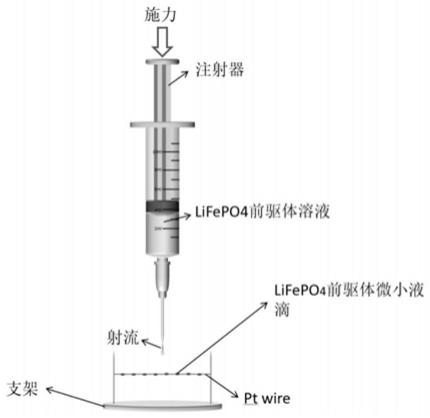
1.本发明涉及微电极制备技术领域,具体涉及一种利用射流注射法制备微电极的方法。
背景技术:2.微电极通常指工作面积很小的电极。根据制作材料的不同,可分为玻璃管微电极和金属微电极。玻璃管微电极是把玻璃毛细管制成颈缩形后,在管腔内填充电解液而成的。传统的玻璃管微电极在制备时需要对玻璃管进行打磨,工艺复杂,成本较高,且由于只能在玻璃管尖端放置电极材料颗粒,因此只能制备单颗粒的微单极,难以做到颗粒数目的可控,并且传统的玻璃管微电极在进行电池组装时较为困难,难以将其应用于锂离子电池的性能研究领域。金属微电极可用易熔金属锡、铅或难溶金属银、钼、镍铬合金、不锈钢等制成。早期的金属微电极由于易受极化电位的影响,电极电位不稳定等而较少被采用。近年来由于技术的进步,金属微电极的电学特性得到改善,但由于这种金属微电极的制备过程较为复杂,国内外的应用还不普遍。
技术实现要素:3.鉴于现有技术的不足,本发明提供一种利用射流注射法制备微电极的方法。
4.本发明方案包括以下方面:
5.一种利用射流注射法制备微电极的方法,包括以下步骤:
6.①
配制电极材料前驱体溶液;
7.②
取金属丝,使金属丝处于拉直状态;
8.③
用注射器吸取前驱体溶液,将注射器针头对准金属丝,推动注射器,使前驱体溶液以射流状射出并均匀依附在金属丝上;
9.④
将步骤
③
处理后的金属丝干燥;
10.⑤
将步骤
④
处理后的金属丝进行预烧结;
11.⑥
将预烧结后的金属丝在13~17wt%的pva溶液中浸泡;
12.⑦
将步骤
⑥
处理后的金属丝干燥后进行烧结。
13.优选的,步骤
④
,干燥温度是30~40℃,干燥12h以上;步骤
⑦
,干燥温度30~40℃,干燥6h以上;进行干燥处理可防止液滴的脱落,而采用以上干燥温度及干燥时间,能够使得水分缓慢且完全被挥发,进而防止因电极颗粒的破裂影响微电极的电化学性能。
14.优选的,步骤
⑥
,浸泡时间是20~30s。本发明在预烧结后以13~17wt%的pva溶液作为胶粘剂浸泡处理20~30s,有利于提高微电极的电化学性能。
15.优选的,预烧结在ar+h2气氛中进行,预烧结时的升温速率为5℃/min,升温至400℃后保温5h。采用该预烧结处理可有效去除前驱体中的结合水。
16.本发明所述的方法可适用于制备各类微电极,包括但不限于lifepo4微电极和li4ti5o
12
微电极。本发明所述金属丝包括但不限于铂丝、金丝。
17.优选的,lifepo4微电极的前驱体溶液包括锂源、铁源、磷酸根源和碳源;li4ti5o
12
微电极的前驱体溶液包括锂源、钛源和碳源。
18.优选的,lifepo4微电极的前驱体溶液配方为:每15ml前驱体溶液中含有1.1131g fe(no3)3·
9h2o、0.2812g lih2po4、0.0034g lioh
·
h2o、0.0355g蔗糖、0.0435g一水柠檬酸;
19.li4ti5o
12
微电极的前驱体溶液配方为:每15ml前驱体溶液中含有0.0364g ti(oc4h9)4、0.0364g lioh
·
h2o、1.1ml h2o2。
20.优选的,注射器针头的内径为0.06~0.08mm,注射速度为0.1ml/s,针头与金属丝的垂直距离为2~5cm。
21.优选的,所述铂丝的直径是30~50μm。
22.优选的,lifepo4微电极的烧结升温程序是:
23.时间/min01503605907709701450温度/℃30180220450450650650
24.优选的,li4ti5o
12
微电极的烧结升温程序是:
25.时间/min015036059077011201600温度/℃30180220450450800800
26.180℃~220℃保温210min,可使pva充分熔融;450℃保温180min,使pva炭化;650℃或800℃处理480min有利于材料快速成型。
27.本发明所取得的有益效果:
28.本发明提出的微电极制备方法,其工艺简单,成本低,能有效降低传统电极的缺点,相比于其他微电极的制备方法,该方法能够制备出单颗粒的微电极,且颗粒数目可根据研究需要进行加减。
29.本发明方法可适用于制备各类微电极,适用范围广。
30.本发明所得微电极的电化学性能良好,电池极化小,库伦效率高。
附图说明
31.图1:使用注射器向铂丝注射前驱体溶液的示意图;
32.图2:lifepo4微电极扫描电镜图;
33.图3:li4ti5o
12
微电极扫描电镜图;
34.图4:lifepo4微电极充放电循环曲线(5圈);
35.图5:lifepo4微电极充放电库伦效率;图中1~5代表第1~5圈;
36.图6:li4ti5o
12
微电极充放电循环曲线(6圈);
37.图7:li4ti5o
12
微电极充放电库伦效率;图中1~6代表第1~6圈;
38.图8:对比例1微电极充放电曲线图;
39.图9:对比例2微电极充放电曲线图;
40.图10:对比例3微电极充放电曲线图;
41.图11:对比例4微电极充放电曲线图;
42.图12:对比例5微电极充放电曲线图;
43.图13:电池结构。
具体实施方式
44.为了更好理解本发明技术内容,下面提供具体实施例,对本发明做进一步的说明。
45.本发明实施例所用的实验方法如无特殊说明,均为常规方法。
46.本发明实施例所用的材料、试剂等,如无特殊说明,均可从商业途径得到。
47.实施例1 lifepo4微电极的制备
48.一种利用射流注射法制备微电极的方法,包括以下步骤:
49.①
配制电极材料前驱体溶液;
50.前驱体溶液配方为:每15ml前驱体溶液中含有1.1131g fe(no3)3·
9h2o、0.2812g lih2po4、0.0034g lioh
·
h2o、0.0355g蔗糖、0.0435g一水柠檬酸,余量是水;
51.②
取长度约4~5cm,直径30~50μm的铂丝固定于支架上,保证铂丝处于拉直状态;
52.③
用注射器吸取前驱体溶液,将注射器针头(针头内径0.06~0.08mm)对准铂丝,推动注射器,使前驱体溶液以射流状射出从而以微小液滴的形态均匀依附在铂丝上;其中,注射速度约0.1ml/s,针头与铂丝的垂直距离为2~5cm。
53.④
将步骤
③
处理后的铂丝30~40℃干燥12h;
54.⑤
将步骤
④
处理后的铂丝放入管式炉并在ar+h2气氛中进行预烧结,预烧结时的升温速率为5℃/min,升温至400℃后保温5h。
55.⑥
将预烧结后的铂丝在15wt%的pva溶液中浸泡20~30s;
56.⑦
将步骤
⑥
处理后的铂丝30~40℃干燥6h,然后在管式炉中(ar+h2气氛)进行烧结。
57.烧结升温程序是:
58.时间/min01503605907709701450温度/℃30180220450450650650
59.将所得微电极装配成如图13所示的电池结构,进行电化学性能检测。具体操作为:将外径3mm、内径0.4mm、长1.5~2.0cm的石英管的一端塞进pvc软管(外径4mm、内径2mm,长为1.5~2.0cm)中,将长4cm、粗50μm的cu丝从石英管的另一端塞入5mm,cu丝多出来的部分用胶布固定在pvc软管外壁;将熔融的锂吸入石英管内,控制吸入锂高度在1.0~1.5cm之间,封口;将cu丝和石英管从pvc软管中拆下,从石英管的另一端注入电解液,将石英管的剩余空间填满,电解液与铜丝不能接触;
