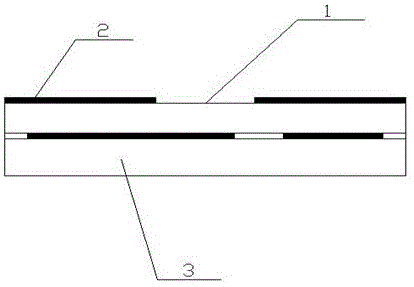
本发明属于金属化薄膜
技术领域:
,具体涉及一种高压互感器用电容器金属化薄膜材料。
背景技术:
:金属化薄膜电容器可用于直流(dc)用以及交流(ac)用均可,现有的交流(ac)用薄膜电容器的金属蒸着电极是用锌作为表面蒸镀的,直流(dc)用金属化薄膜电容器的金属蒸着电极是用纯铝作为表面蒸镀的,因交流电压印施加时沿面放电易于引发膜表面氧化,通过释放的电子使金属蒸着电极被腐蚀这种现象频繁发生,另外,对直流电压用途的高电压施加领域的电容器类型、被要求需要自我保护性好的不易被氧化的材料。然而近年来、即使应用到交流(ac)用途的电容器也提高了使用电压区域,也要求高耐压化,因此,现在所要解决的问题是如何避免现有的在ac用途的金属化薄膜电容器中、锌合金的材料制作的电容器易于在沿面放电时素子内易引起膜表面氧化、蒸镀金属减少,金属蒸镀有效面积减少、导致电容器静电电容量衰减的问题。技术实现要素:本发明的目的是针对现有的问题,提供了一种高压互感器用电容器金属化薄膜材料。本发明是通过以下技术方案实现的:一种高压互感器用电容器金属化薄膜材料,所述高压互感器用电容器金属化薄膜材料构造包括:留边、蒸镀金属、塑料薄膜;在诱电体塑料薄膜上使用蒸镀金属蒸镀电极,形成金属化薄膜材料;在在诱电体塑料薄膜上使用蒸镀金属蒸镀电极时设置有一段未进行金属化蒸镀的空白区域,所述空白区域即为留边。进一步的,所述蒸镀金属按重量份计由以下成分制成:铝55-85份、硅7-13份、铜3-5份。进一步的,所述铜的重量份小于硅的一半重量份。进一步的,所述塑料薄膜为聚丙烯薄膜、多聚苯硫醚薄膜、聚酯乙烯薄膜、聚苯乙烯薄膜中的任一种。进一步的,所述在诱电体塑料薄膜上使用蒸镀金属蒸镀电极为采用高真空薄膜蒸镀机进行蒸镀处理。进一步的,所述高压互感器用电容器金属化薄膜材料制成的金属化薄膜电容器在交流ac使用的场合中应用,静電容量変化得了有效的抑制。进一步的,高压互感器用电容器金属化薄膜材料制成的金属化薄膜电容器在直流dc使用的场合中应用。进一步的,所述高压互感器用电容器金属化薄膜材料好包括以下两种膜结构:压互感器用电容器金属化薄膜a与压互感器用电容器金属化薄膜b;所述压互感器用电容器金属化薄膜a由四组塑料薄膜构成,四组塑料薄膜按从上到下依次排列,最上方的塑料薄膜与最下方的塑料薄膜上分别采用蒸镀金属进行蒸镀电极,并分别设置有留边,中间两组塑料薄膜不处理;压互感器用电容器金属化薄膜b由两组塑料薄膜构成,从上到下依次排列,上方的塑料薄膜与下方的塑料薄膜上分别采用蒸镀金属进行蒸镀电极,并分别设置有留边。使用本发明中的蒸镀金属能够防止因交流电压印施加时沿面放电易引起膜表面氧化、通过释放的电子使金属蒸着电极被腐蚀这种现象发生。对直流电压用途的高电压施加领域的电容器使用本发明高压互感器用电容器金属化薄膜材料、被要求需要自我保护性好的不易被氧化的材料。铝比锌电阻低、为了使膜厚变薄、充放电时自我恢复良好,因此在直流dc用途上本发明中的蒸镀金属材料性能更好。本发明制备的高压互感器用电容器金属化薄膜材料制成的金属化薄膜电容器应用范围包括了:各种电子机器、电子电力设备、工业机器、新能源汽车、太阳能发电等。然而近年来,即使是应用到交流(ac)用途的电容器也提高了使用电压区域、也要求高耐压化,采用本发明薄膜材料制成的电容器具有更高的耐压性能。特别是在交流(ac)用途的金属薄膜电容器中,以铝(al)为主要材料,协同硅铜辅助蒸镀金属的自我恢复性良好,可实现良好的金属蒸着形成金属膜的电极、使薄膜电容器的静电容量衰减得到有效的抑制。