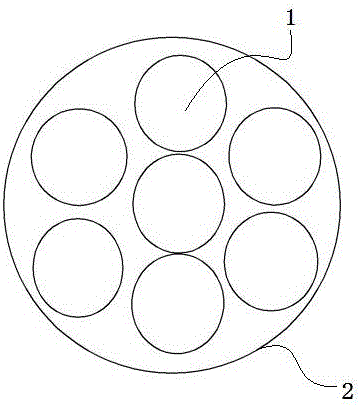
本发明涉及一种在海上使用的水中构件装置系留缆绳及其制作方法。
背景技术:海上水中构件装置主要指海面浮筒泊位、浮标、潜标、航标灯、水中兵器(水雷)等。过去这些水中构件装置在使用时的系留缆绳都采用钢丝缆绳或锚链。现在随着系留缆绳系统装置使用范围的扩大和水深的增加,系留缆绳加长,重量随之增加,浮体浮力无法支承。根据我国海区情况和海军、海事(航管)部门的要求,不可能再用钢丝缆绳或锚链作为系留索,需要替代材料。在实际使用中发现单层8股、12股结构缆绳容易被海上风力割断和磨损,并不适合海上深水系泊。国内外10多年海上系泊系统缆绳使用证明,超高分子量聚乙烯(UHMWPE)纤维是目前世界上强度最高的商业化高性能纤维。等直径时,其强度及伸长率与相应的钢缆相近,但重量仅为钢缆的15%;等重量时,其强度比钢缆高15倍之多;其使用寿命比普通化纤缆绳一般高出2~3倍。用其纤维材料制成的系泊缆绳具有高强、高模、轻质、低延伸、低蠕变,断裂伸长率只有3%左右、耐海水腐蚀、耐紫外线辐射、漂浮于水、操作方便、经久耐用、安全性高等特点,所以超高分子量聚乙烯缆绳最适合长时间深水海上系泊的应用。但在实际使用中发现,超高分子量聚乙烯系泊缆绳如在高温和持久强力下使用会发生蠕变性能不太好之弱点,而蠕变的发展可导致纤维材料的破损和老化失效,限制其在海上系泊中的长期应用。如作为长久性海上水中构件装置系留缆绳选用基材必须对其蠕变性能加以改善与提高,确保长久性海上水中构件装置系留缆绳在实际使用条件下的可靠性、耐久性、安全性。
技术实现要素:本发明要解决的技术问题是提供一种内层缆芯由超高分子量聚乙烯制成8股形态结构,外层由耐磨高强型涤纶纤维编织成固定护套,具有更轻、更安全、更耐久性能的缆绳及其制作方法;为克服现有系留缆绳索扣存在的不耐磨和容易打滑松脱的现象,并保证缆绳及索扣综合性能的利用。为了解决上述技术问题,本发明提供了一种海上用水中构件装置系留缆绳,为皮芯复合双层结构;内层缆芯由DM20超高分子量聚乙烯制成的8股形态结构,外层为耐磨高强型涤纶的固定护套。本发明一种海上用水中构件装置系留缆绳制作方法如下:步骤一:8股形态结构的缆芯制备方法如下:a、制粗纱,选取纤度DM20超高分子量聚乙烯纤维3根通过拼线机捻合成粗纱;b、制绳纱,将7根合成的粗纱通过加捻机捻合成绳纱;c、制绳股,将3根合成的绳纱通过制股机捻合成绳股;d、编绳,将8根合成的绳股经制绳机编织成8股缆芯;e、浸树脂,将8股缆芯经自动浸胶机多次重复浸渍、涂覆LAG045树脂,并通过挤胶装置,挤出多余的树脂;f、预拉处理,采用特制拉力机对缆芯进行预拉,拉力为缆绳设计的实际使用拉力的2~3倍,预拉时间50~60秒,通过预拉处理,使缆芯形态相对固定,蠕变减小;g、烘干,预拉处理后,将缆芯放到绳架上晾干或送入烘房烘干,同时卷装成形候用;步骤二、固定护套编制如下:a、拼线,选取纤度1118D耐磨高强型涤纶长丝3根,捻合成粗纱;b、加捻,将拼线后的7根粗纱,通过加捻机进行加捻,制作绳纱;c、制股,将加捻后的3根绳纱,在制股机上制成符合双层编绳机锭子大小的筒子绳股;d、编制,将32根绳股围绕缆芯经双层编绳机一次性编织成固定护套。采用本发明后,其有益效果为:采用超高分子量聚乙烯纤维,其超高分子量聚乙烯(UHMWPE)纤维是目前世界上强度最高的商业化高性能纤维。等直径时,其强度及伸长率与相应的钢缆相近,但重量仅为钢缆的15%;等重量时,其强度比钢缆高15倍之多;其使用寿命比普通化纤缆绳一般高出2~3倍。用其纤维材料制成的系泊缆绳具有高强、高模、轻质、低延伸、低蠕变,断裂伸长率只有3%左右、耐海水腐蚀、耐紫外线辐射、漂浮于水、操作方便、经久耐用、安全性高等特点,所以超高分子量聚乙烯缆绳最适合长时间深水海上系泊的应用。但在实际使用中发现,超高分子量聚乙烯系泊缆绳如在高温和持久强力下使用会发生蠕变性能不太好之弱点,而蠕变的发展可导致纤维材料的破损和老化失效,限制其在海上系泊中的长期应用。如作为长久性海上水中构件装置系留缆绳选用基材必须对其蠕变性能加以改善与提高,确保长久性海上水中构件装置系留缆绳在实际使用条件下的可靠性、耐久性、安全性。