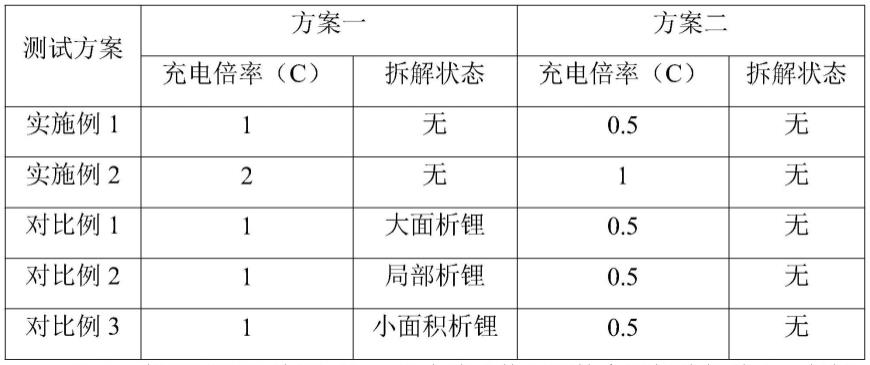
1.本发明属于电池制造技术领域,具体涉及一种高能量密度型极片及其制备方法和电芯。
背景技术:2.锂离子电池的迅速发展衍生出各种类型的电池,包括快充型锂离子电池,高能量密度型锂离子电池,低成本锂离子电池以及超长循环锂离子电池。目前,随着电动汽车的快速发展,市场对电动汽车的要求也越来越严格,既要满足长续航里程又要实现快速的充电。然而,从材料的本身来说高能量密度型电池所用的正负极材料的表面积和粒径等性质已经决定其无法实现2c到10c或者更高的倍率充放电,是材料本征的导电性低。而快充型电池在制备过程中需要添加更多的导电剂,其主材的活性占比较低,其能量密度是远低于高能量密度型电池。另一方面高能量密度型电池在充放电过程中的电流密度过大会导致电池的析锂带来极大的安全隐患。
3.高能量密度型电池的析锂是一个持续性过程,其基本原因可以理解为当2c的电流到达铜箔会产生2c的电子,这时电池电解液中的锂离子就需要2c的量和活性材料反应中和2c的电子,但是材料的导电性只能承受1c的中和反应过程,那多出1c的锂离子就会在材料表面沉积。主要原因在于铜箔的导电性很高,而材料的导电性很低,导致锂离子来不仅传输到整个活性空间,所以会在电流密度大的区域有过量的锂离子聚集,之后进行反应发生析锂。为了解决析锂的问题,在电池充电的时候降低电池内锂离子的浓度和限制传输到活性材料中的电流的速度。
4.中国专利cn 111354950a公开了一种箔材、其制备方法和电芯、电池模组以及储能设备,主要是用锂盐掺杂导电聚合物涂布在集流体上,通过锂盐的掺杂和脱掺杂实现电导与绝缘之间的相互转换,能够切断箔材与活性物质之间的电子通道,防止出现过充和过放电。然而,这种方法并不能实现高能量密度的高倍率充放电,同时也解决不了电池的析锂问题。
5.因此,找到既能提高锂离子电池快充性能又不会降低电池能量密度方法是二次电池领域急需解决的问题。
技术实现要素:6.本发明提供一种高能量密度型极片及其制备方法和电芯,其目的是为了解决现有技术中,高能量密度型电池无法实现高倍率充放电以及在高倍率充电条件下电池析锂的问题。
7.针对上述技术缺陷,本发明的目的之一是提供一种高能量密度型极片,本发明的目的之二是提供所述高能量密度型极片的制备方法,本发明的目的之三是提供包含所述高能量密度型极片的电芯。
8.第一方面,本发明提供一种高能量密度型极片,包括:集流体,以及自所述集流体
一侧面或双侧面起向外依次设置的氧化还原型导电聚合物层、高能量型活性材料层。
9.在上述高能量密度型极片中,作为一种优选实施方式,所述氧化还原型导电聚合物层中所述导电聚合物为聚乙炔、聚吡咯、聚噻吩或聚苯胺的掺杂态共轭聚合物;
10.所述掺杂态共轭聚合物中的掺杂物优选为碘蒸汽、质子酸、五氧化二砷、萘基锂或萘基钠;
11.所述掺杂物占所述掺杂态共轭聚合物的摩尔百分比为5-50%(例如:15%、25%、35%、45%),优选为10-30%。
12.优选地,所述导电聚合物的电导率为10-106s/cm(例如:102s/cm、103s/cm、104s/cm、105s/cm);但并不仅限于所列举的数值,该数值范围内其他未列举的数值同样适用。
13.在上述高能量密度型极片中,作为一种优选实时方式,所述氧化还原型导电聚合物层的厚度为1-100μm(例如:10μm、30μm、40μm、50μm、60μm、70μm、80μm、90μm),优选为5-20μm;
