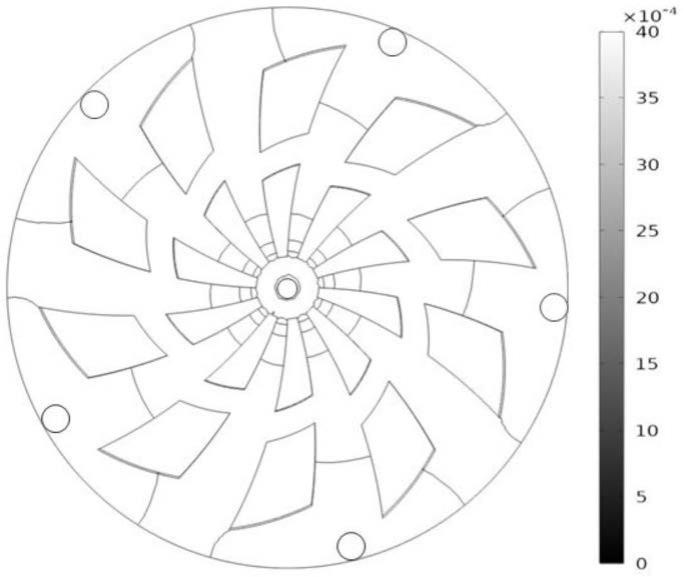
1.本发明涉及低温质子交换膜燃料电池技术领域,具体的说是一种能够促进流场内气体压强均匀分布、促进阴极侧水分排出、提高电池性能和稳定性的基于四周进气式螺旋辐射状流场的燃料电池双极板。
背景技术:2.质子交换膜燃料电池(proton exchange membrane fuel cells,pemfcs)是一种将氢气和氧气电化学反应中的化学能直接转化为电能的“化学能发电”装置,其能量转换效率不受卡诺循环的限制,电池组的发电效率可达50%以上。pemfcs具有环境友好、启动特性优良和能量转换效率高等特征,有望在诸多领域得到应用,特别是在汽车动力系统中的使用更具有得天独厚的优势。pemfcs电堆的核心部件包括膜电极和双极板,其中,双极板具有分配反应气体到达电极表面、收集和传导电子、支撑膜电极等重要作用,同时,双极板流道的设计还严重影响进、出口气体分布的均匀性、压力降以及排水能力,担负起整个电池系统的散热和排水功能,对电池的输出功率和长期稳定运行起到至关重要的作用。
3.pemfcs中的电极反应类同于其他酸性电解质燃料电池。阳极侧氢气通过双极板扩散到电极的催化层,并在催化剂的作用下发生氧化反应,产生的氢质子(h
+
)通过nafion质子交换膜电解质到达阴极,电子经双极板收集后由外电路到达阴极。阴极侧氧气(或空气)发生还原反应,与h
+
和电子反应生成水。生成的水除了润湿电解质外,过量的水则通过双极板随反应气体排出。由此可见,双极板流场的设计至关重要。
4.常见的双极板流场主要有平行流场、蛇形流场、交错流场等。蛇形流场的优点在于具有良好的水管理,电池性能高,缺点是气体分布不均,压降过大。平行流场可改善气体压降大、分布不均的缺点,但水管理能力差,电池内部易发生水淹。交错流场的优点在于有最佳的电池性能,容易排水,反应分布均匀,达到有效的水管理,缺点是压降非常高,泵送功率较大。最近,研究者们通过对流场进行优化和改进,逐渐衍生出了螺旋状的齿形流场、辐射流场、金属泡沫等复杂的结构设计。其中,螺旋状流场有利于水分的管理,从而降低进气所需的相对湿度,然而进、出口气体的压降较大;而辐射状流场可促进气体传输与电流密度均匀分布。
技术实现要素:5.本发明针对上述现有双极板流场结构中存在的缺点和不足,提出了一种旨在解决上述背景技术涉及的现有双极板流场结构中气体分布不均、压降不合理、水管理差等问题,从而提高电池整体功率性能和稳定性的基于四周进气式螺旋辐射状流场的燃料电池双极板。
6.为实现上述目的,本发明采用如下技术方案:
7.一种基于四周进气式螺旋辐射状流场的燃料电池双极板,包括对称设置的阴极板和阳极板,其特征在于,所述阴极板或阳极板均设有圆形基板,圆形基板外侧均匀设有至少
5个气体入口,圆形基板中央设有气体出口,所述圆形基板上设有交替排列的螺旋辐射凸脊和凹槽,凸脊和凹槽分别沿半径方向由圆形基板中央向圆形基板周向辐射,凸脊的中间有凹槽流道,凹槽流道连通相邻的两个凹槽,凹槽流道的深度一致;所述气体入口设置径向螺旋凹槽流道的中心线与圆形基体外侧流道中心线的交点处。
8.本发明所述圆形基板的半径为10-20mm,圆形基板外侧均匀设有5个、直径为1mm的气体入口,且气体入口均设置在对应的凹槽处;圆形基板中心设有1个、直径为1mm的气体出口。
9.本发明所述圆形基板内部有10条相邻的凸脊和凹槽分别交替排列,均沿半径方向、以18
°
由内向外宽度呈辐射状逐渐变大;所述的凸脊的外凸脊外沿弧度为20
°
,内侧弧度为19
°
,凸脊中间有扇形凹槽流道,将联通相邻的两个凹槽,凹槽流道的高度保持一致,为1mm深度。
10.本发明中内凸脊与外凸脊错开,内凸脊沿凸脊中心线顺时针偏移30
