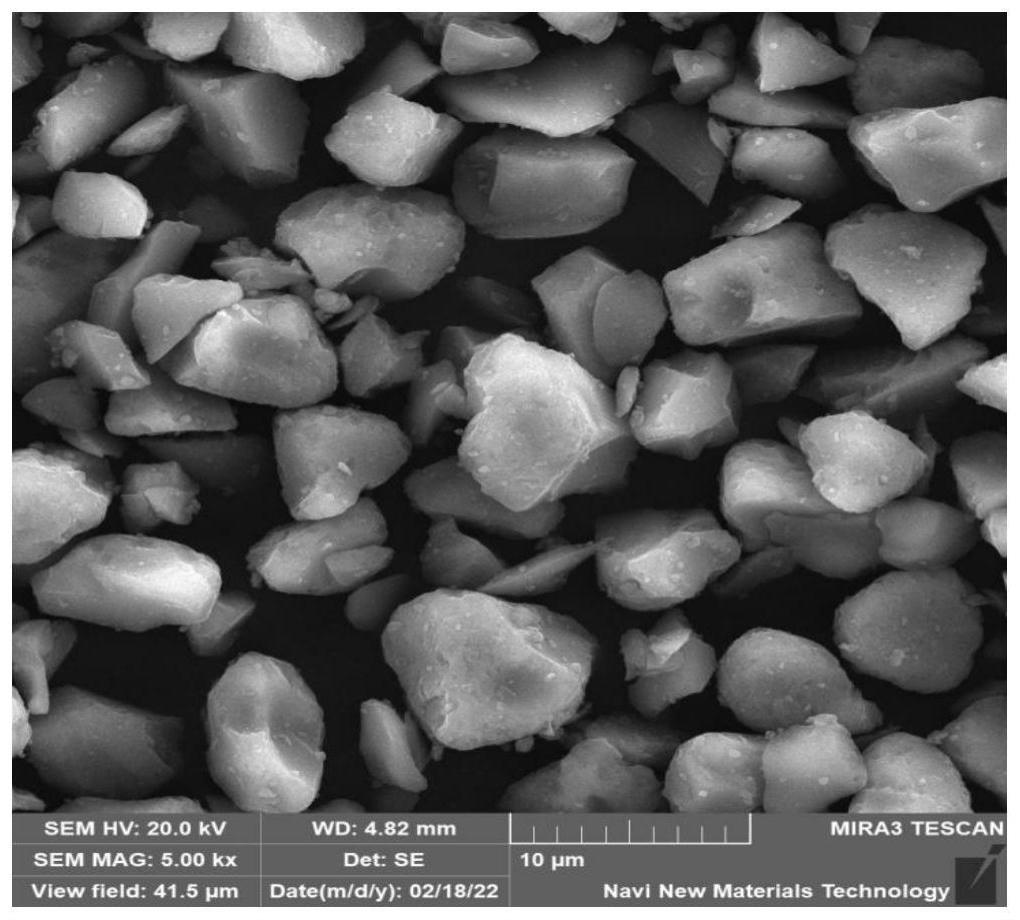
1.本发明涉及一种氧化亚硅材料的改性方法,尤其涉及一种氧化亚硅材料流动性的改性方法,属于氧化亚硅材料制备技术领域。
背景技术:2.随着社会的发展和科技的进步,能源消耗日益加剧,环境污染也日益严重,且已严重威胁到人类未来的生存。在急需开发清洁环保的可再生能源的背景下,锂离子电池由于具有能量密度高、循环寿命长、环境友好等优点而得到迅速发展。在众多锂离子电池负极材料中碳基石墨负极材料最为常用,但是该材料比容量较低(372mah/g)、不可逆容量损失较大,致使锂离子电池难以满足使用性能需求,发展空间难以有所突破。而在目前所有已知的负极材料中,硅基材料的比容量是最高的,达到了4200mah/g。是最具潜力替代石墨负极的下一代锂离子电池负极材料之一,具有优秀的市场前景。
3.氧化亚硅(sio)硅基材料因具有较高理论比容量(2680mah/g)及较小体积膨胀率(160%),在众多硅基负极材料中脱颖而出。但其粉体流动性差,一方面会造成收集桶、挡板等地方出现物料粘壁滞留,造成收率下降,生产成本增加;另一方面,物料粘壁滞留会导致连续生产过程中碳包覆效果不理想,引起碳包覆量不一致,产品批次内一致性差等问题;因此,解决粉料流动性已成为氧化亚硅加工生产中急需解决的关键性问题。而影响氧化亚硅粉体流动性的主要原因在于材料的疏水性和抗静电性差。中国专利(公开号为cn 112289999a)公开了一种氧化亚硅/碳复合材料及制备方法和应用,该专利技术在一定程度上改善粉料流动性差的问题,但是其制备中出现的含氧的废气易与裂解气本身及裂解气分解后产生的氢气发生反应,会增加裂解气的消耗,导致成本增加;且含氧的废气与氢气高温交互,存在严重的安全隐患,制备难度大,难以放大,实际上并不适合大规模的工业化生产,同时该方法对物料流动性的改善效果不明显,碳包覆稳定性和收率均有待进一步提升。
技术实现要素:4.为克服上述现有的技术缺陷,本发明的目的是在于提供一种氧化亚硅流动性的改性方法,该方法利用疏水性氨基酸在氧化亚硅颗粒表面形成一层具有疏水和防静电的包覆层,可有效改善水分子表面吸附和粒子间因静电引起的相互吸附,降低氧化亚硅粉体的团聚,减轻物料粘壁滞留的现象,疏水性氨基酸经过热解后,可在氧化亚硅表面上形成一层均匀的薄碳层,有利于获得均匀的cvd碳包覆层,能增加氧化亚硅材料的流动性,解决了氧化亚硅负极生产过程中出现的低收率和一致性差的问题,且该方法过程简单,无安全风险,可满足大规模的工业化生产需求。
5.为了实现上述技术目的,本发明提供了一种氧化亚硅流动性的改性方法,该方法是将疏水性氨基酸和氧化亚硅粉均匀混合后,置于保护气氛下,进行煅烧处理,得到改性氧化亚硅粉;在改性氧化亚硅粉表面通过高温气相沉积生成碳包覆层,得到碳包覆氧化亚硅负极材料。
6.将疏水性氨基酸与氧化亚硅粉充分混合均匀后,可以利用疏水性氨基酸在氧化亚硅粉表面上包覆形成具有疏水性和防静电性的保护膜,可有效防止团聚,形成均匀的包覆,疏水性氨基酸经过煅烧后,可在氧化亚硅表面上形成一层均匀的薄碳层,有利于获得均匀的cvd碳包覆层,增加氧化亚硅材料的流动性。