14.和/或,所述高能量密度型极片的厚度为50-200μm(例如:70μm、90μm、110μm、130μm、150μm、170μm、190μm)。
15.在上述高能量密度型极片中,作为一种优选实施方式,所述高能量型活性材料层的活性材料为石墨类或/和碳硅类高能量型活性材料。优选理论能量密度达到140mah/g以上的高能量型活性材料。所述石墨类高能量型活性材料为人造石墨。
16.在上述高能量密度型极片中,作为一种优选实施方式,所述氧化还原型导电聚合物层是通过将含有导电聚合物的胶液涂布到集流体上、经干燥、辊压后得到的。
17.在本发明的某一实施方案中,所述高能量型活性材料层是通过将含有高能量密度型活性材料的浆料涂布到所述氧化还原型导电聚合层上、经干燥、辊压后得到的。
18.在本发明的某一实施方案中,所述集流体的厚度为4.5-8μm(例如:5μm、7μm)。
19.在本发明的某一实施方案中,制备所述氧化还原型导电聚合物层和所述高能量型活性材料层时,按照1.2-1.8(例如:1.3、1.4、1.6、1.7)的压实比例(即辊压前厚度/辊压后厚度=1.2-1.8)进行辊压。
20.第二方面,本发明还提供了一种上述高能量密度型极片的制备方法,包括以下步骤,
21.s1:将含有导电聚合物的胶液涂布至集流体一侧面或两侧面,经干燥、辊压后得到带有氧化还原型导电聚合物层的集流体;
22.s2:将含有所述高能量型活性材料层的活性材料的浆料涂布至所述氧化还原型导电聚合物层上,经干燥、辊压后得到所述高能量密度型极片。
23.在上述高能量密度型极片的制备方法中,作为一种优选实施方式,在s1中,所述含有导电聚合物的胶液的涂布方式为微凹版涂布、凹版涂布和狭缝式涂布中的一种;
24.和/或,所述导电聚合物胶液的涂布厚度为1μm-100μm(例如:10μm、30μm、40μm、50μm、60μm、70μm、80μm、90μm),更优选为5μm-20μm;
25.和/或,所述含有导电聚合物的胶液的固含量为55%-70%(例如:50%、60%、65%、70%);这里的固含量为质量含量;
26.和/或,所述含有导电聚合物的胶液包括氧化还原型导电聚合物、第一粘结剂和第一溶剂。
27.更优选地,所述氧化还原型导电聚合物和第一粘结剂的质量比为(95-100):(0-5),且二者比例之和为100;
28.和/或,所述第一溶剂包括去离子水、乙腈、甲醇和n-甲基吡咯烷酮;
29.和/或,所述第一粘结剂为羧甲基纤维素钠(sbr),丁苯橡胶(cmc),聚偏氟乙烯(pvdf),聚氧化乙烯(peo)中的一种或多种;用于制备所述导电聚合物胶液的粘结剂包括但不限于上述粘结剂,能起到同样粘结作用的粘结剂都可适用于本发明。
30.在所述氧化还原型导电聚合层的制备方法中,所述第一溶剂的添加量根据所述导电聚合物胶液的固含量、氧化还原型导电聚合物的质量、粘结剂的质量计算可得。
31.在上述高能量密度型极片的制备方法中,作为一种优选实施方式,含有所述高能量型活性材料层的活性材料的浆料还包括导电剂、第二粘结剂和第二溶剂。导电剂、第二粘结剂和第二溶剂的种类和用量关系可以根据活性材料种类进行调整,均为常规技术,此处不再赘述。
32.第三方面,本发明还提供了一种电芯,包括多个负极极片、多个隔膜、多个正极极片,负极极片和正极极片交替设置且每个正极极片和每个负极极片之间均设置有隔膜,其中所述负极极片包括上述高能量密度型极片和快充型极片,所述快充型极片的活性材料倍率大于所述高能量密度型极片的活性材料倍率。
33.在上述电芯中,作为一种优选实施方式,所述快充型极片的个数满足以下公式:
34.n0=n(c
2-c1)/(c3+c
2-c1);