°
。
11.本发明中圆形基板上进气孔的数量优选为10个。
12.本发明中凹槽沿外部向圆形基板中心以0.06
°
的倾斜角下沉。
13.本发明所述圆形基板上设有气体入口、气体出口、螺旋辐射状流场凹槽、螺旋辐射状凸脊和外流道,在圆形基板外凸脊的外侧与内壁之间设有气体入口,在圆形基板中心设有气体出口;径向螺旋槽流道覆盖在圆形基板上,径向螺旋槽流道由十条螺旋向外的流道构成,由圆形基板中心呈辐射状向外逐渐变宽;径向螺旋槽流道与圆形基板内壁之间有5个进气孔,圆形基板中心为气体出口,基板上有10条沿半径方向的径向螺旋辐射状凹槽流道,在基板上呈中心对称;进气孔位于螺旋凸脊中心线与外流道中心线的交点处,且在两条螺旋凸脊间隔分布;凸脊侧面圆弧的切线与沿半径方向的夹角为20
°
,外凸脊的外流道侧斜面的弧度为20
°
;凸脊中间部分凹槽的弧度为19
°
;其中记圆形基板的中心点为o点,内凸脊的最外端点为a点,则oa之间距离为4mm,与内凸脊对应的外凸脊中,与a点处于同一弧线上的端点为b点,则ob之间距离为5mm,外凸脊的最外端点记为c点,则oc之间距离为8mm,内凸脊靠近圆形基板中心点的端点为d,则od之间距离为1mm,外凸脊中b端点的对角点记为e点,则oe弧与oc弧尖角为18度,oc弧的半径为15mm。
14.本发明提出的四周进气、中心出气式螺旋辐射状双极板流场内部的气体流速在中心出气口附近得到提升,且倾斜的流道有利于将产生的过多的水分及时排出,具有良好的排水能力,不易发生水淹现象;气体从进气口到出气口的压降减小,有利于气体充分反应,从而整体提高了电池的功率性能和稳定性。
附图说明
15.图1为本发明实施例1中燃料电池双极板结构中压力分布图。
16.图2为本发明实施例2中燃料电池双极板结构中与压力分布图。
17.图3为本发明实施例3中燃料电池双极板结构中压力分布图。
18.图4为本发明实施例4中燃料电池双极板流场中压力分布图。
19.图5为本发明实施例5对应的燃料电池双极板漏斗状流场结构的侧视图。
20.图6为本发明实施例5中燃料电池双极板流场中压力分布图。
21.图7为本发明实施例中分别以出气口圆心上方0.7mm处为圆点,出气口与进气口上
方0.7mm处连线为x轴,速度为y周构成的折线图。图8为本发明的一种结构示意图。
22.附图标记:圆形基板1、气体入口2、气体出口3、凸脊4、凹槽5、凹槽流道6、内凸脊7、外凸脊8、外侧流道9。
具体实施方式
23.本发明针对现有技术中存在的缺点和不足,提出了一种基于四周进气式螺旋辐射状流场的燃料电池双极板,包括对称设置的阴极板和阳极板,所述阴极板或阳极板均设有圆形基板1,圆形基板1外侧均匀设有至少5个气体入口2,圆形基板1中央设有气体出口3,所述圆形基板1上设有交替排列的螺旋辐射凸脊4和凹槽5,凸脊4和凹槽5分别沿半径方向由圆形基板中1央向圆形基板1周向辐射,凸脊4的中间有凹槽流道6,凹槽流道6连通相邻的两个凹槽5,凹槽流道6的深度一致;所述气体入口2设置径向螺旋凹槽5流道的中心线与圆形基体外侧流道9中心线的交点处。
24.本发明所述圆形基板1的半径可以为10mm,圆形基板1外侧均匀设有5个、直径为1mm的气体入口2,且气体入口2均设置在对应的凹槽处;圆形基板中心设有1个、直径为1mm的气体出口3。
25.本发明所述圆形基板1内部有10条相邻的凸脊4和凹槽5分别交替排列,均沿半径方向、以18
°
由内向外宽度呈辐射状逐渐变大;所述的凸脊4的外凸脊外沿弧度为20
°
,内侧弧度为19
°
,凸脊4中间有扇形凹槽流道,将联通相邻的两个凹槽5,凹槽5流道的高度保持一致,为1mm深度。
26.本发明中内凸脊7与外凸脊8错开,内凸脊沿凸脊中心线顺时针偏移30
