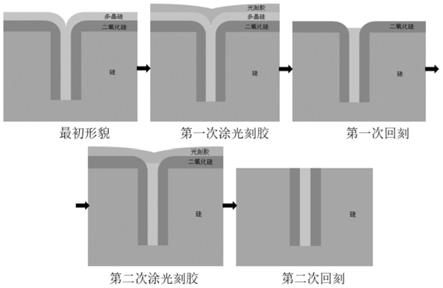
1.本发明属于半导体技术领域,具体属于一种沟槽填充介质后的平坦化回刻方法。
背景技术:2.目前深沟槽结构器件在半导体技术中有着广泛应用,如利用深槽结构进行电绝缘的电子器件,以及使用超级结技术的功率mosfet作为高压开关转换器等,被广泛应用于移动通信、控制电路、汽车电子等方面。沟槽表面介质的不平整,会导致后续工艺金属接触电阻变大,甚至出现金属空洞影响硅基表面良率。
3.传统以及现的有技术对于沟槽填充后的介质平坦化采用化学机械研磨方法,这种方法价格高,且均匀性差。
技术实现要素:4.为了解决现有技术中存在的问题,本发明提供了一种沟槽填充介质后的平坦化回刻方法,对硅基表面沟槽外的双层介质(多晶硅和二氧化硅)膜质进行刻蚀,将槽外介质刻蚀干净至硅基表面,槽顶获得平坦的介质表面。
5.为实现上述目的,本发明提供如下技术方案:一种沟槽填充介质后的平坦化回刻方法,具体步骤如下:
6.s1在硅基表面沟槽中填充第一介质和第二介质,在硅基表面由上到下形成第一次介质层和第二介质层,在第一介质层上进行第一次光刻胶涂胶对硅基表面进行平坦化;
7.s2对光刻胶和第一介质层进行刻蚀,刻蚀后硅基表面的光刻胶刻蚀完全,硅基表面的沟槽顶部剩余一定高度的第一介质层;
8.s3在步骤s2处理后的硅基表面的第二介质层上进行第二次光刻胶涂胶对硅基表面进行平坦化;
9.s4通过调整光刻胶与第一介质和第二介质的选择比,将第二介质层、步骤s3涂覆的光刻胶、以及步骤s2剩余的第一介质层同时刻蚀完全。
10.进一步的,步骤s2中,所述沟槽顶部剩余的第一介质层的高度由第一次刻蚀时的刻蚀速率决定。
11.进一步的,步骤s4中,所述选择比由光刻胶、第一介质层和第二介质层的厚度决定。
12.进一步的,决定的选择比通过调整刻蚀气体用量来实现。
13.进一步的,第一介质层为多晶硅,第二介质层为二氧化硅。
14.进一步的,步骤s2中,所述第一次刻蚀采用干法等离子体刻蚀,刻蚀气体为cl2、hbr、heo2。
15.进一步的,第一次光刻胶涂胶和第二次光刻胶涂胶的厚度均为
16.进一步的,步骤s4中,第二次回刻采用干法等离子体刻蚀,刻蚀气体为cf4、chf3、o2、ar。
17.进一步的,步骤s2中,所述第一次回刻使用机台为amat centura5200。
18.进一步的,步骤s4中,所述第二次回刻使用机台为tel te8500。
19.与现有技术相比,本发明至少具有以下有益效果:
20.本发明提供的沟槽填充介质后的平坦化回刻方法,通过两次光刻胶涂胶平坦化的方法减少硅基表面沟槽处介质的台阶差,刻蚀后可以得到平坦的多晶硅表面,提高了加工质量;本发明的平坦化回刻方法工艺简单稳定,可操作性强,减少了后续工艺缺陷产生。
21.本发明两次刻蚀均采用干法等离子体刻蚀,该方法刻蚀的均匀性好,刻蚀介质的刻蚀速率选择比易于控制,减少刻蚀后槽内两种介质的高度差,保证了刻蚀后表面平整度,本方法可广泛用于功率器件、图像传感器等产品的深沟槽隔离结构的制作,提高产品良率。
附图说明
22.图1本发明平坦化回刻方法流程图;
23.图2实施例1硅基表面沟槽中介质填充后的形貌图;
24.图3实施例1硅基表面沟槽进行介质回刻后的形貌图。
具体实施方式
25.下面结合附图和具体实施方式对本发明作进一步的说明。