也就是说,在ac用途的金属化薄膜电容器中,锌合金的材料制作的电容器易在沿面放电时易引起膜表面氧化,蒸镀金属减少。金属蒸镀有效面积的减少,导致电容器静电容量衰减,而使用本发明蒸镀金属材料能够有效的避免这些问题,以以铝(al)为主要材料,协同硅铜辅助蒸镀金属的作为电极使用在交流ac电容器用途的情况下,电容器的静电容量变化可以得到有效的抑制为目的,为一种高压互感器用电容器提供了优良的薄膜材料。本发明相比现有技术具有以下优点:本发明通过在金属蒸着电极上以铝为主要基础材料,同时含有一定配比量的硅(si)及铜(cu)金属,从而使得以此材料制造的电容器不容易引起沿面放电。由于硅(si)比铝(al)的工作函数更大,所以此材料制造成的薄膜电容器是更不易被氧化。另外,通过调节硅(si)的含量作为铝-硅(al-si)合金的同晶点附近的浓度配比,使熔点下降,即使金属蒸镀的电极变薄,对诱电体薄膜的热损伤也会降低,在低温条件下,也可以加强喷金金属同蒸镀电极的粘结强度。因此,能够更进一步地改善充放电时良好的自我恢复能力。还有,通过含有一定量的铜(cu),可以抑制铝-硅(al-si)合金的易受侵蚀氧化的空隙、可以抑制沿面放电的发生。也就是说,因为对硅(si)而言,铝的溶解度小,所以析出硅(si),虽然担心在粒界发生空孔,但通过含有铜(cu)在铝(al)的粒界形成铜(cu)浓度高的金属层,能抑制空孔的形成。因此,可以降低金属蒸着电极的缺陷,也可以抑制在缺陷附近发生的沿面放电。本发明,在交流(ac)用途上使用以铝为基础的金属蒸着电极的材料的情况下,电容器的静电容量变化得到抑制。另外,此材料结构可以提高喷镀的金属与膜的电极的结合强度。根据本发明的材料形成的金属化薄膜电容器,主要作为高压互感器用电容器可以很好地采用的材料。附图说明图1为一种高压互感器用电容器金属化薄膜材料结构图。图2为压互感器用电容器金属化薄膜a结构图。图3为压互感器用电容器金属化薄膜b结构图。具体实施方式下面结合附图图1对作详细说明:实施例1一种高压互感器用电容器金属化薄膜材料,所述高压互感器用电容器金属化薄膜材料构造包括:留边1、蒸镀金属2、塑料薄膜3;在诱电体塑料薄膜3上使用蒸镀金属2蒸镀电极,形成金属化薄膜材料;在在诱电体塑料薄膜3上使用蒸镀金属2蒸镀电极时设置有一段未进行金属化蒸镀的空白区域,所述空白区域即为留边1。进一步的,所述蒸镀金属按重量份计由以下成分制成:铝55份、硅7份、铜3份。进一步的,所述铜的重量份小于硅的一半重量份。进一步的,所述塑料薄膜为聚丙烯薄膜、多聚苯硫醚薄膜、聚酯乙烯薄膜、聚苯乙烯薄膜中的任一种。进一步的,所述在诱电体塑料薄膜上使用蒸镀金属蒸镀电极为采用高真空薄膜蒸镀机进行蒸镀处理。进一步的,所述高压互感器用电容器金属化薄膜材料制成的金属化薄膜电容器在交流ac使用的场合中应用,静電容量変化得了有效的抑制。进一步的,高压互感器用电容器金属化薄膜材料制成的金属化薄膜电容器在直流dc使用的场合中应用。使用本发明中的蒸镀金属能够防止因交流电压印施加时沿面放电易引起膜表面氧化、通过释放的电子使金属蒸着电极被腐蚀这种现象发生。对直流电压用途的高电压施加领域的电容器使用本发明高压互感器用电容器金属化薄膜材料、被要求需要自我保护性好的不易被氧化的材料。铝比锌电阻低、为了使膜厚变薄、充放电时自我恢复良好,因此在直流dc用途上本发明中的蒸镀金属材料性能更好。本发明制备的高压互感器用电容器金属化薄膜材料制成的金属化薄膜电容器应用范围包括了:各种电子机器、电子电力设备、工业机器、新能源汽车、太阳能发电等。