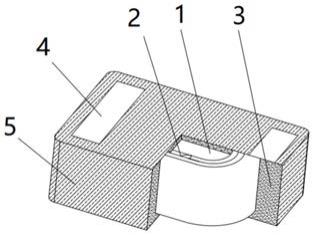
1.本发明涉及电感元件技术领域,具体涉及一种贴片式功率电感及其制备方法。
背景技术:2.贴片式功率电感作为一种基础电子元件,广泛应用于各类电子器件或电子控制电路中。当前各类电子器件向小型化、轻量化、多功能化方向的发展,所应用的贴片式功率电感的数量越来越多,但同时对贴片式功率电感也提出了小型化、低安装厚度、大电感量等新的要求。
3.当前贴片式功率电感主要由软磁材料、线圈、端电极等部分组成,且软磁材料在贯穿线圈的同时也包覆在线圈外部,起到屏蔽电磁场的作用。贴片式功率电感所用的软磁材料一般由软磁合金粉末经粘结、模压、固化等工艺制成,磁导率比较低,造成电感的线圈匝数较多、尺寸较大,不利于当前电感的小型化和大电感量的要求。
4.如公开号为cn102856037b的专利说明书中公开了一种模塑成型功率电感元件,包括预制磁芯、安置在所述预制磁芯上的线圈以及模塑成型覆盖于所述磁芯及线圈上的磁性塑封层,与所述线圈相连的电极暴露在外。该专利中的磁芯塑封层由软磁粉颗粒、有机胶黏剂、润滑剂和固化剂组成,预制磁芯也是通过软磁粉末的模压或注塑成型工艺制作完成。或如公开号为cn104616878b的专利说明书中公开一种微型模压电感元件的制造方法,包括预制磁芯和线圈、将磁芯和线圈形成组合体、模压粉料及所述组合体以成型压制体、金属化电极、整脚及形成端电极。该专利中所述的预制磁芯是采用铁氧体或金属软磁材料作为成型粉料,所述的模压粉料步骤所用的粉料也是由经过绝缘处理的软磁粉、有机胶黏剂、硬化剂及润滑剂配制而成。这两种技术方案均存在上述提及的磁导率较低、不利于电感小型化的问题。
5.目前已有小尺寸、高电感量的贴片式功率电感的线圈尺寸已非常贴近于电感成品的尺寸,易产生线圈裸露、漏磁等问题,对电感后续使用的可靠性和安全性产生隐患,而且这还使得小尺寸电感的制造难度和成本大幅增加。
6.因此,针对目前贴片式功率电感结构及工艺方面的不足,有待于做进一步的改进。
技术实现要素:7.本发明的一个目的在于提供一种新型的贴片式功率电感设计,解决当前贴片式功率电感设计中线圈尺寸较大、电感成品的尺寸难以减小且电感量难以升高等问题。
8.一种贴片式功率电感,包括软磁合金中柱、线圈、磁粉部、及端电极;所述线圈绕置在所述软磁合金中柱上,所述磁粉部包覆在软磁合金中柱和线圈的组合件外部;所述线圈的两个端头引出到所述磁粉部外,并分别与对应所述端电极连接。
9.作为优选,所述磁粉部外表面涂覆有绝缘包覆层。
10.进一步优选,所述绝缘包覆层材料为环氧树脂、聚氨酯、硅酮树脂、有机硅树脂、氨基树脂、聚酰亚胺树脂、酚醛树脂、氰酸脂、丙烯酸树脂中的至少一种。
11.作为优选,所述软磁合金中柱的横截面为圆形、椭圆形或跑道形,所述软磁合金中柱的材料为非晶软磁合金块材和纳米晶软磁合金块材中的一种。
12.作为优选,所述线圈选用扁平的漆包铜线或者自粘圆形漆包线。
13.作为优选,所述线圈的绕制形状为圆形、椭圆形或跑道形,并与所述软磁合金中柱采用间隙配合固定。
14.本发明的另一目的在于提供一种贴片式功率电感的制备方法,包括如下步骤:
15.s1、预制软磁合金中柱:将软磁合金液浇注到中柱模具中,快速冷却得到软磁合金中柱坯体,将坯体脱模后进行加工得到设计尺寸的中柱坯体,然后将坯体进行热处理,得到软磁合金中柱;
16.s2、预制线圈:将漆包线绕按照设计尺寸和形状绕制成线圈;
