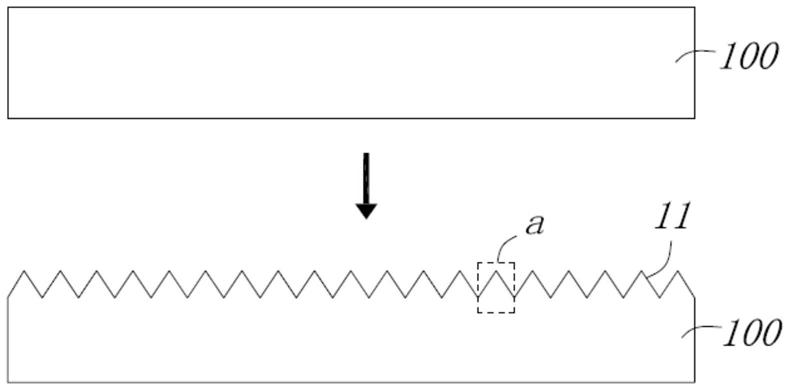
1.本发明涉及光伏制造领域,尤其涉及一种硅片复合绒面制作方法及由该方法制作的硅片。
背景技术:2.随着光伏技术的发展,大家对于太阳能电池片光电转换效率的要求不断提升。其中,在硅片绒面方面,正金字塔绒面可优化的空间已经较小了。近年来,倒金字塔绒面作为一种更加有效的陷光结构被提出,它能使入射光线在硅片表面多次反射,增加硅片对入射光线的吸收,减少反射,从而提升相应太阳能电池片的短路电流。但是倒金字塔由于深度较深,其钝化效果不如正金字塔,相应太阳能电池片的开路电压会有损失,整体效率相对正金字塔绒面硅片所构成太阳能电池片的效率并没有明显提升,且不利于组件功率。
3.有鉴于此,有必要提供一种改进的技术方案以解决上述问题。
技术实现要素:4.本发明旨在至少解决现有技术存在的技术问题之一,为实现上述发明目的,本发明提供了一种硅片复合绒面制作方法,其具体设计方式如下。
5.一种硅片复合绒面制作方法,其包括:
6.s1、将硅片放置于第一碱性溶液中进行各向异性蚀刻处理,在所述硅片表面形成正金字塔结构;
7.s2、于所述硅片的所述正金字塔表面上设置一层高分子微球,并使得所述所述高分子微球的间隙位置处填充有金属氧化物前驱体溶液;
8.s3、高温退火去除所述硅片表面的所述高分子微球,并使得所述金属氧化物前驱体溶液转变为具有孔洞的金属氧化物薄膜;
9.s4、将所述正金字塔表面附有所述金属氧化物薄膜的硅片放置于含有金属离子的第一酸性溶液中,在所述正金字塔表面与所述金属氧化物薄膜孔洞相对应的位置处沉积金属颗粒;
10.s5、将沉积有所述金属颗粒的硅片放置于第二酸性溶液中进行金属催化化学腐蚀,在所述正金字塔表面形成纳米级腐蚀坑;
11.s6、去除所述硅片表面的金属氧化物薄膜。
12.进一步,所述s5步骤与所述s6步骤之间还包括s50步骤,所述s50步骤为:将形成有所述纳米级腐蚀坑的硅片放置于第二碱性溶液中进行再次蚀刻处理,使得所述纳米级腐蚀坑扩大成亚微米级倒金字塔腐蚀坑。
13.进一步,所述高分子微球为直径10nm-1μm的聚苯乙烯微球。
14.进一步,所述s3步骤中的高温退火工艺温度为300-800℃,时间为100-600s。
15.进一步,所述金属氧化物前驱体溶液为氧化锌前驱体溶液、氧化锡前驱体溶液或氧化钛前驱体溶液。
16.进一步,所述第一碱性溶液包括质量百分比浓度为1%-10%的naoh或koh、质量百分比浓度为1%~10%的异丙醇或乙醇、质量百分比浓度为1%~10%的四甲基氢氧化铵、以及质量百分比浓度为1%~10%的硅酸钠。
17.进一步,所述s1步骤中,所述第一碱性溶液的温度为50-85℃,各向异性蚀刻处理的时间为200-600s。
18.进一步,所述金属离子包括au+、ag+、cu2+、pt2+、ni2+或pd2+中的至少一种。
19.进一步,所述第一酸性溶液包括质量百分比浓度为1%-5%的hf、质量百分比浓度为1%~10%的蛋白酶以及质量百分比浓度为5%~10%的非离子表面活性剂。
20.进一步,所述s4步骤中,所述第一酸性溶液的温度为20-40℃,金属沉积的时间为20-200s。
21.进一步,所述第二酸性溶液包括质量百分比浓度为5%-20%的hf溶液以及质量百分比浓度为1%-10%的氧化剂,所述氧化剂包括h2o2、hno3及臭氧水中的至少一种。
22.进一步,所述s5步骤中,所述第二酸性溶液的温度为20-40℃,所述金属催化化学腐蚀的时间为20-200s。
23.进一步,所述第二碱性溶液包括质量百分比浓度为1%-10%的naoh或koh、质量百分比浓度为1%~10%的异丙醇或乙醇、质量百分比浓度为1%~10%的四甲基氢氧化铵、以及质量百分比浓度为1%~10%的硅酸钠。
24.进一步,所述s50步骤中,所述第二碱性溶液的温度为50-85℃,所述第二碱性溶液蚀刻处理的时间为50-200s。
25.进一步,所述s50步骤之后还包括s7步骤,所述s7步骤包括:将所述硅片放置于第三酸性溶液中进行清洗,所述第三酸性溶液包括质量百分比浓度为20%-50%的hno3或10-30ppm的臭氧水。