35.其中,n0是电芯中快充型极片个数,n是电芯中负极极片的总数,c2是电芯的实际倍率,c1是电芯中高能量密度型极片的最大承受倍率,c3是快充型极片的最大承受倍率。
36.在本发明中,n0取整数,当实算结果存在小数位数时,可以不考虑小数点后的数值,直接取整数部分或者整数部分加1即可。
37.本发明通过设置电芯中快充型极片的个数,可以在保证电芯能量密度不受影响的情况下,可以进行大倍率的充放电。
38.在上述电芯中,作为一种优选实施方式,所述快充型极片均匀分布于电芯中。
39.在上述电芯中,作为一种优选实施方式,所述电芯包括多个单体以及设置在相邻单体间的第一正极极片;每个所述单体包括一个所述快充型极片,以及在所述快充型极片两侧均设置的第二正极极片和所述高能量密度型极片,在单体中,所述快充型极片一侧的第二正极极片和所述高能量密度型极片数量相同,所述快充型极片两侧的极片数量相同或者相近(比如在单体中,其中一侧的极片总数与另一侧的极片总数之差为2或4,当差为2时,即一侧比另一侧少一个第二正极极片和一个高能量密度型极片);第二正极极片和负极极片交替设置,且相邻的第二正极极片和负极极片间均设置第二隔膜;相邻的单体与第一正极极片间也设置第一隔膜。
40.为了清楚表达本发明电芯的优选结构,上述优选电芯结构中,根据正极极片的位置不同将正极极片分为位于单体内的第二正极极片和位于单体外的第一正极极片,不同位置的正极极片的制备方法和活性材料相同;根据隔膜的位置不同将隔膜分为位于单体内的第二隔膜和位于单体外的第一隔膜,不同位置的隔膜的制备方法和材料相同;负极极片包括快充型极片和高能量密度型极片。
41.在上述电芯中,作为一种优选实施方式,所述快充型极片的活性材料层和高能量
密度型极片的活性材料层的厚度之比为(1-1.5):1;
42.所述高能量密度型极片的厚度为50-200μm。
43.在上述电芯中,作为一种优选实施方式,所述快充型极片的活性材料为石墨类或/和碳硅类快充型活性材料;所述石墨类快充型活性材料优选为硬碳或/和软碳。所述快充型极片的活性材料的倍率为1-50c,优选为1-5c。
44.在上述电芯中,作为一种优选实施方式,所述快充型极片的活性材料倍率与高能量密度型极片的活性材料倍率之差为0.2c-2c,优选为0.2c-1c;比如高能量型活性材料层活性材料的最大充放电倍率为0.33c,快充型极片活性材料的倍率为0.83c-1.33c。二者倍率差在本发明优选范围内,可以更好地构建浓度差,确保不会造成析锂情况的发生。当倍率差太大会让快充型极片析锂,太小会导致构建不了浓度差,没浓度差就无法发挥快充型极片的作用。
45.本发明的某些实施方案中,所述快充型极片按照常规负极极片的制备工艺进行制备,比如将快充型极片的活性材料、导电剂、粘结剂和溶剂制作成浆料,然后将其涂布到集流体上。
46.本发明的某些实施方案中,所述快充型极片活性材料和高能量型活性材料层活性材料的涂布都可以采用挤压式涂布、转移式涂布或喷涂中的一种来完成。
47.本发明电芯可以是卷绕式也可以是叠片式。本发明电芯还可以包括电解液/固体电解质、壳体等常规组件。
48.本发明电芯的正极极片的活性材料可以选用二次电池的常见正极活性材料,本发明优选为锂电池正极活性材料,比如是磷酸铁锂、磷酸钴锂、磷酸锰铁锂或镍钴锰酸锂三元材料。正极极片的制备可以采用常规湿法或干法制备。
49.在本发明电芯中,上述高能量密度型极片和快充型极片均作为负极使用,集流体优选为铜箔。
50.本发明与现有技术相比,至少具有如下有益效果之一:
