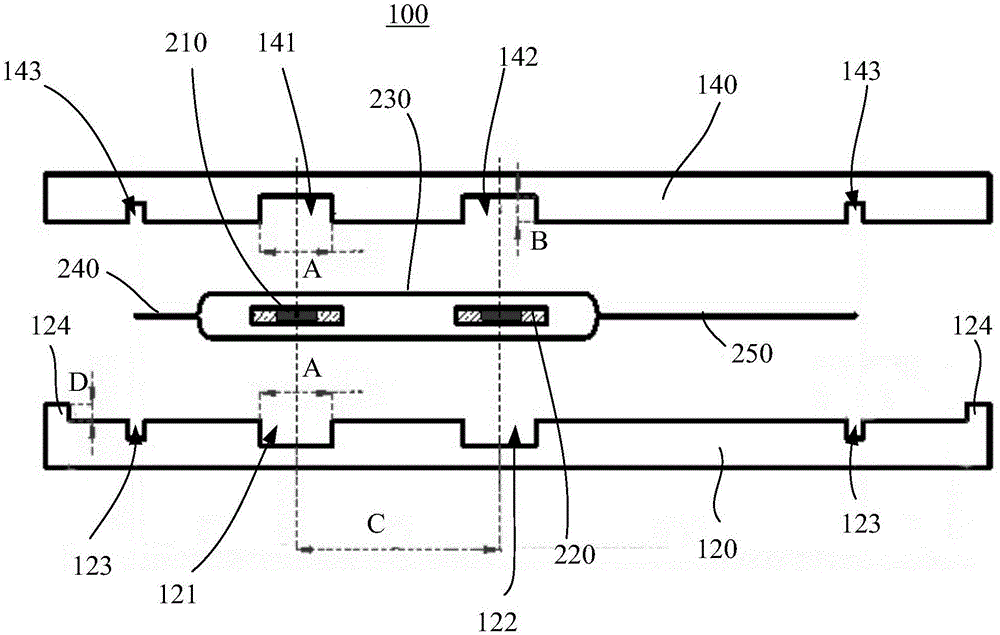
本发明涉及电池封装
技术领域:
,特别是涉及一种提高软包电池铝塑膜封装可靠性的方法。
背景技术:
:在聚合物锂离子电池的生产过程中,通常采用钢壳、铝壳或者铝塑膜对裸电芯进行封装。相比于钢壳和铝壳等刚性外壳材料,铝塑膜具有一定延展性,可在电池经历过充、短路等非正常情况而胀气时,起到一定缓冲作用,所以用铝塑膜封装的软包电池安全性能更好。目前,随着软包电池大量应用于需要大功率和大容量的场所,如汽车动力系统和其他电动工具等,安全性能开始成为软包电池性能的重点。通过技术革新,使铝塑膜获得更高的封装强度、更好的耐电解液性能、更高的水蒸气隔层性能和更丰富的尺寸形状多样性是电池软包装技术的关键。软包电池铝塑膜是由外保护层(如尼龙层或者聚对苯二甲酸乙二酯层等)、中间铝箔层、内层热封层(如聚丙烯层)所构成的复合膜,各复合层之间使用胶黏剂进行粘结。软包锂离子电池铝塑膜的封装主要是在铝塑膜包裹裸电芯后,通过封头的高温高压使封装区域热封层发生熔合,从而形成密闭空间。用铝塑膜对裸电芯进行封装时,根据位置的不同可分为顶封、侧封和底封三个区域,相较于侧封和底封,顶封区域由于有电芯的正负极耳存在,其顶封极耳区和非极耳区的封装可靠性较差,主要体现在封装厚度一致性差和封装强度低等方面。顶封区域密封可靠性差,易造成铝塑膜开裂和漏液等安全问题的出现。为了减小铝塑膜封装问题对软包电池产品的安全性能的影响,目前的解决方式主要有两种:一种是通过提高对封装不良品的筛选能力,防止不良品流入后工序的方法来达到降低出货产品的封装不良率的目的,但是没从根本上解决该问题;另一种思路是通过设计特殊的封装设备配合特定的封装工艺参数来实现封装可靠性的提高,这类方法可以一定程度上提高铝塑膜的封装强度,但是对封装设备精度要求极高,且不同型号和结构的电芯之间封装设备不能通用,因此不适合多样化产品的生产。技术实现要素:基于此,有必要提供一种适用范围广的提高软包电池铝塑膜封装可靠性的方法,以提高电芯的安全性能。一种提高软包电池铝塑膜封装可靠性的方法,包括以下步骤:在含有聚丙烯热封层的铝塑膜熔融粘结之后,对所述铝塑膜进行热压退火处理,所述热压退火处理的温度低于所述铝塑膜中聚丙烯热封层的熔点。在其中一个实施例中,所述热压退火处理的温度为90℃~150℃。在其中一个实施例中,所述热压退火处理的温度为110℃~120℃。在其中一个实施例中,所述热压退火处理的热压压力为0.1mpa~1mpa,保压时间为2.5s~10s。在其中一个实施例中,所述热压退火处理的热压压力为0.3mpa~0.5mpa。在其中一个实施例中,所述热压退火处理采用热压模头对电芯的顶封区域和侧封区域的铝塑膜进行热压。在其中一个实施例中,所述热压模头包括第一热压头和第二热压头,所述第一热压头上设有第一正极耳让位槽和第一负极耳让位槽,所述第二热压头上设有第二正极耳让位槽和第二负极耳让位槽,所述第一正极耳让位槽与所述第二正极耳让位槽相对设置,所述第一负极耳让位槽与所述第二负极耳让位槽相对设置。