26.如图1所示,本发明对硅基表面沟槽外双层介质(多晶硅和二氧化硅)膜质进行刻蚀,将沟槽外介质刻蚀至硅基表面,槽内介质不凸出硅基表面,显著提高介质刻蚀后沟槽表面平整度;
27.本发明提供的一种沟槽填充介质后的平坦化回刻方法,包括第一次光刻胶涂胶、第一次回刻、第二次光刻胶涂胶和第二次回刻,具体步骤如下:
28.(1)第一次光刻胶涂胶,在硅基表面沟槽中填充双介质后,在硅基表面上形成第一介质层和第二介质层,在第一介质层上进行第一次光刻胶涂胶,得到光刻胶层,光刻胶层的厚度为由于光刻胶的流动性,可将槽内介质缝隙填平,达到表面平坦化目的;
29.优选的,第一介质层为多晶硅层,第二介质层为二氧化硅层;
30.(2)第一次回刻,使用干法等离子体刻蚀,刻蚀气体为cl2、hbr和heo2,具体的,将硅基表面的光刻胶刻蚀干净;
31.因第二次回刻时会同时对两个多晶硅和二氧化硅进行刻蚀,所以刻蚀多晶硅层时需要在沟槽顶部预留一定量的多晶硅,为刻蚀二氧化硅层做准备,避免第二次回刻时多晶硅刻蚀过度,影响沟槽顶部平坦度。
32.(3)第二次光刻胶涂胶,在步骤(2)回刻后的硅基表面的二氧化硅层上涂覆光刻胶,得到厚度为的光刻胶层,进行硅基表面平坦化;
33.(4)第二次回刻,使用干法等离子体刻蚀,刻蚀气体为cf4、chf3、o2和ar,具体的,调整光刻胶层和被刻蚀介质层(多晶硅层和二氧化硅层)刻蚀速率的选择比,同时将二氧化硅层上的光刻胶、二氧化硅层及高于沟槽顶部的多晶硅层刻蚀完成。
34.优选的,步骤(2)中,沟槽顶部多晶硅层剩余量通过切片后扫描电子显微镜确认,以规定后续产品第一次回刻的时间;
35.优选的,步骤(2)中,第一次回刻后多晶硅层的剩余量由两次回刻过程中的刻蚀速
率决定。
36.优选的,步骤(4)中,需要达到的选择比由光刻胶层的厚度和被刻蚀介质层厚度决定,通过调整刻蚀过程中刻蚀气体的用量来实现上述决定的选择比,从而实现同时刻蚀完成。
37.优选的,第一次回刻使用机台为amat centura5200多晶硅刻蚀机,所述第二次回刻使用机台为tel te8500氧化硅刻蚀机。
38.实施例1
39.如图2所示,选用6寸硅圆片,在硅圆片沟槽中先进行2.0μm厚的二氧化硅层生长,后进行1.5μm厚的多晶硅层填充,填充后硅圆片表面上多晶硅层厚度为1.5μm,二氧化硅层厚度为2.0μm,进行第一次光刻胶涂胶,光刻胶厚度为表面平坦化后进行第一次刻蚀,采用amat centura5200多晶硅刻蚀机,压力为4mtorr、source功率为475w、bias功率为100w;刻蚀气体选用hbr、cl2和heo2,其中hbr的流量为20sccm、cl2的流量为68sccm、heo2的流量为2sccm,多晶硅层的刻蚀速率为/min,光刻胶层的刻蚀速率为/min,去除二氧化硅层上部的全部的光刻胶层和多晶硅层,沟槽顶部剩余高度为的多晶硅;
40.第二次光刻胶涂胶,光刻胶厚度为表面平坦化后进行第二次刻蚀,去除硅圆片表面全部光刻胶、2.0μm厚的二氧化硅及沟槽顶部剩余的多晶硅,采用tel te8500氧化硅刻蚀机,压力为300mtorr、功率为800w,刻蚀气体选用cf4、chf3、o2和ar,其中cf4的流量为30sccm、chf3的流量为30sccm、o2的流量为15sccm、ar的流量为350sccm,二氧化硅层的刻蚀速率为/min、多晶硅层的刻蚀速率为/min,光刻胶刻层的蚀速率为/min;保证回刻后沟槽外无二氧化硅残留,使得最后的沟槽内的多晶硅及二氧化硅与槽顶齐平,如图3所示。