26.进一步,所述s7步骤中,所述第三酸性溶液的温度为20-40℃,清洗时间为100-300s。
27.进一步,所述s6步骤为:将附着有所述金属氧化物薄膜的所述硅片放置于盐酸或硫酸溶液中反应。
28.进一步,所述s2步骤包括:s21、先于所述硅片的所述正金字塔表面上设置一层所述高分子微球;s22、再将所述正金字塔表面设置有所述高分子微球的所述硅片放置于金属氧化物前驱体溶液中,使所述金属氧化物前驱体溶液填充于所述高分子微球的间隙位置处;或,所述s2步骤包括:s21'、先将所述高分子微球加入至金属氧化物前驱体溶液中形成悬浮液;s22'、再通过旋涂方式将具有所述高分子微球的所述悬浮液涂布于所述硅片具有所述正金字塔的一侧表面。
29.本发明还提供了一种硅片,该硅片由以上所述硅片复合绒面制作方法制作而成。
30.本发明的有益效果是:基于本发明所提供的硅片复合绒面制作方法,能够在硅片表面的正金字塔结构上进一步形成腐蚀坑,使得所获取的硅片表面形成有由正金字塔结构与腐蚀坑共同构成的复合绒面,在具体应用于太阳能电池片的场景中,该复合绒面具有正金字塔钝化效果好、开压高的优点;还能够兼具腐蚀坑陷光效果好、电流高、与电极接触面积大、接触电阻小的优势。
附图说明
31.为了更清楚地说明本发明实施例或现有技术中的技术方案,下面将对实施例或现有技术描述中所需要使用的附图作简单地介绍,显而易见地,下面描述中的附图仅仅是本发明的实施例,对于本领域普通技术人员来讲,在不付出创造性劳动的前提下,还可以根据提供的附图获得其他的附图。
32.图1所示为本发明在硅片表面形成正金字塔结构的示意图;
33.图2所示为图1中a部正金字塔表面设置有高分子微球的放大示意图;
34.图3所示为正金字塔表面设置有高分子微球的平面示意图;
35.图4所示为高分子微球间隙位置处填充有金属氧化物前驱体溶液的示意图;
36.图5所示正金字塔表面附有金属氧化物薄膜的示意图;
37.图6所示为正金字塔表面与金属氧化物薄膜孔洞相对应的位置处沉积有金属颗粒的示意图;
38.图7所示为正金字塔表面形成纳米级腐蚀坑的示意图;
39.图8所示为正金字塔表面形成有亚微米级倒金字塔腐蚀坑的示意图;
40.图9所示为正金字塔表面金属氧化物薄膜被去除后的示意图。
41.图中,100为硅片,11为正金字塔,200为高分子微球,201为高分子微球200的间隙,301为金属氧化物前驱体溶液,300为金属氧化物薄膜,302为金属氧化物薄膜300的孔洞,400为金属颗粒,501为纳米级腐蚀坑,500为亚微米级倒金字塔腐蚀坑。
具体实施方式
42.下面将结合本发明实施例中的附图,对本发明实施例中的技术方案进行清楚、完整地描述,显然,所描述的实施例仅仅是本发明一部分实施例,而不是全部的实施例。基于本发明中的实施例,本领域普通技术人员在没有做出创造性劳动前提下所获得的所有其他实施例,都属于本发明保护的范围。
43.本发明所提供的硅片复合绒面制作方法包括:
44.s1、参考图1所示,将硅片100放置于第一碱性溶液中进行各向异性蚀刻处理,在硅片100表面形成正金字塔11结构。
45.s2、结合图2、图3、图4所示,于硅片100的正金字塔11表面上设置一层高分子微球200,并使得高分子微球200的间隙201位置处填充有金属氧化物前驱体溶液。
46.s3、参考图5所示,高温退火去除硅片100表面的高分子微球200,并使得金属氧化物前驱体溶液301转变为具有孔洞302的金属氧化物薄膜300。较为容易理解,高分子微球200在高温下容易分解,如此,在金属氧化物前驱体溶液301受热形成金属氧化物薄膜300时,高分子微球200所在位置会相应的形成孔洞302。
47.s4、参考图6所示,将正金字塔11表面附有金属氧化物薄膜300的硅片100放置于含有金属离子的第一酸性溶液中,在正金字塔11表面与金属氧化物薄膜300孔洞302相对应的位置处沉积金属颗粒400。