在其中一个实施例中,所述第一热压头用于与所述第二热压头压合的一侧设有限位凸起。在其中一个实施例中,所述限位凸起有两个,两个所述限位凸起分别设置在所述第一热压头的相对的两端。在其中一个实施例中,所述第一热压头上设有第一溢胶槽,所述第二热压头上设有第二溢胶槽,所述第一溢胶槽与所述第二溢胶槽相对设置。与现有方案相比,本发明具有以下有益效果:本发明在铝塑膜经过高温高压的封装工序之后,对铝塑膜进行热压退火处理,能够提高铝塑膜的封装可靠性,进而提高电芯的安全性能,具体体现包括:1、热压退火处理可以消除铝塑膜在热封工序中产生的各复合层(包括熔合的pp热封层)之间的残余内应力,提高铝塑膜层间结合强度;2、热压时在一定程度上软化pp(聚丙烯)热封层,热封层pp链段的可移动性得到提高,有助于消除角位等应力集中处的pp热封层在封装过程中因过度受挤压变形而形成的褶皱,提高电芯表观质量;在一定压力下有利于各封印区pp热封层厚度的重新调整,从而提高铝塑膜各封装区域封装厚度、强度一致性;3、热压退火处理有利于提高pp热封层的结晶度,从而提升热封层的力学性能。此外,本发明的方法简单易行,对设备要求较低,适用范围广,便于批量生产,且能大大提高电芯品质,产生良好的经济效益。附图说明图1为一实施例的提高软包电池铝塑膜封装可靠性的方法中采用的热压模头的结构示意图;图2为实施例4、实施例8以及对比例1中pp封装层的xrd测试图;图3为实施例4、实施例8以及对比例1中pp封装层的dsc测试图。具体实施方式为了便于理解本发明,下面将参照相关附图对本发明进行更全面的描述。附图中给出了本发明的较佳实施例。但是,本发明可以以许多不同的形式来实现,并不限于本文所描述的实施例。相反地,提供这些实施例的目的是使对本发明的公开内容的理解更加透彻全面。需要说明的是,当元件被称为“固定于”另一个元件,它可以直接在另一个元件上或者也可以存在居中的元件。当一个元件被认为是“连接”另一个元件,它可以是直接连接到另一个元件或者可能同时存在居中元件。除非另有定义,本文所使用的所有的技术和科学术语与属于本发明的
技术领域:
的技术人员通常理解的含义相同。本文中在本发明的说明书中所使用的术语只是为了描述具体的实施例的目的,不是旨在于限制本发明。本文所使用的术语“和/或”包括一个或多个相关的所列项目的任意的和所有的组合。本发明一实施例的提高软包电池铝塑膜封装可靠性的方法,包括以下步骤:在含有聚丙烯热封层的铝塑膜熔融粘结之后,对铝塑膜进行热压退火处理,热压退火处理的温度低于铝塑膜中pp(聚丙烯)热封层的熔点。在铝塑膜封装工序中,其条件为高温高压,温度在pp的熔点以上使得pp能够熔融粘结,如175~195℃,施压压力一般为0.2~0.9mpa。本实施例中,在铝塑膜封装工序之后,又对铝塑膜进行热压退火处理。热压退火处理的温度低于所述铝塑膜中pp的熔点,防止工艺过程中pp热封层再次熔融而达不到提高封装可靠性的效果。在其中一个示例中,热压退火处理的温度为90℃~150℃。进一步地,在其中一个示例中,热压退火处理的温度为110℃~120℃,在该处理温度下,铝塑膜封装可靠性综合评价较好。