°
。
27.本发明中圆形基板上进气孔的数量优选为10个。
28.本发明中凹槽沿外部向圆形基板中心以0.06
°
的倾斜角下沉。
29.下面结合本发明实施例和附图,对具体的技术方案进行完整的描述。
30.鉴于现有的双极板流道不能平衡气体分布、电流密度分布和水分分布,从而导致电极内部电化学反应不充分,降低了氢气和氧气的利用率,导致燃料电池的功率性能下降。为此,本发明提出了一种四周进气、中心出气式螺旋辐射状流道的双极板。本技术中,通过模拟流道内气体流速分布和压强分布,来评价燃料电池双极板流道设计的合理性。
31.实施例1
32.如图1所示,通过设置进气口流速为0.01m/s,通过comsol仿真结果发现,气体流速在0.002到0.01m/s之间的面积占凹槽总面积的41.54%;气体流速在0.01到0.06m/s之间的面积占凹槽总面积的5.27%;以气体出口为中心,5mm为半径内的凹槽的流速为到0.0001到0.0057;进气口气体压强为0.1474pa,到出气口的压降为0.1435pa。
33.实施例2
34.如附图2所示,实施例2与实施例1的区别在于:进气口的数量为10个,且在凹槽中心线与外侧流道中心线的交点处。通过comsol仿真结果发现:本实施例中气体流速在0.002到0.01m/s的面积占凹槽总面积的42.14%;气体流速在0.01到0.06m/s之间的面积占凹槽总面积的10.64%;进出口压力降为0.2656pa,比实施例1增大了83.00%.
35.实施例3
36.实施例3与实施例1的区别在于:内凸脊沿顺时针方向旋转30
°
。通过comsol仿真结
果发现:本实施例中气体流速在0.002到0.01m/s的面积占凹槽总面积的43.05%;气体流速在0.01到0.06m/s之间的面积占凹槽总面积的5.28%;。进出口压力降为0.1438pa,比实施例1增大的非常不明显。
37.实施例4
38.实施例4与实施例2的区别在于:双极板的圆形基体增加到半径为20mm,在凸脊的14mm和4mm处设有2个凹槽,联通相邻的螺旋凹槽。通过comsol仿真结果发现:本实施例中气体流速在0.002到0.01m/s的面积占凹槽总面积的49.24%气体流速在0.01到0.06m/s之间的面积占凹槽总面积的12.17%;进出口压力降为0.5185pa,比实施例1增大了261.29%;由于该模型末端流场部分所占的面积小,导致流速分布看起来高于其他实例。
39.实施例5
40.实施例5与实施例4的区别在于:圆形基体底部设计为沿外侧向中心倾斜0-10
°
的漏斗状流场,外流道深度为0.5mm,中心深度为1mm。通过comsol仿真结果发现:本实施例中气体流速在0.002到0.01m/s的面积占凹槽总面积的40.16%;气体流速在0.01到0.06m/s之间的面积占凹槽总面积的0.90%;进出口压力降为0.1597pa,比实例一增大了0.001%。
41.实施例6
42.实施例6与实施例5的区别在于:有五个进气孔改为十个进气孔。通过comsol仿真结果发现:本实施例中气体流速在0.002到0.01m/s的面积占凹槽总面积的42.95%;气体流速在0.01到0.06m/s之间的面积占凹槽总面积的20.23%;。进出口压力降为0.2871pa,比实例一增大了0.001%。
43.本发明通过四周进气、中心出气的方式,使双极板流场内气体压力降减少,气体分布更均匀;出气口流速增加,有助于气体推动燃料电池产生的水及时排出,防止电池“水淹”的问题。上述实施例仅为本发明的优选方案,不限制本发明的专利范围。因此,凡是利用本发明说明书及附图所优化的结构,直接或间接运用到燃料电池及其他相关领域的,均包括在本发明专利的保护范围内。