48.s5、参考图7所示,将沉积有金属颗粒400的硅片100放置于第二酸性溶液中进行金属催化化学腐蚀,在正金字塔11表面形成纳米级腐蚀坑501。
49.s6、参考图9所示,去除硅片100表面的金属氧化物薄膜300。具体实施时,将附着有
10%的naoh或koh。优选地,所述第一碱性溶液内还包括第一辅助添加剂,所述第一辅助添加剂包括质量百分比浓度为1%~10%的异丙醇或乙醇、质量百分比浓度为1%~10%的四甲基氢氧化铵、以及质量百分比浓度为1%~10%的硅酸钠。
60.在本发明具有第一辅助添加剂的第一碱性溶液中,第一辅助添加剂可以控制各向异性蚀刻处理的反应速率,进而使得硅片100表面的金字塔11结构相对更为均匀。
61.进一步,在s1步骤中,第一碱性溶液的温度为50-85℃,各向异性蚀刻处理的时间为200-600s。
62.通常,s4步骤中所涉及的金属离子包括au
+
、ag
+
、cu
2+
、pt
2+
、ni
2+
或pd
2+
中的至少一种。基于这些金属离子,在正金字塔12表面沉积的金属颗粒200相应的可以是au、au、ag、cu、pt、ni或pd颗粒。
63.s4步骤中所涉及的第一酸性溶液包括质量百分比浓度为1%-5%的hf溶液。作为优选的所述第一酸性溶液内还包括第二辅助添加剂,所述第二辅助添加剂包括质量百分比浓度为1%~10%的蛋白酶以及质量百分比浓度为5%~10%的非离子表面活性剂。
64.在s4步骤中,每个孔洞302内的金属粒子起始浓度一致,由于金属氧化物薄膜300的作用,在金属颗粒400沉积过程中,不同孔洞302的周边溶液对孔洞302内的金属离子补充速度基本一致,使得各个空洞内的金属颗粒400具有基本一致的沉积速率。进而在后续s5步骤的金属催化化学腐蚀过程中,能够在正金字塔11表面与不同孔洞302对应的位置处形成尺寸基本一致的纳米级腐蚀坑501。
65.具体实施过程中,在s4步骤中,第一酸性溶液的温度为20-40℃,金属沉积的时间为20-200s。
66.本发明的一些具体实施例中,s5步骤中所涉及的第二酸性溶液包括质量百分比浓度为5%-20%的hf溶液以及质量百分比浓度为1%-10%的氧化剂,氧化剂包括h2o2、hno3及臭氧水中的至少一种。优选地,在s5步骤中,第二酸性溶液的温度为20-40℃,金属催化化学腐蚀的时间为20-200s。
67.在本发明s50步骤中,所涉及的第二碱性溶液包括质量百分比浓度为1%-10%的naoh溶液或koh溶液。优选地,所述第二碱性溶液内还包括第三辅助添加剂,所述第三辅助添加剂包括包括质量百分比浓度为1%~10%的异丙醇或乙醇、质量百分比浓度为1%~10%的四甲基氢氧化铵、以及质量百分比浓度为1%~10%的硅酸钠。具体实施时,第三辅助添加剂可以与第一辅助添加剂配比完全一致。
68.在s50步骤中,由于亚微米级倒金字塔腐蚀坑500是在正金字塔11基础上形成,当第二碱性溶液与第一碱性溶液的成分一致时,s50步骤中第二碱性溶液蚀刻处理的时间应当短于s1步骤中各向异性蚀刻处理的时间。
69.具体而言,在本发明的一些具体实施过程中,s50步骤中第二碱性溶液的温度为50-85℃,第二碱性溶液蚀刻处理的时间为200-600s。在本发明的另一些实施例中,也可以适当调低s50步骤中第二碱性溶液的温度范围,例如为50-70℃,以降低s50步骤中第二碱性溶液的蚀刻处理速率。
70.本本发明的又一些实施例中,s50步骤之后还包括s7步骤,s7步骤包括:将硅片放置于第三酸性溶液中进行清洗。通过s7处理可以将硅片100表面的金属颗粒200去除,进而使得硅片100具有较为清洁的表面。
71.具体实施时,第三酸性溶液包括质量百分比浓度为20%-50%的hno3或10-30ppm的臭氧水。优选地,s4步骤中,第三酸性溶液的温度为20-40℃,清洗时间为100-300s。
72.上文所列出的一系列的详细说明仅仅是针对本发明的可行性实施方式的具体说明,它们并非用以限制本发明的保护范围,凡未脱离本发明技艺精神所作的等效实施方式或变更均应包含在本发明的保护范围之内。