17.s3、预制杯形磁体:将软磁合金复合粉材装入杯形模具并压制成型,获得带有磁芯腔的杯形磁体,所述杯形磁体不脱模,随模具进入下一工序;
18.s4、预制平板磁体:将软磁合金复合粉材装入平板模具中并压制成型,脱模获得平板磁体;
19.s5、热压成型:将上述步骤制得的软磁合金中柱、线圈、杯形磁体、平板磁体组合后热压成型,脱模后经烘烤、固化、得到电感半成品;
20.s6、喷涂:在步骤s5制得的所述电感半成品的表面喷涂绝缘保护材料,烘烤使表面的绝缘保护材料固化;
21.s7、电极制作:将步骤s6制得的所述电感半成品的线圈端头处的绝缘保护材料和漆包线的漆皮剥除,并在剥漆处电镀电极,获得所述贴片式功率电感。
22.作为优选,所述步骤s5具体为:将所述步骤s1中制得的软磁合金中柱插入所述步骤s2的线圈中,然后将所述线圈与所述软磁合金中柱的组合件置于步骤s3制得的所述杯形磁体的磁芯腔内,最后将步骤s4制得的平板磁体置于杯形磁体顶部进行热压成型,脱模后经烘烤、固化,得到电感半成品。
23.作为优选,所述步骤s3和步骤s4中的软磁合金复合粉材均为软磁合金粉末与粘结剂、润滑剂组成的复合材料。
24.作为优选,所述软磁合金粉末选自非晶软磁合金粉末、纳米晶软磁合金粉末、铁硅铝合金粉末、铁硅铬合金粉末、铁硅合金粉末、铁硅镍合金粉末、铁硅铝镍合金粉末、铁镍合金粉末、铁镍铝合金粉末、羰基铁粉中的至少一种。
25.作为优选,所述粘结剂为环氧树脂、聚氨酯、硅酮树脂、有机硅树脂、氨基树脂、聚酰亚胺、酚醛树脂、氰酸脂、丙烯酸树脂中的至少一种;所述润滑剂为硬脂酸锌、硬脂酸镁、硬脂酸铝、硬脂酸钙、石墨粉和石墨烯中的至少一种。
26.作为优选,所述平板磁体上设有用于线圈端头引出的电极槽。
27.本发明的有益效果:
28.(1)本发明采用非晶软磁合金块材或纳米晶软磁合金块材制备贴片式功率电感的中柱,与现有技术中采用软磁合金粉材粘结制备的中柱相比,本发明的中柱具有更高的磁导率,可实现在减小中柱尺寸和减少线圈匝数的同时大幅提高电感量,即:可以在电感尺寸不变甚或减小的情况下大幅提高其电感值,或在保持电感值不变的情况下显著降低电感成品的尺寸。
29.(2)本发明由于可在电感值不变甚或升高的同时实现线圈匝数的减少,电感的直流电阻(rdc)也得以降低,磁粉部对线圈的包覆效果更好,有效避免了线圈裸露、漏磁等问题,电感的综合性能也大幅提升。
附图说明
30.图1为本发明贴片式功率电感的整体结构透视图;
31.图2为本发明软磁合金中柱的示意图;
32.图3为本发明线圈的结构示意图;
33.图4为本发明线圈与软磁合金中柱组合件的结构示意图;
34.图5为本发明杯形磁体的结构示意图;
35.图6为本发明线圈、软磁合金中柱、杯形磁体组合的结构示意图;
36.图7为本发明平板磁体的结构示意图;
37.图8为本发明贴片式功率电感半成品透视示意图;
38.图9为对比例1贴片式功率电感的绕组磁芯结构示意图;
39.图10为本发明贴片式功率电感制备工艺流程图。
40.附图标示:1、软磁合金中柱;2、线圈;21、线圈端头;3、磁粉部; 4、端电极;5、绝缘包覆层;6、杯形磁体;61、磁芯腔;7、平板磁体; 71、电极槽;8、t形磁体;81、t形磁体中柱。
具体实施方式
41.下面将结合本发明实施例中的附图,对本发明实施例中的技术方案进行清楚、完整地描述,显然,所描述的实施例仅仅是本发明一部分实施例,而不是全部的实施例。基于本发明中的实施例,本领域普通技术人员在没有做出创造性劳动前提下所获得的所有其他实施例,都属于本发明保护的范围。