7.作为一个优选的方案,所述疏水性氨基酸为丙氨酸、缬氨酸、亮氨酸、苯丙氨酸、色氨酸、甲硫氨酸、脯氨酸中至少一种。采用疏水性的氨基酸能够防止氧化亚硅表面吸水,从而可以有效防止团聚,如果采用亲水性氨基酸在混合后会在氧化亚硅表明形成一层亲水层,在混合过程中会增加物料的团聚,导致包覆不均匀,降低了其煅烧后碳层包裹的均匀性,难以达到提高氧化亚硅流动性的目的。
8.作为一个优选的方案,所述疏水性氨基酸和氧化亚硅粉的质量之比为1:(1~10)。疏水性氨基酸和氧化亚硅粉的质量之比较优选为1:(2.5~10);疏水性氨基酸和氧化亚硅粉的质量之比进一步优选为1:5~10。如果疏水性氨基酸比例过低,混合后氧化亚硅粉表面无法形成均匀的疏水、防静电包覆层,煅烧后表面无法形成均匀的薄碳层,如果疏水性氨基酸比例过高时,多余的氨基酸材料将不再参与包覆过程,造成不必要的浪费,意义不大。
9.作为一个优选的方案,所述氧化亚硅粉为d50中值为4.0~7.0μm。更优选的d50中值为5.5
±
0.5μm。
10.作为一个优选的方案,所述混合采用搅拌方式,搅拌速度为300~1000rpm,搅拌时间为1~5h。在适当的高速搅拌条件下有利于疏水性氨基酸在氧化亚硅表面的均匀吸附。
11.作为一个优选的方案,所述煅烧处理的条件为:升温速率为2.0~15.0℃/min,煅烧温度为600~800℃,煅烧时间为4h~6h。升温速率进一步优选为5~10℃/min。煅烧过程中保护气氛为氮气、氦气、氩气、氩氢混合气中至少一种。煅烧温度过低、煅烧时间过短,则会造成疏水性氨基酸热解不充分,且包覆的碳层不够均匀,造成改性的效率过低。如果煅烧温度过高、煅烧时间过长,会导致氧化亚硅出现歧化反应,硅晶粒生长,造成氧化亚硅循环性能降低。
12.作为一个优选的方案,所述高温气相沉积通过连续回转炉实现,连续回转炉主机转频为5~50hz,下进料转频为5~50hz。连续回转炉主机转频为20~30hz,下进料转频为20~30hz。
13.作为一个优选的方案,所述高温气相沉积的条件为:以甲烷、乙炔、丙烯中至少一种作为裂解气,裂解气流量控制在2.0~5.0l/min,气相沉积温度为800~1050℃,时间为1h~4h。在气相沉积时,气流量过低时,碳包覆所需的碳源不足,严重影响包覆效果;气流量过高,提供碳源远远超过所需碳源,虽不影响碳包覆效果但大部分碳源未能参与气相沉积导致天然气碳源流失,天然气属于易燃易爆气体,流量过大将大大提高其安全隐患,而适当的温度条件,能够保证裂解气的充分裂解。裂解气流量控制更优选为2.0~4.0l/min。
14.本发明的氧化亚硅流动性的改性方法还具有以下可替代方案,如氧化亚硅可以替换为单质硅、碳硅材料、二氧化硅材料等。
15.本发明提供的氧化亚硅粉流动性的改性方法,包括以下步骤:
16.步骤1):将疏水性氨基酸粉体和粒度中值d50=4.0~7.0μm的氧化亚硅粉按照质量比1:(2.5~10)置于搅拌机中,在300~1000rpm的转速下,搅拌1~5h后,得到均匀的混合物料;疏水性氨基酸材料为丙氨酸、缬氨酸、亮氨酸、苯丙氨酸、色氨酸、甲硫氨酸、脯氨酸等
结晶性粉末状疏水性氨基酸;
17.步骤2):将步骤1)中的物料置于箱式炉中,在氮气、氦气、氩气或氩氢混合气气氛保护气下,按2~15℃/min速率升温600~800℃后,恒温4~6小时,然后自然冷却,获得改性氧化亚硅粉;
