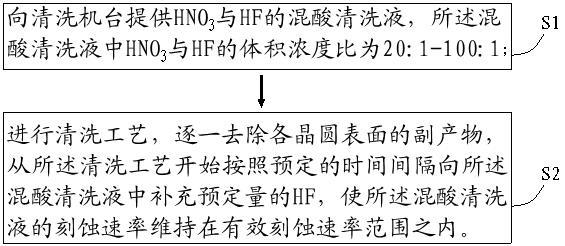
1.本发明涉及半导体制造领域,具体涉及一种晶圆清洗方法。
背景技术:2.硝酸(hno3)和氢氟酸(hf)的混酸清洗液(以下简称混酸清洗液),凭借其自身优异的化学性能,被广泛应用于晶圆清洗中。特别是混酸清洗液对许多金属,例如铜金属,具有优异的清洗能力,常被用于去除晶圆表面的金属副产物的清洗工艺当中,可有效防止晶圆表面金属残留导致的器件短路,同时也可有效降低机台混用导致的金属交叉污染的风险。
3.混酸清洗液的清洗原理为:利用hno3的强氧化性和酸性,溶解掉晶圆表面的金属副产物,所述金属副产物包括金属和/或金属氧化物,利用hf中氟离子的强配位性腐蚀掉硅晶圆表面的sio2副产物,然后hno3和hf对暴露的硅层进行刻蚀并释放出扩散进硅层的金属副产物,最后hno3对扩散进硅层的金属副产物进行溶解去除,从而确保对金属副产物的去除效果。
4.实际的清洗工艺中,一般都选用富hno3的混酸清洗液,以确保对金属副产物的去除效果,所述富hno3的混酸清洗液中,hno3含量远高于hf含量,hno3与hf的体积浓度比通常达到20:1~100:1。富hno3的混酸清洗液在对晶圆进行循环清洗的过程中,随着混酸清洗液中hf的消耗,hf的浓度逐渐降低,导致混酸清洗液的刻蚀速率降低,当刻蚀速率降低至稳定刻蚀速率范围之外时,会造成刻蚀速率的不稳定。更进一步地,在经过一定时间的循环清洗后,混酸清洗液的刻蚀速率继续降低至有效刻蚀速率范围(此有效刻蚀速率范围可根据具体的工艺标准而定)之外,此时可认为混酸清洗液失效,为保证清洗工艺的品质,需要更换混酸清洗液。频繁地更换混酸清洗液降低了清洗机台的产能,并且更换下来的混酸清洗液中含有大量未充分利用的hno3,导致混酸清洗液的使用效率低下,并且因为使用效率低导致混酸清洗液的使用成本高和回收成本高的问题。
技术实现要素:5.有鉴于此,本发明提供了一种晶圆清洗方法,以提高混酸清洗液的使用效率和刻蚀速率稳定性。
6.一种晶圆清洗方法,其特征在于,包括:向清洗机台提供hno3与hf的混酸清洗液,该混酸清洗液中的hno3与hf的体积浓度比为20:1~100:1;进行清洗工艺,逐一去除各晶圆表面的副产物,从清洗工艺开始按照预定的时间间隔向混酸清洗液中补充预定量的hf,使混酸清洗液的刻蚀速率维持在有效刻蚀速率范围之内。
7.优选地,晶圆包括硅晶圆。
8.优选地,晶圆表面包括晶圆背面。
9.优选地,预定的时间间隔为200s~800s,预定量的hf为0.01v mol/l~0.02v mol/l
的hf,其中v为所述混酸清洗液的体积。
10.优选地,从清洗工艺开始按照预定的时间间隔向混酸清洗液中补充预定量的hf包括:在清洗工艺开始之后的0min~40min时间段内,每隔500s~800s向混酸清洗液中补充预定量的hf,在清洗工艺开始之后的41min~80min时间段内,每隔200s~300s向混酸清洗液中补充预定量的hf。
11.优选地,副产物包括金属和/或金属氧化物,金属包括铜,金属氧化物包括氧化铜。
12.优选地,所述清洗工艺的工艺参数包括:每片晶圆的清洗时间为3s~60s,混酸清洗液的温度为23℃~28℃,混酸清洗液的流量为750ml/min~850ml/min。
13.优选地,清洗液中的hno3与hf的体积浓度比为50:1。
14.优选地,清洗机台包括单片式清洗机台。
15.优选地,清洗工艺的时间小于6000s。
16.与现有技术相比,本发明所提供的一种晶圆清洗方法方法,具有以下优点:本发明提供的一种晶圆清洗方法,通过按照预定时间间隔向所述混酸清洗液中补充预定量的hf,使所述混酸清洗液的刻蚀速率维持在有效刻蚀速率范围之内,提高了混酸清洗液的使用效率,降低了混酸清洗液的使用成本,避免了频繁更换混酸清洗液导致清洗机台产能降低的问题;同时本发明提供的晶圆清洗方法,改善了混酸清洗液的刻蚀速率下降导致的刻蚀速率不稳定的问题。
附图说明
17.图1为一实施例提供的晶圆清洗方法的流程图;图2为现有技术的晶圆清洗方法中,混酸清洗液的刻蚀速率随刻蚀时间的变化曲线;图3为一实施例提供的晶圆清洗方法中,混酸清洗液的刻蚀速率随刻蚀时间的变化曲线;图4为另一实施例提供的晶圆清洗方法中,混酸清洗液的刻蚀速率随刻蚀时间的变化曲线;图5为图4所对应的另一实施例提供的晶圆清洗方法中,晶背清洗前后的金属铜含量的对比柱状图。
具体实施方式
18.为使本发明的目的、优点和特征更加清楚,以下结合附图对本发明所提供的一种晶圆清洗方法作进一步详细说明。需说明的是,附图均采用非常简化的形式且均使用非精准的比例,仅用以方便、明晰地辅助说明本发明实施例的目的。
19.发明人经过研究分析发现,混酸清洗液对硅晶圆的晶背清洗的过程主要分为刻蚀副产物和刻蚀硅层两个步骤,所述副产物包括氧化硅和金属副产物,所述金属副产物包括金属和/或金属氧化物。以含有铜副产物的晶背清洗工艺为例,清洗过程中包括以下化学反应:sio
2 + 4hf
ꢀ→ꢀ
sif4↑
+ 2h2o (1)cu + 4hno3ꢀ→ꢀ
cu(no3)
2 + 2no2↑
+ 2h2o (2)
cuo + 2hno3ꢀ→ꢀ
cu(no3)
2 + h2o (3)si + hno
3 + 6hf
ꢀ→ꢀ
h2sif
6 + hno
2 + h2o + h2↑
(4)混酸清洗液的清洗过程,首先是对表层副产物进行清洗。所述表层包括自然氧化形成的sio2膜层以及该sio2膜层上沉积的少量金属和金属氧化物的颗粒和/或膜层。这个过程发生化学反应(1)、(2)和(3)。
20.在所述表层被清洗去除之后,会接着刻蚀所述表层之下一定厚度的硅层。由于金属的扩散性,会有少量的金属副产物扩散进所述硅层,因此实际的清洗工艺中,为确保金属副产物能够被完全去除,通常需要刻蚀掉一定厚度的硅层,这个过程发生化学反应(4)。化学反应(4)为总反应,其分步反应为:首先,利用hno3的氧化性将si氧化成+4价的si
4+
,然后si
4+
与f-配位反应形成h2sif6。刻蚀硅层的过程中,扩散进硅层的金属副产物也随之暴露,因此同时发生化学反应(2)和(3)。由于金属副产物含量极少,且硝酸充足,可认为反应(2)和(3)立即发生。因此,刻蚀硅层的刻蚀速率主要由化学反应(4)的反应速率决定。
21.由于清洗工艺中,刻蚀掉的硅层厚度(超过1500
å
)远远大于刻蚀掉的表层厚度(几十
å
),因此主要发生的是化学反应(4);并且表层的刻蚀时间相较于硅层的刻蚀时间很短,可忽略不计,因此,整个清洗工艺的刻蚀速率以及清洗剂的消耗情况也主要由刻蚀硅层的步骤决定。清洗工艺中,为保证对金属副产物的良好去除效果,同时避免硅层的刻蚀过于剧烈(化学反应(4)反应速率快并且放出大量热量),一般选用富hno3的混酸清洗液,所述混酸清洗液中hno3含量较高而hf含量较低。而由化学反应(4)可知,清洗工艺中,hf的消耗较大。因此随着清洗工艺的进行,hf的浓度降低,所述混酸清洗液的刻蚀速率下降,导致所述混酸清洗液刻蚀速率不稳定甚至失效,降低了清洗工艺的品质。
22.为解决上述问题,本发明提供了一种方便、可行的解决方法,该方法通过向所述混酸清洗液中及时补充hf,使所述混酸清洗液的刻蚀速率维持在有效刻蚀速率范围内,确保所述混酸清洗液的有效性。本发明中,采用业内常用的评价所述混酸清洗液的有效性的两个标准:第一标准和第二标准,随时检测所述混酸清洗液在清洗工艺的不同时刻的有效性。所述第一标准为:所述混酸清洗液对热氧化形成的sio2膜层的刻蚀速率稳定在205
å
/min~245
å
/min的有效刻蚀速率范围,此标准能确保清洗工艺的有效进行;第二标准:所述混酸清洗液对铜制程中经过化学机械研磨(cmp)后的晶背进行清洗后,晶背铜含量达到icpms标准,即铜原子数量小于5
×
109/cm2,此标准能确保混酸清洗液对金属的去除效果良好。当所述混酸清洗液同时满足所述第一标准和所述第二标准时,可判断所述混酸清洗液具有有效性。
23.请参阅图1,本发明提供了一种晶圆清洗方法,包括以下步骤:s1:向清洗机台提供hno3与hf的混酸清洗液,所述混酸清洗液中hno3与hf的体积浓度比为20:1~100:1;s2:进行清洗工艺,逐一去除各晶圆表面的副产物,从所述清洗工艺开始按照预定的时间间隔向所述混酸清洗液中补充预定量的hf,使所述混酸清洗液的刻蚀速率维持在有效刻蚀速率范围之内。
24.在本实施例中,清洗工艺在现有的单片式清洗机台中进行,采用流程化方式对各晶圆进行逐一、连续地清洗,清洗的晶圆数量与清洗工艺进行的时间(同时也是所述混酸清洗液的刻蚀总时间)呈线性关系。
25.所述混酸清洗液中hno3与hf的体积浓度比优选为50:1,但不限于此,该体积浓度比也可以为20:1~100:1之间的任意值,以确保所述混酸清洗液中hno3含量远大于hf含量。所述混酸清洗液中还包括一定量的去离子水,用所述去离子水进行稀释以使hno3与hf达到预期的浓度,并确保在该预期的浓度下,所述混酸清洗液符合所述第一标准,即对热氧化形成的sio2膜层的刻蚀速率在205
å
/min~245
å
/min的有效刻蚀速率范围之内;在该合适的浓度下,所述混酸清洗液对硅片的刻蚀速率为500
å
/s~800
å
/s。
26.本实施例中,以铜(cu)制程中经过化学机械研磨(cmp)后的硅晶圆为例进行说明,因此所述清洗工艺需要去除的副产物包括sio2以及cu副产物(包括cu和cuo),所述晶圆表面优选为晶圆背面。本领域的技术人员可以理解的是,所述副产物还可以包括其他金属副产物,所述晶圆表面也可以为晶圆正面。
27.为确保清洗工艺中,刻蚀速率的稳定性,会对所述清洗工艺的工艺参数进行控制。优选的工艺参数包括:每片晶圆的清洗时间为3s~60s,所述混酸清洗液的温度为23℃~28℃,所述混酸清洗液的流量为750ml/min~850ml/min,喷洗方式为扫描方式喷洗。其中,由于清洗液的温度影响着刻蚀过程中发生的化学反应的速率,因此对刻蚀速率的影响较大,经实验测试后优选的清洗液温度范围为23℃~28℃。清洗液的流量对刻蚀速率也有一定的影响,经实验测试后,确定优选的清洗液的流量为750ml/min~850ml/min。另外,扫描式的喷洗比中心式喷洗会表现出更好的表面刻蚀速率均匀性。
28.本发明提供的晶圆清洗方法,为确保所述混酸清洗液的刻蚀速率维持在有效刻蚀速率范围内,需按照预定的时间间隔向所述混酸清洗液中补充预定量的hf。
29.优选地,所述预定的时间间隔为200s~800s,所述一定量的hf为0.01v mol/l~0.02v mol/l的hf,其中v为所述混酸清洗液的体积。可以理解的是,所述时间间隔优选为200s~800s,可以确保清洗过程中消耗的hf及时得到补充,并且在所述混酸清洗液的有效时间(清洗液维持有效刻蚀的时间,一般为数千秒)内,补充hf的次数一般为十几次,便于操作。所述预定量的hf不宜过少也不宜过多,过少会导致步骤s2中维持所述混酸清洗液的刻蚀速率的效果微弱,过多会导致在刚加入hf的短时间内所述混酸清洗液的刻蚀速率的较大提升引起刻蚀速率震荡甚至可能导致刻蚀速率超过预期的刻蚀速率范围,不利于保持所述混酸清洗液的刻蚀速率稳定性。补充预定量的hf的操作可以采用补充hf水溶液的方式进行,所述hf水溶液中hf的质量分数优选为不小于5%,以避免补充hf时向所述混酸清洗液中加入较多的水引起所述混酸清洗液的体积发生变化。
30.在上述的基础上,优选地,所述从清洗工艺开始按照预定的时间间隔向所述混酸清洗液中补充预定量的hf包括:在0min~40min内,每隔500s~800s向所述混酸清洗液中补充0.01v mol/l~0.02v mol/l的hf,在41min~80min内,每隔200s~300s向所述混酸清洗液中补充0.01v mol/l~0.02v mol/l的hf,其中v为所述混酸清洗液的体积。
31.以下,将结合图2~图4对上述的步骤s2的特征和优点进行说明。图2~图4表示不同方式补充hf的清洗方法中,所述混酸清洗液的刻蚀速率随刻蚀时间的变化曲线。需说明的是,图2~图4中的纵坐标的刻蚀速率指的是所述混酸清洗液对炉管制程中热氧化形成的sio2的刻蚀速率(采集适量的所述混酸清洗液对炉管制程中热氧化形成的sio2进行刻蚀,测量得到刻蚀速率),并非是所述清洗工艺对晶圆表面的刻蚀速率。这是由于所述混酸清洗液对晶圆表面的刻蚀速率较快,一般达到500
å
/s~800
å
/s,且刻蚀速率波动较大,导致难以测
量得到所述混酸清洗液对晶圆表面的刻蚀速率的准确值;并且业内通常用前述的第一标准对所述混酸清洗液的有效性进行评估判断,所述第一标准为:所述混酸清洗液对热氧化形成的sio2膜层的刻蚀速率稳定在205
å
/min~245
å
/min。图2~图4中的横坐标的刻蚀时间指的是所述混酸清洗液刻蚀各晶圆的总时间,在一般的单片式清洗工艺中,每片晶圆的刻蚀时间固定,并且所述混酸清洗液对晶圆进行逐一、连续地清洗,因此所述混酸清洗液刻蚀各晶圆的总时间与清洗的晶圆数量成正比,并且该总时间一般等于清洗工艺持续的时间。图2~图4对应的各清洗工艺中,除了补充hf的方式不同,其他工艺参数均相同,具体的工艺参数包括:每片晶圆的清洗时间为5s,所述混酸清洗液的温度为23℃~28℃,所述混酸清洗液的流量为750ml/min~850ml/min,所述混酸清洗液的体积为40l。并且图2~图4对应的清洗工艺均在单片式清洗机台中进行,清洗对象均为铜制程后的晶背,所述混酸清洗液逐一、批量地刻蚀各晶背表面,并进行总时长达80min的晶背清洗工艺。因此清洗晶圆的数量随着所述混酸清洗液的刻蚀时间线性增加。可以理解的是,图2~图4中测量了有限个不同时刻的所述混酸清洗液的刻蚀速率,并根据所述有限个刻蚀速率模拟出所述混酸清洗液的刻蚀速率随刻蚀时间的变化曲线。
32.请参阅图2,图2所示为不补充hf的晶圆清洗方法中(现有技术中),所述混酸清洗液的刻蚀速率随其刻蚀总时间的变化曲线。其中,随着所述混酸清洗液中hf的消耗,其刻蚀速率逐渐下降,在1200s(图2中t1)之后,刻蚀速率已跌出了215
å
/min(图2中v2)至235
å
/min(图2中v3)的稳定刻蚀速率范围,一般认为此时所述混酸清洗液失去刻蚀速率稳定性;进一步地,在2000s(图2中t2)之后,刻蚀速率已经小于205
å
/min(图2中v1),跌出了上述第一标准中所提到的有效刻蚀速率范围(205
å
/min~245
å
/min),此时所述混酸清洗液已经不再满足清洗工艺的要求,需要被更换。图2中的t1可定义为所述混酸清洗液的稳定刻蚀时间,即所述混酸清洗液保持稳定刻蚀速率的时间;图2中的t2可定义为所述混酸清洗液的有效刻蚀时间,即所述混酸清洗液保持有效刻蚀速率的时间。在2000s的有效刻蚀时间内,当每片晶圆清洗时间为5s时,清洗的晶圆数量为400片。提高所述t1和t2可以提高所述混酸清洗液的刻蚀稳定性和有效刻蚀时间,从而可提高清洗工艺的品质。
33.请参阅图3,图3所示为一实施例提供的晶圆清洗方法中,所述混酸清洗液的刻蚀速率随其刻蚀时间的变化曲线,在该清洗方法中,补充hf的方式为:每隔600s向所述混酸清洗液中补充0.02v mol/l的hf,其中v为所述混酸清洗液的体积。与图2相比,图3中的刻蚀速率在初次补充hf后的刻蚀时间内均有一定的提高,并且稳定刻蚀时间t1(图3中的t1),即刻蚀速率维持在215
å
/min(图3中v2)至235
å
/min(图3中v3)的稳定刻蚀速率范围内的时间,提高至2500s;在整个清洗工艺过程中(清洗工艺时间达到4800s),所述混酸清洗液的刻蚀速率均大于205
å
/min(图3中v1),因此所述混酸清洗液在整个清洗工艺中均保持有效,有效刻蚀时间t2(图3中的t2)达到4800s。与现有技术(图2所对应的晶圆清洗方法)相比,一实施例提供的晶圆清洗方法,所述混酸清洗液的稳定刻蚀时间t1(图3中的t1)提高了一倍(从1200s提升至2500s),有效刻蚀时间t2(图3中的t2)提高了至少一倍(从2000s提升至至少4800s)。在至少4800s的有效刻蚀时间内,当每片晶圆清洗时间为5s时,清洗的晶圆数量至少为960片,即与现有技术相比,一实施例中的所述混酸清洗液的清洗能力提高了至少一倍。因此一实施例提供的晶圆清洗方法,可有效提高所述混酸清洗液的刻蚀速率稳定性和使用效率。
34.图3中所示的刻蚀速率,在清洗工艺的后半段(40min之后),仍然存在不稳定的情
况(刻蚀速率跌出215
å
/min~235
å
/min的稳定刻蚀速率范围),因此可通过进一步优化补充hf的方式进一步提高所述混酸清洗液的刻蚀速率稳定性。
35.请参阅图4,图4所示为另一实施例提供的晶圆清洗方法中,所述混酸清洗液的刻蚀速率随其刻蚀时间的变化曲线,该实施例提供的晶圆清洗方法中,采用分段补充hf的方式,即:在0min~40min内,每隔500s补充0.02v mol/l的hf,在41min~80min内,每隔250s补充0.02v mol/l的hf,其中v为所述混酸清洗液的体积。图4所对应的的实施例在整个清洗工艺的后半段(40min之后),加快了hf的补充频率,有效提高了后半段的混酸清洗液的刻蚀速率,从而确保在整个清洗工艺中,所述混酸清洗液的刻蚀速率均维持在215
å
/min(图4中v2)至235
å
/min(图4中v3)的稳定刻蚀速率范围内。与现有技术(图2所对应的晶圆清洗方法)相比,图4所对应的另一实施例提供的晶圆清洗方法,稳定刻蚀时间t1(图4中的t1)至少提高了三倍(从1200s提升至至少4800s),有效刻蚀时间至少提高了一倍(从2000s提升至至少4800s),因此图4所对应的另一实施例提供的晶圆清洗方法,可有效提高所述混酸清洗液的刻蚀速率稳定性和使用效率。与图3所对应的一实施例相比,图4所对应的另一实施例提供的晶圆清洗方法,稳定刻蚀时间提高了近一倍(从2500s提高至至少4800s),进一步提高了清洗工艺的品质。
36.可以理解的是,上述各实施例中,补充hf的方式中涉及的具体参数选择为某一确定值,仅为了方便说明,这些具体参数是可以在合适的范围内变动的。例如,发明人经过大量的测试实验后,最终总结出较优的补充hf的方式包括:在0min~40min内,每隔500s~800s补充0.01v mol/l~0.02v mol/l的hf,在41min~80min内,每隔200s~300s补充0.01v mol/l~0.02v mol/l的hf,其中v是所述混酸清洗液的体积。在此表述中,补充hf的量可以是0.01v mol/l~0.02v mol/l之间的任意一个数值,补充hf的时间间隔也可以是200s~800s之间的合适数值;并且在同一种补充hf方式下,补充hf的时间间隔可以是不相同的,补充hf的量也可以是不同的。
37.并且如前所述,每次补充的hf的量需在一个合适范围内,在上述的各实施例中,每次补充0.01v mol/l~0.02v mol/l的hf时(其中v为所述混酸清洗液的体积),引起的短时间内刻蚀速率的提升不超过10
å
/min,较好地避免了补充hf引起的刻蚀速率的震荡,确保了刻蚀速率的稳定性,如图3和图4所示。
38.同时,根据前述的第二标准,对上述各实施例中的所述混酸清洗液对金属的去除效果进行评估,可进一步说明本发明的优点。以图4所对应的另一实施例为例,通过检测清洗工艺的不同时刻1000s、2000s、3000s、4000s、4500s被清洗的晶圆1、晶圆2、晶圆3、晶圆4、晶圆5在清洗前后的金属铜含量,形成图5所示的清洗前后含铜量对比柱状图。根据所述清洗前后铜含量对比柱状图,并根据前述的第二标准,可以判断图4所对应的另一实施例的所述混酸清洗液对金属副产物的去除能力是否符合标准。从图5中可以得出,在清洗前,各晶圆背面的铜原子数量在10
10
/cm2量级,清洗后的晶背铜原子数量不超过0.15
×
109/cm2(图5中虚线所示),满足第二标准,因此可视为对金属副产物的去除能力良好。上述的其他实施例中的所述混酸清洗液,经过所述第二标准的检测,也同样对金属副产物有良好的去除能力。因此,进一步证明了所述混酸清洗液的有效性。
39.综上所述,本发明提供的一种晶圆清洗方法,通过按照预定的时间间隔向所述混酸清洗液中补充预定量的hf,使所述混酸清洗液的刻蚀速率维持在有效刻蚀速率范围之
内,提高了所述混酸清洗液的有效刻蚀时间,从而提高了混酸清洗液的使用效率,解决了现有的清洗工艺中混酸清洗液的使用效率低和频繁更换混酸清洗液导致清洗机台产能降低的问题;同时本发明提供的晶圆清洗方法,也能提高混酸清洗液的稳定刻蚀时间,提高了所述混酸清洗液的刻蚀速率稳定性,提高了清洗工艺品质。
40.此外,可以理解的是,虽然本发明已以较佳实施例披露如上,然而上述实施例并非用以限定本发明。对于任何熟悉本领域的技术人员而言,在不脱离本发明技术方案范围情况下,都可利用上述揭示的技术内容对本发明技术方案作出许多可能的变动和修饰,或修改为等同变化的等效实施例。因此,凡是未脱离本发明技术方案的内容,依据本发明的技术实质对以上实施例所做的任何简单修改、等同变化及修饰,均仍属于本发明技术方案保护的范围内。而且还应该理解的是,本发明并不限于此处描述的特定的方法、化合物、材料、制造技术、用法和应用,它们可以变化。还应该理解的是,此处描述的术语仅仅用来描述特定实施例,而不是用来限制本发明的范围。必须注意的是,此处的以及所附权利要求中使用的单数形式“一个”、“一种”以及“该”包括复数基准,除非上下文明确表示相反意思。因此,例如,对“一个步骤”引述意味着对一个或多个步骤的引述,并且可能包括次级步骤。应该以最广义的含义来理解使用的所有连词。因此,词语“或”应该被理解为设有逻辑“或”的定义,而不是逻辑“异或”的定义,除非上下文明确表示相反意思。此处描述的结构将被理解为还引述该结构的功能等效物。可被解释为近似的语言应该被那样理解,除非上下文明确表示相反意思。