⑦
将微电极塞入石英管中,使微电极颗粒完全浸没在电解液中,并保证微电极和锂带有一段距离,封口;
⑧
组装完成后用黑色绝缘胶带将石英管包裹住。电解液为liclo4,浓度为1mol/l,电流大小为5na。
60.结果见图4和图5。图4显示电池极化低于60mv,图5显示库伦效率达到99%以上。
61.实施例2 li4ti5o
12
微电极的制备
62.一种利用射流注射法制备微电极的方法,包括以下步骤:
63.①
配制电极材料前驱体溶液;
64.前驱体溶液配方为:每15ml前驱体溶液中含有0.0364g ti(oc4h9)4、0.0364g lioh
·
h2o、1.1ml h2o2,余量是水。
65.②
取长度约4~5cm,直径30~50μm的铂丝固定于支架上,保证铂丝处于拉直状态;
66.③
用注射器吸取前驱体溶液,将注射器针头(针头内径0.06~0.08mm)对准铂丝,推动注射器,使前驱体溶液以射流状射出从而以微小液滴的形态均匀依附在铂丝上;其中,
注射速度约0.1ml/s,针头与铂丝的垂直距离为2~5cm。
67.④
将步骤
③
处理后的铂丝30~40℃干燥12h;
68.⑤
将步骤
④
处理后的铂丝放入管式炉并在ar+h2气氛中进行预烧结,预烧结时的升温速率为5℃/min,升温至400℃后保温5h。
69.⑥
预烧结后的铂丝在15wt%的pva溶液中浸泡20~30s;
70.⑦
将步骤
⑥
处理后的铂丝30~40℃干燥6h,然后在管式炉中(ar+h2气氛)进行烧结。
71.所述铂丝的直径是30~50μm。
72.烧结升温程序是:
73.时间/min015036059077011201600温度/℃30180220450450800800
74.将所得微电极进行电化学性能检测,结果见图6和图7。图6显示电池极化低于20mv,图7显示库伦效率达到90%以上。
75.对比例1
76.本例与实施例1的区别是:pva溶液浓度为20wt%。
77.其微电极的充放电循环曲线(图8)显示,无充放电平台。其原因主要是:过高浓度的pva溶液在微电极表面形成一层较厚的pva薄膜,烧结后形成碳层,阻碍微电极与电解质的接触导致无法进行充放电。
78.对比例2
79.本例与实施例2的区别是:pva溶液浓度为20wt%。
80.本例所得微电极的电化学性能测试结果见图9。充放电循环曲线显示无充放电平台。
81.对比例3
82.本例与实施例1的区别是:pva溶液浓度为10wt%。
83.其微电极的充放电循环曲线(图10)显示,有充放电平台,但是电化学性能很差。其原因主要是:过低的pva浓度不能够起到胶粘剂的作用,导致烧结后的微电极颗粒破裂。
84.对比例4
85.本例与实施例2的区别是:pva溶液浓度为10wt%。
86.本例所得微电极的电化学性能测试结果见图11,充放电循环曲线显示:有充放电平台,但是电化学性能很差。
87.对比例5
88.本例与实施例1的区别是:
89.将pva溶液与前驱体溶液等质量混合后再进行射流喷射使混液滴依附在pt丝上,而后再进行干燥、烧结,省略步骤
⑤
、步骤
⑥
以及省略步骤
⑦
的干燥处理。
90.本例所得微电极的电化学性能测试结果见图12,结果显示电化学性能较差。其原因主要是:pva与前驱体溶液混合后,干燥,烧结得到的微电极结构密实,阻碍了电极材料与电解液的接触。
91.以上所述仅为本发明的较佳实施例而已,并不用以限制本发明,凡在本发明的精神和原则之内,所作的任何修改、等同替换、改进等,均应包含在本发明的保护范围之内。