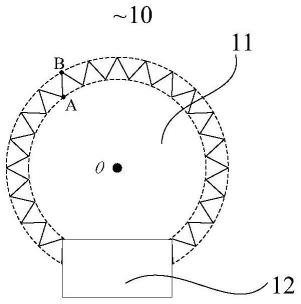
1.本发明涉及光电显示技术领域,特别是涉及一种显示模组及制备方法。
背景技术:2.随着显示技术的发展,柔性显示面板得到越来越广泛的应用,如应用于折叠显示设备、卷曲显示设备中。然而柔性显示面板厚度较薄、材质较软,为防止柔性显示面板在生产、搬运及运输过程中受力产生裂纹导致水汽入侵形成黑斑及线路断裂,通常会在柔性显示面板上贴附保护膜。
技术实现要素:3.本发明主要解决的技术问题是提供一种显示模组及制备方法,能够提高显示面板的良率。
4.为解决上述技术问题,本发明采用的一个技术方案是:提供一种显示模组,显示模组包括显示面板,显示面板包括显示区和邦定区,显示区为设置发光器件的区域,邦定区为邦定电子元件的区域,显示区包括弧形边框,且弧形边框的至少部分区域设置有尖锐角。通过在弧形边框上设置尖锐角,能够提供撕膜时的起撕点,方便膜层起角,以免撕膜过程中带起显示面板,对显示面板带来损伤。
5.在一实施方式中,显示区的弧形边框呈锯齿状。通过将显示区的弧形边框设置成锯齿状,能够增大显示区边缘的周长,使得被加热融化的胶流动路径变大,继而流动至保护膜处的胶量减少,以降低保护膜与显示面板间的粘附性,利于保护膜的撕除。
6.在一实施方式中,显示区的弧形边框包括多个相连接的锯齿段,每个锯齿段包括内端点和外端点,各锯齿段的内端点在同一个圆周上,各锯齿段的外端点在同一个圆周上。通过这种设置,能够方便测量锯齿段的加工位点,利于加工路径的规划。
7.在一实施方式中,内端点形成的圆与外端点形成的圆为同心圆。通过这种设置,能够使显示区弧形边框各个区域受力更均衡,防止应力不均对显示面板带来损伤。
8.在一实施方式中,锯齿的深度为10~30μm,其中,锯齿的深度为锯齿段内端点到外端点的长度。通过这种设置,不会影响显示模组的外观检查,不会影响显示模组的尺寸精度。
9.在一实施方式中,显示模组还包括功能层,功能层设置于显示面板上,功能层的边缘轮廓与显示面板的弧形边框轮廓相同。通过设置功能层,能够提高显示模组的显示及强度等性能。
10.在一实施方式中,功能层包括偏光片和支撑膜,偏光片设置于显示面板的出光侧;支撑膜设置于显示面板的背光侧。通过贴装偏光片来减少眩光,增强屏幕显示的对比度;通过贴装支撑层来增强显示面板的强度。
11.在一实施方式中,显示面板为柔性显示面板。
12.为解决上述技术问题,本发明采用的另一个技术方案是:提供一种显示模组制备
方法,显示模组制备方法包括提供显示模组预制体,显示模组预制体包括显示面板预制体和保护膜,显示面板预制体包括显示区和邦定区,显示区为设置发光器件的区域,邦定区为邦定电子元件的区域;对显示面板预制体以及覆盖显示面板预制体的保护膜进行切割,以使显示面板的显示区具有弧形边框,且弧形边框的至少部分区域设置有尖锐角;撕除保护膜。
13.在一实施方式中,显示模组预制体包括层叠设置的显示面板预制体、功能层预制体和保护膜,对显示面板预制体以及覆盖显示面板预制体的保护膜进行切割包括:利用激光对显示面板预制体、功能层预制体和保护膜进行切割,控制切割路线,使得显示面板的弧形边框、功能层和保护膜的边缘呈锯齿状。
14.本发明的有益效果是:区别于现有技术的情况,本发明通过在弧形边框上设置尖锐角,能够提供撕膜时的起撕点,方便膜层起角,以免撕膜过程中带起显示面板,对显示面板带来损伤。
附图说明
15.图1是本技术实施方式中显示模组的结构示意图;
16.图2是本技术另一实施方式中显示模组的结构示意图
17.图3是本技术又一实施方式中显示模组的结构示意图;
18.图4是本技术实施方式中显示模组的剖面结构示意图;
19.图5是本技术另一实施方式中显示模组的剖面结构示意图;
20.图6是本技术实施方式中显示模组制备方法的流程示意图;
21.图7是本技术实施方式中显示模组预制体的结构示意图。
具体实施方式
22.为使本技术的目的、技术方案及效果更加清楚、明确,以下参照附图并举实施例对本技术进一步详细说明。