18.步骤3),将步骤2)中的改性氧化亚硅粉,置于主机转频5~50hz和下进料转频为5~50hz的回转炉中,在氮气、氦气、氩气或氩氢混合气保护气和2~5l/min甲烷、乙炔、丙烯中至少一种裂解气条件下,800~1050℃气相沉积1~4小时,最终获得碳包覆氧化亚硅负极材料。
19.对比现有技术,本发明技术方案具有的优势如下:
20.1、本发明的氧化亚硅粉流动性改性过程中,采用的疏水性氨基酸属于较为常见的生物材料,获取途径广泛,成本低廉,不会生成有毒物质对环境较为友好;
21.2、本发明的氧化亚硅粉流动性改性过程中,利用疏水性氨基酸在氧化亚硅粉表面包覆一层具有疏水和防静电修饰层,可有效改善水分子表面吸附和粒子间因静电引起的相互吸附,防止氧化亚硅颗粒之间的团聚,减轻物料粘壁滞留的现象,疏水性氨基酸经过碳化后,可在氧化亚硅表面上形成一层均匀的薄碳层,有利于获得均匀的cvd碳包覆层,能增加氧化亚硅材料的流动性,解决了氧化亚硅负极生产过程中出现的低收率和一致性差的问题。
22.3、本发明的氧化亚硅粉流动性改性过程制备过程简单,无安全风险,可满足大规模的工业化生产需求。
23.4、本发明的氧化亚硅粉流动性改性过程中产品收率高、碳包覆的一致性好。
附图说明
24.图1为实施例1制备的碳包覆氧化亚硅负极材料的sem图谱。
具体实施方式
25.以下具体实施例旨在进一步详细说明本发明内容,而不是限制权利要求的保护范围。
26.下面给出本发明中使用的部分学术术语的定义,其他未述及的学术术语具有本领域所公知的定义和含义:
27.本发明改性氧化亚硅粉材料,可作为前驱体材料进行碳包覆、预锂化、电池制备等后续制备工艺。
28.实施例1
29.步骤1)将5kg丙氨酸粉体和粒度中值d50=5.5μm的50kg氧化亚硅粉置于搅拌机中,在600rpm的转速下,搅拌2h后,得到均匀的混合物料;
30.步骤2)将步骤1中的物料置于箱式炉中,在氮气气氛保护气下,按8℃/min速率升温750℃后,恒温5小时,然后自然冷却,获得改性氧化亚硅粉;
31.步骤3)将步骤2中的改性氧化亚硅粉,置于主机转频25hz和下进料转频为25hz的回转炉中,在氮气保护气和3l/min甲烷气氛条件下,980℃气相沉积2小时,最终获得碳包覆氧化亚硅负极材料。
32.实施例2
33.步骤1)将7.5kg丙氨酸粉体和粒度中值d50=5.5μm的50kg氧化亚硅粉置于搅拌机中,在600rpm的转速下,搅拌2h后,得到均匀的混合物料;
34.步骤2)将步骤1中的物料置于箱式炉中,在氮气气氛保护气下,按8℃/min速率升温750℃后,恒温5小时,然后自然冷却,获得改性氧化亚硅粉;
35.步骤3)将步骤2中的改性氧化亚硅粉,置于主机转频25hz和下进料转频为25hz的回转炉中,在氮气保护气和3l/min甲烷气氛条件下,980℃气相沉积2小时,最终获得碳包覆氧化亚硅负极材料。
36.实施例3
37.步骤1)将10kg丙氨酸粉体和粒度中值d50=5.5μm的50kg氧化亚硅粉置于搅拌机中,在600rpm的转速下,搅拌2h后,得到均匀的混合物料;