51.1.本发明的氧化还原型导电聚合层采用具有共轭结构的共轭聚合物,将其和粘结剂混合制成浆料涂布在箔材层上,在充电时能够通过得失电子来降低电子进入活性材料的速度同时又不会影响电池的倍率充电,相当于一个容器暂存电子并逐步释放给活性材料。
52.2.本发明提供的氧化还原型导电聚合物能够在低电位结合电子,随着电位的逐渐升高会逐渐释放电子,能够有效化解高能量密度型活性材料的化学反应,从而提高其倍率性能,也就是快充性能。
53.3.本发明提供了一种电芯,在电芯中插入快充型极片,能够快速和锂离子相结合,在快充型极片和高能量密度型极片之间构建锂离子浓差梯度,降低高能量密度型极片表面的锂离子浓度,从而有效降低高能量密度型极片发生析锂的可能,并且提高了电池的快充性能。
54.4.本发明通过优化电芯结构,添加快充型的活性材料极片,将快充型极片和高能量密度型极片制成一个电芯,快充型极片在大功率充电时可以很快的和锂离子结合从而消耗电解液中的锂,锂离子在浓度差的作用下会减缓向高能量密度型极片的移动速度。
附图说明
55.图1为本发明制备的高能量密度型极片的结构示意图;
56.图2为实施例1中制备的电芯单元结构示意图;
57.图3为实施例1中制备的电芯的整体结构示意图;
58.图4为实施例1中氧化还原型导电聚合物的工作原理图;
59.图5为负极极片工作原理示意图,其中,(a)为快充型极片和高能量密度型极片间在充放电过程中的工作原理示意图;(b)为高能量密度型极片间在充放电过程中的工作原理示意图;
60.图6为实施例1中电芯循环100圈后的电芯拆解图;
61.图7为实施例2中制备的电芯单元之一的结构示意图;
62.图8为对比例1中电芯循环100圈后的电芯拆解图。
63.附图标记如下:
64.1-高能量密度型极片;2-快充型极片;3-正极极片;4-高能量型活性材料层;5-氧化还原型导电聚合物层;6-箔材层(集流体);7-快充型活性材料层。
具体实施方式
65.为使本发明的目的、技术方案和优点更加清楚,下面将结合本发明的实施例,对本发明实施例中的技术方案进行清楚、完整地描述。本领域技术人员应该明了,所述实施例仅仅是帮助理解本发明,不应视为对本发明的具体限制。基于本发明中的实施例,本领域普通技术人员在没有做出创造性劳动前提下所获得的所有其他实施例,都属于本发明保护的范围。
66.本发明的实施例是在以本发明技术方案为前提下进行实施,给出了详细的实施方式和过程,但本发明的保护范围不限于下述的实施例,下列实施例中未注明具体条件的工艺参数,通常按照常规条件。
67.在本发明中所披露的范围的端点和任何值都不限于该精确的范围或值,这些范围或值应当理解为包含接近这些范围或值的值。对于数值范围来说,各个范围的端点值之间、各个范围的端点值和单独的点值之间,以及单独的点值之间可以彼此组合而得到一个或多个新的数值范围,这些数值范围应被视为在本发明中具体公开。
68.实施例1
69.本实施例提供了一种在集流体上制备氧化还原型导电聚合层的方法,包括以下步骤:
70.(1)选择导电率为104s/cm的氧化还原型聚乙炔(掺杂物为碘,碘占聚乙炔的摩尔比为10%)作为氧化还原型导电聚合物。聚乙炔和丁苯橡胶(cmc)的质量比为96:4。首先按照导电聚合物胶液固含量65%计算去离子水的含量,然后将丁苯橡胶和去离子水全部加入到搅拌罐中,搅拌速度3000rpm,时间120min,再加入聚乙炔搅拌,搅拌速度3500rpm,时间为90min,得到导电聚合物胶液。
71.(2)使用微凹版涂布机将导电聚合物胶液涂布在铜箔材(厚度为6μm)的两面,经干燥、辊压后得到带有20μm厚的氧化还原型导电聚合物层的集流体,即复合集流体,其厚度为26μm。