23.本技术提供了一种显示模组,该显示模组包括显示面板,显示面板包括发光器件和阵列基板。发光器件可以是oled发光器件、量子点发光器件,micro-led发光器件等,即本技术公开的显示面板可用于多种显示方式,例如oled显示、量子点显示,micro-led显示等。这里以oled显示为例进行说明,但不限于该显示方式。
24.阵列基板包括衬底层和阵列层。衬底可以是柔性衬底,即本技术所公开的显示面板可以是柔性显示面板。柔性衬底的材料可以但不限于为聚酰亚胺(pi)、聚醚酰亚胺(pei)、聚苯硫醚(pps)及聚芳酯(par)或pet中的一种或多种的组合,或者是可弯折钢片。阵列层内设置有阵列驱动电路(即像素电路)用于控制发光器件发光,阵列层上还设置有信号线、外围电路、邦定的驱动芯片、柔性电路板等其他电子元件。阵列层一般由缓冲层、薄膜晶体管层(例如低温多晶硅/非晶硅/氧化物/有机薄膜晶体管)形成的cmos/nmos/pmos的顶栅/底栅等结构,及其所延伸出来的其他结构。薄膜晶体管层包括半导体层(有源层)、栅极、源极、漏极、绝缘层等。通过对这些薄膜晶体管层进行构图,可以形成控制发光器件发光的阵列驱动电路,其具体电路结构有多种实现方式,在此不再赘述。
25.随着显示技术的发展进步,显示面板的应用领域越来越广泛,随即涌现出多种显
示设备,如电视,电脑,手机,车载显示设备,智能手表、智能眼镜等可穿戴设备。为适用不同的显示设备,显示面板可以具有不同的形状,如可以是矩形显示面板、圆形显示面板、椭圆形显示面板、梯形显示面板等。当显示面板为柔性显示面板时,因为柔性显示面板厚度较薄、材质较软,为防止柔性显示面板在生产、搬运及运输过程中受到损坏,特别是防止柔性显示面板的边缘受力产生裂纹,导致水汽入侵形成黑斑及线路断裂。通常先形成显示面板预制体,显示面板预制体的形状尺寸稍大于目标显示面板的形状尺寸,待使用时,再对显示面板预制体进行处理,切割成目标形状尺寸。同时,为了保护显示面板预制体在运输、切割过程中表面不被划伤,还会在显示面板预制体表面贴附保护膜,在尺寸形状加工时,将保护膜和显示面板预制体一起切割成需要的外形尺寸,再撕除保护膜。
26.一般地,可以使用激光对显示面板预制体进行外形切割,但是经过发明人长期研究发现,激光切割时产生的热量会使得保护膜与显示面板预制体中的胶层熔融,导致切割形成的边缘区域的保护膜与显示面板粘接,使得保护膜撕离时较为困难,容易将显示面板带起,造成显示面板损坏。特别地,当显示面板为圆形显示面板或椭圆形显示面板时,显示面板的边缘是弧形的,在撕膜时,弧形边框不利于膜层起角,使得膜层撕除困难。
27.请参阅图1,图1是本技术实施方式中显示模组的结构示意图。该实施方式中,显示模组包括显示面板10,显示面板10包括显示区11和邦定区12,显示区11为设置发光器件的区域,邦定区12为邦定电子元件的区域,具体的,电子元件包括驱动芯片和/或柔性电路板,显示区11包括弧形边框。如图1所示,显示面板10包括圆形的显示区11,圆形的显示区11具有弧形边框。
28.其中,显示面板10可以利用矩形显示面板预制体切割形成,具体的,先制备形成矩形的显示面板预制体,矩形的显示面板预制体包括矩形显示区和矩形邦定区,对矩形的显示面板预制体的显示区进行切割,形成圆形的显示区11,而目标显示面板10的邦定区12是矩形,所以不用对矩形的邦定区12进行切割。即圆形的显示面板10除了邦定区12是直边不切割外,其余区域都是切割形成的圆形边缘。可以是利用激光技术切割形成圆形的显示区11,切割时,由于激光会散发热量,容易导致显示面板10中的胶层熔融,流至保护膜与显示面板10的切割边缘,即弧形边框,使得边缘处的保护膜与显示面板10较难分离。
29.在撕除保护膜时,由于邦定区12线路较多,较为脆弱,较难承受住起撕时的应力,易造成线路断裂,不易将邦定区12作为膜层起撕点,也就意味着撕膜只能从显示区11起撕。然而,显示区11的弧形边框是圆形,弧形边框较为圆滑,本就不容易使膜层起角形成起撕点,且切割时熔融的胶又使得弧形边框位置的保护膜与显示面板10较难分离,导致膜层撕除变得困难。
30.基于此,本技术所提供的方案,对显示区11的弧形边框的至少部分区域进行处理,形成尖锐角,如图1中r区域所示。通过这种设置,尖锐角处比较容易起角形成起撕点,使得保护膜可以很好的撕开,避免带起显示面板10,对显示面板10带来损坏。其中,可以是在切割成形的过程中,改变局部区域的切割路线,形成尖锐角。