42.如图1所示,一种贴片式功率电感,包括软磁合金中柱1、线圈2、磁粉部3、端电极4及绝缘包覆层5。
43.其中,线圈2绕置在软磁合金中柱1上,如图2-4所示,线圈2与软磁合金中柱1之间具体采用间隙配合固定;磁粉部3完全包覆在软磁合金中柱1和线圈2的组合件外部,形成长方体的外形,绝缘包覆层5涂覆在磁粉部3外表面;端电极4有两个,线圈2的两个端头21引出到磁粉部3 外,并分别与两个端电极4连接,端电极4嵌于磁粉部3表面并暴露于绝缘包覆层5外。
44.本实施例中,两个端电极4沿电感宽度方向设置于电感底面,且分别位于电感长度方向的两端。
45.本实施例中,磁粉部3为软磁合金粉末与粘结剂、润滑剂的复合材料经模压而成;软磁合金粉末选自非晶软磁合金粉末、纳米晶软磁合金粉末、铁硅铝合金粉末、铁硅铬合金粉末、铁硅合金粉末、铁硅镍合金粉末、铁硅铝镍合金粉末、铁镍合金粉末、铁镍铝合金粉末、羰基铁粉中的至少一种。
46.本实施例中,软磁合金中柱1材料可选用非晶软磁合金块材、纳米晶软磁合金块材中的一种;具体选用fe-si-b-p-cu非晶软磁合金。软磁合金中柱1的横截面为圆形、椭圆形或跑道形;具体为跑道形。
47.本实施例中,绝缘包覆层5的材料为环氧树脂、聚氨酯、硅酮树脂、有机硅树脂、氨基树脂、聚酰亚胺树脂、酚醛树脂、氰酸脂、丙烯酸树脂中的至少一种;具体选用环氧树脂。
48.本实施例中,线圈2选用扁平的漆包铜线或者自粘圆形漆包线;具体选用扁平的漆包铜线,且线圈2的绕制形状为与软磁合金中柱1横截面形状一致的跑道形。
49.如图10所示,一种贴片式功率电感制备工艺流程图,用于制得上述贴片式功率电感,具体包括如下步骤:
50.s1、预制软磁合金中柱:将软磁合金液浇注到中柱模具中,快速冷却得到软磁合金中柱坯体,将坯体脱模后进行加工得到设计尺寸的中柱坯体,然后将坯体进行热处理,得到软磁合金中柱;
51.s2、预制线圈:将漆包线按照设计尺寸和形状绕制成线圈;
52.s3、预制杯形磁体:将软磁合金复合粉材装入杯形模具并压制成型,获得带有磁芯腔的杯形磁体,所述杯形磁体不脱模,随模具进入下一工序;
53.s4、预制平板磁体:将软磁合金复合粉材装入平板模具中并压制成型,脱模获得平板磁体;
54.s5、热压成型:将上述步骤制得的软磁合金中柱、线圈、杯形磁体、平板磁体组合后热压成型,脱模后经烘烤、固化得到电感半成品;
55.s6、喷涂:在步骤s5制得的所述电感半成品的表面喷涂绝缘保护材料,烘烤使表面的绝缘保护材料固化;
56.s7、电极制作:将步骤s6制得的所述电感半成品的线圈端头处的绝缘保护材料和漆包线的漆皮剥除,并在剥漆处电镀电极,获得所述贴片式功率电感。
57.实施例1
58.本实施例中软磁合金中柱材料选用fe-si-b-p-cu非晶软磁合金块材,软磁合金复合粉材选用fe-ni软磁合金粉末与铁粉混合的复合粉末,所用粘结剂为环氧树脂,所用润滑剂为硬脂酸锌,将复合粉末与粘结剂、润滑剂和丙酮混合后筛选得到目标软磁复合粉材,本实施例中贴片式功率电感的制备方法具体包含以下步骤:
59.s1、预制软磁合金中柱:按质量比称取一定量的fe-si-b-p-cu母合金并置于真空熔炼炉中熔炼完全,将软磁合金液浇注到中柱模具中,快速冷却得到软磁合金中柱坯体,将坯体脱模后进行加工得到尺寸为 1.2
×
0.8
×
0.7mm的中柱坯体,然后将坯体置于真空热处理炉中在380℃下热处理120min,得到软磁合金中柱1(如图2所示);
60.s2、预制线圈:选用规格为0.065
×