72.本实施例还提供了一种高能量密度型极片及其制备方法,包括以下步骤:
73.选择人造石墨作为高能量密度型极片的活性材料,其充放电倍率为0.5c。将人造石墨和粘结剂cmc、导电剂sp按照96.5:2:1.5的比例一起制备成浆料采用挤压式涂布的方式涂布在氧化还原型导电聚合层上,经干燥、辊压后得到高能量密度型极片,其中单面高能量型活性材料层的厚度为58μm(即两面高能量型活性材料层总厚度为116μm)。高能量密度型极片的具体结构如图1所示,包括箔材层6,设置于箔材层6两侧面的氧化还原型导电聚合物层5以及设置在氧化还原型导电聚合物层5表面上的高能量型活性材料层4。高能量密度型极片的厚度为142μm。
74.本实施例还提供了一种快充型极片的制备方法,包括以下步骤:
75.选择硬碳作为快充型极片的活性材料,其充放电倍率为2c。将硬碳和粘结剂cmc、导电剂sp按照95.5:2.5:2的比例一起制备成浆料采用挤压式涂布的方式涂布在铜箔材(厚度为6μm)两侧面上,经干燥、辊压后得到快充型极片,活性材料层的厚度为58μm。快充型极片的厚度为122μm。
76.正极片的制备方法,包括如下步骤:将磷酸铁锂和导电剂sp、粘结剂pvdf按照96.8:2:1.2的比例制成浆料涂布在铝箔两面,经干燥、辊压,得到正极片。
77.本实施例还提供了一种电芯,电芯的基本构成为正极片、负极片和隔膜。其中负极片包括两种即本实施例制备的高能量密度型极片和快充型极片,根据公式:n0=n(c
2-c1)/(c3+c
2-c1),电芯负极片的总层数为20层,电芯的实际倍率c2为1c,高能量密度型极片的最大承受倍率c1为0.5c,快充型极片的最大承受倍率c3为2c。根据公式计算得出快充型极片的个数为4片。如图2和3所示的电芯结构示意图,其中,图2给出了电芯中单体的结构,即一个快充型极片2的两边分别设有2片高能量密度型极片1和2片正极极片3,正负极极片3交替设置且相邻极片间设置隔膜(图中未示出),具体地,快充型极片2的两侧叠置隔膜,然后隔膜上再叠置正极极片3,之后再在正极极片3上叠置隔膜,然后再在该隔膜上叠置高能量密度型极片1,后面依次叠置隔膜、正极极片3、隔膜、高能量密度型极片1,此结构为构成电芯的单元,整个电芯按照此单元叠片,整个电芯中包括四个单元,单元间设置正极极片3,单元间的正极极片3两侧叠置隔膜,由此形成整个电芯的基本结构,参见图3。当然,电芯中还包括必要的电解液和壳体,电解液和壳体可以是锂离子电池的常规电解液和壳体,在本实施例中使用的电解液的电解质为lipf6,溶剂为体积比为1:1的碳酸乙烯酯(ec)和碳酸二甲酯(dmc),隔膜材质为pe。得到的电芯的理论容量为20ah。
78.如图4所示,电芯中氧化还原型导电聚合物的工作原理图,外电路电子首先流经箔材,箔材的导电性(106s/cm)很高几乎对电子不构成阻碍作用,电子会传导至导电聚合物上,导电聚合物具有优异的导电性,尽管其导电性不如箔材,因其导电聚合物是氧化还原型聚合物,具有共轭结构,能够通过氧化还原得失电子,所以电子的传输速度会相对降低但是数目不会减少。在充电初期,电芯的电压比较低导电聚合物发生n-型掺杂被还原,导电聚合物先容纳部分电子,一部分电子传输到高能量型活性材料层4,活性材料接收的电子数目减少,对应的锂离子数目减少,高能量密度型极片1依据本身的倍率足够处理这些锂离子而不会析锂。随着电压的升高,导电聚合物发生p-型掺杂被氧化失去电子补充到高能量型活性材料层4。氧化还原型导电聚合物层5相当于电子储存器,暂时储存体系的电子,但不会降低体系的电子个数,也不会降低电芯的倍率性能。