31.请参阅图2,图2是本技术另一实施方式中显示模组的结构示意图。该实施方式中,可以将显示区11的弧形边框处理成锯齿状,即显示面板10的显示区11弧形边框整体均设计成锯齿结构。通过将显示区11的弧形边框整体设计成锯齿状,在撕膜时比较容易起角,形成起撕点,且能够增大显示区11边缘的周长,使得被加热融化的胶流动路径变大,继而流动至
保护膜处的胶量减少,以降低保护膜与显示面板10间的粘附性,利于保护膜的撕除。
32.请参阅图3,图3是本技术又一实施方式中显示模组的结构示意图。该实施方式中,显示区11的弧形边框包括多个相连接的锯齿段,如图3中线段ab,每个锯齿段包括内端点(如图3中点a)和外端点(如图3中点b)。其中,各锯齿段的内端点在同一个圆周上,各锯齿段的外端点在同一个圆周上,且内端点形成的圆与外端点形成的圆为同心圆。如图3中所示,两个圆的圆心均为o。具体的,两个圆的圆心可以与显示区11的圆心重叠。通过这种设置,一方面能够方便测量锯齿段的加工位点,另一方面能够使显示区11弧形边框的各个区域受力更均衡,防止应力不均对显示面板10带来损伤。在其他实施方式中,也可以只将显示区11弧形边框的一部分设计成锯齿状,如仅将显示区11的左上角区域或右上角区域的弧形边框设计成锯齿状。
33.在一实施方式中,锯齿的深度为10~30μm,其中,锯齿的深度为锯齿段内端点到外端点的长度,即线段ab的长度。通过这种设置,不会影响显示模组的外观检查,不会影响显示模组的尺寸精度。
34.请结合参阅图4和图5,图4是本技术实施方式中显示模组的剖面结构示意图,图5是本技术另一实施方式中显示模组的剖面结构示意图。该实施方式中,显示模组还包括功能层,即显示模组包括显示面板10和功能层20,功能层20至少位于显示面板10上。功能层20可以是用来改善显示面板10显示效果的膜层,也可以是用来保护显示面板10的膜层。如功能层20可以是偏光层、增透层、反射层、支撑层等。如图4所示,显示模组包括显示面板10和功能层20。
35.其中,功能层20的边缘轮廓与显示面板10的弧形边框轮廓相同。换句话说,功能层20与显示面板10在一道工序中同时被切割成形。
36.具体地,在制备显示模组时,完成基础显示面板10的制作后,会在显示面板10上贴附一层或多层功能层20,以提升显示面板10的显示性能。例如,可以通过贴装偏光片来减少眩光,增强显示面板10的对比度;可以通过贴装支撑层来增强显示面板10的强度。一般地,先形成显示面板预制体,再在显示面板预制体上形成功能层预制体,例如分别先在显示面板预制体两侧贴附对应的功能层预制体,所贴附的功能层预制体同样稍大于目标形状和尺寸;然后再一起对功能层预制体和显示面板预制体进行切割,得到目标形状尺寸。通过这种方式,所制得的显示模组中,功能层20的边界轮廓与显示面板10的边界轮廓相同,能够使功能层20完全覆盖显示面板10,增强显示面板10边缘的强度;同时,因为功能层20的存在,进一步增强了显示面板预制体的强度,在生产、搬运及运输过程中不易受到损坏。
37.在一具体实施例中,功能层20包括偏光片21和支撑膜22,偏光片21设置于显示面板10的出光侧;支撑膜22设置于显示面板10的背光侧,可以是先分别在显示面板预制体正反面分别贴附功能层预制体如偏光片预制体及功能层预制体如支撑膜预制体,然后一起激光切割成需要的外形尺寸,保证显示面板10边缘的强度,最后再在偏光片预制体表面贴附oca及在支撑膜预制体背面贴附缓冲材料,形成显示模组预制体,其中偏光片预制体和支撑膜预制体非胶面贴附有防止划伤、脏污的保护膜,激光切割时也保留。利用激光对显示模组预制体进行切割,虽然激光切割时产生的热量使得偏光片21、支撑膜22与显示面板10之间的胶层熔融,导致切割区域的保护膜与显示面板粘接,会使得在撕除保护膜时起撕点无法起角,易对显示面板带来损伤。但是,本技术方案中,在弧形边框区域设计切割形成了尖锐
角,可以从尖锐角处起撕,使得保护膜更容易被撕除,且不会对显示面板10带来损伤。