38.步骤2)将步骤1中的物料置于箱式炉中,在氮气气氛保护气下,按8℃/min速率升温750℃后,恒温5小时,然后自然冷却,获得改性氧化亚硅粉;
39.步骤3)将步骤2中的改性氧化亚硅粉,置于主机转频25hz和下进料转频为25hz的回转炉中,在氮气保护气和3l/min甲烷气氛条件下,980℃气相沉积2小时,最终获得碳包覆氧化亚硅负极材料。
40.实施例4
41.步骤1)将7.5kg亮氨酸粉体和粒度中值d50=5.5μm的50kg氧化亚硅粉置于搅拌机中,在600rpm的转速下,搅拌2h后,得到均匀的混合物料;
42.步骤2)将步骤1中的物料置于箱式炉中,在氮气气氛保护气下,按8℃/min速率升温650℃后,恒温6小时,然后自然冷却,获得改性氧化亚硅粉;
43.步骤3)将步骤2中的改性氧化亚硅粉,置于主机转频25hz和下进料转频为25hz的回转炉中,在氮气保护气和3l/min甲烷气氛条件下,850℃气相沉积3小时,最终获得碳包覆氧化亚硅负极材料。
44.对比实施例1(采用亲水性氨基酸作为对照)
45.步骤1)将7.5kg甘氨酸粉体和粒度中值d50=5.5μm的50kg氧化亚硅粉置于搅拌机中,在600rpm的转速下,搅拌2h后,得到均匀的混合物料;
46.步骤2)将步骤1中的物料置于箱式炉中,在氮气气氛保护气下,按8℃/min速率升温750℃后,恒温5小时,然后自然冷却,获得改性氧化亚硅粉;
47.步骤3)将步骤2中的改性氧化亚硅粉,置于主机转频25hz和下进料转频为25hz的回转炉中,在氮气保护气和3l/min甲烷气氛条件下,980℃气相沉积2小时,最终获得碳包覆氧化亚硅负极材料。
48.对比实施例2(以煅烧条件作为对照)
49.步骤1)将7.5kg丙氨酸粉体和粒度中值d50=5.5μm的50kg氧化亚硅粉置于搅拌机中,在600rpm的转速下,搅拌2h后,得到均匀的混合物料;
50.步骤2)将步骤1中的物料置于箱式炉中,在氮气气氛保护气下,按2℃/min速率升温400℃后,恒温2小时,然后自然冷却,获得改性氧化亚硅粉;
51.步骤3)将步骤2中的改性氧化亚硅粉,置于主机转频25hz和下进料转频为25hz的回转炉中,在氮气保护气和3l/min甲烷气氛条件下,980℃气相沉积2小时,最终获得碳包覆
氧化亚硅负极材料。
52.对比实施例3(以气相沉积条件作为对照)
53.步骤1)将7.5kg丙氨酸粉体和粒度中值d50=5.5μm的50kg氧化亚硅粉置于搅拌机中,在600rpm的转速下,搅拌2h后,得到均匀的混合物料;
54.步骤2)将步骤1中的物料置于箱式炉中,在氮气气氛保护气下,按8℃/min速率升温750℃后,恒温5小时,然后自然冷却,获得改性氧化亚硅粉;
55.步骤3)将步骤2中的改性氧化亚硅粉,置于主机转频25hz和下进料转频为25hz的回转炉中,在氮气保护气和1l/min甲烷气氛条件下,980℃气相沉积2小时,最终获得碳包覆氧化亚硅负极材料。
56.对比实施例4
57.与实施例1的唯一不同之处为:取消步骤1和步骤2,直接用氧化亚硅粉进行步骤3的高温气相沉积,获得碳包覆氧化亚硅负极材料。
58.应用例1