0.33mm的扁平漆包铜线通过自动绕线机在绕线治具上绕制7.5匝漆包线,并将漆包线的两个端头21呈水平状折弯,从绕线治具上取出后获得具有特定尺寸和形状的线圈2(如图3 所示);
61.s3、预制杯形磁体:将筛选好的软磁合金复合粉材装入预设结构和尺寸的杯形模具中,启动高精密伺服成型压机在常温下进行冲压成型,获得带有磁芯腔61的杯形磁体6(如图5所示),杯形磁体1置于冷压成型模具中不脱离,随模具进入下一工序;
62.其中,压制杯形磁体1时所采用的冷压压力为3t/cm2,保压时间为1s。
63.s4、预制平板磁体:将筛选好的软磁合金复合粉材装入预设结构和尺寸的平板冷压成型模具中,启动高精密伺服成型压机在常温下进行冲压成型,获得带有两电极槽71的平板磁体7(如图7所示),电极槽71用于引出线圈2的端头21;
64.其中,压制平板磁体7时所采用的冷压压力为3t/cm2,保压时间为1s。
65.s5、热压成型:将步骤s3中制得的杯形磁体6在模穴内呈开口朝上随模具放置,将模具整体加热至180℃并保温;将步骤s1中制得的软磁合金中柱1插入步骤s2的线圈2内部(如图4所示),再将线圈2与软磁合金中柱1的组合件置于杯形磁体6的磁芯腔61内(如图6所示),然后将平板磁体7置于杯形磁体6顶部;将模具置于热压成型机的机台上,启动成型压机进行热压成型,脱模后制得电感坯体,再对电感坯体进行烘烤,得到固化的电感半成品(如图8所示);
66.其中,热压时所采用的热压压力为3t/cm2,保压时间150s,保温温度为180℃。对电感坯体进行烘烤固化处理,具体的,将电感坯体放入烘箱中进行加热升温,使电感坯体中的树脂发生固化反应得到电感坯体。此处采用的树脂是环氧树脂,在固化时仅有较小的体积收缩,不至于让电感坯体在固化成型后变形。具体地,烘烤固化温度为180℃,此处可选用带有升降温阶梯曲线的烘烤设备,保温3h,最终获得电感半成品,电感半成品的尺寸为2.0
×
1.6
×
1.0mm。
67.s6、喷涂:采用恒温加热喷涂设备,在步骤s5制得的电感半成品表面包覆一层环氧树脂保护材料,即绝缘包覆层5,然后烘烤喷涂后的电感半成品,使电感半成品表面的环氧树脂固化。其中,烘烤条件为:在150℃下烘烤2h,使电感半成品表面树脂固化。
68.s7、电极制作:采用激光剥漆设备将步骤s6制得的电感半成品的端头21处铜电极表面的环氧树脂保护材料和铜线漆皮剥除,使底部铜电极显露出来,在剥漆处电镀铜层、镍层和锡层,实现端电极4引出,获得贴片式功率电感(如图1所示)。
69.对制备的贴片式功率电感样品进行测试,利用阻抗分析仪测得样品在 1v/1mhz条件下的平均电感值ls为1.173μh,平均饱和电流isat为4.81a,平均直流电阻rdc为31.5mω。
70.对比例1
71.本对比例采用现有的贴片式功率电感的结构设计和制备技术,即电感中柱采用软磁合金复合粉材经模压、固化工艺制备,电感成品制备采用行业内现有常用的“预制t形磁体、在t形磁体上绕线、热压成型、喷涂、电极制作”的步骤。选用与实施例1相同的软磁合金复合粉材,相同的漆包线、粘结剂、润滑剂及外部绝缘包覆材料,电感中的中柱尺寸和形状、线圈绕制匝数和形状、电极结构和尺寸、电感成品的尺寸等参数均与实施例1的相同,但不使用非晶软磁合金块材或纳米晶软磁合金块材制备中柱,而是利用软磁合金复合粉材制备电感中柱。本对比例中电感的制备方法具体包含以下步骤:
72.s1、预制t形磁体:将筛选好的软磁合金复合粉材装入预设结构和尺寸的t形模具内,启动高精密伺服成型压机在常温下进行压制成型,然后脱模,获得第一t形磁体;将第一t形磁体放入烘箱中进行烘烤,得到具有一定的强度的t形磁体8。