79.如图5所示,快充型极片2和高能量密度型极片1之间的锂离子传输,此传输不叠加氧化还原型导电聚合物层的作用。在充电过程中正极失去锂离子进入电解液中,之后锂离子会从正极移动到负极并与负极发生反应。在大倍率下如果负极的倍率低于充电倍率则电解液中的锂离子的消耗就是一个非平衡状态,锂离子浓度就会急剧上升,在电场的作用下锂离子就会快速沉积在负极材料表面导致析锂的发生。快充型负极片由于具有比较大的充电倍率,在充电过程中会迅速消耗极片周边的锂离子,从图5(b)中可以看出没有快充型负极片的电芯其锂离子浓度是相对均匀的,有快充型负极片的电芯,参见图5(a),高能量密度型极片周边的锂离子会因为快充型极片周围的锂离子浓度降低在浓差作用力下和电场驱动下逐渐向快充型极片负极移动从而达到降低高能量型负极片周边的锂离子浓度,减少析锂的风险。
80.对本实施例组装的电芯性能进行测试,具体测试方法如下:方案一:在常温25℃条件下,充电工步以1c的倍率恒流恒压充电到3.65v,放电工步以0.5c为恒流放电到2.5v,100圈循环后,拆解电芯以查看极片表面是否析锂。同时设置方案二:充电工步以0.5c的倍率恒流恒压充电到3.65v,放电工步以0.5c为恒流放电到2.5v,100圈循环后,拆解电芯查看极片表面是否析锂的对照试验。
81.在上述导电聚合物层和快充型负极片的作用下,电池的倍率性能得到明显的提升,完全能够实现从0.5c到1c的提升,并且如图6所示,100圈循环后,拆解电芯发现极片的表面没有发生析锂,具体结果参见表1。
82.实施例2
83.本实施例提供了一种在集流体上制备氧化还原型导电聚合层的方法,包括以下步骤:
84.(1)选择导电率为103s/cm的氧化还原型聚苯胺(掺杂物为质子酸,质子酸占聚苯胺的摩尔比为15%)。聚苯胺和聚氧化乙烯(peo)的质量比为95:5。
85.首先按照导电聚合物胶液固含量70%计算n-甲基吡咯烷酮(nmp)的含量,然后将聚氧化乙烯和n-甲基吡咯烷酮全部加入到搅拌罐中,搅拌速度3500rpm,时间100min,再加入聚苯胺搅拌,搅拌速度4000rpm,时间为110min,得到导电聚合物胶液。
86.(2)使用微凹版涂布机将导电聚合物胶液涂布在铜箔材(厚度为6μm)的两面,经干燥、辊压后得到带有25μm厚的氧化还原型导电聚合层的集流体,即复合集流体,其厚度为31μm。
87.本实施例还提供了一种高能量密度型极片及其制备方法,包括以下步骤:
88.选择人造石墨作为高能量密度型极片的活性材料,其充放电倍率为1c。将人造石墨和粘结剂cmc、导电剂sp按照96:2:2的比例一起制备成浆料采用挤压式涂布的方式涂布在氧化还原型导电聚合层经干燥、辊压后得到高能量密度型极片,其中单面高能量型活性材料层的厚度为50μm。高能量密度型极片的厚度为131μm。高能量密度型极片的具体结构如图1所示。
89.本实施例还提供了一种快充型极片的制备方法,包括以下步骤:
90.选择硅氧石墨作为快充型极片的活性材料,其充放电倍率为3c。将硅氧石墨(由硅氧30%,石墨70%复配而成)和粘结剂cmc、导电剂sp按照95:3:2的比例一起制备成浆料采用挤压式涂布的方式涂布在铜箔材(厚度为6μm)两侧面上,经干燥、辊压后得到快充型极
片,单面活性材料层的厚度为55μm。快充型极片的厚度为116μm。
91.正极片的制备方法,包括如下步骤:将磷酸铁锂和导电剂sp、粘结剂pvdf按照96.8:2:1.2的比例制成浆料涂布在铝箔两面,经干燥、辊压,得到正极片。