超高分子量聚乙烯缆绳蠕变的程度取决于UHMWPE纤维的型号、工作温度、平均载荷和加载时间。通过改善与提高UHMWPE蠕变性能后,使得Dyneema纤维既具有最高的拉伸强度和模量,又具有最好的抗蠕变性能。不同蠕变性能Dyneema等级纤维特性与应用比较长久性海上水中构件装置系留缆绳绳体选用具有超低蠕变性能的超高分子量聚乙烯DM20等级纤维制成缆芯,经实验室测试证明达到系留缆绳高强、超轻、低延展、耐疲劳、30年持久寿命的基本特性要求。为进一步增强系留缆绳使用的耐磨性、耐久性、耐候性,控制磨损和老化程度,保持缆绳强度的最佳化,系留缆绳缆芯外层设有固定护套,选用耐磨高强型涤纶纤维(PET)制作。不仅耐磨性能好、高强,而且低延展、耐疲劳性能良好,综合性能媲美锦纶。同时由于涤纶纤维价格便宜,相比锦纶等纤维更具性价比,相比普通涤纶长丝,耐磨高强型涤纶具有更好的耐磨性,能完善缆绳对耐磨性要求较高产品的性能。不同纤维材料耐磨及基本性能比较超高分子量聚乙烯和耐磨高强型涤纶复合双层结构系留缆绳既能满足水中构件装置在风暴中定位时最大载荷对刚度的要求,又能保证具有足够的弹性来削弱由波浪运动引起的最大峰值载荷。已经证明UHMWPE-PET复合双层结构绳缆是最适合长时间固定深海水中构件装置海上系留的应用。同时确认这种复合双层结构缆绳在海上深水中的应用比钢缆和锚链系泊系统具有更轻、更安全、更耐久的优势。超高分子量聚乙烯和耐磨高强型涤纶皮芯复合双层结构系留缆绳不仅具备超高分子量聚乙烯缆绳强度大、重量轻、低延展、低蠕变、耐老化、浮于水、易操作的特点,而且具有和涤纶相当的摩擦系数及耐磨性能,从而极大地延长缆绳的使用寿命。附图说明图1为本发明海上用水中构件装置系留缆绳皮芯复合双层结构示意图。图2为本发明海上用水中构件装置系留缆绳截面结构示意图。具体实施方式如图1和图2所示,一种海上用水中构件装置系留缆绳,为皮芯复合双层结构;内层缆芯1由DM20超高分子量聚乙烯制成的8股形态结构,外层为耐磨高强型涤纶纤维编织的固定护套2。本发明一种海上用水中构件装置系留缆绳制作方法,其制作过程如下:步骤一:8股形态结构的缆芯制备方法如下:a、制粗纱,选取纤度DM20超高分子量聚乙烯纤维3根通过拼线机捻合成粗纱;b、制绳纱,将7根合成的粗纱通过加捻机捻合成绳纱;c、制绳股,将3根合成的绳纱通过制股机捻合成绳股;d、编绳,将8根合成的绳股经制绳机编织成8股缆芯;e、浸树脂,将8股缆芯经自动浸胶机多次重复浸渍、涂覆LAG045树脂,并通过挤胶装置,挤出多余的树脂;f、预拉处理,采用特制拉力机对缆芯进行预拉,拉力为缆绳设计的实际使用拉力的2~3倍,预拉时间50~60秒,通过预拉处理,使缆芯形态相对固定,蠕变减小;g、烘干,预拉处理后,将缆芯放到绳架上晾干或送入烘房烘干,同时卷装成形候用;编织工艺的关键在于控制缆芯的直径,提高强力和力求粗细均匀。控制直径主要在于适当配置纤维的根数并合理组合,而缆芯的强度除与纤维材料的强度有关外,还与纤维纤度和编织时的密度大小有关。一般来说,纤度大有利于强度利用率的发挥。另外,随着编织密度的减小,则缆芯的强度就增大。编织密度不能过大,否则缆芯不仅强度低而且手感较硬。编织密度适当调节,不仅有利于强度的提高,而且还能获得良好的手感,缆芯的粗细均匀性与编织时的张力有关。在制粗纱、制绳纱、制绳股和编绳过程中,保持每根纤维所受张力基本一样,捻距控制在20~30cm。在制粗纱、绳纱、绳股时,均具有一定的捻度,这样可以确保单丝的断裂不会将强度的损失传递很远,一般在几个捻距后就没有影响了。同样单股绳纱的强力损失也不会传递很远。这样提高了缆绳的整体耐磨性能,即便缆绳表面磨起毛,也不会对强度产生大的影响。实际使用证明,这种编织工艺与普通编织工艺相比缆绳强力能够提高8~10%。步骤二、固定护套的编制如下:a、拼线,选取纤度1118D耐磨高强型涤纶长丝3根,捻合成粗纱;b、加捻,将拼线后的7根粗纱,通过加捻机进行加捻,制作绳纱;c、制股,将加捻后的3根绳纱,在制股机上制成符合双层编绳机锭子大小的筒子绳股;d、编制,将32根绳股围绕缆芯经双层编绳机一次性编织成固定护套。上述工艺流程为: