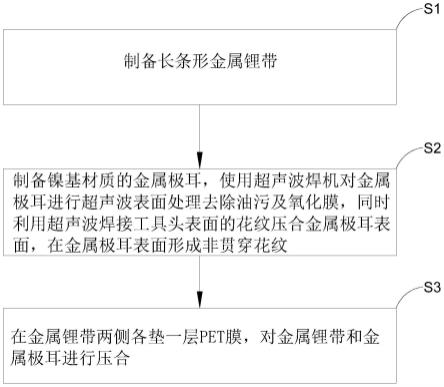
1.本发明属于新能源锂电池技术领域,更具体地说,是涉及一种锂金属负极极耳连接方法。
背景技术:2.金属锂的电位为-3.04v,是所有金属元素中电位最低的,其相对密度约为水的一半,密度=0.53g/cm3,也是所有金属元素中最轻的金属元素,金属锂具有极高的理论比容量(3860mah/g),所以以金属锂为负极活性物质的锂原电池具有超高的比能量,实际可达250~1000wh/kg,相当于锂离子电池的数倍。另外,锂原电池良好的安全性、贮存性能及便携性而备受市场(军用及民用)青睐。
3.目前的锂原电池虽可满足高比能的需求,但在比功率方面还存在一定的限制,除去材料体系本身限制外,电池制作工艺对电池功率特性影响也是较大的。由于锂金属质地极软、粘性大,在金属极耳焊接工序中不能使用超声焊设备去实现,所以通常采用金属极耳与金属锂带压合的方式去实现金属极耳的连接。采用此机械方式的连接,如果压力不够的情况下会造成金属极耳与金属锂带贴合不牢,接触不良。另外,金属极耳表面会存在一层致密光滑的氧化膜,而氧化膜的存在也会降低金属极耳与金属锂带的连接效果。锂金属在电池中作为负极集流体及活性物质同时存在,在电池使用过程中会逐渐消耗,如果金属极耳处连接效果较差,可能会出现局部或完全剥落情况,从而使得接触内阻变大,在大功率放电下会造成电池容量牺牲,产热严重甚至完全断路等问题。另外,如果压合过程中的压力过大会造成锂金属的延展,影响电池的尺寸,造成安全隐患。
技术实现要素:4.本发明的目的在于提供一种锂金属负极极耳连接方法,通过超声波焊机对金属极耳表面进行超声波表面处理,并在金属极耳表面形成非贯穿的花纹结构,提高金属极耳和金属锂带压合的结合效果。
5.为实现上述目的,本发明采用的技术方案是:提供一种锂金属负极极耳连接方法,包括以下步骤:
6.s1:制备长条形金属锂带;
7.s2:制备镍基材质的金属极耳,使用超声波焊机对金属极耳进行超声波表面处理去除油污及氧化膜,同时利用超声波焊接工具头表面的花纹压合金属极耳表面,在金属极耳表面形成非贯穿花纹;
8.s3:在金属锂带两侧各垫一层pet膜,对金属锂带和金属极耳进行压合。
9.在一种可能的实现方式中,步骤s2中,超声波焊机的焊接参数为:能量 10~30j,振幅30~65%,压力40~60psi;超声波焊接工具头采用锯齿形结构,以在金属极耳表面压合形成锯齿形非贯穿花纹。
10.在一种可能的实现方式中,步骤s2中,将垫好pet膜的金属锂带和金属极耳放在金
属托板上一起送入平压机进行压合处理;其中,平压机参数为:压力 0.2~0.4mpa,时间为3~5s。
11.在一种可能的实现方式中,步骤s1中,金属锂带的厚度为60~150μm,锂含量>99.9%,金属极耳厚度为0.1~0.2mm。
12.本发明提供的一种锂金属负极极耳连接方法的有益效果在于:与现有技术相比,通过超声波焊机对金属极耳表面进行超声波表面处理,并利用带有花纹的超声波焊接工具头压合金属极耳表面,在金属极耳表面形成非贯穿的花纹结构,提高金属极耳和金属锂带压合的结合效果。增强了金属锂带与金属极耳间的粘合效果,有利于降低电池内阻、提高导电效率、提高功率特性。可在较小的压力下得到紧密的锂金属极耳连接效果,对设备的功能性要求降低,操作简单、易实现产业化。
附图说明
13.为了更清楚地说明本发明实施例中的技术方案,下面将对实施例或现有技术描述中所需要使用的附图作简单地介绍,显而易见地,下面描述中的附图仅仅是本发明的一些实施例,对于本领域普通技术人员来讲,在不付出创造性劳动的前提下,还可以根据这些附图获得其他的附图。
14.图1为本发明实施例提供的一种锂金属负极极耳连接方法的工艺流程图;
15.图2为本发明实施例提供的一种锂金属负极极耳连接方法的结构示意图;
16.图3为经表面处理过和未经表面处理的镍金属极耳与锂片压合后结合程度对比图;
17.图4为实施例3和对比例1的电池内阻对比图;
18.图5为实施例3和对比例1的电池放电对比图。
19.附图标记说明:
20.1、金属锂带;2、金属极耳;3、表面处理后的极耳;4、未经表面处理的极耳。
具体实施方式
21.为了使本发明所要解决的技术问题、技术方案及有益效果更加清楚明白,以下结合附图及实施例,对本发明进行进一步详细说明。应当理解,此处所描述的具体实施例仅仅用以解释本发明,并不用于限定本发明。
22.请参阅图1和图2,现对本发明提供的一种锂金属负极极耳连接方法进行说明。所述一种锂金属负极极耳连接方法,包括以下步骤:s1:制备长条形金属锂带1;s2:制备镍基材质的金属极耳2,使用超声波焊机对金属极耳2进行超声波表面处理去除油污及氧化膜,同时利用超声波焊接工具头表面的花纹压合金属极耳2表面,在金属极耳2表面形成非贯穿花纹;s3:在金属锂带1两侧各垫一层pet膜,对金属锂带1和金属极耳2进行压合。
23.本发明提供的一种锂金属负极极耳连接方法,与现有技术相比,通过超声波焊机对金属极耳2表面进行超声波表面处理,并利用带有花纹的超声波焊接工具头压合金属极耳2表面,在金属极耳2表面形成非贯穿的花纹结构,提高金属极耳2和金属锂带1压合的结合效果。增强了金属锂带1与金属极耳2间的粘合效果,有利于降低电池内阻、提高导电效率、提高功率特性。可在较小的压力下得到紧密的锂金属极耳2连接效果,对设备的功能性
要求降低,操作简单、易实现产业化。
24.其中,超声波焊机的焊接参数为:能量10~30j,振幅30~65%,压力40~ 60psi。超声波焊接工具头采用锯齿形结构,以在金属极耳2表面压合形成锯齿形非贯穿花纹。
25.一种锂金属负极极耳连接方法,其中包括金属锂带1、金属极耳2以及金属极耳2预处理设备。金属极耳2经设备表面预处理与金属锂带1压合为紧密的一体结构。
26.其中,金属极耳2预处理设备为超声波焊机或其他设备。在超声焊处理过程中,换能器产生的高频振动通过锯齿状焊接工具头传递到待焊金属极耳2表面,金属极耳2界面金属氧化膜在一定的压力和超声振动的剧烈摩擦作用下破碎,而氧化膜的破碎也会增强金属极耳2与金属锂带1之间的粘合性。另外,磨擦导致金属极耳2温度升高使金属极耳2屈服强度降低,有利于金属极耳2 表面氧化膜破碎及发生塑性变形,经该锯齿状焊接工具头处理后表面会形成凹凸颗粒可增大与金属锂带1的接触面积,部分的凸起部分还能与金属锂带1实现嵌入的效果,最终使金属锂带1与金属极耳2更加牢固的粘合为一体。其中,通过设定合适的焊接参数,使金属极耳2在经过超声焊锯齿焊接工具头处理后不会造成穿孔,从而避免影响过流效果。
27.金属极耳2材质为金属镍或镀镍铜,厚度为0.1~0.2mm,包括带胶和不带胶金属极耳2。金属锂带1为电池级金属锂带1,锂含量>99.9%,厚度为60~ 150μm。
28.实施例1:
29.1.将0.06mm厚的金属锂带1裁切为58*900mm长度,裁切时注意金属锂带1上下铺pet膜防止粘连刀具。
30.2.将长65mm,宽4mm,厚度0.1mm金属镍基金属极耳2置于定位工装中经超声波焊机进行表面处理,使金属极耳2形成均匀凹凸的表面,该金属极耳 2不带胶块,其中焊接参数为:能量—20j,振幅—45%,压力—50psi。。
31.3.表面处理后金属镍基金属极耳2通过定位工装放置在金属锂带1固定位置,注意用金属极耳2表面凸起的一面接触金属锂带1,金属锂带1上下铺pet 膜,然后放在金属托板一起送放入平压机中进行压合,最终获得紧密连接的锂金属负极片。其中平压机参数设置为:压力—0.2mpa,时间—5s。
32.实施例2:
33.1.将0.07mm厚的金属锂带1裁切为50*850mm长度,裁切时注意金属锂带1上下铺pet膜防止粘连刀具。
34.2.将长53mm,宽6mm,厚度0.15mm金属镍基金属极耳2置于定位工装中经超声波焊机进行表面处理,使金属极耳2形成均匀凹凸的表面,该金属极耳2带胶块。其中焊接参数为:能量—30j,振幅—40%,压力—40psi。
35.3.表面处理后金属镍基金属极耳2通过定位工装放置在金属锂带1固定位置,注意用金属极耳2表面凸起的一面接触金属锂带1,金属锂带1上下铺pet 膜,然后放在金属托板一起送放入平压机中进行压合,最终获得紧密连接的锂金属负极片。其中平压机参数设置为:压力—0.3mpa,时间—4s。
36.实施例3:
37.1.将0.1mm厚的金属锂带1裁切为98*884mm长度,裁切时注意金属锂带 1上下铺pet膜防止粘连刀具。
38.2.将长53mm,宽10mm,厚度0.1mm金属镍基金属极耳2置于定位工装中经超声波焊机进行表面处理,使金属极耳2形成均匀凹凸的表面,该金属极耳2带胶块。其中焊接参数为:能量—10j,振幅—60%,压力—60psi。
39.3.表面处理后金属镍基金属极耳2通过定位工装放置在金属锂带1固定位置,注意用金属极耳2表面凸起的一面接触金属锂带1,金属锂带1上下铺pet 膜,然后放在金属托板一起送放入平压机中进行压合,最终获得紧密连接的锂金属负极片。其中平压机参数设置为:压力—0.4mpa,时间—5s。
40.对比例1:
41.1.将0.1mm厚的金属锂带1裁切为98*884mm长度,裁切时注意金属锂带 1上下铺pet膜防止粘连刀具。
42.2.将长53mm,宽10mm,厚度0.15mm金属镍基金属极耳2通过定位工装放置在金属锂带1固定位置,金属锂带1上下铺pet膜,然后放在金属托板一起送放入平压机中进行压合,最终获得连接完成的锂金属负极片。其中平压机参数设置为:压力—0.4mpa,时间—5s。
43.参考图3中对比表面处理后的极耳3与未经表面处理的极耳4与金属锂带 1压合效果,表面处理后的极耳3剥离后已和金属锂带1紧密的粘结为一体,而未经表面处理的极耳4总体可单独从金属锂带1剥离,说明其强度较弱。
44.将实施例3和对比例1的连接结构应用于锂二氧化锰电池中,两种方案各制作5支电池。电池包括正极二氧化锰、负极金属锂、隔膜、电解液、负极镍金属极耳2和铝正极金属极耳2。负极金属极耳2的连接结构采用实施例3和对比例1中制备的金属极耳2连接结构。
45.图4为分别应用实施例3和对比例1的连接结构制得的电池内阻测量情况。通过对比观察可发现应用实施例3所制得电池内阻明显低于对比例1所制得电池且整体均一性要优于对比例1所制得电池。原因为经过表面处理后的金属极耳2与金属锂带1连接强度增加,整体接触内阻变小。
46.对制得的锂锰电池进行大倍率放电,倍率为1.5c。图5为两种电池的放电曲线,其中1号电池的最低滞后电压为2.434v,放电容量为6.8ah,放电能量为16.45wh;2号电池最低滞后电压为2.229v,放电容量为6.5ah,放电能量为15.46wh。从电池放电性能对比1号电芯明显优于2号电芯,由此说明采用本发明方法可提高锂金属负极金属极耳2的连接可靠性,导电性能提高,有助于电芯最大容量的发挥。
47.以上所述仅为本发明的较佳实施例而已,并不用以限制本发明,凡在本发明的精神和原则之内所作的任何修改、等同替换和改进等,均应包含在本发明的保护范围之内。