在其中一个示例中,热压退火处理的热压压力为0.1mpa~1mpa,保压时间为2.5s~10s。进一步地,在其中一个示例中,热压退火处理的热压退火处理的热压压力为0.3mpa~0.5mpa,在该热压压力下,铝塑膜封装可靠性综合评价较好。如图1所示,本实施例中,对所述铝塑膜进行热压退火处理,是采用热压模头100对电芯顶封区230和侧封区230的铝塑膜进行热压。本实施例中采用的热压模头100包括第一热压头120和第二热压头140。第一热压头120上设有第一正极耳让位槽121和第一负极耳让位槽122,第二热压头140上设有第二正极耳让位槽141和第二负极耳让位槽142,第一正极耳让位槽121与第二正极耳让位槽141相对设置,第一负极耳让位槽122与第二负极耳让位槽142相对设置。第一正极耳让位槽121和第二正极耳让位槽141的宽度a大于电芯正极耳210宽度3~5mm,深度b小于电芯正极耳210厚度0.01~0.04mm。正极耳让位槽与负极耳让位槽之间的间距c为电芯正极耳210与电芯负极耳220中心距±0.5mm。使电芯正极耳210与第一正极耳让位槽121以及第二正极耳让位槽141位置对应,电芯负极耳220与第一负极耳让位槽122以及第二负极耳让位槽142位置对应。从而热压时,电芯正极耳210位于第一正极耳让位槽121以及第二正极耳让位槽141之间的空间中,电芯负极耳220位于第一负极耳让位槽122以及第二负极耳让位槽142之间的空间中。如图1所示,在其中一个示例中,第一热压头120用于与第二热压头140压合的一侧设有限位凸起124,用来控制第一热压头120与第二热压头140压合的距离。进一步地,限位凸起124有两个,分别设置在第一热压头120的相对的两端。限位凸起124高度根据电芯设计的顶侧封厚度确定,在其中一个示例中,限位凸起124的高度d为顶封厚度±0.05mm。如图1所示,在其中一个示例中,第一热压头120上设有第一溢胶槽123,第二热压头140上设有第二溢胶槽143,第一溢胶槽123与第二溢胶槽143相对设置。第一溢胶槽123和第二溢胶槽143均有两个,设置在极耳让位槽的外围,其中一个用来收集退火过程中从侧封区230的边缘溢出的胶液,另一个用来收集退火过程中从气袋250的边缘溢出的胶液。使用上述热压模头100对铝塑膜进行热压之前,先对热压模头100进行预热和参数设置。在铝塑膜各封装区域熔融粘结之后,用机械手将电芯移入退火工艺实施工位,使电芯正极耳210与第一正极耳让位槽121以及第二正极耳让位槽141位置对应,电芯负极耳220与第一负极耳让位槽122以及第二负极耳让位槽142位置对应。再启动热压模头100,第一热压头120与第二热压头140互相靠近,对铝塑膜封装区域进行加压加热。本发明在铝塑膜经过高温高压的封装工序之后,对铝塑膜进行热压退火处理,能够提高铝塑膜的封装可靠性,具体体现包括:1、热压退火处理可以消除铝塑膜在热封工序中产生的各复合层(包括熔合的pp热封层)之间的残余内应力,提高铝塑膜层间结合强度;2、热压时在一定程度上软化热封pp热封层,热封层pp链段的可移动性得到提高,有助于消除角位等应力集中处的pp热封层在封装过程中因过度受挤压变形而形成的褶皱,提高电芯表观质量;在一定压力下有利于各封印区pp热封层厚度的重新调整,从而提高铝塑膜各封装区域封装厚度、强度一致性;3、热压退火处理有利于提高pp热封层的结晶度,从而提升热封层的力学性能。