73.其中,压制磁体时所采用的冷压压力为3t/cm2,保压时间为1s,烘烤温度为160℃,烘烤时间为30min。
74.s2、线圈绕制:利用自动绕线机将漆包线绕在t形磁体8上的磁体中柱81上,绕制7.5匝,并将两端引脚折弯后贴合到t形磁体8的平板底面,得到绕组磁芯(如图9所示)。
75.s3、热压成型:将绕组磁芯置于热压成型模具中,使t形磁体呈“丄”形放置,并将软磁合金复合粉材置于绕组磁芯上部热压成型,脱模后经烘烤、固化,得到电感半成品。
76.其中,热压时所采用的热压压力为3t/cm2,保压时间150s,保温温度为180℃。对电
感坯体进行烘烤固化处理,具体的,将电感坯体放入烘箱中进行加热升温,使电感坯体中的树脂发生固化反应得到电感坯体。此处采用的树脂是环氧树脂,在固化时仅有较小的体积收缩,不至于让电感坯体在固化成型后变形。具体地,烘烤固化温度为180℃,此处可选用带有升降温阶梯曲线的烘烤设备,保温3h,最终获得电感半成品,电感半成品的尺寸为2.0
×
1.6
×
1.0mm。
77.s4、喷涂:喷涂工艺如实施例1中步骤s6。
78.s5、电极制作:电极制作如实施例1中步骤s7。
79.采用与实施例1相同的性能测试设备和条件,对制得的电感样品的主要性能进行测试,测得的性能参数如表1中所示。
80.对比例2
81.本对比例采用另一种现有的贴片式功率电感的结构设计和制备技术,电感成品制备采用行业内现有常用的“预制线圈、填粉、热压成型、喷涂、电极制作”的步骤。选用与实施例1相同的软磁合金复合粉材,相同的漆包线、粘结剂、润滑剂及外部绝缘包覆材料,线圈绕制匝数和形状、电极结构和尺寸、电感成品的尺寸等参数均与实施例1的相同,但不使用非晶软磁合金块材或纳米晶软磁合金块材制备中柱,而是利用软磁合金复合粉材与线圈组合模压制备成贴片式功率电感,电感中柱此处为线圈内部软磁合金复合粉材经模压、固化而成的部分。本对比例中贴片式功率电感的制备方法具体包含以下步骤:
82.s1、预制线圈:选用规格为0.065
×
0.33mm的扁平漆包铜线通过自动绕线机在绕线治具上绕制7.5匝漆包线,并将漆包线的两个端头21呈水平状折弯,从绕线治具上取出后获得具有特定尺寸和形状的线圈2(如图3 所示)。
83.s2、热压成型:将步骤s1预制线圈2置于热压成型模具的模穴内,将软磁合金复合粉材填入模穴,然后将模具置于热压成型机的机台上,启动成型压机进行热压成型,脱模后经烘烤、固化,得到电感半成品,电感半成品的尺寸为2.0
×
1.6
×
1.0mm。
84.其中,热压时所采用的热压压力为3t/cm2,保压时间150s,保温温度为180℃。对电感坯体进行烘烤固化处理,具体的,将电感坯体放入烘箱中进行加热升温,使电感坯体中的树脂发生固化反应得到电感坯体。此处采用的树脂是环氧树脂,在固化时仅有较小的体积收缩,不至于让电感坯体在固化成型后变形。具体地,烘烤固化温度为180℃,此处可选用带有升降温阶梯曲线的烘烤设备,保温3h,最终获得电感半成品。
85.s3、喷涂:喷涂工艺如实施例1中步骤s6。
86.s4、电极制作:电极制作如实施例1中步骤s7。
87.采用与实施例1相同的性能测试设备和条件,对制得的电感样品的主要性能进行测试,测得的性能参数如表1中所示。
88.表1实施例1及对比例1-2制得的贴片式功率电感的性能参数
[0089][0090]
实施例2
[0091]