92.本实施例还提供了一种电芯,电芯的基本构成为正极片、负极片和隔膜,其中负极片包括两种即本实施例制备的高能量密度型极片和快充型极片。根据公式:n0=n(c
2-c1)/(c3+c
2-c1),电芯负极片的总层数为30层,电芯的实际倍率c2为2c,高能量密度型极片的最大承受倍率c1为1c,快充型极片的最大承受倍率c3为3c。根据公式计算得出快充型极片的个数为7片。如图7所示的电芯单元结构示意图,快充型极片2的两边分别有3片高能量密度型极片1和3片正极极片3,由于高能量密度型极片的数量为23片,无法保证每个快充型极片2两侧都分别有3片高能量密度型极片,所以对于其中一个快充型极片2的单侧不能满足3片高能量密度型极片,可以改为2片高能量密度型极片1和2片正极极片3,即有三个电芯单元是快充型极片2的两边分别有3片高能量密度型极片1和3片正极极片3,有一个电芯单元是快充型极片2的一侧有3片高能量密度型极片1和3片正极极片3,另一侧有2片高能量密度型极片1和2片正极极片3。整个电芯按照此单元叠片。具体地,整个电芯中包括四个单元,单元间设置正极极片3,单元间的正极极片3两侧叠置隔膜,由此形成整个电芯的基本结构。当然,电芯中还包括必要的电解液和壳体,电解液和壳体可以是锂离子电池的常规电解液和壳体,在本实施例中使用的电解液的电解质为lipf6,溶剂为体积比为1:1的碳酸乙烯酯(ec)和碳酸二甲酯(dmc),隔膜材质为pp。得到的电芯的理论容量为35ah。
93.对本实施例组装的电芯性能进行测试,具体测试方法如下:方案一:在常温25℃条件下,充电工步以2c的倍率恒流恒压充电到3.65v,放电工步以0.5c为恒流放电到2.5v,100圈循环后,拆解电芯以查看极片表面是否析锂。同时设置方案二:充电工步以1c的倍率恒流恒压充电到3.65v,放电工步以0.5c为恒流放电到2.5v,100圈循环后,拆解电芯查看极片表面是否析锂的对照试验。
94.本实施例使用了电导性小的导电聚合物是因为peo是电导型粘结剂,可以起到导电子的作用,并且涂厚了导电聚合物层使用了更大倍率的快充型极片,能够有效提高电芯的实际倍率并且不会析锂,具体结果参见表1。
95.对比例1
96.本对比例与实施例1相同,不同之处在于没有氧化还原型导电聚合物层和快充型负极极片。电芯结构中,快充型负极极片由高能量密度型极片代替。
97.电芯性能测试同实施例1。
98.如图8所示,100圈循环后,拆解电芯发现极片的表面发生析锂,具体结果参见表1。
99.对比例2
100.本对比例与实施例1相同,不同之处在于没有快充型极片,电芯结构中,快充型负极极片由高能量密度型极片代替。
101.电芯性能测试同实施例1。
102.100圈循环后拆解电池发现极片表面有小区域析锂,主要是由于高能量密度型极片表面的锂离子浓度过高,增加了析锂的风险,具体结果参见表1。
103.对比例3
104.本对比例与实施例1相同,不同之处在于没有氧化还原型导电聚合层。
105.电芯性能测试同实施例1。
106.100圈循环后拆解电池发现极片表面析锂,但是析锂程度低于对比例1,具体结果参见表1。
107.表1不同测试倍率的电池拆解结果汇总
[0108][0109]
从表1的测试汇总结果可知,导电聚合物层和快充型极片的结合,能够缓冲高能量型极片在高倍率充电时表面的锂离子电池的浓度,能够起到提升电池倍率的作用。
[0110]
以上所述仅为本发明的较佳实施例而已,并不用以限制本发明,凡在本发明的精神和原则之内,所作的任何修改、等同替换、改进等,均在本发明待批权利要求保护范围之内。