59.将实施例1~4和对比实施例4所制备的改性和未改性的氧化亚硅负极材料,进行扣式电池性能测试,其扣式电池制作步骤如下:将上述条件下制备的负极材料、碳黑、羧甲基纤维素、丁苯橡胶按质量比90:5:4:1混合均匀后,加入固含量为50%的去离子水,配成浆料,然后在涂布机上将浆料均匀涂覆在铜箔上,最后在真空空箱中100℃烘烤4h后制成工作电极。以锂片为对电极,采用25umpp的隔膜,1mol/l lipf6(溶剂为体积比1:1的碳酸乙烯酯和碳酸二甲酯混合液)作为电解液,在氩气保护条件下的手套箱中组装完成扣式电池制作。
60.应用例2
61.将实施例1~4和对比实施例4所制备的改性和未改性的氧化亚硅负极材料,进行安息角测试,其具体测试步骤如下:借助水平仪,调节底板上的三个支脚,使装置呈水平状态。
62.用高度量规调节漏斗下料口刚好与高度量规平面接触,在此位置用螺丝固定好漏斗,并移去高度量规。
63.把所制备的改性和未改性的氧化亚硅负极材料从大约40mm高处加入到漏斗中心,不得振动实验装置。控制下料量为20g/min~60g/min,供料应尽量均匀连续。筛网被堵时,可用软毛刷轻轻地扫一下,注意不得振动实验装置。当试料锥体顶部到达漏斗出口时,停止加入材料。将锥体底部圆周的八条半径划在底板上,移去试料,测量出径向辐射方向上已标记的四条直径。
64.应用例3
65.将实施例1~4和对比实施例4所制备的改性氧化亚硅负极材料,进行碳含量测试,其具体测试方法为采用碳硫分析仪进行测试,将得出测试结果进行比较分析。
66.实验情况:
67.实施例1~4及对比实施例1~3所制备的改性氧化亚硅粉以及对比例1所制备的未改性氧化亚硅粉根据应用例1~3的检测方法进行测试,表1为步骤1混合物料安息角测试数据,内容如下:
68.案例安息角/
°
实施例150
实施例247实施例347实施例448对比实施例151对比实施例249对比实施例347对比实施例452
69.从表1中可以看出,疏水性氨基酸的混合加入可以降低物料的安息角;当疏水性氨基酸与氧化亚硅粉的比例提高时,其流动性改善的效果也有所提高;且丙氨酸的改善效果要略优于亮氨酸的;使用亲水性氨基酸混合,安息角并未有明显的改善;煅烧温度和时间也对流动性有着明显的影响,当煅烧温度过低、时间过短时,氧化亚硅粉体流动性的改性效果效率不佳。
70.表2为步骤3物料出炉后不同时间段出炉的碳包覆氧化亚硅的出料量和碳含量测试数据,内容如下:
[0071][0072]
从表2中可以看出,相比较对比实施例4,疏水性氨基酸的加入,可明显提高碳包覆氧化亚硅的出料量和碳含量的稳定性;且通过疏水性氨基酸改性后的物料,其收率基本在
80%以上,显现高于无疏水性氨基酸改性的物料(物料总收率为60.0%)。相比较实施例2,对比实施例3中气相沉积时的气流量过低,碳含量和出炉量均有所降低。
[0073]
表3为实施例1~4及对比实施例1~4所制备的改性氧化亚硅负极材料根据应用例1所制备扣式电池的电化学测试数据,内容如下:
[0074][0075]
从表3中可以看出,相比较对比实施例4,疏水性氨基酸的加入,可明显提高材料的循环性能,50
th
容量保持率在87~90%之间(对比实施例4:50
th
容量保持率在80%左右)。对比实施例1相比较实施例2,亲水性氨基酸的改性效果远不如疏水性氨基酸;当煅烧温度过低,氧化亚硅粉的改性效果较差,电化学性能降低。