进一步的,所述高压互感器用电容器金属化薄膜材料好包括以下两种膜结构:压互感器用电容器金属化薄膜a与压互感器用电容器金属化薄膜b;所述压互感器用电容器金属化薄膜a由四组塑料薄膜构成,四组塑料薄膜按从上到下依次排列,最上方的塑料薄膜与最下方的塑料薄膜上分别采用蒸镀金属进行蒸镀电极,并分别设置有留边,中间两组塑料薄膜不处理;压互感器用电容器金属化薄膜b由两组塑料薄膜构成,从上到下依次排列,上方的塑料薄膜与下方的塑料薄膜上分别采用蒸镀金属进行蒸镀电极,并分别设置有留边。实施例2一种高压互感器用电容器金属化薄膜材料,所述高压互感器用电容器金属化薄膜材料构造包括:留边1、蒸镀金属2、塑料薄膜3;在诱电体塑料薄膜3上使用蒸镀金属2蒸镀电极,形成金属化薄膜材料;在在诱电体塑料薄膜3上使用蒸镀金属2蒸镀电极时设置有一段未进行金属化蒸镀的空白区域,所述空白区域即为留边1。进一步的,所述蒸镀金属按重量份计由以下成分制成:铝85份、硅13份、铜5份。进一步的,所述铜的重量份小于硅的一半重量份。进一步的,所述塑料薄膜为聚丙烯薄膜、多聚苯硫醚薄膜、聚酯乙烯薄膜、聚苯乙烯薄膜中的任一种。进一步的,所述在诱电体塑料薄膜上使用蒸镀金属蒸镀电极为采用高真空薄膜蒸镀机进行蒸镀处理。进一步的,所述高压互感器用电容器金属化薄膜材料制成的金属化薄膜电容器在交流ac使用的场合中应用,静電容量変化得了有效的抑制。进一步的,高压互感器用电容器金属化薄膜材料制成的金属化薄膜电容器在直流dc使用的场合中应用。使用本发明中的蒸镀金属能够防止因交流电压印施加时沿面放电易引起膜表面氧化、通过释放的电子使金属蒸着电极被腐蚀这种现象发生。对直流电压用途的高电压施加领域的电容器使用本发明高压互感器用电容器金属化薄膜材料、被要求需要自我保护性好的不易被氧化的材料。铝比锌电阻低、为了使膜厚变薄、充放电时自我恢复良好,因此在直流dc用途上本发明中的蒸镀金属材料性能更好。本发明制备的高压互感器用电容器金属化薄膜材料制成的金属化薄膜电容器应用范围包括了:各种电子机器、电子电力设备、工业机器、新能源汽车、太阳能发电等。进一步的,所述高压互感器用电容器金属化薄膜材料好包括以下两种膜结构:压互感器用电容器金属化薄膜a与压互感器用电容器金属化薄膜b;所述压互感器用电容器金属化薄膜a由四组塑料薄膜构成,四组塑料薄膜按从上到下依次排列,最上方的塑料薄膜与最下方的塑料薄膜上分别采用蒸镀金属进行蒸镀电极,并分别设置有留边,中间两组塑料薄膜不处理;压互感器用电容器金属化薄膜b由两组塑料薄膜构成,从上到下依次排列,上方的塑料薄膜与下方的塑料薄膜上分别采用蒸镀金属进行蒸镀电极,并分别设置有留边。实施例3一种高压互感器用电容器金属化薄膜材料,所述高压互感器用电容器金属化薄膜材料构造包括:留边1、蒸镀金属2、塑料薄膜3;在诱电体塑料薄膜3上使用蒸镀金属2蒸镀电极,形成金属化薄膜材料;在在诱电体塑料薄膜3上使用蒸镀金属2蒸镀电极时设置有一段未进行金属化蒸镀的空白区域,所述空白区域即为留边1。进一步的,所述蒸镀金属按重量份计由以下成分制成:铝86份、硅9.5份、铜4份。进一步的,所述铜的重量份小于硅的一半重量份。进一步的,所述塑料薄膜为聚丙烯薄膜、多聚苯硫醚薄膜、聚酯乙烯薄膜、聚苯乙烯薄膜中的任一种。进一步的,所述在诱电体塑料薄膜上使用蒸镀金属蒸镀电极为采用高真空薄膜蒸镀机进行蒸镀处理。进一步的,所述高压互感器用电容器金属化薄膜材料制成的金属化薄膜电容器在交流ac使用的场合中应用,静電容量変化得了有效的抑制。进一步的,高压互感器用电容器金属化薄膜材料制成的金属化薄膜电容器在直流dc使用的场合中应用。