此外,本发明的方法简单易行,对设备要求较低,适用范围广,便于批量生产,且能大大提高电芯品质,产生良好的经济效益。以下结合具体实施例和性能测试试验对本发明的提高软包电池铝塑膜封装可靠性的方法作进一步说明。实施例1在铝塑膜经过热封工序熔融粘结之后,采用热压模头对电池顶封和侧封区域的铝塑膜(原铝塑膜厚度为113μm,其中pp层厚度为40μm)的进行热压。热压模头温度为120℃,热压模头压力为1mpa,保压2.5s后,移开热压模头,自然冷却,热压退火工序结束后,按照后续流程制成成品电芯。实施例2在铝塑膜经过热封工序熔融粘结之后,采用热压模头对电池顶封和侧封区域的铝塑膜(原铝塑膜厚度为113μm,其中pp层厚度为40μm)的进行热压。热压模头温度为120℃,热压模头压力为0.3mpa,保压6s后,移开热压模头,自然冷却。热压退火工序结束后,按照后续流程制成成品电芯。实施例3在铝塑膜经过热封工序熔融粘结之后,采用热压模头对电池顶封和侧封区域的铝塑膜(原铝塑膜厚度为113μm,其中pp层厚度为40μm)的进行热压。热压模头温度为120℃,热压模头压力为0.1mpa,保压8s,移开热压模头,自然冷却。热压退火工序结束后,按照后续流程制成成品电芯。实施例4在铝塑膜经过热封工序熔融粘结之后,采用热压模头对电池顶封和侧封区域的铝塑膜(原铝塑膜厚度为113μm,其中pp层厚度为40μm)的进行热压。热压模头温度为120℃,热压模头压力为0.5mpa,保压10s后,移开热压模头,自然冷却。热压退火工序结束后,按照后续流程制成成品电芯。实施例5本实施例与实施例4区别之处在于所用热压模头温度为90℃。实施例6本实施例与实施例4区别之处在于所用热压模头温度为100℃。实施例7本实施例与实施例4区别之处在于所用热压模头温度为110℃。实施例8本实施例与实施例4区别之处在于所用热压模头温度为150℃。对比例1在铝塑膜经过热封工序熔融粘结之后,没有采用热压退火工艺对封装区域进行处理。封印厚度值标准偏差实验将上述实施例1~8制成的电芯和对比例1制成的电芯各50ea,分别测试各组电芯的顶封和侧封的封印厚度值的标准偏差,统计各区域封印厚度值标准偏差,记录于表1。表1由表1可知,实施例1~8中顶、侧封区域的封装厚度标准偏差均小于对比例1。说明采用本发明的热压退火工艺可以大大提高封装区域的厚度均匀性,消除应力集中点和封装薄弱点,提高封装可靠性。从实施例4~8可知,随热压温度的上升,封印厚度值标准偏差呈降低趋势。封装拉力大小实验将上述实施例1~8制成的电芯和对比例1制成的电芯各50ea,分别测试各组电芯的顶封和侧封的封装拉力大小,统计各区域封装拉力大小平均值,记录于表2。表2由表2可知,相比于对比例1,采用本发明中热压退火工艺的实施例1~8中顶侧封区域的封装拉力值均得到提高,这说明采用本发明中的方法可以有效提高顶侧封的封装强度,达到提升电芯安全性能的目的。