38.请参阅图6,图6是本技术实施方式中显示模组制备方法的流程示意图。该实施方式中,显示模组制备方法具体包括:
39.s610:提供显示模组预制体。
40.其中,显示模组预制体包括显示面板预制体和保护膜,显示面板预制体包括显示区和邦定区,显示区为设置发光器件的区域,邦定区为邦定电子元件的区域,其中,电子元件包括驱动芯片和/或柔性电路板。
41.s620:对显示面板预制体以及覆盖显示面板预制体的保护膜进行切割,以使显示面板的显示区具有弧形边框,且弧形边框的至少部分区域设置有尖锐角。具体的,可以是对显示面板预制体的显示区进行切割。
42.s630:撕除保护膜。
43.请参阅图7,图7是本技术实施方式中显示模组预制体的结构示意图。该实施方式中,显示模组预制体包括显示面板预制体10’,分别位于显示面板预制体10’两侧的功能层预制体,功能层预制体包括偏光片预制体21’和支撑膜预制体22’,以及分别覆盖偏光层预制体21’和支撑层预制体22’的保护膜30。保护膜30的贴附能够防止偏光片预制体21’和支撑膜预制体22’的非胶面在运输过程中被划伤、脏污。
44.在一实施方式中,可以利用激光技术对显示模组预制体进行切割,切割形成目标形状尺寸。其中,在激光切割时保护膜30也保留,以持续对显示模组预制体进行保护,防止切割过程中显示模组预制体被划伤。同时,保护膜30会随显示模组预制体一起被切割,形成与显示模组预制体相同的边缘线。
45.本技术所提供的方案,当显示模组的形状为圆形、椭圆形等具有圆弧形等没有尖锐角的形状时,在进行图形切割时,调整激光切割路线,将部分或全部弧形边框处理成带有尖锐角的形状,如处理成锯齿状。以在后续保护膜30撕除时能够好的起角。
46.请结合参阅图2,可以通过调整激光切割路径,将显示模组边缘切割成多段线锯齿状。其中,应控制锯齿宽度不可过小,过小会导致切割时间过长、效率过低,且锯齿深度较小;锯齿宽度也不能过大,不可超出需求外形精度。具体地,所形成的锯齿形结构,在人工肉眼检测时,肉眼不可视的锯齿感,不会影响产品外观;但是若使用显微镜等仪器进行检测时,如将产品放大20倍或50倍后,能够明显看出锯齿形状。其中,本文附图仅是示例性的结构,旨在清楚标明相关结构,并不是实际尺寸,实际中肉眼观察时不易觉察到锯齿状,因此不会影响弧形边框位置的显示效果。进一步地,应调控激光热量不可辐射至显示面板10的封装膜层,防止封装膜层损坏。
47.请结合参阅图3,每个锯齿段包括内端点和外端点,各锯齿段的内端点在同一个圆周上,各锯齿段的外端点在同一个圆周上,且内端点形成的圆与外端点形成的圆为同心圆。通过这种设置,一方面能够方便测量锯齿段的加工位点,方便控制激光切割路径;另一方面能够使显示区11弧形边框各个区域受力更均衡,防止应力不均对显示面板10带来损伤。
48.切割完成后,撕除偏光片和支撑膜两侧的保护膜。撕膜时,从显示区的锯齿边缘开始,以锯齿的尖锐角为起撕点,因为尖锐角的存在,比较容易起角。进一步地,多段锯齿状切割路径使得显示模组边缘周长增大,使得激光切割产生的热量将偏光片、支撑膜与显示面板之间的胶层熔融时,胶层的流动路径增加,继而流动至外层保护膜的胶量减少,保护膜与
偏光片、支撑膜之间的粘性也相应降低;同时后续工站设备撕除偏光片及支撑膜上的保护膜时,撕膜滚轮与保护膜的接触面积也增加,且显示模组弧形边框锯齿形尖角位置应力也大,使得起撕位置保护膜受力较大;从而保护膜可以很好的撕开,避免带起显示面板,有效降低显示面板被损坏的概率。
49.保护膜撕除后,可继续完成显示模组的其他结构,如盖板的贴附、缓冲材料的设置等,具体工艺可以用现有工艺制成,在此不再赘述。所得显示模组结构从上到下依次为盖板、oca、偏光片21、显示面板10、支撑膜22及缓冲材料。
50.本技术所提供的方案,在撕除显示面板上的保护膜,特别是对于撕除具有弧形边框的柔性显示面板的保护膜具有显著效果,能够保护显示面板在撕膜过程中不被损坏。
51.以上所述仅为本技术的实施方式,并非因此限制本技术的专利范围,凡是利用本技术说明书及附图内容所作的等效结构或等效流程变换,或直接或间接运用在其他相关的技术领域,均同理包括在本发明的专利保护范围内。