进一步的,所述高压互感器用电容器金属化薄膜材料好包括以下两种膜结构:压互感器用电容器金属化薄膜a与压互感器用电容器金属化薄膜b;所述压互感器用电容器金属化薄膜a由四组塑料薄膜构成,四组塑料薄膜按从上到下依次排列,最上方的塑料薄膜与最下方的塑料薄膜上分别采用蒸镀金属进行蒸镀电极,并分别设置有留边,中间两组塑料薄膜不处理;压互感器用电容器金属化薄膜b由两组塑料薄膜构成,从上到下依次排列,上方的塑料薄膜与下方的塑料薄膜上分别采用蒸镀金属进行蒸镀电极,并分别设置有留边。使用本发明中的蒸镀金属能够防止因交流电压印施加时沿面放电易引起膜表面氧化、通过释放的电子使金属蒸着电极被腐蚀这种现象发生。对直流电压用途的高电压施加领域的电容器使用本发明高压互感器用电容器金属化薄膜材料、被要求需要自我保护性好的不易被氧化的材料。铝比锌电阻低、为了使膜厚变薄、充放电时自我恢复良好,因此在直流dc用途上本发明中的蒸镀金属材料性能更好。本发明制备的高压互感器用电容器金属化薄膜材料制成的金属化薄膜电容器应用范围包括了:各种电子机器、电子电力设备、工业机器、新能源汽车、太阳能发电等。在实施例中,作为诱电体使用了聚丙烯薄膜,除此之外,也可以使用多聚苯硫醚、聚酯乙烯、聚苯乙烯等。si的工作函数是4.9ev,比al的工作函数(4.15ev)大,因此,对si氧化所需要的能量更大,硅(si)是很难氧化的,al-si合金比al单体的金属蒸着电极更不易腐蚀。关于al和si的含有率,例如,通过对al表面形成一定比重的si,可以抑制部分放电时的腐蚀,在al单体的情况下,可以降低静电容量的变化。以下(表1),本发明材料的金属蒸着电极的组成比表示电容器的容量变化大小,关于电容器的容量变化,金属化薄膜电容器(容量1μf)在室温(23℃)环境中,施加380vac负荷试验,测量电容器的容量减少5%的时间。容量变化-5%的时间为500小时以上的话,判断容量变化比较小,如果时间不到500个小时的话,判断为容量变化大:表1蒸镀金属的组成(重量份)时间容量变化al(86份)-si(9.5份)-cu(4份)500小时以上小al(90份)-si(10份)500小时以上小al(100份)500小时以下大由此可见,以al(86份)-si(9.5份)-cu(4份)的组成相较于硅铝组合或纯铝来说,具有更好的容量。另外,在本发明中,将al:si:cu的比由(95:5:0)变更为(86:9.5:4)的范围,al-si合金是共晶点或在共晶点附近,可以降低熔点20℃-85℃左右。另外,在本实施例中,通过将cu原子能在si的原子浓度比率的一半以下时,使金属层中含有cu原子,抑制al-si合金中的si原子的析出,并难以产生由si原子的析出的金属蒸到电极中的侵蚀和空隙(腐蚀),以此来降低金属蒸着电极的缺陷,可以抑制以缺陷为起点的沿面放电的发生。下面说明理由,因为si对al的溶解度小,al-si合金中的si容易析出,是金属蒸着电极的侵蚀、空隙的主要原因。但是,在al-si合金中含有cu原子的话,cu为了迅速地向al的粒界析出,可以填补si析出的空隙,然后,可以抑制金属蒸着电极的缺陷。另外,在半导体领域的al-si-cu合金布线中,通过将cu包含si的原子浓度的一半左右,能够抑制断线,本实施例的金属蒸着电极也同样的理由推测出了更能抑制的缺陷。另外,cu的工作函数是4.6ev,比al的工作函数(4.15ev)高,但比si的工作函数(4.9ev)还小。因此,如果cu的含量多的话,会影响si的工作函数的降低效果,因此在本实施例中,将cu作为si的原子浓度的一半以下。当前第1页12