从实施例4~8可知,随着热压温度的上升,封装拉力呈先上升后降低趋势。pp热封层结晶度对比实验对实施例4、实施例8以及对比例1的pp封装层进行xrd和dsc测试。从图2中的衍射峰位置和图3的放热峰温度可以看出,本发明中实施例和对比例所使用的铝塑膜内封pp层为常见的α单斜晶系。由图2可知,采用热压退火工艺后,铝塑膜内层pp热封层的xrd主峰强度由大到小依次为实施例8>实施例4>对比例1,主峰强度越高反映出聚合物结晶度更高,说明采用本发明的热压退火工艺后可以提高铝塑膜热封层pp的结晶度,从而提高铝塑膜热封层的封装可靠性。由图3测试结果获得表3中热分析特征数据。从图3和表3可以利用dsc法算出铝塑膜热封层pp的结晶度,计算方法是通过测量样品熔融热焓与100%结晶时pp的熔融焓(209j/g)之比得出。由表3可知,三种样品的结晶度由小到大依次为:实施例8(结晶度:42.92%)>实施例4(结晶度:40.86%)>对比例1(结晶度:38.42%)。从而再次证明采用本发明的热压退火工艺后可以提高铝塑膜热封层pp的结晶度,从而提高铝塑膜热封层的封装可靠性。表3组别tm,p/℃△h/(j·g-1)tm,on/℃tm,end/℃对比例1164.480.3155.2171.9实施例1166.385.4154.8175.2实施例5162.889.7151.1171.7其中tm,p为熔融峰温度,△h为结晶熔融热焓,tm,on为熔融峰开始温度,tm,end为熔融峰结束温度。安全性能对比实验将上述实施例1~8制成的电芯和对比例1制成的电芯各3000ea,按照《gb/t31485-2015电动汽车用动力蓄电池安全要求及试验方法》对各组电芯的过充电、加热和短路性能进行测试,测试结果如表4所示。表4由测试结果可知,与对比例1相比,采用本发明中的热压退火工艺后,电芯的过充电、加热和短路测试通过率均得到明显提高。通过观察各组电芯上述三种安全性能的测试过程发现,对于通过测试的电芯,随着安全测试的进行,电芯均不同程度地出现铝塑膜鼓胀的现象,但在实验结束后未出现起火和爆炸的情况,因此按照国标可判定其通过安全测试。而对于未通过测试的电芯,在电芯测试过程中先后出现了电芯鼓胀、封装区开裂以及起火燃烧等几个阶段,这说明电芯封装可靠性低是导致安全性能不达标的主要原因。而采用本发明中的热压退火工艺可有效提高电芯的封装可靠性,从而显著降低由于封装失效而导致的电芯安全问题的出现概率。以上所述实施例的各技术特征可以进行任意的组合,为使描述简洁,未对上述实施例中的各个技术特征所有可能的组合都进行描述,然而,只要这些技术特征的组合不存在矛盾,都应当认为是本说明书记载的范围。以上所述实施例仅表达了本发明的几种实施方式,其描述较为具体和详细,但并不能因此而理解为对发明专利范围的限制。应当指出的是,对于本领域的普通技术人员来说,在不脱离本发明构思的前提下,还可以做出若干变形和改进,这些都属于本发明的保护范围。因此,本发明专利的保护范围应以所附权利要求为准。当前第1页12