验no.2,除了将振动部件的振幅设定为最大振幅的100%,除此之外,进行与试验no.1相同的试验。在该试验no.2中,被熔接的2片间隔件的熔接部的平均厚度为32.6μm、剥离强度为4.9n。此外,确认剥离试验后的试验片的剥离面,其结果在熔接部发生了剥离。此外,使用了浸透探伤剂的密封性的检查结果良好。(试验no.3)作为试验no.3,使用仅由树脂层构成的间隔件,除此之外,进行与试验no.2相同的试验。在该试验no.3中,被熔接的2片间隔件的熔接部的平均厚度为37.1μm、剥离强度为14.5n。此外,剥离试验后的试验片在熔接部发生了剥离。此外,使用了浸透探伤剂的密封性的检查结果良好。(试验no.4)作为试验no.4,将振动部件的移动速度设为250mm/sec,除此之外,进行与试验no.2相同的试验。在该试验no.4中,被熔接的2片间隔件的熔接部的平均厚度为17.1μm、剥离强度为10.5n。此外,剥离试验后的试验片在熔接部发生了剥离。此外,使用了浸透探伤剂的密封性的检查结果良好。(试验no.5)作为试验no.5,将振动部件的压接载重设为18n,除此之外,进行与试验no.2相同的试验。在该试验no.5中,被熔接的2片间隔件的熔接部的平均厚度为28.2μm、剥离强度为5.9n。此外,剥离试验后的试验片在熔接部发生了剥离。此外,使用了浸透探伤剂的密封性的检查结果良好。(试验no.6)作为试验no.6,将振动部件的压接载重设为24n,除此之外,进行与试验no.2相同的试验。在该试验no.6中,2片间隔件在发生熔接的同时在熔接部被切断。如此熔接的2片间隔件的熔接部的平均宽度(被切断的两侧的合计)为23.7μm、剥离强度(被切断后的仅一侧)为2.0n。此外,剥离试验后的试验片中的树脂层发生断裂。此外,使用了浸透探伤剂的密封性的检查结果良好。(试验no.7)作为试验no.7,将振动部件的移动速度设为250mm/sec,除此之外,进行与试验no.1相同的试验。在该试验no.7中,被熔接的2片间隔件的熔接部的平均宽度为23.7μm、剥离强度为5.6n。此外,剥离试验后的试验片中的树脂层发生断裂。此外,使用了浸透探伤剂的密封性的检查结果良好。(试验no.8)作为试验no.8,将振动部件的振幅设定为最大振幅的60%,将振动部件的移动速度设为250mm/sec,除此之外,进行与试验no.1相同的试验。在该试验no.8中,能够将2片间隔件进行熔接。如此熔接的2片间隔件的熔接部的平均厚度为20.0μm、剥离强度为5.7n。此外,剥离试验后的试验片中的树脂层发生断裂。此外,使用了浸透探伤剂的密封性的检查结果良好。(试验no.9)作为试验no.9,将振动部件的振幅设定为最大振幅的90%,将振动部件的移动速度设为250mm/sec,除此之外,进行与试验no.1相同的试验。在该试验no.9中,能够将2片间隔件进行熔接。如此熔接的2片间隔件的熔接部的平均厚度为25.2μmm、剥离强度为18.2n。(试验no.10)作为试验no.10,使用以线状抵接于间隔件的振动部件,将振动部件的压接载重设为200n,以30khz的频率、将振动部件的振幅设定为最大振幅(49μm)的90%,尝试了进行熔接。在该试验no.10中,勉强能够将2片间隔件进行熔接。然而,如此熔接的2片间隔件的剥离强度因测定时的操作而发生了剥离,因此无法测定。此外,剥离试验后的试验片中的树脂层发生了断裂。此外,使用了浸透探伤剂的密封性的检查结果是密封不良。针对上述试验no.1~10,将其条件和结果示于以下的表1和表2。需要说明的是,作为熔接状态的评价,“a”表示2片间隔件被熔接,“b”表示2片间隔件在熔接的同时在熔接部被切断,“c”表示2片间隔件未被熔接。[表1]试验no.12345载重(n)1616161618振幅(%)80100100100100移动速度(mm/sec)500500500250500有无耐热层有有无有有熔接状态aaaaa熔接厚度(μm)31.232.637.117.128.2剥离强度(n)1.34.914.510.55.9[表2]试验no.678910载重(n)24161616200振幅(%)10080609090移动速度(mm/sec)500250250250-有无耐热层有有有有有熔接状态baaac熔接厚度(μm)23.723.720.025.2-剥离强度(n)2.05.65.718.2-如上可确认:即使将具有耐热层的间隔件以使耐热层彼此相向的方式进行配置,通过将点状抵接于间隔件并发生超声波振动的振动部件一边按压于间隔件一边进行相对移动,能够将耐热层破坏并将树脂层彼此熔接。此外可确认:通过调整振动部件的压接载重、振幅和移动速度,能够进行接合强度较大的熔接,也能够将2片间隔件在熔接的同时进行切割。产业上的可利用性本发明所述的间隔件的熔接方法可适合用于制造装袋电极板。附图标记说明1树脂层2耐热层a、a1支承部件b基部c熔接部d1第一方向d2第二方向e凸部h,h1振动部件p电极板s间隔件当前第1页12