本实施例中贴片式功率电感的尺寸规格与实施例1的相同,仅将线圈匝数减少为5.5匝,以及软磁合金复合粉末选用fe-si-b-nb-cu纳米晶软磁合金粉末与铁粉混合的复合粉末,其余的电感结构参数、原材料、制备技术和工艺参数均与实施例1的相同,详见实施例1。获得贴片式功率电感样品后,利用阻抗分析仪测得样品在1v/1mhz条件下的平均电感值ls 为1.032μh,平均饱和电流isat为4.8a,平均直流电阻rdc为28.2mω。
[0092]
对比例3
[0093]
本对比例采用现有的贴片式功率电感的结构设计和制备技术,即电感中柱采用软磁合金复合粉材经模压、固化工艺制备,电感成品制备采用行业内现有常用的“预制t形磁体、在t形磁体上绕线、热压成型、喷涂、电极制作”的步骤。
[0094]
本对比例中贴片式功率电感的尺寸规格与实施例2的相同,选用与实施例2中相同的软磁合金复合粉材,即fe-si-b-nb-cu纳米晶软磁合金粉末与铁粉混合的复合粉末,但线圈匝数为6.5匝,不使用非晶软磁合金块材或纳米晶软磁合金块材制备中柱,而是利用软磁合金复合粉材制备电感中柱。其余的电感结构参数、原材料等均与实施例2的相同,电感制造方法、步骤和工艺参数等均与对比例1的相同,详见对比例1。采用与实施例2相同的性能测试设备与条件,对制备的电感样品进行性能测试,获得的性能参数如表2中所示。
[0095]
对比例4
[0096]
本对比例采用另一种现有的贴片式功率电感的结构设计和制备技术,电感成品制备采用行业内现有常用的“预制线圈、填粉、热压成型、喷涂、电极制作”的步骤。
[0097]
本对比例中贴片式功率电感的尺寸规格与实施例2的相同,选用与实施例2中相同的软磁合金复合粉材,即fe-si-b-nb-cu纳米晶软磁合金粉末与铁粉混合的复合粉末,但线圈匝数为7.5匝,不使用非晶软磁合金块材或纳米晶软磁合金块材制备中柱,而是利用软磁合金复合粉材与线圈组合模压制备成贴片式功率电感,电感中柱此处为线圈内部软磁合金复合粉材模压、固化而成的部分。其余的电感结构参数、原材料等均与实施例2 的相同,电感制造方法、步骤和工艺参数等均与对比例2的相同,详见对比例2。采用与实施例2相同的性能测试设备与条件,对制备的电感样品进行性能测试,获得的性能参数如表2中所示。
[0098]
表2实施例2及对比例3-4制得的贴片式功率电感的性能参数
[0099][0100]
表1、表2中包括实施例1-2及对比例1-4在贴片式功率电感制造工艺上的差别以及最终生成的贴片式功率电感的直流电阻rdc、饱和电流 isat和电感量ls等性能。
[0101]
通过比较实施例1和对比例1、2可以得出,本发明中采用非晶软磁合金块材制备贴片式功率电感的中柱,具有更高的磁导率,极有利于提升电感的电感量和饱和电流,而且电感的直流电阻(rdc)也得以降低。
[0102]
由实施例2和对比例3、4的对比可知,本发明的贴片式功率电感设计,可以在电感量保持不变甚或升高的同时,实现线圈匝数的明显减少,电感的直流电阻大幅降低,而且由于线圈匝数的减少,在同等尺寸规格的条件下,电感的磁粉部所占体积更大,其对线圈的包覆效果更好,有效避免了线圈裸露、漏磁等问题,电感的综合性能大幅提升。
[0103]
尽管参照前述实施例对本发明进行了详细的说明,对于本领域的技术人员来说,其依然可以对前述各实施例所记载的技术方案进行修改,或者对其中部分技术特征进行等同替换,凡在本发明的精神和原则之内,所作的任何修改、等同替换、改进等,均应包含在本发明的保护范围之内。